降低硫酸法烷基化酸耗
硫酸烷基化装置工艺优化及节能措施

硫酸烷基化装置工艺优化及节能措施发布时间:2022-10-26T03:10:15.261Z 来源:《科学与技术》2022年第6月第12期作者:李奥[导读] 本文基于对硫酸烷基化装置工艺的研究李奥天津石化化工部天津市滨海新区 300270摘要:本文基于对硫酸烷基化装置工艺的研究,通过对硫酸烷基化概述、硫酸烷基化装置在使用中存在的问题、硫酸烷基化装置工艺的进一步优化以及硫酸烷基化装置工艺的节能措施四个方面的阐述,以期进一步保障硫酸烷基化装置的平稳高效运行。
关键词:硫酸烷基化;烷基化反应;工艺优化;节能措施硫酸烷基化工艺是近年来新建烷基化装置所采用的主流技术之一,但由于其自身存在的特点,例如所需反应温度较低、需要大量异丁烷循环等,使烷基化工艺的能耗较高[1],因此在运用硫酸烷基化装置生产的过程中,如何进行节能降耗工作至关重要,需要不断的进行工艺优化,完善硫酸烷基化装置的使用流程。
1、硫酸烷基化概述(1)烷基化反应烷基化反应是指在酸性催化剂的作用下,烷烃分子与烯烃分子发生的化学加成反应[2]。
在烷基化反应中,烯烃取代了烷烃分子中的活泼氢原子的位置,烷基化装置原料是以催化裂化气体中异丁烷和异丁烯、丁烯-1为主。
在烷基化中常用的酸性催化剂包括硫酸、磷酸、氢氟酸、三氯化铝等。
(2)硫酸烷基化硫酸烷基化是硫酸作为催化剂,实现烯烃烷基化,包括阶梯式和管壳式两种方式,为了使反应保持在较低的温度下进行,阶梯式采用反应物本身部分蒸发吸热降温,管壳式采用反应后的流出物节流膨胀制冷的方法。
影响硫酸烷基化的主要因素包括:反应温度,硫酸烷基化反应的适宜温度在8-12摄氏度之间;硫酸的浓度,适宜的硫酸浓度为95-96mol%,若硫酸浓度高于99mol%,三氧化硫会与异丁烷直接反应,增加酸耗,若是硫酸浓度低于85mol%,催化剂的活性大幅度降低,同时对设备产生严重腐蚀;酸烃比,在实际生产操作中,一般采用1~1.5:1的酸烃比,以确保硫酸处于连续相;除此之外,影响硫酸烷基化的因素还包括异丁烷与烯烃的比例、烃类在硫酸中的分散情况以及反应时间。
低温硫酸法烷基化装置设计方案优化

缩机采用电机驱动( 配齿轮箱) ꎮ
2. 2 方案Ⅱ
制冷压缩机采用 3. 5 MPa( 表压ꎬ下同) 蒸汽
油提供ꎻ制冷压缩机采用 3. 5 MPa 蒸汽全凝式汽
烃含量、改善汽油平均品质、增加汽油调和手段ꎬ
品结构、增加汽油收率ꎬ采用成熟可靠的烷基化工
实现汽油产品国Ⅵ质量升级的需求ꎻ2) 反应馏出
艺生产烷基化油对于改善碳四资源经济性和实现
物采用聚结分离工艺ꎬ无需设置酸洗、碱洗、水洗
汽油产品质量升级具有重要意义ꎮ 烷基化工艺可
流程ꎬ碱液排放量降低ꎬ减少装置的加工和操作费
正丁烷塔和脱丙烷塔再沸器ꎻ电力消耗主要的设
备用户是制冷压缩机ꎬ再沸器蒸汽消耗和制冷压
沸器热源全部由 3. 5 MPa 蒸汽抽汽 / 凝汽式汽轮
机提供ꎮ
2. 3 方案Ⅲ
再沸器采用导热油作为热源ꎬ夏季工况时全
缩机负荷见表 1ꎮ 为平衡全厂蒸汽管网及其电力
厂低压蒸汽过剩ꎬ充分利用过剩的 1. 0 MPa 蒸汽
案和再沸器热源方案的设计并进行多方案比选ꎬ
作ꎮ 联 系 电 话: 0532 - 80950655ꎻ E - mail: xubiao @
以优化烷基化装置设计方 案 和 全 厂 公 用 工 程 管
cnpccei. cn
2019 年第 4 期( 第 36 卷)
徐 彪等. 低温硫酸法烷基化装置设计方案优化
关键词: 烷基化 制冷压缩机 再沸器 公用工程优化
doi:10. 3969 / j. issn. 1005 - 8168. 2019. 04. 007
随着国民经济持续高速增长ꎬ国家对节能减
网ꎬ降低装置能耗ꎬ提高装置经济技术水平ꎮ
质量要求也越来越高ꎬ实现油品质量与国际接轨、
硫酸法烷基化装置节能降耗措施

硫酸法烷基化装置节能降耗措施摘要:近年来,根据现场操作总结,不断提出技改措施以降低装置能耗和酸耗,并取得了良好的效果。
具体措施包括降低脱异丁烷塔、脱正丁烷塔的操作压力,降低制冷压缩机出口压力,调整反应器的操作参数,设置原料的预处理措施,建设废酸处理装置和正丁烷异构装置等,大幅地降低了装置的能耗和酸耗,取得了良好的经济效益。
关键词:硫酸法;烷基化装置;节能降耗;一、硫酸法烷基化装置节能原因在相同烯烃进料情况下,两种制冷方案制冷剂和循环异丁烷总量基本没有变化,反应器人口烷烯物质的量比和温度同样差别不大。
节能罐方案时,循环异丁烷浓度略低,制冷剂和循环异丁烷总量略大一些,烷烯物质的量比略小。
压缩机设计时一般每段压缩比为2.5~3,因此无论哪种制冷方案,制冷压缩机设计都会按照两段进行设计。
两种制冷方案下压缩机设计制造的显著区别是:节能罐方案制冷压缩机需要中间补气,而正是这种中间补气的设置,使得压缩机在进料总量一样的情况下,带中间补气形式压缩机可以有效节省电耗,这一效果的实现得益于节能罐制冷方案工艺设计。
节能罐流程仅仅增加节能罐,并没有像传统方案一样再额外设置制冷压缩机人口分液罐,这使得节能罐制冷工艺相比传统工艺在设备配置数量上保持不变,一次性投资变相减少。
这主要是因为随着闪蒸罐容器内件制造工艺和技术的不断网已经实现国产化且捕雾效果与国外知名厂家相同,但是价格优势非常明显。
随着该制造技术的发展,节能罐制冷工艺无需再额外配置压缩机入口分液罐,提高了其技术综合优势。
二、硫酸法烷基化装置节能降耗措施1.循环水节能降耗措施。
装置循环水主要用于9台冷却采样器、26台冷却器及40台机泵,其用点多、使用面广且受外界环境影响大,为循环水节能降耗提供了较大的优化空间。
装置采样器投用循环水主要是给介质降温以满足样品采出温度要求,通过对装置9台采样器切除循环水前后的采样介质温度进行对比分析得知,可切除燃料气采样器、液化气采样器、冷剂采样器、压缩机出口工艺气采样器及凝结水采样器5台采样器的循环水供应。
浅析硫酸法烷基化装置原料加氢预处理工艺
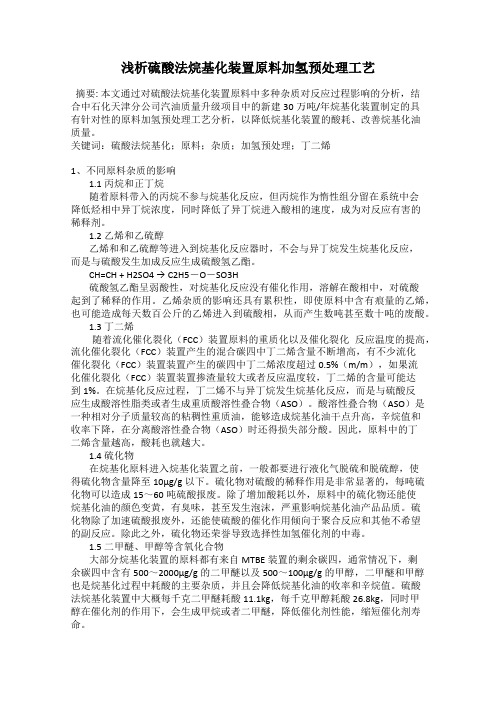
LHSV定义为液体体积流量与催化剂体积之比,二者体积必须用同一种单位表示。在其它条件不变的情况下,空速增大物料在催化剂床层中的停留时间减少,反应效果会变差;反之,反应效果会变好。但空速与H2/丁二烯比、温度相比对工艺性能的影响较小。
1、不同原料杂质的影响
1.1丙烷和正丁烷
随着原料带入的丙烷不参与烷基化反应,但丙烷作为惰性组分留在系统中会降低烃相中异丁烷浓度,同时降低了异丁烷ຫໍສະໝຸດ 入酸相的速度,成为对反应有害的稀释剂。
1.2乙烯和乙硫醇
乙烯和和乙硫醇等进入到烷基化反应器时,不会与异丁烷发生烷基化反应,而是与硫酸发生加成反应生成硫酸氢乙酯。
2、加氢预处理工艺
2.1加氢工艺目的
由于丁二烯是在流化催化裂化(FCC)装置或者焦化装置中主要通过热裂化而产生的一种成分,而来自流化催化裂化(FCC)装置的混合碳四原来中丁二烯浓度偏高,同时,丁二烯作为耗酸的主要杂质,并且影响烷基化油产品收率和质量,因此很有必要将其脱除。加氢的方法可有效地脱除丁二烯,但该加氢工艺过程必须是高选择性的,因为单烯烃是烷基化的有用组分,在加氢过程中不能将其加氢,因此必须采用极具选择性的并且有较高异构化性能的催化剂和非常合适的工艺条件,以使混合碳四经过加氢脱丁二烯工艺处理后达到如下目的:
2)不希望的反应
不希望的反应包括正构烯烃加氢变成正构烷烃、异构烯烃加氢变成异构烷烃的反应,这些副反应的速度都远低于丁二烯加氢反应的速度,只有当丁二烯加氢接近完全时,才开始产生副反应。反应式如下:
CH2=CH-CH2-CH3 + H2 → CH3CH2CH2CH3
CH2=CH(CH3)-CH3 + H2 → CH3-CH2(CH3)-CH3
SINOALKY硫酸烷基化装置工艺优化及节能措施

SINOALKY硫酸烷基化装置工艺优化及节能措施于吉平1,姚建辉1 ,董明会2(1.中国石油化工股份有限公司石家庄炼化分公司,河北省石家庄市050000;2.中国石油化工股份有限公司石油化工科学研究院,北京市100083)摘要:通过对某装置SINOALKY硫酸烷基化工艺运行能耗数据进行分析,发现通过工艺调整,将脱异丁烷塔操作压力由0.65MPa降至0.45MPa,回流量由123t/h降至44t/h后可降低1.0MPa蒸汽消耗5.5t/h;通过合理调整烷基化反应器的操作参数,烷烯比由14∶1降至10∶1可降低1.0MPa蒸汽消耗5t/h,电耗较设计值降低50%;通过将制冷压缩机出口压力由0.74MPa降至0.5MPa,可降低汽轮机3.5MPa蒸汽消耗13t/h。
通过投用精密聚结器,实现切出产物碱洗水洗流程,一方面可降低1.0MPa蒸汽、除盐水、电、新鲜水等公用工程介质的消耗;另一方面可减少含盐污水外排量、降低酸碱消耗,年综合效益约500万元。
采取上述措施后装置总能耗降低约30%。
关键词:SINOALKY 硫酸烷基化 工艺节能 反应系统 分馏系统 精制系统 制冷系统 烷基化油是以C8支链烷烃为主不含烯烃与芳烃的混合物,几乎不含硫元素和氮元素,敏感性和蒸气压低,是一种清洁、理想的高辛烷值汽油调合组分。
2020年国Ⅵ汽油标准与乙醇汽油标准的全面实施,将对现有MTBE装置运行造成较大冲击,这意味着市场对烷基化油的需求将出现井喷式增长[1]。
随着环保法规要求的日益严格,生产满足国家环保法规要求的清洁汽油成为当前中国石油化工行业面临的主要任务之一[2]。
拥有中国石化自主知识产权的新型SINOALKY硫酸烷基化装置于2018年6月在某炼油厂开车成功,装置规模为200kt/a,开工后运行平稳,但运行初期综合能耗高于设计值。
后期根据现场操作总结,不断提出技改措施以降低装置能耗,具体措施包括降低脱异丁烷塔的操作压力,调整核心设备反应器的操作参数,降低制冷压缩机出口压力,切出产物碱洗水洗流程等。
硫酸烷基化工艺腐蚀分析及应对措施

硫酸烷基化工艺腐蚀分析及应对措施陈子香【摘要】硫酸烷基化的催化剂为浓硫酸,其腐蚀性强,对设备管道等影响较大,若设计时考虑不够周到,设备管道等的腐蚀可能会引起物料泄露,严重时会发生事故.这不仅会影响生产,还有可能造成生命和财产损失.因此,对从事这一行业的人员应该重视此问题.对于此工艺中可能出现的腐蚀问题应详细分析,并提出相应的措施,这样可以给同类项目提供一定的参考.【期刊名称】《天津化工》【年(卷),期】2016(030)006【总页数】3页(P15-17)【关键词】硫酸;烷基化;腐蚀;分析;应对措施【作者】陈子香【作者单位】大连派思燃气系统股份有限公司,辽宁大连116600【正文语种】中文【中图分类】TE624.4+8在石油炼制工业中,异丁烷与丁烯的烷基化(碳四烷基化、异丁烷烷基化)是生产清洁高辛烷值汽油调和组分的重要工艺过程之一,国际上的烷基化技术有:固体酸法、硫酸法和氢氟酸法三种。
固体酸法烷基化技术到目前为止都还没有实现工业化[1]。
氢氟酸烷基化装置和硫酸烷基化装置都是技术成熟可靠的工艺。
氢氟酸烷基化装置具有常温下反应、无需制冷系统的优点,但是催化剂氢氟酸具有强腐蚀性及毒性,对环境危害比较大[2]。
硫酸法烷基化装置酸耗量大,需要废酸处理设施,但作为催化剂,硫酸的腐蚀性及对环境的影响要比氢氟酸小。
从环境保护和安全角度考虑,硫酸烷基化技术更具优势。
硫酸法碳四烷基化工艺[3],由以下几个部分组成:原料水洗、进料制冷部分、反应部分、流出物处理部分、脱异丁烷/正丁烷部分、废酸脱气中和部分、酸储存部分。
工艺流程示意图见图1。
本工艺的工艺原理是异丁烷-丁烯进料与装置循环异丁烷和冷剂一起进入反应器,在硫酸的催化作用下,异丁烷和丁烯发生烷基化反应,生成烷基化油。
异丁烷与丁烯烷基化反应很复杂,主反应符合正碳离子链式反应机理,异丁烷与丁烯加成为异辛烷,副反应主要有自聚、断裂、异构化、酯化等反应。
主反应基本如下:由于过程中有浓硫酸做为催化剂,因此防范浓硫酸对设备及管道组成件的腐蚀至关重要。
硫酸法烷基化装置节能降耗措施

硫酸法烷基化装置节能降耗措施
随着能源危机和环境污染问题日益突出,节能降耗的问题已引起广泛关注。
石化行业是能源的大消耗者,其中,硫酸法烷基化技术是产生乙基苯和乙基苯分离时能源耗费最大的部分之一。
因此,在硫酸法烷基化装置中,采取各种节能降耗的措施,减少能源消耗和环境污染是非常必要的。
1. 提高反应温度:可以提高反应速度和减少反应时间,从而减少能源消耗。
但是,提高温度过高会导致反应过程过度发生,甚至会破坏产品质量,因此需要在合适的温度范围内进行操作。
2. 改善催化剂:烷基化反应是由催化剂促进的,因此改善催化剂的性能可以提高催化剂的利用效率和活性。
可以采用新的催化剂,控制催化剂的分布,减少失活等方法提高催化剂的效率。
3. 优化反应器:反应器是烷基化反应最重要的组成部分之一,反应器的优化设计可以减少能源的消耗。
如优化反应器的结构,采用高效的搅拌设备等方法可以提高反应器的混合均匀度,减少能源浪费。
4. 循环利用能源:将废热循环利用,可以减小能源的浪费,降低生产成本,提高工厂的经济效益。
将废气与烟气净化系统结合起来,可以减少污染物的排放。
5. 新技术应用:高温循环热泵技术、热重力耦合技术等新技术的应用也可以提高硫酸法烷基化反应的能源利用效率。
总之,在硫酸法烷基化装置中,采取各种节能降耗的措施是非常必要的。
这不仅有助于减少能源的消耗,还能降低生产成本,提高企业的经济效益。
同时,这也是企业社会责任的一种体现,有助于保护环境,实现可持续发展。
硫酸法烷基化工艺技术探讨
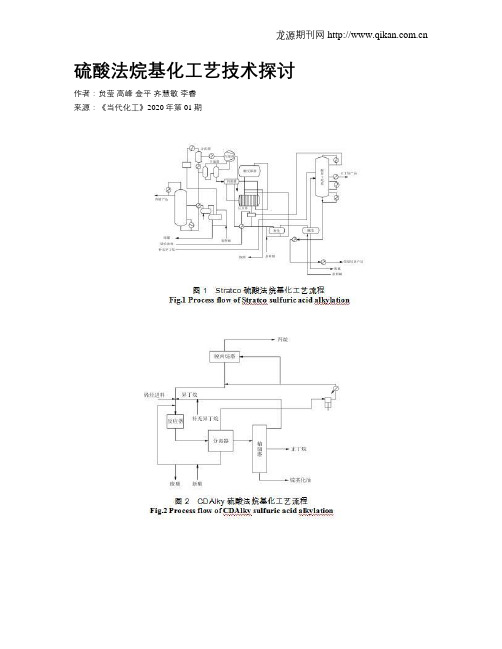
硫酸法烷基化工艺技术探讨作者:贠莹高峰金平齐慧敏李睿来源:《当代化工》2020年第01期Discussion on Sulfuric Acid Alkylation TechnologyYUN Ying,GAO Feng,JIN Ping,QI;Hui-min,LI Rui(Sinopec Dalian Research Institute of Petroleum and Petrochemicals, Liaoning Dalian 116045, China)汽油是以C5~C11的烴类为主的复杂混合物,馏程为35~200;℃。
来自不同生产装置的汽油可分为直馏汽油、催化汽油、重整汽油、烷基化汽油以及醚化汽油等,这些汽油的品质差距很大。
例如:直馏汽油中由于几乎没有不饱和烃,其稳定性相对较高,但其辛烷值较低;而催化裂化汽油辛烷值虽然较高,但烯烃含量却很高。
为了获得合格的产品汽油,一般需要按适当的比例将多种汽油进行调和。
国外汽油调和组分中重整汽油、烷基化汽油以及醚类化合物等高辛烷值组分所占比例较大,汽油中烯烃含量较低。
我国商品汽油组分中催化裂化汽油占7成以上,高烯烃含量会使发动机燃烧室内易形成沉积物、胶质等,影响发动机的正常工作。
国VI 汽油标准的执行进一步严格了汽油中烯烃、芳烃含量以及蒸汽压等指标[1]。
烷基化汽油具有高辛烷值、低蒸气压并且不含烯烃、芳烃等优点,是一种极为难得的优质汽油调和组分。
烷基化反应是将化合物分子中引入烷基的一种反应。
以酸作为催化剂、异丁烷作为烷基化试剂,与C3~C5等烯烃原料反应,生成高辛烷值汽油组分是目前烷基化反应在工业中的最重要应用。
目前烷基化装置中主要应用的催化剂有浓硫酸、氢氟酸和无水氯化铝三种,近几十年来科研人员针对硫酸法和氢氟酸法烷基化工艺进行了大量的研究。
硫酸法烷基化和氢氟酸法烷基化在工艺上各有优缺点,二者都有广泛的应用。
硫酸法烷基化装置由于反应需要在较低温度下发生,需要配套制冷系统。
- 1、下载文档前请自行甄别文档内容的完整性,平台不提供额外的编辑、内容补充、找答案等附加服务。
- 2、"仅部分预览"的文档,不可在线预览部分如存在完整性等问题,可反馈申请退款(可完整预览的文档不适用该条件!)。
- 3、如文档侵犯您的权益,请联系客服反馈,我们会尽快为您处理(人工客服工作时间:9:00-18:30)。
降低硫酸法烷基化酸耗的措施
【摘要】降低酸耗的一些措施。
【关键词】异丁烷与异丁烯;硫酸烷基化;措施
在石油炼制工业中,异丁烷与丁烯的烷基化反应工艺是一个生产清洁的、高辛烷值汽油组分的重要过程。
烷基化汽油具有辛烷值高(RON94~96,MON92~94)和低Reid蒸气压,不含硫、芳烃、烯烃,具有理想的挥发性和清洁的燃烧性,是航空汽油和车用汽油的理想调和组分,采用新配方汽油作为汽油发动机的燃料,将会大大缓和由于汽车尾气排放造成的城市空气污染,烷基化汽油是一种环境友好的石油炼制产品。
烷基化工艺能充分利用炼厂气体资源的优点,而且,随着环保要求越来越高,因此烷基化工艺是炼油厂中应用最广、最受重视的一种气体加工过程。
异丁烷与丁烯的烷基化是将石油炼制工业中的催化裂化反应产
物C4烃组分转化为C8支链异辛烷(烷基化汽油)的催化反应过程。
该反应是在酸性催化剂的存在下,烷烃分子与烯烃分子的有机加成反应。
异丁烷与丁烯在强酸催化剂作用下反应生成的异构C8烷烃(三甲基戊烷)称为烷基化汽油。
硫酸法烷基化装置最主要的一个能耗消耗点就是由于原料中的
一些组份容易造成硫酸消耗,这样就会使生产成本提高,同时造成后
续废酸处理装置负荷增大,也间接的造成了废酸处理装置的生产成本
提高,因此硫酸法烷基化很重要的一点就是控制酸耗。
原料中对硫酸造成污染组份如下:
化合物KG酸KG污染物化合物KG酸KG污染物水9.8甲醚12.5
乙硫醇15.7乙醚10.5
乙基二硫化脂11.7甲基叔丁基醚9.2
硫化氢29.3乙基叔丁基醚15.0
乙烯28.2甲基叔戊基醚12.8
环戊烷 2.31,3-丁二烯8.3
乙炔11.13-甲基-112.6
1-丁烯12.92-甲基-111.3
1-戊炔17.41,3-戊二烯12.4
甲醇26.01,4-戊二烯8.1
乙醇19.4环戊二烯18.5
1-丁醇9.8甲醛16.7
乙醇胺21.0乙醛10.0综合上表造成硫酸烷基化装置酸耗高的原因归结如下:(1)原料
中二烯烃未被饱和,酸耗高;(2)原料中有机氧化物含量高;(3)原料
中二甲醚含量高;(4)原料中硫及硫化物含量高;(5)原料中水含量
高。
针对这四种原因我们应采取如下措施:
(1)安装选择加氢装置,旨在对原料中的二烯烃进行饱和,同时不影响单烯烃的组分,原料中的1.丁烯发生异构化反应、生成顺、反2一丁烯。
其反应过程如下:
CH3二CH—CH=CH2+一C=CH—C一CH3(1)
H2C=CH—CH2一CH3一C—CH=CH—C(2)
(2)利用原料组份溶解度不同的原理,加强原料预处理,在原料进反应器前先对原料进行预处理——安装甲醇水洗回收系统,脱除原料中的有机氧化物。
(3)在原料进反应器之前增设脱轻塔,脱除原料中的轻组分即C1C2组分。
(4)在原料进反应器之前加装原料脱水装置,脱除原料中的水,譬如吸附脱水器、聚结器等。