伟尔沃曼渣浆泵系列综合样本
力士乐A11VO液压泵样本
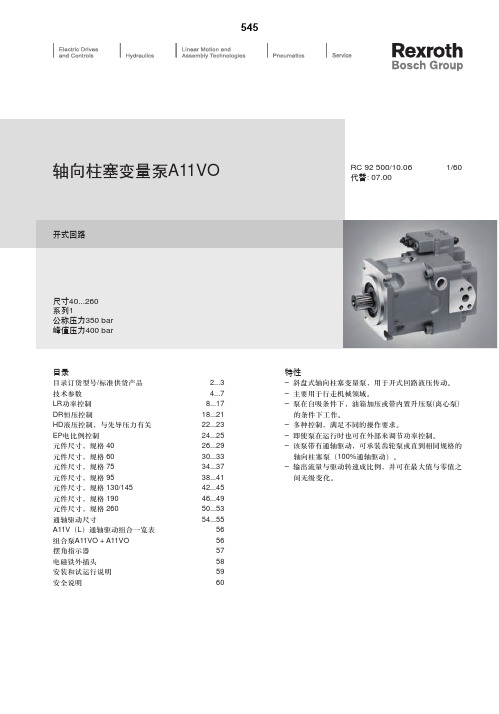
注意:
当温度低于-25°C时须用丁腈橡胶轴密封圈(允许温度范围: 01
-40°C至+90°C)。
增加吸油口S的出口压ዡ力ၠpabዹs或让Vڇg ≤ᇮVg mĂax时ۨ允ଉ许的ԭ转Ă速ՎଉԭĂ
63 … 582
请在订单上注明丁腈橡胶轴密封圈。
ٙڇᇮLjᆩᇀዡၠዹԭڦ੦ጎዃ
– 6)
01 02 03 04 05
/60 博世力士乐 | 行走机械液压
548
A11VO | RC 92 500/06.04
技术参数
液压油
项目开始前,有关液压油的选择和应用条件请参见本公 司的样本活页RC 90220(矿物油),RC 90221(环保液压 油)和RC 90223(HF难燃液压油)
工作粘度。
按 ISO 4406的20/18/15级
液压油处于高温时(90°C至最高115°C),最低的清洁度 等级为
温度在-25°C至-40°C,应当采取特殊措施,请与我公司 联系。低温操作时的详细信息,请参见RC 90300-03-B。
按ISO4406的19/17/14级。
如果不能达到上述清洁度等级,请咨询供应商。
੦ጎዃ
ࠀ୲੦
LR
ټሁ੦ ֮ߌد੦
੦ LR
C
ᇑߛუᆶ࠲
੦ LR3
ᇑံڞუ૰ᆶ࠲
੦ LG1
ኟ੦ LG2
ۉጱሁ 12V
੦ LE1
24V
੦ LE2
ټუ૰ൎ
D
ټუ૰ൎ
ᅂუ੦Lj2प
E
ᅂუᇺײ੦
ߌدࢁټ੦
ۉጱԲ૩ሁLj24V
ᅂუԲ૩ሁ
阿尔法拉瓦尔SX超级纯净旋转泵说明书

Benefits•Low pulsation and very gentle pumping, making the pump ideal for sensitive products.•Minimized shearing to protect end-product quality.•Low maintenance, increased process uptime.•Low contamination risk due to full material traceability and USP Class VI elastomers that reduce the risk of processcontamination from extractables.•Smooth qualification, validation and process control:material traceability, and pump supplied with the Alfa Laval Q-doc package in line with Good DocumentationPractices.Standard designAll media contacting steel components, like the rotor case, front cover, rotors and rotor nuts, are in W. 1.4404 (AISI 316L). The stainless steel gearbox provides maximum shaft rigidity and easy oil seal replacement. The gearbox design is universal, which enables the flexibility of mounting pumps with the inlet and outlet ports in either a vertical or horizontal plane by changing the foot and its position.The standard Alfa Laval SX UltraPure has four-lobe rotors rated to 150°C, facilitating use with CIP and SIP processes.Fully front-loading and fully interchangeable single, single flushed and double mechanical shaft seals are available. All media contacting elastomers are controlled compression joints, the latest technology where static and dynamic elastomer seals are used to prevent leakage of pumped media to the atmosphere.The Alfa Laval SX UltraPure can be supplied either as a bare shaft pump or mounted on a base plate complete with coupling, guard, gear motor and shroud for easy, plug-and-play installation.Working principleA gear train in the pump gearbox drives the rotors and provides accurate synchronization of the multi-lobe rotors. The movement of the counter-rotating rotors creates a partial vacuum that allows atmospheric pressure or other external pressures to force fluid into the pump chamber. As the rotors revolve, an expanding cavity forms, filling with fluid. As the blades disengage, each dwell forms a cavity. As the rotor blades engage, the cavity diminishes and fluid is displaced into the outlet port.CertificatesTECHNICAL DATAInside surface finish:Mech Ra ≤ 0.8Gearbox:Stainless steel Base plate:Stainless steel Coupling guard:Stainless steel Rotor:Four-lobeProduct wetted elastomers:EPDM - USP Class VI, 249.8°F . Chapter 88, and Chapter 87Other elastomers:FPMShaft seal:Single mechanical (R00)Rotary seal face:Silicon Carbide Stationary seal face:Silicon CarbideMax. flush pressure, single flush:Max. 0.5 bar Max. flush pressure, double mechanical:Max. 1 bar over product pressure Water consumption, flushed or double mechanical:0.5 l/min Flush connections:BSPT or NPTMedia contacting elastomersAll media contacting elastomers are controlled compression joints, the latest technology where static and dynamic elastomerseals are used to prevent pumped media leaking to atmosphere.1. Front cover compression joint.2. Spline sealing cup seal.3. Cup seal.4. Squad ring.Flows/Pressures/ConnectionsSX UltraPure 1/0070.07 1.54 1.8540 1.571001200SX UltraPure 2/0130.128 2.82 3.3840 1.5152151000SX UltraPure 2/0180.181 3.98 4.7850271001000SX UltraPure 3/0270.266 5.857.03502152151000SX UltraPure 3/0350.357.709.2565 2.571001000SX UltraPure 4/0460.4610.1212.15502152151000SX UltraPure 4/0630.6313.8616.6565 2.5101451000SX UltraPure 5/0820.8218.0421.6765 2.515215600SX UltraPure 5/115 1.1525.3030.3880310145600SX UltraPure 6/140 1.4030.8036.9980315215500SX UltraPure 6/190 1.9041.8050.20100410145500SX UltraPure 7/250 2.5055.0066.05100415215500SX UltraPure 7/380 3.8083.60100.401506101455001 These pressure ratings may vary for pumps with certain threaded connections.SX UltraPure 1/0071617SX UltraPure 2/0133233SX UltraPure 2/0183334SX UltraPure 3/0275759SX UltraPure 3/0355961SX UltraPure 4/046107110SX UltraPure 4/063113116SX UltraPure 5/082155155SX UltraPure 5/115165165SX UltraPure 6/140278278SX UltraPure 6/190290290SX UltraPure 7/250-340SX UltraPure 7/380-362Shaft Seal Options•Single or single flush/quench (steam barrier for aseptic application) R00 type mechanical seals.•Double R00 type mechanical seal for flush.All sealing options are fully front loading and fully interchangeable without the need for additional housings or pump component changes. Specialised seal setting of the mechanical seal is not required as the seal is dimensionally set on assembly. This feature further enhances fast and efficient on-site seal interchangeability.Materials for Mechanical SealsAs standard the SX UltraPure is supplied with EHEDG compliant Silicon Carbide/Silicon Carbide seal faces avoiding any risk of potential extractable contamination.Standard Specification Options•Screwed male inlet and outlet ports to DIN11851, SMS, RJT, Triclamp for ASME, DIN 32676 Clamp, DIN 11864-1 (Union) Form A, DIN 11864-2 (Flange) Form A or DIN 11864-3 (Clamp) Form A.•Heating/Cooling Jacket for Rotorcase Cover.•Product wetted surface finish electropolished to Ra ≤ 0.38 μm.•Passivated surface.•Surface finish measurement with certificate.•Hydrostatic testing with certificate.•ATEX compliance.•Complete pump unit comprising: Pump + stainless steel baseplate + coupling with guard + Geared electric motor suitable for (or supplied with) frequency speed control or manual variable speed drive (advise motor enclosure and electrical supply).•Low delta ferrite material for product wetted components.•High alloy materials for product wetted components i.e. AL6XN or Titanium.Q-docStandard documentation package:•Declaration of compliance with Regulation (EC) No.: 1935/2004.•Declaration of compliance to EN 10204 type 3.1 (MTR).•Declaration of compliance to the U.S. Food & Drug Administration CFR 21 (non-metallic parts).•Declaration of compliance to the U.S. Pharmacopeia (Elastomers and polymers).•TSE (Transmissible Spongiform Encephalopathy) / ADI (Animal Derivative Ingredient) declaration.•Declaration of surface finish compliance.•Declaration of passivation and electro polishing (if specified).•3.1 certification in accordance to EN10204.•Pump performance test certificate.Optional documentation:•Hydrostatic test certificate.•Surface measurement report.Pump SizingIn order to correctly size a rotary lobe pump some essential information is required. Provision of this information listed below enables our Technical Support personnel to obtain the optimum pump selection.Product/Fluid Data:•Fluid to be pumped.•Viscosity.•SG/Density.•Pumping temperature, minimum, normal and maximum.•Cleaning in Place temperature(s), minimum, normal and maximum.Performance Data:•Flow rate, minimum, normal and maximum.•Discharge head/pressure (closest to pump outlet).•Suction condition.Bareshaft Pump DimensionsFigure 1. Vertically portedSX UltraPure 1/0074095113208151640305294601008022114104801017423.5SX UltraPure 2/0134010514725215225032632559111100121241241001221332.5SX UltraPure 2/0185010514725215225032634166111100121241241001221332.5SX UltraPure 3/0275012517530022286140843171142155151851551251424637.5SX UltraPure 3/0356512517530022286140844777142155151851551251424637.5SX UltraPure 4/04650150213363253880631051474174200172341841501430149.5SX UltraPure 4/06365150213363253880631053381174200172341841501430149.5SX UltraPure 5/0826*******.5431.53045110701459961264200202402201801434460SX UltraPure 5/11580175256.5431.53045110701462981264200202402201801434460SX UltraPure 6/140801902954853048110701468777267260203002502101440070SX UltraPure 6/1901001902954853048110701471589267260203002502101440070SX UltraPure 7/2501002053655703060110901876394288280253302902401847581.5SX UltraPure 7/38015020536557030601109018817121288280253302902401847581.5TOP SHAFTDRIVEFigure 2. Horizontally portedAll dimensions in mmSX UltraPure 1/007409590.5189101640671143052943612480101001008010 SX UltraPure 2/0134010511523315225082.5147.5326325391311001913212410012 SX UltraPure 2/0185010511523315225082.5147.5326341461311001913212410012 SX UltraPure 3/027********.5272182860100175408431681751253018115412514 SX UltraPure 3/0356*******.5272182860100175408447741751253018115412514 SX UltraPure 4/04650150163325203880113.5212.56310514742251503520218415014 SX UltraPure 4/06365150163325203880113.5212.56310533812251503520218415014 SX UltraPure 5/0826517519537620451101352557014599462791803527521018014 SX UltraPure 5/1158017519537620451101352557014626662791803527521018014 SX UltraPure 6/1408019022542920481101552957014687782662604037022019014 SX UltraPure 6/19010019022542920481101552957014715902662604037022019014This document and its contents are subject to copyrights and other intellectual property rights owned by Alfa Laval Corporate AB. No part of this document may be copied, re-produced or transmitted in any form or by any means, or for any purpose, without Alfa Laval Corporate AB’s prior express written permission. Information and services provided in this document are made as a benefit and service to the user, and no representations or warranties are made about the accuracy or suitability of this information and these services for any purpose. All rights are reserved.200006102-1-EN-GB© Alfa Laval Corporate AB How to contact Alfa LavalUp-to-date Alfa Laval contact details for all countries are always availableon our website at 。
熊猫 SMGW型泵循环水泵样本
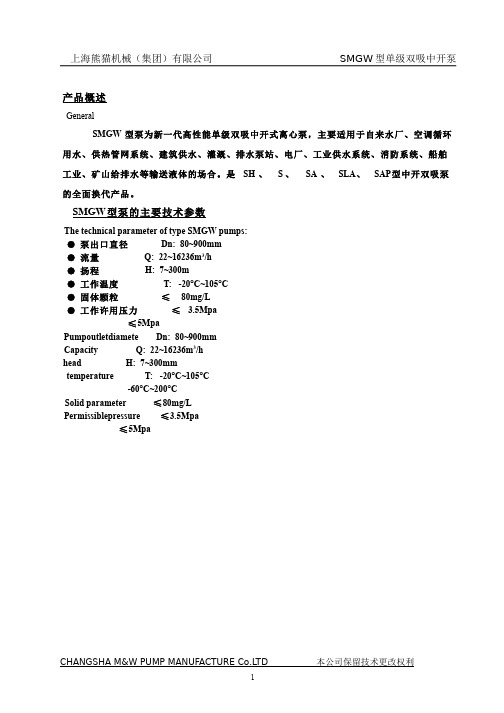
70.0
76.0
74.0
5.5
68.0
75.0
73.0
75
73.0
78.5
78.0
75
72.0
77.5
75.0
55
72.0
76.0
74.0
37
71.0
75.0
74.0
22
66.0
75.0
72.0
15
66.0
SMGW 型单级双吸中开泵
4.5
255
1.6
2.3
3.5
235
1.5
2.0
3.0
215
1.5
2.0
成本优势
● 选(采)用优异的水力模型,使泵的效率比同类型泵高 2-3% ,大大降低了泵的运 行成本。 ● 真空高度提高 1-3 米,从而降低土建投资,延长了使用寿命。 ● 选用进口轴承,零件材料可根据用户应用要求选用,使泵能适应各种现场运行条件, 大大降低了维修成本。
维修优势
● 无调整式机械密封,更换机械密封成为轻松简单的工作。 ● 应用弹性预应力设计装配, 转子部件装拆简单迅速。 ● 装配时无须调整各种间隙。
≤ 5Mpa
CHANGSHA M&W PUMP MANUFACTURE Co.LTD
1
本公司保留技术更改权利
上海熊猫机械(集团)有限公司
SMGW 型单级双吸中开泵
泵型号意义
(discription of pump type) 举例 (for example):
SMGW 250–450 A– L–R(M.F)– J
215
1.5
1.6
1.8
200
1.5
ZGB系列渣浆泵说明书样本
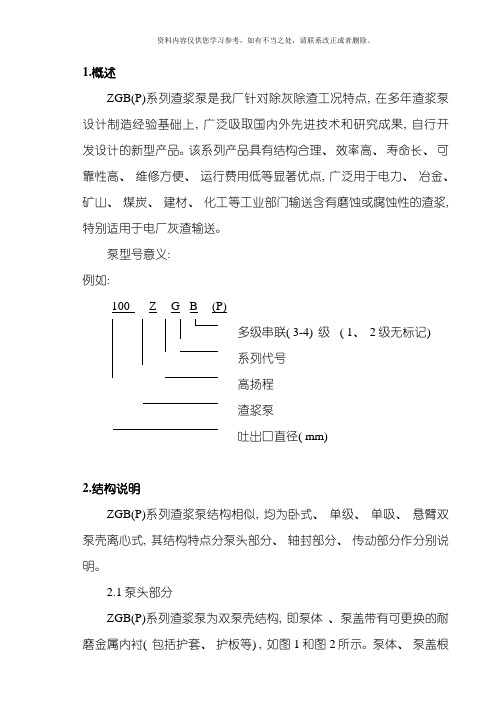
1.概述ZGB(P)系列渣浆泵是我厂针对除灰除渣工况特点, 在多年渣浆泵设计制造经验基础上, 广泛吸取国内外先进技术和研究成果, 自行开发设计的新型产品。
该系列产品具有结构合理、效率高、寿命长、可靠性高、维修方便、运行费用低等显著优点, 广泛用于电力、冶金、矿山、煤炭、建材、化工等工业部门输送含有磨蚀或腐蚀性的渣浆, 特别适用于电厂灰渣输送。
泵型号意义:例如:100 Z G B (P)多级串联( 3-4) 级( 1、2级无标记)系列代号高扬程渣浆泵吐出口直径( mm)2.结构说明ZGB(P)系列渣浆泵结构相似, 均为卧式、单级、单吸、悬臂双泵壳离心式, 其结构特点分泵头部分、轴封部分、传动部分作分别说明。
2.1泵头部分ZGB(P)系列渣浆泵为双泵壳结构, 即泵体、泵盖带有可更换的耐磨金属内衬( 包括护套、护板等) , 如图1和图2所示。
泵体、泵盖根据工作压力采用灰铸铁或球墨铸铁制造。
该系列泵均为垂直中开式, 吐出口方向可按450间隔八个角度旋转安装。
叶轮前后盖板设有付叶轮以减少泄漏及提高泵的使用寿命。
该系列进口均为水平方向, 从传动端看泵为顺时针旋转。
起动及运转时, 严禁电机反方向旋转。
否则, 将使泵叶轮脱落造成事故。
2.2 轴封部分轴封有两种型式:(1) 付叶轮加填料组合式密封: 该种密封型式是我厂采用可靠性设计研制的高性能密封, 它使轴封的泄漏减少到了最小。
针对某些不允许稀释、不允许加轴封水的特殊工况( 单级) 也能正常工作, 并达到无任何泄漏的效果。
付叶轮、减压盖、轴套均采用耐磨材料制造, 维修量少、使用寿命长, 使整机平均无故障工作时间MTBF大大提高。
(2) 机械密封: 该形式的密封特别适用于多级串联渣浆泵的密封, 完全无泄漏。
凡串联渣浆泵二级及二级以上, 建议采用高压轴封水的机械密封, 单级采用付叶轮加填料组合式密封。
2.3轴封水压对于单级( 或串联一级) 采用填料加付叶轮组合式密封, 轴封水压力一般不低于0.2Mpa。
WQE系列新型潜水排污泵样本
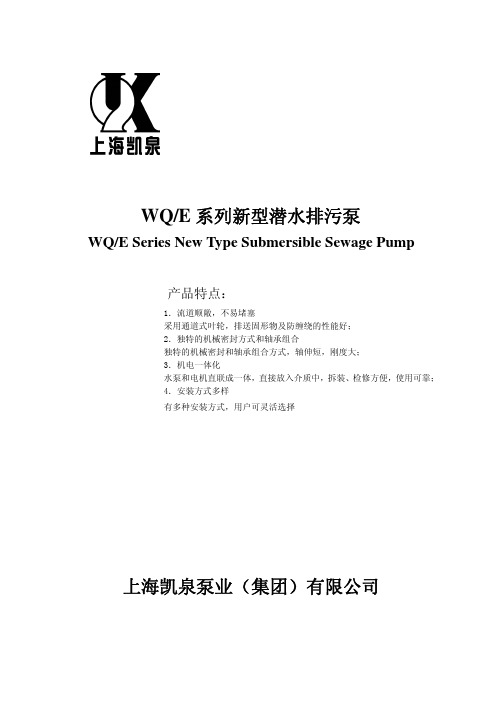
单位:除英寸外均为 mm
泵排出口径 项目
50
65
80
100
导杆
1″自来水管或 32×3.5 无缝钢管
导杆长度
地脚螺栓数量、规格
膨胀螺栓数量、规格 地脚螺栓的 预留孔尺寸
池深-300
池深-305 池深-425 池深-410
4-M16×220
4-M20×300
2-M16×150Ⅰ
80×80×270
100×100×350
保留技术更改的权力
8
下滑到底,耦合架就会与出水管座对齐扣紧。需要维修泵时,只需把泵 向上提,泵与出水管座就脱开了。这种安装方式很便于泵的维修。
由于耦合装置和泵是相对独立的,所以,如果您的泵站因情况变化需 换用同口径的低扬程或高扬程的泵,可以仍然使用原来的耦合装置。
自动耦合安装相关尺寸 软管移动安装配用的软管尺寸
O 形密封圈材质为耐油橡胶
螺母 M10×1.25 弹簧垫圈 10
叶轮压板 WQB07-01A
螺钉 M8×25 弹簧垫圈 8
叶轮压板 WQB07-10
螺钉 M10×25 弹簧垫圈 10 叶轮压板 WQB07-16
螺母、螺钉、弹簧垫圈材质为不锈钢,叶轮压板材质为 Q235
155×3.55 一个 180×3.55 二个 10×2.65 三个
并在订单上注明。 4、成套供货件是按用户选定的安装方式配套供货。选购件、备件须
用户另外订购。 5、由于耦合装置的简洁设计,导杆只须用一般的自来水管或钢管。
我们在前面已经提供了用作导杆的自来水管或钢管的规格及长度计算方 法,用户只需自行购置自来水管或钢管,切成需要的长度就可以使用了, 所以导杆不作为耦合安装时的成套供货件。用户需要由我公司提供导杆 时,须另外订购并写入订单。
G2_Etanorm_ch
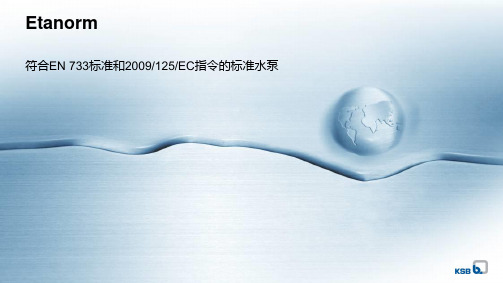
A1 A1 A2 A1 A1
3
I Etanorm I KSB I February 2013 I
材料代号 Description
G
灰铁 JL1040 /灰铁A 48 CL 35B 不锈钢 1.4408 / A743 Gr CF8 M 102 / 蜗壳
B1 B1 -
GB
B1 B1
GC
B1 -
GI
B1 -
GB
A1 -
GC
A1 -
GI
B
S
-
SB
-
SC
-
C
-
Etanorm
A1
-
材料 (欧洲)
在欧洲可选用的材料
不锈钢 1.4408 / A743 Gr CF8 M
灰铁 JL1040 / 灰铁 A 48 CL 35B 230 / 叶轮 青铜 CC480K-GS/B30 C90700 不锈钢 1.4408 / A743 Gr CF8 M 灰铁 JL1040 / 灰铁 A 48 CL 35B 青铜 CC480K-GS/B30 C90700 161 / 泵盖,锥形 球铁 JS1030/A536 GR 60-40-18
GB
D1
GC
D1
GI
-
B
-
S
-
SB
-
SC
-
C
-
Etanorm
材料 (中国)
在中国可选用的材料
D1 中国默认的材料类型 D2 中国可选用的材料类型
青铜 CC495K-GS
灰铁 JL1040 / A 48 CL 35B 502.02 / 泵体密封环,压出侧 灰铁 (CrNiMoST) 青铜 CC495K-GS 523 / 轴套 524 / 护轴套 铬钢 1.4122HV500+80 不锈钢 (CrNiMoST) 不锈钢 (CrNiMoST)
迈德斯姆泥水泵WS_B系列模型3886商业用途说明书

115
208 4.69
230
115
208
230
200 5.00
230
460
575
208 1750 230
200
5.38
230
460
575
208
230
200
5.75
230
460
575
IMPELLER DIA. (in.)
MAX. AMPS
L RA
KVA FULL LOAD CODE MOTOR EFF.
RESISTANCE START LINE-LINE
WT. (LBS.)
WS0311B WS0318B 0.33 WS0312B 1 WS0511B WS0518B WS0512B WS0538B 0.5 WS0532B 3 WS0534B WS0537B WS0718B 1 WS0712B WS0738B 0.75 WS0732B 3 WS0734B WS0737B WS1018B 1 WS1012B WS1038B 1 WS1032B 3 WS1034B WS1037B
■ Casing: Cast iron volute type for maximum efficiency. Designed for easy installation on A10-20 guide rail or base elbow rail systems.
长沙工业泵总厂产品电子样本(带目录)
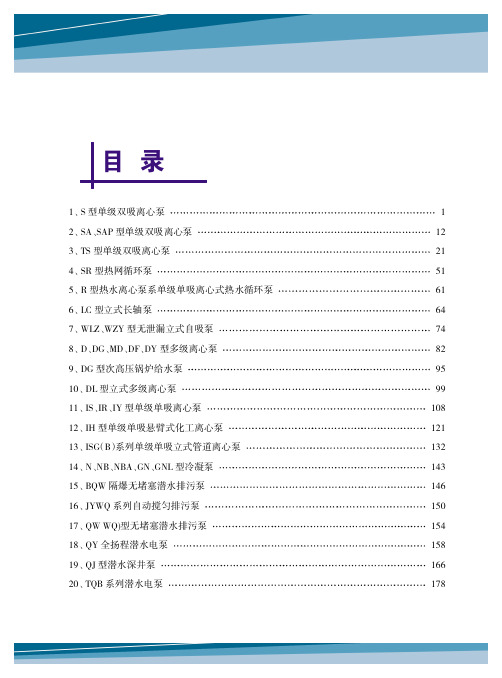
1、S型单级双吸离心泵12、SA、SAP型单级双吸离心泵123、TS型单级双吸离心泵214、SR型热网循环泵515、R型热水离心泵系单级单吸离心式热水循环泵616、LC型立式长轴泵647、WLZ、WZY型无泄漏立式自吸泵748、D、DG、MD、DF、DY型多级离心泵829、DG型次高压锅炉给水泵9510、DL型立式多级离心泵9911、IS、IR、IY型单级单吸离心泵10812、IH型单级单吸悬臂式化工离心泵12113、ISG(B)系列单级单吸立式管道离心泵13214、N、NB、NBA、GN、GNL型冷凝泵14315、BQW隔爆无堵塞潜水排污泵14616、JYWQ系列自动搅匀排污泵15017、QW(WQ)型无堵塞潜水排污泵15418、QY全扬程潜水电泵15819、QJ型潜水深井泵16620、TQB系列潜水电泵178S 型单级双吸离心泵S 型泵为单级、双级、泵体水平中开的离心泵;可供抽送清水或物理化学性质类似于清水的其它液体之用,被抽送液体温度不得超过80℃;适用于工厂、矿山、城市、电站给排水、农田排灌和各种水利工程。
在S 型泵的基础上通过改变材质、密封、结构等措施可派生出能输送含磨损介质的SM 型、输送腐蚀性介质的SF 型、输送油类介质的SY 型中开离心泵,其性能参数和外形尺寸与同规格S 型泵一致。
泵的进口允许压力不超过0.3MPa。
改变材料可输送更高进口压力介质。
150S(SM、SF、SY)78A(I、G)150-泵进口直径为150mmS-卧式单级双吸清水离心泵SM-卧式单级双吸耐磨离心泵SF-卧式单级双吸耐腐蚀离心泵SY-卧式单级双吸离心油泵78-泵设计点扬程78mA-叶轮外径切割代号I-代表叶轮外径加大G-代表更改叶轮流量:160~18000m 3/h扬程:12~130mS型泵的吸入口与吐出口均在水泵轴心线下方,与轴线垂直呈水平方向,泵壳中开,检修时无需拆卸进、出水管路及电动机(或其它原动机)。
- 1、下载文档前请自行甄别文档内容的完整性,平台不提供额外的编辑、内容补充、找答案等附加服务。
- 2、"仅部分预览"的文档,不可在线预览部分如存在完整性等问题,可反馈申请退款(可完整预览的文档不适用该条件!)。
- 3、如文档侵犯您的权益,请联系客服反馈,我们会尽快为您处理(人工客服工作时间:9:00-18:30)。
WARMAN®Centrifugal Slurry PumpsHorizontal Slurry PumpsSpecialists in delivering and supporting slurry and dewatering equipment solutions for global mining and mineral processing, the power sector, and general industry.Weir Minerals DivisionWeir Minerals is a world leader in the design andmanufacture of pumps, mill liners, hydrocyclones,slurry valves, screens, and rubber products for themining and minerals processing, dewatering, sulfurchemical and general industries. Based on advanced,and often patented, materials and designs, ourproducts are designed to add value to virtually anyaggressive, corrosive process.Superior wear life, low cost of operationIn slurry pumping, processing and control applications- where the cost of ownership often outweighscapital cost as a priority - we help our customersaddress issues such as longevity, capacity, efficiency ofoperation, and maintenance.Product strength lies in the superiority of our advancedhydraulic designs and our high performing wear andcorrosion resistant materials. Our leading research andmaterials scientists, plus our state of the art materialproduction facilities, support our world class productsand materials with a focus on superior wear life andlow cost of operation.Weir Minerals North AmericaLocated in Madison WI, Weir Minerals North Americais one of the many Weir Minerals facilities aroundthe world. These facilities include foundries, rubbermolding shops, and machining centers.1:A state-of-the-art hydraulic test laboratory is located in Madison, Wisconsin2:A Warman® 600 HTP pump being prepared for hydraulic testing. The massive rib reinforced casing and 102,000 lb (46,260 kg) bare weight illustrate the robust design and inherent safety of this 580 psi(4,000 kPa) rated pump 1: World class manufacturing facilities are part of Weir Minerals on six continents of the world2: A 20 ton fixture enables Weir Minerals to produce the largest slurry pumps in the world2New 4-vane Warman® WRT® impeller and matching throatbush is designed to improve wear performance, and assist our customers in reducing total ownership cost12Warman® horizontal slurry pump models include adiverse range of designs for the toughest duties.Warman® pumps deliver exceptional performanceThe Warman® horizontal slurry pump range is one of the world’s mostcomprehensive range of centrifugal slurry pumps for use in mining, chemical andindustrial applications. These horizontal slurry pumps are designed for ultra heavyduty applications such as mill discharge, process plant and tailings, high pressurepipelines, as well as other specialty applications.Typical applications and Warman® pump models most suitable for theseapplications are shown below. For special applications not listed, contact WeirMinerals North America or your local Weir Minerals representative. Since particlesize, concentration and abrasivity may affect your final selection, please consultWeir Minerals for final pump selection.Warman® AHP pumpWarman® horizontal pump models3servicesThe Warman® AH® pump is the world’s standard for the most difficult mill duties.A wide variety of impellers and shaft seals provide a perfect fit for a wide range of applications. The AH® pump provides excellent wear life while maintaining efficiency during the wear cycle, resulting in low total operating costs. The AH® pump, together with the Warman® MC™ pump series, provides a complete selection for most duties in the mill. From cyclone feed to regrind, flotation and tailings, the AH® pump is the best choice.4•Heavy duty construction with through-boltdesign provides ease of maintenance and minimaldowntime•Ductile iron fully lined casing provides durability,strength, safety, and long service life•Large diameter, slow turning, high efficiencyimpellers designed to achieve maximum wear lifeand low operating costs•Large, open internal passages designed to reduceinternal velocities, maximize wear life and loweroperating costs•Thick elastomer or alloy bolt-in liners providesuperior corrosion resistance plus offer ease of linerchange-out and interchangeability to reduce overallmaintenance costs and maximize wear life•Minimal shaft/impeller overhang reduces shaftdeflection and increases packing life•Cartridge-style bearing assembly allows formaintenance in a clean environment withoutremoval of the pump, resulting in reliable operationand prolonged bearing life•Grease or oil lubrication bearing assembly optionsoffer ease of maintenance and reduced downtime•Optional dry running shaft seal reduces or eliminatesflush water requirements•Effective expeller prolongs packing life whilereducing or eliminating flush water requirement Warman® AH®Warman® WRT®The new Warman® WRT®throatbush and impellercombination is a superiorupgrade for your existing pump,and is designed to enhanceefficiency and improve wearperformance5servicesThe Warman ® WBH ® slurry pump range offers more than 20 enhancements to the already state-of-the-art Warman ® AH ® slurry pumping technology, including a fully adjustable and rotatable throatbush to more evenly spread the wear and maintain the pump in tip-top performance for longer periods.Boasting a revolutionary one-piece frame for correct alignment of bearings, seal and impeller to front liner; as well as easier access for impeller adjustments, the WBH ® pump was built with enhanced efficiency and operational savings in mind.• One-point adjustment allows for adjusting the throatbush both rotationally and axially while the pump is in operation, overcoming localized wear• One-piece bearing frame design ensures correctalignment of bearings, seal and impeller • New hydraulics were shown to increase efficiency and lower energy consumption by up to 12% in the pump trials at CSA, Australia, compared with Warman ® AH ® pump in same duty • Large diameter expeller seals against high intake pressures without the need for gland seal water • Quick and easy impeller gap adjustments to maximize performance without shutdown • Fully lined design minimizes the risk of catastrophic failure with safety features including standard leak detection, optional vibration, temperature and wear monitoring, and the ability to add pressure relief and thermal cut-out devices • Warman ® Wear Reduction Technology (WRT ®) throatbush and four-vane impeller design with vanelets for extended wear life and reduced NPSH requirements • Large diameter shaft with short overhang combined with a robust and rigid one-piece bearing frame keeps the bearings aligned, which minimizes shaft deflection and vibration, as well as distortion from external piping loads • The one-piece bearing frame ensures goodcomponent alignment and concentricity through the seal area to reduce wear and extend seal lifeWarman ® WBH ®Warman ® WRT ®The new Warman ® WRT ® throatbush and impeller combination is a superiorupgrade for your existing pump and is designed to enhance efficiency and improve wear performanceWarman® MCR™/MC™ Metal/MCU™Severe duty lined pump designed for the most aggressive applications, such as mill circuitThe Warman® MC™ pump series is for the most aggressive wear applications. The Warman® MC™ pump easily manages large size particles in dense abrasive slurries and offers the right combination of ruggedness, durability, hydraulics and materials. From the most difficult mill discharge to water flushed crusher, the Warman® MC™pump series is the best choice.When paired with the Warman® AH® pump, virtually all the duties in your mill can be satisfied.•Ductile iron fully lined casing provides durability,strength, safety, and long service life•Large diameter, slow turning, high efficiencyimpellers designed to achieve maximum wear lifeand low operating costs•Large, open internal passages designed to reduceinternal velocities, maximize wear life and loweroperating costs•Unique, easily centered stuffing box reduces glandseal maintenance and extends packing life•Adjustable side liner maintains efficiency andextends service life (adjustable while running)•Quick wet end exchange minimizes downtime•Thick elastomer liners with alloy impellers providesuperior wear life on the most difficult cyclone feedand screen feed services•Interchangeable elastomer and alloy bolt-inliner offer ease of liner change-out and reducedmaintenance costs•Heavy duty construction with through-boltdesign provides ease of maintenance and minimaldowntime•Minimal shaft/impeller overhang reduces shaftdeflection and increases packing life•Cartridge-style bearing assembly allows formaintenance in a clean environment withoutremoval of the pump, resulting in reliable operationand prolonged bearing life•Separate fully removable suction cover on Warman®400 MCR™ pump facilitates access and replacementof the impeller, throatbush, and shaft sleeve withoutdisturbing coverplate or discharge piping•Left or right hand operation availableWarman® MCR™/MC™ Metal/MCU™WARMAN®Centrifugal Slurry Pumps6Warman® HTPFully lined pump for severe multi-stage applications which offers numerous ease of maintenance featuresThe Warman® HTP pump range represents the highest pressure-rated, large, lined pumps available from Weir Minerals with priority given to increased safety, wear life, and reliability.The Warman® HTP pump is rapidly establishing itself as the dominant pump in the Canadian oil sands, providing an efficient and durable solution to long distance hydro-transport and tailings duties.•Specifically designed hydraulics emphasize solidpassing capability, head generation, wear life,and efficiency to deliver overall outstandingperformance•Multi-stage high pressure operation to 580 psi•Major components designed with lifting pointslocated with respect to center of gravity andspecialized lifting tools enable rapid pumpmaintenance and turnarounds•Ductile iron fully lined casing provides durability,strength, safety, and long service life•Separate fully removable suction cover facilitatesaccess and replacement of impeller, throatbush,and shaft sleeve without disturbing coverplate ordischarge piping•Unique, easily centered stuffing box reduces glandseal maintenance and extends packing life•Grease or oil lubrication bearing assembly optionsoffer ease of maintenance and reduced downtime•Cartridge-style bearing assembly allows formaintenance in a clean environment withoutremoval of the pump, resulting in reliable operationand prolonged bearing life•Liner design reduces operating costs by allowingreplacement of individual components•Erosion and corrosion resistant elastomers or alloysare available to handle solids-laden and/or corrosiveslurriesWarman® HTP7 WARMAN®Centrifugal Slurry Pumps8Warman ® AHP/AHPPFully lined high pressure pump for multi-stage applicationsBased upon the popular Warman ® AH ® series pump, the Warman ® AHP/AHPPseries high pressure pump offers the same features and benefits as the AH ® pump, including identical hydraulics at up to 1000 psi.The high pressure capability allows the user to operate several pumps in series all consolidated into one pump house, saving the expense of supporting systems like gland water supply systems in an alternative design of several pump houses along the transport line.• Multi-stage high pressure operation to 1000 psi • Heavy duty construction with through-boltdesign provides ease of maintenance and minimal downtime• Ductile iron fully lined casing provides durability, strength, safety, and long service life • Large diameter, slow turning, high efficiencyimpellers designed to achieve maximum wear life and low operating costs • Large, open internal passages reduce internalvelocities, maximize wear life and lower operating costs • Thick elastomer or alloy bolt-in liners providesuperior corrosion resistance plus offer ease of liner change-out and interchangeability to reduce overall maintenance costs and maximize wear life • Minimal shaft/impeller overhang reduces shaft deflection and increases packing life • Grease or oil lubricated bearing options offer ease of maintenance and reduced downtime • Cartridge-style bearing assembly allows for maintenance in a clean environment withoutremoval of the pump, resulting in reliable operation and prolonged bearing lifeWarman ® AHPWARMAN ®Centrifugal Slurry PumpsWarman ® XUHeavy duty slurry pumpThe Warman ® XU pump range is Weir Mineral’s most recently released all metalunlined pump range that integrates newly designed wet end wear components with the long proven Warman ® mechanical end. Casing, impeller and liner have been optimized to provide low wear while delivering outstanding efficiency over a wide range of medium to heavy slurry applications such as coal, sand and gravel. With many unique features, the Warman ® XU pump is easy to maintain and is designed to offer the lowest cost of ownership in its class.Warman ® XU9• Configured volute casing distributes material at point of maximum wear to extend life when pumping large solids• Low V cutwater design reduces slurry velocities and wear in the casing, allowing operation over a wide range of flows • Five-vane, thick sectioned, high efficiency impellers offer maximum wear life and low operating costs • Patented impeller wear ring profile reduces wear on impeller and throatbush area by restricting recirculation • Unique “tear drop” shaped frame plate liner insert insures any localized side wall wear occurs on liner and not on casing • Wet end components constructed from abrasion resistant solid chrome iron, providing excellent wear life in most slurry applications • Multiple shaft sealing configurations are available to best suit application requirements and are easily converted from one to another without expensive mechanical end changes • Compact cartridge-style bearing assemblies offer reduced shaft/impeller overhang and minimize shaft deflection resulting in increased packing life and the ability to accept a range of mechanical seals • Exceptional dry gland sealing performance due to improved expeller/impeller ratios reduces flush water requirements and lowers operating costs • Full and low flush gland sealing options allow precise matching of seal water consumption to application needs • Grease or oil lubrication bearing assembly options offer ease of maintenance and reduced downtime • Quick release clamping collar design facilitates impeller removal • Hydraulically interchangeable with long proven Warman ® AH ® pump designsWARMAN ®Centrifugal Slurry PumpsWarman® AHF/LF/MFHeavy duty froth pump for tough flotation froth duties Designed to handle heavy froth, the Warman® horizontal froth pump has a unique inlet and impeller design that is very successful where others fail.A large oversized inlet with a unique impeller inducer blade handles heavy froth and higher viscosity dense slurries with ease. The Warman® AHF/LF/MF line of horizontal froth pumps has proven valuable for very dense slurries where viscosity starts to become a pumping issue for the standard slurry pump.10•Heavy duty construction with through-boltdesign provides ease of maintenance and minimaldowntime•Ductile iron fully lined casing provides durability,strength, safety, and long service life•Large diameter, slow turning, high efficiencyimpellers designed to achieve maximum wear lifeand low operating costs•Large, open internal passages designed to reduceinternal velocities, maximize wear life and loweroperating costs•Unique impeller design for most difficult frothapplications•Thick elastomer or alloy bolt-in liners providesuperior corrosion resistance plus offer ease of linerchange-out and interchangeability to reduce overallmaintenance costs and maximize wear life•Minimal shaft/impeller overhang reduces shaftdeflection and increases packing life•Cartridge-style bearing assembly allows formaintenance in a clean environment withoutremoval of the pump, resulting in reliable operationand prolonged bearing life•Standard Warman® AH® pump and Warman® Lpump can be converted by replacing cover plate,throatbush and impeller•Full flush, low flow or dry running centrifugal sealsminimize water usage and operating costsWarman® AHF/LF/MF*Lower light blue areas: recommended maximum operating range on aerated slurriesWARMAN®Centrifugal Slurry PumpsWarman ® Series 1000General purpose slurry pumpThe Warman® Series 1000 pump is a long proven horizontal end suction centrifugalpump that will reliably and economically handle abrasive and corrosive medium duty services.Several unique features make the Series 1000 pump ideal for handling stringy/fibrous slurries, low NPSHA applications and services that require minimum dilution due to gland seal water.• Heavy duty construction with through-bolt casing design provides ease of maintenance and minimal downtime • Erosion and corrosion resistant elastomers or metal alloy liners are available to handle solids-laden and/or corrosive slurries • Semi-open impeller easily passes large or stringy particles and is well suited for froth-laden slurries • Unique impeller hydraulic design allows operation in systems with low NPSHA • Cartridge-style bearing assemblies offer a compact reliable design that reduces shaft/impeller overhang, decreasing deflection for improved packing life and allows for easy rebuilds • Multiple shaft sealing configurations are available to best suit application requirements including standard wet and dry glands as well as mechanical seals • Effective expeller prolongs packing life while reducing or eliminating flush water requirement • Casing drain plug allows for component wearinspection as well as draining slurry from the pump to prevent freezing or corrosion after flushing • Grease or oil lubricated bearing assemblies offer ease of maintenance and reduce downtime11Warman ® Series 1000WARMAN ®Centrifugal Slurry PumpsWarman® HH/H/HRMHeavy duty high head lined slurry pumpThe Warman® HH/H/HRM pump lines were designed to produce high heads per stage at high pressures.Commonly used for long distance transport lines, the Warman® HH/H/HRM pump lines can often satisfy application duties with a single pump where others require multiple pumps in series.12•Ductile iron fully lined casing provides durability,strength and long service life•Multi-stage high pressure operation to 750 psi(Warman® H pump to 1000 psi)•Heavy duty construction with through-boltdesign provides ease of maintenance and minimaldowntime•Large diameter, slow turning, high efficiencyimpellers designed to achieve maximum wear lifeand low operating costs•Large, open internal passages designed to maximizewear life and lower operating costs•Thick elastomer and alloy liners provide superiorcorrosion resistance and maximum wear life•Full flush gland, low flow, and dry runningcentrifugal seals reduce flush water usageminimizing pump operating costsWarman® HH/HRMWARMAN®Centrifugal Slurry PumpsWarman ® LRugged heavy duty slurry pump for medium to lower headsThe Warman ® L series pumps incorporate the same design points as the Warman ® AH ® pump plus higher efficiency impellers at an attractive initial cost.Designed for rugged duties while offering higher efficiencies, the Warman ® L series is a combination of the proven Warman ® AH ® pump’s unique features. The Warman ® L series provides the widest range of hydraulics from the 3/4” to a 26” discharge pumps. The 3/4” is perfect for the laboratory or in demonstration plants.• Heavy duty construction with through-boltdesign provides ease of maintenance and minimal downtime • Ductile iron fully lined casing provides durability, strength, safety, and long service life • Large diameter, slow turning, high efficiencyimpellers designed to achieve maximum wear life and low operating costs • Large, open internal passages designed to reduce internal velocities, maximize wear life and lower operating costs • Thick elastomer or alloy bolt-in liners providesuperior corrosion resistance plus offer ease of liner change-out and interchangeability to reduce overall maintenance costs and maximize wear life • Designed for rugged duties while offering excellent efficiencies • Minimal shaft/impeller overhang reduces shaft deflection and increases packing life • Cartridge-style bearing assembly allows for maintenance in a clean environment withoutremoval of the pump, resulting in reliable operation and prolonged bearing life • Grease or oil lubrication bearing assembly options offer ease of maintenance and reduced downtime • Full flush gland, low flow, and dry running centrifugal seals reduce flush water usage minimizing pump operating costs • Mechanical seals reduce flush water usage, minimizing pump operating costs13Warman ® LWARMAN ®Centrifugal Slurry PumpsWarman® GSLAbsorber recycle pumpSince the introduction of the first Flue Gas Desulfurization (FGD) systems in the 1970s, Weir Minerals has supplied more than 4,000 specially designed FGD pumps worldwide.Warman® GSL pumps have the highest efficiencies in the industry achievable throughout the life of the impeller.14Warman® GSL•Ductile iron fully lined casing provides durability,strength, safety, and long service life•Cartridge-style bearing assembly allows formaintenance in a clean environment withoutremoval of the pump, resulting in reliable operationand prolonged bearing life•High efficiency design minimizes energyconsumption and reduces operating costs•Liner design reduces operating costs by allowingreplacement of individual components•Back pull design affords easy maintenance•Mechanical seals reduce flush water usageminimizing pump operating costs• Warman® GSL pump design incorporates thelatest material development, hydraulic designimprovements and modern manufacturingmethods of the Warman® L pump WARMAN®Centrifugal Slurry PumpsNew Warman® GSL polymer castceramic components available.Contact your local Weir Minerals salesrepresentative for more information.®Warman ® WGR ®Medium duty slurry pumps for sand and aggregate applicationsThe streamlined design allows easy access to all parts of the pump and theinternal components, making servicing easier and reducing downtime. When this is combined with the long service life of our parts and the proven wear life of our proprietary Linatex ® premium rubber, Weir Minerals provides pumping solutions that are designed to achieve the lowest total cost of ownership in operation.Warman ®WGR ®pump - quick selection chart• Our new patented Warman ® WRT ® throatbush and impeller designs minimize turbulence and cavitation for extended wear life and maintenance performance • Impeller and gland assembly can be replaced through the suction side of the pump• Replaceable Linatex ® rubber liners provide superiorabrasion resistant performance in fine slurry applications • Patented flexible discharge adaptor is the same size as the inlet and positioned so the pump can be fully serviced without removing the discharge piping • Loose swivel flanges are offered to match mating pipe orientations • Adjustable impeller with release collar can beadjusted externally to achieve optimum clearance between the impeller and the throatbush for the full working life of the wear components • Newly designed larger impeller allows for lower speeds which results in longer wear life • Incorporation of the removable suction cover in the cover plate means that the throatbush can be replaced without incurring the cost of removal of the cover plate • New design gives increased durability, resulting in lower overall lifetime costsWarman ® WGR ®1001000 10000Flowrate ( usgpm )351008050250200150T o t a l h ea d (f e e t )US gallons per minute (gpm)0 20406080100120 14016010H e a d ( f t ) Warman ® WRT ®The new Warman ® WRT ®throatbush and impeller combination is a superiorupgrade for your existing pump, and is designed to enhance efficiency and improve wear performanceCubic meters per hour (m /hr)Total head (meters)15For further information on any of these products or our support services contact your nearest sales office or visit:WARMAN ® Centrifugal Slurry Pumps GEHO ® PD Slurry PumpsLINATEX ® Rubber Products VULCO ® Wear Resistant Linings CAVEX ® HydrocyclonesFLOWA Y ® PUMPS Vertical Turbine Pumps ISOGATE ® Slurry ValvesMULTIFLO ® Mine Dewatering Solutions HAZLETON ® Specialty Slurry PumpsLEWIS ® PUMPS Vertical Chemical Pumps WEIR MINERALS SERVICES™Copyright © 2008, 2012 Weir Slurry Group, Inc.. All rights reserved. WARMAN is a registered trademark of Weir Minerals Australia Ltd and Weir Group African IP Ltd; CAVEX, HAZLETON, AH, WRT, WBH, WGR and MULTIFLO are registered trademarks of Weir Minerals Australia Ltd; LEWIS and LEWIS PUMPS are registered trademarks of Envirotech Pumpsystems Inc; GEHO is a registered trademark of Weir Minerals Netherlands bv; FLOWAY is a registered trademark of Weir Floway Inc.; VULCO is a registered trademark of Vulco SA; ISOGATE is a registered trademark of Weir do Brasil Ltda.; LINATEX is a registered trademark of Linatex Ltd; SENTINEL is a registered trademark of Weir Slurry Group, Inc.; MC, MCR and MCU are trademarks of Weir Slurry Group, Inc.; WEIR is a registered trademark of Weir Engineering Services Ltd. Certain features of some of the products featured in this publication are protected worldwide by patents pending and registered.The Weir Minerals Services ™ Sentinel ® program is a team concept providing lower Measured Total Ownership Cost (MTOC) throughimproved reliability, lower power consumption and reduced maintenance cost.Our menu approach allows each customer to select the level of commitment and participation they feel best meets their needs.Weir Minerals Services ™ Sentinel ® Program Pump users enter into formal agreements with Weir Minerals with the aim of benefiting from ongoing reductions in operating costs.WEIR MINERALS SERVICES ™Weir Minerals Services ™ Sentinel ® Program modules include:• Cooperative cost focus groups • Pump audits• Equipment maintenance monitoring • Wear life monitoring• Performance based agreements • Spare parts supply agreements • Customized training programs • Equipment rebuild services • Pump exchange services •Tailored maintenance packages。