一氧化碳变化反应催化剂
一氧化碳的变换

一氧化碳变换时半水煤气借助于催化剂的作用,在一定温度下,水蒸气反应,生成二氧化碳和氢的工艺过程。
通过变换即除去了一氧化碳,又得到了合成氨的原料气氢和氨加工的原料气二氧化碳。
近年来,变换工段由于采用了低温高活性的催化剂和高串低,高-低-低(俗称“中串低”、“中-低-低”),全低变等多种新工艺流程,加强了热量回收利用,工段面貌发生了很大变化。
1、一氧化碳变换反应的基本原理时什么?其反应的特点时怎么样的?一氧化碳变换反应是在一定条件下,半水煤气中的一氧化碳和水蒸气反应生成氢气和二氧化塔的工艺过程。
CO + H2O <==> CO2 +H2+41kj/mol这是一个可逆放热反应,从化学平衡来看,降低反应温度,增加水蒸气用量,有利于上述可逆反应向二氧化碳和氢气的方向移动,提高平衡变换率。
但是水蒸气增加到一定值后,变换率增加幅度会变小。
温度对变化反应的速度影响较大,而且对正逆反应速度的影响不一样。
温度升高,放热反应即上述变换反应速度增加的慢,逆反应(吸热反应)速度增加得快。
因此,当变换反应开始时,反应物浓度大,提高温度,可加快变换反应,在反应的后一段,二氧化碳和氢的浓度增加,逆反应速度加快,因此,需降低反应温度,使逆反应速度减慢,这样可得到较高的变换率。
提高变化压力,分子间的有效碰撞次数,可以加快变换反应速度,提高催化剂的生产能力。
2“高串低”工艺与传统的高温变换工艺主要有什么不同?有何优点?传统的高温变换工艺,变换炉入口温度一般控制在320~340℃。
在流程设置上一般是一个变换炉,炉内装填铁-铬系催化剂,分两段或三段,半水煤气从上到下一次通过各段催化此后即完成变换过程。
“高串低”工艺与创痛的高温变换工艺主要不同之处是在原高变炉之后,又串联了一个装有钴-钼系列耐硫宽温催化剂的低变炉,形成高变串低变的工艺流程。
耐硫宽温变换催化剂在“高串低”工艺中被利用做低变催化剂。
低变炉入口气体温度一般可控制在210~230℃。
一氧化碳高温变换催化剂使用说明-图片版[1]
![一氧化碳高温变换催化剂使用说明-图片版[1]](https://img.taocdn.com/s3/m/310e8e95dd88d0d233d46ae2.png)
一氧化碳高温变换催化剂使用说明一、变换反应原理一氧化碳变换反应是指一氧化碳与水蒸汽作用生成二氧化碳和氢气的反应,反应如下:C O+H2O H2+C O2+41.19k J/m o l上式是一个典型的气固相反应,它在合成氨,合成甲醇,制氢气、羰基合成气、城市煤气工业中得到了广泛的应用。
一氧化碳变换反应是可逆放热反应,该反应在一般条件下进行得非常缓慢,远不能满足工业生产的需要。
在变换催化剂作用下,可显著提高变换反应的速度,并可防止和减少副反应。
根据化学平衡原理,反应温度越高,变换反应的平衡转化率越低。
在绝热的变换反应器中,为了获得较高的CO变换率,就需要尽可降低催化剂床层入口温度,以使床层出口温度尽可能低,这就要求催化剂具有良好的低温活性。
为了保证变换催化剂不被过度还原,必须在超过化学计量的汽气比下操作。
催化剂使用温度越高,必需采用的汽气比也越高。
如果使用低温活性好的催化剂,整个催化剂床层可在较低的温度下操作,则可以降低变换系统的操作汽气比,节省蒸汽消耗。
二、催化剂的装填催化剂的装填非常重要,将直接影响床层的压力降和气流分布,进而影响催化剂效能的正常发挥。
催化剂的装填方案应认真讨论,可装单一型号的催化剂,也可采用混装法。
如果要使用部分筛过的、比较完好的旧催化剂,应该在一段上部装三分之二的低温活性好的新催化剂;第三段应全装新催化剂;而在一段剩下的三分之一和二段温度较高的部位可装填部分旧催化剂。
这样装填既能发挥新催化剂的低温活性又能合理利用旧催化剂的剩余活性。
推荐装填高度比,二段式1:0.8,三段式1:1:1。
如此装填的目的在于保证一段在较高温度下加快变换反应的速度,而在变换炉最末端温度较低的条件下获得较高的变换率,在装填总量相等的情况下,变换率最高,或变换率一定的情况下蒸汽消耗最低。
1.催化剂装填之前要清除变换炉内杂物,并根据各段的催化剂装量,在炉内标出催化剂装填的高度。
2.炉篦上面要铺一层耐火球和金属网。
一氧化碳变换反应的特点

一氧化碳变换反应的特点
一氧化碳变换反应是一种重要的化学反应,其特点包括氧化还原性质,催化剂的存在以及反应条件的影响等。
一氧化碳变换反应是一种氧化还原反应。
在反应中,一氧化碳(CO)被氧气(O2)氧化为二氧化碳(CO2),伴随着电子的转移。
这是一个典型的氧化反应,其中一氧化碳失去电子,氧气获得电子,因此反应具有明显的氧化性质。
一氧化碳变换反应通常需要催化剂的存在。
由于一氧化碳的氧化反应反应速度较慢,因此需要催化剂来提高反应速率。
常用的催化剂包括过渡金属催化剂如铜、镍、铁等,以及贵金属催化剂如铂、钯等。
催化剂能够提供活性位点,吸附和激活一氧化碳分子,加速反应过程。
一氧化碳变换反应的反应条件对反应速率和选择性有重要影响。
反应温度是影响反应速率的关键因素,一般情况下,较高的反应温度有利于提高反应速率,但过高的温度可能会导致催化剂的失活。
反应气氛也是影响反应的重要因素,一般情况下,反应需要在氧气气氛下进行,以提供氧供反应使用。
在一氧化碳变换反应中,催化剂起着至关重要的作用。
催化剂不仅可以加速反应速率,还可以改变反应的选择性。
例如,在一氧化碳的选择性氧化反应中,铜催化剂可以促使一氧化碳选择性地氧化为
二氧化碳,而不发生过氧化反应。
此外,不同催化剂的选择也会影响反应速率和选择性。
例如,铂催化剂在一氧化碳的氧化反应中具有较高的活性,可以在较低温度下实现高选择性的反应。
一氧化碳变换反应具有明显的氧化还原性质,需要催化剂的存在来提高反应速率,反应条件对反应速率和选择性有重要影响。
这些特点使得一氧化碳变换反应在工业生产和环境保护等领域具有重要应用价值。
影响一氧化碳变换反应的主要因素

影响一氧化碳变换反应的主要因素1.温度对一氧化碳变换反应的影响一氧化碳变换反应是一个可逆放热反应,因此温度升高对反应平衡不利,也就是说一氧化碳的平衡变换率随温度的升高而降低,但在催化剂的活性范围内,提高温度可以加快反应速度,在同一气体组成和汽气比条件下,选择适宜的温度,使它既有利于CO平衡变换率的提高,又能使反应速度加快,以达到最佳的反应效果及最合理的催化剂用量。
催化剂的活性温度越低,在相同条件下,CO的平衡变换率越高,即变换气中CO含量越低。
或者说,在达到相同的CO变换率时,活性越低的催化剂可以控制较低的汽气比,从而节省蒸汽用量。
2.汽气比对CO变换反应的影响汽气比是指入变换炉水蒸汽与煤气中CO的体积比。
(也可用水蒸汽与干半水煤气的体积比表示)汽气比对CO变换率有很大的影响。
CO平衡变换率是随汽气比提高而增加的,但其趋势是先快后慢,即当汽气比较低时CO变换率曲线的斜率很大,随着汽气比的提高,CO变换率曲线斜率逐渐减小,当汽气比提高到某一值时,CO平衡变换率曲线逐渐趋于平坦。
汽气比对反应速度的影响。
一般在汽气比较低时反应速度随汽气比的提高而上升较快,而后随着汽气比的不断上升而逐渐缓慢下,其情况类似于汽气比对CO平衡变换率的影响。
因此在汽气较低的情况下,适当提高汽气比对提高CO变换率及反应速度均有利,但过高的汽气比在经济上是不合算的。
3.压力对CO变换反应的影响CO变换反应是等分子反应,反应前后气体的总体积不变,故压力对反应平衡没有影响。
在变换过程采用加压操作,其目的在于;增加CO的反应速度,提高系统的热利用率减少动力消耗,同时压力提高设备的占地面积更少,流程更紧凑。
研究表明,压力提高催化剂的活性显著提高,反应速度加快。
换句话说,由于加压下反应速度加快,所以催化剂的用量少于同规模下常压变换。
4.空间速度对CO变换反应的影响空间速度简称“空速”。
是指单位时间内通过单位体积的催化剂的气体标准体积数,单位为m3(标)/[m3(催化剂)•h]或简写成h-1。
一氧化碳变换反应温度
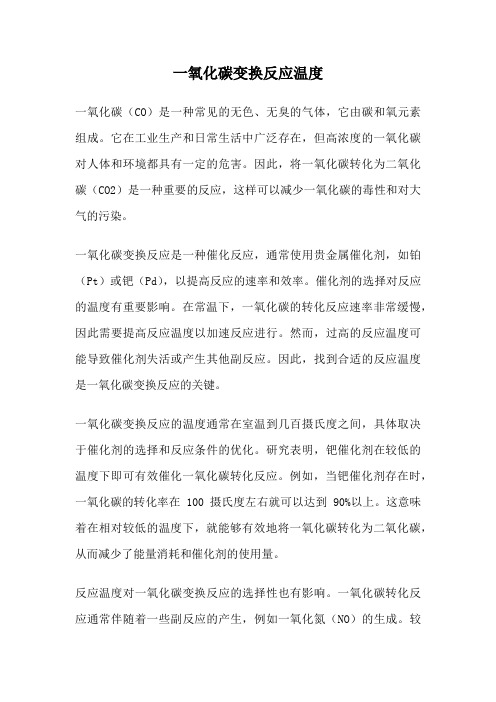
一氧化碳变换反应温度一氧化碳(CO)是一种常见的无色、无臭的气体,它由碳和氧元素组成。
它在工业生产和日常生活中广泛存在,但高浓度的一氧化碳对人体和环境都具有一定的危害。
因此,将一氧化碳转化为二氧化碳(CO2)是一种重要的反应,这样可以减少一氧化碳的毒性和对大气的污染。
一氧化碳变换反应是一种催化反应,通常使用贵金属催化剂,如铂(Pt)或钯(Pd),以提高反应的速率和效率。
催化剂的选择对反应的温度有重要影响。
在常温下,一氧化碳的转化反应速率非常缓慢,因此需要提高反应温度以加速反应进行。
然而,过高的反应温度可能导致催化剂失活或产生其他副反应。
因此,找到合适的反应温度是一氧化碳变换反应的关键。
一氧化碳变换反应的温度通常在室温到几百摄氏度之间,具体取决于催化剂的选择和反应条件的优化。
研究表明,钯催化剂在较低的温度下即可有效催化一氧化碳转化反应。
例如,当钯催化剂存在时,一氧化碳的转化率在100摄氏度左右就可以达到90%以上。
这意味着在相对较低的温度下,就能够有效地将一氧化碳转化为二氧化碳,从而减少了能量消耗和催化剂的使用量。
反应温度对一氧化碳变换反应的选择性也有影响。
一氧化碳转化反应通常伴随着一些副反应的产生,例如一氧化氮(NO)的生成。
较高的反应温度可能导致一氧化氮的生成增加,从而降低了一氧化碳的转化率。
因此,在优化反应温度时,不仅需要考虑反应速率,还需要考虑反应的选择性,以实现高效的一氧化碳转化。
反应温度还与反应系统的热力学平衡有关。
一氧化碳转化反应是一个可逆反应,根据Le Chatelier原理,在较高的温度下,反应平衡会偏向生成较少的产物,即一氧化碳。
因此,在选择反应温度时,需要在反应速率和产物选择性之间进行权衡,以获得最佳的反应效果。
一氧化碳变换反应的温度选择是一个复杂而关键的问题。
合适的反应温度能够提高反应速率和选择性,减少能量消耗和催化剂的使用量。
钯催化剂在较低的温度下已经显示出良好的催化性能,为一氧化碳变换反应的实际应用提供了新的可能性。
co变换反应原理与催化剂

co变换反应原理与催化剂
答案:
CO变换反应是一种重要的化学反应,主要涉及一氧化碳(CO)与水蒸气在催化剂的作用下反应生成氢气(H2)和二氧化碳(CO2)。
这一反应在化工生产中具有广泛的应用,特别是在合成氨和尿素的生产过程中。
反应的化学方程式为:
CO+H2O→H2+CO2
这个反应是可逆的,意味着在一定的条件下,二氧化碳和氢气也可以逆向反应生成一氧化碳和水。
同时,这个反应是放热的,即在反应过程中会释放出热量。
由于这个反应在较高温度下进行时速度较慢,因此需要使用催化剂来加快反应速度。
在实际应用中,使用的催化剂包括铁铬系、铜锌系和钴钼系等,这些催化剂能够显著提高反应速率,使得一氧化碳能够更有效地转化为氢气和二氧化碳。
CO变换反应在工业生产中的应用非常广泛,特别是在合成氨的生产过程中。
由于一氧化碳不是合成氨的直接原料,而且能够使氨合成催化剂中毒,因此在送往合成工序之前,必须将一氧化碳脱除。
通过CO变换反应,可以将大部分一氧化碳转化为二氧化碳和氢气,从而满足合成氨等化工过程的需求。
此外,CO变换反应还在冶金工业和化学工业中用于处理含有一氧化碳的废气,通过加水变换的方式,利用催化剂将一氧化碳转化为无害的二氧化碳,从而达到环保和处理污染的目的。
总的来说,CO变换反应原理及其使用的催化剂在化工生产和环境保护中扮演着重要的角色,通过这一反应,可以有效处理含有一氧化碳的废气,同时为化工过程提供必要的原料气体。
一氧化碳变换
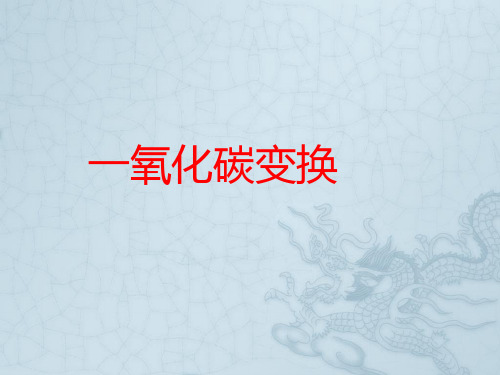
由于CO变换过程是强放热过程,必须分段进行以 利于回收反应热,并控制变换段出口残余CO含量。 第一步是高温变换,使大部分CO转变为CO2和H2;第 二步是低温变换,将CO含量降至0.3%左右。因此, CO变换反应既是原料气制造的继续,又是净化的过程, 为后续脱碳过程创造条件。
• 变化反应热力学
• 反应方程式
结论:在原料气组成一定的条件下,随着温度的降低,变换气 中CO的平衡含量降低,CO 转化率提高;水蒸气的加入量对转 化率有影响,水蒸气的加入量 , CO转化率 。
• 生产实际中反应并没有达到平衡,故常用实际变 换率x表示。
• 以1 mol干原料气为基准,对反应过程中的CO做 物料衡算得
ya yax yax 1 ya
0.009210
450
0.120184
0.036818
0.020748
0.014310
500
0.141059
0.050849
0.029791
0.020951
550
0.161286
0.066249
0.040362
0.028866
600
0.180547
0.082407
0.052123
0.037937
备注 原料干基组成:CO:31.7% CO2:8% H2: 40% N2:20.3%
主活性组分,还 原成Fe3O4后具 有活性
稳定剂,分散在 助催化剂, Fe3O4晶粒之间,提 提高催化剂 高催化剂的耐热性 的活性 和活性,防止Fe3O4 过渡还原为FeO
提高耐 热和耐 硫性能
表 1.3
• 起活性的成份是Fe3O4,催化剂使用前要还原: • 3Fe2O3(s) + CO(g) = 2Fe3O4(s) + CO2(g) • 3Fe2O3(s) + H2(g) = 2Fe3O4(s) + H2O(g) • 还原过程中,除转化成Fe3O4外,还可转化为FeO, Fe等,
一氧化碳变换
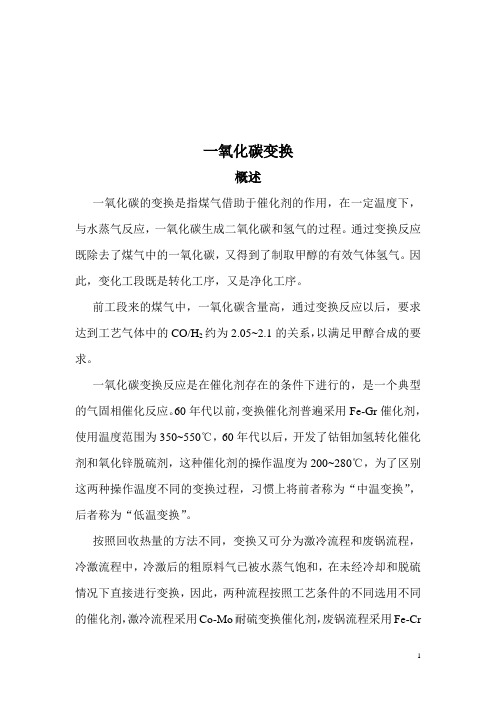
一氧化碳变换概述一氧化碳的变换是指煤气借助于催化剂的作用,在一定温度下,与水蒸气反应,一氧化碳生成二氧化碳和氢气的过程。
通过变换反应既除去了煤气中的一氧化碳,又得到了制取甲醇的有效气体氢气。
因此,变化工段既是转化工序,又是净化工序。
前工段来的煤气中,一氧化碳含量高,通过变换反应以后,要求达到工艺气体中的CO/H2约为2.05~2.1的关系,以满足甲醇合成的要求。
一氧化碳变换反应是在催化剂存在的条件下进行的,是一个典型的气固相催化反应。
60年代以前,变换催化剂普遍采用Fe-Gr催化剂,使用温度范围为350~550℃,60年代以后,开发了钴钼加氢转化催化剂和氧化锌脱硫剂,这种催化剂的操作温度为200~280℃,为了区别这两种操作温度不同的变换过程,习惯上将前者称为“中温变换”,后者称为“低温变换”。
按照回收热量的方法不同,变换又可分为激冷流程和废锅流程,冷激流程中,冷激后的粗原料气已被水蒸气饱和,在未经冷却和脱硫情况下直接进行变换,因此,两种流程按照工艺条件的不同选用不同的催化剂,激冷流程采用Co-Mo耐硫变换催化剂,废锅流程采用Fe-Cr变换催化剂。
第一节变换反应原理变换过程为含有C、H、O三种元素的CO和H2O共存的系统,在CO变换的催化反应过程中,除了主要反应CO+H2O=CO2+H2以外,在某种条件下会发生CO分解等其他副反应,分别如下:2CO=C+CO22CO+2H2=CH4+CO2CO+3H2=CH4+H2OCO2+4H2=CH4+2H2O这些副反应都消耗了原料气中的有效气体,生成有害的游离碳及无用的甲烷,避免副反应的最好方法就是使用选择性好的变换催化剂。
一、变换反应的热效应一氧化碳变换反应是一个放热反应,CO+H2O=CO2+H2+41kJ/gmol反应的热效应视H2O的状态而定,若为液态水,则是微吸热反应,若是水蒸气,则为放热反应。
变换反应的反应热随温度的升高而降低,具体反应热列表如下:表1 CO+H2O=CO2+H2的反应热温度℃25 200 250 300 350 400 450 500 550 △HkJ/gmol 41 39.8 39.5 39 38.5 38 37.6 37 36.6压力对变换反应的反应热影响较小,一般不做考虑。
- 1、下载文档前请自行甄别文档内容的完整性,平台不提供额外的编辑、内容补充、找答案等附加服务。
- 2、"仅部分预览"的文档,不可在线预览部分如存在完整性等问题,可反馈申请退款(可完整预览的文档不适用该条件!)。
- 3、如文档侵犯您的权益,请联系客服反馈,我们会尽快为您处理(人工客服工作时间:9:00-18:30)。
一氧化碳变化反应催化剂一氧化碳变换反应无催化剂存在时,反应速率极慢,即使温度升至700℃以上反应仍不明显,因此必须采用催化剂。
一氧化碳变换催化剂视活性温度和抗硫性能的不同分为铁铬系、铜锌系和钴钼系三种。
一、铁系催化剂1.催化剂的组成和性能以Fe3O4为主相的铁系催化剂因为单纯的Fe3O4在操作温度(温度区间在300~470℃,常称为中温或高温)下,由于结晶颗粒的长大而很快失活,因此在催化主相中加入一定量的结构性助催化剂。
工业上较为成功的助催化剂主要有Cr2O3,因此铁系催化剂也称为铁铬中(高)变催化剂。
铁铬系催化剂其化学组成以Fe2O3为主,促进剂有Cr2O3和K2CO3,活性组分为Fe3O4,开工时需用H2或CO将Fe2O3还原成Fe3O4才有催化活性,适用温度范围300~550℃。
传统的铁铬中变催化剂的结构性助催化剂Cr2O3的含量一般为7%~12%,此外为了改善催化剂的催化活性还添加助催化剂如K+等。
该类催化剂称为中温或高温变换催化剂,因为温度较高,反应后气体中残余CO 含量最低为3%~4%。
如要进一步降低CO残余含量,需在更低温度下完成。
国产中温变换催化剂的性能参数见表1。
为了改善催化剂的使用性能,国内外开发了一系列铁系催化剂。
①低铬型铁铬中变催化剂。
由于Cr2O3对于人体和环境具有毒害作用,为了减少Cr2O3对人体和环境的影响而开发的低铬型铁铬中变催化剂,主要型号有:Bll2、Bll6、Bll7等,其铬含量一般在3%~7%范围内。
②耐硫型铁铬中变催化剂。
为了适应中国中小化肥企业的国情,改善铁铬中变催化剂的耐硫性能,通过添加铝等金属化合物来提高催化剂的耐硫性能,主要型号有:B112、Bll5、Bll7等。
③低水汽比铁铬中变催化剂。
为了改善铁铬中变催化剂对水汽比的适应性,特别是节能型烃类蒸汽转化流程(水碳比小于2.75) 通过添加铜促进剂,改善了铁铬中变催化剂对低水汽比条件的适应性,主要型号有:B113-2等。
表1 国产中温变换催化剂性能参数尽管各种铁铬中变催化剂具有不同的特点,但却具有共同的特性:①具有较高的催化活性。
在活性温度范围内,反应速度较快,可以满足一般工艺的要求;②具有较好的机械强度和较长的使用寿命;③活性温度较高,不利于变换反应的化学平衡,蒸汽消耗较高;④具有一定的抗毒性能,对硫的耐受限度为200mg/m3 (视不同催化剂而不同),但磷砷、氟、氯、硼等化合物是催化剂的毒物;⑤对水汽浓度有一定的要求,当水汽浓度过低时会导致催化剂过度还原。
2.催化剂的还原与氧化中温变换催化剂中的Fe2O3,需经还原成Fe3O4才具有活性,通常是用H2或CO在一定温度下进行还原。
其主要反应式为:3Fe2O3 + H2 = 2Fe3O4 + H2O + 9.6kJ3Fe2O3 + CO = 2Fe3O4 + CO2 + 50.8kJ由于还原反应为放热反应,还原时要严格控制H2和CO的加入量,以避免反应剧烈引起温度急剧升高,而影响催化剂的活性。
同时要加入适量水蒸气,以防Fe3O4被一步还原成Fe,发生过度还原现象。
活性组分Fe3O4在50~60℃以上十分不稳定,遇氧即被氧化,且是剧烈的放热反应。
反应式如下:4Fe3O4 + O2 = 6Fe2O3 + 466kJ因此,在生产中要严格控制原料气中的氧气含量。
在系统停车检修时,先用水蒸气或氮气降低催化剂温度,同时,通入少量空气使催化剂缓慢氧化,在表面形成一层Fe2O3保护膜后,才能与空气接触,这一过程称为催化剂的钝化。
3.催化剂的中毒与衰老在变换生产中,原料气中的硫化物会引起催化剂的中毒,使其活性下降,其反应如下:Fe3O4 + 3H2S + H23FeS + 4H2O + Q由于CO变换时将大部分的有机硫转化为硫化氢,从而使催化剂受大量H2S 毒害。
然而,这个反应是一个可逆放热反应,属于暂时性中毒,当增大水蒸气用量、降低原料气中H2S含量,催化剂的活性即能逐渐恢复。
但是,这种暂时中毒如果反复进行,也会引起催化剂微晶结构发生变化,而导致活性下降。
原料气的灰尘及水蒸气中的无机盐等物质,也会使催化剂的活性显著下降造成永久性中毒。
促使催化剂活性下降的另一个重要因素是催化剂的衰老。
所谓衰老,是指催化剂经过长期使用后活性逐渐下降的现象。
使催化剂衰老的原因有:长期处于高温下,逐渐变质;温度波动,使催化剂过热或熔融;气流不断冲刷,破坏了催化剂表面状态;操作不当,半水煤气中氧含量高和带水等。
二、铜系催化剂1.催化剂的组成与性能金属铜对一氧化碳的变换反应具有较高的活性,但纯的金属铜在催化剂的操作温度(温度区间为200~280℃,常称为低温)下会烧结而引起表面积减小,从而失去活性。
因此必须加入结构性助催化剂以减缓催化剂的烧结。
通常使用最多的结构性助催化剂是氧化锌,因此也称为铜锌低变催化剂。
此外为了改善铜锌低变催化剂的某一方面的性能而引入其他的助催化剂。
铜锌系催化剂由铜、锌、铝(或铬)的氧化物组成,又称低变换催化剂。
其化学组成以CuO为主,ZnO和Al2O3为促进剂和稳定剂。
铜锌系催化剂的活性组分为金属铜,开工时先用氢气将氧化铜还原成具有活性的细小铜晶粒,操作时必须严格控制氢气浓度,以防催化剂烧结。
铜锌系催化剂的弱点是易中毒,低温变换催化剂对硫特别敏感,而且其中毒属于永久性中毒,所以原料气中硫化物的体积分数不得超过0.1×10-6。
铜锌系催化剂适用温度范围200~280℃,反应后残余CO可降至0.2%~0.3%(V/V)。
铜锌系催化剂活性高,若原料气中CO含量高时,应先经高温变换,将CO降至3%左右,再接低温变换,以防剧烈放热而烧坏低变催化剂。
国产低温变换催化剂的性能参数见表2。
为了改善铜系催化剂对硫、水等毒物的耐受性,常添加少量的Cr2O3,但因其毒害作用影响人体和环境,还原期放热量大易导致超温而逐步被淘汰。
主要型号有:B203等。
为了改善铜锌低变催化剂的热稳定性,常添加少量Al2O3,Al2O3能阻止Cu和ZnO微晶的长大,从而稳定催化剂的内部结构,保证其在正常工艺条件下长期运行。
主要型号有:B205、B206等。
铜锌低变催化剂具有共同的特性:①催化活性温度较低.在200℃以下就有很好的催化活性;②催化剂的耐毒性能较差,硫、氯等都是催化剂的毒物,极少量的硫、氯就会引起催化剂中毒;③催化剂的热稳定性也较差,超过300℃就会引起催化剂的活性组份金属铜的烧结而失活;④催化剂的选择性较好,一般不会发生副反应。
表2 国产低温变换催化剂性能参数2.还原和氧化低温变换催化剂用H2或CO进行还原,其反应式如下:CuO + H2 = Cu + H2O(g)+ 86.7kJCuO + CO = Cu + CO2 + 127.7kJ氧化铜的还原反应是强放热反应,而低温变换催化剂对热比较敏感,因此,必须严格控制还原条件,将催化剂层的温度控制在230℃以下。
还原后的催化剂与空气接触,会发生如下反应: CuO + 21CO = CuO + 322.2kJ如果铜催化剂与大量空气接触,放出的反应热将足以使催化剂超温烧结。
因此,停车取出催化剂之前,应先通入少量氧气逐渐将其氧化,在催化剂表面形成一层氧化铜保护膜,才能与空气接触,即进行催化剂的钝化。
钝化过程是用氮气将催化剂层的温度降至150℃,然后在氮气中配入0.2%的氧,在温升不大于50℃的情况下逐渐提高氧的浓度,直到全部切换为空气时,钝化结束。
3.催化剂的中毒低温变换催化剂对毒物十分敏感。
引起催化剂中毒或活性降低的物质有冷凝水、硫化物和氯化物。
原料气在变换系统中,含有大量水蒸气,为避免冷凝水的出现,低变温度一定要高于该条件下气体的露点温度。
硫化物主要来自原料气和中变催化剂的“放硫”,它会使低温变换催化剂永久中毒。
当催化剂硫含量达1.1%,催化剂就基本失去了活性。
所以必须对原料气精细脱硫,使H 2S 含量小于1cm 3/m 3。
所以,采用低温变换的工艺时,前面的脱硫工序一定要采用干法脱硫的方法。
氯化物是对低变催化剂危害最大的毒物,当原料气中氯含量达0.01%时,催化剂就明显中毒。
当氯含量达0.1%时,催化剂的活性基本丧失。
原料气中的氯主要来源于水蒸气,为了保护催化剂,要求水蒸气中氯含量小于0.01cm 3/m 3。
所以,生产上必须对产生蒸汽的锅炉用水进行严格的去氯处理。
三、钴钼耐硫系催化剂钴钼系催化剂是上世纪50年代后期开发的一种耐硫变换催化剂,主要成分为钴、钼氧化物。
活性温度不同,有只适用于高温变换的,也有适于高、低温变换的。
其化学组成是钴、钼氧化物并负载在氧化铝上,活性组分为钼的硫化物,反应前将钴、钼氧化物转变为硫化物(预硫化)才有活性,故开工时需先进行硫化处理。
钴钼系耐硫催化剂适用温度范围160~500℃,属宽温变换催化剂。
其特点是耐硫抗毒,使用寿命长。
国内外耐硫宽温变换催化剂性能参数见表表国内外耐硫宽温变换催化剂性能参数⒉催化剂的活化钴钼系耐硫催化剂的主要组分是氧化钴和氧化钼,使用前需将其转化为硫化钴和硫化钼才具有活性,这一过程称为硫化。
对催化剂进行硫化,可用含氢的二硫化碳,也可直接用硫化氢或用未脱硫的原料气。
为了缩短硫化时间,保证活化效果,工业上一般都采用在干半水煤气中加CS2为硫化剂。
其硫化反应式如下:CS2 + 4H22H2S + CH4 + 240.6kJM O O3 + 2H2S + H2M O S2 + 3H2O + 48.1kJC O O + H2S C O S + H2O + 13.4kJ催化剂硫化前需升温,可用氮气或天然气及干半水煤气(或干变换气)作为热载体,通过电加热器加热后,进入催化剂床层进行升温。
升温过程不能使用水蒸气,否则会降低催化剂活性。
当催化剂的温度升到200℃时,向系统通入CS2使其与氧气发生反应产生H2S,进行硫化,并在床层低于250℃时升温硫化完成,直到入口和出口气体中的硫化氢含量基本相同时即为硫化终点。
硫化反应为放热反应,因此气体中硫化物的浓度不宜过高,以免催化剂床层超温。
硫化反应是可逆的,在一定反应温度、蒸汽量和H2S浓度下,活性组分COS 和M O S2将会发生水解,转化为氧化态并放出硫化氢,即反硫化反应,使催化剂活性下降。
因此,正常操作时原料气中应有一最低的硫化氢含量。
最低硫化氢含量受反应温度及汽气比的影响,温度及汽气比越低,最低硫化氢含量越低,催化剂不易反硫化。
⒊催化剂的中毒在变换过程中,原料气中的氧会使耐硫变换催化剂缓慢发生硫酸盐化,使C O S和M O S2中的硫离子氧化成硫酸根,继而硫酸根与催化剂中的钾离子反应生成K2SO4,从而导致催化剂低温活性的丧失。
所以用于低变的耐硫催化剂床层前一定要设置一层保护剂及除氧剂,以避免氧等杂质进入低变催化剂,使催化剂活性下降。