精益管理基础知识、5S及目视化
5S及目视化管理
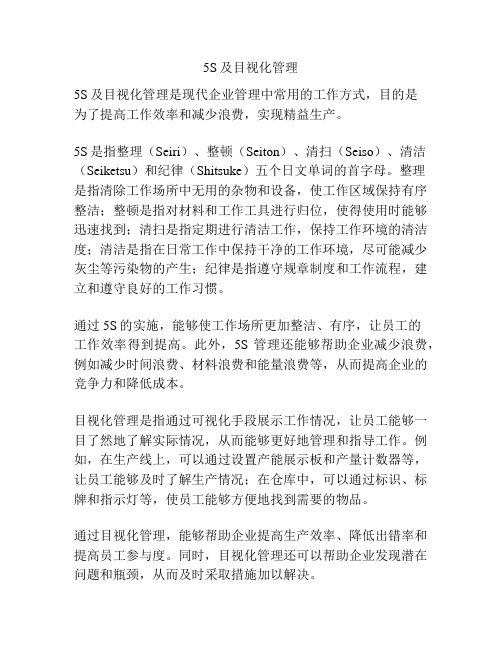
5S及目视化管理5S及目视化管理是现代企业管理中常用的工作方式,目的是为了提高工作效率和减少浪费,实现精益生产。
5S是指整理(Seiri)、整顿(Seiton)、清扫(Seiso)、清洁(Seiketsu)和纪律(Shitsuke)五个日文单词的首字母。
整理是指清除工作场所中无用的杂物和设备,使工作区域保持有序整洁;整顿是指对材料和工作工具进行归位,使得使用时能够迅速找到;清扫是指定期进行清洁工作,保持工作环境的清洁度;清洁是指在日常工作中保持干净的工作环境,尽可能减少灰尘等污染物的产生;纪律是指遵守规章制度和工作流程,建立和遵守良好的工作习惯。
通过5S的实施,能够使工作场所更加整洁、有序,让员工的工作效率得到提高。
此外,5S管理还能够帮助企业减少浪费,例如减少时间浪费、材料浪费和能量浪费等,从而提高企业的竞争力和降低成本。
目视化管理是指通过可视化手段展示工作情况,让员工能够一目了然地了解实际情况,从而能够更好地管理和指导工作。
例如,在生产线上,可以通过设置产能展示板和产量计数器等,让员工能够及时了解生产情况;在仓库中,可以通过标识、标牌和指示灯等,使员工能够方便地找到需要的物品。
通过目视化管理,能够帮助企业提高生产效率、降低出错率和提高员工参与度。
同时,目视化管理还可以帮助企业发现潜在问题和瓶颈,从而及时采取措施加以解决。
综上所述,5S及目视化管理是现代企业管理中常用的工作方式,通过实施5S管理和目视化管理,能够帮助企业实现精益生产,提高工作效率和降低浪费,从而提升企业竞争力。
5S及目视化管理是现代企业管理中常用的工作方式,目的是为了提高工作效率和减少浪费,实现精益生产。
首先,5S管理是一种以整顿工作场所为基础的管理方法,其核心理念是通过整理、整顿、清扫、清洁和纪律的五个环节,优化工作环境,提高工作效率。
其中,整理的目标是通过清除不必要的杂物和设备,使工作区域保持简洁和整洁。
整顿则是将需要使用的材料和工具进行整理归纳,以便员工在工作时能够快速找到所需。
5S与现场目视化管理(1)
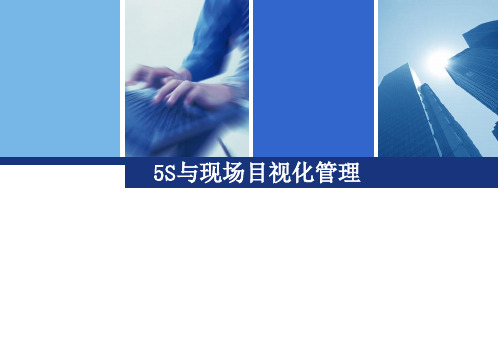
生产现场“查找污染源”活动操作流程
对现场划分区域,分组进行清扫、清洁活动。
组员对长期给现场带来污染的问题进行记录——填 写《现场“污染源”问题清单》。
活动负责人将查找到的污染进行汇总,填写《现场 5S问题改进跟踪评价表》。
清扫
活动负责人组织组员对污染进行源头分析。
讨论解决方案,明确实施负责人和改进期限。 实施改进。
缓冲工作台表面无污垢、杂物、蜘蛛网
流水线段 工位区域内流水线面板表面无污垢、杂物
地面 当班保持工位区域地面清洁干净、无杂物
班组 版本
A线A1、A2班
频次 使用工具
1次/班
抹布
方法 擦试
1次/班 1次/班 1次/周
51次/班
抹布 油枪 抹布
擦试 注油 擦试
1次/班 1次/班 1次/班
抹布 抹布 扫把/垃圾斗
44
修养
修养==对自身的高要求
➢ 人人养成好习惯,依规定行事,做遵守公
司制度,严于自律的员工
有人丢垃圾,无人捡垃圾是三流的工厂; 有人丢垃圾,有人捡垃圾是二流的工厂; 无人丢垃圾,有人捡垃圾是一流的工厂。
45
修养 坚持不懈地教育,才能养成良好的习惯
制度化 行动化 习惯化
一切活动都靠人,假如“人” 缺乏遵守规则的习惯,或者缺 乏自动自发的精神,推行5S易 于流于形式,不易持续
32
定点摄影法
现场一点改善对比图( CIP )
车间: XX车间
姓 名:
徐XX
成员:
生产线:
A线
班组:
活动名称
车间现场问题改善
活动时间: 2006.1.9
XX、XX、XXX A1、A2
Before 改善 前
5S与目视化管理概论
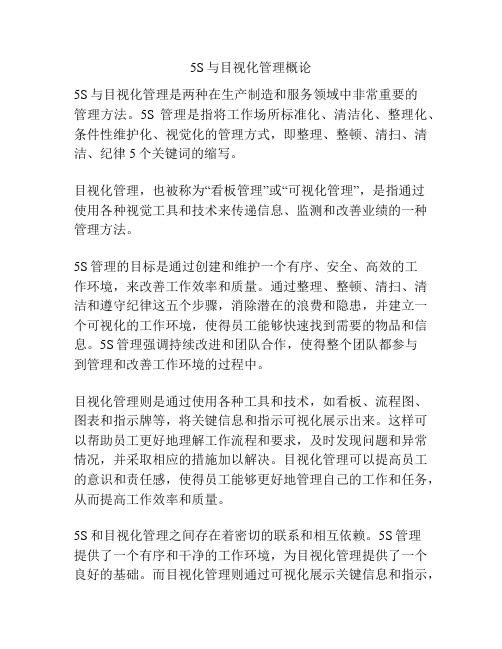
5S与目视化管理概论5S与目视化管理是两种在生产制造和服务领域中非常重要的管理方法。
5S管理是指将工作场所标准化、清洁化、整理化、条件性维护化、视觉化的管理方式,即整理、整顿、清扫、清洁、纪律5个关键词的缩写。
目视化管理,也被称为“看板管理”或“可视化管理”,是指通过使用各种视觉工具和技术来传递信息、监测和改善业绩的一种管理方法。
5S管理的目标是通过创建和维护一个有序、安全、高效的工作环境,来改善工作效率和质量。
通过整理、整顿、清扫、清洁和遵守纪律这五个步骤,消除潜在的浪费和隐患,并建立一个可视化的工作环境,使得员工能够快速找到需要的物品和信息。
5S管理强调持续改进和团队合作,使得整个团队都参与到管理和改善工作环境的过程中。
目视化管理则是通过使用各种工具和技术,如看板、流程图、图表和指示牌等,将关键信息和指示可视化展示出来。
这样可以帮助员工更好地理解工作流程和要求,及时发现问题和异常情况,并采取相应的措施加以解决。
目视化管理可以提高员工的意识和责任感,使得员工能够更好地管理自己的工作和任务,从而提高工作效率和质量。
5S和目视化管理之间存在着密切的联系和相互依赖。
5S管理提供了一个有序和干净的工作环境,为目视化管理提供了一个良好的基础。
而目视化管理则通过可视化展示关键信息和指示,帮助实现5S管理的目标和要求。
两者相辅相成,共同促进了组织的运作和绩效改善。
综上所述,5S和目视化管理是两种在生产制造和服务领域中非常重要的管理方法。
它们通过整理、整顿、清扫、清洁、纪律以及可视化展示关键信息和指示,帮助组织实现工作环境的有序、安全、高效,并提高工作效率和质量。
这两种管理方法相互依赖、相互促进,对于组织的运作和绩效改善具有重要的作用。
5S与目视化管理是现代企业管理中非常重要的两种方法,它们都以提高工作效率、降低成本和提升质量为目标,是实现精益生产和持续改进的重要工具。
首先,5S管理强调工作场所的整理、整顿、清扫、清洁和纪律。
精益管理基础知识

精益管理基础知识1、5S指的是什么?整理、整顿、清扫、清洁、素养(有先后顺序)2、5S对应的内涵整理:区分要与不要,处理不要物品整顿:定区域、定位置、定数量,做到物品摆放整齐、存取方便清扫:及时清理所属区域积料、杂物,所属设备经常清洁,及时除掉积尘、油污清洁:维持整理、整顿、清扫工作,使其标准化素养:养成良好的习惯,形成制度3、整理的三要素是:Who(谁整理)、IIow(怎么整理)、Where (整理范围)4、S DA (大课题)SGA (中等课题)kaizen (小问题)5、K AIZEN,是日语“改善”的音译,特指小的、持续的改善活动。
个人层面即可开展6、K AIZEN分为8类分别是:(1)创新类(2)技改类(3)流程类(4)安全类(5)修旧利废类(6)减少浪费类(7) 5S管理类(8)微小缺陷类7、精益管理的核心是改善。
8、精益思想五原则包括:(1)价值(2)价值流(3)流动(4)需求拉动(5)完美9、激励全员提案的做法包括:(1)反馈速度、采纳率(2)当面的鼓励与感谢(3)改善墙展示(4)物质激励、金钱奖励(5)管理层去现场交流(6)工作调整或升职机会10、KAIZEN实施的要点有:(1)全员参与(2)改善内容不限,注重身边微小的事物(3)改善尽量为自己工作范围内,可由自己完成,或由自己的部门内同事帮助即可完成(4)每天都改善(持续改善)11、中层管理者辅导Kaizen的方法:(1)与提案人当面交谈(2)如有必要,实施“三现主义”(3)讨论是否有更好对策(4)修改对策(5)员工实施对策,拍下改善后照片(6)追踪员工提交共享12、精益改善项目实施中的14个常见问题:0选题范围太大,想一次性解决所有问题0核心组员过多,沟通协调成本高0项目组长大包大揽,项目变成为一个人的项目0缺少过程管理,无内部辅导0对组员的激励不够0对现状把握重视度不足,未遵循“五现主义”0数据可靠性未调查,不重视测量系统的研究0用“原因分析"取代“现状把握”0目标设定不合理,且无分目标和阶段性目标0原因分析不深入,未找到真因,匆忙下对策0未掌握分析工具0对策不易执行,浮于表面0对策未落实,效果无验证0措施未进行固化13、精益改善八步法:(1)主题选定(2)现状把握(3)目标设定(4)要因分析(5)对策拟定(6)对策实施(7)效果确认(8)标准化14、7大浪费包括:(1)等待的浪费(2)搬运的浪费(3)不良品的浪费(4)动作的浪费(5)加工的浪费(6)库存的浪费(7)制造过多(早)的浪费15、SDA、SGA、KAIZEN S者之间的关系可理解为:(1)大的课题可以通过SDA活动解决,中等课题可以通过SGA活动解决,而由个人实施的小问题就需要通过不断的Kaizen活动来解决。
精益知识题库

精益管理知识题库一、5S 知识(1~40题)1、问:5S的内容是什么?答:整理、整顿、清扫、标准化、素养。
2、问:整理的定义是什么?答:整理的定义是在工作现场,区分要与不要的东西,留下有用的东西,把不要的东西清理掉。
3、问:整理的作用有哪些?答:(1)、节省作业空间;(2)、简化管理对象;(3)、提高工作效率;(4)、减少作业差错;(5)、避免资金浪费。
4、问:整理时现场检查常用的方法有哪些?答:(1)、老鼠蟑螂检查法;(2)、下班后检查法;(3)、红牌作战法;(4)、定点摄影法。
5、问:整顿的定义是什么?答:对整理之后留在现场的必要的物品分门别类放置,排列整齐,明确数量,有效标识。
6、问:整顿的“三定原则”及“三要素”分别是什么?答:三定原则:定位、定容、定量;三要素:场所、标识、方法。
7、问:整顿的“三易原则”是什么?答:易取、易放、易管理(即缺什么东西一目了然)。
8、问:标识的方法指的是什么?答:(1)、在放置场所标明所摆放物品;(2)、在摆放物体上进行标识;(3)、标识卡上的说明应和物品一致。
9、问:清扫的定义是什么?答:是去除所有的脏污并且不断的寻找方法保持干净。
10、问:实施清扫时的三扫原则是什么?答:三扫是扫黑、扫漏、扫怪。
扫黑:垃圾、灰尘、粉尘、纸屑、蜘蛛网等;扫漏:漏水、漏油、漏气等;扫怪:异常声音、温度、振动等。
11、问:清扫的三个作用是什么?答:(1)、环境整洁、心情愉快;(2)、产品干净、没有划痕;(3)、没有赃污、设备完好。
12、问:清扫的推行要领是什么?答:(1)、管理干部以身作则,人人参与;(2)、建立清扫责任区,责任到人,不留死角;(3)、清扫、点检、保养有效相结合;(4)、杜绝污染源,建立清扫制度,形成规范。
13、问:清扫用具的放置原则是什么?答:(1)、打扫类用具应单只悬挂,手柄向上,不得杂乱堆放;(2)、拖把应拧干水分后悬挂,以免弄湿地面;(3)、抹布的大小要适宜,用起来顺手,抹布应逐块挂放;(4)、扫帚或抹布等应进行数量管理,不能因堆放抹布而破坏现场的整洁度。
精益管理安全生产安全生产

精益管理安全生产1、精益生产管理包含哪些方法精益生产管理包含的方法有以下11种:1、5S与目视控制“5S”是整理(Seiri) 、整顿(Seiton) 、清扫(Seiso) 、清洁(Seikeetsu)和素养(Shitsuke)这5个词的缩写“5S”,起源于日本。
5S是创建和保持组织化,整洁和高效工作场地的过程和方法,可以教育、启发和养成良好“人性”习惯,目视管理可以在瞬间识别正常和异常状态,又能快速、正确的传递讯息。
2、准时化生产(JIT)准时生产方式是起源于日本丰田汽车公司,其基本思想是“只在需要的时候,按需要的量生产所需的产品” 。
这种生产方式的核心是追求一种无库存的生产系统,或使库存达到最小的生产系统。
3、看板管理(Kanban)Kanban是个日语名词,表示一种挂在或贴在容器上或一批零件上的标签或卡片,或流水线上各种颜色的信号灯、电视图象等。
看板是可以作为交流厂内生产管理信息的手段。
看板卡片包含相当多的信息并且可以反复使用。
常用的看板有两种:生产看板和运送看板。
4、零库存管理工厂的库存管理是供应链的一环,也是最基本的一环。
就制造业而言,加强库存管理,可缩短并逐步消除原材料、半成品、成品的滞留时间,减少无效作业和等待时间,防止缺货,提高客户对“ 质量、成本、交期” 三大要素的满意度。
5、全面生产维护(TPM)TPM起源于日本,是以全员参与的方式,创建设计优良的设备系统,提高现有设备的利用率,实现安全性和高质量,防止故障发生,从而使企业达到降低成本和全面生产效率的提高。
6、运用价值流图来识别浪费生产过程中到处充斥着惊人的浪费现象,价值流图(Value Stream Mapping)是实施精益系统、消除过程浪费的基础与关键点。
7、生产线平衡设计由于流水线布局不合理导致生产工人无谓地移动,从而降低生产效率;由于动作安排不合理、工艺路线不合理,导致工人三番五次地拿起或放下工件。
8、拉系统与补充拉系统所谓拉动生产是以看板管理为手段,采用“取料制”即后道工序根据“市场”需要进行生产,对本工序在制品短缺的量从前道工序取相同的在制品量,从而形成全过程的拉动控制系统,绝不多生产一件产品。
5s及目视化管理

亦即在工作现场,如果把整理整顿做好,
It means if doing well on Sort and Stabilize ,
则推展其他管理活动,就可以顺水推舟, 易如反掌了
Other management activities will be promoted and easy act on .
5S的定义
(The definition of 5S)
• 平心而论,日本企业在推动整理整顿活动 时,比较具体而实在。他们很干脆地将整 理整顿剖成五个名词,同时给它们下了非 常明确的定义,让员工不但一听就懂,而 且能做;这五个字词都是以『s』为开头 的日文罗马拼音,故简称『5s』。
整理(Seiri;Sort)
清洁(Seiketsu;Standardize)
维护清扫过后的厂区及环境整洁美观,使工 作的人觉得干净、卫生而产生无比的干劲。 现场时时刻刻保持美观状态 Keep pretty status onsite every moment 维持前3S之效果 keep 3s effect made before
(How is going…?If not good on Sort and Stabilize)
1.物品未有效整 理定位 2.通道受阻 1.物品用时找不到
作 业 现 场 不 良 现 象
3.物品直接散落 地面 4.工模工具任意 弃置 5.良品、不良品 混淆 6.管、线路跨越 通道 7.员工不守规则 8.私人物品乱放
以设备异常的未然防 止活动来减低损失。
TM TQ
以品质保证活动来生产 高品质的制品。 排除人、物的动作(流 动)之浪费,追求有效 率的生产性
TP TQM 、4S
工厂的第一印象
(The first image on factory)
第 4章 实施精益管理的基础——5S活动
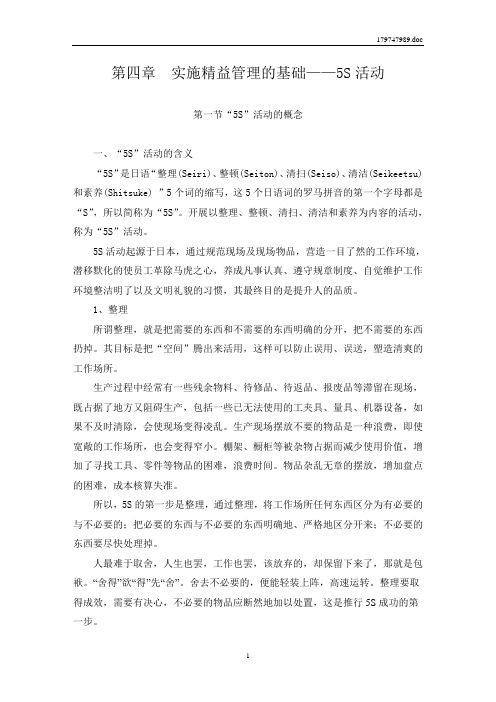
第四章实施精益管理的基础——5S活动第一节“5S”活动的概念一、“5S”活动的含义“5S”是日语“整理(Seiri)、整顿(Seiton)、清扫(Seiso)、清洁(Seikeetsu)和素养(Shitsuke) ”5个词的缩写,这5个日语词的罗马拼音的第一个字母都是“S”,所以简称为“5S”。
开展以整理、整顿、清扫、清洁和素养为内容的活动,称为“5S”活动。
5S活动起源于日本,通过规范现场及现场物品,营造一目了然的工作环境,潜移默化的使员工革除马虎之心,养成凡事认真、遵守规章制度、自觉维护工作环境整洁明了以及文明礼貌的习惯,其最终目的是提升人的品质。
1、整理所谓整理,就是把需要的东西和不需要的东西明确的分开,把不需要的东西扔掉。
其目标是把“空间”腾出来活用,这样可以防止误用、误送,塑造清爽的工作场所。
生产过程中经常有一些残余物料、待修品、待返品、报废品等滞留在现场,既占据了地方又阻碍生产,包括一些已无法使用的工夹具、量具、机器设备,如果不及时清除,会使现场变得凌乱。
生产现场摆放不要的物品是一种浪费,即使宽敞的工作场所,也会变得窄小。
棚架、橱柜等被杂物占据而减少使用价值,增加了寻找工具、零件等物品的困难,浪费时间。
物品杂乱无章的摆放,增加盘点的困难,成本核算失准。
所以,5S的第一步是整理,通过整理,将工作场所任何东西区分为有必要的与不必要的;把必要的东西与不必要的东西明确地、严格地区分开来;不必要的东西要尽快处理掉。
人最难于取舍,人生也罢,工作也罢,该放弃的,却保留下来了,那就是包袱。
“舍得”欲“得”先“舍”。
舍去不必要的,便能轻装上阵,高速运转。
整理要取得成效,需要有决心,不必要的物品应断然地加以处置,这是推行5S成功的第一步。
2、整顿所谓整顿就是把需要的物品按需要时便于使用的原则整齐的放置,明确标示,以便无论是谁都清楚明白。
通过整理,工作现场留下的都是必要的物品。
但如果这些物品杂乱无章、毫无规则地堆放在工作现场,将会导致一系列不良后果。
- 1、下载文档前请自行甄别文档内容的完整性,平台不提供额外的编辑、内容补充、找答案等附加服务。
- 2、"仅部分预览"的文档,不可在线预览部分如存在完整性等问题,可反馈申请退款(可完整预览的文档不适用该条件!)。
- 3、如文档侵犯您的权益,请联系客服反馈,我们会尽快为您处理(人工客服工作时间:9:00-18:30)。
如何激励员工持续做好Kaizen:活性化管理
改善积分榜;助人改善榜 优秀改善团队奖;组间差异分析 最佳改善的组织推动奖 推广奖 专题改善活动(如:安全专题活动;消除七大浪费活动 等) Kaizen有奖征文、漫画、微视频 微信发布 邀请他人给自己提改善活动 Kaizen家庭展(员工家里的改善活动展示)
浪费,从而提高作业效率。
弯腰作业的浪费
转身作业的浪费
38
整顿
寻找物料百态图:
39
整顿—实例
过方便作业
40
整顿—实例
改善前
改善后
41
整顿 整顿的三定原则
平南公司维修班工具柜
平南公司润滑油库
定点
三
定
放在哪里合适
原
则 定容
用什么容器、颜色
定量
规定合适的数量
• 小创新、小发明 • 找出安全隐患 • 找5S改善点 • 找目视化改善点
多问几个为什么
• 找出问题背后的原因,根据原 因下对策,而不仅仅是消除问 题现象。例如,绿化植物被车 辆碾压破坏,改善对策不仅应 着眼于如何恢复绿化,还要分 析原因,找到预防的办法。
20
Kaizen 精益管理三大损失
各种波动: 为了应付生产的波峰, 往往需要配备超出平均 需求的场地、人员或其 它资源,从而形成一种 不定时的浪费。
善:就是更好。
Kai
Zen
change
better
丰田要求员工对生产和管理现场进行一点一滴的持续改善。作业 时间缩短一秒,步行数量减少一步,微小缺陷和隐患消除一个, 这些小的改进一个个积累起来后,就能取得显著成效。
19
Kaizen Kaizen在哪里?
开拓改善视野
• 找出存在的三类精益损失,即 不均衡、超负荷、七大浪费
没有控制温度标准
疑惑
焦点
24
5Why提问法
25
5Why提问法 通过反问来确认和验证原因
发动机爆缸
(为什么?) 润滑油不足
润滑油不足会引起发动机爆缸 (反问也成立)
吵架吵了架了
(为什么?) 关系不好
只要关系不好就会吵架吗?(反问不成立)
26
5Why提问法—水泥案例
27
分小组研讨(15分钟): 如何激励员工持续做好Kaizen?
丰田7天后恢复生产 本田汽车30天后恢复生产 日产汽车公司50天恢复生产
7
精益的起源
詹姆斯·P·沃麦克 (James P. Womack )
前MIT资深教授,为企业提 供精益咨询,也向小型制造 厂投资。他创办了精益企业 研究所(LEI)并担任所长,这 家研究所是一个非营利教育 和研究机构,致力于精益思 想的传播和应用。
5
持续推进5S现场检查工作和红牌作 战
61
精益管理基础知识 Kaizen 5S 目视化管理
目视化管理 目视化管理是利用形象直观而又色彩适宜的各种视觉感知信息来组 织现场生产活动,达到提高劳动生产率的一种管理手段,也是一种 利用视觉来进行管理的方法。 特点 以视觉信号显示为基本手段,大家都能够看得见。 要以公开化,透明化的基本原则,尽可能的将管理者的要求和意 图让大家看得见,借以推动自主管理。 现场的作业人员可以通过目视的方式将自己的建议、成果、感想 展示出来,与领导、同事进行相互交流。
Kaizen原理
事故
磨损、松动、 泄露、污垢、 灰尘、腐蚀、 变形、原物料 的粘连、表面 缺陷、破裂、 过热、颤动、 噪音及其他异 常现象
海因里希法则 1:29:300:1000
16
挑战者航天飞机失事视频
17
18
Kaizen
Kaizen是日语“改善”的音译,特指小的、持续的改善活动。
改:就是改动,改变。
42
整顿—实例
定置案例——影子法、形迹法
43
整顿—实例
定置案例——站立法、插立法、卡槽法
44
整顿 定置案例
贵港公司* 部门值班室
45
整顿 定置案例(平南公司)
46
整顿 定置案例:贵港公司
制造部机械工段库房
制造部机械工段库房
电气部余热发电工段库房
47
整顿 定置案例:江门公司
48
整顿 定置案例:江门公司
整理
整顿
清扫
清洁
素养
58
素养的推行要点
1. 制定服装、标识牌、工作帽等识别标准;
2. 制定公司有关规则/规定并贯彻实施;
3. 制定礼仪守则;
4. 教育训练;
5. 推动各种激励活动;
6. 遵守规章制度; 7. 推行打招呼,礼貌活动。
深圳理光十年如一日,在早 会上领读:
“早上好、谢谢、对不起、 辛苦啦、请”
丰田纺织的创始人:丰 田佐吉
5
精益的起源
世界四大汽车公司净利润走势图(亿美元)
300
200
100
0 2001 2002 2003 2004 2005 2006 2007 2008 2009 2010 2011 2012 2013 2014
-100
丰田 大众 通用 福特
-200
-300
-400
6
精益的起源
华润水泥
精益黄带培训
精益基础、5S及目视化管理
精益管理基础知识 Kaizen 5S 目视化管理
一、精益管理基础知识 1、精益的起源 2、什么是精益
3
精益生产方式 丰田生产方式 大野生产方式 零库存生产方式 JIT生产方式 准时化生产 后拉动的生产方式 消除七大浪费的生产方式 持续改善的生产方式
二、Kaizen 1、Kaizen 2、5Why提问法
14
Kaizen
SDA SGA KAIZEN
SDA项目可派生出数个SGA项 目;SGA活动针对性强,对 SDA项目有支持作用。
引导基层微小改善逐步趋向 “不均衡、超负荷和七大浪 费”,一些提案的解决思路, 可以升级为SGA项目。
15
Kaizen
8
什么是精益
丰田精益生产系统
最优的质量 – 最低的成本 – 最短的交货期
通过消除浪费缩短生产流程
准时化生产制 JIT
“在正确的时间 以正确的量 生产正确的零件
•连续流 •拉动系统 •看板
平准化生产
自働化
“内在质量”
•自动停机 •固定工位拉线停止 •可视化控制
遇到不正常的情况 就停止生产
标准化工作 预防性维护; 5S
• 改善的大房间
66
目视化管理案例:
67
目视化管理案例: 看板(平南公司)
68
目视化管理案例:
69
目视化管理案例:
在机床上挂上行车使用信号的标志牌,让车间辅助工提前将行车开至机床边, 节省了等待时间
70
目视化管理案例: 用好颜色
任何人都能做出正确 的判断!
71
目视化管理案例: 水管、气管标记
59
5S大作战
• 摄影作战 • 红牌作战 • 定位作战 • 油漆作战
60
红牌作战
第一周,5S检查小组对各区域进行 1 现场检查,发现问题点,发放红牌
公布红牌作战结果,并要求各部门在
红 牌
2 一周内对红牌问题点进行整改
作
战
流 程
3
第二周,5S检查小组验收红牌问题 点整改情况
公布红牌整改情况,公示5S检查评 4 比结果,并在管理例会上颁奖
35
整理 整理的步骤
现场检查
每天循环整理
整理永无止境
区分物品
清理非必需品
处理非必需品
全面检查—桌 面、文件柜、 工具柜、柜子 顶上,电脑等 等。
区分必需品与非必需品,应 按使用频率进行区分为经常 用的、暂时不用的、长期不 用的;并且要准确把握适 量,引入最低限量。
从不需要的 岗位、现场 中清理出 去。
49
整顿 定置案例:江门公司
50
整顿计划表
列出所有整顿事项清单,完成一轮定位标识作战。改善前后拍 照比对上墙。
51
清扫
52
清扫
灰尘 松动 断裂
附着氧化 脱落 故障
锈蚀 部件变形
53
清扫
清扫与故障预防 微缺陷的消除
零故障,零事故
大缺陷 累积或成长
灾害、事故 事故隐患
1大 29中 300小
微缺陷
• 提问环节,用一句话描述精益。
4
精益的起源
起源于20世纪50年代丰田汽车公司,又被称为丰田生产方式。是指通过消除企业所有环节 上的不增值活动,使得内外部客户价值最大化的一种生产方式。
没有汽车制造经验的外行科长: 大野耐一
坚定的支持者: 丰田英二
1951年,丰田英二到福特鲁奇工厂参观, 他对这个庞大企业的每一个细微之处都作 了审慎的考察,在他写给丰田总部的报告 中说:“那里的生产体制还有些改进的可 能。”
改善前:摆放零乱
改善后:摆放整齐
5Why提问法
注意!!
23
5Why提问法
方法1
方法2
为什么? 零件不符合规格
为什么? 没有正确的工具
为什么? 我们没有第二个工具 为什么? 根据管理层,投资回报
率太低,无法另购一个
为什么? 为什么? 为什么? 为什么?
由于全球竞争,产品的市场 价格过低
零件不符合规格 使用了错误的工具 标准工具已烧坏 油温过高
72
目视化管理案例: 警示、标识、说明、对比等
73
目视化管理案例: 图例
74
目视化管理案例: 图例
化学试剂标签:名称、注 意事项
固定文件夹摆放顺序
75
目视化管理案例: