常用超声波探伤标准要求
超声探伤2级探伤标准
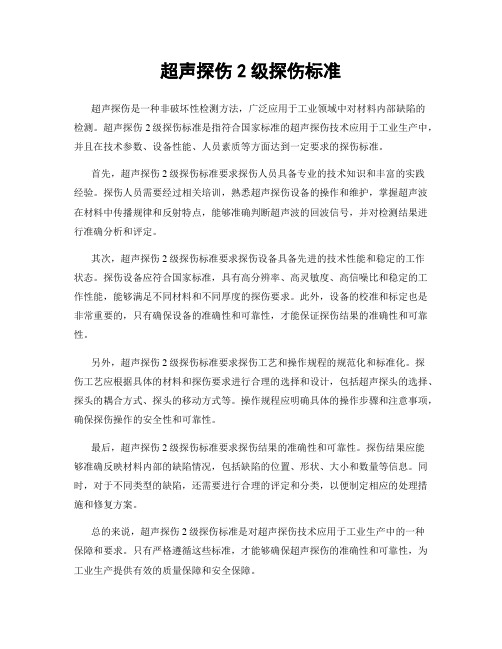
超声探伤2级探伤标准超声探伤是一种非破坏性检测方法,广泛应用于工业领域中对材料内部缺陷的检测。
超声探伤2级探伤标准是指符合国家标准的超声探伤技术应用于工业生产中,并且在技术参数、设备性能、人员素质等方面达到一定要求的探伤标准。
首先,超声探伤2级探伤标准要求探伤人员具备专业的技术知识和丰富的实践经验。
探伤人员需要经过相关培训,熟悉超声探伤设备的操作和维护,掌握超声波在材料中传播规律和反射特点,能够准确判断超声波的回波信号,并对检测结果进行准确分析和评定。
其次,超声探伤2级探伤标准要求探伤设备具备先进的技术性能和稳定的工作状态。
探伤设备应符合国家标准,具有高分辨率、高灵敏度、高信噪比和稳定的工作性能,能够满足不同材料和不同厚度的探伤要求。
此外,设备的校准和标定也是非常重要的,只有确保设备的准确性和可靠性,才能保证探伤结果的准确性和可靠性。
另外,超声探伤2级探伤标准要求探伤工艺和操作规程的规范化和标准化。
探伤工艺应根据具体的材料和探伤要求进行合理的选择和设计,包括超声探头的选择、探头的耦合方式、探头的移动方式等。
操作规程应明确具体的操作步骤和注意事项,确保探伤操作的安全性和可靠性。
最后,超声探伤2级探伤标准要求探伤结果的准确性和可靠性。
探伤结果应能够准确反映材料内部的缺陷情况,包括缺陷的位置、形状、大小和数量等信息。
同时,对于不同类型的缺陷,还需要进行合理的评定和分类,以便制定相应的处理措施和修复方案。
总的来说,超声探伤2级探伤标准是对超声探伤技术应用于工业生产中的一种保障和要求。
只有严格遵循这些标准,才能够确保超声探伤的准确性和可靠性,为工业生产提供有效的质量保障和安全保障。
超声波探伤国家标准
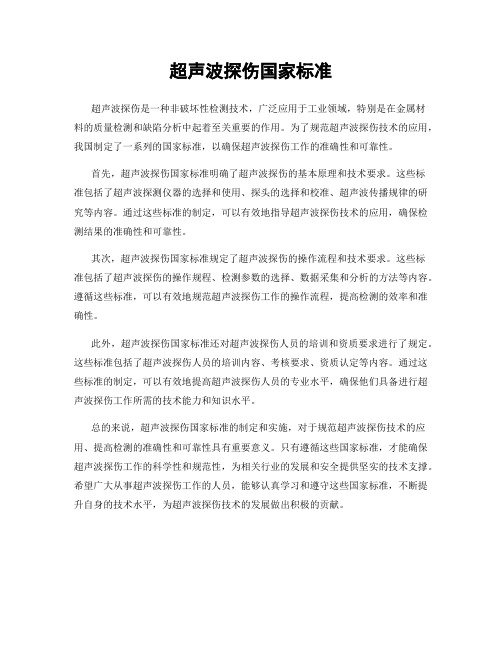
超声波探伤国家标准
超声波探伤是一种非破坏性检测技术,广泛应用于工业领域,特别是在金属材
料的质量检测和缺陷分析中起着至关重要的作用。
为了规范超声波探伤技术的应用,我国制定了一系列的国家标准,以确保超声波探伤工作的准确性和可靠性。
首先,超声波探伤国家标准明确了超声波探伤的基本原理和技术要求。
这些标
准包括了超声波探测仪器的选择和使用、探头的选择和校准、超声波传播规律的研究等内容。
通过这些标准的制定,可以有效地指导超声波探伤技术的应用,确保检测结果的准确性和可靠性。
其次,超声波探伤国家标准规定了超声波探伤的操作流程和技术要求。
这些标
准包括了超声波探伤的操作规程、检测参数的选择、数据采集和分析的方法等内容。
遵循这些标准,可以有效地规范超声波探伤工作的操作流程,提高检测的效率和准确性。
此外,超声波探伤国家标准还对超声波探伤人员的培训和资质要求进行了规定。
这些标准包括了超声波探伤人员的培训内容、考核要求、资质认定等内容。
通过这些标准的制定,可以有效地提高超声波探伤人员的专业水平,确保他们具备进行超声波探伤工作所需的技术能力和知识水平。
总的来说,超声波探伤国家标准的制定和实施,对于规范超声波探伤技术的应用、提高检测的准确性和可靠性具有重要意义。
只有遵循这些国家标准,才能确保超声波探伤工作的科学性和规范性,为相关行业的发展和安全提供坚实的技术支撑。
希望广大从事超声波探伤工作的人员,能够认真学习和遵守这些国家标准,不断提升自身的技术水平,为超声波探伤技术的发展做出积极的贡献。
超声波探伤检测标准
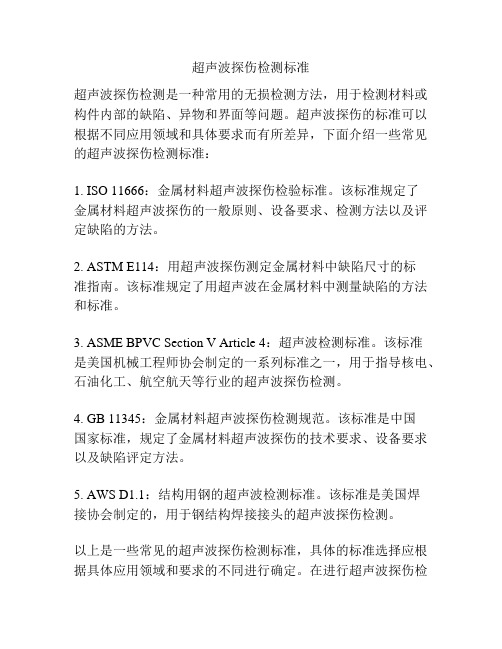
超声波探伤检测标准
超声波探伤检测是一种常用的无损检测方法,用于检测材料或构件内部的缺陷、异物和界面等问题。
超声波探伤的标准可以根据不同应用领域和具体要求而有所差异,下面介绍一些常见的超声波探伤检测标准:
1. ISO 11666:金属材料超声波探伤检验标准。
该标准规定了
金属材料超声波探伤的一般原则、设备要求、检测方法以及评定缺陷的方法。
2. ASTM E114:用超声波探伤测定金属材料中缺陷尺寸的标
准指南。
该标准规定了用超声波在金属材料中测量缺陷的方法和标准。
3. ASME BPVC Section V Article 4:超声波检测标准。
该标准
是美国机械工程师协会制定的一系列标准之一,用于指导核电、石油化工、航空航天等行业的超声波探伤检测。
4. GB 11345:金属材料超声波探伤检测规范。
该标准是中国
国家标准,规定了金属材料超声波探伤的技术要求、设备要求以及缺陷评定方法。
5. AWS D1.1:结构用钢的超声波检测标准。
该标准是美国焊
接协会制定的,用于钢结构焊接接头的超声波探伤检测。
以上是一些常见的超声波探伤检测标准,具体的标准选择应根据具体应用领域和要求的不同进行确定。
在进行超声波探伤检
测时,还需要考虑材料的特性、检测设备的性能以及操作人员的技术水平等因素。
超声波探伤方法和探伤标准
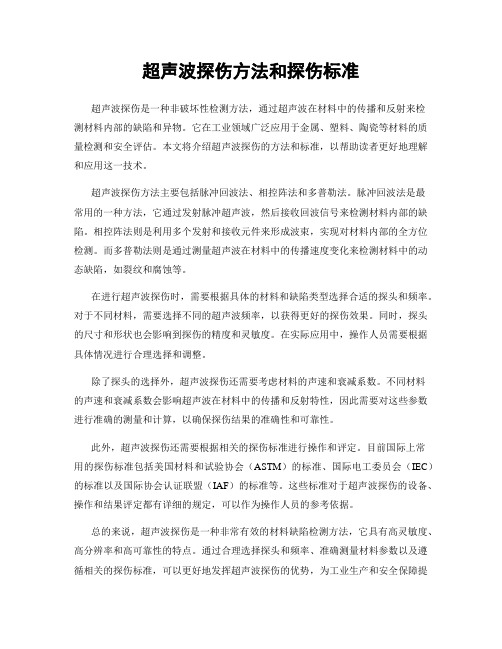
超声波探伤方法和探伤标准超声波探伤是一种非破坏性检测方法,通过超声波在材料中的传播和反射来检测材料内部的缺陷和异物。
它在工业领域广泛应用于金属、塑料、陶瓷等材料的质量检测和安全评估。
本文将介绍超声波探伤的方法和标准,以帮助读者更好地理解和应用这一技术。
超声波探伤方法主要包括脉冲回波法、相控阵法和多普勒法。
脉冲回波法是最常用的一种方法,它通过发射脉冲超声波,然后接收回波信号来检测材料内部的缺陷。
相控阵法则是利用多个发射和接收元件来形成波束,实现对材料内部的全方位检测。
而多普勒法则是通过测量超声波在材料中的传播速度变化来检测材料中的动态缺陷,如裂纹和腐蚀等。
在进行超声波探伤时,需要根据具体的材料和缺陷类型选择合适的探头和频率。
对于不同材料,需要选择不同的超声波频率,以获得更好的探伤效果。
同时,探头的尺寸和形状也会影响到探伤的精度和灵敏度。
在实际应用中,操作人员需要根据具体情况进行合理选择和调整。
除了探头的选择外,超声波探伤还需要考虑材料的声速和衰减系数。
不同材料的声速和衰减系数会影响超声波在材料中的传播和反射特性,因此需要对这些参数进行准确的测量和计算,以确保探伤结果的准确性和可靠性。
此外,超声波探伤还需要根据相关的探伤标准进行操作和评定。
目前国际上常用的探伤标准包括美国材料和试验协会(ASTM)的标准、国际电工委员会(IEC)的标准以及国际协会认证联盟(IAF)的标准等。
这些标准对于超声波探伤的设备、操作和结果评定都有详细的规定,可以作为操作人员的参考依据。
总的来说,超声波探伤是一种非常有效的材料缺陷检测方法,它具有高灵敏度、高分辨率和高可靠性的特点。
通过合理选择探头和频率、准确测量材料参数以及遵循相关的探伤标准,可以更好地发挥超声波探伤的优势,为工业生产和安全保障提供可靠的技术支持。
希望本文所介绍的超声波探伤方法和标准能够对读者有所帮助,促进这一技术的应用和发展。
常用超声波探伤标准要求

≤5
≤3
≤2
锻件和锻材的超声检测
SEP1921-84
允许极限值的大小分级
尺寸级别
单个缺陷(mm)
长条缺陷(mm)
最大面积(mm)
A
14
10
80
B
10
7
60
C
7
5
40
D
5
3
30
E
3
2
30
25MW以下汽轮机转子体和主轴锻件技术条件
JB/T7025-93
●转子体任何部位不得有当量直径>5mm的缺陷。
●其他部位不允许当量直径>3mm的缺陷。
●在锻件中心φ150 mm范围内,不允许有当量直径大于3.0 mm(100 MW以下转子锻件,不允许有当量直径大于3.5 mm)的单个缺陷和大于或等于当量直径2.0 mm的密集缺陷信号。
●外圆槽深加25 mm范围内,不允许有当量直径大于3.0 mm(100 MW以下转子锻件,不允许有当量直径大于3.5 mm)的单个缺陷。其余部位允许2~4 mm分散缺陷存在,但相邻两个缺陷的距离不小于其较大缺陷直径的7倍。
●对于镶套支承辊的辊套,当出现缺陷波时,在离辊套表面l00mm深的表层,要求不允许有大雨当量直径¢2mm的缺陷。
●其余深度范围内,应用AvG法推算出缺陷大小,且不大于当量直径¢3mm。
水轮机、水轮发电机大轴锻件技术条件
JB/T1270-2002
●不允许存在当量直径5mm和5mm以上的密集缺陷。
●允许有单个、分散的、当量直径为6~10mm的缺陷存在,但相邻两缺陷的间距不小于较大缺陷直径的5倍。
常用超声波探伤标准要求
标准名称
标准号
要求
常用超声波探伤标准要求

常用超声波探伤标准要求
•不允许有当量直径》2mm 的密集缺陷。
(密集型缺陷信号是指在边长 50mm 立方 体内,数量不少于5个,当量直径不小于 2mm 的缺陷信号) • > 2mm 当量单个缺陷在合格证书中注明。
•当量直径2mm 以下的单个分散缺陷信号不计,但杂波高度应低于当量直径 2mm 幅度的50%
•单个分散的缺陷定义为: 相邻两缺陷之间的距离大于其中较大缺陷当量直径 10
倍的缺陷。
•单个分散的缺陷应符合下表规定
•轴身部位离中心孔表面 30mm 以内和外圆槽深加
1.6m m 的密集型缺陷。
允许有当量直径 3mm 以下的单个分散缺陷存在。
•不允许有游动缺陷信号和条状缺陷信号。
标准名称 标准号 承压设备无损检测第 3 JB/T4730.3-
•记录当量直径超过0 4mm 单个缺陷 部分:超声检测 2005 •记录密集型缺陷:饼性锻件,
当量直径》0 4mm 其它锻件,当量直径》0 3mm
钢锻件
单个缺陷的质量分级
mm
等级
密集区缺陷占检测总面积的百分比
I
V
钢锻件超声检测方法 0 > 0~5
> 5~10
>10~20
V > 20
体和主轴锻件技术条件 3
•其他部位不允许当量直径 >3mm 的缺陷
锻件和锻材的超声检测 25MW 以下汽轮机转子 25-200MW 汽轮 机转子 JB/T1265-9 体和主轴锻件技术条件
3。
超声波焊缝探伤标准

超声波焊缝探伤标准超声波焊缝探伤是一种常用的无损检测方法,广泛应用于焊接质量的评定和缺陷的检测。
本文将介绍超声波焊缝探伤的标准,包括其定义、应用范围、技术要求等内容,以期为相关领域的从业人员提供参考。
超声波焊缝探伤是指利用超声波技术对焊缝进行缺陷检测的方法。
它可以有效地检测焊缝中的各种缺陷,如气孔、夹杂、裂纹等,对焊接质量的评定具有重要意义。
超声波焊缝探伤广泛应用于航空航天、汽车制造、铁路运输等领域,对提高产品质量、保障安全生产具有重要意义。
超声波焊缝探伤的标准主要包括以下几个方面:首先,超声波探伤设备的选择和校准。
超声波探伤设备是进行焊缝探伤的关键工具,其选择和校准直接影响着探伤结果的准确性。
因此,超声波探伤设备的选择和校准应符合相关标准要求,确保其性能和准确性。
其次,超声波探伤操作规程的制定和执行。
超声波焊缝探伤需要进行严格的操作规程,包括探头的放置、超声波的发射和接收、数据的采集和分析等步骤。
操作规程的制定和执行应符合相关标准要求,确保探伤结果的准确性和可靠性。
再次,焊缝探伤的技术要求和评定标准。
超声波焊缝探伤需要对焊缝中的各种缺陷进行检测和评定,其技术要求和评定标准应符合相关标准要求,确保焊接质量的评定准确性和一致性。
最后,超声波焊缝探伤的报告和记录。
超声波焊缝探伤的结果应当进行报告和记录,报告和记录内容应符合相关标准要求,确保探伤结果的可追溯性和可验证性。
综上所述,超声波焊缝探伤标准是保障焊接质量和产品安全的重要依据,相关领域的从业人员应当严格遵守相关标准要求,确保超声波焊缝探伤工作的准确性和可靠性。
同时,相关标准的制定和更新也是保障超声波焊缝探伤工作质量的重要保障,应当引起相关部门和单位的重视和关注。
超声波探伤标准
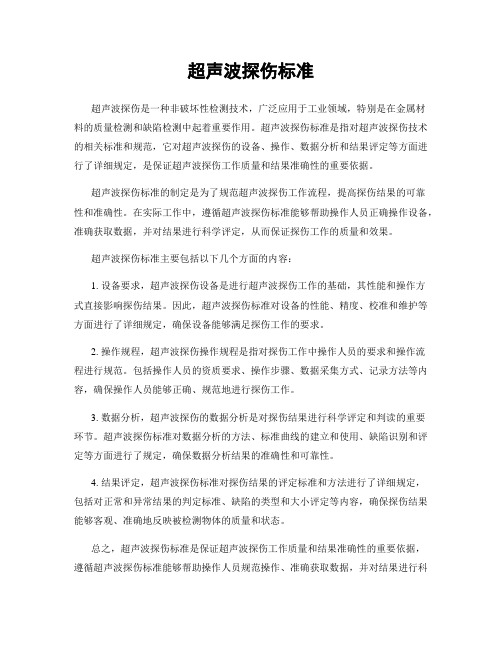
超声波探伤标准超声波探伤是一种非破坏性检测技术,广泛应用于工业领域,特别是在金属材料的质量检测和缺陷检测中起着重要作用。
超声波探伤标准是指对超声波探伤技术的相关标准和规范,它对超声波探伤的设备、操作、数据分析和结果评定等方面进行了详细规定,是保证超声波探伤工作质量和结果准确性的重要依据。
超声波探伤标准的制定是为了规范超声波探伤工作流程,提高探伤结果的可靠性和准确性。
在实际工作中,遵循超声波探伤标准能够帮助操作人员正确操作设备,准确获取数据,并对结果进行科学评定,从而保证探伤工作的质量和效果。
超声波探伤标准主要包括以下几个方面的内容:1. 设备要求,超声波探伤设备是进行超声波探伤工作的基础,其性能和操作方式直接影响探伤结果。
因此,超声波探伤标准对设备的性能、精度、校准和维护等方面进行了详细规定,确保设备能够满足探伤工作的要求。
2. 操作规程,超声波探伤操作规程是指对探伤工作中操作人员的要求和操作流程进行规范。
包括操作人员的资质要求、操作步骤、数据采集方式、记录方法等内容,确保操作人员能够正确、规范地进行探伤工作。
3. 数据分析,超声波探伤的数据分析是对探伤结果进行科学评定和判读的重要环节。
超声波探伤标准对数据分析的方法、标准曲线的建立和使用、缺陷识别和评定等方面进行了规定,确保数据分析结果的准确性和可靠性。
4. 结果评定,超声波探伤标准对探伤结果的评定标准和方法进行了详细规定,包括对正常和异常结果的判定标准、缺陷的类型和大小评定等内容,确保探伤结果能够客观、准确地反映被检测物体的质量和状态。
总之,超声波探伤标准是保证超声波探伤工作质量和结果准确性的重要依据,遵循超声波探伤标准能够帮助操作人员规范操作、准确获取数据,并对结果进行科学评定,从而保证探伤工作的质量和效果。
因此,在超声波探伤工作中,必须严格遵循超声波探伤标准的要求,确保探伤工作的准确性和可靠性。
- 1、下载文档前请自行甄别文档内容的完整性,平台不提供额外的编辑、内容补充、找答案等附加服务。
- 2、"仅部分预览"的文档,不可在线预览部分如存在完整性等问题,可反馈申请退款(可完整预览的文档不适用该条件!)。
- 3、如文档侵犯您的权益,请联系客服反馈,我们会尽快为您处理(人工客服工作时间:9:00-18:30)。
●允许有当量直径1.6~3.55mm的缺陷存在,但相邻两个缺陷的距离不小于其较大缺陷直径的10倍,总数量不得超过30个。
●在应力较大区域,不允许有当量直径大于2mm的缺陷,和≥1.6mm当量直径的密集缺陷信号。
锻钢件无损检测
JB/T5000-15-2007
¢4+(>8dB~12dB)
¢4+(>12dB~16dB)
>¢4+16dB
密集区缺陷的质量分级mm
等级
Ⅰ
Ⅱ
Ⅲ
Ⅳ
Ⅴ
密集区缺陷占检测总面积的百分比
0
>0~5
>5~10
>10~20
>20
钢锻件超声检测方孔直径mm)
1
2
3
4
单个点状不连续
≤12
≤8
≤5
≤3
长条或密集性点状不连续
●单个分散的缺陷应符合下表规定
允许极限值的大小分级
当量范围
部位允许量
总数
轴身
传动轴
非传动轴
¢2~¢3
12
5
5
22
>¢3~¢4
3
1
4
8
总数
15
6
9
30
●在应力较大区域不允许有当量直径大于3mm的单个缺陷缺陷和≥2mm当量直径的密集缺陷信号。
300~600MW汽轮发电机转子锻件技术条件
JB/T7178-93
标准号
要求
模锻锤和大型机械锻压机用模块技术条件
GB11880-89
●允许存在个别的、分散的、不大于当量直径¢2mm的冶金缺陷。
●在100cm2的面积内,当量直径¢2~¢4 mm的冶金缺陷不超过3个,其中¢3~¢4 mm的冶金缺陷只允许有1个。
●允许有2-4个小于当量直径¢2mm的冶金缺陷的密集区,但每区不得超过10cm3,每区之间距不得小于150mm。
不同缺陷类型质量等级划分
缺陷类别
等级
Ⅰ
Ⅱ
Ⅲ
Ⅳ
Ⅴ
起始记录当量值¢,mm
1.6
2
3
5
8
单个缺陷最大允许当量值¢,mm
2
3
5
8
12
缺陷任一方向延伸的最大长度,mm
不允许
30
40
60
80
缺陷处底波降低量的最大允许值 dB
6
8
12
16
20
密集型缺陷最大允许范围 ×10mm3
125
250
500
1000
3000
标准名称
冶金设备制造通用技术条件(锻钢件超声波探伤方法)
YB/T036.10-1992
●密集缺陷:在钢中距离50mm的范围内,有5个以上大于或等于探伤灵敏度基准的缺陷波,称密集缺陷。
●条状缺陷:当缺陷反射波幅大于或等于探伤灵敏度基准波幅,长度大于或等于30mm的连续性缺陷,称条状缺陷。
●不允许有当量直径≥2mm的密集缺陷。(密集型缺陷信号是指在边长50mm立方体内,数量不少于5个,当量直径不小于2mm的缺陷信号)
●≥2mm当量单个缺陷在合格证书中注明。
25-200MW汽轮机转子体和主轴锻件技术条件
JB/T1265-93
●当量直径2mm以下的单个分散缺陷信号不计,但杂波高度应低于当量直径2mm幅度的50%。
●单个分散的缺陷定义为:相邻两缺陷之间的距离大于其中较大缺陷当量直径10倍的缺陷。
●单个分散的缺陷应符合下表规定
当量范围
部位允许量
允许缺陷个数
轴身
传动轴
非传动轴
¢2~¢5
其中:
>¢4~¢5
>¢3~¢4
28
4
8
10
1
3
18
3
5
56
8
16
●轴身部位离中心孔表面30mm以内和外圆槽深加25mm范围内不应当有直径1.6mm的密集型缺陷。允许有当量直径3mm以下的单个分散缺陷存在。
●距中心孔表面75mm以外部位,允许有3个小于当量直径1.6mm的密集缺陷区,但密集区在任何方向的尺寸均应不大于20mm,并且任何两缺陷区间距离应不小于120mm。
●不允许有游动缺陷信号和条状缺陷信号。
50MW以下汽轮发电机转子锻件技术条件
JB/T7026-93
●小于当量直径2mm的缺陷不计。
●不允许有当量直径≥2mm的密集型缺陷密集型缺陷信号,连续性缺陷信号,及游动信号。
●重量超过5吨的模块,除倍尺外,可允许有1个当量直径¢6mm的冶金缺陷存在。
大型锻造合金钢支撑辊
JB/T4120-2006
●对于整锻支承辊,离辊身表面100mm深的表层不允许有大于当量直径¢2mm的缺陷。
●在其他超声波检测区域范围内,当单个缺陷波连续保持F≥1/2,有缺陷部位的底波Bf≤1/2的缺陷面积不大于25cm2。
●允许有当量直径2~5mm分散的单个缺陷存在,但相邻两个缺陷的距离不小于其较大缺陷直径的5倍,总数量不得超过56个。
●在应力较大区域不允许有当量直径大于4mm的缺陷。
50~200MW汽轮发电机转子锻件技术条件
JB/T1267-93
●不允许有当量直径≥2.0mm连续性缺陷信号和游动缺陷信号。
●当量直径小于2mm的缺陷不计,允许2~4mm缺陷存在,但相邻两缺陷的距离不小于其中较大缺陷直径的7倍。
常用超声波探伤标准要求
标准名称
标准号
要求
承压设备无损检测第3部分:超声检测
JB/T4730.3-2005
钢锻件
●记录当量直径超过¢4mm单个缺陷。
●记录密集型缺陷:饼性锻件,当量直径≥¢4mm;其它锻件,当量直径≥¢3mm。
单个缺陷的质量分级mm
等级
Ⅰ
Ⅱ
Ⅲ
Ⅳ
Ⅴ
缺陷当量直径
≤¢4
¢4+(>0dB~8 dB)
●不允许有游动缺陷信号和条状缺陷信号。
标准名称
标准号
要求
300-600MW汽轮机转子锻件技术条件
JB/T7027-93
●当量直径1.6mm以下的单个分散缺陷信号不计,但杂波高度应低于当量直径1.6mm幅度的50%。
●当量直径为1.6mm~3.5mm的所有缺陷应记录其位置,并报告给需方。当量直径为1.6mm~3.5mm的缺陷总数不得超过20个,并不允许当量直径大于3.5mm的任何缺陷。
●对于镶套支承辊的辊套,当出现缺陷波时,在离辊套表面l00mm深的表层,要求不允许有大雨当量直径¢2mm的缺陷。
●其余深度范围内,应用AvG法推算出缺陷大小,且不大于当量直径¢3mm。
水轮机、水轮发电机大轴锻件技术条件
JB/T1270-2002
●不允许存在当量直径5mm和5mm以上的密集缺陷。
●允许有单个、分散的、当量直径为6~10mm的缺陷存在,但相邻两缺陷的间距不小于较大缺陷直径的5倍。
≤8
≤5
≤3
≤2
锻件和锻材的超声检测
SEP1921-84
允许极限值的大小分级
尺寸级别
单个缺陷(mm)
长条缺陷(mm)
最大面积(mm)
A
14
10
80
B
10
7
60
C
7
5
40
D
5
3
30
E
3
2
30
25MW以下汽轮机转子体和主轴锻件技术条件
JB/T7025-93
●转子体任何部位不得有当量直径>5mm的缺陷。
●其他部位不允许当量直径>3mm的缺陷。