5铜合金固溶时效处理工艺规范-悉云飞
固溶处理和时效处理【范本模板】

固溶处理和时效处理1、固溶处理所谓固溶处理,是指将合金加热到高温奥氏体区保温,使过剩相充分溶解到固溶体中后快速冷却,以得到过饱和固溶体的热处理工艺。
固溶处理的主要目的是改善钢或合金的塑性和韧性,为沉淀硬化处理作好准备等。
适用多种特殊钢,高温合金,特殊性能合金,有色金属。
尤其适用:1.热处理后须要再加工的零件。
2。
消除成形工序间的冷作硬化。
3。
焊接后工件。
原理序言固溶处理是为了溶解基体内碳化物、γ'相等以得到均匀的过饱和固溶体,便于时效时重新析出颗粒细小、分布均匀的碳化物和γ'等强化相,同时消除由于冷热加工产生的应力,使合金发生再结晶。
其次,固溶处理是为了获得适宜的晶粒度,以保证合金高温抗蠕变性能。
固溶处理的温度范围大约在980~1250℃之间,主要根据各个合金中相析出和溶解规律及使用要求来选择,以保证主要强化相必要的析出条件和一定的晶粒度。
对于长期高温使用的合金,要求有较好的高温持久和蠕变性能,应选择较高的固溶温度以获得较大的晶粒度;对于中温使用并要求较好的室温硬度、屈服强度、拉伸强度、冲击韧性和疲劳强度的合金,可采用较低的固溶温度,保证较小的晶粒度。
高温固溶处理时,各种析出相都逐步溶解,同时晶粒长大;低温固溶处理时,不仅有主要强化相的溶解,而且可能有某些相的析出。
对于过饱和度低的合金,通常选择较快的冷却速度;对于过饱和度高的合金,通常为空气中冷却。
不锈钢固溶热处理碳在奥氏体不锈钢中的溶解度与温度有很大影响.奥氏体不锈钢在经400℃~850℃的温度范围内时,会有高铬碳化物析出,当铬含量降至耐腐蚀性界限之下,此时存在晶界贫铬,会产生晶间腐蚀,严重时能变成粉末.所以有晶间腐蚀倾向的奥氏体不锈钢应进行固溶热处理或稳定化处理。
固溶热处理:将奥氏体不锈钢加热到1100℃左右,使碳化物相全部或基本溶解,碳固溶于奥氏体中,然后快速冷却至室温,使碳达到过饱和状态。
这种热处理方法为固溶热处理。
固溶热处理中的快速冷却似乎象普通钢的淬火,但此时的‘淬火'与普通钢的淬火是不同的,前者是软化处理,后者是淬硬。
铸造合金的固溶处理与时效硬化

铸造合金的固溶处理与时效硬化铸造合金的固溶处理与时效硬化是一种常用的金属材料热处理方法,旨在利用热处理工艺改善合金的性能,提高其力学性能和耐蚀性。
本文将详细介绍铸造合金的固溶处理和时效硬化的原理、工艺条件及其对合金性能的影响。
一、固溶处理固溶处理是指将固溶体相中的溶质元素加热至合金固溶区,使其尽可能均匀地分布在母相中,并随后以适当速率冷却。
固溶处理的目的是通过溶解溶质元素,使合金的晶体结构得到改善,并提高其力学性能和耐蚀性。
1. 原理固溶处理的原理基于固相反应和扩散行为。
在加热过程中,溶质元素会从固溶体中解出,扩散至母相中。
随着加热温度和时间的增加,溶质元素的浓度分布逐渐均匀化。
冷却过程中,溶质元素重新溶解,并在晶界、位错和空位等缺陷区域重新分布,从而使晶体结构得到改善。
2. 工艺条件固溶处理的工艺条件包括温度、时间和冷却速率。
合金的化学成分、晶体结构和应用要求决定了具体的固溶处理参数。
常见的固溶处理工艺包括均匀化处理和超固溶处理。
均匀化处理是指将合金加热至固溶温度区进行足够时间的保温,使溶质元素均匀分布在母相中,然后以适当速率冷却。
超固溶处理是在均匀化处理的基础上进行再加热,目的是加速溶质元素的扩散和再结晶行为。
3. 影响性能固溶处理对铸造合金的性能有着显著影响。
首先,固溶处理能改善合金的强度和硬度。
通过溶解溶质元素,可以增加固溶体的强度,减小晶界的能量,提高晶体的硬度。
其次,固溶处理还能提高合金的塑性和延展性。
通过溶解溶质元素,使晶体内的位错易于运动,从而增加合金的塑性和延展性。
最后,固溶处理能改善合金的耐腐蚀性能。
在固溶处理中,溶质元素的均匀分布可以有效抑制晶界腐蚀和局部腐蚀,提高合金的耐腐蚀性能。
二、时效硬化时效硬化是固溶处理后的继续热处理过程,通过固溶体中的溶质元素在室温下产生沉淀相的方式,进一步改善合金性能。
时效硬化可增加合金的强度和硬度,同时保持较好的塑性。
1. 原理当固溶体在室温下保持一段时间后,溶质元素会聚集形成超饱和的溶质团簇,随着时间的增加,这些溶质团簇逐渐长大并转变为稳定的沉淀相。
固溶处理标准规范要求

固溶处理标准规范要求
固溶处理作为一种常见的热处理工艺,在工业生产中起着至关重要的作用。
其通过改变材料的组织结构和性能,从而提高材料的力学性能、耐腐蚀性能和疲劳寿命。
为了确保固溶处理的效果,避免不必要的质量问题,制定了一系列标准和规范来指导工程师和操作人员进行固溶处理。
首先,固溶处理的温度和时间是至关重要的参数。
在进行固溶处理时,必须严格控制固溶温度和时间,以确保达到预期的固溶效果。
通常情况下,固溶温度应该高于合金的固溶温度范围,固溶时间则应根据具体材料和要求而定。
过高或过低的固溶温度和时间都会造成固溶效果不理想。
其次,冷却速度也是固溶处理中需要重点关注的参数之一。
合适的冷却速度可以帮助固溶处理后的材料获得理想的晶粒结构,并保持材料的优良性能。
通常情况下,固溶处理后的材料应采用适当的冷却速度进行冷却,以避免出现过快或过慢的冷却速度导致的问题。
此外,固溶处理前后的检测和验证也是固溶处理标准规范中必不可少的一环。
在进行固溶处理之前,需要对材料的组织结构和性能进行全面检测,以确保固溶处理的必要性和可行性。
而在固溶处理完成后,则需要对固溶效果进行验证和评估,确认固溶处理的效果是否符合要求。
总的来说,固溶处理是一项复杂而重要的工艺,在工程实践中需要严格按照标准规范要求进行操作。
只有通过合理的固溶温度和时间控制、适当的冷却速度以及全面的检测和验证,才能够确保固溶处理的效果达到预期,提高材料的性能和可靠性。
只有这样,固溶处理才能够发挥其应有的作用,为工业生产质量和效率提供保障。
1。
高强高导铜合金固溶时效处理工艺及组织性能研究

南京理工大学硕士学位论文高强高导铜合金固溶时效处理工艺及组织性能研究姓名:张森林申请学位级别:硕士专业:材料科学与工程指导教师:孔见;陶圣祥20070701高(具体分析参见本章3。
3.1)。
经过时效处理以后又有大量的Cr粒子析出,并随着时效处理时间的延长,析出粒子数量进一步增加但逐渐粗化,如图3.3e、f所示,不过始终为圆形或近圆形。
Cr析出粒子呈弥散分布。
形成沉淀相,这样能有效阻止晶界和位错移动,从而使得Cu.0.7Cr合金材料的强度获得了极大地提高,当然,超过一定时效后,合金材料强度将有所下降(具体分析参见本章3.3.2)。
关于Cu.0.7er合金的析出物形貌和取向关系。
一般认为受到淬火和时效条件影响p”,水淬有利于均匀形核,可获得择优取向较为稳定的针状析出相。
图3.3不同处理态Cu.0.7Cr合金的金相显微组织a.铸态:b.热加工态;C-冷加工态;d-固溶态;e.45012、2h时效;f-450"C、24h时效选取不同固溶温度对Cu.0.7Cr合金金相组织进行观察,如图3.4所示。
比较图3.4a、b、c可以看出,在1000℃范围内,随着固溶温度的升高,析出的Cr粒子数量逐渐减少,溶入固溶体中的Cr粒子相应增多,固溶量增大。
从表3.1可知,随着固溶温度的升高,Cu.0.7Cr合金材料硬度值上升,但变化不是很明显,同样在450℃、4h的时效制度下,960℃、lh,980℃、Ih,1000℃、lh固溶温度时,Cu.0.70r合金硬度值分别为76.1Hv、76.4Hv、77.0Hv。
从表3.2看出.同样在450℃、12h时效制度下,经过960℃、lh,980℃、Ih,1000℃、lh固溶处理,Cu.0.7Cr合金材料的力学性能得到了有效改善,其抗拉强度分别为352MPa、354MPa、358MPa,屈服强度分别为235MPa、270MPa、287MPa,但导电性能略微有所下降。
Cu.0.7Cr、Cu.0.7Cr.0.4Zr合金材料在1000℃、980℃、960℃下均为不完全固溶。
固溶与时效

一、合金的固溶与时效处理 二、时效对合金组织结构及性能的影响
一、合金的固溶与时效处理
固溶与时效处理的工艺过程
(一)固溶处理
把某一成分的合金加热到固溶度曲线以上,在 某一温度保持一定时间,使得B组元充分溶入α固 溶体中,然后迅速冷却,抑制B元素析出,得到过 饱和α固溶体,这就是固溶处理。 (二)时效处理 经固溶处理后的合金在室温下放置或加热到 低于溶解度曲线的某一温度保温,合金将产生脱 溶析出,即B将以新相的形式从过饱和α相中弥散 析出,这个过程即是时效。通常将在室温下放置 产生的时效称为自然时效;将加热到室温以上某 一温度进行的时效称为人工时效。
二、时效对合金组织结构及、硬度升高,这种 现象称为时效硬化时效硬化即脱溶沉淀引 起的沉淀硬化。
Al-Cu合金在130℃时效曲线及其结构变化
Al-Cu合金在130℃时效时结构变化: 过饱和固溶体→G..P(Ⅰ)区→G.P(Ⅱ)区→θ' 相 (共格)→θ相(非共格) 1. 形成溶质原子偏聚区(即G.P区) 2. 形成过渡相( θ') 3. 形成平衡相( θ) 硬度提高
硬度提高减缓 硬度降低 过时效
合金脱溶沉淀与时效

二.调幅分解过程
是纯扩散过程,一般脱溶分解是下坡扩散,即高浓度向 低浓度扩散,而调幅分解是上坡扩散,低浓度向高浓度 扩散。 三.组织、构造、性能 1.构造特点:分解产物与母相晶体构造相同,仅成份不 同,故新相与母相一直保持共格关系。 2.组织特点:因新相与母相在分解过程中,一直保持共 格关系,必然产生应力场,应变能增长。 (1)择优取向析出 (2)弥散度大
强度、硬度较低(HRC30,因C量低),成型性能 好。 时效强化效应,时效后屈服强度为: 1400~3500MPa. 二.铁基合金中旳淬火时效 1.铁素体中合金K脱溶 2.奥氏体钢淬火时效现象
§7.6合金旳调幅分解
调幅分解定义:由过饱和固溶体分 解产生两种构造相同,成份不同旳 固溶体(但一种为溶质富化,一种 为溶质贫化),这种分解按扩散--偏聚机构进行旳固态相变。 一.热力学条件 成份在拐点之间旳合金(G-C曲线 下凹) 换句话:只有在旳范围内旳合金才 干进行调幅分解,即RKV范围内。
2. 脱溶析出:从过饱和固溶体中析出(沉淀相)或形成 溶质原子汇集区及亚稳定相旳过程,称为脱溶析出或 沉淀,是溶解旳逆过程。
3. 时效:合金在脱溶过程中,其力学、物理、化学性能 均随之发生变化旳现象。
4.时效硬化(沉淀强化):时效析出过程中,合金中旳 强度、硬度逐渐升高旳过程。
三.时效析出过程与亚稳定平衡相图
第七章合金旳脱溶沉淀与时效
Hale Waihona Puke §7.1 脱溶过程和脱溶物旳构造
一、对比钢旳淬火+回火后HRC变化曲线和AlCu合金旳时效强化曲线
二、名词解释
1. 固溶:将某一成份旳合金加热到单相区(α相),经 足够时间保温,使合金元素(溶质元素)充分溶解入 固溶体中,然后予以速冷,以克制这些元素重新析出, 致室温下取得一种过饱和固溶体。
固熔处理、时效处理工艺概述
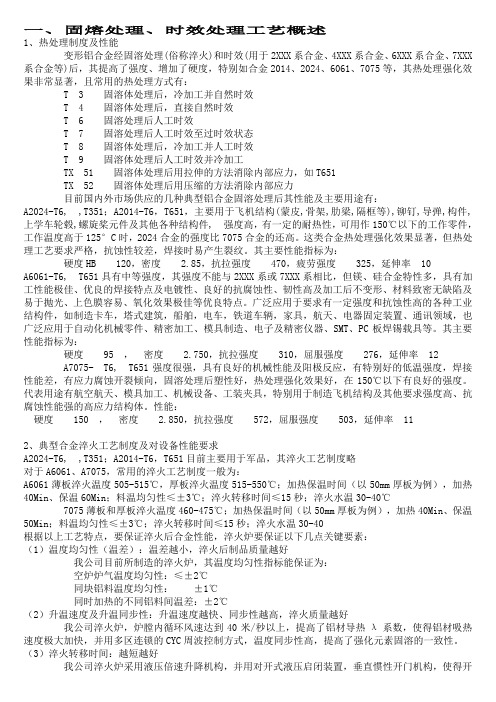
一、固熔处理、时效处理工艺概述1、热处理制度及性能变形铝合金经固溶处理(俗称淬火)和时效(用于2XXX系合金、4XXX系合金、6XXX系合金、7XXX 系合金等)后,其提高了强度、增加了硬度,特别如合金2014、2024、6061、7075等,其热处理强化效果非常显著,且常用的热处理方式有:T 3 固溶体处理后,冷加工并自然时效T 4 固溶体处理后,直接自然时效T 6 固溶处理后人工时效T 7 固溶处理后人工时效至过时效状态T 8 固溶体处理后,冷加工并人工时效T 9 固溶体处理后人工时效并冷加工TX 51 固溶体处理后用拉伸的方法消除内部应力,如T651TX 52 固溶体处理后用压缩的方法消除内部应力目前国内外市场供应的几种典型铝合金固溶处理后其性能及主要用途有:A2024-T6, ,T351;A2014-T6,T651,主要用于飞机结构(蒙皮,骨架,肋梁,隔框等),铆钉,导弹,构件,上学车轮毂,螺旋桨元件及其他各种结构件, 强度高,有一定的耐热性,可用作150℃以下的工作零件,工作温度高于125°C时,2024合金的强度比7075合金的还高。
这类合金热处理强化效果显著,但热处理工艺要求严格,抗蚀性较差,焊接时易产生裂纹。
其主要性能指标为:硬度HB 120,密度 2.85,抗拉强度470,疲劳强度325,延伸率10A6061-T6, T651具有中等强度,其强度不能与2XXX系或7XXX系相比,但镁、硅合金特性多,具有加工性能极佳、优良的焊接特点及电镀性、良好的抗腐蚀性、韧性高及加工后不变形、材料致密无缺陷及易于抛光、上色膜容易、氧化效果极佳等优良特点。
广泛应用于要求有一定强度和抗蚀性高的各种工业结构件,如制造卡车,塔式建筑,船舶,电车,铁道车辆,家具,航天、电器固定装置、通讯领域,也广泛应用于自动化机械零件、精密加工、模具制造、电子及精密仪器、SMT、PC板焊锡载具等。
其主要性能指标为:硬度95 ,密度 2.750,抗拉强度310,屈服强度276,延伸率12A7075- T6, T651强度很强,具有良好的机械性能及阳极反应,有特别好的低温强度,焊接性能差,有应力腐蚀开裂倾向,固溶处理后塑性好,热处理强化效果好,在150℃以下有良好的强度。
固溶处理

固溶所谓固溶处理,是指将合金加热到高温奥氏体区保温,使过剩相充分溶解到固溶体中后快速冷却,以得到过饱和固溶体的热处理工艺。
固溶处理的主要目的是改善钢或合金的塑性和韧性,为沉淀硬化处理作好准备等。
固溶处理是材料科学实验中一种非常常见的加工处理工艺。
由固溶可得到固溶体。
目的主要是改善钢和合金的塑性和韧性,为沉淀硬化处理作好准备等。
使合金中各种相充分溶解,强化固溶体,并提高韧性及抗蚀性能,消除应力与软化,以便继续加工或成型。
适用多种特殊钢,高温合金,特殊性能合金,有色金属。
尤其适用:1.热处理后须要再加工的零件。
2.消除成形工序间的冷作硬化。
3.焊接后工件。
原理序言固溶处理是为了溶解基体内碳化物、γ’相等以得到均匀的过饱和固溶体,便于时效时重新析出颗粒细小、分布均匀的碳化物和γ’等强化相,同时消除由于冷热加工产生的应力,使合金发生再结晶。
其次,固溶处理是为了获得适宜的晶粒度,以保证合金高温抗蠕变性能。
固溶处理的温度范围大约在980~1250℃之间,主要根据各个合金中相析出和溶解规律及使用要求来选择,以保证主要强化相必要的析出条件和一定的晶粒度。
对于长期高温使用的合金,要求有较好的高温持久和蠕变性能,应选择较高的固溶温度以获得较大的晶粒度;对于中温使用并要求较好的室温硬度、屈服强度、拉伸强度、冲击韧性和疲劳强度的合金,可采用较低的固溶温度,保证较小的晶粒度。
高温固溶处理时,各种析出相都逐步溶解,同时晶粒长大;低温固溶处理时,不仅有主要强化相的溶解,而且可能有某些相的析出。
对于过饱和度低的合金,通常选择较快的冷却速度;对于过饱和度高的合金,通常为空气中冷却。
不锈钢固溶热处理碳在奥氏体不锈钢中的溶解度与温度有很大影响。
奥氏体不锈钢在经400℃~850℃的温度范围内时,会有高铬碳化物析出,当铬含量降至耐腐蚀性界限之下,此时存在晶界贫铬,会产生晶间腐蚀,严重时能变成粉末。
所以有晶间腐蚀倾向的奥氏体不锈钢应进行固溶热处理或稳定化处理。
- 1、下载文档前请自行甄别文档内容的完整性,平台不提供额外的编辑、内容补充、找答案等附加服务。
- 2、"仅部分预览"的文档,不可在线预览部分如存在完整性等问题,可反馈申请退款(可完整预览的文档不适用该条件!)。
- 3、如文档侵犯您的权益,请联系客服反馈,我们会尽快为您处理(人工客服工作时间:9:00-18:30)。
铜合金固溶时效处理工艺规范
总体说明:
本技术规范规定了铝青铜合金、硅青铜合金及铜镍硅合金固溶时效强化处理的方式、工艺、设备及验收检验规则。
一、适用范围
本技术规范适用于电气化铁路接触网零件用铝青铜合金、硅青铜合金、铜镍硅合金零件的热处理强化。
二、设备及要求
2.1 淬火加热炉可选用带风扇搅动炉气的箱式电阻炉、井式电阻炉或网带式炉或流态炉。
炉温控温精度为±3℃,炉温均匀度应在±5℃范围内。
2.2 回火加热炉可选用带风扇搅动炉气的箱式电阻炉、井式电阻炉。
电温控温精度为±2℃,炉温均匀度应在±5℃范围内。
2.3 淬火槽应满足零件淬火冷却时的需要,淬火液的温度不应超过5~40℃范围。
淬火槽应具有淬火液强制循环功能或具有搅动功能,保证淬火液温度均匀。
三、工艺参数
3.1固溶淬火:
铜合金加热温度、保温时间、冷却方式按下表1选择:
表1 固溶淬火工艺参数 合金种类 加热温度℃
保温时间 冷却方式 QAl9-2 790~810 水冷至室温QAl9-4 840~860 水冷至室温QSi1-3 790~810 水冷至室温CuNi2Si 850~870 按每25mm厚度1h计算 水冷至室温 注:选择加热温度时应考虑所采用的加热设备和装炉方式、装炉量。
3.2 时效:
铜合金加热温度、保温时间、冷却方式按下表2选择:
表2 时效处理工艺参数 合金种类 加热温度℃ 保温时间h
冷却方式 QAl9-2 390~410 2~3 空冷至室温
QAl9-4 340~360 2~3 空冷至室温
QSi1-3 410~475 1~3 空冷至室温
CuNi2Si 420~470 1~3 空冷至室温
四、 工艺要求
4.1 铜合金零件固溶处理加热要求热炉装料,随炉升温。
4.2零件装炉时应采用专用的装料筐。
对采用箱式电炉加热的方式,应保证装料筐距加热元件不小于100mm。
4.3零件应有序的排放至装料筐内,防止因放置不当造成零件的变形或对螺纹、牙型造成损伤。
4.4淬火时零件在淬火液中作垂直上下和圆周均匀移动,以保证零件的淬透性。
4.5淬火过程中不允许零件露出淬火液面。
4.6固溶淬火后到时效处理的时间间隔不允许超过8h。
五、检验与验收
5.1 经固溶强化处理后的零件表面不允许出现裂纹、严重变形等热处理缺陷。
出厂前应逐件进行检查。
5.2经固溶强化处理后的零件按5%抽检硬度,HB应不小于185。