丁烷氧化
氧化工艺
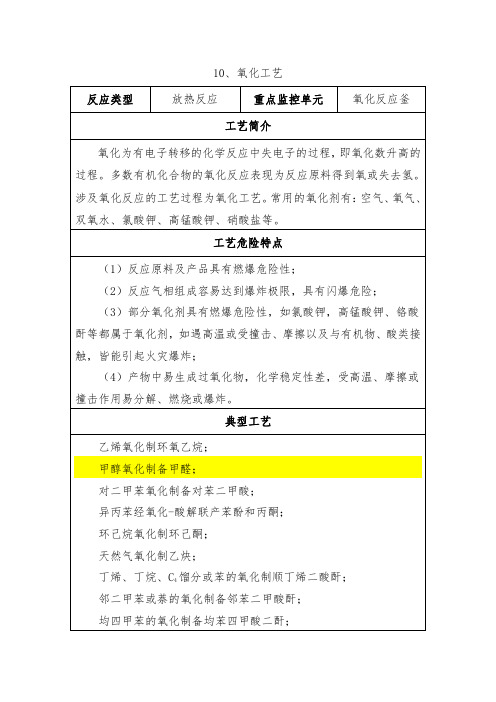
氨氧化制硝酸等。
重点监控工艺参数
氧化反应釜内温度和压力;氧化反应釜内搅拌速率;氧化剂流量;反应物料的配比;气相氧含量;过氧化物含量等。
安全控制的基本要求
反应釜温度和压力的报警和联锁;反应物料的比例控制和联锁及紧急切断动力系统;紧急断料系统;紧急冷却系统;紧急送入惰性气体的系统;气相氧含量监测、报警和联锁;安全泄放系统;可燃和有毒气体检测报警装置等。
1监控单元
氧化反应釜
工艺简介
氧化为有电子转移的化学反应中失电子的过程,即氧化数升高的过程。多数有机化合物的氧化反应表现为反应原料得到氧或失去氢。涉及氧化反应的工艺过程为氧化工艺。常用的氧化剂有:空气、氧气、双氧水、氯酸钾、高锰酸钾、硝酸盐等。
工艺危险特点
(1)反应原料及产品具有燃爆危险性;
4-甲基吡啶氧化制4-吡啶甲酸(异烟酸);
2-乙基已醇(异辛醇)氧化制备2-乙基己酸(异辛酸);
对氯甲苯氧化制备对氯苯甲醛和对氯苯甲酸;
甲苯氧化制备苯甲醛、苯甲酸;
对硝基甲苯氧化制备对硝基苯甲酸;
环十二醇/酮混合物的开环氧化制备十二碳二酸;
环己酮/醇混合物的氧化制己二酸;
乙二醛硝酸氧化法合成乙醛酸;
甲醇氧化制备甲醛;
对二甲苯氧化制备对苯二甲酸;
异丙苯经氧化-酸解联产苯酚和丙酮;
环己烷氧化制环己酮;
天然气氧化制乙炔;
丁烯、丁烷、C4馏分或苯的氧化制顺丁烯二酸酐;
邻二甲苯或萘的氧化制备邻苯二甲酸酐;
均四甲苯的氧化制备均苯四甲酸二酐;
苊的氧化制1,8-萘二甲酸酐;
3-甲基吡啶氧化制3-吡啶甲酸(烟酸);
(2)反应气相组成容易达到爆炸极限,具有闪爆危险;
(3)部分氧化剂具有燃爆危险性,如氯酸钾,高锰酸钾、铬酸酐等都属于氧化剂,如遇高温或受撞击、摩擦以及与有机物、酸类接触,皆能引起火灾爆炸;
正丁烷氧化法生产顺酐
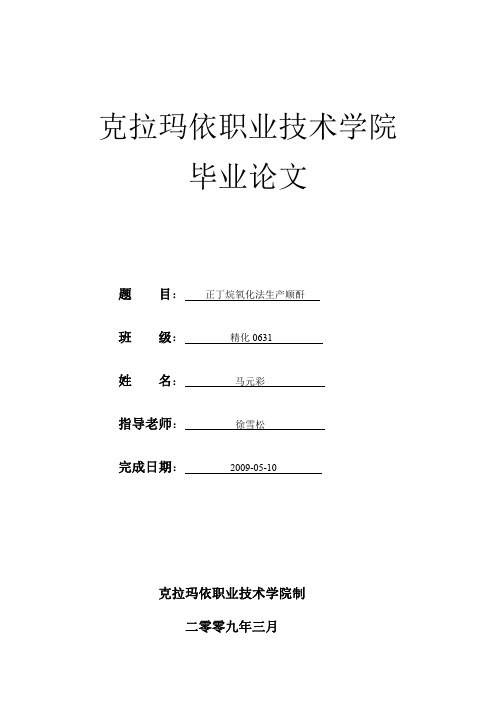
克拉玛依职业技术学院毕业论文题目:正丁烷氧化法生产顺酐班级:精化0631姓名:马元彩指导老师:徐雪松完成日期:2009-05-10克拉玛依职业技术学院制二零零九年三月克拉玛依职业技术学院石油化学工程系正丁烷氧化法生产顺酐摘要主要介绍了国内外顺酐的发展趋势,分析了我国顺酐工业的生产现状及国外的差距,对我国顺酐工业的发展提出了建议。
正文简述了以正丁烷为原料,固定床,有机溶剂回收生产顺酐的工艺流程,同时介绍了工业上采用正丁烷固定床氧化法的工艺特点及流程,并与流化床工艺进行了比较,最后得出结论:采用正丁烷氧化法生产工艺有很大的优势和发展前景,不但原料丰富,而且降低了一部分的动力费用等。
[关键词]顺酐正丁烷固定床流化床氧化法AbstractMainly introduces the development trend of domestic and maleic anhydride,maleic anhydride analysis of industrial production in China and abroad,the gap between the status quo of China's maleic anhydride industrial development proposals.Outlined in the body of n-butane as the raw material,fixed bed,organic solvent recovery process of the production of maleic anhydride and at the same time introduced the use of industrial fixed bed butane oxidation is the process characteristics and processes,and fluidized bed technology and compared,and finally come to the conclusion:the use of n-butane production of Oxidation technology have great advantages and development prospects,not only rich in raw materials,and reduced costs as part of the driving force.[Key words]Maleic anhydride N-butane fixed bed fluidized bed Oxidation目录前言 (3)1.概论 (4)1.1顺酐的国内外现状及发展趋势 (4)1.2对我国顺酐发展的建议 (4)1.2.1做好苯氧化法向正丁烷氧化法转变的技术准备工作 (4)1.2.2扩大装置生产能力,提高市场竞争能力,积极参与国际竞争 (5)2.顺酐的性质、用途 (6)2.1顺酐的性质 (6)2.2顺酐的用途 (6)3.生产顺酐的方法 (7)3.1苯氧化法生产顺丁烯二酸酐 (7)3.1.1反应原理 (7)3.1.2工艺条件 (8)3.1.3工艺流程 (8)3.2丁烷氧化法生产顺丁烯二酸酐 (9)3.2.1反应原理 (9)3.2.2工艺条件 (10)3.2.3工艺流程 (11)3.3工业采用正丁烷固定床氧化生产顺酐工艺流程 (11)3.3.1工艺流程 (11)3.4.工业生产中两种方法的优缺点 (13)3.4.1原料成本 (13)3.4.2产量 (13)3.4.3催化剂 (13)4.生产顺酐的先进方法 (14)结束语 (16)致谢 (17)参考文献 (18)前言本论文是根据《有机化工生产技术》教材和实习单位工业上生产顺酐书写而成。
正丁烷氧化制顺酐催化剂的制备及其催化性能
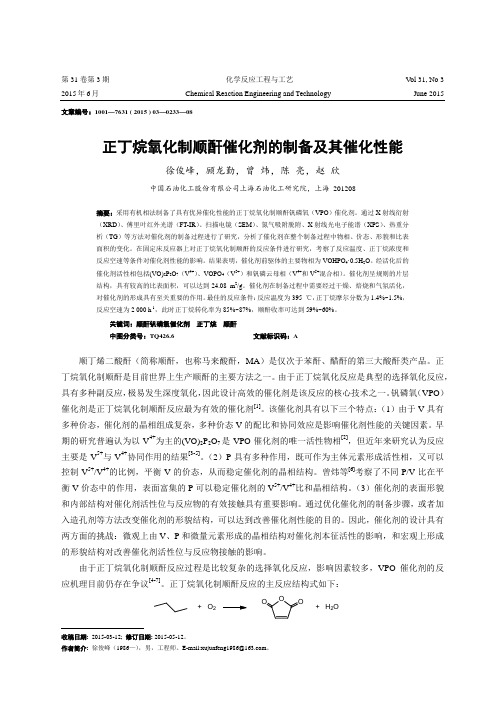
第31卷第3期 化学反应工程与工艺 V ol 31, No 3 2015年6月 Chemical Reaction Engineering and Technology June 2015 收稿日期: 2015-03-12; 修订日期: 2015-05-12。
作者简介: 徐俊峰(1986—),男,工程师。
E-mail:xujunfeng1986@ 。
文章编号:1001—7631 ( 2015 ) 03—0233—08正丁烷氧化制顺酐催化剂的制备及其催化性能徐俊峰,顾龙勤,曾 炜,陈 亮,赵 欣中国石油化工股份有限公司上海石油化工研究院,上海 201208摘要:采用有机相法制备了具有优异催化性能的正丁烷氧化制顺酐钒磷氧(VPO )催化剂。
通过X 射线衍射(XRD )、傅里叶红外光谱(FT-IR )、扫描电镜(SEM )、氮气吸附脱附、X 射线光电子能谱(XPS )、热重分析(TG )等方法对催化剂的制备过程进行了研究,分析了催化剂在整个制备过程中物相、价态、形貌和比表面积的变化。
在固定床反应器上对正丁烷氧化制顺酐的反应条件进行研究,考察了反应温度、正丁烷浓度和反应空速等条件对催化剂性能的影响。
结果表明,催化剂前驱体的主要物相为VOHPO 4·0.5H 2O 。
经活化后的催化剂活性相包括(VO)2P 2O 7(V 4+)、VOPO 4(V 5+)和钒磷云母相(V 4+和V 5+混合相)。
催化剂呈规则的片层结构,具有较高的比表面积,可以达到24.08 m 2/g 。
催化剂在制备过程中需要经过干燥、焙烧和气氛活化,对催化剂的形成具有至关重要的作用。
最佳的反应条件:反应温度为395 ℃,正丁烷摩尔分数为1.4%~1.5%,反应空速为2 000 h -1,此时正丁烷转化率为85%~87%,顺酐收率可达到59%~60%。
关键词:顺酐钒磷氧催化剂 正丁烷 顺酐中图分类号:TQ426.6 文献标识码:A顺丁烯二酸酐(简称顺酐,也称马来酸酐,MA )是仅次于苯酐、醋酐的第三大酸酐类产品。
正丁烷氧化法顺丁烯二酸酐生产工艺尾气的循环利用

消耗量不应超过 765 kg / d。在生产过程中通过统 计发现, 溶剂消耗异常升高时有发生, 溶剂最高 消耗量甚至超过 2 t / d, 严重影响着尾气循环工艺
第1 期
吴振阔. 正丁烷氧化法顺丁烯二酸酐生产工艺尾气的循环利用
· 53·
降低空气的流通阻力。 将丝网均匀地分层缠绕 在一个锥 形 固 定 架 上, 每层丝网网孔均拉成菱 形, 丝网整体均具有导流作用, 分离下来的液滴 在重力作用下沿菱形丝网下落、 集聚, 最后通过 分离器的锥形边缘导向塔壁并沿塔壁流到塔盘 上。在丝网除沫器中增设导流筋更有利于导流。 实现分离、 导流一体化后就不需要再设置导流 设施。
3 达到了预期的 10 000 m / h, 占反应单元工艺尾气 总量的 15% 。正丁烷回收量为 65 kg / h。 正丁烷
为 10. 101 。为保证天然气在锅炉中充分燃烧, 新 3 12 121. 2 m / h 。 鲜空气需要量应为 4. 2 正丁烷氧化为顺酐需要的氧气量 ( Q2 ) 理论上 2 分子正丁烷与 7 分子氧气反应, 生成
图3
改造前后装置的点仪、 pH 计等, 在尾气循环区域内增加可燃气体在线 监测报 警 仪。 采 取 前 期 控 制, 包括稳定反应状 态, 使尾气中正丁烷含量稳定; 中期做好尾气质 量监控; 后期预防的控制措施, 包括投用装置联 锁、 预 防 装 置 产 生 CO 等, 以保障人员及财产 安全。 3 运行效果
2. 3
改造气液分离罐底部排液口 由于鼓风机入口为微负压, 所以气液分离罐
中也是微负压。将出口改造为双 U 型结构, 使出 , 口水平段低于罐底出口管连接部位 由高度差形 成的液柱压力略高于罐中 负 压 值 ( 改 造 情 况 如 图 4 所示) , 使罐中积液在排出口未积满时便可自 压流出, 实现了罐中低液位的自动控制, 避免了 因巡检不及时或异常状况时罐中积液过多而被 吸入鼓风机入口, 影响到尾气循环系统的正常使
乙酸

乙酸百科名片编辑本段现在的大部分醋是通过液态的细菌培养基制备的,由Otto Hromatka和Heinrich Ebner在1949年首次提出。
在此方法中,酒精在持续的搅拌中发酵为乙酸,空气通过气泡的形式被充入溶液。
通过这个方法,含乙酸15%的醋能够在两至三天制备完成。
无氧发酵部分厌氧细菌,包括梭菌属的部分成员,能够将糖类直接转化为乙酸而不需要乙醇作为中间体。
总体反应方程式如下:C6H12O6 → 3 CH3COOH更令工业化学感兴趣的是,许多细菌能够从仅含单碳的化合物中生产乙酸,例如甲醇,一氧化碳或二氧化碳与氢气的混和物。
2 CO2 + 4 H2 → CH3COOH + 2 H2O2 CO + 2 H2 → CH3COOH梭菌属因为有能够直接使用糖类的能力,减少了成本,这意味着这些细菌有比醋菌属细菌的乙醇氧化法生产乙酸更有效率的潜力。
然而,梭菌属细菌的耐酸性不及醋菌属细菌。
耐酸性最大的梭菌属细菌也只能生产不到10%的乙酸,而有的醋酸菌能够生产20%的乙酸。
到现在为止,使用醋酸属细菌制醋仍然比使用梭菌属细菌制备后浓缩更经济。
所以,尽管梭菌属的细菌早在1940年就已经被发现,但它的工业应用仍然被限制在一个狭小的范围。
甲醇羰基化法大部分乙酸是通过甲基羰基化合成的。
此反应中,甲醇和一氧化碳反应生成乙酸,方程式如下CH3OH + CO → CH3COOH这个过程是以碘代甲烷为中间体,分三个步骤完成,并且需要一个一般由多种金属构成的催化剂(第二部中)(1) CH3OH + HI → CH3I + H2O(2) CH3I + CO → CH3COI(3) CH3COI + H2O → CH3COOH + HI通过控制反应条件,也可以通过同样的反应生成乙酸酐。
因为一氧化碳和甲醇均是常用的化工原料,所以甲基羰基化一直以来备受青睐。
早在1925年,英国塞拉尼斯公司的Henry Drefyus已经开发出第一个甲基羰基化制乙酸的试点装置。
正丁醇生产工艺
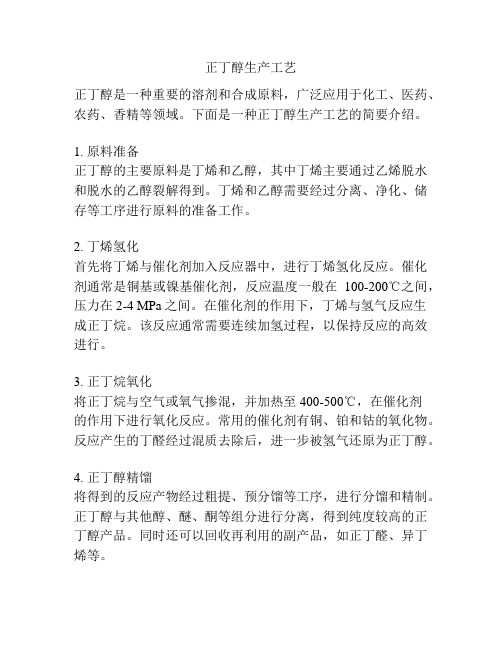
正丁醇生产工艺
正丁醇是一种重要的溶剂和合成原料,广泛应用于化工、医药、农药、香精等领域。
下面是一种正丁醇生产工艺的简要介绍。
1. 原料准备
正丁醇的主要原料是丁烯和乙醇,其中丁烯主要通过乙烯脱水和脱水的乙醇裂解得到。
丁烯和乙醇需要经过分离、净化、储存等工序进行原料的准备工作。
2. 丁烯氢化
首先将丁烯与催化剂加入反应器中,进行丁烯氢化反应。
催化剂通常是铜基或镍基催化剂,反应温度一般在100-200℃之间,压力在2-4 MPa之间。
在催化剂的作用下,丁烯与氢气反应生成正丁烷。
该反应通常需要连续加氢过程,以保持反应的高效进行。
3. 正丁烷氧化
将正丁烷与空气或氧气掺混,并加热至400-500℃,在催化剂
的作用下进行氧化反应。
常用的催化剂有铜、铂和钴的氧化物。
反应产生的丁醛经过混质去除后,进一步被氢气还原为正丁醇。
4. 正丁醇精馏
将得到的反应产物经过粗提、预分馏等工序,进行分馏和精制。
正丁醇与其他醇、醚、酮等组分进行分离,得到纯度较高的正丁醇产品。
同时还可以回收再利用的副产品,如正丁醛、异丁烯等。
5. 正丁醇储存和包装
得到的正丁醇产品需要进行储存和包装,以确保产品的质量和安全。
正丁醇通常储存在密闭的容器中,避光和防潮。
在搬运和包装过程中,需要注意防火和防爆,确保操作安全。
以上是一种正丁醇生产工艺的简要介绍,不同厂家、不同工艺可能会有所不同。
在实际生产中,还需要考虑熔剂、配料比例、催化剂的选择和反应条件的优化等因素,以提高生产效率和产品质量。
常见的有机化学反应类型

三、常见的有机化学反应类型:1、取代反应:有机分子里的某些原子或原子团被其它原子或原子团所代替的反应,即原子或原子团“有进有出”。
常见取代反应:①烷烃的卤代 ②苯的卤代、硝化、磺化 ③卤代烃的水解 ④醇和钠反应⑤醇分子间脱水 ⑥酚和浓溴水反应 ⑦羧酸和醇的酯化反应 ⑧ 酯的水解反应 发生取代反应的基/官能团2、加成反应:有机分子里的不饱和碳原子跟其它原子或原子团直接结合成一种新有机物的反应,即原子或原子团“只进不出”。
目前学习到的不饱和碳原子主要存在于碳碳双键、碳碳三键、苯环、碳氧双键等基团中,发生加成反应的物质主要有烯烃、炔烃、芳香族化合物、醛等物质。
其中烯、炔常见的加成物质是氢气、卤素单质、卤化氢和水。
醛常见的加成物质是氢气,而羧酸、酯、肽键中的碳氧双键一般不能加成。
3、消去反应:有机化合物在适当条件下,从一分子中脱去一个小分子(如水、卤化氢),而生成不饱和(含双链或叁键)化合物的反应,即原子或原子团“只出不进”。
能发生消去反应的有机物有:卤代烃、醇。
发生消去的结构要求:有机物分子中与官能团(—OH ,—X )相连碳原子的邻碳原子必须要有氢原子。
4、聚合反应加聚反应:含有碳碳双链等的不饱和有机物,以加成的方式相互结合,生成高分子化合物的反应。
发生加聚反应的有烯烃以及它们的衍生物如:丙烯酸、甲基丙烯酸甲酯等。
缩聚反应:单体间的相互反应生成高分子,同时还生成小分子副产物(如H 2O 、有机物无机物/有机物 反应名称 烷,芳烃,酚X 2 卤代反应 苯的同系物HNO 3 硝化反应 苯的同系物H 2SO 4 磺化反应 醇 醇 脱水反应 醇 HX 取代反应 酸 醇 酯化反应 酯醇酯交换反应酯/卤代烃酸溶液或碱溶液水解反应二糖、多糖 H 2O水解反应蛋白质H 2O水解反应羧 酸 盐碱石灰 脱羧反应HX等)的反应。
5、氧化反应:氧化反应就是有机物分子里“加氧”或“去氢”的反应。
有机物的燃烧,烯烃、炔烃、苯的同系物的侧链、醇、醛等可被某些氧化剂所氧化。
丁烷理化性质

打火机内液体的主要成分是丁烷:结构简式CH3CH2CH2CH3分子式C4H10热化学方程式:C4H10+13/2O2=4CO2+5H2O(l)△H=-2878KJ/mol (25℃ 101kPa)与空气形成爆炸混合物,爆炸极限为1.9%~8.4%理化性质外观与性状:无色气体,有轻微的异味。
主要用途:用于有机合成和乙烯制造,仪器校正,也用作燃料等。
熔点:-138.4沸点:-0.5相对密度(水=1):0.58相对密度(空气=1):2.05饱和蒸汽压(kPa):106.39/O℃溶解性:易溶于水、醇、氯仿。
临界温度(℃):151.9临界压力(MPa):3.79燃烧热(kj/mol):2653燃烧爆炸危险性避免接触的条件:燃烧性:易燃,最小引燃能量(mj):0.25建规火险分级:甲闪点(℃):-60自燃温度(℃):287爆炸下限(V%):1.5爆炸上限(V%):8.5危险特性:与空气混合能形成爆炸性混合物,遇明火、高热能引起燃烧爆炸。
其蒸气比空气重,能在较低处扩散到相当远的地方,遇火源引着回燃。
若遇高热,容器内压增大,有开裂和爆炸的危险。
燃烧(分解)产物:一氧化碳、二氧化碳。
稳定性:稳定禁忌物:强氧化剂、卤素。
聚合危害:不能出现灭火方法:切断气源。
若不能立即切断气源,则不允许熄灭正在燃烧的气体。
喷水冷却容器,可能的话将容器从火场移至空旷处。
雾状水、泡沫、二氧化碳。
普通的一元打火机内的液体体积大约是5毫升,通常情况下,液体变成气体,体积要扩大1000倍左右(并非绝对,因各种打火机的压强不同而有所不同),所以打火机内的液体释放之后体积大约是5000毫升左右,核算为12.975g,0.22324摩尔,完全燃烧后放热592.269KJ。
应该就是这些了还有别的需要再告诉我……。
- 1、下载文档前请自行甄别文档内容的完整性,平台不提供额外的编辑、内容补充、找答案等附加服务。
- 2、"仅部分预览"的文档,不可在线预览部分如存在完整性等问题,可反馈申请退款(可完整预览的文档不适用该条件!)。
- 3、如文档侵犯您的权益,请联系客服反馈,我们会尽快为您处理(人工客服工作时间:9:00-18:30)。
化工专业实验报告实验名称:正丁烷氧化制顺丁烯二酸酐实验人员:熊传烨同组人:徐志良、伟昌鹏实验地点:天大化工技术实验中心 630 室实验时间:2015年3月25日班级/学号: 12级化工三班 23 组 3006207084号指导教师:实验成绩:一、实验目的及要求1、学习固定床反应器的流程布置及一般控制原理,了解气固相催化反应中温度和气体空速(单位时间单位催化剂通过原料气的量)变化对反应过程的影响。
2、学习使用气相色谱分析气体含量,并学会用色谱对气体定性和定量分析的方法,掌握气体校正因子的计算和气体真实含量的计算。
3.掌握自动化控制仪表在实验中的应用,学会不同仪表的使用和温度设置。
了解气体质量流量计的原理和使用,并掌握气体流量的测试方法。
4.了解气体六通阀的原理,了解气体自动进样分析的管路连接方式,了解色谱工作站的部分使用。
二、实验原理1、苯氧化法:通常采用V-P-Ti-O催化剂,在固定床或流化床反应器于380~450℃下反应。
该方法工艺路线成熟,原料易得,是国内应用比较普遍的方法,但是由于在苯的六个碳中有两个变成CO2,对原料浪费较大,在国际上开始被正丁烷氧化代替。
C6H6 + 4.5O2→C4H2O3 +CO2 +H2O2、碳四馏分氧化法CH3-CH2-CH2-CH3 +2O2→C4H2O3 +H2O丁烷是碳四馏分中最廉价又容易获得的原料,它与空气混合氧化生产成本较低,采用V-O-P催化剂,由于能充分利用原料,且原料的重量收率较高,近年来该法发展迅速,工业上已有替代苯氧化法的趋势,本实验采用此方法。
但是,由于近年国际市场石油价格变动较大,丁烷气的价格也变化较大,使该工艺在原料材料价格上不占优势。
同时,由于丁烷气在空气中的爆炸极限只有1.8%,在用固定床进行生产时,反应放热剧烈,反应器体积和操作空速要求较高,生产的工艺要求和技术比苯直接氧化法高,现在国际上使用流化床反应器,可以使原料气浓度在丁烷的爆炸上限范围,即40%以上,但该反应器对催化剂强度和活性要求较高,在我国尚未投入生产。
三、实验流程及仪器设备本实验由原料气配气系统,反应器控温系统,催化反应器,产物吸收及气相色谱分析系统组成。
具体介绍如下:1、原料气配气系统由液化丁烷气罐、空气压缩机、空气储罐、丁烷气体及空气质量流量计、原料气混合罐组成。
空气首先由压缩机压缩到空气储气罐里,然后经过减压阀到空气流量计,流量计的读数由显示仪控制,一般为1000ml/min左右,注意流量计的读数是指气体在标准状态下的体积,不是实际测定状态下的体积或质量流量,流量计的读数和气体温度、压力没有太大关系。
可以换算摩尔或质量。
丁烷经过减压阀也到质量流量计,并根据实验的条件,一般控制和空气的体积比为1.6%以下,以免发生爆炸危险。
丁烷气体质量流量计的读数需乘以0.29,才是丁烷的标准体积。
和空气分别进入红色混合罐的上部,并在罐内进行混合,当混合气体的压力达到0.2Mpa时,才能开始实验。
配好的反应原料气从罐的下部出来,分别进入到稳压阀、压力表和气体六通阀,然后进入每个反应器的转子流量计,可以根据实验要求调节进入反应器的流量。
2、反应器控温系统反应器采用三段加热系统控制,每段加热功率1000W,分别控制反应器上段、中段和下段。
反应器上段加热主要起对原料气进行预热,由位式仪表控制,该仪表使用时需设定高限和低限温度,控温精度较差,电流一般不大于1.5A。
反应器中段温度采用人工智能仪表控制,只需要设定一个温度,使用方便,控制精度高,被用来控制床层中段的催化剂温度,加热电流不大于1.5A。
下段加热和上段加热一样,使用位式仪表控制,主要是防止产物顺丁烯二酸酐在出口和反应器底部凝结堵塞。
3、反应器反应器由不锈钢制造,内径20mm,长度为500mm。
反应器底部装有支撑作用的瓷环,然后在中部装填催化剂,装填量20毫升(堆体积),催化剂上部再装入瓷环,用于对原料气加热。
反应管插入三个加热炉,分别给反应管的上、中、下三台仪表控制,为了达到最好的恒温区,三块仪表的温度通常设置相同,一般和反应所需要的温度一样。
为了准确测定催化剂的温度,在开始装填催化剂的时候,首先在反应器中心插入一根一端封死的φ3mm金属管。
准确测量催化剂在反应器内的起始高度,然后慢慢震荡加入用量筒准确测量体积的催化剂,并用天平称量重量。
在催化剂加入完毕后,再测量出催化剂在反应器内的高度。
金属管内可以插入热电偶,用于测量催化剂床层的中心温度,当热电偶在床层上下移动时,可以测定催化剂床层的轴向温度分布,并确定床层的热点温度和位置。
4、产物吸收丁烷气通过催化剂床层时被空气氧化,部分变成产物顺丁烯二酸,还有少量的变成CO和CO2,产物和没有反应的气体一起从反应器下部流出,进入到水吸收瓶,吸收瓶加入少量蒸馏水,产物中的顺丁烯二酸酐被水吸收,变成顺丁烯二酸,没有反应的气体经过六通阀,可以分析丁烷含量,然后经过湿式气体流量计,记录尾气总体积后排入大气中。
5、色谱在线分析混合好的原料气和反应完毕的气体,均分别通过不同的六通阀进入气相色谱进行分析,色谱柱为邻苯二甲酸二壬酯,使用95℃,检测室100℃温度,柱前压0.05Mpa,色谱出峰的顺序为空气(0.2min),水(0.4min),丁烷(1.4~1.7min),由于水对结果没有太大的影响,且尾气里的水多数是由于吸收饱和,含量不高,故为了方便数据处理,一般把空气和水峰放在一起。
丁烷的含量采用归一法处理,因为原料气用质量流量计配制,可以作为标准气体来分析,用原料分析进样,可以得到原料气在色谱的分析结果,由此计算出丁烷相对空气的校正因子,然后,将几次分析得到的校正因子平均。
将用尾气分析阀进样得到数值用校正因子计算,可得到尾气里丁烷的真实含量。
四、实验流程图五、操作步骤1. 调节转子流量计,使流量在0.2L/min。
取下尾气吸收瓶,将其洗净,并换上蒸馏水(约2/3处),并记下湿式流量计的读数。
2. 打开主电源,然后在分别打开上、中、下三段加热电源,再打开显示仪表电源。
按仪表使用说明,调节三段的加热温度为380℃、400℃、420℃,保持每段的加热电流不得超过1.5A。
3. 反应器中段状填催化剂,使用程序仪表控制。
按“设定”键,设定灯开始闪亮,此时可通过上下光标键调节温度值到需要的数值,然后再按设定键即可完成。
4. 当反应器每段温度都达到设定值后,再稳定15分钟,然后开始正式实验。
将吸收瓶清洗干净,然后加入适量的水,使出气管能在水中鼓泡即可。
记录尾气流量计的读数,记录开始实验的时间,以吸收瓶开始换上的时间为准。
5. 每个温度条件下实验持续30分钟,在30分钟内应分析原料和尾气含量两次,并记录反应温度和床层中心轴向温度分布和热点温度。
实验结束时换下吸收瓶,记录尾气流量计的读数,前后的差值即30分钟内渡过反应器的尾气(原料)气体体积。
吸收瓶内的酸溶液用稀碱滴定。
6. 改变反应器各段的温度为380℃和380℃,当温度稳定时,再重复上述步骤,再做两组实验,完成后再改变各段温度为400℃,完成相同的步骤。
7. 色谱分析采用六通阀进样,一般阀应顺时针放置在进样位置,在点击工作站到出现“确定”键的界面后,点击开始,再向逆时针方向转动阀,使分析样品进入六通阀的定量管,20秒以后再点击工作站的“确定”键的同时将阀转到进样位置。
五、原始数据记录表表-1 反应过程温度记录表表-2 反应过程湿式流量计记录表表-3 色谱分析结果记录六、实验结果一览表表-4 校正因子一览表表-5 尾气丁烷浓度CA表表-6 正丁烷转化率、顺酐收率、选择性数据表七、实验数据处理(举例计算)(以380℃中的原料气1及尾气1为例)1.原料气丁烷浓度计算:校正后丁烷质量流量计读数校正后空气质量流量计读数校正后丁烷质量流量计读数其中:校正后丁烷质量流量计读数丁烷质量流量计读数2、丁烷相对空气校正因子计算原料气丁烷浓度色谱分析原料丁烷气面积色谱分析空气面积色谱分析原料丁烷气面积可得:原料气丁烷浓度色谱分析空气面积色谱分析原料丁烷气面积色谱分析原料丁烷气面积原料丁烷气浓度色谱分析空气面积色谱分析原料丁烷气面积()代入数据可得:()3、尾气丁烷浓度C A计算色谱分析尾气丁烷气面积色谱分析空气面积色谱分析尾气丁烷气面积代入数据:4、正丁烷转化率计算原料混合气丁烷量尾气丁烷量原料混合气丁烷量即:5、顺酐收率计算碱用量()碱浓度()顺酐尾气取样总体积()原料气丁烷浓度丁烷即:6、顺酐选择性计算7、实验结果分析:由数据分析可知,正丁烷转化率随反应温度升高而增大,本反应是可逆放热反应,故反应温度应该尽量靠近处在最佳反应温度的一侧,这样既可以保证实验快速高效地完成,如果反应温度离最佳反应温度较远,则反应速率很慢,顺酐收率随反应温度升高增大,顺酐选择性同样随反应温度减小。
说明当反应温度升高时,副反应加剧是引起选择性降低的主要原因。
转化率收率选择性随温度如下图。
图-1转化率、收率、选择性随温度变化图八、思考题1.为什么在用质量流量计准确配置原料气浓度后,仍然用色谱分析原料浓度?答:原料气采用质量流量计配置,可以作为标准气体来分析,用原料气分析进样,则可以得到原料气在色谱的分析结果,由此可以反算出丁烷相对空气的校正因子。
将几次分析得到的校正因子平均,将用尾气分析阀进样得到数值用校正因子计算,可得到尾气里丁烷的真实含量。
2.如何利用质量流量计读数计算气体的摩尔浓度?答:气体浓度读数校正后目标气体质量流量计读数校正后其他气体质量流量计读数校正后目标气体质量流量计本实验中,校正后丁烷质量流量计读数为丁烷质量流量计读数乘以0.29后的值,而校正后的空气质量流量计读数等于空气质量流量计读数。
3.如何计算气体的校正因子?如何计算气体的准确浓度?答:利用流量计定量进样配置标准气体,而后根据气相色谱峰面积,利用下面公式列出方程组,即可以得到气体中各组成的相对校正因子。
已知利用此公式正向运算,就可以求出气体的准确浓度。
4.怎样选择反应温度?反应温度对实验结果有什么影响?答:本反应是可逆放热反应,故反应温度应该尽量靠近处在最佳反应温度的一侧,这样既可以保证实验快速高效地完成,如果反应温度离最佳反应温度较远,则反应速率很慢,改变反应温度,达到稳态需要较长的时间,不利于实验的操作。
在本次实验中,反应温度越高,反应转化率越高。
5.如何测定反应温度?如何确定反应器热点温度?有什么意义?答:温度即床层温度,在开始装填催化剂时,首先在反应器中心插入一根一端金属管,金属管内可以插入热电偶,用语测量催化剂床层的中心温度,当热电偶在床层上下移动时,还可以测定催化剂床层的轴向温度分布,并确定床层的热点温度和位置。
确定反应热点温度,有助于判断反应是否正常进行。
6.利用尾气流量计计算收率和选择性有什么误差?如何修正?答:实验中测量的数据是在非标准状态下的,而流量计的刻度是以标准状况下的气体标定的。