无损检测基本知识及相关标准简介
无损检测基本知识
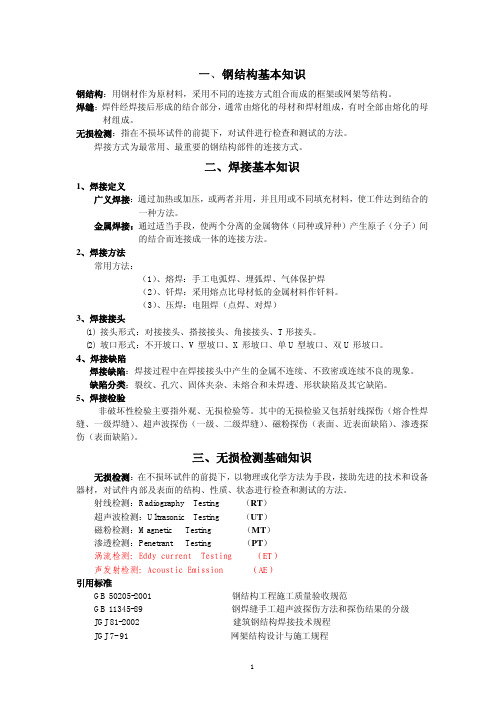
一、钢结构基本知识钢结构:用钢材作为原材料,采用不同的连接方式组合而成的框架或网架等结构。
焊缝:焊件经焊接后形成的结合部分,通常由熔化的母材和焊材组成,有时全部由熔化的母材组成。
无损检测:指在不损坏试件的前提下,对试件进行检查和测试的方法。
焊接方式为最常用、最重要的钢结构部件的连接方式。
二、焊接基本知识1、焊接定义广义焊接:通过加热或加压,或两者并用,并且用或不同填充材料,使工件达到结合的一种方法。
金属焊接:通过适当手段,使两个分离的金属物体(同种或异种)产生原子(分子)间的结合而连接成一体的连接方法。
2、焊接方法常用方法:(1)、熔焊:手工电弧焊、埋弧焊、气体保护焊(2)、钎焊:采用熔点比母材低的金属材料作钎料。
(3)、压焊:电阻焊(点焊、对焊)3、焊接接头(1) 接头形式:对接接头、搭接接头、角接接头、T形接头。
(2) 坡口形式:不开坡口、V型坡口、X形坡口、单U型坡口、双U形坡口。
4、焊接缺陷焊接缺陷:焊接过程中在焊接接头中产生的金属不连续、不致密或连续不良的现象。
缺陷分类:裂纹、孔穴、固体夹杂、未熔合和未焊透、形状缺陷及其它缺陷。
5、焊接检验非破坏性检验主要指外观、无损检验等。
其中的无损检验又包括射线探伤(熔合性焊缝、一级焊缝)、超声波探伤(一级、二级焊缝)、磁粉探伤(表面、近表面缺陷)、渗透探伤(表面缺陷)。
三、无损检测基础知识无损检测:在不损坏试件的前提下,以物理或化学方法为手段,接助先进的技术和设备器材,对试件内部及表面的结构、性质、状态进行检查和测试的方法。
射线检测:Radiography Testing (RT)超声波检测:Ultrasonic Testing (UT)磁粉检测:Magnetic Testing (MT)渗透检测:Penetrant Testing (PT)涡流检测:Eddy current Testing (ET)声发射检测:Acoustic Emission (AE)引用标准GB 50205-2001 钢结构工程施工质量验收规范GB 11345-89 钢焊缝手工超声波探伤方法和探伤结果的分级JGJ 81-2002 建筑钢结构焊接技术规程JGJ 7- 91 网架结构设计与施工规程JG/T 3034.1-1996 焊接球节点钢网架焊缝超声波探伤及质量分级法JG/T 3034.2-1996 螺栓球节点钢网架焊缝超声波探伤及质量分级法ZBY 230- 84(JB/T10061-1999)A型脉冲反射式超声探伤仪通用技术条件ZBY 231-84(JB/T10062-1999) 超声探伤用探头性能测试方法ZBY 232-84(JB/T10063-1999) 超声探伤用1号标准试块技术条件ZB J04 001- 87(JB/T9214-1999) A型脉冲反射式超声探伤系统工作性能测试方法(一)、射线检测(RT)射线探伤是利用射线可穿透物质和在穿透物质时能量有衰减的特性来发现缺陷的一种探伤方法。
无损检测4730标准

无损检测4730标准无损检测是一种通过对材料和构件进行检测,而不影响其使用性能和结构完整性的检测方法。
无损检测4730标准是对无损检测方法和技术的规范,其制定的目的是为了保证无损检测的准确性和可靠性,从而确保被检测物体的安全性和可靠性。
本文将对无损检测4730标准进行详细介绍,包括其背景、内容要点以及应用范围等方面的内容。
1. 背景。
无损检测4730标准是由国际无损检测协会(International Society for Non-Destructive Testing,简称ISNT)制定的国际标准。
该标准是基于对无损检测技术的深入研究和实践经验总结而制定的,旨在统一无损检测的方法和要求,提高无损检测的准确性和可靠性,从而确保被检测物体的安全性和可靠性。
无损检测4730标准的制定,为无损检测技术的发展和应用提供了重要的指导和依据。
2. 内容要点。
无损检测4730标准主要包括以下内容要点:(1)无损检测的基本原理和方法,对无损检测的基本原理和常用方法进行了详细的介绍,包括超声波检测、磁粉检测、涡流检测、射线检测等。
(2)无损检测的设备和工艺,对无损检测所需的设备和工艺进行了规定,包括设备的选择和校准、检测的操作流程和注意事项等。
(3)无损检测的评定标准,对无损检测结果的评定标准进行了规定,包括缺陷的分类、尺寸和位置的评定要求等。
(4)无损检测的报告和记录,对无损检测结果的报告和记录进行了规定,包括报告的内容和格式、记录的保存和管理要求等。
3. 应用范围。
无损检测4730标准适用于各种材料和构件的无损检测,包括金属材料、非金属材料、焊接接头、铸件、锻件等。
该标准适用于工业生产、航空航天、铁路运输、核能领域等各个领域,为相关行业的无损检测工作提供了重要的依据和指导。
总结。
无损检测4730标准是对无损检测方法和技术的规范,其制定的目的是为了保证无损检测的准确性和可靠性,从而确保被检测物体的安全性和可靠性。
7 无损检测基础知识
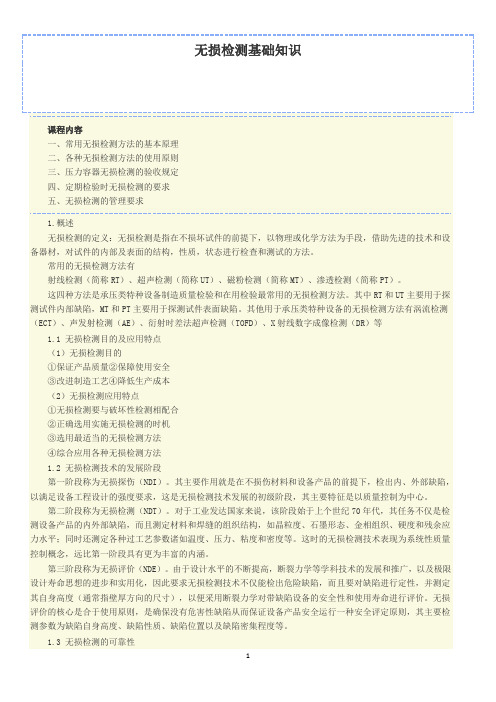
无损检测基础知识课程内容一、常用无损检测方法的基本原理二、各种无损检测方法的使用原则三、压力容器无损检测的验收规定四、定期检验时无损检测的要求五、无损检测的管理要求1.概述无损检测的定义:无损检测是指在不损坏试件的前提下,以物理或化学方法为手段,借助先进的技术和设备器材,对试件的内部及表面的结构,性质,状态进行检查和测试的方法。
常用的无损检测方法有射线检测(简称RT)、超声检测(简称UT)、磁粉检测(简称MT)、渗透检测(简称PT)。
这四种方法是承压类特种设备制造质量检验和在用检验最常用的无损检测方法。
其中RT和UT主要用于探测试件内部缺陷,MT和PT主要用于探测试件表面缺陷。
其他用于承压类特种设备的无损检测方法有涡流检测(ECT)、声发射检测(AE)、衍射时差法超声检测(TOFD)、X射线数字成像检测(DR)等1.1 无损检测目的及应用特点(1)无损检测目的①保证产品质量②保障使用安全③改进制造工艺④降低生产成本(2)无损检测应用特点①无损检测要与破坏性检测相配合②正确选用实施无损检测的时机③选用最适当的无损检测方法④综合应用各种无损检测方法1.2 无损检测技术的发展阶段第一阶段称为无损探伤(NDI)。
其主要作用就是在不损伤材料和设备产品的前提下,检出内、外部缺陷,以满足设备工程设计的强度要求,这是无损检测技术发展的初级阶段,其主要特征是以质量控制为中心。
第二阶段称为无损检测(NDT)。
对于工业发达国家来说,该阶段始于上个世纪70年代,其任务不仅是检测设备产品的内外部缺陷,而且测定材料和焊缝的组织结构,如晶粒度、石墨形态、金相组织、硬度和残余应力水平;同时还测定各种过工艺参数诸如温度、压力、粘度和密度等。
这时的无损检测技术表现为系统性质量控制概念,远比第一阶段具有更为丰富的内涵。
第三阶段称为无损评价(NDE)。
由于设计水平的不断提高,断裂力学等学科技术的发展和推广,以及极限设计寿命思想的进步和实用化,因此要求无损检测技术不仅能检出危险缺陷,而且要对缺陷进行定性,并测定其自身高度(通常指壁厚方向的尺寸),以便采用断裂力学对带缺陷设备的安全性和使用寿命进行评价。
无损检测基础知识

一、无损检测基础知识1.1无损检测概况1.1.1无损检测的定义和分类什么叫无损检测,从文字上面理解,无损检测就是指在不损坏试件的前提下,对试件进行检查和测试的方法。
但是这并不是严格意义上的无损检测的定义,对现代无损检测的定义是:在不损坏试件的前提下,以物理或化学为手段,借助先进的技术和设备器材,对试件的内部及表面的结构、性质、状态进行检查和测试的方法。
在无损检测技术发展过程中出现三个名称,即:无损探伤(Non-destructive lnspction),无损检测(Non-des tructive Testing),无损评价( Non-destructive Evaluation)。
一般认为,这三个名称体现了无损检测技术发展的三个阶段,其中无损探伤是早期阶段的名称,其内涵是探测和发现缺陷;无损检测是当前阶段的名称,其内涵不仅仅是探测缺陷,还包括探测试件的一些其它信息。
而无损评价则是即将进入或正在进入的发展阶段,无损评价包涵更广泛,更深刻的内容,它不仅要求发现缺陷,探测试件的结构、性质、状态,还要求获取全面的、更准确的、综合的信息。
射线检测(Radiographyic Testing,,简称RT),超声波检测(Uitrasonic Tes ting,简称UT),磁粉检测(MagneticTesting简称MT),渗透检测(Penetrant Testing,简称PT)是开发较早,应用较广泛的探测缺陷的方法,称为四大常规检测方法,到目前为止,这四种方法仍是锅炉压力容器制造质量检验和再用检验最常用的无损检测方法,其中RT和UT主要用于检测试件内部缺陷。
PT主要用于检测试件表面缺陷,MT主要用于检测试件表面及近表面缺陷。
其它用于锅炉压力容器的无损检测方法有涡流检测(Eddy current Testing,简称ET)、声发射检测(Acoustic Emission,简称AE)。
1.1.2无损检测的目的用无损检测技术,通常是为了达到以下目的:1、保证产品质量;2、保障使用安全;3、改进制造工艺;4、降低生产成本。
无损检测知识基础知识

(3)射线的安全防护。射线的安全防护主要是采用 时间防护、距离防护和屏蔽防护三大技术。
时间防护即为尽量缩短人体与射线接触的时间。 如果到射线源的距离增大2倍,射线的强度会降低3/4。 利用这一原理,可以采用机械手、远距射线源操作等 方法进行距离防护。还可在人体与射线源之间隔上一 层屏蔽物,以阻挡射线,即进行屏蔽防护。
常用胶片类别
T2类胶片: AgfaD4、D5;天津Ⅴ;上海GX-A5。
T3类胶片: AgfaD7、D8;天津Ⅲ;上海GX-A7
工艺要点(3)透照方式选择
工艺要点(4)透照参数选择
1、焦距——影响几何不清晰度,选择焦距必须大于标准规定最 小值;
2、K值——影响横向裂纹检出率,选择K值不得大于标准规定值; 3、射线能量——影响底片对比度、固有不不清晰度、颗粒度; 选择射线能量应在标准限定范围; 4、曝光量——影响底片黑度,选择曝光量应在标准限定范围;
(2)设计温度低于-290C的管道,不锈钢和淬硬倾向较大的合 金钢管道焊缝表面,不得有咬边现象。其它材质管道焊缝咬边深度 不应大于0.5mm,连续咬边长度不应大于100mm,且连续咬边总长 度不大于该焊缝全长的10%; (3)焊缝表面不得低于管道表面。焊缝余高Δh≤1﹢0.2b1,且 不大于3mm。 (4)焊接接头错边不应大于壁厚的10%,且不大于2mm.
什么是无损检测——定义与分类
在承压类特种设备构件的内部,常常存在着不易发现的缺陷;如焊 缝中的未熔合、未焊透、夹渣、气孔、裂纹等。要想知道这些缺陷的位 置、大小、性质,对每一台设备进行破坏性检查是不可能的,为此出现 了无损检测法。 它是在不损伤被检工件的情况下,利用材料和材料中缺陷所具有 的物理特性探查其内部是否存在缺陷的方法。 应用无损检测技术通常是为了达到4个目的:保证产品质量、保障 安全使用、改进制造工艺、降低生产成本。
无损检测项目及标准

无损检测(Non-Destructive Testing,简称NDT)是一种在不破坏被检测物体的情况下,通过对其进行探测和分析,以了解其内在质量、缺陷和性能的方法。
无损检测项目包括多种检测技术,如X射线无损检测、超声波无损检测、磁粉无损检测、渗透无损检测等。
这些检测项目各自有相应的标准规范。
以下是无损检测项目及部分相关标准:
1. X射线无损检测:X射线无损检测主要用于检测内部缺陷、结构组成等。
相关标准有:
- GB/T 7704-2017《无损检测X射线应力测定》
- GB/T 12604.2-2005《无损检测术语射线照相检测》
2. 超声波无损检测:超声波无损检测主要用于检测内部缺陷、厚度、强度等。
相关标准有:
- GB/T 5616-2014《无损检测应用导则》
- GB/T 11343-2008《无损检测接触式超声斜射检测》
- GB/T 12604.1-2005《无损检测术语超声检测》
3. 磁粉无损检测:磁粉无损检测主要用于检测表面缺陷。
相关标准有:
- GB/T 12604.3-2013《无损检测术语渗透检测》
- GB/T 12604.4-2005《无损检测术语声发射》
4. 渗透无损检测:渗透无损检测主要用于检测表面缺陷。
相关标准有:
- GB/T 12604.3-2013《无损检测术语渗透检测》
- GB/T 12604.4-2005《无损检测术语声发射》。
无损检测方法及设备性能检验流程与标准
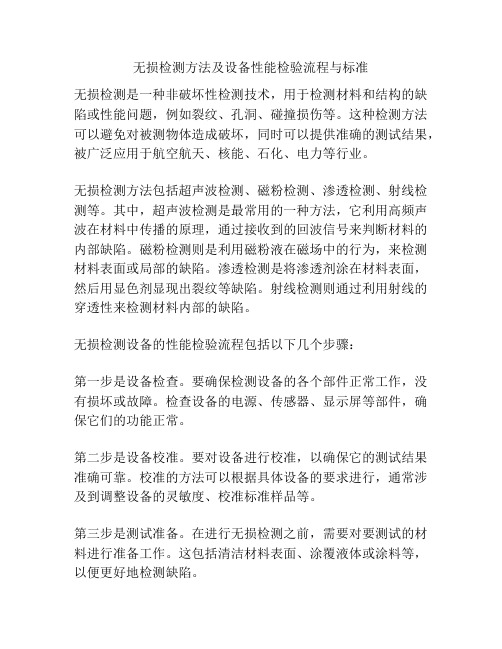
无损检测方法及设备性能检验流程与标准无损检测是一种非破坏性检测技术,用于检测材料和结构的缺陷或性能问题,例如裂纹、孔洞、碰撞损伤等。
这种检测方法可以避免对被测物体造成破坏,同时可以提供准确的测试结果,被广泛应用于航空航天、核能、石化、电力等行业。
无损检测方法包括超声波检测、磁粉检测、渗透检测、射线检测等。
其中,超声波检测是最常用的一种方法,它利用高频声波在材料中传播的原理,通过接收到的回波信号来判断材料的内部缺陷。
磁粉检测则是利用磁粉液在磁场中的行为,来检测材料表面或局部的缺陷。
渗透检测是将渗透剂涂在材料表面,然后用显色剂显现出裂纹等缺陷。
射线检测则通过利用射线的穿透性来检测材料内部的缺陷。
无损检测设备的性能检验流程包括以下几个步骤:第一步是设备检查。
要确保检测设备的各个部件正常工作,没有损坏或故障。
检查设备的电源、传感器、显示屏等部件,确保它们的功能正常。
第二步是设备校准。
要对设备进行校准,以确保它的测试结果准确可靠。
校准的方法可以根据具体设备的要求进行,通常涉及到调整设备的灵敏度、校准标准样品等。
第三步是测试准备。
在进行无损检测之前,需要对要测试的材料进行准备工作。
这包括清洁材料表面、涂覆液体或涂料等,以便更好地检测缺陷。
第四步是测试操作。
根据不同的无损检测方法,进行相应的测试操作。
例如,对于超声波检测,需要设置传感器的位置和方向,并对回波信号进行分析解读。
第五步是测试评估。
根据测试结果,对材料进行评估,判断是否存在缺陷或性能问题。
评估的标准可以根据行业标准或相关规范来确定。
无损检测的相关标准是确保无损检测结果可靠的重要依据。
例如,超声波检测的标准是GB/T 11144-2008《金属材料超声波检测技术通则》、磁粉检测的标准是GB/T 9445-2017《用磁粉检测钢铁零件缺陷的一般规定》等。
这些标准规定了测试方法、设备性能要求、测试结果的评估等内容,确保了无损检测的准确性和可靠性。
总之,无损检测是一种非破坏性的检测方法,可以用于检测材料和结构的缺陷或性能问题。
无损检测标准简介

EJ/T1039- EJ/T1039-96 标准介绍
核电厂核岛机械设备无损检验规范 第一篇 超声检验 第二篇 射线检验 第三篇 液体渗透检验 第四篇 磁粉检验 第五篇 管材制品涡流检验 其它检验(目视和泄漏) 第六篇 其它检验(目视和泄漏)
EJ/T1041- EJ/T1041-96 标准介绍
无损检测标准简介
标准《 一、美国ASME标准《锅炉及压力容器规范》 美国ASME标准 锅炉及压力容器规范》 ASME规范总共11卷 规范总共11 ASME规范总共11卷 第 I卷 动力锅炉 II卷 第II卷 材料技术条件 III卷 核动力装置设备NCA NCA分卷 第III卷 核动力装置设备NCA分卷 第IV 卷 采暖锅炉
第V 卷 VI卷 第VI卷 VII卷 第VII卷 VIII卷 第VIII卷 IX卷 第IX卷 第X 卷 第XI卷 XI卷
无损检测 采暖锅炉维护和运行的推荐规程 动力锅炉维护的推荐规程 压力容器 焊接及钎焊评定 玻璃纤维增强塑料压力容器 核动力装置设备在役检测规程
ቤተ መጻሕፍቲ ባይዱ
RCCRCC-M标准介绍
RCC二、法国 RCC-M标准 《压水堆核电站核岛机械部件设计建造规则 》 现行的RCC RCC现行的RCC-M在我国有翻译本共五卷 第一卷 核岛机械部件 材料(M (M卷 第二卷 材料(M卷) 检测方法(MC (MC卷 第三卷 检测方法(MC卷) 焊接(S (S卷 第四卷 焊接(S卷) 第五卷 制造
- 1、下载文档前请自行甄别文档内容的完整性,平台不提供额外的编辑、内容补充、找答案等附加服务。
- 2、"仅部分预览"的文档,不可在线预览部分如存在完整性等问题,可反馈申请退款(可完整预览的文档不适用该条件!)。
- 3、如文档侵犯您的权益,请联系客服反馈,我们会尽快为您处理(人工客服工作时间:9:00-18:30)。
缺陷的定量
当量法(试块比较法):将所发现的缺陷与对比试块中规则 形状的人工反射体在同样检测条件下比较,如两者埋藏深 度及反射波高均相同则该反射体的面积既为缺陷当量值
当量曲线法(DGS) 计算法 测长法: 相对灵敏度、绝对灵敏度 距离-波幅曲线(DAC)
无损检测基本知识及相关标 准简介
第一部分 超声波检测
优点与局限性
没有任何一种无损检测方法是万能的。每种方法都有它 的优点和局限性。问题的关键在于选择一种解决检测问 题的最有效方法。当决定超声波检验是否为最合适的方 法时,需要考虑以下一些因素: 被检件的几何形状。 材料类型。 材料厚度。 材料的加工方法——铸造锻造等。 要检测不连续的类型。 要检测的不连续的最小尺寸。 不连续的位置——表面开口型的,还是内部的 。 不连续的方位(在选择方法时尤为重要)。 检测区域的可达性。 表面条件。 所要求的检测记录类型。
干粉法也采用银灰色的铁粉。直径为10~130μm的空心球 粉是铁、铬、铝的复合氧化物,可以在400摄氏度以下的 温度范围内用于干粉法。****焊缝清根
荧光磁粉是以磁性氧化铁粉、工业纯铁粉、或羰基铁粉等 为核心,外面包覆一层荧光染料所致成的,可明显提高磁 痕的可见度和对比度。
磁粉的特性
磁性 磁粉应该有较高的磁导率以利于被漏磁场磁化和吸 引以形成磁痕;同时还应该具有较低的剩磁和矫顽力以利 于磁粉的分散及移动;
置反映了声波传播的时间即声传播的距离。反射幅度取决于接受的声能大小 ,声能的大小又与缺陷反射面的形状尺寸有关,因此根据反射波的有无、位 置、幅度高低等信息,可以判断缺陷的有无,以及定位、定量和评价缺陷, 这就是反射法探伤的基本原理。
A型脉冲超声波探伤仪一般工作原理
A型显示——主要显示反射面(缺陷)在试件中的埋藏深度及反射信号 的幅度(缺陷大小)
试块的分类: 按试块用途分类:标准试块、对比试块 按人工反射体分类: 平底孔、横孔试块、槽 形试块
对比试块用与试件声性能相同或相近的材料制作
探伤灵敏度的调节
1. 试块调整法 2. 工件底波调整法
波高法 当量计算法
探伤耦合剂
耦合剂的作用:通过在探头和试件之间涂敷液体 (耦合剂)以排除空气隙实现声能的传递。
磁写:由磁场畸变而产生的磁痕显示叫磁写。已磁化且保 留有很大剩磁的待做剩磁法探伤的工件,探伤前与其他铁 磁性工件相接触,如划碰等,则在相应部位吸引磁粉,产 生松散的模糊不清的伪缺陷磁痕即磁写。***退磁消失
操作不当引起的伪缺陷磁痕显示:如工件表面清理不良,残 留油污或粘附纤维以及多余的磁粉或磁悬液滞留工件表面 ,易形成显示。*****认真清理表面,重做可消失。
可以用肉眼或3倍放大镜观察。
磁痕分类
线性缺陷磁痕(LM):长度与宽度之比大于等于3的缺陷。 非线性缺陷磁痕(SM):长度与宽度之比和小于3的缺陷
。 可叠加磁痕显示(AM):
线性:两个磁痕的间距小于其中最小磁痕的长度L ; 非线性:磁痕间距小于2mm且最少为三个磁痕。 可叠加缺陷可计为一个缺陷,其长度等于缺陷的总长 度L, L为第一个缺陷起点到最后一个缺陷终点之间的距离,例 下图: L=l1+l2+l3+l4+l5
表1 缺陷特点和相应的磁痕类型
表2 磁粉探伤的要求等级-单个非线性缺陷
表3 磁粉探伤的严重程度-线性和线列磁痕
表4:线形(LM)和线列(AM)磁痕
磁化工件绝大多数是用电流产生的磁场进行的,因此,大 的工件往往用很大电流。磁化后一些较大剩磁的工件还要 进行退磁。
磁粉检测方法
纵向磁化(线圈法)
纵向磁化(磁轭法)
周向磁化(周向通电法)
周向磁化(触头法)
周向磁化(中心导体法)
复合磁化
包括交叉磁轭法(见下图)和交叉线圈法等多 种方法。
脉冲反射法
单晶探头构造示意图
单晶直探头:用于锻件、铸件、钢板检测 单晶斜探头:用于检测焊缝
频率范围:0.5-10MHz,常用1-5MHz频率越高发现小缺陷的能力越强但 杂波影响也越大
双晶探头构造示意
双晶探头用于检测近表面缺陷 常用于堆焊层检测
试块
试块的作用: 确定探伤灵敏度 测试仪器和探头性能 调整扫描速度 评定缺陷大小
超声波检测成为对较小而不致密不连续的一 种理想定位方法,需要满足一下假设:
声能的发射角将对反射体的方位产生良好的效应; 不连续尺寸和材料晶粒结构之间的关系允许获得一个可接
受的信噪比; 表面条件适合扫查。不良的扫查表面不仅需要更粘的耦合
剂,而且还可能要采用较低的频率。这样就可能达不到所 需的必要分辨率。
尺寸 干粉粒度5~150μm范围的均匀混合物为宜 湿粉粒度1~10μm;
形状 同球形分相比,细长形粉易于极化更容易显示缺陷 ,但如果完全由细长形粉组成则容易结块、流动性不好 难以均匀散布而影响灵敏度,所以理想的磁粉应有足够的 球形粉与高比例的细长粉组成;
缺陷状况的影响
缺陷性质的影响 缺陷种类很多,如裂纹、白点、气孔、重皮、夹渣等,这 些缺陷由于其介质磁导率不同,进而缺陷产生的漏磁场也 不同,这就造成了缺陷磁痕的显示能力不同。
JB/T4730.4-2005 压力容器磁粉验收标准
BS EN1369简介
英国标准,由欧洲标准委员会(CEN)1996年10月26日批准发 行。
适用于铁磁性铸铁和铸钢件的磁粉探伤。 其给出了根据缺陷性质、区域尺寸所规定的各质量等级的验
收标准。 表面要求:
进行检测的表面应洁净无稀油、油脂、砂、氧化皮、铸造 和涂漆过程中残留的有可能影响正确操作及探伤结果解释的 其他任何污染物。 检查条件:
超声检测的优点如下:
检测可以从一个表面上完成。 能够检测到较小的不连续。 可充分的控制检测变量。 采用不同的波型可获得不同的方法。 对于适合的设备可以进行高温检测。 可检测较厚或较长的工件。 埋藏构件的检测(如轴承箱内的主轴等)。 对表面和内部不连续可精确定位。 可提供不连续的深度信息。 可检测表面和近表面的不连续。 采用信号电子门和报警系统后可实现高速检测。 生产线上的“Go/No-Go”检测。 可重复检测。 检测设备轻,携带方便。 不需要设置人员的隔离区。 不需要有放射源那样的特殊许可证。 最少量的易耗品
超声波的基本原理
1.声波与超声波 机械振动在弹性介质中的传播称为声波。声波可划分为次声波(f<20Hz)、
可闻声波(20Hz < f<20kHz)和超声波(f>20kHz) 2.超声波传播特性 直线性: 指向性: 反射、折射与波型(纵波、横波、表面波): 能量大: 穿透能力强: 3.脉冲反射法超声检验的基本原理 **压电效应** 仪器的时基线线与扫描电压有关,扫描电压与时间成正比,因此发射波的位
磁粉检测优点
可发现表面缺陷,如裂纹、夹杂、发纹、白点、折叠、冷 隔和疏松等缺陷,缺陷形状、大小和位置显示直观一目了 然;
对于工件表面的细小缺陷也能检查出来,有较高检测灵敏 度;
采用合适磁化工艺,能检测到工件所有表面; 同其它方法相比较,磁粉检测工艺简单,速度较快,检测
费用也比较低廉。
磁粉检测缺点
电极或磁极处伪缺陷磁痕显示,这种显示特征是分散的沿 金属流线方向分布的粗壮密集而又清晰的显示。
工件局部冷作硬化处产生的伪缺陷磁痕显示: 工件冷作加 工如弯曲、打磨、抛光、低温矫正变形、锤击等,产生局 部硬化,组织成分发生变化,产生局部应力,形成短而宽 的模糊不清的伪缺陷磁痕。****工件退火后,为磁痕消失
磁悬液浓度过大施加方式不当,多余磁粉吹除不当等,也 能形成伪缺陷磁痕显示。
应力集中处产生的伪缺陷磁痕显示: 工件在加工以及使用 过程中由于温度、载荷等原因产生局部应力过大,磁化时 这些部位也能产生漏磁通,形成多而松散的不清晰的伪缺 陷磁痕显示。
缺陷磁痕的分类
线形缺陷磁痕:长度与宽度之比大于3的缺陷。如裂纹、 折叠、分层等缺陷。
圆形缺陷磁痕:长度与宽度之比等于和小于3的缺陷。 纵向缺陷磁痕:缺陷的长轴方向与工件轴线或母线夹角小
于30度的缺陷。 横向缺陷磁痕:缺陷的长轴方向与工件轴线或母线夹角大
于或等于30度的缺陷。 分散缺陷磁痕:在一定区域内同时存在几个缺陷磁痕。
常用标准简介
BS EN1369
铸件磁粉验收标准
DIN EN 10228-1 锻钢件磁粉探伤验收标准
DGS曲线
DAC曲线
分层缺陷的典型图形
底波消失的典型特征
各种锻件的检测方向和检测面
第二部分 磁粉检测
磁粉探伤的原理
1.磁粉探伤同涡流一样是电磁探伤方法,以电磁理
论为基础。
2. 漏磁场原理
工件表面磁化时,如果在其表面或近表面有能遮 挡其磁力线的缺陷存在,则在这部分表面空间将 产生漏磁场,而且在缺陷的两侧会出现磁极。此 时如果在此处喷洒具有一定分散性的干磁粉或湿 磁粉,磁粉颗粒在被空间磁场磁化后就变成了带 有磁极的小磁铁。同极相斥、异极相吸,磁粉就 会聚集在缺陷上(磁粉堆积)。 **这种显示的磁痕容易识别。
工件表面粗糙度及机械损伤以及表面附着物包括镀层、涂 层、氧化皮、锈蚀、污垢等对探伤结果均有影响。
表面粗糙不平尤其是附着物和机械损伤影响磁场强度及分 布。当附着物较厚时,能掩盖缺陷,增大缺陷与被检表面 的距离,降低漏磁场强度,减小对磁粉的吸引力,影响磁 粉流动,妨碍显示,降低探伤灵敏度,容易造成漏检。
缺陷形状和大小的影响 与磁场方向垂直的线、面状缺陷比气孔等圆形缺陷产生的 漏磁场强,易形成磁痕显示,检测灵敏度高。 同等宽度的表面缺陷,在一定范围内漏磁场强度与缺陷的 高度成正比,即高度越大,漏磁场越强,检测灵敏度越高 。
缺陷方位的影响 缺陷的断面形状、方向及与表面的距离等都影响磁粉探伤 的结果。
工件形状和尺寸的影响
工件形状规则均与,易选择和制定磁化规范。而对于形状 不规则的工件,磁化产生的磁场也不均匀,灵敏度也不一 样,检测效果也规范;