苯-甲苯精馏浮阀塔
课程设计----苯-甲苯连续精馏浮阀塔设计.

设计任务书设计题目:苯-甲苯连续精馏浮阀塔设计设计条件:常压: 1p atm =处理量:100Kmol h进料组成: 0.45f x =馏出液组成: 98.0=d x釜液组成: 02.0=w x (以上均为摩尔分率)塔顶全凝器: 泡点回流 回流比: min (1.1 2.0)R R =-加料状态: 0.96q =单板压降: 0.7a kp ≤设 计 要 求 :(1) 完成该精馏塔的工艺设计(包括物料衡算、热量衡算、筛板塔的设计算)。
(2) 画出带控制点的工艺流程图、塔板负荷性能图、精馏塔工艺条件图。
(3) 写出该精馏塔的设计说明书,包括设计结果汇总和设计评价。
目录摘要 (1)绪论 (2)设计方案的选择和论证 (3)第一章塔板的工艺计算 (4)1.1基础物性数据 (4)1.2精馏塔全塔物料衡算 (4)1.2.1已知条件 (4)1.2.2物料衡算 (5)1.2.3平衡线方程的确定 (5)1.2.4求精馏塔的气液相负荷 (6)1.2.5操作线方程 (6)1.2.6用逐板法算理论板数 (6)1.2.7实际板数的求取 (7)1.3精馏塔的工艺条件及有关物性数据的计算 (8)1.3.1进料温度的计算 (8)1.3.2操作压力的计算 (8)1.3.3平均摩尔质量的计算 (8)1.3.4平均密度计算 (9)1.3.5液体平均表面张力计算 (10)1.3.6液体平均粘度计算 (10)1.4 精馏塔工艺尺寸的计算 (10)1.4.1塔径的计算 (10)1.4.2精馏塔有效高度的计算 (11)1.5 塔板主要工艺尺寸的计算 (12)1.5.1溢流装置计算 (12)1.6浮阀数目、浮阀排列及塔板布置 (13)1.7塔板流体力学验算 (14)1.7.1计算气相通过浮阀塔板的静压头降h f (14)1.7.2计算降液管中清夜层高度Hd (15)1.7.3计算雾沫夹带量e V (15)1.8塔板负荷性能图 (16)1.8.1雾沫夹带线 (16)1.8.2液泛线 (17)1.8.3 液相负荷上限线 (18)1.8.4漏液线 (18)1.8.5液相负荷下限线 (18)1.9小结 (19)第二章热量衡算 (20)2.1相关介质的选择 (20)2.1.1加热介质的选择 (20)2.1.2冷凝剂 (20)2.2热量衡算 (20)第三章辅助设备 (23)3.1冷凝器的选型 (23)3.1.1计算冷却水流量 (23)3.1.2冷凝器的计算与选型 (23)3.2冷凝器的核算 (24)3.2.1管程对流传热系数α1 (24)3.2.2计算壳程流体对流传热系数α0 (25)3.2.3污垢热阻 (26)3.2.4核算传热面积 (26)3.2.5核算压力降 (26)第四章塔附件设计 (29)4.1接管 (29)4.1.1进料管 (29)4.1.2回流管 (29)4.1.3塔底出料管 (29)4.1.4塔顶蒸气出料管 (30)4.1.5塔底进气管 (30)4.2筒体与封头 (30)4.2.1筒体 (30)4.2.2封头 (30)4.3除沫器 (31)4.4裙座 (31)4.5人孔 (31)4.6塔总体高度的设计 (32)4.6.1塔的顶部空间高度 (32)4.6.2塔的底部空间高度 (32)4.6.3塔立体高度 (32)设计结果汇总 (33)结束语 (34)参考文献 (35)主要符号说明 (36)附录 (38)摘要化工生产常需进行二元液相混合物的分离以达到提纯或回收有用组分的目的,精馏是利用液体混合物中各组分挥发度的不同并借助于多次部分汽化和多次部分冷凝达到轻重组分分离目的的方法。
化工原理课程设计 苯-甲苯浮阀精馏塔共19页

3.课程设计报告内容3.1 流程示意图冷凝器→塔顶产品冷却器→苯的储罐→苯↑↓回流原料→原料罐→原料预热器→精馏塔↑回流↓再沸器← → 塔底产品冷却器→甲苯的储罐→甲苯3.2 流程和方案的说明及论证3.2.1 流程的说明首先,苯和甲苯的原料混合物进入原料罐,在里面停留一定的时间之后,通过泵进入原料预热器,在原料预热器中加热到泡点温度,然后,原料从进料口进入到精馏塔中。
因为被加热到泡点,混合物中既有气相混合物,又有液相混合物,这时候原料混合物就分开了,气相混合物在精馏塔中上升,而液相混合物在精馏塔中下降。
气相混合物上升到塔顶上方的冷凝器中,这些气相混合物被降温到泡点,其中的液态部分进入到塔顶产品冷却器中,停留一定的时间然后进入苯的储罐,而其中的气态部分重新回到精馏塔中,这个过程就叫做回流。
液相混合物就从塔底一部分进入到塔底产品冷却器中,一部分进入再沸器,在再沸器中被加热到泡点温度重新回到精馏塔。
塔里的混合物不断重复前面所说的过程,而进料口不断有新鲜原料的加入。
最终,完成苯与甲苯的分离。
3.2.2 方案的说明和论证本方案主要是采用浮阀塔。
精馏设备所用的设备及其相互联系,总称为精馏装置,其核心为精馏塔。
常用的精馏塔有板式塔和填料塔两类,通称塔设备,和其他传质过程一样,精馏塔对塔设备的要求大致如下:一:生产能力大:即单位塔截面大的气液相流率,不会产生液泛等不正常流动。
二:效率高:气液两相在塔内保持充分的密切接触,具有较高的塔板效率或传质效率。
三:流体阻力小:流体通过塔设备时阻力降小,可以节省动力费用,在减压操作是时,易于达到所要求的真空度。
四:有一定的操作弹性:当气液相流率有一定波动时,两相均能维持正常的流动,而且不会使效率发生较大的变化。
五:结构简单,造价低,安装检修方便。
六:能满足某些工艺的特性:腐蚀性,热敏性,起泡性等。
而浮阀塔的优点正是:而浮阀塔的优点正是:1.生产能力大,由于塔板上浮阀安排比较紧凑,其开孔面积大于泡罩塔板,生产能力比泡罩塔板大 20%~40%,与筛板塔接近。
苯-甲苯二元物系浮阀精馏塔设计
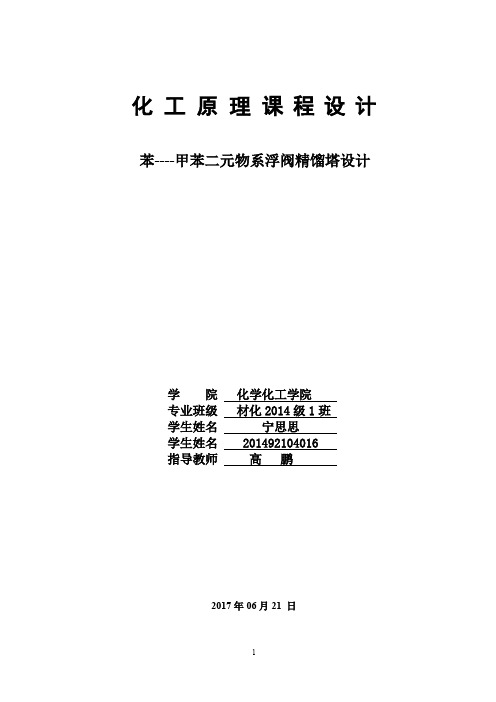
2.1.5 平均密度 计算
[3]
...................................................................... 16
2.2 精馏塔有效塔高的计算 .............................................. 19
..................................................... 26
2.4.4 液相负荷的下限线的绘制 .............................................. 28 2.4.5 液相负荷的上限线的绘制 .............................................. 28 2.4.6 小结 ........................................................... 28
第四章 塔高的计算 .............................................................................................................................................. 33
1.精馏塔概述 .................................................................................................................................... 1 2.仪器的选用 .................................................................................................................................... 2 设 计 方 案 .................................................................. 3 1.1 装置流程的确定 ......................................................................................................................... 3 1.2 操作压力的选择 ......................................................................................................................... 4 1.3 进料状况的选择 ......................................................................................................................... 4 1.4 加热方式的选择 ......................................................................................................................... 4 1.5 回流比的选择 ............................................................................................................................. 5 第一章 塔板的工艺的计算 .................................................................................................................................5 1.1 主要基础物性参数 .......................................................... 5 1.2 精馏塔实际塔板的计算 ...................................................... 6 1.2.1 精馏塔物料衡算 .......................................................... 6 1.2.2 理论塔板数的确定 ........................................................ 7 2.相对挥发度 m 的计算 ......................................................... 7 3.最小回流比的计算 ............................................................ 8 4.精馏塔的气、液相负荷 ........................................................ 8 5.操作线方程的计算 ............................................................ 8 6.精馏塔理论塔板的确定 ........................................................ 9 7.板效率的计算 ................................................................ 9 第二章 精馏塔主要工艺尺寸的设计 .............................................................................................................. 11 2.1 精馏塔的工艺条件及有关物性数据的计算........................................................................................ 11
浮阀精馏塔设计-苯和甲苯

理论塔板计算
相对挥发度α 回流比R 精馏塔的气、液相负荷V’、L’
操作线方程
理论板计算 实际板数计算
理论塔板计算
1.相对挥发度的求取
苯的沸点为 80.1℃,甲苯沸点为 110.6℃ ① 当温度为 80.1℃时
1206 .35 2.006 80.1 220 .24 1343 .94 lg P B 6.078 1.593 80.1 219 .58 lg P A 6.023
物料衡算
2.原料液、塔顶、塔底产品的平均摩尔质量
精馏段的平均摩尔质量 Mvm=(78.35+84.34)/2=81.34 kg/kmol MLm=(78.68+87.43)/2=83.06kg/kmol 提馏的平均摩尔质量 Mvm=(91.49+84.34)/2=87.92 kg/kmol MLm=(91.80+87.43)/2=89.62kg/kmol
1.000 0.922 0.830 0.720 0.596 0.453 0.304 0.128 0
由上表可有 origin 作出如图 1(t-x)曲线
实际板的计算
图1
t-x-y 图
由 t-x-y 图可查得 tD=80.40℃,tW=111.52℃,tF=97.33℃ 全塔平均温度
t td tw 95.96℃ 2
物料衡算
2.原料液、塔顶、塔底产品的平均摩尔质量
进料板平均摩尔质量 由XF =0.336代入气液平衡方程得yF=0.556 MvFm= yFMA+(1-yF)MB =0.556×78.11+(1-0.556)×92.14=84.34kg/kmol MLFm= xFMA+(1-xF)MB =0.336×78.11+(1-0.336)×92.14=87.43kg/kmol 塔底平均摩尔质量 由xw=0.024代入气液平衡方程得yw=0.046 MvFm= ywMA+(1-yw)MB =0.046×78.11+(1-0.046)×92.14=91.49kg/kmol MLFm= xwMA+(1-xw)MB =0.024×78.11+(1-0.024)×92.14=91.80kg/kmol
苯-甲苯浮阀精馏塔课程设计

第一篇化工原理课程设计任务书1.1设计题目苯-甲苯连续精馏(浮阀)塔的设计1.2设计任务1、精馏塔设计的工艺计算及塔设备计算(1)流程及操作条件的确定;物料衡算及热量衡算;(2)塔板数的计算;(3)塔板结构设计(塔板结构参数的确定、流动现象校核、负荷性能图);(4)塔体各接管尺寸的确定;(5)冷却剂与加热剂消耗量的估算。
2.设计说明及讨论3.绘制设计图(1)流程图(A4纸);(2)塔盘布置图(8开坐标纸);(3)工艺条件图(1号绘图纸)。
1.3原始设计数据1、原料液:苯-甲苯,其中苯含量为35 %(质量),常温;2、馏出液含苯:99.2 %(质量);3、残液含苯: 0.5 %(质量);4、生产能力:4000 (kg/h).第二篇流程及流程说明为了能使生产任务长期固定,适宜采用连续精流流程。
贮罐中的原料液用机泵泵入精馏塔,塔釜再沸器用低压蒸汽作为热源加热料液,精馏塔塔顶设有全凝器,冷凝液部分利用重力泡点回流部分连续采出到产品罐(具体流程见附图)。
在流程确定方案选择上,本设计尽可能的减少固定投资,降低操作费用,以期提高经济效益。
1、加料方式的选择:设计任务年产量虽小,但每小时4000Kg的进料量,为维持生产稳定,采用高位槽进料,从减少固定投资,提高经济效益的角度出发,选用泡点进料的加料方式。
2、回流方式的选择:塔的生产负荷不大,从降低操作费用的角度出发,使用列管式冷凝器,利用重力泡点回流,同时也减少了固定投资。
3、再沸器的选择:塔釜再沸器采用卧式换热器,使用低压蒸汽作为热源,做到了不同品位能源的综合利用,大大降低了能源的消耗量。
第三篇 设计计算3.1全塔的物料衡算1、将任务书中的质量分数换算成摩尔分数,进料h km ol 4000=F35%78.110.33835%78.1165%92.13F x ==+(摩尔百分数)0.5%78.110.005890.5%78.1199.5%92.13W x ==+(摩尔百分数)99.2%78.110.99399.2%78.110.8%92.13D x ==+(摩尔百分数)2、求平均分子量,将h kg 换算成 h km ol进料处: 78.110.38892.130.61286.69kg kmol F M =⨯+⨯= 塔顶处: 78.110.99392.130.00778.21kg kmol D M =⨯+⨯= 塔釜处: 78.110.0058992.130.9941192.05kg kmol W M =⨯+⨯= 进料: kmol/h 46.144000/86.69==F 3、全塔的物料衡算由物料衡算得:F F DF W DF x W x D x =+⎧⎨⨯=⨯+⨯⎩代入数据得: ⎩⎨⎧⨯+⨯=⨯+=993.000589.0388.014.4614.46D W DW解之得: ⎩⎨⎧==h kmol 86.17hkmol 28.28D W3.2相对挥发度α及回流比Rα:1、求全塔平均相对挥发度表3-11 2 3 4 5 6 7 8 9 t C。
[工学]浮阀精馏塔设计苯-甲苯混合液年产量65万吨
![[工学]浮阀精馏塔设计苯-甲苯混合液年产量65万吨](https://img.taocdn.com/s3/m/e4d8351e0b4c2e3f572763ea.png)
课程设计任务书一、设计题目:分离苯-甲苯混合液的浮阀精馏塔设计二、原始数据及操作条件1.生产能力:年处理苯-甲苯混合液6.5万吨(开工率300天/年)2. 原料:苯的含量44%(质量分数,下同)进料状况自选3. 分离要求:塔顶馏出液中苯含量不低于95%塔底釜液中含苯量不高于2%4. 操作压力:常压101.3 kPa操作塔顶表压4 kPa 单板压降不低于0.7 kPa5. 回流比:R=(1.1~2.0)Rmin6. 塔顶采取用全辽凝气泡点回流7. 塔釜采用间接饱和水蒸气加热三、设计内容1. 精馏流程的确定(附流程简图);2. 精馏塔的物料衡算、塔板数的确定、工艺条件及相关物性数据的计算;3. 精馏塔和塔板主要工艺尺寸的计算、塔板流体力学的校核并作出塔板负荷性能图。
四、设计要求1. 设计程序简练清楚,结果准确并汇总表;2. 计算公式、图表正确并注明来源,符号和单位要统一。
五、设计日期2010 年5月15日至2010年5月31日设计步骤1. 设计方案的确定及工艺流程的说明拟设计一台年处理苯-甲苯混合液6.5万吨(开工率300天/年)的浮阀精馏塔,要求塔顶馏出液中苯含量不低于95%,塔底釜液中含苯量不高于2%。
先设计苯-甲苯混合液经预热器加热后,用泵送入精馏塔;塔顶上升蒸汽采用冷凝器冷凝后部分回流,其余作为塔顶产品冷却后送至贮槽;塔釜采用间接蒸汽再沸器供热,塔底产品经冷却后送入贮槽。
工艺流程图见附图1。
操作压力为常压101.3 kPa ,采取泡点进料。
2. 全塔物料衡算2.1 进料、塔顶及塔底产品的摩尔分数48.00.44)/921(0.44/780.44/78X F =-+=09692/95.0(10.95/780.95/78X D =-+=)X W =92/)02.01(78/02.078/02.0-+0.02=2.2 平均摩尔质量M F = 780.52920.48⨯+⨯=85.28 kg/kmol2.3 物料衡算F 0=24300106.57⨯⨯= 9027.78 kg/h F = 85.289027.78=105.86 kmol/hD = FWD W F X -X X -X = 105.860.02-0960.02-0.48⨯ = 51.80 kmol/hW = F -D = 54.06 kmol/h3. 塔板数的确定 3.1 确定理论塔板数3.1.1由苯-甲苯气液平衡数据绘制x-y , t-x-y 图苯(A)-甲苯( B)饱和蒸汽压数据:由公式: y = 000BA B P P P P -- , y = x P P A 0 计算得苯-甲苯的t-x-y 数据如下:由上表数据绘制得x-y , t-x-y 图(见附图 2)用作图法求R min 并选取R本设计的进料状态选取的是泡点进料,即q=1,q 线方程为:0.48X X F == 作图得694.0=P yR min =DD X X --P Py y = 48.0694.0694.00.96-- = 1.29R = 1.6R min = 2.1由此可得精、提馏短的操作线方程分别为: y = 0.68x+ 0.31 y = 1.3x – 0.008 3.1.3 用图解法求理论板数N T求解过程见附图 2,总理论板数N T =13(包括塔釜)。
苯_甲苯浮阀式精馏塔的设计说明

化工原理课程设计任务书一 设计题目:苯-甲苯连续浮阀式精馏塔的设计 二 任务要求设计一连续浮阀式精馏塔以分离苯和甲苯, 具体工艺参数如下:原料加料量 F=75kmol/h 进料组成 xf=0.41 馏出液组成 965.0=D x 釜液组成 035.0=W x 塔顶压力 k P a P 325.101=单板压降 0.7kPa ≤ 进料状态 965.0=q2 工艺操作条件:常压精馏,塔顶全凝器,塔底间接加热,泡点回流。
三 主要设计内容1、设计方案的选择及流程说明2、工艺计算3、主要设备工艺尺寸设计 (1)塔径及塔板结构尺寸的确定 (2)塔板的流体力学校核 (3)塔板的负荷性能图 (4)总塔高4、辅助设备选型与计算设计结果汇总5、工艺流程图及精馏塔设备条件图目录任务书 (1)目录 (Ⅱ)摘要 (1)第1 章绪论 (2)1.1 设计流程 (2)1.2 设计思路 (2)第2 章精馏塔的工艺设计 (4)2.1 产品浓度的计算 (4)2.2 最小回流比的计算和适宜回流比的确定 (5)2.3 物料衡算 (6)2.4 精馏段和提馏段操作线方程 (7)2.5 逐板法确定理论板数及进料位置(编程) (7)2.6 全塔效率、实际板数及实际加料位置 (8)第3 章精馏塔主要工艺尺寸的设计计算 (8)3.1 物性数据计算 (8)3.2 精馏塔主要工艺尺寸的计算 (11)3.3 塔板主要工艺尺寸的计算 (13)3.4 塔板流体力学校核 (17)3.5 塔板符合性能图 (20)第4 章热量衡算 (24)4.1 热量衡算示意图 (24)4.2 热量衡算 (24)第5 章塔附属设备的计算 (29)5.1 筒体与封头 (29)5.2 除沫器 (29)5.3 裙座 (29)5.4 塔总体高度的设计 (30)5.5 换热器(进料预热器或产品冷却器)的设计计算 (30)5.6 进料管的设计 (32)5.7 泵的选型 (32)5.8 贮罐的计算 (33)第6 章结论 (35)6.1 结论 (35)6.2 主要数据结果总汇 (35)结束语 (36)参考文献 (31)附录1主要符号说明 (38)附录2 程序框图 (41)附录3 精馏塔工艺条件图 (43)附录4 生产工艺流程图 (44)教师评语.................................................................................................................... 错误!未定义书签。
分离苯—甲苯混合液的浮阀板式精馏塔工艺设计

分离苯—甲苯混合液的浮阀板式精馏塔工艺设计苯和甲苯是两种常用的有机溶剂,它们通常通过精馏过程进行分离。
浮阀板式精馏塔是一种常用的精馏设备,具有高效、节能、操作方便等特点。
下面就对分离苯和甲苯混合液的浮阀板式精馏塔工艺进行设计。
1.工艺流程:分离苯和甲苯混合液的浮阀板式精馏塔工艺流程一般包括进料、初留、尾留和回流等环节,具体流程如下:1)进料:将苯和甲苯混合液进料到精馏塔的顶部。
进料包括苯和甲苯的混合物以及一部分回流。
2)初留:通过多个塔板的精馏,将苯分离出来,初留液位以下的液体为初馏液,初留液通过凝气冷却器冷却后分为初留顶部产品和初留底部回流。
3)尾留:在塔底通过降温器冷却后,即可得到尾液,尾留底部产品通常作为顶部产品的回流,以保证塔托和稳定操作。
4)回流:回流是为了提高塔板的效率,减小焦失和能耗。
可通过将一部分的顶部产品送回到塔顶部作为回流。
2.浮阀板式精馏塔的设计参数:在进行浮阀板式精馏塔的工艺设计时,需要考虑以下参数:1)塔高:塔高应根据塔板的数量和塔板高度来确定,总体来说,塔高越高,分馏效果越好,但是设备成本和能耗也会增加。
2)塔板数:塔板数的确定需要考虑到初留和尾留的要求,一般根据初留质量分数和尾留质量分数进行迭代计算。
3)流量:进料流量、回流流量以及所需的产品流量都需要根据需求和经验来确定,可通过仪表和流量控制阀来调节。
4)进料温度:进料温度一般在常温下进行,如果需要提高分离效率,可以适当降低进料温度。
5)塔底温度:塔底温度是通过冷凝器来冷却的,根据具体情况来确定冷凝器的设计参数。
3.优化调整:在实际工艺操作中,可能需要对工艺参数进行优化调整,以达到更好的分离效果和降低能耗。
具体调整方法如下:1)调整回流比:根据实际需要,调整回流比可以提高塔板的效率。
2)改变操作压力:通过改变操作压力,可以改变馏出物的温度和塔板的效果,进而实现优化调整。
3)塔板节流孔调整:通过调整塔板节流孔的大小,可以影响流体的分布和液体在塔板上的停留时间,从而达到更好的分离效果。
- 1、下载文档前请自行甄别文档内容的完整性,平台不提供额外的编辑、内容补充、找答案等附加服务。
- 2、"仅部分预览"的文档,不可在线预览部分如存在完整性等问题,可反馈申请退款(可完整预览的文档不适用该条件!)。
- 3、如文档侵犯您的权益,请联系客服反馈,我们会尽快为您处理(人工客服工作时间:9:00-18:30)。
《化工原理》课程设计题目苯-甲苯精馏浮阀塔设计学院化学化工学院专业无机非金属材料班级 2012无机01姓名罗钢学号 20124620123指导教师杜可杰2015年 1月 20日目录绪论第一章、设计方案的确定1、设计方案2、设计要求第二章、工艺设计1、基础物性数据2、塔的工艺计算3、逐板计算法求理论板数计算4、精馏塔的工艺条件及有关物性数据的计算5、精馏塔的工艺尺寸的计算6、塔板负荷性能图7、辅助设备的选型第三章、讨论总结1、进料状况的影响2、回流比的选择3、精馏塔的操作和调节4、热量衡算和节能5、三废的处理结束语附录:参考文献附:精馏塔优化设计任务书一、设计题目苯-甲苯连续精馏浮阀塔设计二、工艺条件与原始数据1.体系可以看成理想溶液,φ=0.5, K=1;2.原料液组成:含苯0.42(质量分数,下同);3.生产能力:50000吨/年(按进料计),年生产时间300天;4.馏出液组成:苯95%;塔釜液要求:含苯3%。
三、设计条件1.常压操作,连续操作、泡点回流;2.进料状况:进料温度为20 -50℃;3.回流温度为塔顶蒸汽的露点;4.间接蒸汽加热,加热蒸汽压力 (绝压);5.冷却水进口温度为20℃,出口温度为40℃。
四、设计任务1.物料衡算,热量衡算;2.塔板数、塔径计算;3.溢流装置、塔盘设计;4.流体力学计算、负荷性能图。
五、设计成果1.设计说明书一份;2.设计图纸,包括塔板布置图,负荷性能图,塔设备的平面、立面图(要求手工绘图)。
绪论塔设备是炼油、化工、石油化工、制药等生产中广泛应用的气液传质设备。
根据塔气液接触部件的结构型式,可分为板式塔和填料塔。
板式塔设置一定数目的塔板,气体以鼓泡或喷射形式穿过板上液层进行质热传递。
在正常操作下,气相为分散相,液相为连续相,气液相组成呈阶梯变化,属逐级接触逆流操作过程。
填料塔装有一定高度的填料层,液体自塔顶沿填料表面下流,气体逆流向上(也有并流向下者)流动,气液相密切接触,进行质热传递。
在正常操作下,气相为连续相,液相为分散相,气液相组成沿塔高连续变化,属微分接触操作过程。
浮阀塔主要特点是在塔板的开孔上装有可浮动的浮阀,气流经阀片与塔板间的间隙而与板上横流的液体进行两相接触。
浮阀开度随气体负荷而变,可以自行调节;浮阀塔的主要优点是结构简单、制作方便、造价低、塔板开孔率大、生产能力大,由于阀片随气量变化自由升降,故操作弹性较大,气液接触时间较长,故塔板效率高;其缺点是处理易结焦、高粘度的物料时,阀片易与塔板黏结,在操作过程中有时会发生阀片脱落或卡死现象,使塔板效率和操作弹性下降。
本设计书对苯和甲苯的分离设备─浮阀精馏塔做了较详细的叙述,主要包括:工艺计算,辅助设备计算,塔设备等的附图。
采用浮阀精馏塔,塔高15.54米,塔径1.4米,按逐板计算理论板数为13。
塔顶使用全凝器,部分回流。
精馏段实际板数为25,提馏段实际板数为12。
实际加料位置在第11块板(从上往下数)。
通过板压降、漏液、液泛、雾沫夹带的流体力学验算,均在安全操作围。
塔的附属设备中,所有管线均采用无缝钢管。
再沸器采用卧式浮头式换热器。
用加热蒸汽压力 300 kPa加热,用15℃循水作冷凝剂。
饱和蒸汽走管程,釜液走壳程。
第一章设计方案的确定1、设计方案本设计任务为分离苯、甲苯混合物。
对于二元混合物的分离,采用连续精馏流程。
设计中采用泡点进料,将原料液通过预热器加热至泡点后送入精馏塔。
塔顶上升蒸气采用全凝器冷凝,冷凝液在泡点下一部分回流至塔,其余部分经产品冷凝器冷却后送至储罐。
该物系属易分离物系,最小回流比较小,故操作回流比取最小回流比的2倍。
塔釜采用间接蒸汽加热,塔底产品经冷却后送至储罐。
2、设计要求1、生产能力较大,分离效率较高。
2、流体的通量大,单位设备体积的处理量大。
3、流体流动阻力小;气体通过塔构件的压降低、能耗低。
4、有一定的操作弹性;在气液负荷较大的变动围,能够维持传质速率基本不变。
5、对物料的适应性强,适于分离组成复杂的物料。
6、性能稳定,稳定运行时间长;结构简单,造价低,易于安装、检修和清洗。
第二章工艺设计1、基础物性数据2、塔的工艺计算(一)原料规格及分离要求1、年产5万吨即GF=50000000Kg/(300*24)hr=6944Kg/h;2、泡点进料,q=13、塔顶苯含量不低于95%,塔底苯含量不高于3%(以上均为质量分率)。
(二)生产条件1.常压操作,连续操作、泡点回流;2.进料状况:进料温度为20~50℃;3.回流温度为塔顶蒸汽的露点;4.间接蒸汽加热,加热蒸汽压力 (绝压);5.冷却水进口温度为20℃,出口温度为40℃。
(三)精馏塔物料衡算1.原料液及塔顶、塔底产品的摩尔分率苯的摩尔质量MA=78.11Kg/Kmol甲苯的摩尔质量MB=92.13Kg/KmolX=(0.42/78.11)/[(0.42/78.11)+(0.58/92.13)]=0.460 FX=(0.95/78.11)/[(0.95/78.11)+(0.05/92.13)]=0.957 DX=(0.03/78.11)/[(0.03/78.11)+(0.97/92.13)]=0.W2.原料液及塔顶、塔底产品的平均摩尔质量M=0.460* 78.11+(1-0.46)*92.13=85.68kg/kmol FM=0.957* 78.11+(1-0.957)*92.13=78.71kg/kmol DM=0.* 78.11+(1-0.)*92.13=91.64kg/kmolW3.物料衡算原料处理量 F=6944/85.68=81.04kmol/h总物料衡算 81.04=D+W苯物料衡算 81.04* 0.460=0.975D+0.035W联立解得 D=44.01kmol/h W=37.03kmol/h三塔板数的确定1.理论板层数N的求取T苯-甲苯属理论物系,可采用图解法求理论板层数。
①由手册查得苯-甲苯物系的气液平衡数据,绘出x-y图2)求最小回流比及操作回流比。
采用作图法求最小回流比。
在(图1)中对角线上,自点e(0.45,0.45)作垂线ef即为进料线(q线),该线与平衡线的交点坐标为 y=0.678 x=0.460故最小回流比为 1.28取操作回流比为最小回流比的2倍 R= 2 Rmin=2 *1.28=2.563)求精馏塔的气、液相负荷L=RD=2.68* 44.01=117.94kmol/hV=(R+1)D=(2.68+1)44.01=161.96kmol/hL’=L+F==.98kmol/hV’=V=161.96kmol/h故精馏段操作线方程式为∶提馏段操作线方程为5)图解法求理论板层数采用图解法求理论板层数,求解结果为; 总理论板层数 NT=13(包括再沸器) 进料板位置 NF=6 2.实际板层数的求取精馏段实际板层数 N1 =5/0.52=9.6 =10 提馏段实际板层数 N2=7.5/0.52=14.42 =154、精馏塔的工艺条件及有关物性数据的计算 (1)操作压力的计算塔顶的操作压力每层塔板的压降 KPa P 7.0=∆进料板压力精馏段平均压力塔底压力提馏段(2)温度,根据操作压力通过试差计算 P= ,塔顶 ℃, ℃,℃kpap w 7.1207.0223.105=⨯+=KPa P D 3.10543.101=+=KPaP m 8.1082/)3.1123.105(=+=KPa P F 3.112107.03.105=⨯+=)(5.1162kpa p p p Dw m =+=m t B B A A x p x p θθ+74.82=D t 21.93=F t 54.110=w t∴精馏段温度, 提馏段温度 (3)平均摩尔质量 塔顶949.01==y x D 883.01=xD V M . =0.949×78.11+(1-0.949) ×92.13=78.83(kg/kmol) D L M .=0.883×78.11+(1-0.883) ×92.13=79.95(kg/kmol) 进料板:F V M .=0.5991×78.11+(1-0.5991) ×92.13=83.73(kg/kmol) F L M .=0.3770×78.11+(1-0.3770) ×92.13=86.85(kg/kmol)塔 底:01846.0=w x 4439.0=w yw V M .=0.4439×78.11+(1-0.4439) ×92.13=85.90(kg/kmol) w L M .=0.01846×78.11+(1-0.01846) ×92.13=91.86(kg/kmol) 精.L M =25.7795.886+=83.3(kg/kmol)精.L M =23.783.985+=81.28(kg/kmol)提.L M =26.8915.886+=83.3(kg/kmol)提.v M =273.839.85+=84.82(kg/kmol)(4)平均密度计算 ① 气相平均密度计算由理想气体状态方程式计算,即② 液相平均密度计算M5991.0=F y 3770.0=F x 3./95.2)2738.987(314.88.281.8108m Kg RT M p mv m V =+⨯⨯==精。
精ρ3/7.13)273.8101(314.82.8845.116m Kg RT M p mV m V =+⨯⨯==。
提。
提ρ98.872=+F D tt t 精75.81012=+W F tt t 提液相平均密度计算依下式计算,即: 塔顶液相平均密度的计算由,查液体在不同温度下的密度表得: 3/.9811m Kg A =ρ 3/.3807m Kg B =ρ .380706.0.981194.01+=LDmρ 3/.2810m Kg LDm =ρ 进料板液相平均密度的计算由,查液体在不同温度下的密度表得 3/.1800m Kg A =ρ 3/797m Kg B =ρ339.013.92)377.01(11.78377.011.78377.0=⨯-+⨯⨯=A a79739.30-1.1800339.01+=LFmρ 3/.4800m Kg LDm =ρ 精馏段的平均密度为3/3.8052/).4800.2810(m Kg Lm =+=ρ塔底液相平均密度的计算由C tw ︒=54.110,查液体在不同温度下的密度表得3/779.5m Kg A =ρ 3/6.779m Kg B =ρ015.013.92)01846.01(11.7801846.011.7801846.0=⨯-+⨯⨯=A a779.60157.01779.50157.01-+=Lwmρ 3/779.7m Kg Lwm =ρ提馏段的平均密度3/1.7902/).4800779.7(m Kg Lm =+=ρ(5)液体平均表面力的计算LBBLAALma a ρρρ+=1C tD ︒=4.782C t F ︒=21.93n液相平均表面力依下式计算,即 塔顶液相平均表面力的计算由,查液体表面力共线图得 m mN A /9.820=σ m mN B /39.21=σ m mN LDm /43.2039.21)949.01(89.20949.0=⨯-+⨯=σ进料板液相平均表面力的计算由,查液体表面力共线图得: m mN A /44.19=σ m mN B /4.220=σ m mN LFm /4.9194.220)377.01(44.19377.0=⨯-+⨯=σ塔底液相平均表面力的计算由,查液体表面力共线图得: m mN A /4.417=σ m mN B /6.318=σm mN LDm /4.3186.318)01846.01(4.41701846.0=⨯-+⨯=σ精馏段平均表面力m mN Lm /43.202/)4.9191.920(=+=σ提馏段平均表面力m mN Lm /4.1192/)4.31894,19(=+=σ(6)液体平均黏度计算 液相平均黏度依下式计算,即∑=ii Lm x μμlg lg塔顶液相平均黏度的计算由,查气体黏度共线图得: C t D ︒=4.782C t F ︒=21.93C t D ︒=4.5110C t D ︒=74.82s mPa A ⋅=301.0μ s mPa B ⋅=305.0μs mpa LDm •=⨯+⨯=302.0305.0051.0301.0949.0lg μ精馏段液相平均黏度的计算:由,查气体黏度共线图得: s Pa A ⋅=273.0μ s mPa B ⋅=280.0μ s mpa LFm •=⨯+⨯=277.0280.0623.0273.0377.0μ精馏段液相平均黏度s mPa Lm ⋅=+=29.02/)277.0302.0(μ精馏段液相平均黏度的计算由,查气体黏度共线图得: s Pa A ⋅=234.0μ s mPa B ⋅=245.0μ s mpa LFm •=⨯+⨯=244.0245.098154.0234.001846.0μ提馏段液相平均黏度s mPa Lm ⋅=+=261.02/)277.0244.0(μ5、精馏塔工艺尺寸的计算(1)塔径的计算 精馏段气液相体积流率)/(49.14855.45)126.2()1(h kmol D R V =⨯+=+=精馏段的气、液相体积流率s m VM V Vm Vm S /14.195.2360049.14828.8136003=⨯⨯==ρ )/(94.10255.4526.2h kmol RD L =⨯==C t F ︒=21.93C t w ︒=54.110s m LM L Lm Lm S /0030.03.80536003.8394.10236003=⨯⨯==ρ提馏段的气、液相体积流率)/(49.148'h kmol V V ==s m VM V Vm Vm S /10.117.3360049.14882.8436003=⨯⨯==ρ )/(76.20584.10294.102,h kmol F L L =+=+=(2)塔板工艺尺寸计算塔径 空塔气速max ()u u =⨯安全系数max u =精馏段max u =取板间距H T =0.45m,取上板液层高度h L =0.07m ,则图中参数值为;m h H L T 38.007.045.0=-=-由V V L C u ρρρ-⋅=max ,式中C 由2.020)20(L C C σ=求取,其中20C 由筛板塔汽液负荷因子曲线图查取,图横坐标为根据以上数据,由史密斯关联图查得 08.020=C因物系表面力为m mN /43.20=σ时的C:0803.0)2043.20(072.0)20(08.02.02.0=⨯=⋅=LC σ sm LM L Lm Lm s /0060.01.790360036.8996.20536003,=⨯⨯==ρ0435.0)95.23.805()360014.13600003.0()(2121=⨯⨯⨯=⋅V L h h V L ρρs m C u V V L /32.195.295.23.8050803.0max =-⨯=-⋅=ρρρ 取安全系数为0.7,则空塔气速s m u u /924.032.17.07.0max =⨯=⋅=m u V D S 25.1924.014.314.144=⨯⨯==π 按标准塔径圆整 m D 4.1=塔截面积为 22254.14.1785.0785.0m D A T =⨯==s m A v u T S /74.054.114.1===精馏段取板间距H T =0.45m,取上板液层高度h L =0.07m ,则图中参数值m h H L T 38.007.045.0=-=-由V V L C u ρρρ-⋅=max ,式中C 由2.020)20(L C C σ=求取,其中20C 由筛板塔汽液负荷因子曲线图查取,图横坐标为086.0)17.31.790()36001.13600006.0()(2121=⨯⨯⨯=⋅V L h h V L ρρ 根据以上数据,由史密斯关联图查得 076.020=C因物系表面力为m mN /14.19=σ时的C:075.0)2014.19(076.0)20(076.02.02.0=⨯=⋅=LC σ s m C u V V L /18.117.317.31.790075.0max =-⨯=-⋅=ρρρ 取安全系数为0.7,则空塔气速7s m u u /83.018.17.07.0max =⨯=⋅=m u V D S 30.183.014.31.144=⨯⨯==π 按标准塔径圆整 m D 4.1=。