车刀前角的选择
车刀种类和角度选择原则详解
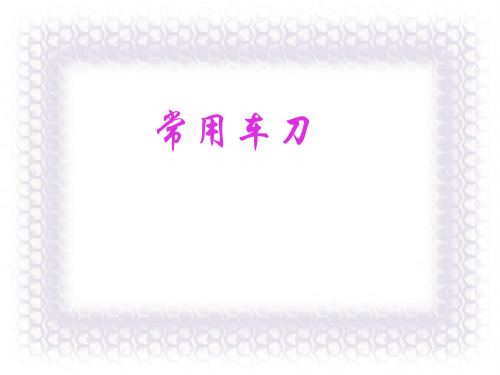
车刀不对准工件中心对角度的影响
五、车刀刃磨
无论硬质合金车刀(焊接)或高速钢 车刀,在使用之前都要根据切削条 件所选择的合理切削角度进行刃磨 ,一把用钝了的车刀,为恢复原有 的几何形状和角度,也必须重新刃 磨。
重 要 性
三分手艺、七分刀 徒弟的手、师傅的刀
1.磨刀步骤(图a~d)
⑴磨前刀面 把前角和刃倾角磨正确。 ⑵磨主后刀面 把主偏角和主后角磨正确。 ⑶磨副后刀面 把副偏角和副后角磨正确。 ⑷磨刀尖圆弧 圆弧半径约0.5~2mm左右。 ⑸研磨刀刃 车刀在砂轮上磨好以后,再用油石加些机油研磨车 刀的前面及后面,使刀刃锐利和光洁。这样可延长车刀的使用寿命。 车刀用钝程度不大时,也可用油石在刀架上修磨。硬质合金车刀可 用碳化硅油石修磨。
前角γo
——在主切削刃选定点的正交平面po内, 前刀面与基面之间的夹角
。
后角αo
——在正交平面po内,主后刀面与切削 平面之间的夹角。
主偏角κr
——主切削刃在基面上的投影与进给方 向的夹角。
刃倾角λs ——在切削平面ps内,主切削刃与 基面pr的夹角。
其他角度:
副前角γoˊ、 副后角αoˊ、 副偏角κrˊ、 刃倾角λsˊ
3.主偏角、副偏角的选择 (1)主偏角的选择 A、主偏角κr的增大或减小对切削加工有利的一 面 在背吃刀量ap与进给量f 不变时,主偏角κr减小 将使切削厚度hD减小,切削宽度bD增加,参加 切削的切削刃长度也相应增加,切削刃单位长度 上的受力减小,散热条件也得到改善。 主偏角κr减小时,刀尖角增大,刀尖强度提高, 刀尖散热体积增大。 所以,主偏角κr减小,能提高刀具耐用度。
(4)良好的工艺性和经济性
刀具前角后角的选用原则

刀具前角后角的选用原则1.前角的主要功用(1)影响切削区域的变形程度:若增大刀具前角,可减小前刀面挤压切削层时的塑性变形,减小切屑流经前刀面的摩擦阻力,从而减小了切削力、切削热和功率.第四章图4—14所示,为前角γ.对三个切削分力的影响,当前角增大时,Fc、Fp、Ff 力均显著减小,这是增大前角的有利方面.(2)影响切削刃与刀头的强度、受力性质和散热条件:增大刀具前角,会使切削刃与刀头的强度降低,刀头的导热面积和容热体积减小;过份加大前角,有可能导致切削刃处出现弯曲应力,造成崩刃.这些都是增大前角的不利方面.(3)影响切屑形态和断屑效果:若减小前角,可以增大切屑的变形,使之易于脆化断裂.(4)影响已加工表面质量:前角与表面质量的关系,在第九章已有论述.值得法意的是,前角大小同切削过程中的振动现象有关,减小前角或者采用负前角时,振幅急剧增大,如图10—5所示.2.合理前角的概念从上述前角的作用可知,增大或减小前角,各有其有利和不利两方面的影响.例如,从切削热的产生和散热来说,增大前角,可以减小切削热的产生,切削温度不致太高;但如果前角太大,则因刀头导热面积和容热体积减小,切削温度反而升高.在切削很硬的材料时,应用较小的前角,甚至选用适宜的负前角,以加强切削刃,并改善刀头容热和散热条件;但若是前角太小,或取很大的负前角,则因切削变形严重,产生热量多,来不及散逸,结果还会使切削温度上升.可见,在一定的条件下,前角有一个合理的数值.可见前角太大、太小都会使刀具使用寿命显著降低.对于不同的刀具材料,各有其对应着刀具最大使用寿命的前角,称为合理前角γopt.显然,由于硬质合金的抗弯强度较低,抗冲击韧性差,其γopt也就小于高速钢刀具的γopt.同理,工件材料不同时,刀具的合理前角也不同(图10—7).从实验曲线可以看出,加工塑性材料比加工脆性材料的合理前角值大,加工低强度钢比加工高强度钢的合理前角值大.这是因为切削塑性大的金属材料产生的切屑,在切削过程中,它同前刀面接触长度(刀—屑接触长度)较大,由于塑性变形的缘故,刀—屑之间的压力和摩擦力很大,为了减少切削变形和切屑流动阻力,应取较大的前角.加工材料的强度硬度较高时,由于单位切削力大,切削温度容易升高,为了提高切削刃强度,增加刀头导热面积和容热体积,需适当减小前角.切削脆性材料时,塑性变形不大,切出的崩碎切屑,与前刀面的接触长度很小,压力集中在切削刃附近,为了保护切削刃,宜取较小的前角.以上所讲的都是保证刀具最大使用寿命的前角.在某些情况下,这样选定的γopt未必是最适宜的,例如在出现振动的情况下,为了减小振动的振幅或消除振动,除采取其他措施外,有时需增大前角;在精加工条件下,往往需要考虑加工精度和已加工表面的粗糙度要求,选择某一适宜的前角;有些刀具需考虑其重磨次数最多而选择某一前角,等等.3.合理前角的选择原则(1)工件材料的强度、硬度低,可以取较大的甚至很大的前角;工件材料强度、硬度高,应取较小的前角;加工特别硬的工件(如淬硬钢)时,前角很小甚至取负值.(2)加工塑性材料时,尤其是冷加工硬化严重的材料,应取较大的前角;加工脆性材料时,可取较小的前角.(3)粗加工,特别是断续切削,承受冲击性载荷,或对有硬皮的铸锻件粗切时,为保证刀具有足够的强度,应适当减小前角;但在采取某些强化切削刃及刀尖的措施之后,也可增大前角至合理的数值.(4)成形刀具和前角影响刀刃形状的其它刀具,为防止刃形畸变,常取较小的前角,甚至取γ.=0,但这些刀具的切削条件不好,应在保证切削刃成形精度的前提下,设法增大前角,例如有增大前角的螺纹车刀和齿轮滚刀等.(5)刀具材料的抗弯强度较大、韧性较好时,应选用较大的前角,如高速钢刀具比硬质合金刀具,允许选用较大的前角(约可增大5—10o).(6)工艺系统刚性差和机床功率不足时,应选取较大的前角.(7)数控机床和自动机、自动线用刀具,应考虑保障刀具尺寸公差范围的使用寿命及工作的稳定性,而选用较小的前角. 硬质合金车刀合理前角参考值见附录9的表9.1.二、后角的功用及合理后角值的选择后角也是刀具上主要的几何参数之一,它的数值合理与否直接影响已加工表面的质量、刀具使用寿命和生产率.1.后角的功用(1)后角的主要功用是减小后刀面与过渡表面之间的摩擦.由于切屑形成过程中的弹性、塑性变形和切削刃钝圆半径rn 的作用,在过渡表面上有一个弹性恢复层.后角越小,弹性恢复层同后刀面的摩擦接触长度越大,它是导致切削刃及后刀面磨损的直接原因之一.从这个意义上来看,增大后角能减小摩擦,可以提高已加工表面质量和刀具使用寿命.(2)后角越大,切削刃钝圆半径rn值越小,切削刃越锋利.(3)在同样的磨钝标准VB下,后角大的刀具由新用到磨钝,所磨去的金属体积较大(图10—8a),这也是增大后角可以延长刀具使用寿命的原因之一.但它带来的问题是刀具.。
切车刀几何参数选择

切车刀几何参数选择
2020年12月9日星期三
切车刀几何参数选择
1.6过渡刃选择
如图2-21所示 ,过渡刃的形状有直线形和圆弧形(即刀尖圆弧半径rε)
两种,前者因呈直线形,其偏角κrε大小通常均取主偏角κr值的一半左
右,过渡刃长度为0.5~2 mm。而后者不但能提高车刀的耐用度,还 可减少车削后的残留面积,降低工件已加工表面粗糙度。但刀尖圆弧 半径rε不宜过大,否则会引起振动。
2020年12月9日星期三
切车刀几何参数选择
• 硬质合金车刀刀尖圆弧半径参考值见表2-7。
2020年12月9日星期三
车工工艺与技能训练
车工工艺与技能训练
切车刀几何参数选择
1.1 前角选择
前角的选择主要遵循以下原则: (1)加工塑性材料时,前角应取较大值;加工脆性材料时,应选用
较小的前角。 (2)工件材料的强度、硬度较低时,选用较大的前角;反之,选用
较小 的前角。 (3)刀具材料坚韧性好时,前角应选大些(如高速钢车刀);刀具
材料 韧性差时,前角应选小些(如硬质合金车刀)。 (4)粗加工和断续切削时应选较小的前角,精加工时应选较大的前
尖强度。 硬质合金车刀副偏角参考值见表2-5。
2020年12月9日星期三
切车刀几何参数选择
1.5刃倾角选择
刃倾角的选择主要根据以下几点原则: (1)一般粗车时(指工件圆整、被切削层均匀),选取稍偏于负值
的刃倾角(-3°~0°);精车时,应选取负值的刃倾角(- 8°~-3°)。 (2)强力车削时,选取负值的刃倾角(-10°~-5°);冲击负 荷大的断续车削时,应选取较大负值的刃倾角(-10°以上)。 (3)加工高硬材料时,应选取负值的刃倾角,以提高刀尖强度。 硬质合金车刀刃倾角参考值见表2-6。
90度外圆车刀角度参数
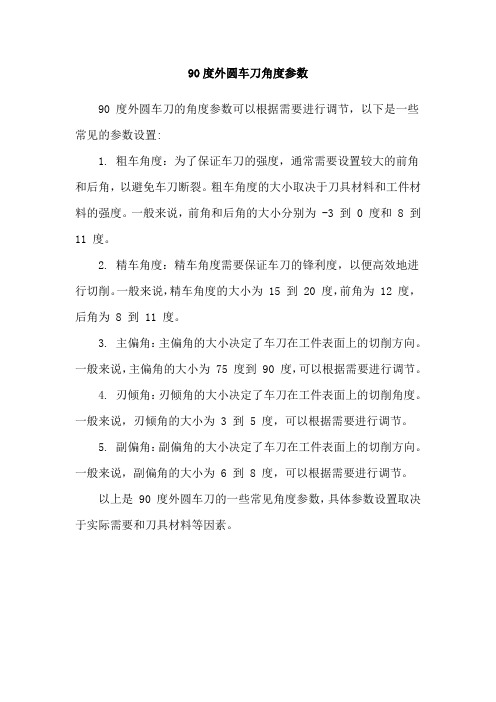
90度外圆车刀角度参数
90 度外圆车刀的角度参数可以根据需要进行调节,以下是一些常见的参数设置:
1. 粗车角度:为了保证车刀的强度,通常需要设置较大的前角和后角,以避免车刀断裂。
粗车角度的大小取决于刀具材料和工件材料的强度。
一般来说,前角和后角的大小分别为 -3 到 0 度和 8 到11 度。
2. 精车角度:精车角度需要保证车刀的锋利度,以便高效地进行切削。
一般来说,精车角度的大小为 15 到 20 度,前角为 12 度,后角为 8 到 11 度。
3. 主偏角:主偏角的大小决定了车刀在工件表面上的切削方向。
一般来说,主偏角的大小为 75 度到 90 度,可以根据需要进行调节。
4. 刃倾角:刃倾角的大小决定了车刀在工件表面上的切削角度。
一般来说,刃倾角的大小为 3 到 5 度,可以根据需要进行调节。
5. 副偏角:副偏角的大小决定了车刀在工件表面上的切削方向。
一般来说,副偏角的大小为 6 到 8 度,可以根据需要进行调节。
以上是 90 度外圆车刀的一些常见角度参数,具体参数设置取决于实际需要和刀具材料等因素。
刀主要角度
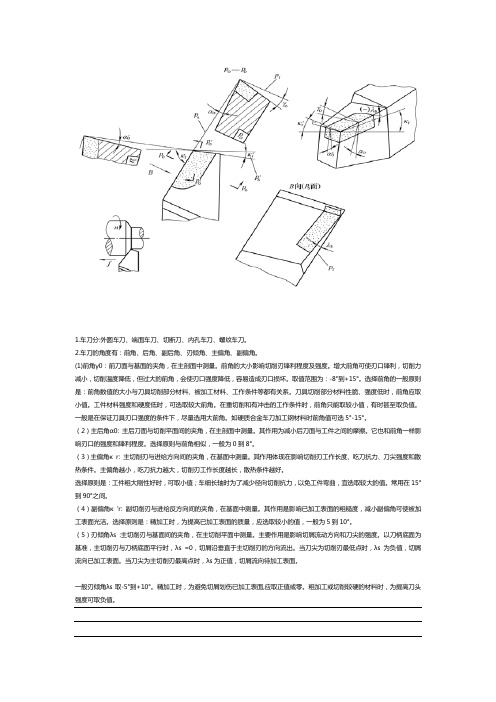
1.车刀分:外圆车刀、端面车刀、切断刀、内孔车刀、螺纹车刀。
2.车刀的角度有:前角、后角、副后角、刃倾角、主偏角、副偏角。
(1)前角γ0:前刀面与基面的夹角,在主剖面中测量。
前角的大小影响切削刃锋利程度及强度。
增大前角可使刃口锋利,切削力减小,切削温度降低,但过大的前角,会使刃口强度降低,容易造成刃口损坏。
取值范围为:-8°到+15°。
选择前角的一般原则是:前角数值的大小与刀具切削部分材料、被加工材料、工作条件等都有关系。
刀具切削部分材料性脆、强度低时,前角应取小值。
工件材料强度和硬度低时,可选取较大前角。
在重切削和有冲击的工作条件时,前角只能取较小值,有时甚至取负值。
一般是在保证刀具刃口强度的条件下,尽量选用大前角。
如硬质合金车刀加工钢材料时前角值可选5°-15°。
(2)主后角α0: 主后刀面与切削平面间的夹角,在主剖面中测量。
其作用为减小后刀面与工件之间的摩擦。
它也和前角一样影响刃口的强度和锋利程度。
选择原则与前角相似,一般为0到8°。
(3)主偏角κr: 主切削刃与进给方向间的夹角,在基面中测量。
其作用体现在影响切削刃工作长度、吃刀抗力、刀尖强度和散热条件。
主偏角越小,吃刀抗力越大,切削刃工作长度越长,散热条件越好。
选择原则是:工件粗大刚性好时,可取小值;车细长轴时为了减少径向切削抗力,以免工件弯曲,宜选取较大的值。
常用在15°到90°之间。
(4)副偏角κ'r: 副切削刃与进给反方向间的夹角,在基面中测量。
其作用是影响已加工表面的粗糙度,减小副偏角可使被加工表面光洁。
选择原则是:精加工时,为提高已加工表面的质量,应选取较小的值,一般为5到10°。
(5)刃倾角λs :主切削刃与基面间的夹角,在主切削平面中测量。
主要作用是影响切屑流动方向和刀尖的强度。
以刀柄底面为基准,主切削刃与刀柄底面平行时,λs =0,切屑沿垂直于主切削刃的方向流出。
[讲解]车刀角度对车削加工质量的影响文档
![[讲解]车刀角度对车削加工质量的影响文档](https://img.taocdn.com/s3/m/65fb825af6ec4afe04a1b0717fd5360cba1a8d07.png)
车刀角度对切削加工的影响(以车削为例)大前角刃口锋利,切屑变小,切削力小,切削轻快。
但易产生崩刃。
后角作用主要是减少后刀面和过渡表面之间的摩擦。
增大后角可减少摩擦,提高已加工表面质量和刀具使用寿命,并使切削刃锋利。
但是后角过大,楔角减小,降低切削刃的强度,减少散热体积,磨损反而加剧,降低刀具的耐用度。
主偏角影响切削层的形状,切削刃的工作长度和单位切削刃上的负荷。
减少κr,主切削刃单位长度上的负荷减少,刀具磨损小,耐用度提高,使已加工表面粗糙度减小。
较小的主偏角容易形成长而连续的螺旋屑,不利于断屑,因此对切屑控制严格的自动化加工,宜取较大的主偏角。
副偏角影响已加工表面的粗糙度和刀尖强度。
减少κr´,减少表面的粗糙度的数值,还可提高刀具强度,改善散热条件。
过小,会使副切削刃与已加工面的摩擦增加,引起震动,降低表面质量和刀具耐用度。
副偏角的大小主要根据已加工表面粗糙度要求和刀具强度来选择,不引起振动的情况下,尽量取小值。
车刀的角度对加工质量及效率的影响车刀的主要标注角度有以下5个:1.前角2.主后角3.主偏角4.副偏角5.刃倾角根据经验主偏角和副偏角构成刀尖角度,这个角度要根据粗精加工而定,粗加工时由于主要目的是去除大量的余量,所以这个角度可以适当的大一些,以适应大的进给量;精加工时,余量较少,要保证好的表面质量,所以刀尖角度要小,断屑槽要开的深一些,以免切屑流经已加工表面划伤工件表面。
还有刃倾角,负的刃倾角可以保护切削刃,承受大的进给量,反之则可以提高表面质量。
车刀前角对刀具切削性能影响的研究关于前角大小要根据加工工艺和工件材料来选择!1.前角有正前角和负前角之分(还有一种是0度前角多用于石墨加工)2.取正前角的目的是为了减小切屑被切下时的弹性变形和切屑流出时与前面的摩擦阻力,从而减小切削力和切削热,使切削轻快,提高已加工表面的质量。
3.取负前角的目的是在于改善刃部的受力状况和散热条件,提高切削刃强度和耐冲击能力。
外圆车削中前角的选择

前角为正的时候刀具锋利但是强度会降低负前角强度高但是加工表面质量不好一般粗加工用负前角精加工用正前角再就是加工比较软的或者塑性材料时用正前角!为了保证粗糙度与质量一般会选择在刀具承受内力内尽量选正前角!但是如果工件材料过硬容易蹦刀所以要根据实际情况和需要选取前角!
一般车比较软的材料时,应选用大前角的车刀;比如车铝合及镁合金时,高速钢和硬质合金车刀的前角均为30~35º;而车比较硬的材料时,比如钢α b>80~100时,高速钢车刀的前角为20~25º,硬质合金车刀的前角为10~15º;车淬火钢时,硬质合金车刀的前角为-5~10º。
而车钛合金时,高速钢的前角为20º;硬质合金车刀的前角为0º;车灰口铸铁HB≥220时,高速钢车刀的前角为10º,硬质合金车刀的前角为8º。
刀具角度的功用与选择精选文档
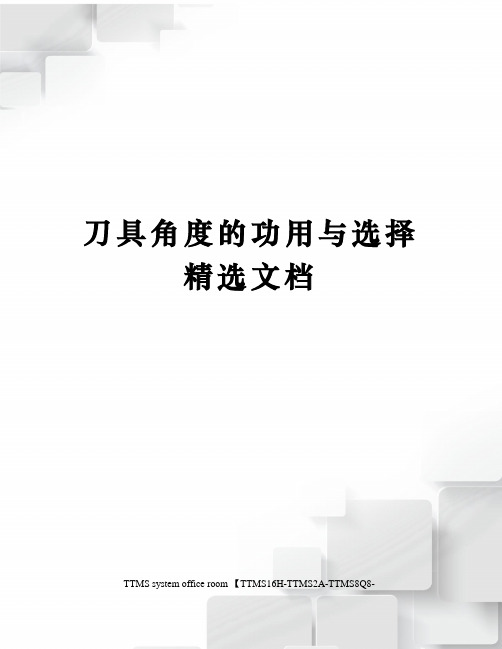
副偏角的大小主要根据表面粗糙度的要求选取,一般为5°~15°,粗加工时取大值,精加工时取小值。切断刀、锯片刀为保证刀头强度,只能取很小的副偏角,一般为1°~2°。
(1)根据工件材料选择前角。加工塑性材料时,特别是硬化严重的材料(如不锈钢等),为了减小切削变形和刀具磨损,应选用较大的前角;加工脆性材料时,由于产生的切屑为崩碎切屑,切削变形小,因此增大前角的意义不大,而这时刀屑间的作用力集中在切削刃附近,为保证切削刃具具有足够的强度,应采用较小的前角。
工件强度和硬度低时,切削力不大,为使切削刃锋利,可选用较大的甚至很大的前角。工件材料强度高时,应选用较小的前角;加工特别硬的工件材料(如淬火钢)时,应选用很小的前角,甚至选用负前角。因为工件的强度、硬度愈高,产生的切削力愈大,切削热愈多,为了使刃具有足够的强度和散热,防止崩刃和磨损,应选用较小的前角。
(1)根据切削厚度选择后角。合理后角大小主要取决于切削厚度(或进给量),切削厚度hD愈大,则后角应愈小;反之亦然。如进给量较大的外圆车刀后角=6°~8°,而每齿进刀量不超过mm的圆盘铣刀后角=?30°。这是因为切削厚度较大时,切削力较大,切削温度也较高,为了保证刃口强度和改善散热条件,所以应取较小的后角。切削厚度愈小,切削层上被切削刃的钝圆半径挤压而留在已加工表面上并与主后刀面挤压摩擦的这一薄层金属占切削厚度的比例就越大。若增大后角,就可减小刃口钝圆半径,使刃口锋利,便于切下薄切屑,可提高刀具耐用度和加工表面质量。
数控机床、自动机床和自动线用刀具,为保证刀具工作的稳定性,使其不易发生崩刃和破损,一般选用较小的前角。
- 1、下载文档前请自行甄别文档内容的完整性,平台不提供额外的编辑、内容补充、找答案等附加服务。
- 2、"仅部分预览"的文档,不可在线预览部分如存在完整性等问题,可反馈申请退款(可完整预览的文档不适用该条件!)。
- 3、如文档侵犯您的权益,请联系客服反馈,我们会尽快为您处理(人工客服工作时间:9:00-18:30)。
对车刀锋利程度、切削力大小、切屑变 形的影响:
增大前角,车刀变锋利,切削力减小,切 屑变形小
前角的作用
对车刀强度、受力情况和散热条件的影响
增大前角,楔角减小,刀头强度减小,散热 体积减小,从而散热条件变差,易使切削温 度升高。
前角的作用
对加工表面质量的影响
增大前角,刃口锋利,摩擦力小,可避 免积屑瘤产生,提高表面质量
车工工艺与技能训练
——车刀前角的选择——
学习目标
熟悉车刀工作图的画法 掌握车刀前角的作用 会根据实际情况合理选择车刀前角
车刀工作图
前角正负的确定
正前角:当前刀面与切削平面之间的夹角 小于90°时为正前角 负前角:当前刀面与切削平面之间的夹角 大于90°时为负前角
前角的作用
2、车刀前角的作用
3、车刀前角的选择
布置作业
1、车刀前角的作用是什么?如何根据实际情 况合理的选择车刀前角?(必做题) 2、试画出75°车刀的工作图。(选做题)
前角的选择
1、加工脆性材料或硬度较高的材料时应选择 较小 的前角;加工塑性材料或硬度较低的料 时应选择 较大 的前角。 2、精加工时应选择 较大 的前角;粗加工 时应选择 较小 的前角。 3、高速钢材料的车刀前角一般应 小于 (大于,小于)硬质合金材料的车刀前角。
课堂小结
本节