防静电铝箔袋信息五大弊端
14.铝箔常见缺陷
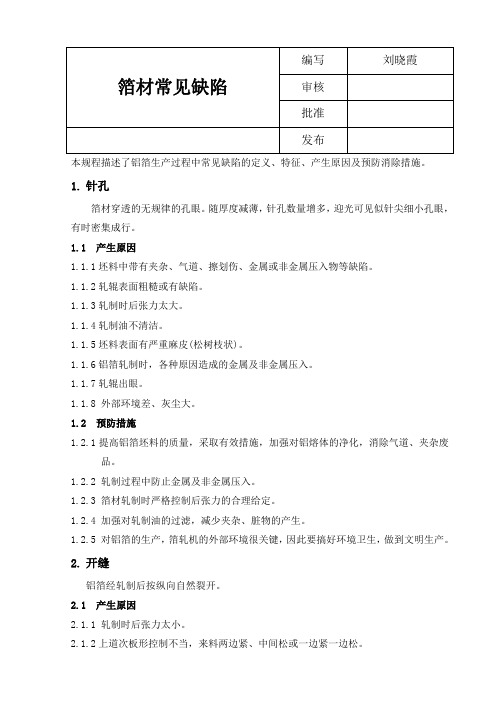
本规程描述了铝箔生产过程中常见缺陷的定义、特征、产生原因及预防消除措施。
1.针孔箔材穿透的无规律的孔眼。
随厚度减薄,针孔数量增多,迎光可见似针尖细小孔眼,有时密集成行。
1.1 产生原因1.1.1坯料中带有夹杂、气道、擦划伤、金属或非金属压入物等缺陷。
1.1.2轧辊表面粗糙或有缺陷。
1.1.3轧制时后张力太大。
1.1.4轧制油不清洁。
1.1.5坯料表面有严重麻皮(松树枝状)。
1.1.6铝箔轧制时,各种原因造成的金属及非金属压入。
1.1.7轧辊出眼。
1.1.8 外部环境差、灰尘大。
1.2 预防措施1.2.1提高铝箔坯料的质量,采取有效措施,加强对铝熔体的净化,消除气道、夹杂废品。
1.2.2 轧制过程中防止金属及非金属压入。
1.2.3 箔材轧制时严格控制后张力的合理给定。
1.2.4 加强对轧制油的过滤,减少夹杂、脏物的产生。
1.2.5 对铝箔的生产,箔轧机的外部环境很关键,因此要搞好环境卫生,做到文明生产。
2.开缝铝箔经轧制后按纵向自然裂开。
2.1 产生原因2.1.1 轧制时后张力太小。
2.1.2上道次板形控制不当,来料两边紧、中间松或一边紧一边松。
2.1.3辊型控制不当。
2.1.4双合滴油过大或不均匀。
2.2 预防措施2.2.1 轧制时,在允许的范围内尽量增大后张力。
2.2.2 控制来料的板形,使其平整。
2.2.3 轧制时合理的控制冷却润滑油的喷射量和位置。
2.2.4 轧辊磨削严格按规定的参数执行。
2.2.5 双合滴油时,使滴油嘴畅通并控制滴油量。
3. 松树枝状花纹(麻皮)箔材表面呈现的有规律的松树枝状花纹。
表面有明显的色差,但较光滑。
3.1产生原因3.1.1轧制时道次压下量过大,金属在轧辊间由于摩擦力大,流动速度慢,产生滑移。
3.1.2辊型不好,温度不均。
3.1.3轧辊粗糙度不均。
3.1.4由于添加剂含量不够等原因造成油膜强度不够。
3.1.5 轧辊局部温度过高。
3.2 预防措施3.2.1 轧制时适当控制道次压下量。
铝箔加工缺陷及措施
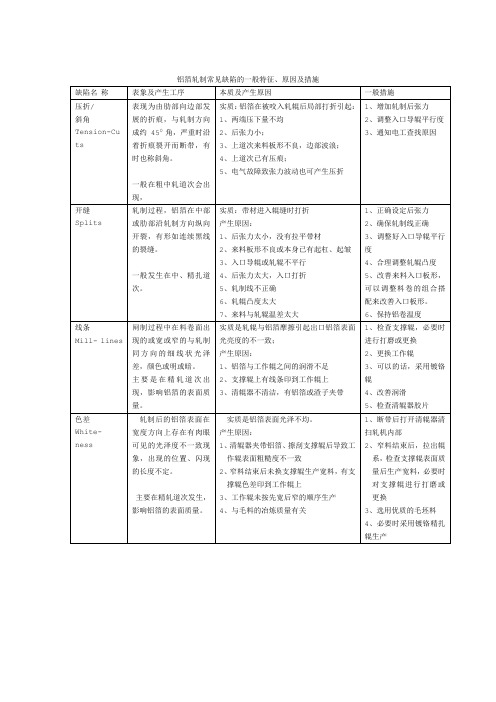
铝箔轧制常见缺陷的一般特征、原因及措施在轧辊的表面与机体中形成高微裂纹的铬层。
这种高高微裂纹的网状结构有利于轧制油吸附在轧辊表面,以便润滑。
网状结构的铬层可以承受轧制力高达2000吨以上的的压力。
以下是其与传统镀铬的金相结构图的比较对照表:轧辊镀铬的铬层硬度是随着镀铬的技术条件变化而变化的。
科德工作辊服务集团的镀铬层硬度通过其技术的创新可以达到900-1100VICKERS PN。
这么高的硬度值就是所谓的“镀硬铬”技术。
通过这样的硬度值来增加轧辊的耐磨性能。
它的硬度要比通常的铸铁或者热处理的锻钢工作辊的硬度还要高。
镀铬层的摩擦系数更低,以下是一些金属表面的摩擦系数表:铝箔轧辊的镀铬对铝箔的生产带来了较好的效果。
工作辊—所有机架(粗轧→中轧)冷轧镀铬辊的所有绩效在铝箔轧辊上都能体现出来,此外,还具备以下优点:(1)、能够成倍减缓随通过量轧制速度下降的趋势从而获得稳定的轧制速度;(2)、能够从窄到宽的变规格轧制;(3)、大幅度改善润滑状态减少了不明断带;(4)、获得稳定一致的板型和表面质量。
在生产10—30um的箔材中,由于支撑辊的原因常常损坏工作辊。
而对支撑辊的镀铬可以改善工作辊的损伤,减少氧化物的产生和线条的产生。
在铝箔精轧中,使用镀铬工作辊可以获得更稳定均匀的表面质量,延缓线条产生。
抑制原料带来色差的倾向。
分切常见缺陷及调整措施工艺参数与铝箔质量产量的关系COMALCOFOIL DIVISIONDEFECT CATALOGUEDanyang Training VisitMay 1992Comalco Aluminium Ltd SMP 7479.00Yennora Words Page 1 of xxxFoil Division Date 9.9.91Standard Metallurgical Practices Prepared by: C. Cleary Foil Division Defect CatalogueScopeThis S.M.P. is for all foil personnel and covers the description and classification of various defects found in the Foil Division. It describes defects which occur during rolling, slitting and annealing.This catalogue describes the defect, why it occurs and when possible, tells you how to eliminate it.The numbering system follows the Comalco Claim System used site wide for categorizing claims from external customers (see page 2 and 3 for a full listing).This S.M.P. covers the following defects:0.1 Stickiness0.1.1 Orange Peel0.1.2 Exploded Areas0.2 Wettability1.6.1 Hot Spots1.9 Tension Cuts2.1 Water Stain2.2.1 Herringbone2.2.2 Line of Holes2.2.3 Roll Holes2.2.4 Chatter2.2.5 Mill Lines2.2.6 Bruised coil2.2.7 Indents2.2.8 Splits2.5.1 Dross2.5.2 Staining2.6.1 Chicken Tracks2.7 Broken Matte2.7.1 Streaky Matte6.3 Step Outs6.4 Telescoping6.5 Out of Round6.7.1 Edge Cracks6.7.2 Laminations6.10 BridgingFULL LISTING OF SITE WIDE DEFECTS0.0 Annealing 0.1 Stickiness 0.1.1 Orange Peel 0.1.2 Exploded Areas 0.2 Wettability1.0 Dimensional 1.1 Gauge1.2 Width1.3 Lateral Bow1.4 Length1.6 Flatness 1.6.1 Hot Spots1.6.2 Creasing1.7 Edge Burr1.8 Mass1.9 Tension Crease2.0 Surface 2.1 Water Stain2.2 Metal Surface 2.2.1 Herringbone2.2.2 Line of Holes2.2.3 Roll Holes2.2.4 Chatter2.2.5 Mill Lines2.2.6 Bruised Coil2.2.7 Indents2.2.8 Splits2.3 Surface Condition2.4 Applied Coating2.5 Surface Contamination 2.5.1 Dross2.5.2 Staining2.6 Blade Marks 2.6.1 Chicken Tracking 2.7 Broken Matte 2.7.1 Streaky Matt3.0 Metallurgy 3.1 Alloy3.2 Mechanical Properties3.3 Earing3.4 Inclusion3.5 Failure To Form Cans4.0 Document 4.1 Specification4.2 Planning4.3 Sales5.0 Packaging 5.15.2 Identification6.0 Coil Cond n 6.1 Loose Wraps6.2 Broken Welds6.3 Step Outs6.4 Telescope6.5 Out of Round6.6 Coil Size6.7 Broken Edge 6.7.1 Edge Cracks 6.7.2 Laminations 6.8 Edge Damage6.9 Handling Damage6.10 Bridging7.0 Transport 7.1 Seafreight7.2 Road/Rail8.0 Acc Reject9.0 No Defect 9.1 BU/CP Wrecks0.1 StickinessWhat is stickiness?Stickiness is a measure of how difficult it is to pull a single layer of foil from the coil. This defect can cause problems, especially when it occurs in light gauge foils such as insulation and flexible packaging metal.When does stickiness occur?When the annealing process is out of specification or the wrong annealing cycle has been used for a particular product if the metal is kept at the incorrect temperature.Why does stickiness occur?* incorrect conditions in the annealing furnace:-any residual rolling oil left from the rolling process can polymerise and form weak bonds with the meta.What can you do about it?* monitor the annealing cycle closely and watch the:-heat up rate-soak time-temperature-cool down rate;* report any furnace problems-e.g. burner failure;* keep excess coolant carryover to a minimum.STICKY COILIT REQUIRES FORCE TO PULL THESINGLE SHEET FROM THE COIL FREE UNWIND COILTHE METAL SHEET EASILY FALLS AWAYFROM THE COIL UNDER ITS OWN WEIGHT0.1.1 Orange Peel EffectWhat is orange peel effect?Orange peel effect is a change in the surface of the metal. It becomes mottled, like the surface of an orange peel. This defect is always associated with high stickiness levels (see 0.1).When does orange peel effect occur?This defect mainly occurs on medium gauge coils (30 to 70 microns) and of a soft alloy and O Temper.Why does orange peel effect occur?* too much coolant left on the coil:-during annealing, the excess coolant between the foil layers forms a vapour.-the pressure from the vapour deforms the foil in localized pockets.What can you do about it?Minimize the amount of coolant left on the coil:* always use the splash guard when rolling the final. pass on No. 1 foil mill; * make sure the air wiper system is working properly;* check the amount of residual coolant on the metal when it is on the slitter -if the level is high, make a note of this on the lot ticket.0.1.2 Exploded AreasWhat are exploded areas?Exploded areas are small blister-like bubbles that occur between layers of light gauge foil after it has been annealed. You will find this defect mainly on annealed household foil coil.When do exploded areas occur?When light gauge foil is annealed.Why do exploded areas occur?* too much coolant left on the coil:-as the foil is annealed, the excess coolant between the foil layers forms a vapour-the foil is deformed by pressure from the vapour in localized pockets, this causes an exploded blistered effect.* incorrect anneal practice-too high an annealing temperature will also cause exploded areas.What can you do about them?* keep the amount of the coolant left on the coil to a minimum: -make sure the mill air wiper system is working properly,-check the amount of residual coolant on the metal when it is on the slitter.Make a note on the lot ticket if the level is high.* make sure the metal is annealed correctly and check:-heat up rate-soak time-temperature-cool down rate0.2 WettabilityWhat is wettability?Wettability is a measure of the amount of rolling lubricant left on the foil strip after annealing. If there is too much, it can interfere when plastics and inks are applied to the metal at the customers plant.When does wettability occur?When there is too much rolling lubricant left on the metal after it has been anneal.Why does wettability occur?* excess coolant carryover on the mill;* incorrect conditions in the annealing furnace.Why can you do about it?* monitor the annealing cycle closely and watch the:-heat up rate-soak time-temperature-cool down rate;* report any furnace problems-e.g. burner failure;* keep excess coolant carryover to a minimum.A GRADE WETTABILITYWHEN WATER IS APPLIED TO A SHEET OF FOILIT STAYS ON THE FOIL e.g. IT WETS THE SURFACEB BRADE WETTABILITYWHEN WATER IS APPLIED TO A SHEET OF FOILIT DOES NOT STAY ON THE FOIL SURFACE1.6.1 Hot SpotsWhat are hot spots?Hot spots are a continuous buckle (or belly) anywhere on the width of the exit strip. Provided the exit tension is not too high, hot spots are very easy to see when you are rolling. The buckled area is a lower gauge and longer than the rest of the strip. As a result it ‘puckers’.When do hot spots occur?When excess heat builds up in a section of a work roll or backup roll, the roll expands more in this area. The metal which comes into contact with this area is rolled to a lower gauge than the rest of the strip.Why do hot spots occur?Excess heat in a localized section of a work roll or backup roll is caused by: * foreign objects rubbing against the roll;* too mach wiper pressure in one area of the roll;* a blocked coolant spray;* coolant sprays which are not correctly aligned;* too much thermal crown;* local hard or soft spots on the roll;* disturbed oxide layer in the area of the buckle.What can you do about them?* check for foreign objects and remove any you find;* check the pressure on the wiper and alter it if uneven or too high;* unblocked any blocked coolant sprays;* make sure the coolant sprays are correctly aligned;* check the coolant pressure and increase it if necessary;* change the work rolls.Hot Spot \ Shape Defect Description1.9 Tension CutsWhat are tension cuts?Tension cuts are stretched bands of broken metal on the edges of the strip. They point towards the centre of the strip and spread out as they reach the edges. This defect is very easy to identify during rolling.When do tension cuts occur?When the strip wrinkles or folds over as it enters the mill bite.Why do tension cuts occur?* if the unwind tension is too low to hold the strip flat as it enters the work roll bite, the strip edges can wavy and wrinkle;* if the bridle is uneven or out of alignment, it may not hold the strip flat.What can you do about them?* increase the unwind tension until you can’t see any more fractures;* make sure the bridle is correctly aligned and the strip is flat as it enters the mill bite.2.1 Water stainsWhat are water stains?Water stains are a white or grey discolouration on the surface of the metal. Water reacts with the metal, causing surface oxidation and the formation of a metal oxide. This oxide stain is harder than the rest of the strip. When it passes through the mill bite, it can cause the strip to break.When do water stains occur?When the metal comes into contact with water.Why do water stains occur?* direct exposure to water;* condensation caused by rapid temperature changes in the metal:* when water is trapped between two closely packed metal surfaces there is no air circulating and the metal surface reacts with the water, this is known as surface oxidation.What can you do about them?* keep water away from the aluminium at all time- store away from roof leaks or keep the metal covered- keep the metal off the floor;* make the wooden boxes have low moisture content when you pack coils in them; * make sure the coils are cool before you pack them;* cover coils when transporting them from No. 1 to No. 2 mill on an overcast day.How to determine where the water staining occurredUsing a Scanning Electron Microscope, a good understanding of where the staining occurred can be achieved. With this type of microscope the stain can be studied, and other elements other than Aluminium can be detected. These will give you a rough estimate of the nature of the stain.* If Sodium or Chlorine are detected, then the stain is probably from sea water. * If Sulphur is detected, then the stain could be caused by acid rain.* If Calcium or Iron is detected, then the water source could possibly be unclean tap water.These generalizations can only be used as a rough guide when determining where the water staining has occurred..01 5.12 KeV Typical SEM Trace for a salt water caused “Waterstain”.2.2.1 HerringboneWhat is Herringbone?Herringbone is a surface marking along the strip which resembles a string of corpo ral’s stripes or the backbone of a fish.When does herringbone occur?There are a number of possible reasons:* the coolant may not be lubricating the strip well enough under the extreme pressure of the mill bite;* the strip may have a poor shape either from a previous pass or the present one; * the gauge reduction may be too great;* an earlier annealing treatment may have been missed* work roll finish may be incorrectly ground.What can you do about it?Herringbone is probably not the fault of your rolling technique, so you should follow or report on these matters:* check the composition of the coolant to ensure it has the correct levels of additives to give lubrication. The Rolling Superintendent or Foil Metallurgist keeps records of coolant additive levels;* check the previous rolling and annealing history of the coil from the Lot Ticket - report any ways in which this differs from the process schedule;* check the Roll Grind Requisition form, ensuring that the rolls have had the correct grinding performed on them.2.2.2 Lines of HolesWhat is lines of holes?Lines of holes are a continuous line of little holes in the metal. It varies in severity and can sometimes occur consistently throughout a coil. Lines of holes often cause strip break during the last single and the final doubling passes.When does lines of holes occur?This defect occurs when the metal has been scratched at any stage of processing or when a source of pick-up is introduced to the roll bite.Why do lines of holes occur?When the surface of the strip has been broken, by:* mechanical failure, for example- pulling the strip over a seized roll- a scratch on the work roll surface;* careless handling of the metal;* the work rolls have been ground with no relief on the ends. This results in small pieces of work roll surface breaking off and being forced through the bite.What can you do about it?Try to protect the metal throughout the process:* check and maintain a high level of cleanliness on the mill regularly;* when you detect lines of holes, the coil should be isolated and put on hold. The coil should not be processed any further;* check the work rolls for signs of spoiling.2.2.3 Roll HolesWhat are roll holes?Roll holes are small marks or holes that repeat at a regular interval along the metal strip. This defect is very difficult to see during rolling.When do roll holes occur?When a roll work become damaged and the damaged portion imprints a mark onto the metal surface.Why do roll holes occur?The work rolls can be damaged by a number of things:* grit;* dirt;* dust;* an inclusion in the strip.What can you do about them?* make sure the mill is cleaned thoroughly- after a PM- after a strip break;* make sure the metal stays off the ground;* wear clean gloves when you handle the metal;* remove one wrap from the feed coil if it has been standing for a long time; * if the holes are repeating at an interval of about 1 metre when you measure them along the length of the strip, then the mark is caused by your work rolls - change the rolls;* if the holes are about 2 metres apart, they were caused before you received the coil- there is nothing you can do about them.2.2.4 ChatterWhat is chatter?Chatter is evenly spaced, two tone lines which run across the width of the strip. If you could see the edge of the strip magnified, it would look similar to the edge of a piece of corrugated iron. You will hear chatter occurring before see it.When does chatter occur?Chatter often occurs during mill acceleration and deceleration, for short periods only. Only when this occurs at longer periods of times does the defect become a problem.Why does it occur?Chatter is caused by machine resonance. Machine resonance can occur under the following condition:* the coolant is out of specification;* the feed strip is a hard alloy;* the pass line is incorrect;* the drive transfer box is worn;* the drive couplings are worn.What can you do about it?* if you want to finish the coil, try altering the mill speed and unwind tension,then stop rolling and look for the problem;* make sure the coolant is within specification at all times - if it is not, stop the mill until you can correct it;* change the product or program until someone alters the mill; * if the pass line is wrong, check the mill shims;* change the work rolls.THE LINES ON THE STRIP IF MAGNIFIEDWOULD SHOW VARIATIONS OF GAUGE WHICH WOULD GIVETHE CROSS SECTION A CORRUGATED EFFECT AS SHOWN ABOVE 2.2.5 Mill LinesWhat are mill lines?Mill lines are very narrow stripes which run along the strip in the rolling direction. To see them clearly, you need to straight down onto the strip.When do mill lines occur?When the work rolls or backup rolls are damaged.Why do mill lines occur?There are a number of reasons:* there is a scratch on the work roll;* the oxide layer on the work roll is uneven;* there are lines on the work roll caused by the damaged backup roll - the backup roll can be damaged by a worn wiper.What can you do about them?* if the defect is present in the following products, you must do a roll change - R No. 62715 Leigh Mardon .040mm x 592mm- R No. 62780 Leigh Mardon .040mm x 674mm- R No. 62576 Leigh Mardon .050mm x 675mm- R No. 62303 Leigh Mardon .040mm x 643mm* if there are lines on the backup roll, there is no point in changing the work rolls because the damaged backup roll will mark the new rolls- remove the mark from the backup roll with emery paper or a fine grinding wheel - if you can not remove the lines, change the backup roll;* if only the work roll is damaged, change the work rolls.2.2.6 Bruised CoilWhat is a bruised coil?A bruised coil is an area of discolouration which repeats along the metal strip at regular interval.When does a bruised coil occur?When a work roll has an impact placed upon it. The bruise can occur at any upstream process and can manifest itself upon further reductions as a discolouration on the metal or shape problems with the coil.Why does a bruised coil occur?* when the tail of a coil passes through the roll bite and damages the work rolls. This mark is then transferred onto the strip.- this occurs most often on heavier gauges and when you roll hard alloys (e.g.3003 and 3004 alloys).What can you do about it?* when you are rolling a breakdown pass, stop the mill before the tail of the strip passes through the mill bite;* cut the tail in an arc, reduce the load and pull the tail through;* when programming semi-rigid container metal on No. 1 Mill, always programme 8001 and other soft alloys before 3003 and 3004 alloys. The 3003 and 3004 alloys are harder than the 8001 alloy and are therefore less susceptible to the effect of bruising the work rolls.2.2.7 IndentsWhat are indents?Indents are small depressions that appear on the surface of the metal as the coil unwinds.When do indents occur?This defect mainly occurs on medium gauge coils (30 to 70 microns). It is most obvious on O-Temper metal.Why do indents occur?* small particles of dust, dirt and grit get trapped between the metal layers as the coil is slit- the problem gets worse when the metal is annealed because the metal is softer and more prone to mark.What can you do about them?* clean the slitter thoroughly before you use it- this is especially important if the slitter has not been used for a while; * keep the metal off the floor;* handle the metal with clean gloves;* when slitting metal on the 755 slitter always use rotary blades, as razer blades tend to produce a larger amount of swarf which then deposits on the metal strip.2.2.8 SplitsWhat are splits?Splits are very thin creases which have been rolled into the metal. These creases weaken the metal and will easily break apart during rolling. When you are rolling, a split looks like a continuous black line, usually on the centre of the rewinding coil, but sometimes on other side. Take care you don’t confuse this defect with mill lines which look very similar.When do splits occur?When you roll a fold or crease into the strip.Why do splits occur?There are a number of reasons:* incorrect pass line- if the pass line is wrong, the strip will not be level when it enters the mill bite;* the unwind tension is too high, cause a crease in the unwinding strip - this occurs mainly in light gauge strips;* the entry bridle is not correctly aligned.* the backup roll has recently been changed and the work roll camber has not been change to accommodate this change.* the work roll finish may be incorrectly ground.What can you do about them?* carry out a pass line check whenever you change the top backup roll;* make sure the pass line is correct;* make sure the unwind tension is correct;* make sure the correct shims are inserted at every work roll change;* check that the entry bridle is correctly aligned.* ensure that the correct work roll camber is used after the backup rolls have been change.2.5.1 DrossWhat is dross?Dross is a mark or hole in the strip. In very severe cases, it ban lead to web break.When does dross occur?True dross is very rare. It occurs when the metal has not been sufficiently drossed off during casting. Many other defects are mistakenly reported as dross.Why does dross occur?* oxidational impurities form in the metal during casting and hard oxide particlesbecome embedded in the aluminium;* during rolling the oxide particles do not deform as readily as the aluminium and can damage the work rolls;* this leads to marks and holes in the strip and finer gauge strips may disintegrate.What can you do about it?* there is nothing you can do about true dross because the defect is already in the metal before you receive it;* by keeping the metal clean, you can avoid defects which show similar characteristics, but are not in reality dross.2.5.2 StainingWhat is staining?Staining is a black or brown mark which appears or the coil after annealing.When does staining occur?When there are organic compounds left on the strip during annealing, they burn on and cause staining.Why does staining occur?Staining can occur on different parts of the coil:* on the side- if the staining compound was deposited during rolling;* on the side, but only near a join- if the compound was left when the coil was being joined or welded;* on the outside wraps- if the compound came into contact with the metal inside the furnace;* if there is ‘wet lube’ on the furna ce tree when it enters the furnace, the lube evaporates, concentrates and burns on the coil- this could come from a side arm tree that has had container coils on it.What can you do about it?* make sure the coils do not have excess coolant left on them- use the splash guards during the final pass on No. 1 foil mill;* make sure the side arm trees do not have any wet lube on them before you place a coil on them for annealing;* make sure the mill air wiper system is working properly;* check that there is no tape or other foreign matter on the coil before you anneal it.* always ensure that furnace exhaust vents are working properly.2.6.1 Chicken trackingWhat is chicken tracking?Chicken tracking is a slit defect that looks like lines on the edge of a slit coil which radiate from the centre to the outside.When does chicken tracking occur?This defect is a result of slitter blade flutter.Why does chicken tracking occur?Slitter blade flutter can be caused by following:* a damaged female knife roll:* a loose knife;* badly shaped feed metal.What can you do about it?* make sure the knives are firm;* make sure the female knife roll is in good condition.2.7 Broken MatteWhat is broken matte?Broken matte are shiny spots scattered over the dull, matte side of the metal.When does broken matte occur?Broken matte occurs when you are doubling strips and the two strips weld together in spots. As the strips are separated, the welded areas break leaving shiny spots.Why does broken matte occur?There are a number of possible reasons:* not enough inter lap solvent used;* too much speed when rolling;* uneven roll grind;* the two entry strips have different surface textures;* in some alloys, broken matte can occur if the inter lap solvent has a higher lubrication capability than the coolant (e.g. alloy 1145).What can you about it?* make sure you use enough inter lap solvent;* make sure the mill speed is correct;* change the work rolls if you suspect the roll grind is mismatched.2.7.1 Streaky MatteWhat is streaky matte?Streaky matte is also known as no matte and is exactly as the name suggests, a section of the metal strip on the matte surface where there is no matte.When does streaky matte occur?When you are doubling two strips and the solvent application is not consistent you get varied lubrication characteristics in different areas of the strip.Why does streaky matte occur?* there is not adequate inter lap solvent being deposited across the whole strip of foil.What can you do about it?* use plenty of inter lap solvent;* ensure that none of the inter lap sprays have become blocked;* if you increase the mill speed during doubling, then ensure that the inter lap sprays are accordingly adjusted to a greater outflow.6.3 Step OutsWhat are step outs?Step outs are uneven wraps in the coil that have deviated from the normally smooth end face of the coil.When do step outs occur?When you alter variables such as steering or tension during rolling or slitting.Why do step outs occur?* when you alter variables such as steering or tension during rolling or slitting. What can you do about them?* if you need to change any variables when the metal is either being slit or rolled, then do so gradually and smoothly. Any quick changes could result in step outs.6.4 TelescopingWhat is telescoping?The wraps of the coil slip out sideways and result in a telescoped effect.When does telescoping occur?Telescoping generally occurs when there are steerage problems on the slitter or mill.Why does telescoping occur?* incorrect steerage on the slitter- because of badly shaped feed metal;* insufficient tension during rolling/slitting can result in a loose coil, that may slip to one side during coil handling.What can you do about it?* increase the ironing roll pressure on the side of the coil that the telescoping is steering away from;* increase the unwind tension on the side of the coil that the telescoping is steering towards.LATERAL MOVEMENT OF FOIL LAYERS RELATIVE TOEACH OTHER HAS CAUSED THE COIL TO GELESCOPE6.5 Out of RoundWhat is out of round?This term describes a coil which is not perfectly round. To measure the extent of the defect, find the maximum distance between the core and the outside diameter (shown by the bottom arrow in the diagram) and from this, take the minimum distance (shown by the top arrow in the diagram).maximum distance – minimum distance = extent of defectNote: this diagram has been exaggeratedNORMAL SLIT COILTELESCOPING OF SLIT COILWhen does out of round occur?Out of round generally occurs on insulation coils and wide flexible packaging coils.Why does out of round occur?* the bulk of the metal sags to the bottom of the coil during annealing - the cool down rate is particularly important, if the cooldown rate is too high it creates a thermal gradient in the coil. This defect is minised by using 152mm cores.What can you do about it?* make sure the cool down rate is within specification.6.7.1 Edge CracksWhat are edge cracks?Edge cracks are cracks or small splits along the edge of the strip. They are generally 0.2 to 0.3 mm long. Edge cracks are particularly a problem in hard alloys and can make it difficult, Sometimes impossible to roll the final pass.When do edge cracks occur?When the coolant composition, the pass schedule or the condition of the strip are out of specification.Why do edge cracks occur?There are a number of reasons:* too much friction during rolling;* the gauge reduction may be too great;* the edges of the strip may be shorter than the body of the strip, putting more tension on the edges.What can you do about them?* bend the edges of the coil, to do this:- turn positive bending off- increase negative bending to -2- increase the load;。
防静电袋市场分析报告

防静电袋市场分析报告1.引言1.1 概述概述静电是一个普遍存在且具有潜在危害的现象,尤其在现代电子产品生产和储存过程中更是一大隐患。
为了应对静电带来的危害,防静电袋逐渐成为了必备的一种防护工具。
本报告旨在对防静电袋市场进行全面分析,探讨其现状、趋势以及展望,为相关企业和机构提供市场参考和决策依据。
通过对防静电袋市场的深入研究,我们可以更好地理解其发展状况,帮助企业更好地把握市场机遇,推动行业的健康发展。
1.2 文章结构文章结构:本报告将分为引言、正文和结论三个部分。
在引言中,将对静电和防静电袋的概念进行概述,并说明文章的结构和目的。
在正文部分,将详细介绍静电及其危害,防静电袋的作用以及防静电袋市场的现状。
在结论部分,将对市场趋势进行分析,展望市场前景,并提出相关建议与总结。
通过对这三个部分的分析,读者将能够全面了解防静电袋市场的现状和未来发展趋势。
1.3 目的目的部分的内容应该包括对撰写本报告的目的进行详细说明,包括为什么要进行防静电袋市场分析以及对市场趋势和前景的探讨的重要性和必要性。
目的部分还应该说明本报告旨在为相关行业和企业提供有价值的市场信息和分析,以便他们能够制定更有效的营销策略和业务决策。
1.4 总结总结:防静电袋市场是一个不断发展和变化的市场,随着科技的进步和应用领域的不断拓展,防静电袋的需求和市场规模也在不断增加。
通过本报告的市场分析,我们可以清晰地看到防静电袋市场的现状和发展趋势。
在竞争激烈的市场环境中,企业需要不断创新,提高产品质量和性能,以抓住市场机遇并保持竞争优势。
同时,企业也需要关注市场的发展趋势,制定有效的市场策略,更好地把握市场机遇和应对市场挑战。
相信通过本报告的分析,读者们能够对防静电袋市场有更清晰的认识,为相关企业的决策提供一定的参考和指导。
2.正文2.1 静电及其危害静电是指物体表面带有不平衡的电荷,当两个带有不同电荷的物体接触时,会产生静电放电现象。
静电在现代工业生产和日常生活中广泛存在,其危害也不容忽视。
防静电包装材料应用指导和误区
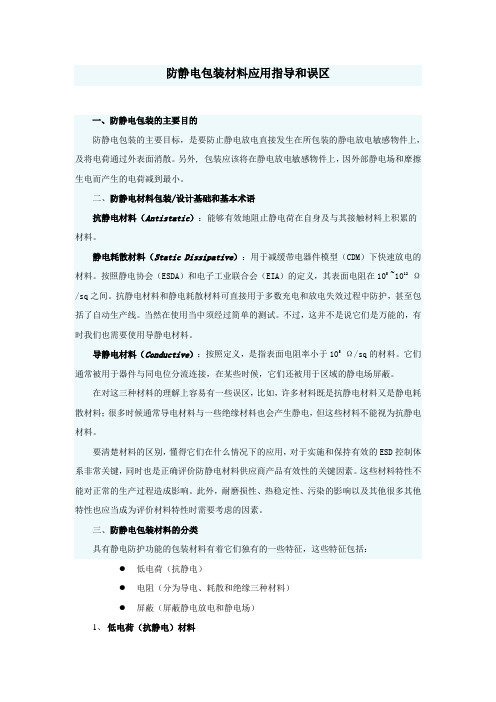
防静电包装材料应用指导和误区一、防静电包装的主要目的防静电包装的主要目标,是要防止静电放电直接发生在所包装的静电放电敏感物件上,及将电荷通过外表面消散。
另外, 包装应该将在静电放电敏感物件上,因外部静电场和犘擦生电而产生的电荷减到最小。
二、防静电材料包装/设计基础和基本术语抗静电材料(Antistatic):能够有效地阻止静电荷在自身及与其接触材料上积累的材料。
静电耗散材料(Static Dissipative):用于减缓带电器件模型(CDM)下快速放电的材料。
按照静电协会(ESDA)和电子工业联合会(EIA)的定义,其表面电阻在105~1012Ω/sq之间。
抗静电材料和静电耗散材料可直接用于多数充电和放电失效过程中防护,甚至包括了自动生产线。
当然在使用当中须经过简单的测试。
不过,这并不是说它们是万能的,有时我们也需要使用导静电材料。
导静电材料(Conductive):按照定义,是指表面电阻率小于105Ω/sq的材料。
它们通常被用于器件与同电位分流连接,在某些时候,它们还被用于区域的静电场屏蔽。
在对这三种材料的理解上容易有一些误区,比如,许多材料既是抗静电材料又是静电耗散材料;很多时候通常导电材料与一些绝缘材料也会产生静电,但这些材料不能视为抗静电材料。
要清楚材料的区别,懂得它们在什么情况下的应用,对于实施和保持有效的ESD控制体系非常关键,同时也是正确评价防静电材料供应商产品有效性的关键因素。
这些材料特性不能对正常的生产过程造成影响。
此外,耐磨损性、热稳定性、污染的影响以及其他很多其他特性也应当成为评价材料特性时需要考虑的因素。
三、防静电包装材料的分类具有静电防护功能的包装材料有着它们独有的一些特征,这些特征包括:●低电荷(抗静电)●电阻(分为导电、耗散和绝缘三种材料)●屏蔽(屏蔽静电放电和静电场)1、低电荷(抗静电)材料低电荷材料主要体现在它的电荷累积总量与其他包装材料比较起来会保持在较低水平。
化工原料厂除尘布袋优缺点

化工原料厂除尘布袋优缺点
化工原料厂是一个高污染行业,除尘工作是必不可少的环节。
而除尘布袋作为一种常用的除尘设备,其优缺点也备受关注。
本文将从多个角度分析化工原料厂除尘布袋的优缺点,帮助读者更好地了解该设备。
1.高效除尘
除尘布袋的优点就是其高效除尘能力。
其过滤精度高,能有效地过滤掉微小的尘粒,使空气中的颗粒物浓度得到有效的降低。
2.长使用寿命
除尘布袋的使用寿命长,一般可使用数年之久。
这是由于其材质的特殊性质所决定的,能够承受高温、高压等恶劣的工作环境,不易损坏。
3.维护方便
除尘布袋的维护相对来说比较简单,只需进行定期的清洗和更换即可。
这极大地降低了设备的维护成本。
1.价格高昂
除尘布袋的价格相对较高,这是由于其材质和生产工艺的特殊性所决定的。
在选择除尘设备时,需要考虑到设备成本的问题。
2.易受损
除尘布袋虽然使用寿命长,但其材质相对来说比较脆弱,易受损。
一旦被损坏,就需要更换,会增加设备的维护成本。
3.清洗困难
除尘布袋的清洗相对来说比较困难,需要使用特殊的清洗设备和方法。
如果清洗不当,会导致除尘效果下降,甚无法达到预期的效果。
综上所述,除尘布袋作为一种常用的除尘设备,其优缺点都需要被充分考虑。
在选择除尘设备时,需要根据自身的实际情况进行综合考虑,并选择适合自己的除尘设备。
静电袋真空袋铝箔安全操作及保养规程

静电袋真空袋铝箔安全操作及保养规程为了保障静电袋真空袋铝箔的使用效果及寿命,确保工作人员的人身安全和环境安全,在使用、保养过程中需注意一些规范,具体内容如下:一、静电袋真空袋铝箔的使用规范1.禁止使用钻、刻刀、尖锐物品等直接在袋内操作。
未使用第二次的原材料袋不能加工,即使使用过,也不能直接再次加工,需要清洗后方可使用。
2.禁止将容器覆盖物强制压入袋中,造成袋内爆炸、产生放电现象。
铝箔压不坏,但需要保持一定的空间(至少两厘米),以利于放电后的压力释放。
3.袋体压力不得超过袋体耐压能力。
一般静电袋真空袋耐压指标在65KG/cm2左右,根据实际使用需求,使用者可以选择不同厚度、不同材质的袋进行加固。
4.袋内液体、半液体食品不得超过刻度线范围使用。
切勿超限操作,造成静电袋真空袋铝箔破损,影响使用寿命。
在填充过程中,尽量减少包装对空气的依赖,因为透明材质会受到光的影响。
5.禁止袋子悬挂或吊放,以防袋体受力变形、爆炸。
静电袋真空袋铝箔的制作需要采用执行GB/T1040压缩试验、抗拉强度测试,技术要求严格,但是在使用安装时,由于操作不当或者未遵循操作规程,导致意外伤害的情况6.袋子使用时的温度不能超过60度。
铝箔及其内层材质对温度均有一定的限制,超过限制范围,将导致材质的变形、老化,影响静电袋真空袋铝箔的密封性。
二、静电袋真空袋铝箔的保养规范1.除了材质本身的耐热、防腐能力,还需注意引起性质变化的环境因素。
重要的环境变化因素包括空气中的化学物质、水分子、温度、光的入射角以及相关的热辐射。
环境因素的影响直接影响到袋子的使用寿命。
2.在干燥、阴凉及无灰尘的地方储存袋子。
储存位置应远离阳光和暴露在高温和高湿度的环境中。
同时,尽量避免施加过度的压力。
3.保持接触材料干燥、清洁。
静电袋真空袋铝箔内部积附有许多粉尘杂物需要及时清理。
同时,太潮湿的环境下会降低铝箔的使用寿命,需要注意环境湿度。
4.膜材的表面除了常规物理清洁外,不应涂刷或使用清洗剂清洗。
2023年防静电包装材料行业市场环境分析

2023年防静电包装材料行业市场环境分析随着科技的不断进步,尤其是电子信息技术的快速发展,防静电包装材料逐渐成为电子信息产业、半导体行业、医疗设备等领域中不可或缺的一部分。
防静电包装材料是指能够有效地减少或防止静电的产生或积累,从而达到保护和维护电子元器件及其它精密器材的目的的材料。
与传统包装材料相比,防静电包装材料具有良好的导电性能、超强的防静电性能、超长的防静电周期,能够有效地避免静电对精密器材造成的破坏或损坏,同时也具有防水、防潮、防腐等特点。
一、我国防静电包装材料市场现状我国防静电包装材料市场起步较晚,但近年来市场需求越来越高,市场规模增长迅速。
目前,我国防静电包装材料市场已经形成了一定的规模,主要集中在广东、浙江、江苏等地。
随着互联网技术和物联网的高速发展,防静电包装材料也被广泛用于电子商务物流和智能物流中,为产业链的形成和推进提供了有力的支持。
二、防静电包装材料市场存在的问题1、防静电包装材料行业市场竞争十分激烈,市场上存在着很多品牌,品质也相差较大,因此行业需加强自主品牌建设,提高企业的市场占有率。
2、防静电包装材料中所使用的金属粉末或铜箔等导电材料,某些成分不符合国际环保标准,可能对环境及人体健康造成潜在的危害。
3、部分小企业缺乏专业的技术团队以及质量管理措施,存在生产工艺不稳定、产品性能不稳定等问题,企业需要加强创新研发,提高自身的科技含量和市场竞争力。
三、防静电包装材料市场发展趋势1、随着人们环保意识的提升,防静电包装材料市场将会以环保为中心,不断研发新型环保材料,给使用者更稳定和更好的使用体验。
2、物联网、5G等技术的快速发展,将为防静电包装材料市场提供新的机遇和挑战。
3、产业链向深度、广度拓展以及区域性市场的开发都将是未来防静电包装材料市场的重点。
结论在市场竞争激烈的环境下,防静电包装材料行业需加强自主品牌建设,提高自身的科技含量和市场竞争力,并在环保、新技术的发展趋势下,加大创新力度,提高产品质量,促进企业高速发展。
常见铝箔的质量缺陷

9、板型不良
主要特征:由于不均匀变形使箔材表面局部产生起伏 不平的现象.称为板型不良。根据缺陷产生的部位, 分为中间波浪、边部波浪、二肋波浪及复合波浪等。 在边部称边部波浪,在中间称中间波浪,二者兼有之 称复合波浪,既不在中间又不在边部称二肋波浪。 产生原因: a)来料板型不良; b)轧制压力调整不平衡; c)道次压下量分配不合理; d)轧辊辊型不合理; e)轧制油喷淋不正常。
14、横纹
主要特征:铝箔表面横向有规律的细条纹,一般呈白 色,无凹凸感,有时在卷材局部,有时布满整个表面。 产生原因: a)轧制毛料表面有横纹; b)轧制道次压下量过大; c)轧辊粗糙度不合理; d)轧制油理化指标不合理。 E)轧辊磨削质量差,表面有条纹。
15、人字纹
主要特征:箔材表面呈现的有规律的人字形的花纹, 一般呈白色,表面有明显的色差,但十分光滑。 产生原因: a)轧制时道次压下量过大,金属在轧辊间由于摩擦力太 大,流动速度慢,产生滑移。 b)辊型不好,温度不均; c)轧辊粗糙度不合理; d)轧制油理化指标不合理。 E)轧辊磨削质量差,表面有条纹。
主要特征:铝箔卷表面无法展平的纵向或横向 皱折。 产生原因: a)来料板型不良或有皱折; b)轧辊辊型控制不合理; c)轧制及分切工艺参数不合理; d)轧机辊系精度不够; e)套筒或管芯精度不够。
26、亮点
主要特征:铝箔双合轧制时,出现的铝箔暗面 上不均匀的发亮的点称为亮点。 产生原因: a)双合前箔材表面粗糙不均或有辊印、横波等缺 陷; b)轧辊表面粗糙不均; c)双合油指标不适宜; d) 双合时上下张铝箔厚度相差过大。
37、白条
主要特征:铝箔表面沿轧制方向、宽度或间隔不等的 白色条纹。一般对应铸轧带下表面出现,条纹多集中 在铝箔中间、两肋位置,随着铝箔的压延减薄,条纹 呈明显加重趋势。 产生原因: a)铸轧坯料Ti/B偏析,沉积等; b)铸轧带材中间及两肋位置冷却较差,结晶滞后造成该 位置组织和其他位置不同; c)铸轧辊冷却强度不均,造成成分偏析、晶粒不均。
- 1、下载文档前请自行甄别文档内容的完整性,平台不提供额外的编辑、内容补充、找答案等附加服务。
- 2、"仅部分预览"的文档,不可在线预览部分如存在完整性等问题,可反馈申请退款(可完整预览的文档不适用该条件!)。
- 3、如文档侵犯您的权益,请联系客服反馈,我们会尽快为您处理(人工客服工作时间:9:00-18:30)。
防静电铝箔袋信息五大弊端
据相关统计数据显示,2011年以来,防静电铝箔袋增长率超过了10%。
申凯包装相关专家表示,就目前防静电铝箔袋信息化发展的现状,东莞防静电铝箔袋印刷企业信息化基本存在五大弊端,具体如下:
防静电铝箔袋信息五大弊端一,在精细化管理要求下,订单多变,多样小批量的行业特性导致信息化基础资料数据暴涨,维护工作量剧增,资料维护进度难以满足企业快速高效响应客户的营运需求。
防静电铝箔袋信息五大弊端二,包装业自动化排产成功案例少,目前人工排产效率较低,无法支持企业的快速发展。
防静电铝箔袋信息五大弊端三,缺乏快速有效的估报价系统,企业规模不断扩大,利润却停滞不前。
防静电铝箔袋信息五大弊端四,现有成本人工核算耗时费力,无法为管理层提供及时正确的成本分析数据,进而支持管理决策。
防静电铝箔袋信息五大弊端五,原有行业化包装或企业自行开发系统只能支持企业的基本业务运作,无法支持企业高速扩张过程中实现业务财务一体化、支撑集团化高效运营的管理需求。
来源于:申凯包装高新技术股份有限公司-包装知识。