塑料制品的结构设计规范
塑料制品的结构设计规范

塑料制品的结构设计规范1双林汽车部件股份有限公司企业技术规范塑料制品的结构设计规范-10-20发布 -10-XX实施双林汽车部件股份有限公司发布塑料制品的结构设计又称塑料制品的功能特性设计或塑料制品的工艺性。
§1 塑料制品设计的一般程序和原则1.1 塑料制品设计的一般程序1、详细了解塑料制品的功能、环境条件和载荷条件2、选定塑料品种3、制定初步设计方案, 绘制制品草图( 形状、尺寸、壁厚、加强筋、孔的位置等)4、样品制造、进行模拟试验或实际使用条件的试验5、制品设计、绘制正规制品图纸6、编制文件, 包括塑料制品设计说明书和技术条件等。
1.2 塑料制品设计的一般原则1、在选料方面需考虑: (1) 塑料的物理机械性能, 如强度、刚性、韧性、弹性、吸水性以及对应力的敏感性等; (2) 塑料的成型工艺性, 如流动性、结晶速率, 对成型温度、压力的敏感性等; (3) 塑料制品在成型后的收缩情况, 及各向收缩率的差异。
2、在制品形状方面: 能满足使用要求, 有利于充模、排气、补缩, 同时能适应高效冷却硬化( 热塑性塑料制品) 或快速受热固化( 热固性塑料制品) 等。
3、在模具方面: 应考虑它的总体结构, 特别是抽芯与脱出制品的复杂程度。
同时应充分考虑模具零件的形状及其制造工艺, 以便使制品具有较好的经济性。
4、在成本方面: 要考虑注射制品的利润率、年产量、原料价格、使用寿命和更换期限, 尽可能降低成本。
§2 塑料制品的收缩塑料制品在成型过程中存在尺寸变小的收缩现象, 收缩的大小用收缩率表示。
%10000⨯-=L LL S 式中S ——收缩率;L 0——室温时的模具尺寸; L ——室温时的塑料制品尺寸。
影响收缩率的主要因素有:(1) 成型压力。
型腔内的压力越大, 成型后的收缩越小。
非结晶型塑料和结晶型塑料的收缩率随内压的增大分别呈直线和曲线形状下降。
(2) 注射温度。
温度升高, 塑料的膨胀系数增大, 塑料制品的收缩率增大。
塑料件的设计规范
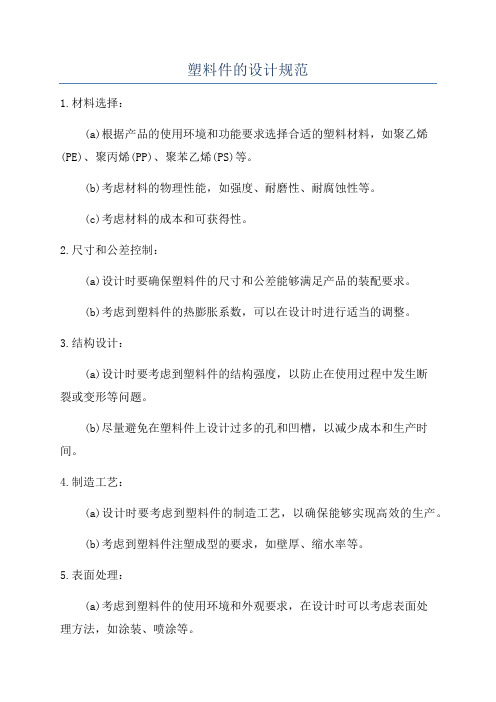
塑料件的设计规范1.材料选择:(a)根据产品的使用环境和功能要求选择合适的塑料材料,如聚乙烯(PE)、聚丙烯(PP)、聚苯乙烯(PS)等。
(b)考虑材料的物理性能,如强度、耐磨性、耐腐蚀性等。
(c)考虑材料的成本和可获得性。
2.尺寸和公差控制:(a)设计时要确保塑料件的尺寸和公差能够满足产品的装配要求。
(b)考虑到塑料件的热膨胀系数,可以在设计时进行适当的调整。
3.结构设计:(a)设计时要考虑到塑料件的结构强度,以防止在使用过程中发生断裂或变形等问题。
(b)尽量避免在塑料件上设计过多的孔和凹槽,以减少成本和生产时间。
4.制造工艺:(a)设计时要考虑到塑料件的制造工艺,以确保能够实现高效的生产。
(b)考虑到塑料件注塑成型的要求,如壁厚、缩水率等。
5.表面处理:(a)考虑到塑料件的使用环境和外观要求,在设计时可以考虑表面处理方法,如涂装、喷涂等。
(b)考虑到塑料件的耐候性,可以选择添加防紫外线(UV)剂。
6.排气和冷却:(a)设计时要确保塑料件的排气和冷却能够满足注塑成型的要求,以避免缺陷的产生。
(b)考虑到塑料件的形状和厚度变化,可以适当设计出气道和冷却系统。
7.注塑模具设计:(a)考虑到塑料件的形状、尺寸和结构,设计合适的注塑模具,以确保能够生产出符合要求的塑料件。
(b)考虑到模具的制造成本和使用寿命,可以合理选择模具材料和加工工艺。
总而言之,塑料件的设计规范是为了确保产品质量和生产效率,在材料选择、尺寸和公差控制、结构设计、制造工艺、表面处理、排气和冷却、注塑模具设计等方面提供了一些指导和标准。
通过遵守这些规范,设计师可以设计出高质量的塑料件,从而满足客户的需求。
塑胶结构设计规范
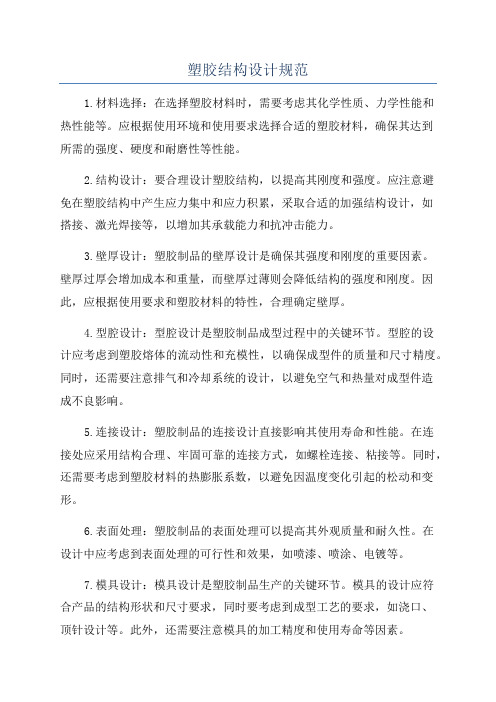
塑胶结构设计规范1.材料选择:在选择塑胶材料时,需要考虑其化学性质、力学性能和热性能等。
应根据使用环境和使用要求选择合适的塑胶材料,确保其达到所需的强度、硬度和耐磨性等性能。
2.结构设计:要合理设计塑胶结构,以提高其刚度和强度。
应注意避免在塑胶结构中产生应力集中和应力积累,采取合适的加强结构设计,如搭接、激光焊接等,以增加其承载能力和抗冲击能力。
3.壁厚设计:塑胶制品的壁厚设计是确保其强度和刚度的重要因素。
壁厚过厚会增加成本和重量,而壁厚过薄则会降低结构的强度和刚度。
因此,应根据使用要求和塑胶材料的特性,合理确定壁厚。
4.型腔设计:型腔设计是塑胶制品成型过程中的关键环节。
型腔的设计应考虑到塑胶熔体的流动性和充模性,以确保成型件的质量和尺寸精度。
同时,还需要注意排气和冷却系统的设计,以避免空气和热量对成型件造成不良影响。
5.连接设计:塑胶制品的连接设计直接影响其使用寿命和性能。
在连接处应采用结构合理、牢固可靠的连接方式,如螺栓连接、粘接等。
同时,还需要考虑到塑胶材料的热膨胀系数,以避免因温度变化引起的松动和变形。
6.表面处理:塑胶制品的表面处理可以提高其外观质量和耐久性。
在设计中应考虑到表面处理的可行性和效果,如喷漆、喷涂、电镀等。
7.模具设计:模具设计是塑胶制品生产的关键环节。
模具的设计应符合产品的结构形状和尺寸要求,同时要考虑到成型工艺的要求,如浇口、顶针设计等。
此外,还需要注意模具的加工精度和使用寿命等因素。
总之,塑胶结构设计规范是保证塑胶制品质量和性能的重要保证。
通过合理的材料选择、结构设计、壁厚设计等,可以提高塑胶结构的强度、刚度和耐久性,从而满足不同的使用需求。
塑胶结构设计规范

1、材料及厚度1.1、材料的选取a. ABS:高流动性,便宜,适用于对强度要求不太高的部件(不直接受冲击,不承受可靠性测试中结构耐久性的部件),如内部支撑架(键板支架、LCD支架)等。
还有就是普遍用在电镀的部件上(如按钮、侧键、导航键、电镀装饰件等)。
目前常用奇美PA-757、PA-777D等。
b. PC+ABS:流动性好,强度不错,价格适中。
适用于作高刚性、高冲击韧性的制件,如框架、壳体等。
常用材料代号:拜尔T85、T65。
c. PC:高强度,价格贵,流动性不好。
适用于对强度要求较高的外壳、按键、传动机架、镜片等。
常用材料代号如:帝人L1250Y、PC2405、PC2605。
d. POM具有高的刚度和硬度、极佳的耐疲劳性和耐磨性、较小的蠕变性和吸水性、较好的尺寸稳定性和化学稳定性、良好的绝缘性等。
常用于滑轮、传动齿轮、蜗轮、蜗杆、传动机构件等,常用材料代号如:M90-44。
e. PA坚韧、吸水、但当水份完全挥发后会变得脆弱。
常用于齿轮、滑轮等。
受冲击力较大的关键齿轮,需添加填充物。
材料代号如:CM3003G-30。
f. PMMA有极好的透光性,在光的加速老化240小时后仍可透过92%的太阳光,室外十年仍有89%,紫外线达78.5% 。
机械强度较高,有一定的耐寒性、耐腐蚀,绝缘性能良好,尺寸稳定,易于成型,质较脆,常用于有一定强度要求的透明结构件,如镜片、遥控窗、导光件等。
常用材料代号如:三菱VH001。
1.2 壳体的厚度a. 壁厚要均匀,厚薄差别尽量控制在基本壁厚的25%以内,整个部件的最小壁厚不得小于0.4mm,且该处背面不是A级外观面,并要求面积不得大于100mm²。
b. 在厚度方向上的壳体的厚度尽量在1.2~1.4mm,侧面厚度在1.5~1.7mm;外镜片支承面厚度0.8mm,内镜片支承面厚度最小0.6mm。
c. 电池盖壁厚取0.8~1.0mm。
d. 塑胶制品的最小壁厚及常见壁厚推荐值见下表。
塑胶结构设计要求规范
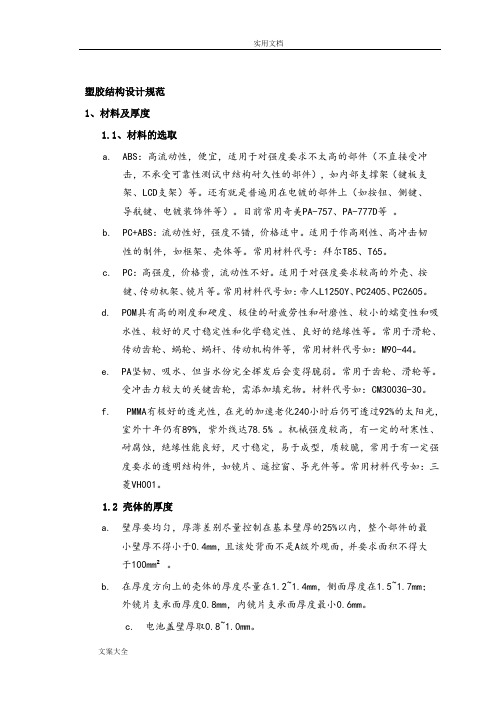
塑胶结构设计规范1、材料及厚度1.1、材料的选取a. ABS:高流动性,便宜,适用于对强度要求不太高的部件(不直接受冲击,不承受可靠性测试中结构耐久性的部件),如内部支撑架(键板支架、LCD支架)等。
还有就是普遍用在电镀的部件上(如按钮、侧键、导航键、电镀装饰件等)。
目前常用奇美PA-757、PA-777D等。
b. PC+ABS:流动性好,强度不错,价格适中。
适用于作高刚性、高冲击韧性的制件,如框架、壳体等。
常用材料代号:拜尔T85、T65。
c. PC:高强度,价格贵,流动性不好。
适用于对强度要求较高的外壳、按键、传动机架、镜片等。
常用材料代号如:帝人L1250Y、PC2405、PC2605。
d. POM具有高的刚度和硬度、极佳的耐疲劳性和耐磨性、较小的蠕变性和吸水性、较好的尺寸稳定性和化学稳定性、良好的绝缘性等。
常用于滑轮、传动齿轮、蜗轮、蜗杆、传动机构件等,常用材料代号如:M90-44。
e. PA坚韧、吸水、但当水份完全挥发后会变得脆弱。
常用于齿轮、滑轮等。
受冲击力较大的关键齿轮,需添加填充物。
材料代号如:CM3003G-30。
f. PMMA有极好的透光性,在光的加速老化240小时后仍可透过92%的太阳光,室外十年仍有89%,紫外线达78.5% 。
机械强度较高,有一定的耐寒性、耐腐蚀,绝缘性能良好,尺寸稳定,易于成型,质较脆,常用于有一定强度要求的透明结构件,如镜片、遥控窗、导光件等。
常用材料代号如:三菱VH001。
1.2 壳体的厚度a. 壁厚要均匀,厚薄差别尽量控制在基本壁厚的25%以内,整个部件的最小壁厚不得小于0.4mm,且该处背面不是A级外观面,并要求面积不得大于100mm²。
b. 在厚度方向上的壳体的厚度尽量在1.2~1.4mm,侧面厚度在1.5~1.7mm;外镜片支承面厚度0.8mm,内镜片支承面厚度最小0.6mm。
c. 电池盖壁厚取0.8~1.0mm。
d. 塑胶制品的最小壁厚及常见壁厚推荐值见下表。
塑料制品的结构设计规范
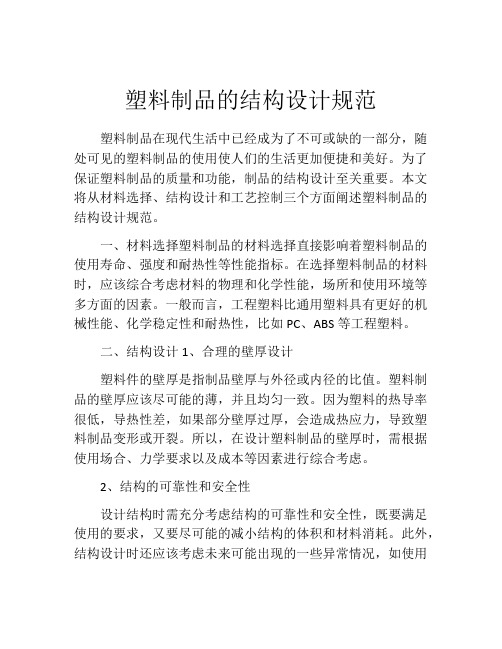
塑料制品的结构设计规范塑料制品在现代生活中已经成为了不可或缺的一部分,随处可见的塑料制品的使用使人们的生活更加便捷和美好。
为了保证塑料制品的质量和功能,制品的结构设计至关重要。
本文将从材料选择、结构设计和工艺控制三个方面阐述塑料制品的结构设计规范。
一、材料选择塑料制品的材料选择直接影响着塑料制品的使用寿命、强度和耐热性等性能指标。
在选择塑料制品的材料时,应该综合考虑材料的物理和化学性能,场所和使用环境等多方面的因素。
一般而言,工程塑料比通用塑料具有更好的机械性能、化学稳定性和耐热性,比如PC、ABS等工程塑料。
二、结构设计1、合理的壁厚设计塑料件的壁厚是指制品壁厚与外径或内径的比值。
塑料制品的壁厚应该尽可能的薄,并且均匀一致。
因为塑料的热导率很低,导热性差,如果部分壁厚过厚,会造成热应力,导致塑料制品变形或开裂。
所以,在设计塑料制品的壁厚时,需根据使用场合、力学要求以及成本等因素进行综合考虑。
2、结构的可靠性和安全性设计结构时需充分考虑结构的可靠性和安全性,既要满足使用的要求,又要尽可能的减小结构的体积和材料消耗。
此外,结构设计时还应该考虑未来可能出现的一些异常情况,如使用环境的变化、超负荷的物理作用和力学应力等因素都应该在结构设计中进行考虑。
三、工艺控制优秀的结构设计标准是塑料制品质量保证的前提,但良好的生产工艺过程也是确保质量的关键。
生产过程中应该选择先进的生产工艺技术,如模具设计、注塑机选型和注射参数的调控等。
此外,应该做好产品的标准化、精细化生产和检验工作,以确保产品品质达到标准。
综上所述,塑料制品的结构设计对产品质量至关重要,必须遵循一定的规范和标准进行设计和制造。
同时,在生产过程中也需要遵循简单、精细、标准化、自动化和人性化原则。
一旦遇到质量问题,企业应该采取积极有效的措施,及时处理,以免造成不必要的损失和影响公司声誉。
塑胶结构设计要求规范
实用文档塑胶结构设计规范1、材料及厚度1.1、材料的选取a. ABS:高流动性,便宜,适用于对强度要求不太高的部件(不直接受冲击,不承受可靠性测试中结构耐久性的部件),如内部支撑架(键板支架、LCD支架)等。
还有就是普遍用在电镀的部件上(如按钮、侧键、导航键、电镀装饰件等)。
目前常用奇美PA-757、PA-777D等。
b. PC+ABS:流动性好,强度不错,价格适中。
适用于作高刚性、高冲击韧性的制件,如框架、壳体等。
常用材料代号:拜尔T85、T65。
c. PC:高强度,价格贵,流动性不好。
适用于对强度要求较高的外壳、按键、传动机架、镜片等。
常用材料代号如:帝人L1250Y、PC2405、PC2605。
d. POM具有高的刚度和硬度、极佳的耐疲劳性和耐磨性、较小的蠕变性和吸水性、较好的尺寸稳定性和化学稳定性、良好的绝缘性等。
常用于滑轮、传动齿轮、蜗轮、蜗杆、传动机构件等,常用材料代号如:M90-44。
e. PA坚韧、吸水、但当水份完全挥发后会变得脆弱。
常用于齿轮、滑轮等。
受冲击力较大的关键齿轮,需添加填充物。
材料代号如:CM3003G-30。
f. PMMA有极好的透光性,在光的加速老化240小时后仍可透过92%的太阳光,室外十年仍有89%,紫外线达78.5% 。
机械强度较高,有一定的耐寒性、耐腐蚀,绝缘性能良好,尺寸稳定,易于成型,质较脆,常用于有一定强度要求的透明结构件,如镜片、遥控窗、导光件等。
常用材料代号如:三菱VH001。
1.2 壳体的厚度a. 壁厚要均匀,厚薄差别尽量控制在基本壁厚的25%以内,整个部件的最小壁厚不得小于0.4mm,且该处背面不是A级外观面,并要求面积不得大于100mm2。
b. 在厚度方向上的壳体的厚度尽量在 1.2~1.4mm,侧面厚度在1.5~1.7mm;外镜片支承面厚度0.8mm,内镜片支承面厚度最小0.6mm。
c. 电池盖壁厚取0.8~1.0mm。
文案大全。
塑料制品的设计(强行脱模、表面质量)
塑胶制品结构的设计
一.制品结构工艺设计的原则:
1.在保证制品性能和使用要求的情况下,尽量选用价廉、且成型性能好的塑料;
2.力求使制品结构简单,避免侧向凹凸结构,使模具结构简单,易于制造;(内侧凹凸结构有两种情况可不用内行位:碰穿和强行脱模)
•注:关于强行脱模:
1)当侧向凹凸较浅且允许有圆角时,可强行脱模;
2)可强行脱模的塑料有PE、PP、POM和PVC等;
三、制品的表面质量:
1、包括制造质量:型腔省模抛光,一般模具型腔粗糙度为
Ra0.02—1.25um,制品的粗糙度比模具型腔粗糙度低1-2级。
2、注塑质量:水花,蛇纹,熔接痕,顶白变形,黑斑,披锋、
凹痕等。
3、烤柒质量:
4、电镀质量:
5、丝印质量:
6、拉丝质量:
7、抛光质量:
8、汤金质量
9、贴纸质量
10、贴片
四.塑料制品的常见结构设计:
1.脱模斜度:
1).不同塑料的脱模斜度不同,在不影响产品性能的情况下,脱模斜度尽量取较大值;
2).脱模斜度不包括在公差范围之内;
3).晒纹脱模斜度应取较大值,
一般为3°~9°;
4).硬质塑料比软质塑料的脱模斜度大,收缩率大的塑料比收缩率小的脱模斜度大;
5)、制品高度越高,孔越深,为保证精度要求,脱模斜度宜取小一点;
6)、制品形状复杂难脱模时,脱模斜度要大一些;
7)、前模脱模斜度大于后模脱模斜度;
8)、配合精度要求越高,脱模斜度要越小;
9)、壁厚大的制品,脱模斜度可取较大值;机械性能强塑料,自润滑性塑料,脱模斜度可取小一些。
塑料产品结构设计通用规范
塑料产品设计规范一、塑料及塑料模的基本概念1.1 塑料的分类及性能塑料的品种很多,可以按其组成、性质和用途等对它们进行分类。
1.1.1 依据其热性能分类按照热性能塑料可以分为热塑性塑料和热固性塑料两类。
塑料受热熔融,冷却后凝固,再次加热又可软化熔融,重新制成产品,这一过程可以反复进行多次,而材料的化学结构基本上不起变化,称之为热塑性塑料。
常用的热塑性塑料有:聚乙烯、聚丙烯、聚苯乙烯、聚氯乙烯等。
在一定温度下能变成粘稠状态,但是经过一定时间加热塑制成形后,不会因再度加热而软化熔融。
这是因为在成形过程中聚合物分子之间发生了化学反应,形成了交联网状结构,使之成为不熔的固态,所以只能塑制一次,称为热固性塑料。
常用的热固性塑料有:酚醛树脂、环氧树脂、有机硅塑料等。
1.1.2 依据其用途分类按用途不同塑料可以分为通用塑料、工程塑料和特种塑料。
一般把价格低、产量大、用途广而受力不大的,常用于制造日用品的塑料称为通用塑料。
例如:聚乙烯、聚丙烯、聚氯乙烯、酚醛、聚苯乙烯等等。
把机械强度高、刚性大的,常用于取代钢铁或有色金属材料制造机械零件或工程结构受力件的塑料称为工程塑料。
例如:聚砜、聚酰胺、聚碳酸酯、聚醚酮等等。
另外,将一些具有特殊功能的塑料,称为特种塑料。
例如:导电的聚乙炔、耐高温的聚芳砜等。
随着聚合物合成技术的发展,塑料可以通过采取各种措施来改进性能和增加强度,从而制成新颖的塑料品种。
1.2 塑料成形方法及塑料的种类1.2.1 塑料的成形方法1.注射成形:注射成形技术是据压铸原理发展起来的,是目前塑料加工中最普遍采用的方法之一。
注射成形是间歇操作,成形周期短,生产效率高,产品种类繁多,生产灵活。
其制品已占塑料制品总产量的30%以上。
注射成形的工艺原理是将颗粒状塑料原料置于塑料注射成形机内并加热熔化,通过压力作用注射到模具内定型,经过一段时间冷却后取出制品。
2.吹塑成形:吹塑成形是目前塑料成形生产的主要方法,它包括挤出吹塑,如吹塑薄膜;中空吹塑,如吹塑中空的塑料容器等。
塑料制品的设计规范
的充模流动阻力。如图3-13 ⑵应避免或减少塑料的局部集中,
以防止产生凹陷和气泡。如图3-14 ⑶加强筋以设计矮一些多一些为好。 ⑷筋与筋的间隔距离应大于塑件的
壁厚。
PPT文档演模板
塑料制品的设计规范
3.4.5 增加刚性减少变形的其他措施
将薄壳状的塑件设计为球面, 拱曲面等, 可 以有效地增加刚性、减少变形。
PPT文档演模板
塑料制品的设计规范
3.4.3 加强筋及其它增强结构
为了提高塑件的强度和防止塑件翘曲变形, 常设计加强筋,如图筋的设置位置应沿塑料 充模流向,降低充模流动阻力. 见图3-12
加强筋的正确形状和尺寸比例如图3-15 所示。
PPT文档演模板
塑料制品的设计规范
3.4.4 加强筋的主要形式
PPT文档演模板
塑料制品的设计规范
3.2 尺寸精度与表面质量
3.2.1 尺寸精度 3.2.2 尺寸精度的确定 3.2.3 表面质量
PPT文档演模板
塑料制品的设计规范
3.2 尺寸精度与表面质量
3.2.1 尺寸精度 1、塑件尺寸概念
塑件尺寸——塑件的总体尺寸。 2.塑料制品总体尺寸受限制的主要 因素:
PPT文档演模板
塑料制品的设计规范
3.2 尺寸精度与表面质量
3.2.2 尺寸精度的确定
表3—1是模塑件尺寸公差国家标 准(GB/T 14486-1993), 表 3—2是常用塑料材料的公差等级选 用。
将表3—1和表3—2结合起来使
用, 先查表3—2, 根据模塑件的材料
品种及用要求选定塑件的尺寸精度
图3—6 可强制脱模的浅侧凹结构
a)(A-B)×100%/B≤5% b) (A-B)×100%/C≤5%
- 1、下载文档前请自行甄别文档内容的完整性,平台不提供额外的编辑、内容补充、找答案等附加服务。
- 2、"仅部分预览"的文档,不可在线预览部分如存在完整性等问题,可反馈申请退款(可完整预览的文档不适用该条件!)。
- 3、如文档侵犯您的权益,请联系客服反馈,我们会尽快为您处理(人工客服工作时间:9:00-18:30)。
双林汽车部件股份有限公司企业技术规范塑料制品的结构设计规范2008-10-20发布2008-10-XX实施双林汽车部件股份有限公司发布塑料制品的结构设计又称塑料制品的功能特性设计或塑料制品的工艺性。
§1 1.1塑料制品设计的一般程序和原则塑料制品设计的一般程序1.21、详细了解塑料制品的功能、环境条件和载荷条件2、选定塑料品种3、制定初步设计方案,绘制制品草图(形状、尺寸、壁厚、加强筋、孔的位置等)4、样品制造、进行模拟试验或实际使用条件的试验5、制品设计、绘制正规制品图纸6、编制文件,包括塑料制品设计说明书和技术条件等。
塑料制品设计的一般原则1、在选料方面需考虑:(1) 塑料的物理机械性能,如强度、刚性、韧性、弹性、吸水性以及对应力的敏感性等;(2) 塑料的成型工艺性,如流动性、结晶速率,对成型温度、压力的敏感性等;(3) 塑料制品在成型后的收缩情况,及各向收缩率的差异。
2、在制品形状方面:能满足使用要求,有利于充模、排气、补缩,同时能适应高效冷却硬化(热塑性塑料制品)或快速受热固化(热固性塑料制品)等。
3、在模具方面:应考虑它的总体结构,特别是抽芯与脱出制品的复杂程度。
同时应充分考虑模具零件的形状及其制造工艺,以便使制品具有较好的经济性。
4、在成本方面:要考虑注射制品的利润率、年产量、原料价格、使用寿命和更换期限,尽可能降低成本。
§2塑料制品的收缩塑料制品在成型过程中存在尺寸变小的收缩现象,收缩的大小用收缩率表示。
S L0 LL0100%式中S——收缩率;L0——室温时的模具尺寸;L——室温时的塑料制品尺寸。
影响收缩率的主要因素有:(1)成型压力。
型腔内的压力越大,成型后的收缩越小。
非结晶型塑料和结晶型塑料的收缩率随内压的增大分别呈直线和曲线形状下降。
(2) 注射温度。
温度升高,塑料的膨胀系数增大,塑料制品的收缩率增大。
但温度升高熔料的密度增大,收缩率反又减小。
两者同时作用的结果一般是,收缩率随温度的升高而减小。
(3) 模具温度。
通常情况是,模具温度越高,收缩率增大的趋势越明显。
(4)成型时间。
成型时保压时间一长,补料充分,收缩率便小。
与此同时,塑料的冻结取向要加大,制品的内应力亦大,收缩率也就增大。
成型的冷却时间一长,塑料的固化便充分,收缩率亦小。
(5)制品壁厚。
结晶型塑料(聚甲醛除外)的收缩率随壁厚的增加而增加,而非结晶型塑料中,收缩率的变化又分下面几种情况:ABS和聚碳酸酯等的收缩率不受壁厚的影响;聚乙烯、丙烯腈—苯乙烯、丙烯酸类等塑料的收缩率随壁厚的增加而增加;硬质聚氯乙烯的收缩率随壁厚的增加而减小。
(6)进料口尺寸。
进料口尺寸大,塑料制品致密,收缩便小。
(7)玻璃纤维等的填充量。
收缩率随填充量的增加而减小。
表2-1、表2-2、表2-3为常用塑料的成型收缩率。
密级:内部公开/秘密§3脱模斜度3.1脱模斜度:为便于脱模,塑料制品壁在出模方向上应具有倾斜角度α,其值以度数表示(参见表2-4)。
脱模斜度确定要点(1)制品精度要求越高,脱模斜度应越小。
(2)尺寸大的制品,应采用较小的脱模斜度。
(3)制品形状复杂不易脱模的,应选用较大的斜度。
(4)制品收缩率大,斜度也应加大。
(5)增强塑料宜选大斜度,含有自润滑剂的塑料可用小斜度。
(6)制品壁厚大,斜度也应大。
(7)斜度的方向。
内孔以小端为准,满足图样尺寸要求,斜度向扩大方向取得;外形则以大端为准,满足图样要求,斜度向偏小方向取得。
一般情况下脱模斜度。
可不受制品公差带的限制,高精度塑料制品的脱模斜度则应当在公差带内。
脱模斜度α值可按表2-4 选取。
3.2由表中可以看出,塑料硬脆、刚性大的,脱模斜度要求大。
具备以下条件的型芯,可采用较小的脱模斜度:(1)顶出时制品刚度足够。
(2)制品与模具钢材表面的摩擦系数较低。
(3)型芯表面的粗糙度值小,抛光方向又与制品的脱模方向—致。
(4) 制品收缩量小,滑动摩擦力小。
制品脱模斜度设计1、箱体与盖类制品(图2-1)当H≤50mm时,S/H=1/30~1/50当50<H≤100mm 时,S/H≤1/602、格子板形制品(图2-2)当格子的间距P≤4mm 时,脱模斜度α=1/10P。
格子C 尺寸越大,脱模斜度越大。
当格子高度H超过8mm,脱模斜度不能取太大值时,可采用图(b)的形式,使一部分进入动模一侧,从而使脱模斜度满足要求。
3、带加强筋类制品(图2-3)arctg A B2Harctg(1/500~1/200)A=(1.0~1.8)T mm;B=(0.5~0.7)T mm 4、底筋类制品(图2-4)arctgA B2Harctg (1 / 150 ~ 1 / 100)A=(1.0~1.8)T mm ;B=(0.5~0.7)T mm 5、凸台类制品(图 2-5、表 2-5)arctgD D '2Harctg (1 / 30 ~ 1 / 20)高凸台制品(H >30mm )的脱模斜度: 型芯:arctg型腔:arctgd d ' arctg (1 / 50 ~ 1 / 30) 2H D D ' arctg (1 / 100 ~ 1 / 50)2H型芯的脱模斜度应大于型腔。
6、最小脱模斜度(表 2-6)脱模斜度影响制品的脱出情况。
如果脱模斜度很小,脱模阻力增大,顶出机构就会失去作用。
在一般情 况下,不能小于最小脱模斜度,以防止制品留模。
§4制品壁厚4.1确定合适的制品壁厚是制品设计的主要内容之一。
制品壁厚的作用(1) 使制品具有确定的结构和一定的强度、刚度,以满足制品的使用要求。
(2)成型时具有良好的流动状态(如壁不能过薄)以及充填和冷却效果(如壁不能太厚)4.2密级:内部公开/秘密(3)合理的壁厚使制品能顺利地从模具中顶出。
(4)满足嵌件固定及零件装配等强度的要求。
(5)防止制品翘曲变形。
制品壁厚的设计基本原则——均匀壁厚。
即:充模、冷却收缩均匀、形状性好、尺寸精度高、生产率高。
(1)在满足制品结构和使用要求的条件下,尽可能采用较小的壁厚。
(2)制品壁厚的设计,要能承受顶出装置等的冲击和振动。
(3)在制品的连接固紧处、嵌件埋入处、塑料熔体在孔窗的汇合(熔接痕)处,要具有足够的厚度。
(4) 保证贮存、搬运过程中强度所需的壁厚。
(5)满足成型时熔体充模所需壁厚,既要避免充料不足或易烧焦的薄壁,又要避免熔体破裂或易产生凹陷的厚壁。
制品上相邻壁厚差的关系(薄壁:厚壁)为:热固性塑料:压制1:3,挤塑1:5热塑性塑料:注塑1:1.5(2)当无法避免不均匀的壁厚时,制品壁厚设计可采用逐步过渡的形式(图2-6,图2-7),或者改制成两个制品然后再装配为一个制品(图2-8)等方法。
制品壁厚的设计可参照表2-7~表2-11。
密级:内部公开/秘密§5 5.1加强筋(含凸台、角撑)加强筋的作用(1) 在不加大制品壁厚的条件下,增强制品的强度和刚性,以节约塑料用量,减轻重量,降低成本。
(2) 可克服制品壁厚差带来的应力不均所造成的制品歪扭变形。
5.2密级:内部公开/秘密(3) 便于塑料熔体的流动,在塑料制品本体某些壁部过薄处为熔体的充满提供通道。
加强筋的形状及尺寸塑料制品上加强筋和凸台的形式和应用如图2-9,图2-10所示。
加强筋尺寸参数如图2-11,图2-12 所示。
凸台的形状及尺寸参数如图2-13~图2-15 所示。
角撑位于制品边缘,支撑制品壁面,以增加强度及刚度,尺寸参数如图2-16所示。
5.3加强筋的设计要点(1) 用高度较低、数量稍多的筋代替高度较高的单一加强筋,避免厚筋底冷却收缩时产生表面凹陷(图2-17、图2-18)。
当筋的背面出现凹陷影响美观时,可采用图2-19所示的装饰结构予以遮掩。
(2)筋的布置方向最好与熔料的充填方向一致(见表2-12中示例)。
(3)筋的根部用圆弧过渡,以避免外力作用时产生应力集中而破坏。
但根部圆角半径过大则会出现凹陷。
(4)一般不在筋上安置任何零件。
(5)位于制品内壁的凸台不要太靠近内壁,以避免凸台局部熔体充填不足(图2-20)。
加强筋在防止制品变形、增加制品刚性方面的应用如图2-21~图2-22 所示。
加强筋设计注意的问题参见表2-12。
§6支承面制品的支承面不能是整个底面,而应采用凸边或凸起支脚类结构,如三点支承、边框支承等,如图2-23~图2-26所示。
§7圆角制品的两相交平面之间尽可能以圆弧过渡,避免因锐角而造成应力集中等弊病(参见图2-27~图2-30)。
制品圆角的作用有:(1)分散载荷,增强及充分发挥制品的机械强度。
(2)改善塑料熔体的流动性,便于充满与脱模,消除壁部转折处的凹陷等缺陷。
(3)便于模具的机械加工和热处理,从而提高模具的使用寿命。
§81.8.1孔制品孔的形式及成型方法孔的形式很多,主要可分为圆形孔(图2-31、图2-32)和非圆形孔两大类。
8.2根据孔径与孔深度的不同,孔可用下述方法成型:(1)一般孔、浅孔,模塑成型。
(2)深孔,先模塑出孔的一部分深度,其余孔深用机械加工(如钻孔)获得。
(3) 小径深孔(如孔径d<1.5mm),机械加工。
(4)小角度倾斜孔、复杂型孔,采用拼合型芯成型,避免用侧抽芯。
(5)薄壁孔、中心距精度高的孔(孔系),采用模具冲孔,以简化塑模结构。
孔的模塑成型1、盲孔成型(型芯一端固定,参见图2-33、图2-34)图中,D——孔径、L——孔深注射、传递模塑D≤1.5mm,L=DD>1.5mm,L=(2~4)D压缩模塑L=(2~2.5)D2、通孔的成型(图2-35~图2-38)3、复杂型孔的成型(图2-39)4、孔的成型尺寸参数(表2-13~表2-15)8.3孔的设计要点(1)孔与孔的中心距应大于孔径(两者中的小孔)的2 倍,孔中心至边缘的距离为孔径的3 倍。
热塑性和热固性塑料制品的孔心距、孔边距还可参见图2-40和表2-16。
(2)响。
(3)孔周边的壁厚要加大,其值比与之相装配件的外径大20%~40%,以避免收缩应力所造成的不良影制品壁上的孔(即孔轴线与开模方向相垂直),为避免侧向抽芯,可用图2-41中的侧壁凹槽代替。
但图中的m-n面的加工难度加大。
(4)塑料熔体围绕型芯流动汇合而形成塑料制品孔时,会在孔的边缘熔体汇合处形成熔接痕(图2-42),熔接痕的存在削弱了制品的强度。
解决的措施有:1)孔与孔之间应适当加大距离,以避免熔接痕的重合连接(图2-42)。
2)型孔按盲孔设计,留有1/3 壁厚的连皮,以便让熔体从型芯头上越过,使之不出现熔体汇合的熔接痕。
最后钻(冲)掉孔的连皮(图2-43)。
3) 热塑性塑料和层压酚醛塑料的薄壁孔形件(如散热器窗),可用冲裁模冲压出型孔。
(5)需要钻孔的制品,模塑孔时应做出钻头的定位或导向部分的形状(图2-44和图2-45)。