热处理原理及工艺8 讲解
热处理原理以及退火正火淬火回火工艺

热处理原理以及退火正火淬火回火工艺热处理是指通过控制金属的加热和冷却过程,改变其组织结构和性能的工艺过程。
常见的热处理工艺包括退火、正火、淬火和回火等。
以下将详细讨论各种工艺的原理及其应用。
1.退火:退火是指将金属加热到一定温度,保持一段时间后,以适当速度冷却到室温的过程。
退火的主要目的是改善金属的塑性、韧性和机械性能。
退火可分为完全退火和不完全退火两种。
完全退火是将材料加热到足够高的温度,使其结构中的晶界、析出物等发生重排和消失。
不完全退火则是将材料加热到一定温度,使其结构中的晶界、析出物等部分发生变化。
退火的应用包括消除金属加工硬化,改善冷作硬化材料的塑性、焊接后消除应力和改善机械加工性能等。
2.正火:正火是指将金属加热到临界温度以上,保持一定时间后冷却至室温的过程。
正火的目的是改变金属的组织结构,提高其硬度和强度。
正火的冷却速度较慢,使金属内部的相转变得以充分进行。
正火的应用包括强化材料的组织结构,提高其抗拉强度、耐磨性和耐腐蚀性。
3.淬火:淬火是指将金属加热到相变温度以上,保持一段时间后迅速冷却至室温的过程。
淬火的目的是使金属中形成高硬度的马氏体结构。
迅速冷却可以抑制相变,使金属的组织结构保持不稳定状态,从而形成硬脆的马氏体。
淬火的应用包括提高材料的硬度和强度、改善耐磨性和耐腐蚀性。
4.回火:回火是指将已经淬火过的金属加热到一定温度,保持一段时间后冷却至室温的过程。
回火的目的是消除淬火产生的应力和脆性,同时调整金属的硬度和韧性。
回火一般在淬火后立即进行,以充分发挥淬火的效果。
回火的应用包括提高材料的韧性和塑性,降低其硬度和强度,调整材料的组织结构。
总结起来,退火、正火、淬火和回火是常见的热处理工艺。
它们通过控制金属的加热和冷却过程,改变其组织结构和性能。
退火主要是为了改善塑性和韧性,正火用于提高硬度和强度,淬火用于形成高硬度的马氏体结构,而回火则用于调整硬度、韧性和组织结构。
这些热处理工艺广泛应用于钢铁、铝合金和铜合金等金属材料的制造和加工过程中,以满足不同应用领域对材料性能的需求。
热处理原理与工艺

热处理原理与工艺热处理是一种通过加热和冷却来改变材料性能的工艺。
它可以使金属材料获得所需的力学性能、物理性能和化学性能,从而满足不同工程要求。
热处理工艺包括退火、正火、淬火、回火等,不同的工艺可以实现不同的效果。
下面将详细介绍热处理的原理和工艺。
首先,我们来介绍退火工艺。
退火是将金属材料加热到一定温度,保持一定时间后,再以适当速度冷却到室温。
退火的目的是消除材料内部的应力,改善塑性和韧性,降低硬度。
这种工艺适用于大多数金属材料,尤其是碳钢和合金钢。
其次,正火工艺是将金属材料加热到临界温度以上,保持一定时间后,再冷却到室温。
正火可以提高金属的硬度和强度,同时保持一定的韧性。
这种工艺适用于低碳钢、合金钢和工具钢等材料。
淬火是将金属材料加热到临界温度以上,然后迅速冷却到室温。
淬火可以使金属材料获得高硬度和高强度,但同时会降低其韧性。
这种工艺适用于合金钢、高速钢和不锈钢等材料。
最后,回火是将经过淬火处理的金属材料加热到一定温度,然后保持一定时间后冷却。
回火可以降低金属的脆性,提高韧性和塑性。
这种工艺适用于经过淬火处理的合金钢和工具钢等材料。
在进行热处理工艺时,需要注意控制加热温度、保温时间和冷却速度,以确保获得所需的材料性能。
同时,还需要考虑材料的化学成分、组织结构和形状等因素,综合运用各种热处理工艺,以达到最佳的效果。
总之,热处理是一种重要的金属材料加工工艺,通过改变材料的组织结构和性能,可以满足不同工程要求。
各种热处理工艺都有其特定的原理和适用范围,只有深入理解这些原理,才能正确地选择和应用热处理工艺,从而获得优质的金属材料。
材料科学与工程专业金属热处理原理及工艺-课件第八章淬火与回火

2.马氏体分解(100--250 ℃ )
(1)高碳马氏体分解 b.马氏体单相分解(150-250 ℃ ) 当温度高于150℃时,碳 原子扩散能力加大,α相中 不同浓度可通过长程扩散 消除,析出的碳化物粒子 可从较远处得到碳原子而 长大。故在分解过程中, 不再存在两种不同碳含量 的α 相,碳含量和正方度不 断下降,当温度达300℃
回火组织(M回、T回、S回)比较
金属热处理原理及工艺 , SMSE,CUMT 本章首页 上一页 下一页 返 回
回火组织(M回、T回、S回)比较
金属热处理原理及工艺 , SMSE,CUMT 本章首页 上一页 下一页 返 回
T8钢的回火组织(M回、T回、S回)
金属热处理原理及工艺 , SMSE,CUMT 本章首页 上一页 下一页 返 回
硬度
金属热处理原理及工艺 , SMSE,CUMT 本章首页 上一页 下一页 返 回
强度
金属热处理原理及工艺 , SMSE,CUMT 本章首页 上一页 下一页 返 回
碳钢淬火后回火时的力学性能的变化总结
钢在回火时力学性能变化如下: (1)硬度:回火时硬度变化的总趋势是随回火温度的升高而下降但低、中 碳钢在250 ℃以下回火硬度下降不多,高碳钢在100℃回火时硬度略有上升, 出现一个峰值。 250 ℃以上回火硬度持续下降。 (2)强度和塑性:回火时强度变化的趋势是随回火温度的升高,强度(σb、
金属热处理原理及工艺 , SMSE,CUMT 本章首页 上一页 下一页 返 回
随温度升高,淬火组织将发生五个阶段变化: • 马氏体中碳原子偏聚(100℃以下) •马氏体的分解(100~250℃)
产物:M回
• 残余奥氏体的转变(200~300℃) 产物:M回(主要)+ B下(微量)
热处理原理
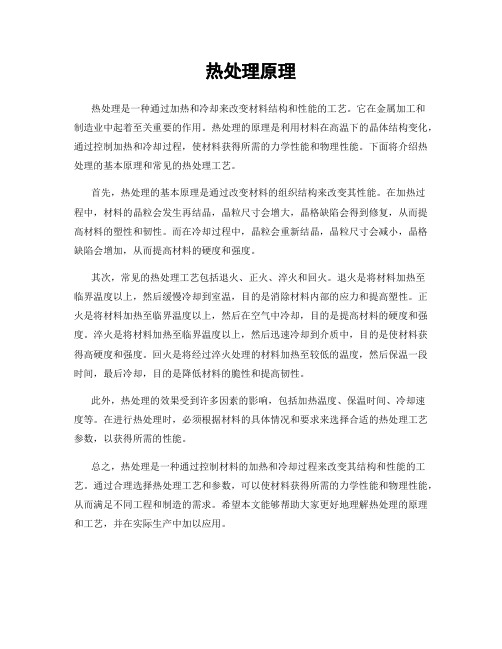
热处理原理
热处理是一种通过加热和冷却来改变材料结构和性能的工艺。
它在金属加工和
制造业中起着至关重要的作用。
热处理的原理是利用材料在高温下的晶体结构变化,通过控制加热和冷却过程,使材料获得所需的力学性能和物理性能。
下面将介绍热处理的基本原理和常见的热处理工艺。
首先,热处理的基本原理是通过改变材料的组织结构来改变其性能。
在加热过
程中,材料的晶粒会发生再结晶,晶粒尺寸会增大,晶格缺陷会得到修复,从而提高材料的塑性和韧性。
而在冷却过程中,晶粒会重新结晶,晶粒尺寸会减小,晶格缺陷会增加,从而提高材料的硬度和强度。
其次,常见的热处理工艺包括退火、正火、淬火和回火。
退火是将材料加热至
临界温度以上,然后缓慢冷却到室温,目的是消除材料内部的应力和提高塑性。
正火是将材料加热至临界温度以上,然后在空气中冷却,目的是提高材料的硬度和强度。
淬火是将材料加热至临界温度以上,然后迅速冷却到介质中,目的是使材料获得高硬度和强度。
回火是将经过淬火处理的材料加热至较低的温度,然后保温一段时间,最后冷却,目的是降低材料的脆性和提高韧性。
此外,热处理的效果受到许多因素的影响,包括加热温度、保温时间、冷却速
度等。
在进行热处理时,必须根据材料的具体情况和要求来选择合适的热处理工艺参数,以获得所需的性能。
总之,热处理是一种通过控制材料的加热和冷却过程来改变其结构和性能的工艺。
通过合理选择热处理工艺和参数,可以使材料获得所需的力学性能和物理性能,从而满足不同工程和制造的需求。
希望本文能够帮助大家更好地理解热处理的原理和工艺,并在实际生产中加以应用。
热处理工艺的原理和应用
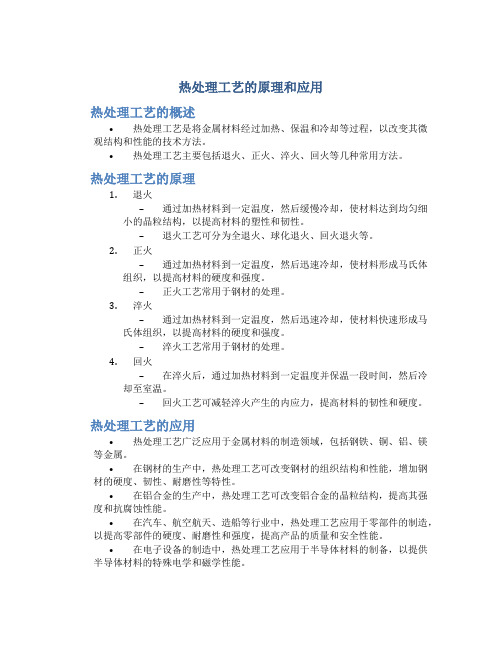
热处理工艺的原理和应用热处理工艺的概述•热处理工艺是将金属材料经过加热、保温和冷却等过程,以改变其微观结构和性能的技术方法。
•热处理工艺主要包括退火、正火、淬火、回火等几种常用方法。
热处理工艺的原理1.退火–通过加热材料到一定温度,然后缓慢冷却,使材料达到均匀细小的晶粒结构,以提高材料的塑性和韧性。
–退火工艺可分为全退火、球化退火、回火退火等。
2.正火–通过加热材料到一定温度,然后迅速冷却,使材料形成马氏体组织,以提高材料的硬度和强度。
–正火工艺常用于钢材的处理。
3.淬火–通过加热材料到一定温度,然后迅速冷却,使材料快速形成马氏体组织,以提高材料的硬度和强度。
–淬火工艺常用于钢材的处理。
4.回火–在淬火后,通过加热材料到一定温度并保温一段时间,然后冷却至室温。
–回火工艺可减轻淬火产生的内应力,提高材料的韧性和硬度。
热处理工艺的应用•热处理工艺广泛应用于金属材料的制造领域,包括钢铁、铜、铝、镁等金属。
•在钢材的生产中,热处理工艺可改变钢材的组织结构和性能,增加钢材的硬度、韧性、耐磨性等特性。
•在铝合金的生产中,热处理工艺可改变铝合金的晶粒结构,提高其强度和抗腐蚀性能。
•在汽车、航空航天、造船等行业中,热处理工艺应用于零部件的制造,以提高零部件的硬度、耐磨性和强度,提高产品的质量和安全性能。
•在电子设备的制造中,热处理工艺应用于半导体材料的制备,以提供半导体材料的特殊电学和磁学性能。
热处理工艺的优点•可改善金属材料的物理性能,提高材料的硬度、韧性、强度等。
•可改变材料的晶粒结构和组织,提供特定的材料性能。
•可改善材料的表面质量,提高耐磨性和耐腐蚀性。
•可通过控制热处理工艺参数,实现材料性能的调控和优化。
热处理工艺的注意事项•热处理工艺的参数,包括加热温度、保温时间、冷却速度等,需要根据材料的类型和要求进行合理选择,以避免材料的过热或过冷现象。
•热处理工艺需要严格控制各个环节的温度和时间,以保证工艺的有效性和一致性。
热处理原理以及退火正火淬火回火工艺

热处理原理以及退火正火淬火回火工艺一、热处理的作用机床、汽车、摩托车、火车、矿山、石油、化工、航空、航天等用的大量零部件需要通过热处理工艺改善其性能。
拒初步统计,在机床制造中,约60%~70%的零件要通过热处理,在汽车、拖拉机制造中,需要热处理的零件多达70%~80%,而工模具及滚动轴承,那么要100%进行热处理。
总之,凡重要的零件都必须进行适当的热处理才能使用。
材料的热处理通常指的是将材料加热到相变温度以上发生相变,再施以冷却再发生相变的工艺过程。
通过那个相变与再相变,材料的内部组织发生了变化,因而性能变化。
例如碳素工具钢T8在市面上购回的经球化退火的材料其硬度仅为20HRC,作为工具需经淬火并低温回火使硬度提高到60~63HRC,这是因为内部组织由淬火之前的粒状珠光体转变为淬火加低温回火后的回火马氏体。
同一种材料热处理工艺不一样其性能差别专门大。
表6-1列出45钢制直径为F15mm的平均园棒材料经退火、正火、淬火加低温回火以及淬火加高温回火的不同热处理后的机械性能,导致性能差别如此大的缘故是不同的热处理后内部组织截然不同。
同类型热处理〔例如淬火〕的加热温度与冷却条件要由材料成分确定。
这些说明,热处理工艺〔或制度〕选择要依照材料的成份,材料内部组织的变化依靠于材料热处理及其它热加工工艺,材料性能的变化又取决于材料的内部组织变化,材料成份-加工工艺-组织结构-材料性能这四者相互依成的关系贯穿在材料加工的全过程之中。
二、热处理的差不多要素热处理工艺中有三大差不多要素:加热、保温、冷却。
这三大差不多要素决定了材料热处理后的组织和性能。
加热是热处理的第一道工序。
不同的材料,其加热工艺和加热温度都不同。
加热分为两种,一种是在临界点A1以下的加热,现在不发生组织变化。
另一种是在A1以上的加热,目的是为了获得平均的奥氏体组织,这一过程称为奥氏体化。
保温的目的是要保证工件烧透,防止脱碳、氧化等。
保温时刻和介质的选择与工件的尺寸和材质有直截了当的关系。
热处理原理及工艺
促进技术创新:热处理在 航空航天工业中的应用促 进了技术创新和进步
航空航天:提高材料的强度和耐热性 汽车工业:提高零部件的耐磨性和耐腐蚀性 机械制造:提高设备的使用寿命和可靠性 电子行业:提高电子元器件的稳定性和可靠性 能源行业:提高能源设备的耐高温性和耐腐蚀性 生物医学:提高生物材料的生物相容性和耐腐蚀性
后处理:对工件 进行清洗、检验 等处理,确保工 件质量符合要求
温度:热处理过程中,温度是影响材料 组织和性能的关键因素。
时间:热处理过程中,时间也是影响材 料组织和性能的关键因素。
气氛:热处理过程中,气氛也是影响材 料组织和性能的关键因素。
冷却速度:热处理过程中,冷却速度也 是影响材料组织和性能的关键因素。
添加标题
添加标题
添加标题
添加标题
热处理质量控制可以保证产品的尺 寸精度、表面质量、力学性能等满 足设计要求。
热处理质量控制可以保证产品的安 全性和可靠性,提高产品的使用寿 命。
制定严格的工艺规程 和操作规程
采用先进的热处理设 备和仪器
定期对热处理设备进 行校准和维护
加强员工培训,提高 操作技能和意识
建立完善的质量管理 体系和检测手段
采用计算机辅助设计 和制造技术,提高热 处理质量和效率
热处理工艺规范:包括温度、时间、气氛等参数的控制 热处理设备:保证设备性能稳定,满足工艺要求 热处理操作人员:具备专业技能和经验,确保操作规范 热处理质量检验:包括外观检查、硬度检测、金相分析等,确保产品质量符合要求
改善材料 的耐磨性 和耐腐蚀 性
改变材料 的疲劳性 能和断裂 韧性
提高材料 的热稳定 性和抗氧 化性
改材料 的磁性能 和电性能
提高材料 的加工性 能和焊接 性能
热处理原理及工艺
热处理原理及工艺热处理是一种用于改善材料性能的重要工艺。
通过控制材料的加热和冷却过程,可以改变材料的晶体结构、力学性能和化学性能,从而提高材料的强度、硬度、耐腐蚀性等。
热处理的原理是基于固体材料的晶体结构与物理性能之间的关系。
晶体结构是由原子或分子的周期性排列所组成,不同的结构会导致不同的物理性能。
在加热过程中,材料中的原子或分子会随着温度的升高而具有更高的热运动能力,从而使晶体结构发生变化。
通过控制加热温度和时间,可以实现晶体结构的改变。
常见的热处理工艺包括退火、淬火、回火、表面处理等。
退火是将材料加热到特定温度,然后缓慢冷却至室温,目的是消除内部应力和改善材料的韧性。
淬火是在材料加热到高温后,迅速冷却至室温,通过快速冷却可以使材料形成硬脆结构,提高材料的硬度和强度,但也会导致内部应力增大,需要进行回火处理来消除应力。
回火是将淬火后的材料加热到适当温度,然后保温一段时间,最后缓慢冷却,目的是降低材料的硬度,提高韧性。
表面处理是在材料表面形成一层特定的化合物或合金层,用于改善材料的耐磨性、耐腐蚀性等。
热处理工艺的选择要根据材料的组成和应用要求进行。
不同材料具有不同的热处理敏感性和适用温度范围。
合理选择热处理工艺可以使材料在满足力学性能和物理性能要求的同时,减少成本和能源消耗。
总之,热处理是一种通过控制材料的加热和冷却过程,改善材料性能的重要工艺。
通过热处理可以改变材料的晶体结构和物理性能,提高材料的强度、硬度、韧性和耐腐蚀性等。
选择合适的热处理工艺对于提高材料的性能和使用寿命至关重要。
热处理是一种将金属或合金材料通过加热和冷却处理来改变其物理和机械性能的工艺。
它是材料加工中非常重要的一部分,因为可以通过控制热处理工艺,使材料的硬度、强度、韧性、耐腐蚀性等性能得到改善。
热处理的核心原理是通过控制材料的加热温度和冷却速度,使材料的晶体结构发生变化。
材料的晶体结构决定了其宏观性能。
例如,在晶体结构较均匀的钢中,碳原子分布均匀,这样就有利于提高钢材的硬度和强度。
热处理原理与工艺第八章 钢 的 淬 火
第八章 钢 的 淬 火
2.在无物态变化的介质中的冷却过程 常用的无物态变化的淬火介质有盐浴、碱浴、金属浴及气体等。
第八章 钢 的 淬 火
三、淬火介质冷却能力的测定及影响因素
图8-3 银球探头法示意图 1—银球 2—热电偶 3—淬火介质
第八章 钢 的 淬 火
1.淬火介质冷却能力的测定及表示 淬火介质的冷却能力常用标准试样的冷却曲线或温度-冷却速度曲
线表示。
表8-1 常用淬火介质的淬火烈度
第八章 钢 的 淬 火
2.影响介质冷却能力的因素 除介质自身性质之外,温度和搅拌对介质冷却能力有较大影响。
(1)温度 (2)搅拌
第八章 钢 的 淬 火
四、常用淬火介质及其冷却特性 1.常用有物态变化淬火介质及其冷却特性 (1)水
图8-4 不同温度静止水与循环水的冷却特性曲线 a)静止水 b)循环水
二、工件在淬火介质中的冷却过程 1.在有物态变化的冷却介质的冷却过程
这类介质的沸点远低于工件温度,赤热工件投入介质后,介质会 发生沸腾汽化。 (1)蒸汽膜阶段—Ⅰ阶段 (2)沸腾阶段—Ⅱ阶段 (3)对流阶段—Ⅲ阶段
第八章 钢 的 淬 火
图8-2 有物态变化的淬火介质的 冷却曲线和冷却速度曲线
1—冷却曲线 2—冷却速度曲线
第八章 钢 的 淬 火
(4)过饱和硝盐水溶液
图8-8 过饱和硝盐水溶液与 水、油的冷却速度比较
第八章 钢 的 淬 火
2.常用无物态变化淬火介质及其冷却特性 (1)硝盐浴
表8-2 常用的硝盐浴和碱浴的成分、熔点及使用温度
第八章 钢 的 淬 火
为提高硝盐浴的冷却能力,常加入一定量的水,因淬火时水的汽 化会吸收大量的热,且水可增大盐浴流动性,从而增大冷速。
热处理基本知识及工艺原理
热处理基本知识及工艺原理1. 热处理的基础热处理听起来很高大上,其实说白了就是给金属“洗澡”,不过这澡可不是一般的洗澡,它是通过加热和冷却,让金属变得更结实、更耐用。
就像人要适当运动一样,金属也需要“锻炼”才能有更好的表现。
大家常常听到的“热处理”这两个字,实际上是金属加工中的一个重要环节,尤其是在制造一些需要承受高强度和高温的零件时,它的重要性就显得尤为突出。
1.1 热处理的类型热处理可分为几种主要的类型,比如淬火、回火、退火、正火等等。
这些名字听起来有点像高深的武功秘籍,但其实它们各有各的妙处。
淬火就像是给金属来个猛击,迅速让它从热状态转为冷状态,达到硬化的效果;而回火则是帮金属放松一下,避免太过刚强造成的脆弱。
退火则是金属的“慢养”,通过长时间的加热和缓慢冷却,让金属的内部结构得到调整。
正火呢,就像是在金属身上做个深层按摩,让它恢复到最佳状态。
1.2 热处理的原理那热处理的原理又是什么呢?其实也不复杂。
热处理过程中,金属的内部原子结构会发生变化,就像是大海中的波涛汹涌,时而平静,时而激烈。
加热的时候,原子就像聚会的朋友,欢快地跳动;冷却时,它们就得迅速找到自己的位置,有时候甚至会出现“打架”的情况,这就影响了金属的强度和韧性。
2. 热处理的工艺2.1 工艺步骤热处理的工艺流程一般包括加热、保温和冷却三个步骤。
先是加热,像开车一样,把温度开到理想值,这个过程要慢慢来,别着急;接着就是保温,保持一段时间,让金属的“细胞”好好“吸收养分”;最后是冷却,冷却的方法可以是水、油,甚至空气,各种各样的方式让金属在不同的环境中“转身”。
这整个流程下来,金属的性能就提升了好几个档次。
2.2 影响因素当然,热处理的效果也受很多因素影响,比如温度、时间、冷却速度等。
就好比炒菜,如果温度掌握不好,时间控制不当,最终的味道可就大相径庭了。
为了得到理想的效果,工艺参数的选择可得仔细斟酌。
3. 热处理的应用热处理在我们生活中无处不在,特别是在汽车、航空、机械等行业,都是大显身手的地方。
- 1、下载文档前请自行甄别文档内容的完整性,平台不提供额外的编辑、内容补充、找答案等附加服务。
- 2、"仅部分预览"的文档,不可在线预览部分如存在完整性等问题,可反馈申请退款(可完整预览的文档不适用该条件!)。
- 3、如文档侵犯您的权益,请联系客服反馈,我们会尽快为您处理(人工客服工作时间:9:00-18:30)。
?若两方面作用大致相当时,则对Ms的影响不大,如 Si 。
2、奥氏体化条件对 Ms的影响
? 一般,不完全奥氏体化,提高加热温度和保温时间, 将使奥氏体中碳和合金元素含量增加,使 Ms降低 ? 完全奥氏体化条件下,温度高时间长,将因马氏体相 变阻力减小,使 Ms 有所提高(约在几度到几十度范围内)
? 因新相与母相 比体积不同 和维持切变而引起的弹性应变 能。
? 产生宏观均匀切变而作的功。 ? 产生微观不均匀切变 而在马氏体内形成的高密度位错或
孪晶所消耗的能量。 ? 近邻奥氏体基体发生的协作形变而作的功。
?马氏体相变热滞大是由于切变特性而引起额外能量消耗造 成的。
2 、T0、Ms、As之间的关系:
3、冷却速度的影响
基本条件:冷却速度>v临时,奥氏体才能过冷到Ms点以下转变 为马氏体。
?在一般生产条件下,冷却速度对Ms无影响。
?若进一步提高冷速,则 Ms点也会发生变化。如对于 Fe-0.5C2.05Ni合金,当冷却速度超过104℃/s 时,Ms点才将上升
原因:
?正常淬火条件下,C原子偏聚倾向随温度降低 扩散能力减弱而逐渐增大,其对 A有强化作用, Ms降低;而A中C降低,Ms升高。 故Ms稳定 ?冷速极快时,则抑制了“碳原子气团”的形成, 使A弱化,降低M相变阻力,Ms↑。 ?冷速足够大时,气团被完全抑制, Ms点不再 随冷速变化。
1、奥氏体化学成份的影响 (1)碳的影响
(2)合金元素的影响 ? 一般规律: 钢中常见的合 金元素,除 Al和Co可以提高 Ms 外,其它合金元素均使Ms 降低。 ? 降低 Ms 点的元素,按其影 响的强烈顺序排列如下:
Mn 、Cr 、 Ni、 Mo 、Cu 、 W、V、Ti ? 钢中单独加入 Si 时,对 Ms 影响不大,但是在 Ni-Cr 钢中可 以降低钢的Ms点。
§5-5 马氏体转变动力学
形核 和 长大 一、马氏体的降温形成(变温瞬时形核、瞬时长大)
碳钢和低合金钢中最常见的一种马氏体转变。 1.动力学特点 ?多数M转变必须在连续不断的降温过程中才能进行,瞬时 形核,瞬时长大,形核后以极大的速度长大到极限尺寸, ? 相变时M量的增加是由于降温过程中 新马氏体片的形成, 而不是已有M片的长大。等温停留转变立即停止。
?逆转变与冷却时的刚好相反,需 过热度 ,逆转变是在升温过程中 进行的。 As与Ms之差视合金的 种类不同而不同。
为什么钢的马氏体相变所以热滞如此之大?
? 一般相变理论的能量方程
ΔG=-ΔGV+ΔGS+ΔGE ?相变驱动力来自于M与A的单位体积自由能之差, ?相变阻力来自: (1)形成新的界面而消耗界面ห้องสมุดไป่ตู้ΔGS (2)弹性能ΔGE主要分以下几方面:
T0 、 Ms 、 As 都是合金 成 分的函数,不同的合金系
As-Ms 之差不同,例如, FeNi 合金中 As 较 Ms 高 420℃, Au-Cd 合 金 中 As 较 Ms 仅 高 16℃。
3、形变诱发马氏体转变
? 实验证明: ? Ms和As之间的温度差可以因为引入塑性变形而减小。 ? 如果在Ms点以上对奥氏体进行塑性变形 会诱发马氏体转 变而引起Ms点升高达到Md点,同样塑性变形也可以使 As下 降到Ad点。
4、形变的影响
在Md 、Ms之间对奥氏体进行塑性变形,可使Ms升 高,马氏体转变提前发生。
获得相同的M转变量,形变温度越低,需要的形变量越小
5、应力的影响
? 单向的拉应力和压应力都促进马氏体转变,使 Ms升高。
? 多向压应力阻碍马氏体转变,使Ms降低。
6、磁场的影响
磁场的存在可使 Ms 升高 ,在相同温度 下马氏体转变量增加, 但磁场对 Ms 以下的转 变行为无影响。
Ms=A-x1C-x2Mn-x3Ni-x4Cr….
? 合金元素的影响Ms点的原因:
主要取决于合金元素对 平衡温度T0的影响及对奥氏体的强 化效应。
? 凡强烈降低 T0及强化奥氏体的元素,就强烈降低 Ms , 如Mn 、Cr 、Ni、Cu 和C类似,既降低T0温度,又稍增加奥 氏体的屈服强度,所以降低Ms点。 ? Al、Co、Si、Mo、W、V、Ti等均提高T0温度,但也不 同程度地增加奥氏体屈服强度,
? Ad点的物理意义是可获得形变奥氏体的最低温度。 ? 马氏体相变的热力学, Md的上限温度为 T0 ,而Ad的 下限温度也为 T0。实验证明 ,Co-Ni合金中 Md和Ad可以重 合,即 Md=Ad=T0。如果某合金系中Md和Ad不重合时,则可 取: T0=1/2(Md+Ad)。
?形变诱发马氏体转变的原因 :
形变能为相变提供一定的能量 ?如果形变能量与化学驱动力 相互作用,能够达到相变所需 的最小驱动力,则相变就可以 提前发生。形变所提供的能量, 称为机械驱动力。
?若机械驱动力可全部代替化 学驱动力,Md 点已上升到T0 , 但这要求一种合适的变形方式 , 以提供足够的机械驱动力。
二、影响钢Ms点的因素
A与M自由能随温度的变化
?Ms的物理意义 母相和马氏体两相之间的自由能之差达到相变所需的最
小驱动力值时的温度。
?马氏体转变热滞代表所需的驱动 力,取决于 马氏体转变时增加的 界面能 (M/A界面共格,故较小) 和弹性能 之和。其中 弹性能是主 要影响因素。
?热滞的大小,视合金的种类和合 金的成份而异, Fe系合金的热滞 可高达 200℃以上 ,而有的合金, 其热滞仅十几度到几十摄氏度, 例如:Au-Cd 、Ag-Cd 。
? Md, Ad分别称为形变马氏体点和形变奥氏体点 。因为形变 诱发马氏体转变而产生的马氏体 ,常称为形变马氏体,同样形变 诱发马氏体逆转变而产生的奥氏体,称为 形变奥氏体。
?Md、Ad点的物理意义 :
? Md 可获得形变马氏体的 最高温度 ,若在高于 Md点的温 度对 A 进行塑性变形,就会失去诱发马氏体转变的作用。
热处理原理及工艺 (8)
§5-4马氏体转变的热力学 一、马氏体转变的热力学条件
1、相变驱动力
?马氏体转变与其它类型的转变有 许多不同之处,但仍然是热学性的, 即相变的驱动力仍是马氏体与母相 之间的自由能之差。
?马氏体转变的热力学条件是必须 在一定的过冷度下转变才能进行。
通常把 Ms与T0之差称为 马氏体 转变的热滞