第二章热处理原理1
热处理基本原理
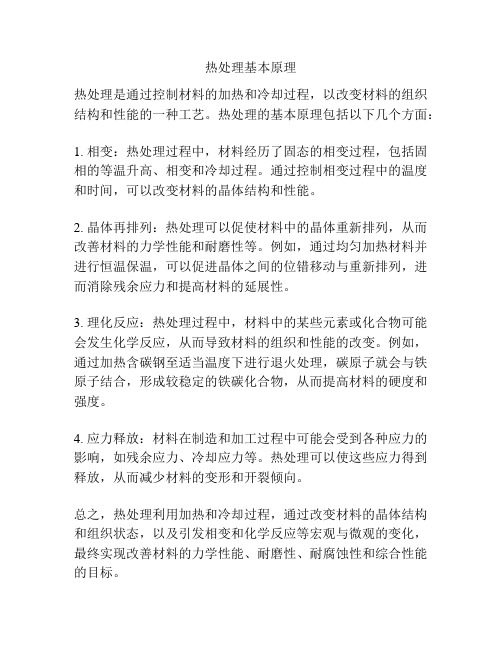
热处理基本原理
热处理是通过控制材料的加热和冷却过程,以改变材料的组织结构和性能的一种工艺。
热处理的基本原理包括以下几个方面:
1. 相变:热处理过程中,材料经历了固态的相变过程,包括固相的等温升高、相变和冷却过程。
通过控制相变过程中的温度和时间,可以改变材料的晶体结构和性能。
2. 晶体再排列:热处理可以促使材料中的晶体重新排列,从而改善材料的力学性能和耐磨性等。
例如,通过均匀加热材料并进行恒温保温,可以促进晶体之间的位错移动与重新排列,进而消除残余应力和提高材料的延展性。
3. 理化反应:热处理过程中,材料中的某些元素或化合物可能会发生化学反应,从而导致材料的组织和性能的改变。
例如,通过加热含碳钢至适当温度下进行退火处理,碳原子就会与铁原子结合,形成较稳定的铁碳化合物,从而提高材料的硬度和强度。
4. 应力释放:材料在制造和加工过程中可能会受到各种应力的影响,如残余应力、冷却应力等。
热处理可以使这些应力得到释放,从而减少材料的变形和开裂倾向。
总之,热处理利用加热和冷却过程,通过改变材料的晶体结构和组织状态,以及引发相变和化学反应等宏观与微观的变化,最终实现改善材料的力学性能、耐磨性、耐腐蚀性和综合性能的目标。
热处理炉内的传热讲解
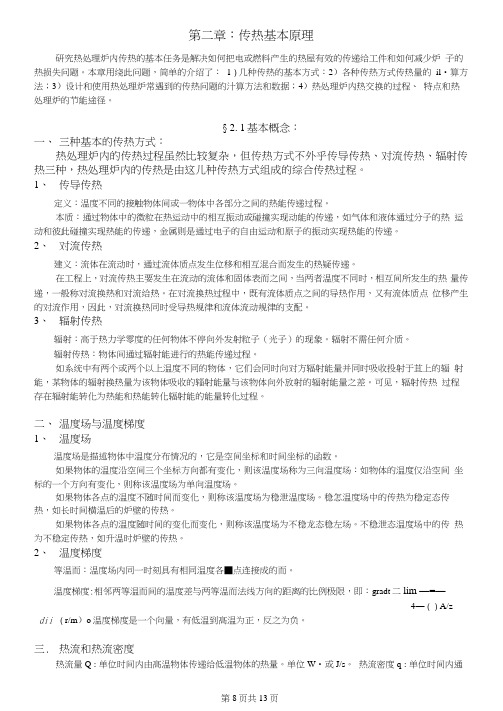
第二章:传热基本原理研究热处理炉内传热的基本任务是解决如何把电或燃料产生的热屋有效的传递给工件和如何减少炉子的热损失问题。
本章用绕此问题,简单的介绍了:1)几种传热的基本方式:2)各种传热方式传热量的il•算方法;3)设计和使用热处理炉常遇到的传热问题的汁算方法和数据;4)热处理炉内热交换的过程、特点和热处理炉的节能途径。
§ 2. 1基本概念:一、三种基本的传热方式:热处理炉内的传热过程虽然比较复杂,但传热方式不外乎传导传热、对流传热、辐射传热三种,热处理炉内的传热是由这儿种传热方式组成的综合传热过程。
1、传导传热定义:温度不同的接触物体间或一物体中各部分之间的热能传递过程。
本质:通过物体中的微粒在热运动中的相互振动或碰撞实现动能的传递,如气体和液体通过分子的热运动和彼此碰撞实现热能的传递,金属则是通过电子的自由运动和原子的振动实现热能的传递。
2、对流传热建义:流体在流动时,通过流体质点发生位移和相互混合而发生的热疑传递。
在工程上,对流传热主要发生在流动的流体和固体表而之间,当两者温度不同时,相互间所发生的热量传递,一般称对流换热和对流给热。
在对流换热过程中,既有流体质点之间的导热作用,又有流体质点位移产生的对流作用,因此,对流换热同时受导热规律和流体流动规律的支配。
3、辐射传热辐射:高于热力学零度的任何物体不停向外发射粒子(光子)的现象。
辐射不需任何介质。
辐射传热:物体间通过辐射能进行的热能传递过程。
如系统中有两个或两个以上温度不同的物体,它们会同时向对方辐射能量并同时吸收投射于苴上的辐射能,某物体的辐射换热量为该物体吸收的辎射能量与该物体向外放射的辐射能量之差。
可见,辐射传热过程存在辐射能转化为热能和热能转化辐射能的能量转化过程。
二、温度场与温度梯度1、温度场温度场是描述物体中温度分布情况的,它是空间坐标和时间坐标的函数。
如果物体的温度沿空间三个坐标方向都有变化,则该温度场称为三向温度场:如物体的温度仅沿空间坐标的一个方向有变化,则称该温度场为单向温度场。
热处理原理
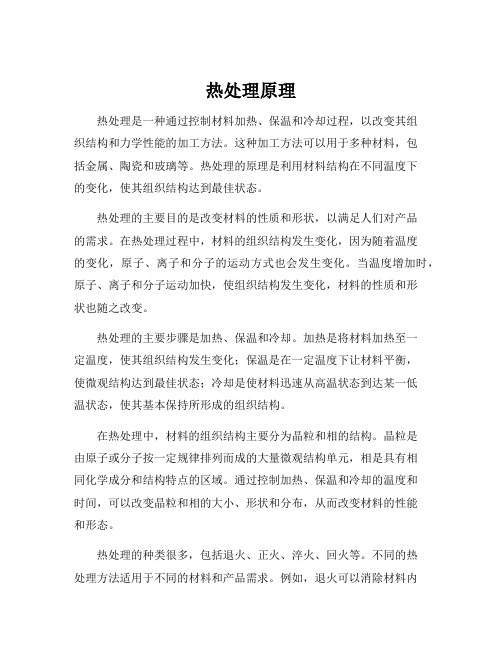
热处理原理热处理是一种通过控制材料加热、保温和冷却过程,以改变其组织结构和力学性能的加工方法。
这种加工方法可以用于多种材料,包括金属、陶瓷和玻璃等。
热处理的原理是利用材料结构在不同温度下的变化,使其组织结构达到最佳状态。
热处理的主要目的是改变材料的性质和形状,以满足人们对产品的需求。
在热处理过程中,材料的组织结构发生变化,因为随着温度的变化,原子、离子和分子的运动方式也会发生变化。
当温度增加时,原子、离子和分子运动加快,使组织结构发生变化,材料的性质和形状也随之改变。
热处理的主要步骤是加热、保温和冷却。
加热是将材料加热至一定温度,使其组织结构发生变化;保温是在一定温度下让材料平衡,使微观结构达到最佳状态;冷却是使材料迅速从高温状态到达某一低温状态,使其基本保持所形成的组织结构。
在热处理中,材料的组织结构主要分为晶粒和相的结构。
晶粒是由原子或分子按一定规律排列而成的大量微观结构单元,相是具有相同化学成分和结构特点的区域。
通过控制加热、保温和冷却的温度和时间,可以改变晶粒和相的大小、形状和分布,从而改变材料的性能和形态。
热处理的种类很多,包括退火、正火、淬火、回火等。
不同的热处理方法适用于不同的材料和产品需求。
例如,退火可以消除材料内部应力和缺陷,降低硬度和延展性;淬火可以使材料快速冷却并增加硬度和强度;回火可以降低材料脆性并保证材料的强度和韧性。
总的来说,热处理是一种非常重要的材料加工方法,可以改变材料的结构和性能,从而满足各种产品的需求。
此外,不同的热处理方法适用于不同的材料和产品需求,因此选择合适的热处理方法也是非常重要的。
热处理基本知识及工艺原理
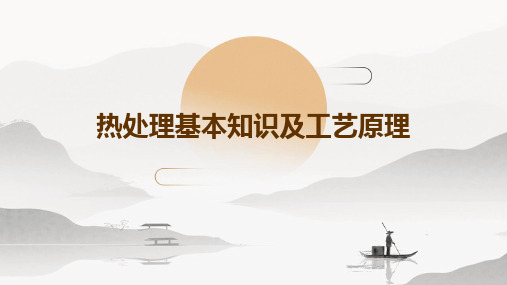
将淬火后的金属材料加热到适当温度,保温一定时间后冷 却至室温。回火可以消除淬火产生的内应力,提高金属材 料的韧性和塑性。
02
热处理工艺原理
加热与冷却
加热
热处理过程中,将金属材料加热至所 需温度,以实现所需的相变和组织转 变。加热方式包括电热、燃气热、微 波加热等。
冷却
热处理过程中,金属材料在加热后需 进行冷却,以控制相变和组织转变的 过程。根据冷却速度的不同,可分为 缓慢冷却和快速冷却。
感谢您的观看
THANKS
热处理的分类
1. 退火
将金属材料加热到适当温度,保温一定时间后缓慢冷却至 室温。退火可以提高金属材料的塑性和韧性,消除内应力 。
3. 淬火
将金属材料加热到适当温度,保温一定时间后快速冷却至 室温。淬火可以提高金属材料的硬度和耐磨性,但可能导 致内应力增大。
2. 正火
将金属材料加热到适当温度,保温一定时间后在空气中自 然冷却。正火可以提高金属材料的强度和韧性,细化组织 结构。
离子注入技术
将具有特定能量的离子注 入材料表面,改变其物理 和化学性质,提高耐磨、 耐腐蚀等性能。
提高热处理效率与节能减排
高效加热方式
采用电磁感应、微波加热 等高效加热方式,缩短加 热时间,提高热处理效率。
余热回收利用
对热处理过程中的余热进 行回收和再利用,减少能 源浪费,降低碳排放。
环保材料与工艺
热处理基本知识及工艺艺原理 • 常见热处理工艺 • 热处理的应用 • 热处理的发展趋势与挑战
01
热处理基本概念
热处理的定义
热处理:通过加热、保温和冷却等工 艺手段,改变金属材料的内部组织结 构,以达到改善其性能、满足使用要 求的一种工艺方法。
热处理工艺的原理和应用
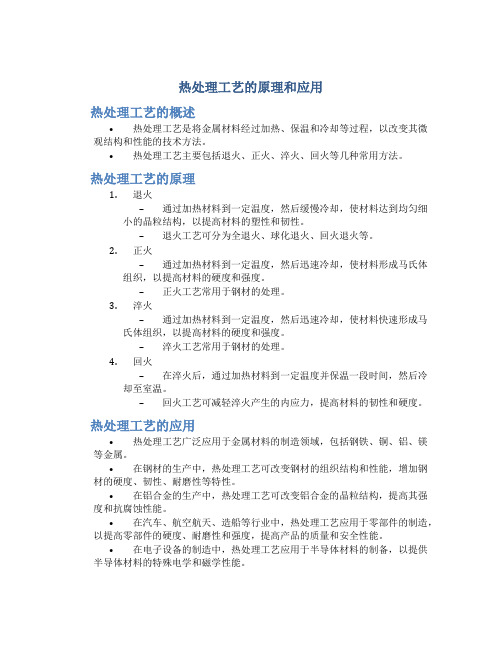
热处理工艺的原理和应用热处理工艺的概述•热处理工艺是将金属材料经过加热、保温和冷却等过程,以改变其微观结构和性能的技术方法。
•热处理工艺主要包括退火、正火、淬火、回火等几种常用方法。
热处理工艺的原理1.退火–通过加热材料到一定温度,然后缓慢冷却,使材料达到均匀细小的晶粒结构,以提高材料的塑性和韧性。
–退火工艺可分为全退火、球化退火、回火退火等。
2.正火–通过加热材料到一定温度,然后迅速冷却,使材料形成马氏体组织,以提高材料的硬度和强度。
–正火工艺常用于钢材的处理。
3.淬火–通过加热材料到一定温度,然后迅速冷却,使材料快速形成马氏体组织,以提高材料的硬度和强度。
–淬火工艺常用于钢材的处理。
4.回火–在淬火后,通过加热材料到一定温度并保温一段时间,然后冷却至室温。
–回火工艺可减轻淬火产生的内应力,提高材料的韧性和硬度。
热处理工艺的应用•热处理工艺广泛应用于金属材料的制造领域,包括钢铁、铜、铝、镁等金属。
•在钢材的生产中,热处理工艺可改变钢材的组织结构和性能,增加钢材的硬度、韧性、耐磨性等特性。
•在铝合金的生产中,热处理工艺可改变铝合金的晶粒结构,提高其强度和抗腐蚀性能。
•在汽车、航空航天、造船等行业中,热处理工艺应用于零部件的制造,以提高零部件的硬度、耐磨性和强度,提高产品的质量和安全性能。
•在电子设备的制造中,热处理工艺应用于半导体材料的制备,以提供半导体材料的特殊电学和磁学性能。
热处理工艺的优点•可改善金属材料的物理性能,提高材料的硬度、韧性、强度等。
•可改变材料的晶粒结构和组织,提供特定的材料性能。
•可改善材料的表面质量,提高耐磨性和耐腐蚀性。
•可通过控制热处理工艺参数,实现材料性能的调控和优化。
热处理工艺的注意事项•热处理工艺的参数,包括加热温度、保温时间、冷却速度等,需要根据材料的类型和要求进行合理选择,以避免材料的过热或过冷现象。
•热处理工艺需要严格控制各个环节的温度和时间,以保证工艺的有效性和一致性。
热处理培训资料
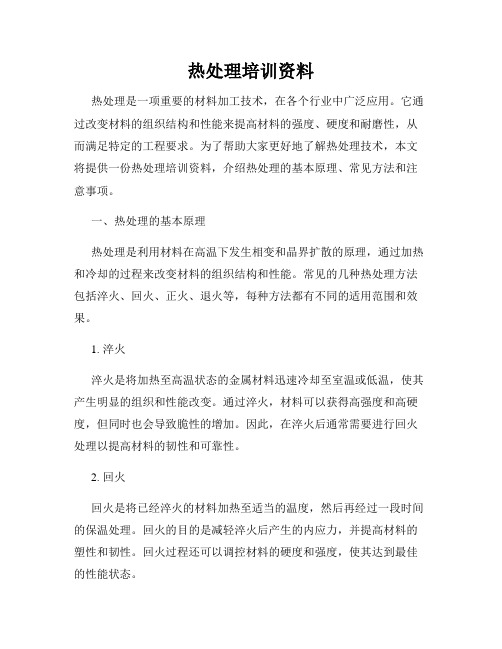
热处理培训资料热处理是一项重要的材料加工技术,在各个行业中广泛应用。
它通过改变材料的组织结构和性能来提高材料的强度、硬度和耐磨性,从而满足特定的工程要求。
为了帮助大家更好地了解热处理技术,本文将提供一份热处理培训资料,介绍热处理的基本原理、常见方法和注意事项。
一、热处理的基本原理热处理是利用材料在高温下发生相变和晶界扩散的原理,通过加热和冷却的过程来改变材料的组织结构和性能。
常见的几种热处理方法包括淬火、回火、正火、退火等,每种方法都有不同的适用范围和效果。
1. 淬火淬火是将加热至高温状态的金属材料迅速冷却至室温或低温,使其产生明显的组织和性能改变。
通过淬火,材料可以获得高强度和高硬度,但同时也会导致脆性的增加。
因此,在淬火后通常需要进行回火处理以提高材料的韧性和可靠性。
2. 回火回火是将已经淬火的材料加热至适当的温度,然后再经过一段时间的保温处理。
回火的目的是减轻淬火后产生的内应力,并提高材料的塑性和韧性。
回火过程还可以调控材料的硬度和强度,使其达到最佳的性能状态。
3. 正火正火是将材料加热至适当的温度,保温一定时间后进行冷却。
正火的目的是通过控制组织形态和材料的相变来调整材料的性能,以满足特定的工程要求。
正火适用于一些对硬度、强度和韧性要求均有的工件。
4. 退火退火是将已经加工或者变形的材料加热至一定温度,然后经过一定时间的保温处理,最后缓慢冷却。
退火的目的是通过晶界扩散来恢复材料的塑性和韧性,减少材料的内应力和变形。
退火可以改善材料的加工性能,提高材料的韧性和可塑性。
二、热处理的常见方法热处理有许多不同的方法和工艺,下面介绍几种常见的热处理方法:1. 淬火和回火工艺淬火和回火是最常用的热处理方法之一。
淬火可以通过控制冷却速度和介质的选择来改变材料的结构和性能,而回火则可以通过加热和保温的方式来调节材料的硬度和韧性。
2. 预淬火和再回火工艺预淬火和再回火是为了进一步改善材料的组织和性能而进行的热处理工艺。
热处理基本知识及工艺原理

热处理基本知识及工艺原理1. 热处理的基础热处理听起来很高大上,其实说白了就是给金属“洗澡”,不过这澡可不是一般的洗澡,它是通过加热和冷却,让金属变得更结实、更耐用。
就像人要适当运动一样,金属也需要“锻炼”才能有更好的表现。
大家常常听到的“热处理”这两个字,实际上是金属加工中的一个重要环节,尤其是在制造一些需要承受高强度和高温的零件时,它的重要性就显得尤为突出。
1.1 热处理的类型热处理可分为几种主要的类型,比如淬火、回火、退火、正火等等。
这些名字听起来有点像高深的武功秘籍,但其实它们各有各的妙处。
淬火就像是给金属来个猛击,迅速让它从热状态转为冷状态,达到硬化的效果;而回火则是帮金属放松一下,避免太过刚强造成的脆弱。
退火则是金属的“慢养”,通过长时间的加热和缓慢冷却,让金属的内部结构得到调整。
正火呢,就像是在金属身上做个深层按摩,让它恢复到最佳状态。
1.2 热处理的原理那热处理的原理又是什么呢?其实也不复杂。
热处理过程中,金属的内部原子结构会发生变化,就像是大海中的波涛汹涌,时而平静,时而激烈。
加热的时候,原子就像聚会的朋友,欢快地跳动;冷却时,它们就得迅速找到自己的位置,有时候甚至会出现“打架”的情况,这就影响了金属的强度和韧性。
2. 热处理的工艺2.1 工艺步骤热处理的工艺流程一般包括加热、保温和冷却三个步骤。
先是加热,像开车一样,把温度开到理想值,这个过程要慢慢来,别着急;接着就是保温,保持一段时间,让金属的“细胞”好好“吸收养分”;最后是冷却,冷却的方法可以是水、油,甚至空气,各种各样的方式让金属在不同的环境中“转身”。
这整个流程下来,金属的性能就提升了好几个档次。
2.2 影响因素当然,热处理的效果也受很多因素影响,比如温度、时间、冷却速度等。
就好比炒菜,如果温度掌握不好,时间控制不当,最终的味道可就大相径庭了。
为了得到理想的效果,工艺参数的选择可得仔细斟酌。
3. 热处理的应用热处理在我们生活中无处不在,特别是在汽车、航空、机械等行业,都是大显身手的地方。
热处理原理PPT课件

.
6
第一节 钢在加热时的转变
加热是热处理的第一道工序,分两种:
➢ 一种是在A1以下加热,不发生相变 ➢ 另一种是在临界点以上加热,目的是获得均匀
的奥氏体组织,称奥氏体化
钢坯加热
.
7
一、奥氏体的形成过程(以共析钢为例)
奥氏体晶核形成:首先在与Fe3C相界形核 奥氏体晶核长大:奥氏体晶核通过碳原子的扩散向
=1012/cm2,又称位错马
氏体
.
38
(2)针状马氏体
立体形态为双凸透镜形的片 状,显微组织为针状
在电镜下,亚结构主要是孪
晶,又称孪晶马氏体
电镜下
光镜下 电镜下
.
39
(3)马氏体的形态
——主要取决于含碳量。 C%小于0.2%时,组织
几乎全部是板条马氏体 C%大于1.0%C时几乎
全部是针状马氏体 C%在0.2~1.0%之间为
一、过冷奥氏体的转变产物及转变过程
处于临界点A1以下的奥氏体称过冷奥氏体,过 冷奥氏体是非稳定组织,迟早要发生转变
随过冷度不同,过冷奥氏体将发生珠光体转变、 贝氏体转变和马氏体转变三种类型转变
——现以共析钢为例说明。
.
20
(一)珠光体转变
1. 珠光体的组织形态及性能
过冷奥氏体在A1到550℃间将转变为珠光体类型组织, 它是铁素体与渗碳体片层相间的机械混合物
通常将钢加热到940 10℃奥氏体化后,设法 把奥氏体晶粒保留到室
温来判断,晶粒度为1~4级的是本质粗晶粒钢, 5~8级的是本质细晶粒钢
前者晶粒长大倾向大,后者晶粒长大倾向小
.
13Hale Waihona Puke 2. 影响奥氏体晶粒长大的因素
- 1、下载文档前请自行甄别文档内容的完整性,平台不提供额外的编辑、内容补充、找答案等附加服务。
- 2、"仅部分预览"的文档,不可在线预览部分如存在完整性等问题,可反馈申请退款(可完整预览的文档不适用该条件!)。
- 3、如文档侵犯您的权益,请联系客服反馈,我们会尽快为您处理(人工客服工作时间:9:00-18:30)。
注意: •孕育期:孕育期的长短表示过冷奥氏体的稳定 性的高低; •由C曲线可知,共析钢在550℃左右孕育期最短, 表示过冷奥氏体最不稳定,此处叫做C曲线的 “鼻子”;“鼻子”所对应的温度叫做“鼻 温”; •从A1到“鼻温”之间,随着过冷度的增大,孕 育期缩短,过冷奥氏体的稳定性下降; •从“鼻温”到Ms线之间,随着过冷度的增大, 孕育期增长,过冷奥氏体的稳定性增大;
4、实际晶粒度:
在具体的热处理工艺下获得的奥氏体晶粒
的大小称为实际晶粒度。
比起始晶粒度大。与具体的热处理工艺有
关,即加热温度和保温时间。 奥氏体的实际晶粒度决定钢材冷却后的组 织和性能。
23
5、奥氏体晶粒大小影响因素 (1)、加热温度和保温时间的影响 加热温度越高,保温时间越长,奥氏体晶粒 就越粗大;控制加热温度和保温时间来控制晶粒 度。加热温度的作用比较大。
t
隔一定时间取一个样淬入盐水。
使未转变的A转变为M。出现白色组织(马氏 体)、黑色组织。从而确定各个等温温度下转 变开始时间和终了时间;这样就获得共析钢的 恒温转变动力学曲线,再将其转变为TTT图, 又叫“C”曲线,如图9-14所示;
2、曲线分析 ①由图中可以看出: 孕育期: 转变开始后转变速度逐渐 加快,当A转变体积分数达 到50%时转变速度最大。 ②TTT图中的线: A1线:奥氏体和珠光体的 平衡温度; Ms线:奥氏体向马氏体转 变的开始线; Mf线:奥氏体向马氏体转 变的终了线; 转变开始线,转变终了线;
②合金元素改变钢的临界点和碳在奥氏体中的 溶解度,于是改变钢的过热度和碳在奥氏体中 的扩散速度。
③钢中合金元素在铁素体和碳化物中的溶解度 是不均匀的,奥氏体形成后,合金元素分布极 不均匀,在A中的扩散速度很小,均匀化时间 长。
合金钢的奥氏体化,加热温度要高,保温 时间要长。
三、奥氏体晶粒大小及其影响因素 (一)、奥氏体晶粒度的概念:
②过共析钢的过冷A等温转变曲线:
如图所示 曲线的鼻尖上部区域比共析钢多了一 条先共析渗碳体的析出线;这表示此 类钢在奥氏体转变之前先有渗碳体的 析出; 在过共析钢中,随着含碳量的增加, 奥氏体的稳定性降低,孕育期缩短, 转变速度增加,C曲线左移。
2、合金元素的影响 ①溶入A中的:除Al和Co外,所有的其它合金 元素当溶入奥氏体中后,都增大奥氏体的稳定性, 使C-曲线右移。 作用大小:Mo、W、Mn、Ni、Si、Al、B 改变C-曲线位置,不改变形状:Ni、Si、Cu及 Mn; 改变C-曲线位置,改变形状:Cr、MO、W、V、 Ti;如图9-18所示; ② 碳化物形成元素V、Ti、Nb、Zr等形成稳定 的碳化物时,不溶入A:减低过冷奥氏体的稳定性, 使C-曲线左移。
1.3 速度与时间: 钢从奥氏体状态以不同的冷却速度冷却 时,将形成不同的转变产物,获得不同的 组织和性能。
慢冷:珠光体( Fe、C均扩散); A冷却 较快冷:贝氏体 ( Fe不扩散,C扩散); 快冷:马氏体( Fe、C均不扩散);
三、固态相变的特点:
驱动力:新旧两相的自由能差; 过程:形核、核长大;
过冷奥氏体的转变类型:
高温、 缓冷(铁、碳均扩散)—炉冷 或空冷—退火或正火—珠光体转变。(扩 散型)
中温、冷速较快(铁不扩散、碳扩散)—
贝氏体。(过渡型)
低温、冷速较快到Ms以下转变(铁、碳均
不扩散)—马氏体。(非扩散型)
过冷奥氏体在连续冷却时,转变是在一个
温度范围内,组织为混合组织。
等温转变---转变过程---产物---组织—性能。
粗珠光体与细珠光体相比;
球状珠光体与片状珠光体相比;
平衡组织和非平衡组织。
§2—3 钢在冷 却时的转变
一、概述 实际生产中,奥氏体 只有通过冷却得到室温 组织才能获得一定的使 用性能。 钢的冷却有两种方式, 一种是等温冷却,一种 是连续冷却,见图9- 13所示。
过冷奥氏体:
在临界点以下存在的,不稳定的,处于 过冷态,将要发生转变的奥氏体称为过冷 奥氏体。
一般强碳化物形成元素易与碳形成强碳化物, 阻碍奥氏体晶粒的长大。
Al—AlN,900℃以上溶入奥氏体,促进。
Ti、 Zr 、 V 、Nb—弥散碳化物和氮化物。 Mn、P、C、N—溶入奥氏体后加速铁原子的扩 散,促进奥氏体晶粒的长大。
(4)、钢的原始组织的影响:
钢的原始组织越细,碳化物的弥散度 越大,则奥氏体的起始晶粒度就越细小。 例如:
11
(二)、奥氏体晶核的长大
A形成后,向铁素体和渗碳体两 方向长大,同时又有新的A晶核形成, 并长大,直到A晶粒彼此相遇,P消失;
(三)、残余渗碳体的溶解 渗碳体在保温的过程中,随着碳的扩散,渗 碳体要不断的向奥氏体中溶解。 (四)、奥氏体成分的均匀化 刚刚形成的奥氏体成分是不均匀的,含碳量 有高有低,经过长时间的扩散,使碳原子进行充 分的扩散奥氏体成分均匀化。
N n0 1.01 G
1 2
的晶粒长大在热力学上是一种自发趋势。
20
3、本质晶粒度: 一定条件下奥氏体晶粒长大的倾向。(规定 条件下,A晶粒的大小) 标准试验:将钢加热到930℃±10℃,保温3~8 小时后测得的奥氏体的晶粒的大小。 1—4级为本质粗晶粒钢, 5—8级为本质细晶粒钢; 规定930℃的原因: ① 930℃左右是本质粗晶粒和本质细晶粒大小差别 最大的温度; ②大多数工件的加热相变都在930℃左右或以下;
9
注意:在转变过程中必须进行碳原子和铁原子
的扩散,以及铁原子发生晶格改组;
通常将这一过程以及A在冷却时的转变过程叫
做“相变重结晶”;
此过程可分为: •A形核; •A的长大; •剩余渗碳体的溶解;
•A成分的均匀化;
(一)、奥氏体形核 如图9-4所示;
P加热到A1以上保温,先在铁素体和渗 碳体的相界面上形成A晶核;
41
(一)、奥氏体成分的影响
1、含碳量的影响: ①亚共析钢的过冷A等温转变曲线: 如图9-17a)所示; 在此曲线的鼻尖上部区域比共析钢多了一 条先共析铁素体析出线;这表示此类钢在 奥氏体转变之前先有铁素体的析出; 在亚共析钢中,随着含碳量的增加,奥氏 体的稳定性增加,孕育期增加,转变速度 减慢,C-曲线右移;
曲线呈C形状原因: 主要是由于扩散和相变驱动力共同决 定的。 当转变温度较高时(过冷度较小时), 虽然原子的扩散速度较大,但由于相变驱 动力(A与P的自由能差)较小,N↓、G↓, 相变速度较小,则孕育期较长; 当转变温度较低时(过冷度较大时), 虽然相变驱动力较大,但由于原子的扩散 速度较小,N↓、G↓,所以,相变速度仍 较小,孕育期仍较长;如图9-15所示;
3、热处理的重要性: 热处理原理:研究钢中组织转变的规律; 热处理工艺:根据热处理原理制定的热处理时 间、温度、介质等参数,实施热处理操作的过 程; 二、热处理与相图: 钢为什么可以进行热处理?
原则:只有在加热或冷却时发生溶解度 显著变化或者发生类似纯铁的同素异构 转变,即有固态相变发生的合金才能进 行热处理;例如:图9-2
§2-2 钢在加热时的转变
热处理的第一道工序是加热,将钢加热到A1以上, P→A,加热是个重要的环节,加热好坏直接影响 着热处理的质量;
奥氏体化:将钢加热到相变点以上获得奥氏体的过 程叫做奥氏体化。
一、共析钢奥氏体的形成过程 珠光体转变为奥氏体的过程如下: α + Fe3C → γ ωc=0.0218% ωc= 6.69% ωc=0.77% 体心立方 正交晶系 面心立方
1.2 非平衡条件下: 在非平衡条件下转变温度要发生不同程 度的滞后,而偏离平衡温度:如图9-3所 示;
通常将加热时的实际临界温度标以“c”: Ac1、Ac3、Accm;
冷却时的实际临界温度标以“r”: Ar1、 Ar3、 Arcm; 加热、冷却速度越快,滞后现象越严重.
加热、冷却转变 A1、A3、Acm Ac1、Ac3、Accm Ar1、Ar3、Arcm
晶粒度:衡量晶粒大小的尺度。单位面积内的晶粒 数目或每个晶粒的平均面积与平均直径。
1、晶粒大小的表示:
①八级晶粒度标准图,N为1~4级,称为粗晶粒, N为5~8级为细晶粒。如图9-8所示;
②公式 n=2N-1 n——放大100倍时每平方英寸(6.45cm2)视野中的 平均晶粒数; N——晶粒度级别
2、起始晶粒度: 奥氏体晶粒边界刚刚相互接触时奥氏体晶粒 的大小为起始晶粒度; 总是十分细小而均匀的。其大小与形核率N 和长大速度G有关。
亚共析钢(Ac3以上得到单相A组织)、过共析 钢(Accm以上得到单相A组织)。
二、影响奥氏体形成速度的因素
(一)、加热温度和保温时间的影响
共析钢奥氏体的等温转变曲线(TTT 图),转变的顺序为: P(α+Fe3C)→P(α+Fe3C)+γ →γ + Fe3C→不均匀γ→均匀γ
14
(二)、原始组织的影响 钢的原始组织越细小,则A形核地点就 多,长大速度快; 例如:钢的原始组织是片状珠光体时,铁素 体和渗碳体组织越细,其相界面就越多,奥 氏体的形核部位也就越多,奥氏体的长大速 度也就越快,因此可以加速奥氏体形成过程, 而经过球化处理获得的粒状珠光体,由于铁 素体和渗碳体的相界面较少,奥氏体的形核 部位也就相应的减少了,因此,奥氏体的形 成速度也就较慢。
③TTT图中的区:如图所示; A1以上的A区; 过冷A区: 转变区:根据转变温度和转变产物的不 同,共析钢C曲线由上至下分为三个区域: 转变终了区:
A1~550℃之间为 珠光体转变区; (扩散型相变) 550~Ms为贝氏体 转变区;(半扩 散型相变) Ms~Mf之间为马 氏体转变区(非 扩散型相变);
(三)、化学成分的影响 1、C:钢中含碳量越高,奥氏体形成速度越 快;(因为含碳量高,增加了铁素体和渗碳体的相 界面;同时,增加碳在奥氏体中的扩散速度。) 2、合金元素(Me): ①影响C在A中的扩散速度: Ⅰ、Co和Ni提高了碳在奥氏体中的扩散速度,故加 快奥氏体的形成速度; Ⅱ、Si、Al、Mn、Cu等,对奥氏体的形成速度影响 不大; Ⅲ、Cr、Mo、W、V等碳化物形成元素显著降低碳 在奥氏体中的扩散速度,因而大大地减慢了奥氏体 的形成速度。