塑料产品设计规范
塑料件的设计规范
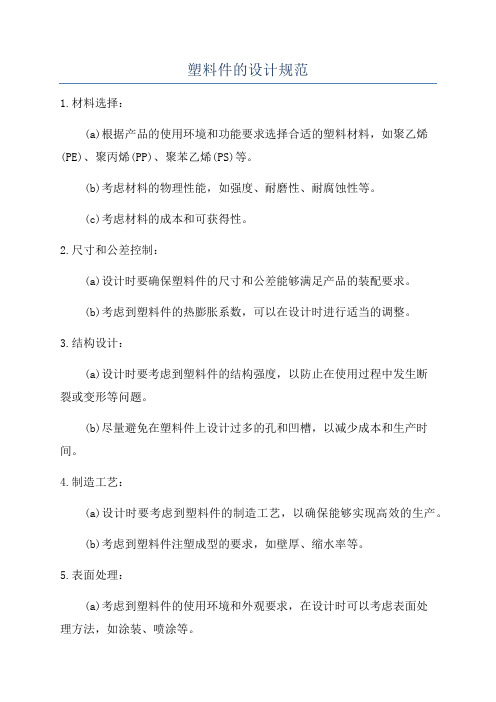
塑料件的设计规范1.材料选择:(a)根据产品的使用环境和功能要求选择合适的塑料材料,如聚乙烯(PE)、聚丙烯(PP)、聚苯乙烯(PS)等。
(b)考虑材料的物理性能,如强度、耐磨性、耐腐蚀性等。
(c)考虑材料的成本和可获得性。
2.尺寸和公差控制:(a)设计时要确保塑料件的尺寸和公差能够满足产品的装配要求。
(b)考虑到塑料件的热膨胀系数,可以在设计时进行适当的调整。
3.结构设计:(a)设计时要考虑到塑料件的结构强度,以防止在使用过程中发生断裂或变形等问题。
(b)尽量避免在塑料件上设计过多的孔和凹槽,以减少成本和生产时间。
4.制造工艺:(a)设计时要考虑到塑料件的制造工艺,以确保能够实现高效的生产。
(b)考虑到塑料件注塑成型的要求,如壁厚、缩水率等。
5.表面处理:(a)考虑到塑料件的使用环境和外观要求,在设计时可以考虑表面处理方法,如涂装、喷涂等。
(b)考虑到塑料件的耐候性,可以选择添加防紫外线(UV)剂。
6.排气和冷却:(a)设计时要确保塑料件的排气和冷却能够满足注塑成型的要求,以避免缺陷的产生。
(b)考虑到塑料件的形状和厚度变化,可以适当设计出气道和冷却系统。
7.注塑模具设计:(a)考虑到塑料件的形状、尺寸和结构,设计合适的注塑模具,以确保能够生产出符合要求的塑料件。
(b)考虑到模具的制造成本和使用寿命,可以合理选择模具材料和加工工艺。
总而言之,塑料件的设计规范是为了确保产品质量和生产效率,在材料选择、尺寸和公差控制、结构设计、制造工艺、表面处理、排气和冷却、注塑模具设计等方面提供了一些指导和标准。
通过遵守这些规范,设计师可以设计出高质量的塑料件,从而满足客户的需求。
塑胶产品结构设计基本规则

塑胶产品结构设计基本规则设计基本规则壁厚的大小取决于产品需要承受的外力、是否作为其它零件的支撑、承接柱位的数量、伸出部份的多少以及选用的塑胶材料而定。
一般的热塑性塑料壁厚设计应以4mm为限。
从经济角度来看,过厚的产品不但增加物料成本,延长生产周期”冷却时间〔,增加生产成本。
从产品设计角度来看,过厚的产品增加引致产生空穴”气孔〔的可能性,大大削弱产品的刚性及强度。
最理想的壁厚分布无疑是切面在任何一个地方都是均一的厚度,但为满足功能上的需求以致壁厚有所改变总是无可避免的。
在此情形,由厚胶料的地方过渡到薄胶料的地方应尽可能顺滑。
太突然的壁厚过渡转变会导致因冷却速度不同和产生乱流而造成尺寸不稳定和表面问题。
对一般热塑性塑料来说,当收缩率”Shrinkage Factor〔低于0.01mm/mm时,产品可容许厚度的改变达;但当收缩率高于0.01mm/mm时,产品壁厚的改变则不应超过。
对一般热固性塑料来说,太薄的产品厚度往往引致操作时产品过热,形成废件。
此外,纤维填充的热固性塑料于过薄的位置往往形成不够填充物的情况发生。
不过,一些容易流动的热固性塑料如环氧树脂”Epoxies〔等,如厚薄均匀,最低的厚度可达0.25mm。
此外,采用固化成型的生产方法时,流道、浇口和部件的设计应使塑料由厚胶料的地方流向薄胶料的地方。
这样使模腔内有适当的压力以减少在厚胶料的地方出现缩水及避免模腔不能完全充填的现象。
若塑料的流动方向是从薄胶料的地方流向厚胶料的地方,则应采用结构性发泡的生产方法来减低模腔压力。
平面准则在大部份热融过程操作,包括挤压和固化成型,均一的壁厚是非常的重要的。
厚胶的地方比旁边薄胶的地方冷却得比较慢,并且在相接的地方表面在浇口凝固后出现收缩痕。
更甚者引致产生缩水印、热内应力、挠曲部份歪曲、颜色不同或不同透明度。
若厚胶的地方渐变成薄胶的是无可避免的话,应尽量设计成渐次的改变,并且在不超过壁厚3:1的比例下。
下图可供叁考。
塑料件的设计准则
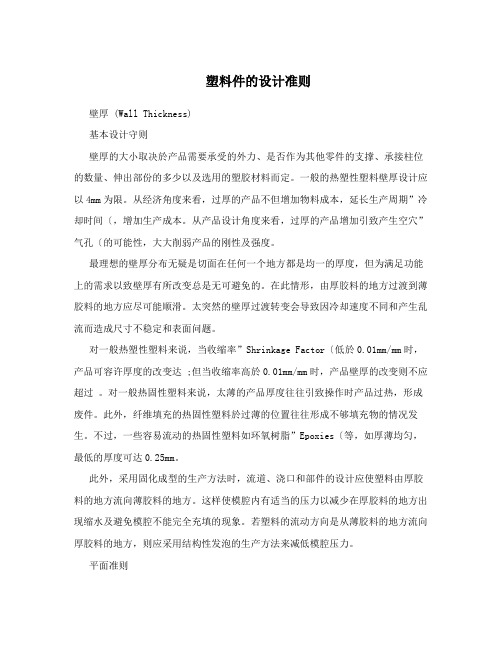
塑料件的设计准则壁厚 (Wall Thickness)基本设计守则壁厚的大小取决於产品需要承受的外力、是否作为其他零件的支撑、承接柱位的数量、伸出部份的多少以及选用的塑胶材料而定。
一般的热塑性塑料壁厚设计应以4mm为限。
从经济角度来看,过厚的产品不但增加物料成本,延长生产周期”冷却时间〔,增加生产成本。
从产品设计角度来看,过厚的产品增加引致产生空穴”气孔〔的可能性,大大削弱产品的刚性及强度。
最理想的壁厚分布无疑是切面在任何一个地方都是均一的厚度,但为满足功能上的需求以致壁厚有所改变总是无可避免的。
在此情形,由厚胶料的地方过渡到薄胶料的地方应尽可能顺滑。
太突然的壁厚过渡转变会导致因冷却速度不同和产生乱流而造成尺寸不稳定和表面问题。
对一般热塑性塑料来说,当收缩率”Shrinkage Factor〔低於0.01mm/mm时,产品可容许厚度的改变达 ;但当收缩率高於0.01mm/mm时,产品壁厚的改变则不应超过。
对一般热固性塑料来说,太薄的产品厚度往往引致操作时产品过热,形成废件。
此外,纤维填充的热固性塑料於过薄的位置往往形成不够填充物的情况发生。
不过,一些容易流动的热固性塑料如环氧树脂”Epox ies〔等,如厚薄均匀,最低的厚度可达0.25mm。
此外,采用固化成型的生产方法时,流道、浇口和部件的设计应使塑料由厚胶料的地方流向薄胶料的地方。
这样使模腔内有适当的压力以减少在厚胶料的地方出现缩水及避免模腔不能完全充填的现象。
若塑料的流动方向是从薄胶料的地方流向厚胶料的地方,则应采用结构性发泡的生产方法来减低模腔压力。
平面准则在大部份热融过程操作,包括挤压和固化成型,均一的壁厚是非常的重要的。
厚胶的地方比旁边薄胶的地方冷却得比较慢,并且在相接的地方表面在浇口凝固後出现收缩痕。
更甚者引致产生缩水印、热内应力、挠曲部份歪曲、颜色不同或不同透明度。
若厚胶的地方渐变成薄胶的是无可避免的话,应尽量设计成渐次的改变,并且在不超过壁厚3:1的比例下。
塑料件设计规范new
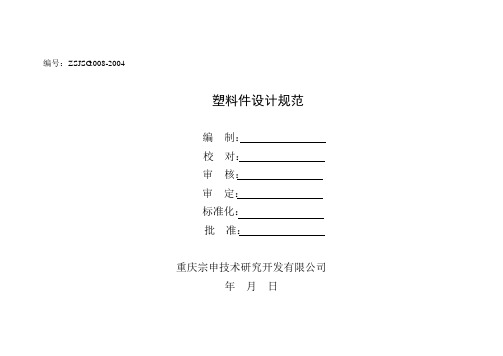
编号:ZSJSG.008-2004塑料件设计规范编制:校对:审核:审定:标准化:批准:重庆宗申技术研究开发有限公司年月日编 号:ZSJSG.008-2004塑料件设计规范一、范围本标准规定了摩托车、通用农业机械塑料零件的(用热塑性塑料如ABS 、PP 、PC 、PVC 、PMMA 、PA1010和热固性塑料如UP 制成的零部件)的设计规范、技术要求。
本标准适用于宗申产业集团生产的摩托车塑料件(包括摩托车发动机塑料件)和通用机械塑料件。
二、名称、术语2.1三、 示意图(以186项目为例)前转向灯挡风玻璃 座垫油箱后车体前侧盖下护板四. 结构特征及分类4.1结构特征4.1.1塑料零件的普通结构特征:重量轻,比强度(单位质量的力学强度)高、电气性能优异、化学稳定性好,具有较好的弹性,易成型。
主要使用注塑模具在注塑机上压制而成,因此对成型模具有较高的要求等等。
4.1.2摩托车、通机塑料件因为外观造型活跃、车身结构复杂、空间有限等特点,所以零件结构复杂、容易起翘变形,对表面质量要求高。
4.1.3对塑料件而言,合理的加工工艺、高效率的设备、先进的模具是必不可少的三项重要因素,其中尤以塑料成型模具起着决定性的作用。
而决定模具制造的很重要的一点就是数据的设计。
所以,塑料件数据的设计质量要求较高。
4.2分类4.2.1 根据塑料件的装配位置(外观要求)可分为覆盖件和非覆盖件;4.2.2 摩托车覆盖件根据造型的特点,也可按车型分类:骑式车、弯梁车、踏板车等。
其中踏板车、弯梁车使用了大量的塑料覆盖件。
五、常用材料及其主要化学成份和机械性能5.1 摩托车、通机常用的塑料主要是热塑性塑料,如ABS、PP、PA、PMMA、PVC、PC等;同时也使用了少量的热固性塑料如UP等。
5.2 摩托车、通机常用塑料的机械性能、成型特点见表1,综合性能见表2、表3。
表1 摩托车、通机常用塑料的机械性能、成型特点表2 摩托车、通机常用热塑性塑料的综合性能六、技术要求及选择范围(含热处理、表面处理、性能参数、加工表面粗糙度、装配要求)6.1 材质性能要求应符合表2和表3的要求。
塑料产品标识和标志设计规范
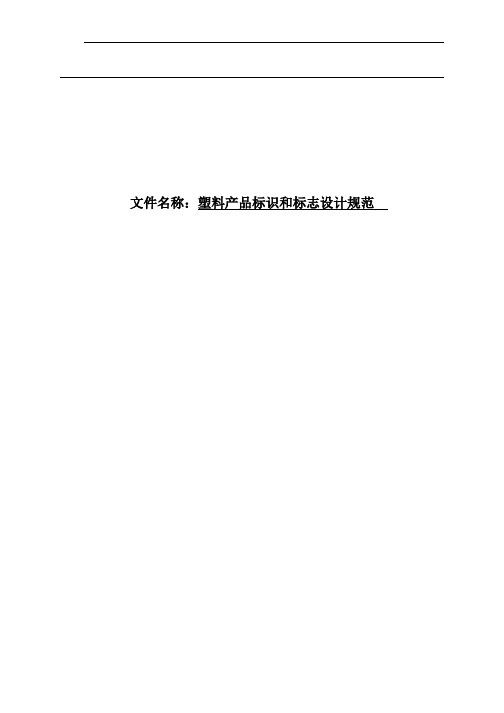
文件名称:塑料产品标识和标志设计规范塑料产品标识和标志设计规范1目的、范围1.1目的为了保护消费者利益,保证产品的品质,加快塑料废弃物分类回收的速度,最终保护环境和人身健康安全,公司对所有使用的塑料制品进行标识,并加以标志。
1.2范围本标准规定了塑料件永久性标识的范围、要求、位置及出口机型海外认证零部件标识的特殊要求(待补充)。
适用于公司所有产品(洗衣机,微波炉,冰箱等)的塑料制品2 标识设计规范产品标识分为A, B两大部分。
2.1 A部分的构成A部分是产品基本信息标志,主要包括“SANYO”品牌标记、产品型号、模具编号、穴号、生产日期等注:图中“产品型号”“穴号”仅为位置标志,其内容根据实际情况确定是否填写。
图 1 标识 A 部分构成2.2 B部分的构成B部分是材料及回收标志,主要包括材料标识,塑料数字编码,图形符号三部分构成。
见示意图图 2。
图 2 标识 B 部分构成2.3 A、B 两部分的排布A、B 两部分的标识要求在零部件的同一个平面内显示出来,在部件的表面积大小允许的情况下,B 部分的标识要排在 A 部分标识的右侧;如果表面积大小不允许 A、B 两部分标识左右排布,可将 B 部分标识排在 A 部分标识的下侧,具体位置由设计人员在图纸上进行标示;如果受部件表面积大小的限制,则 A、B 两部分标识的具体位置由设计人员视具体情况在图纸上分别进行标示。
2.4 A 部分(产品基本信息标识)设计规范2.4.1 “三洋企业标志 SANYO”:“SANYO”采用标准黑体字,大小根据空间及要求采用 4mm、5mm、6mm 等规格。
2.4.2 “产品型号”指该部件的原始使用机型。
附录 A 中的零部件必须标志产品型号,其它部件可依据需求进行标志。
2.4.3 “模具编号”按工程技术部给定的代号。
在设计阶段无法提供具体模具编号,可在产品图中用方框标出位置及大小,以便预留出位置。
2.4.4 “穴号”指所标识件模具型腔的代号;当制品一模多腔时,应按顺序写该制品型腔号和模具中该制品型腔总数,中间用“/”分开。
塑料件的设计规范
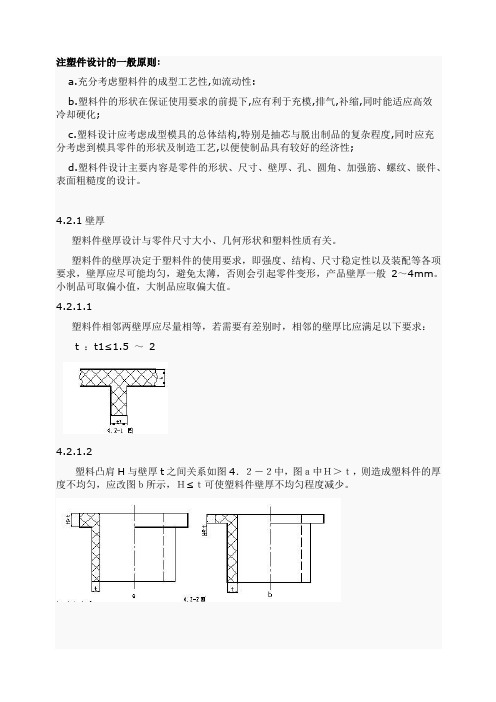
注塑件设计的一般原则:a.充分考虑塑料件的成型工艺性,如流动性:b.塑料件的形状在保证使用要求的前提下,应有利于充模,排气,补缩,同时能适应高效冷却硬化;c.塑料设计应考虑成型模具的总体结构,特别是抽芯与脱出制品的复杂程度,同时应充分考虑到模具零件的形状及制造工艺,以便使制品具有较好的经济性;d.塑料件设计主要内容是零件的形状、尺寸、壁厚、孔、圆角、加强筋、螺纹、嵌件、表面粗糙度的设计。
4.2.1壁厚塑料件壁厚设计与零件尺寸大小、几何形状和塑料性质有关。
塑料件的壁厚决定于塑料件的使用要求,即强度、结构、尺寸稳定性以及装配等各项要求,壁厚应尽可能均匀,避免太薄,否则会引起零件变形,产品壁厚一般2~4mm。
小制品可取偏小值,大制品应取偏大值。
4.2.1.1塑料件相邻两壁厚应尽量相等,若需要有差别时,相邻的壁厚比应满足以下要求:t :t1≤1.5 ~24.2.1.2塑料凸肩H与壁厚t之间关系如图4.2-2中,图a中H>t,则造成塑料件的厚度不均匀,应改图b所示,H≤t可使塑料件壁厚不均匀程度减少。
4.2.2过渡圆角为了避免应力集中,提高强度和便于脱模,零件的各面连接处应设计过渡圆角。
零件结构无特殊要求时,在两面折弯处应有圆角过渡,一般半径不小于0.5~1mm,R≥t。
4.2.2.1内外圆角半径零件内外表面的拐角处设计圆角时,应保证零件壁厚均匀一致,图中以R为内圆角半径,R1为外圆角半径,t为零件的壁厚.4.2.3加强筋为了确保零件的强度和刚度,而又不使零件的壁厚过大,避免零件变形,可在零件的适当部位设置加强筋。
4.2.3.2设计加强筋时,应使中间筋低于外壁0.5~1mm,以减少支承面积,达到平直要求。
4.2.4孔的设计孔的周壁厚会影响到孔壁的强度。
孔口与塑件边缘间距离a不应小于孔径,并不小于零件壁厚t的0.25倍。
孔口间的距离b不宜小于孔径0.75倍,并不小于3mm。
4.2.4.1 孔的周壁厚H和突起部分的壁厚c和高度h、h与c之比不能超过3,如图内螺纹直径不能小于2mm,外螺纹直径不能小于4mm.螺距不小与0.5mm.螺纹的拧合长度一般不大于螺纹直径的1.5倍,为了防止塑料螺纹的第一扣牙崩裂,并保证拧入,必须在螺纹的始端和末端留有0.2~0.8mm的圆柱形.并注意:塑料件螺纹不能有退刀槽,否则无法脱模。
QJ-MF05.001-2006塑料件设计规范
QJ/MF05.001-2006
5.5 耐磨擦零件 用于轴承、轴衬、滑杆、易磨擦面的零件塑料有 PTEE、PA、POM 5.6 电气结构件 电气结构件要求具有阻燃、一定的强度,塑料有 PC、PPO、阻燃 ABS、阻燃 PP 5.7 透光零件 透光零件要求具有较高的透光度、透明度,塑料有 PS、PC、PVC、AS、PMMA 5.8 薄膜料 薄膜料有 PE-PP、PVC、PET 5.9 板材、管材 常用于制做板材、管材的塑料有 PVC、PE、PP、ABS
4. 内容
4.1 总体设计规范 首先深入了解产品的功能,使用环境和载荷等方面的最终用途和要求,包括:a)功能要点, b)结构要求的装配情况,c)成本限制,d)遵循的准则和标准,e)使用和环境条件。充分考虑塑料 的物理机械性能,避免和补偿其缺点。 4.2 设计五项原则 a) 脱模斜度 b) 壁厚的均匀性 c) 消除点角 d) 简化形式 e) 与同类产品比较 4.3 塑料件形状 在保证使用要求的情况下,塑料件的形状应求简单,以便于模塑,即塑料件内、外表面的形 状应有利于开模,取出制品,尽可能不使用瓣合分型结构、抽芯机构等,以达到简化工艺、提高 生产效率的目的。 4.4 塑料件壁厚 壁厚取决于使用要求,即对强度、结构、电性能、尺寸稳定性以及装配等指标的要求,壁厚 对制件质量影响很大,太薄会造成制品的强度和刚度不足,受力后易产生翅曲变形,壁厚过大, 不但会增加成本,还容易产生局部收缩、缩孔、翅曲等不良现象。壁厚要尽量均匀,减少制品的
美的厨房电器有限公司 2006-10-30 批准
2006-11-30 实施
1
QJ/MF05.001-2006
ABS、抗静电 ABS,ABS/PC 合金等。 3.6 PP:聚丙烯的缩写,是以丙烯为单体制成的聚合物,属热塑性塑料,目前以使用其改性料如 改性 PP、耐候 PP 为主。 3.7 PS:聚苯乙烯的缩写,是以苯乙烯为单体制成的聚合物,属热塑性塑料,因其性脆、易裂, 通常工程上使用的是经改性的高抗冲 PS (HIPS) , 在此基础上的改性料有阻燃 HIPS、 增强 HIPS、 高光 HIPS。 3.8 PC:聚碳酸酯的缩写,是对主链中含有碳酸酯的聚合物的总称,属热塑性塑料,综合性能良 好,改性料有阻燃 PC、增强 PC 等。 3.2 注塑件:将热塑性塑料或热固性塑料在料筒中加热软化,以螺杆或柱塞推挤入闭合模具的型 腔内成型,经冷却、启模取出的塑料制品。
塑料结构设计的一些规范标准(详细易读版)
时,
举例分析
分析:
图1-1-12
(2) 加强筋设计示例
图1-1-12
一章
结构设计 1-4
4. 设计中柱子和孔的问题 (1)柱子的问题 a.RUBBER KEY和PCB的相关柱子设计请参考第二章。 b.设计柱子时,应考虑胶位是否会缩水。 c.为了增加柱子的强度,可在柱子四周追加加强筋。
图1-1-12
大机台:aa<25mm(max); 小机台:aa<20mm(max)
(4) “OPEN”标识偏中心的部品卡钩设计,如打印头盖
A
B
图1-1-12
图1-1-12
图1-1-12 卡钩A 卡钩B
如图1-1-12“OPEN”不在卡钩A,B中间,当 开启或关闭头盖时,两卡钩受力不一样, 如卡钩的配合结构相同,则会出现如图 1-1-12扭转的情况,为此将两卡钩设计成 不一样,使其受力均匀。如图1-1-13
结构设计 1-3
a. 为确保塑件制品的强度和刚度,又不致使塑件的壁增厚,而在塑件的适当部位设 置加强筋,不仅可以避免塑件的变形,在某些情况下,加强筋还可以改善塑件成型中 的塑料流动情况。 b.为了增加塑件的强度和刚性,宁可增加加强筋的数量,而不增加其壁厚。
(1) 加强筋厚度与塑件壁厚的关系
当 就不易缩水。
雕刻区通常要求咬薄薄的花纹TH106, 目的:避免在塑胶成型时出现流痕。
c
(3) 凸字雕刻
大机台, 参考机台:EL-1750P CHANGE CORE 小机台, 参考机台:EL-S872 CHANGE CORE
(4) 凹字雕刻
参考机台:EL-S872
CHANGE CORE
一章
结构设计 1-6
塑料制品的设计规范
的充模流动阻力。如图3-13 ⑵应避免或减少塑料的局部集中,
以防止产生凹陷和气泡。如图3-14 ⑶加强筋以设计矮一些多一些为好。 ⑷筋与筋的间隔距离应大于塑件的
壁厚。
PPT文档演模板
塑料制品的设计规范
3.4.5 增加刚性减少变形的其他措施
将薄壳状的塑件设计为球面, 拱曲面等, 可 以有效地增加刚性、减少变形。
PPT文档演模板
塑料制品的设计规范
3.4.3 加强筋及其它增强结构
为了提高塑件的强度和防止塑件翘曲变形, 常设计加强筋,如图筋的设置位置应沿塑料 充模流向,降低充模流动阻力. 见图3-12
加强筋的正确形状和尺寸比例如图3-15 所示。
PPT文档演模板
塑料制品的设计规范
3.4.4 加强筋的主要形式
PPT文档演模板
塑料制品的设计规范
3.2 尺寸精度与表面质量
3.2.1 尺寸精度 3.2.2 尺寸精度的确定 3.2.3 表面质量
PPT文档演模板
塑料制品的设计规范
3.2 尺寸精度与表面质量
3.2.1 尺寸精度 1、塑件尺寸概念
塑件尺寸——塑件的总体尺寸。 2.塑料制品总体尺寸受限制的主要 因素:
PPT文档演模板
塑料制品的设计规范
3.2 尺寸精度与表面质量
3.2.2 尺寸精度的确定
表3—1是模塑件尺寸公差国家标 准(GB/T 14486-1993), 表 3—2是常用塑料材料的公差等级选 用。
将表3—1和表3—2结合起来使
用, 先查表3—2, 根据模塑件的材料
品种及用要求选定塑件的尺寸精度
图3—6 可强制脱模的浅侧凹结构
a)(A-B)×100%/B≤5% b) (A-B)×100%/C≤5%
塑料制品的设计规范
3.2
尺寸精度与表面质量
3.2.1 3.2.2 3.2.3 尺寸精度 尺寸精度的确定 表面质量
3.2 尺寸精度与表面质量 3.2.1 尺寸精度
1、塑件尺寸概念 塑件尺寸——塑件的总体尺寸。 2、塑料制品总体尺寸受限制的主要因素: *塑料的流动性
*成型设备的能力
3.2 尺寸精度与表面质量
影响塑件尺寸精度的因素: 1、模具制造的精度,约为1/3。 2、成型时工艺条件的变化,约为1/3。 3、模具磨损及收缩率的波动。 具体来说,对于小尺寸制品,模具制 造误差对尺寸精度影响最大;而大尺寸制 品则收缩波动为主要。
3.2 尺寸精度与表面质量 3.2.3 表面质量
1、塑件制品的表面质量要求: ①表面粗糙度要求。 ②表面光泽性、色彩均匀性要求。 ③云纹、冷疤、表面缩陷程度要求。 ④熔结痕、毛刺、拼接缝及推杆痕迹等 缺陷的要求。
3.2 尺寸精度与表面质量 3.2.3 表面质量
2、型腔表面粗糙度要求
①一般,型腔表面粗糙度要求达0.20.4mm。 ②透明制品型腔和型芯粗糙度一致。 ③非透明制品的隐蔽面可取较大粗糙 度,即型芯表面相对型腔表面略为粗糙。
第3章
塑件设计
本章难点
对塑件成型工艺性、塑件的形状结构与模 具结构的关系的理解。
第3章
塑件设计
3.1 塑件设计原则 3.2 尺寸精度与表面质量 3.3 形状和结构设计 3.4 壁厚与脱模斜度 3.5 嵌件的安放与塑料螺纹、齿 轮设计 3.6 思考题
3.1
塑件设计
塑件设计原则: ⑴满足使用要求和外观要求 ⑵针对不同物理性能扬长避短 ⑶便于成型加工 ⑷尽量简化模具结构
a 图3-1具有侧孔的塑件
b a
b 图3-2塑件内侧表面形 状改进
- 1、下载文档前请自行甄别文档内容的完整性,平台不提供额外的编辑、内容补充、找答案等附加服务。
- 2、"仅部分预览"的文档,不可在线预览部分如存在完整性等问题,可反馈申请退款(可完整预览的文档不适用该条件!)。
- 3、如文档侵犯您的权益,请联系客服反馈,我们会尽快为您处理(人工客服工作时间:9:00-18:30)。
塑料产品设计规范塑料制品设计特点﹕塑料产品的设计与其它材料如钢,铜,铝,木材等的设计有些是类似的;但是,由于塑料材料组成的多样性,结构﹑形状的多变性,使得它比起其它材料有更理想的设计特性;特别是它的形状设计,材料选择,制造方法选择,更是其它大部分材料无可比拟的.因为其它的大部分材料,其设计者在外形或制造上,都受到相当的限制,有些材料只能利用弯曲﹑熔接等方式来成形.当然,塑料材料选择的多样性,也使得设计工作变得更为困难,如我们所知,目前已经有一万种以上的不同塑料被应用过,虽然其中只有数百种被广泛应用,但是,塑料材料的形成并不是由单一材料所构成,而由一群材料族所组合而成的,其中每一种材料又有其特性,这使得材料的选择,应用更为困难.塑料制品设计原则﹕1.依成品所要求的机能决定其形状﹐尺寸﹐外观﹐材料2.设计的成品必须符合模塑原则﹐既模具制作容易﹐成形及后加工容易﹐但仍保持成品的机能塑料制品设计程序:为了确保所设计的产品能够合理而经济,在产品设计的初期,在外观设计者﹐机构工程师,制图员,模具制造者,成形厂以及材料供应厂之间的紧密合作是必须的,因为没有一个设计者,能够同时拥有如此广泛的知识和经验,而从不同的事业观点所获得的建议,将是使产品合理化的基本前提;除此之外, 一个合理的设计考虑程序也是必须的;以下将就设计的一般程序作出说明:一.确定产品的功能需求,外观.在产品设计的初始阶段,设计者必须列出对该产品的目标使用条件和功能要求;然后根据实际的考虑,决定设计因子的范围,以避免在稍后的产品发展阶段造成可能的时间和费用的漏失.下表为产品设计的核对表,它将有助于确认各种的设计因子.产品设计的核对表一般数据:1.产品的功能?2.产品的组合操作方式?3.产品的组合是否是可以靠着塑料的应用来简化?4.在制造和组合上是否可能更为经济有效?5.所需要的公差?6.空间限制的考虑?7.界定产品使用寿命?8.产品重量的考虑?9.有否承认的规格?10.是否已经有相类似的应用存在?结构考虑:1.使用负载的状态?2.使用负载的大小?3.使用负载的期限?4.变形的容许量?环境:1.使用在什么温度环境?2.化学物品或溶剂的使用或接触?3.温度环境?4.在该种环境的使用期限?外观:1.外形2.颜色3.表面加工如咬花,喷漆等.经济因素:1.产品预估价格?2.目前所设计产品的价格?3.降低成本的可能性?二.绘制预备性的设计图:当产品的功能需求,外观被确定以后,设计者可以根据选定的塑料材料性质,开始绘制预备性的产品图,以作为先期估价,检讨以及原则模型的制作.三.制作原型模型:原型模型让设计者有机会看到所设计的产品的实体,并且实际的核对其工程设计.原型模型的制作一般有两种方式,第一种就是利用板状或棒状材料依图加工再接合成一完整的模型,这种方式制作的模型,经济快速,但是,缺点是量少,而且较难作结构测试;另一种方式,是利用暂用模具,可作少量生产,需花费较高的模具费用,而且所费的时间较长,但是,所制作的产品较类似于真正量产的产品(需要特殊模具机构的部分,可能成形后再以机械加工成形),可做一般的工程测试,而且建立的模具,成形经验,将有助于产品针对实际模具制作,成形需要而作正确的修正或评估.四.产品测试每一个设计都必须在原型阶段,接受一些测试,以核对设计时的计算和假想和实体之间的差异.产品在使用时所需要做的一些测试,大部分都可以籍着原型做有效的测试;此时,面对了所有设计的功能要求,并且能够达成一个完整的设计评估.仿真使用测试通常在模型产品阶段就必须开始,这种型态的测试价值,取决于使用状态被模拟的程度而定.机械和化学性质的加速化测速通常被视为模型产品评估的重要项目.五.设计的再核对与修正对设计的检讨将有助于回答一些根本的问题:所设计的产品是否达到预期的效果?价格是否合理?甚至于在此时,许多产品为了生产的经济性或是为了重要的功能和外形的改变,必须被发掘并改善,当然,设计上的重大改变,可能需要做完整的重新评估;假若所有的设计都经过这种仔细检讨,则能够在这个阶建立产品的细节和规格.六.制定重要规格规格的目的在于消除生产时任何的偏差,以使产品符合外观,功能和经济的要求,规格上必须明确说明产品所必须符合的要求,它应该包括:制造方法,尺寸公差,表面加工,分模面位置,毛边,变形,颜色以及测试规格等.七.开模生产当规格被谨慎而实际的订定之后,模具就可以开始被设计和制作,模具的设计必须谨慎并咨询专家的意思,因为不适当的模具设计和制造,将会使得生产费用提高,效率降低,并用可能造成质量的问题.八. 质量的控制对照一个已知的标准,订定对生产产品的规律检测是良好的检测作法,而检测表应该列出所有应该被检查的项目,另外,相关人员,如品管者或设计者也应与成形厂联合订定一个质量管理的程序,以利于在生产的产品能够符合规格的要求.产品设计细节确定:一.分模线之选定1.不得位于明显影响外观的位置2.开模时不形成死角(undercut)的位置3.位于模具易加工的位置4.位于成品后加工容易的位置5.位于不影响尺寸精度的位置(尺寸关系重要的部分尽量放在模具的同一边)二.脱模斜度脱模斜度是为了便于产品从模具中脱出而设置的。
脱模斜度一采用1~2度﹐最小不小于0.5度。
具体数值视成品形状﹐成形材料的类别﹐模具结构﹐表面精度﹐以及加工方等会有所不同。
在不影响产品质量的前提下﹐脱模斜度愈大愈好。
三.产品外形及肉厚产品外形尽量采用流线外形﹐避免突然的变化﹐以免在成形时因塑料在此处流动不顺引起气泡等缺陷﹔并且此处模具易产生磨损。
决定肉厚的主要因素﹕1.结构强度是否足够2.能否抵脱模力3.能否均匀分散所受的冲击力4.有埋入件时﹐能否防止破裂﹐如产生熔合线是否会影响强度5.成形孔部位的熔合线是否会影响强度6.尽可能肉厚均匀﹐以防止产生缩水7.棱角及肉厚较薄部分是否会阻碍材料流动﹐从而引起充填不足肉厚不均对成形性的影响﹕1.成形品之冷却时间取决于肉厚较厚的部分﹐使成形周期延长﹐生产性能降低2.肉厚不均则成品冷却后收缩不均﹐造成缩水﹐产生内应力﹐变形﹐破裂等我们经常用的材料有:PC,ABS,PMMA等几种,它们的标准肉厚如下:PC:1.5-5.0 ABS:1.2-3.5 PMMA:1.5-5.0四.加强与防止变形方法﹕1.转角部位加R塑料产品的尖锐转角常常是造成产品破坏的最大因素.消除产品尖锐的转角,不但可以降低该处的应力集中,提高产品的结构强度,也可以使得塑料材料成形时有流线型的流路,以及成品更易于顶出.另外,从模具的观点,园角也是有益于模具加工和模具强度.产品所有的内侧和外侧的周边转角园弧都必须尽可能的大,以消除应力集中;但是,太大的园弧可能造成缩水,特别是在肋或突柱根部转角园弧.原则上,最小的转角园弧为0.020到0.030inch.综上所述,园角对于成形品的设计会有以下的一些优点:(1) 园角使得成形品提高强度以及降低应力.(2) 尖锐转角的消除,自动地降低了龟裂的可能性,就是提高对突然的震动或冲击的抵抗能力.(3) 塑料的流动状态将被重大的改善,园形的转角,使得塑料能够均匀,没有滞留现象以及较少应力的流入模穴内所有的断面,并且改善成形品断面的密度之均匀性.(4) 模具强度获得改善,以避免模具内尖锐的转角,造成应力集中,导致龟裂,特别是对于需要热处理或受力较高的部分,园弧转角更为重要.园角加大,应力集中减少.内圆角R<0.3T ----应力剧增内圆角R>0.8T ----几乎无应力集中2.增设加强肋肋根部厚度约为(0.5~0.7)TPC,PPO T<0.6TPA,PE T<0.5TPMMA,ABS T<0.5TPS T<0.6T肋间间距>4T肋高L<3T3.利用变化肉厚及形状1)侧壁加强既可防止变形﹐也可改善流动性2)边缘加强用变化的边缘形状来加强﹐防止变形3)周边加强较大的平面易发生翘曲变形﹐用周边凹凸或波浪形来防止变形4)底部加强箱形件底部﹐为加强及防变形常采用如下方法﹕五.BOSS之设计1.BOSS的长度一般不超过本身直径的两倍﹐否则必须加加强肋。
(长度太长时会引起气孔﹐烧焦﹐充填不足等)2.BOSS的位置不能太接近转角或侧壁3.BOSS的形状以圆形为主﹐设计在底部时取3个 (其它形状则加工不易﹐且流动性也不好)4.BOSS周围可用除去部分肉厚来防收缩下陷六.孔及凹陷之设计孔的形状和位置的选择,必须避免造成产品的脆弱性以及生产上的复杂性.在成形孔的一般方法中,塑料被射出模穴,然后沿着心梢的周边流动而形成孔,因此,当塑料在心梢一端会合时,会形成接合线,这些接合线位置就成为成品本身的潜在脆弱性.1.孔与孔之间距离为孔径2倍以上2.孔与成品边缘之间距离为孔径3倍以上3.孔与侧壁之间距离为孔径3/4倍以上4.孔周边的肉厚宜加强(尤其针对有装配性﹐受力的孔)﹐切开的孔周边也宜加强5.垂直于材料流动方向的盲孔﹐孔径在1.5mm以下时﹐孔深不得超过孔径的2倍(只有一端支撑的模仁梢比起两端都有支撑的模仁梢会高出48倍的变形量)6.孔径不变的通孔不宜设计为两边对合成形﹐会产生偏心﹐可将任一边的孔径加大﹐或设计为不用对合成形的孔孔的形状设计比较﹕七.成形螺纹及辊纹设计成形螺纹设计注意事项﹕1.避免使用32牙/inch(螺距0.75mm)以下的螺纹﹐最大螺距可采用5mm2.长螺纹会因收缩的关系使螺距失真﹐应避免使用﹐如结构需要时可采用自攻螺丝锁紧3.螺纹公差小于成形材料收缩量时应避免使用4.螺纹不得延长至成品末端﹐因如此产生的尖锐部会使模具及螺纹的端面崩裂﹑寿命降低﹐所以至少要留0.8mm的平坦部分5.螺纹需有2~4度的拔模角辊纹通常是平行于脱模方向的沟槽﹐辊纹间距通常为3.0mm,最小为1.5mm。
为防模具崩裂及使后加工容易﹐辊纹与分模面间至少留0.8mm的平坦部分。
八.埋入件设计埋入件举例﹕埋入件需注意点﹕1.由于流动性的关系﹐会在埋入件的周围产生熔接痕﹔由于塑料与金属的收缩率不一样﹐成形后易产生开裂2.使用埋入件成形时﹐会使周期延长3.埋入件高出成形品少许﹐可避免在装配时被拉动而松脱成形品设计要点改善:(1)外观的改善:A.原肋为表面形成收缩下陷之原因尽量减薄,肋原<=0.5-0.6TB.光泽表面可施行一些如放电,喷砂,腐蚀加工等防止收缩下陷及保持表面无痕迹C.尽可能地使分模面变得容易,可使模具加工容易及毛边,浇口切除容易D.肉厚均一,可防收缩下陷E.内部肉厚去除,使肉厚均一,防止收缩下陷F.凸彀周围,除去部分肉厚,防止收缩下陷G.凸彀之设置在同样强度下,可以多数以小凸彀代替,可防止收缩下陷H.格子连接凸彀之场合,可防收缩下陷,并可使强度显著增加(2)强度的改善A.肉厚较薄之孔,把孔边肉厚增加及高度增高以补强B.切离之孔周边肉厚宜增加C.曲面的设置,可使强度增强D.脱模时,心型销受收缩力,使成形品顶出时造成破裂,可设置凸彀承受顶出力量E.角隅设R ,可改善强度,防止应力集中,变形破裂F.加设补强肋及角隅部设R,增强凸彀之强度G.孔与孔之间距,孔与边缘之距离,应有适当之距离,可防止破裂之发生(3)模具及成形品的改善A.锐角薄内部分,易使材料充填不足B.透明成形品,肩角部设充分之脱模斜度,顶出时不被刮痕,才不致于影响透明性C.斜向凸彀,使模具构造变为复杂,改善凸彀方向的形状,使成直角向之分模D.将侧面之孔癖开,可消除UNDERCUT 而不用侧向心型E.上下对合,可免除使用侧向心型,使模具构造简化F.上对对合之孔,恐有偏心之处,宜将另一方孔扩大G.外缘波纹之成形品,后加工不易(毛边去除,浇口切离)可改为边缘,使变为容易H.手扭止滑部,凸形场合模具之切削加工容易I.分模线为阶断形,模具制作困难,毛边修整不易,宜改为直线形式曲线形.J.底部设置凸缘,可使分模线单纯,后加工容易K.切削时左右对称形状加工容易,非对称者加工困难L.车削加工比铣削加工速度快且廉价,成形品应尽量设计为圆形M.成形品加饰,宜设计凸出,模具加工时为下凹,雕削容易N.模具成形加工,在成形品之孔,一般以心型销来成形.所以在模具构造上,宜避免上部内厚过薄O.薄内部位,易造成充填不足P.成形品凸出文字,于模具加工时,反为凹入文字,雕削加工容易Q.内部托架上开孔,模具成本增加,且易发生故障,可改在成形后,钻孔加工R.深凹穴,应尽量为于成形品之同一侧(顶出,成形需要)改变模具固定侧之心型形状,使减少与成形品之接触面积(有利脱模)S.断面内厚较厚时,可改为补强肋,但内厚应与其它内厚均一T.深入之补强肋,尽量使用最大之脱模斜度,以利脱模,波形面之谷底,宜避免锐角形成.锐角部会阻碍材料流动,使模具强度减弱,成形品产生应力集中.其它:a.成形品与组合件,组合时宜在任何一方角部设置间隙b.埋入件螺纹部至成形品顶面留一平坦部避免成形时材料进入螺纹部c.两件成形品熔接,给予t之间隙,使熔接毛边进入d.螺纹埋入件制作成本高,成形时使成形周期延长,应尽量避免使用,成形品可预留攻丝用孔再与攻螺丝配合使用e.埋入件高出成形品少件,固定时可避免被拉取而松脱f.凸壳之预留攻丝用孔,前端,宜予倒角,以便于自攻螺丝导入g.贯穿孔使模具加工变为困难,可预留钻孔定位孔,待成形后,再次加工.h.心型销之分割面,位于埋入件之端面,埋入件受抵压,于成形时能确保固定i. 铰链成形品﹐宜设两段圆弧﹐使用效果更佳。