塑料制品的设计
塑料制品的结构设计规范

塑料制品的结构设计规范1双林汽车部件股份有限公司企业技术规范塑料制品的结构设计规范-10-20发布 -10-XX实施双林汽车部件股份有限公司发布塑料制品的结构设计又称塑料制品的功能特性设计或塑料制品的工艺性。
§1 塑料制品设计的一般程序和原则1.1 塑料制品设计的一般程序1、详细了解塑料制品的功能、环境条件和载荷条件2、选定塑料品种3、制定初步设计方案, 绘制制品草图( 形状、尺寸、壁厚、加强筋、孔的位置等)4、样品制造、进行模拟试验或实际使用条件的试验5、制品设计、绘制正规制品图纸6、编制文件, 包括塑料制品设计说明书和技术条件等。
1.2 塑料制品设计的一般原则1、在选料方面需考虑: (1) 塑料的物理机械性能, 如强度、刚性、韧性、弹性、吸水性以及对应力的敏感性等; (2) 塑料的成型工艺性, 如流动性、结晶速率, 对成型温度、压力的敏感性等; (3) 塑料制品在成型后的收缩情况, 及各向收缩率的差异。
2、在制品形状方面: 能满足使用要求, 有利于充模、排气、补缩, 同时能适应高效冷却硬化( 热塑性塑料制品) 或快速受热固化( 热固性塑料制品) 等。
3、在模具方面: 应考虑它的总体结构, 特别是抽芯与脱出制品的复杂程度。
同时应充分考虑模具零件的形状及其制造工艺, 以便使制品具有较好的经济性。
4、在成本方面: 要考虑注射制品的利润率、年产量、原料价格、使用寿命和更换期限, 尽可能降低成本。
§2 塑料制品的收缩塑料制品在成型过程中存在尺寸变小的收缩现象, 收缩的大小用收缩率表示。
%10000⨯-=L LL S 式中S ——收缩率;L 0——室温时的模具尺寸; L ——室温时的塑料制品尺寸。
影响收缩率的主要因素有:(1) 成型压力。
型腔内的压力越大, 成型后的收缩越小。
非结晶型塑料和结晶型塑料的收缩率随内压的增大分别呈直线和曲线形状下降。
(2) 注射温度。
温度升高, 塑料的膨胀系数增大, 塑料制品的收缩率增大。
塑料制品的设计

塑料制品的设计塑料制品的设计不仅要满足使用要求,而且要符合塑料成型的工艺特点,并且尽可能的使模具简单化。
这样既是成型工艺稳定,保证塑料制品的质量,又可以降低生产成本。
塑料制品要考虑一下因素。
1、塑料性能:塑料的物理学性能和工艺性能。
2、成型方法:要看具体的成型工艺要确定设计法案。
3、模具结构和制造工艺:要利于模具结构简化和方便制造。
一、塑料制品结构设计的一般原则1、力求使制品结构简单,避免侧向凹凸结构,使模具结构简单,易于制造;设计塑料制品时,应满足塑料制品功能的要求的前提下,力求使制品结构简单,尤其是要尽量避免侧向凹凸结构。
因为侧向凹凸结构需要模具增加侧向抽心或斜顶机构,使得模具变复杂,并增加成本。
如果侧向凸凹结构不可避免,则应该使侧向凸凹结构简单化,这里有两种方法可以避免模具采用侧向抽心或斜顶机构:强行脱模和对插。
•注:关于强行脱模:1) 当侧向凹凸较浅且允许有圆角时,可强行脱模; 2)可强行脱模的塑料有PE 、PP 、POM 和PVC 等;斜顶上图的W 不宜小于1/3H 。
制品设计时除了尽量避免侧向抽心外,还力求时模具的其它结构也简单耐用,主要包括一下几方面。
(1) 模具成型零件上不得有尖利和薄弱结构。
模具上的尖利或薄弱结构会影响模具强度及使用寿命。
制品设计时应尽量避免这种现象出现。
制品模具(2)尽可能使成型零件简单易加工。
型芯复杂,难以加工型芯则较容易加工(3)尽量使分型面变得简单。
简单的分型面使模具加工容易,生产时不易产生飞边,容易切除水口。
分型线为阶梯形状,模具加工困难改为直线或曲面,使得模具加工较为容易2、壁厚均匀,避免出现过厚或过薄的胶位壁厚均匀为塑料制件设计的第一原则,应尽量避免出现过厚或过薄的胶位。
这一点即使在转角部位也非常重要。
因为壁厚不均会使制件冷却后收缩不均,造成凹陷,产生内应力、变形及破裂等。
另外,成型制件的冷却时间取决于壁厚角厚的部分,壁厚不均会使成型周期延长,降低生产效率。
塑料制品的结构设计规范
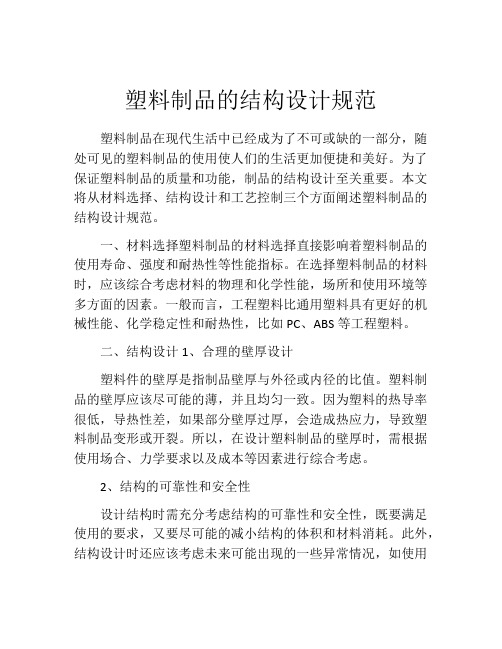
塑料制品的结构设计规范塑料制品在现代生活中已经成为了不可或缺的一部分,随处可见的塑料制品的使用使人们的生活更加便捷和美好。
为了保证塑料制品的质量和功能,制品的结构设计至关重要。
本文将从材料选择、结构设计和工艺控制三个方面阐述塑料制品的结构设计规范。
一、材料选择塑料制品的材料选择直接影响着塑料制品的使用寿命、强度和耐热性等性能指标。
在选择塑料制品的材料时,应该综合考虑材料的物理和化学性能,场所和使用环境等多方面的因素。
一般而言,工程塑料比通用塑料具有更好的机械性能、化学稳定性和耐热性,比如PC、ABS等工程塑料。
二、结构设计1、合理的壁厚设计塑料件的壁厚是指制品壁厚与外径或内径的比值。
塑料制品的壁厚应该尽可能的薄,并且均匀一致。
因为塑料的热导率很低,导热性差,如果部分壁厚过厚,会造成热应力,导致塑料制品变形或开裂。
所以,在设计塑料制品的壁厚时,需根据使用场合、力学要求以及成本等因素进行综合考虑。
2、结构的可靠性和安全性设计结构时需充分考虑结构的可靠性和安全性,既要满足使用的要求,又要尽可能的减小结构的体积和材料消耗。
此外,结构设计时还应该考虑未来可能出现的一些异常情况,如使用环境的变化、超负荷的物理作用和力学应力等因素都应该在结构设计中进行考虑。
三、工艺控制优秀的结构设计标准是塑料制品质量保证的前提,但良好的生产工艺过程也是确保质量的关键。
生产过程中应该选择先进的生产工艺技术,如模具设计、注塑机选型和注射参数的调控等。
此外,应该做好产品的标准化、精细化生产和检验工作,以确保产品品质达到标准。
综上所述,塑料制品的结构设计对产品质量至关重要,必须遵循一定的规范和标准进行设计和制造。
同时,在生产过程中也需要遵循简单、精细、标准化、自动化和人性化原则。
一旦遇到质量问题,企业应该采取积极有效的措施,及时处理,以免造成不必要的损失和影响公司声誉。
塑料制品的常见结构设计
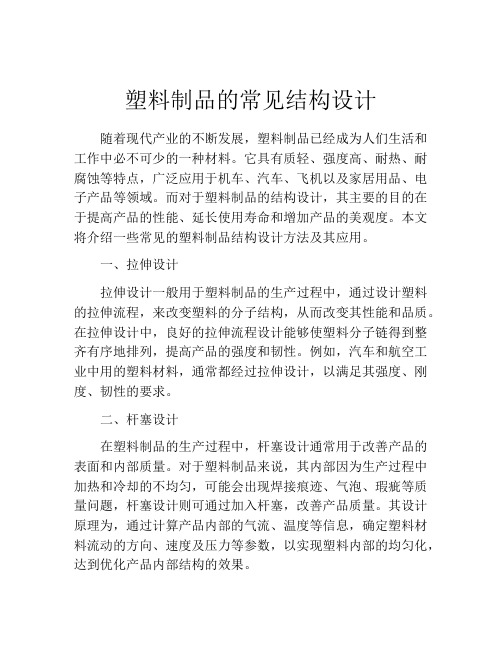
塑料制品的常见结构设计随着现代产业的不断发展,塑料制品已经成为人们生活和工作中必不可少的一种材料。
它具有质轻、强度高、耐热、耐腐蚀等特点,广泛应用于机车、汽车、飞机以及家居用品、电子产品等领域。
而对于塑料制品的结构设计,其主要的目的在于提高产品的性能、延长使用寿命和增加产品的美观度。
本文将介绍一些常见的塑料制品结构设计方法及其应用。
一、拉伸设计拉伸设计一般用于塑料制品的生产过程中,通过设计塑料的拉伸流程,来改变塑料的分子结构,从而改变其性能和品质。
在拉伸设计中,良好的拉伸流程设计能够使塑料分子链得到整齐有序地排列,提高产品的强度和韧性。
例如,汽车和航空工业中用的塑料材料,通常都经过拉伸设计,以满足其强度、刚度、韧性的要求。
二、杆塞设计在塑料制品的生产过程中,杆塞设计通常用于改善产品的表面和内部质量。
对于塑料制品来说,其内部因为生产过程中加热和冷却的不均匀,可能会出现焊接痕迹、气泡、瑕疵等质量问题,杆塞设计则可通过加入杆塞,改善产品质量。
其设计原理为,通过计算产品内部的气流、温度等信息,确定塑料材料流动的方向、速度及压力等参数,以实现塑料内部的均匀化,达到优化产品内部结构的效果。
三、针轮设计针轮设计是一种常用于塑料制品挤压成型中的提高产品质量的方法。
它通过改善挤压过程中塑料流动的方向和速度,使得塑料分子链得到更加有序地排布,从而提高产品的强度和韧性。
其中,针轮是双螺杆挤出机的关键部件,在挤出过程中不断旋转,挤出材料。
针轮设计的核心在于,通过调节针轮的几何参数,使得塑料在针轮的作用下能够得到更充分的塑性变形和拉伸效应,达到优化材料微观结构的效果。
四、辊子设计辊子设计通常应用于塑料薄膜的生产过程中。
塑料薄膜是一种高强度、美观、防水、防镜面反射等重要用途的塑料制品,其质量关键在于生产过程中的辊子设计。
在辊子设计中,优秀的辊子设计能够使塑料薄膜表面均匀、色彩鲜艳、质地光滑。
其设计原理为,在制膜过程中,通过调整压力、速度和温度等参数,使辊子能够完全与塑料材料接触,并实现微观结构的改变,从而优化防水、防结霜以及降低声学反射等性能。
塑料制品的设计(强行脱模、表面质量)

塑胶制品结构的设计
一.制品结构工艺设计的原则:
1.在保证制品性能和使用要求的情况下,尽量选用价廉、且成型性能好的塑料;
2.力求使制品结构简单,避免侧向凹凸结构,使模具结构简单,易于制造;(内侧凹凸结构有两种情况可不用内行位:碰穿和强行脱模)
•注:关于强行脱模:
1)当侧向凹凸较浅且允许有圆角时,可强行脱模;
2)可强行脱模的塑料有PE、PP、POM和PVC等;
三、制品的表面质量:
1、包括制造质量:型腔省模抛光,一般模具型腔粗糙度为
Ra0.02—1.25um,制品的粗糙度比模具型腔粗糙度低1-2级。
2、注塑质量:水花,蛇纹,熔接痕,顶白变形,黑斑,披锋、
凹痕等。
3、烤柒质量:
4、电镀质量:
5、丝印质量:
6、拉丝质量:
7、抛光质量:
8、汤金质量
9、贴纸质量
10、贴片
四.塑料制品的常见结构设计:
1.脱模斜度:
1).不同塑料的脱模斜度不同,在不影响产品性能的情况下,脱模斜度尽量取较大值;
2).脱模斜度不包括在公差范围之内;
3).晒纹脱模斜度应取较大值,
一般为3°~9°;
4).硬质塑料比软质塑料的脱模斜度大,收缩率大的塑料比收缩率小的脱模斜度大;
5)、制品高度越高,孔越深,为保证精度要求,脱模斜度宜取小一点;
6)、制品形状复杂难脱模时,脱模斜度要大一些;
7)、前模脱模斜度大于后模脱模斜度;
8)、配合精度要求越高,脱模斜度要越小;
9)、壁厚大的制品,脱模斜度可取较大值;机械性能强塑料,自润滑性塑料,脱模斜度可取小一些。
塑料制品的设计
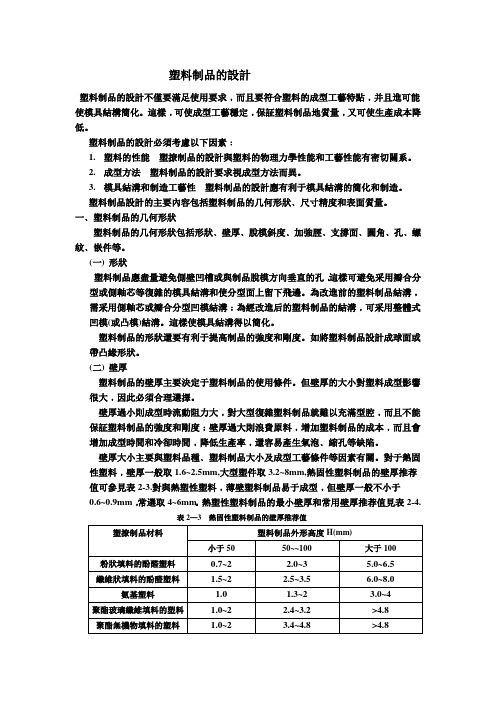
塑料制品的設計塑料制品的設計不僅要滿足使用要求﹐而且要符合塑料的成型工藝特點﹐并且進可能使模具結構簡化。
這樣﹐可使成型工藝穩定﹐保証塑料制品地質量﹐又可使生產成本降低。
塑料制品的設計必須考慮以下因素﹕1.塑料的性能塑撩制品的設計與塑料的物理力學性能和工藝性能有密切關系。
2.成型方法塑料制品的設計要求視成型方法而異。
3.模具結溝和制造工藝性塑料制品的設計應有利于模具結溝的簡化和制造。
塑料制品設計的主要內容包括塑料制品的几何形狀﹑尺寸精度和表面質量。
一﹑塑料制品的几何形狀塑料制品的几何形狀包括形狀﹑壁厚﹑脫模斜度﹑加強脛﹑支撐面﹑圓角﹑孔﹑螺紋﹑嵌件等。
(一)形狀塑料制品應盡量避免側壁凹槽或與制品脫模方向垂直的孔﹐這樣可避免采用瓣合分型或側軸芯等復雜的模具結溝和使分型面上留下飛邊。
為改進前的塑料制品結溝﹐需采用側軸芯或瓣合分型凹模結溝﹔為經改進后的塑料制品的結溝﹐可采用整體式凹模(或凸模)結溝。
這樣使模具結溝得以簡化。
塑料制品的形狀還要有利于提高制品的強度和剛度。
如將塑料制品設計成球面或帶凸緣形狀。
(二)壁厚塑料制品的壁厚主要決定于塑料制品的使用條件。
但壁厚的大小對塑料成型影響很大﹐因此必須合理選擇。
壁厚過小則成型時流動阻力大﹐對大型復雜塑料制品就難以充滿型腔﹐而且不能保証塑料制品的強度和剛度﹔壁厚過大則浪費原料﹐增加塑料制品的成本﹐而且會增加成型時間和冷卻時間﹐降低生產率﹐還容易產生氣泡﹑縮孔等缺陷。
壁厚大小主要與塑料品種﹑塑料制品大小及成型工藝條件等因素有關。
對于熱固性塑料﹐壁厚一般取1.6~2.5mm,大型塑件取3.2~8mm,熱固性塑料制品的壁厚推荐值可參見表2-3.對與熱塑性塑料﹐薄壁塑料制品易于成型﹐但壁厚一般不小于0.6~0.9mm﹐常選取4~6mm。
熱塑性塑料制品的最小壁厚和常用壁厚推荐值見表2-4.表2—3 熱固性塑料制品的壁厚推荐值表2—4 熱塑性塑料制品的最小壁厚和常用壁厚推荐值(mm)塑料制品的壁厚一般應力求均勻﹐否則會因固化或冷卻速度不同而引起收縮不均勻﹐產生內應力﹐導致塑料制品產生翹曲變形或縮孔。
塑料制品设计
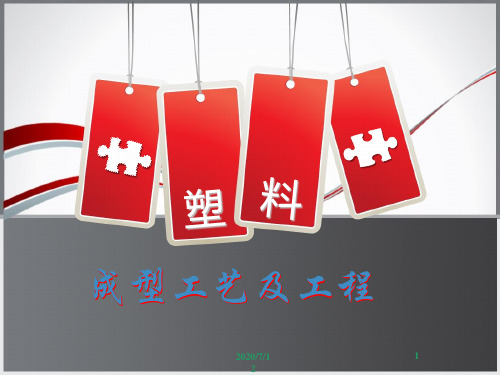
2.1 塑件的几何形状及结构设计
2.脱模斜度
为了便于塑件脱模,防止脱模时擦伤塑件,必 须在塑件内外表面脱模方向上留有足够的斜度α,
在模具上称为脱模斜度。
脱模斜度取决于 塑件的形状、壁厚 及塑料的收缩率,
一般取30 ′~1°30′
。
2.1 塑件的几何形状及结构设计 2.脱模斜度 脱模斜度表示方法:
2.1 塑件的几何形状及结构设计
6.孔的设计
(1) 孔的极限尺寸
模塑通孔要求孔径比(长度与孔径的比值)要小些
(2)孔间距 孔与孔间、孔与塑件边缘间距离应足够大 (3)孔的类型 通孔、盲孔和异形孔
通孔、盲孔加工方法: 直接模塑出来 模塑成盲孔再钻孔通 塑件成型后再钻孔
异形孔设计实例
2 .2 塑件螺纹的设计
加强筋与 支承面间 留有间隙
2.1 塑件的几何形状及结构设计
4.塑件的支承面 通常塑件一般不以整个平面作为支承面,而是
以底脚或边框为支承面。
2.1 塑件的几何形状及结构设计 4.塑件的支承面 支承面结构形式
2.1 塑件的几何形状及结构设计
5.圆角 在满足使用要求的前提下,制件的所有的ቤተ መጻሕፍቲ ባይዱ角尽
可能设计成圆角,或者用圆弧过渡。
• 中心距尺寸偏差数据除以2,冠(+-)
一般配合部分尺寸精度高于非配合部分尺寸 精度。
模具尺寸精度比塑件尺寸精度高2-3级。
1.3 塑件的表面质量
表面质量
表面粗糙度、光亮程度 色彩均匀性 表面缺陷:缩孔、凹陷 推杆痕迹 对拼缝、熔接痕、毛刺等
一般模具表面粗糙度要比塑件的要求高 1~2级
2 塑件结构设计及典型实例
1.2 塑件的尺寸和精度
2.塑件的精度
塑料制品的设计规范
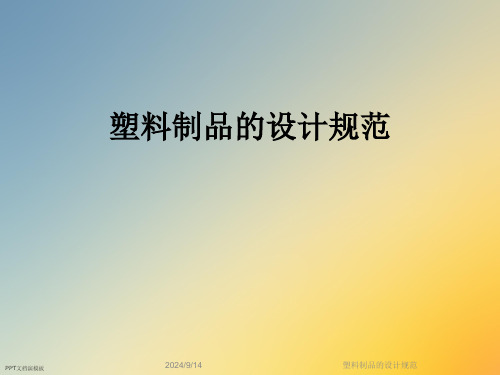
的充模流动阻力。如图3-13 ⑵应避免或减少塑料的局部集中,
以防止产生凹陷和气泡。如图3-14 ⑶加强筋以设计矮一些多一些为好。 ⑷筋与筋的间隔距离应大于塑件的
壁厚。
PPT文档演模板
塑料制品的设计规范
3.4.5 增加刚性减少变形的其他措施
将薄壳状的塑件设计为球面, 拱曲面等, 可 以有效地增加刚性、减少变形。
PPT文档演模板
塑料制品的设计规范
3.4.3 加强筋及其它增强结构
为了提高塑件的强度和防止塑件翘曲变形, 常设计加强筋,如图筋的设置位置应沿塑料 充模流向,降低充模流动阻力. 见图3-12
加强筋的正确形状和尺寸比例如图3-15 所示。
PPT文档演模板
塑料制品的设计规范
3.4.4 加强筋的主要形式
PPT文档演模板
塑料制品的设计规范
3.2 尺寸精度与表面质量
3.2.1 尺寸精度 3.2.2 尺寸精度的确定 3.2.3 表面质量
PPT文档演模板
塑料制品的设计规范
3.2 尺寸精度与表面质量
3.2.1 尺寸精度 1、塑件尺寸概念
塑件尺寸——塑件的总体尺寸。 2.塑料制品总体尺寸受限制的主要 因素:
PPT文档演模板
塑料制品的设计规范
3.2 尺寸精度与表面质量
3.2.2 尺寸精度的确定
表3—1是模塑件尺寸公差国家标 准(GB/T 14486-1993), 表 3—2是常用塑料材料的公差等级选 用。
将表3—1和表3—2结合起来使
用, 先查表3—2, 根据模塑件的材料
品种及用要求选定塑件的尺寸精度
图3—6 可强制脱模的浅侧凹结构
a)(A-B)×100%/B≤5% b) (A-B)×100%/C≤5%
- 1、下载文档前请自行甄别文档内容的完整性,平台不提供额外的编辑、内容补充、找答案等附加服务。
- 2、"仅部分预览"的文档,不可在线预览部分如存在完整性等问题,可反馈申请退款(可完整预览的文档不适用该条件!)。
- 3、如文档侵犯您的权益,请联系客服反馈,我们会尽快为您处理(人工客服工作时间:9:00-18:30)。
第1讲1、塑料制品的新成型方法与新材料改善普通成型的缺陷。
答:气体辅助注射成型、水辅成型技术、注射压制成型技术、热流道技术、低压注射成型、可熔芯技术的注射成型。
常规塑料制品成型方法容易出现精度低、内应力大、翘曲变形、表面凹陷、内部缩孔、外观档次低、光泽差等各种缺陷。
2、设计塑料产品要求既要考虑使用者(在功能上、在使用操作上、在外型上、材料应用与加工方法上),又要考虑企业(将来性、技术性、领先性、销售可能性、经济性);新制品产生的方式有(再设计、组合、创新)。
3、塑料制品设计的特点是:必须材料考虑物性,尤其是环境变化对物性影响及在长时间负载下对产品影响。
第2讲1、塑料制品开发包括:答:市场需求分析,产品造型设计,模具方案设计和模具结构设计,模具工程分析,模具制造装配,制品生产,产品检验2、串行工程与并行工程优缺点答:优点:(1)、制品开发的各个环节可及时接受其他环节的分析和反馈,并立即进行修改,提高了设计质量和可靠性。
(2)、充分利用了各个环节的时域交叉性,几个环节同时进行,大大缩短了模具产品的开发周期性。
(3)、不构成修改的大循环,降低了总的开发成本。
缺点:(1)整个开发过程信息单向流动,下游结果不能及时反馈给上游进行评价和修改;(2)制品设计和模具设计脱节,制品设计的质量靠最终生产来检验,往往要多次修模,不易控制各环节质量;(3)、各阶段按顺序进行导致产品开发周期长。
3、逆向工程答:现在采用三坐标测量机,将模拟信息转化为数字化的模型,这种通过样件开发产品的过程称为逆向工程4、快速原型(不考)5、设计塑料制品应考虑塑料材料的如下性能:材料的使用性能、材料的成型性能、材料的经济性6、塑料材料的加工性1)评定塑料可模性的目的:确定加工条件;评定物料成型各种制品可能性;试制新的塑料品种和改性。
2)评定方法:一般用能生产合格制品的速率和难易度来评价。
测定成型速率最好的办法是测定最短注射周期;测定成型难易程度是确立完成充模的温度和压力的综合工艺窗口,最直观的办法是绘制成型图。
第3讲掌握分析塑料制品力学状态,简支梁与柱体的力学计算第4讲1、塑料制品的尺寸为满足装配和使用,必须确定恰当的尺寸精度和形位精度,使制品具有互换性,既满足要求又能尽量降低成本。
2、塑件精度取决于原料、模具、设备、工艺和环境条件。
3、国内外塑料件尺寸标准的特点俄罗斯:公差表包含了尺寸分段、精度等级、配合座别和上下偏差;也有基孔制、基轴制。
德国:只有公差值,没有配合,也没有上下偏差。
美国:每种塑料分为精密、标准和粗糙三个精度等级,三个尺寸段0~6英寸、6~12及大于12。
我国标准的尺寸范围从0~1000,分28个尺寸段,其中0~500分25段。
该标准参照了德国标准DIN16901-1982,但有差异4、塑件表面粗糙度跟哪些有关。
答:由模具型腔表面粗糙度和所成型塑料的品种和成型加工方法决定第5讲1、设计塑料制品必须考虑模具的限制,以保证制品的成型、防止产生缺陷,并简化模具结构,降低成本,提高生产效率。
2、模具工程师对塑件结构分析(工艺性)应考虑:(1)注塑工艺对胶件结构的要求;(2)模具对胶件结构的要求;(3)产品装配对胶件结构的要求;(4)表面要求。
3、侧凸凹制品成型中的不利点:(1) 模具结构复杂,需采用对开式型腔、伸缩式型芯、侧向抽芯等结构。
(2) 模具制造费用加大,制造周期加长。
(3) 制品模塑周期加长,生产成本增加。
(4) 模具分型面缝隙溢料机会增多,制品的飞边多因此塑件应尽量避免侧面凸凹;若结构要求一定要抽芯,应尽量使抽芯机构简单。
4、制品成型后冷却收缩而包紧型芯,为便于脱模,以避免出现顶白、顶伤和拖白现象,在制品内外壁面平行于脱模方向应设有一定的脱模斜度。
脱模斜度与胶料性能、胶件形状、表面要求有关。
5、理解掌握选取脱模斜度的原则答:热固性塑料制品,脱模斜度小收缩率大,脱模斜度大刚性大,脱模斜度小壁愈厚,脱模斜度大制品的几何形状复杂而且很不规则,脱模斜度大制品较大、长度较长、高度较高的尺寸,脱模斜度小,以保证制品的尺寸精度若考虑留模,制品的内表面的脱模斜度可比外表面小;反之,外表面的脱模斜度应小于其内表面的脱模斜度。
成型增强塑料制品,脱模斜度大。
成型含有润滑剂、增塑剂等的塑料制品,脱模斜度比不含有的可小一些。
斜度的方向:当塑件为轴,应保证大端尺寸,塑件为孔,应保证小端尺寸;一般制品脱模斜度不包括在制品公差范围内。
6、脱模斜度表示方法:线性、比例、角度P1127、制品壁厚的作用(1) 使制品具有确定的结构和一定的强度、刚度,以满足制品的使用要求。
(2) 成型时具有良好的流动状态(如壁不能过薄)以及充填和冷却效果(如壁不能太厚)(3) 合理的壁厚使制品能顺利地从模具中顶出。
(4) 满足嵌件固定及零件装配等强度的要求。
(5) 防止制品翘曲变形。
8、壁厚设计的原则壁厚尽可能均匀一致,以便消除或减小制品内应力,防止模塑制品翘曲变形和开裂;满足要求前提下尽量减小壁厚,节省原料和缩短成型时间。
壁厚若不均匀,不能相差太多,应采用逐步过渡的形式或将制品设计成两个。
9、加强筋的作用1)在不增加整个制品厚度的条件下,增加制品的刚度和强度;2)适当地使用加强筋,能有效地克服制品扭曲、变形现象;3)起辅助流道作用,改善熔料的充模流动,有利于制品成型;4)减小制品厚度,能避免壁厚过大而产生缩孔、气泡、凹陷等现象,且能减轻制品质量。
10、加强筋设计原则(理解)1)方向:加强筋的走向应与熔料充模方向一致,与模具成型零件的运动方向一致,还应与制品的收缩方向一致。
2)高度:加强筋的高度不宜过大,宜设计得低一些、多一些,加强筋之间的中心距应大于2倍制品壁厚。
3)尽量避免在加强筋上装置任何零部件。
4)筋的根部用圆弧过渡,以避免外力作用时产生应力集中而破坏。
但根部圆角半径过大则会出现凹陷。
11、塑料制品上圆角的作用1)成型时,料流阻力小,改善了充模流动状态,利于充模与成型;2)可以减少因塑料收缩而导致的制品变形;3)避免因锐角而引起的应力集中,提高制品的强度;4)有时圆弧过渡改善制品外观;5)圆角可降低模具零件内应力、防止变形开裂,提高强度,延长模具寿命。
12、当塑件需要支撑面时,应采用凸起的边框或几个凸起的支脚作为支承,一整个面作支承面很难得到平直的表面。
第6讲1、塑料制品上得到孔的方法有:模塑成型,机械加工,模塑成型与机械加工相结合,冲压2、凸台作用:(作用)增强孔或供装配零件连接固定,承受应力和减少应变,(位置)一般设置在制品边缘及加强筋部位。
3、制品边缘、大面积部位为增加制品的刚度、强度,防止变形,应设计成特殊结构。
3、塑料制品上获得螺纹的方法:机械加工、模塑成型、螺纹嵌件。
4、塑料制品上使用的螺纹结构形状的选择P1345、塑料制品螺纹设计时始端与末端应有过渡段;塑料螺纹与金属螺纹的配合长度不能太长小于螺纹大径1.5倍;同一制品多段螺纹,螺纹旋向应相同;螺纹制品应设计有止转部分;应尽量采用公制标准螺纹。
6、塑料制品表面的花纹,可遮掩成型过程中的缺陷,增加美观,增大摩擦力,防止滑动;增加粘接表面积及粘接可靠性,粘结表面上作出细麻纹。
第7讲1、塑料制品上直接成型的三种形式文字:凸出制品表面:塑件文字为凸形,则模具为凹形,可用机械或手工雕刻,制造容易,但文字在使用中容易损坏;凹入制品表面:制品文字为凹形,相应模具为凸,用雕刻,则加工面积大,加工量大,粗糙度难保证,应尽量避免;凹坑凸字:制品上做出凹坑凸字,成型部分作成镶块,这样既能保证制品使用时不易被损坏又能使模具制造容易,且易更换。
2、异色标志:双色注射成型3、嵌件:定义、作用(功能性作用)、材料作用:功能性作用,如抗蚀性、抗磨性、导磁性、导电性、尺寸稳定性、表面装饰、提高制造精度以及便于拆卸。
定义:镶入塑料制品中的零件,使之成为模塑制品不可拆卸的组成部分,这些嵌入制品中的零件称为嵌件。
材料:铜、铝、钢、陶瓷、玻璃、塑料、木材、橡胶等。
4、结构设计:要求必须牢固固定在制品中,防止旋转和拔出,5、嵌件的安放、定位要求(1) 不能因设备的运动或振动而松动甚至脱落。
(2) 在高压塑料熔体的冲击下不产生位移和变形。
(3) 嵌件与模具的配合部分应能防止溢料,避免出现毛刺,影响使用性能。
第8讲1、异型材设计:截面形状应尽量简单、对称,断面壁厚应均匀,尽可能避免或减少设筋和凸台。
2、共挤异型材两种塑料相容性越好,粘接强度越高;若相容性不好,则截面间可采用机械连接。
3、中空容器几何形状有圆形、椭圆形、方形、异型。
4、中空吹塑制品结构设计应考虑强度与刚度,底部、身部、口部螺纹结构设计中空容器主要承受垂直方向的压力。
它主要来自三方面:(1)容器包装物料的自重;(2)容器堆叠时压力;(3)物料灌装时压力和瓶盖压配时压力。
吹塑成型用螺纹,设计为梯形或半圆形的截面,不采用三角形细牙或粗牙螺纹5、注塑吹塑制品的结构•剪边或铰孔加工后不需精加工;•有利于缩短时间和节约原料;•壁厚容易控制;•螺纹精度高;•底部不用截坯口;•不受场合的限制,生产速度快;•可制得高强度的制品。
6、热成型工艺过程7、制品设计•制品不能有侧孔、侧凹,否则难以脱模;•侧壁有凸凹,要考虑采用活动型芯或抽芯机构;•孔或开口不能直接成型,可采用二次加工。
•设计制品应考虑加强筋、脊或凹凸图案等;•对于薄壁、面积大的热成型制品,一般需要对表面增加凸凹,成拱形,进行增强,以提高制品刚度;•避免制品上的大凸凹,易造成壁厚不均,若壁太薄,强度不足,易出现皱折。
8、旋转模塑制品特点:大型、封闭、形状复杂,小型中空制品,也可制造特大型塑料制品;壁厚均匀,内应力极小,壁厚可以自由调整(假如原料重量不同);形状可以非常复杂,设计自由度大;9、中空成型有吹塑、滚塑、热成型和气体辅助注塑成型法等多种方法。
大型中空制品成型工艺有吹塑、滚塑和热成型法。
滚塑适宜设计和加工复杂形状和侧面有孔的制品,多种内表面可同时成型为主要特点,制品壁厚均匀性优于吹塑成型法。
吹塑成型法原料贵,制品尺寸稳定性好,翘曲小,成型时间短,产量高,人力和能源成本低。
热成型(片材)法加工设备贵,而制品强度是3种方法中最高的。
10、旋转成型只为增加其强度,可在大面积平坦制品上布置筋或凹凸图案,起增强作用,但凹凸不能太窄而深。
或做成双层壁结构,成型后中空部分填入泡沫塑料,起增强作用。
第9讲1、塑料制品的装配分为可拆卸式的装配和固定而不可拆卸的装配两种2、可拆卸式装配有螺纹连接和弹性联接3、塑料制品的不可拆卸联接有粘接与焊接第10讲1、塑料作为支承材料的优点:•优良的摩擦和磨损性能;•不用或少用润滑剂,可减少冲击和噪声;•制造成本低;•化学稳定性好。
2、轴承材料PF、PA、氟塑料、POM、UHMWPE、聚酰亚胺3、轴承类型全塑料轴承:PA、POM应用最多,UHMWPE最有前途;金属轴瓦内衬氟塑料:金属轴瓦一般为钢,轴衬为多孔青铜用PTFE用浓缩分散液浸渍或涂覆;增强塑料轴瓦与编织的薄层轴衬:4、模塑齿轮的要求:•型芯与型腔都设于动模边;•多联齿轮型腔应设分型面同一侧;•将互相啮合的两齿轮放同一副模具;•考虑浇口类型和位置,避免偏心。