最新电机SpTA控制算法资料
基于图像检测的光伏面板自清洁系统设计与实现

设计应用esign & ApplicationD基于图像检测的光伏面板自清洁系统设计与实现*Design and implementation of solar panel self cleaning system李晨阳,曹子卿,洪章富,陈沛雯,钟张佳玟,董笑凡(上海大学 工程训练国家级实验教学示范中心,上海 200044)摘 要:光伏面板受到环境中扬尘、积雪等影响,表面易沾染杂质,导致发电效率降低。
日晒会使面板出现裂纹和热斑,严重破坏电池组件甚至系统。
目前市面上的太阳能板修正产品只能单一实现清洁功能,并且无法脱离人工而实现自动化。
本文旨在针对光伏面板的日常维护进行机械智能化设计,研制一套集用户前端、远程控制、自动清洗、智能图像检测为一体的全自动智能清洁光伏面板装置。
关键词:光伏面板;全自动;清洁;图像检测0 引言随着太阳能产业的迅速发展,其使用规模不断扩大。
光伏面板表面沾染的扬尘、积雪等杂质会使其发电效率大幅降低。
此外,经过长时间的日晒,其表面会出现裂纹及热斑,可能严重破坏太阳电池组件,甚至造成不可预估的灾难,所以极有必要进行实时热斑检测。
市场调查显示,目前太阳能板维护装置只能实现清洁功能,故现迫切需要一套兼具清洁和检测功能的太阳能板机构,以最大限度地优化现有设备。
对家庭而言,可直接实时检测太阳能板表面并进行简单操作,降低发生事故的风险。
对于企业而言,可以达到定时清扫太阳能板及自动查找裂纹的功能,最大限度地提高经济效益。
1 光伏面板清洁与监测系统分析与设计1.1 系统需求分析目前世界上普遍认为晶硅光伏电池的平均寿命是25~30年,非晶硅光伏电池的寿命也在15~20年以上,其他材料的太阳能光伏板使用寿命也被认为在20~30年左右。
影响太阳能光伏板使用寿命的原因主要有光伏电池效率衰减(晶硅光伏组件效率衰减一般平均为0.5%~ 1%);组件内部电池脱焊,由于太阳电池片之间的间距设计不合理或焊接质量不良,且组件昼夜间温差使焊带和电池之间每天都要经历热胀冷缩的运动,最终导致焊带和电池片焊接脱焊而导致组件报废;太阳能光伏组件工作环境恶劣,日温差:-30~+70 ℃;由于太阳电池片之间的间距设计不合理或焊带质量不良,导致由于组件昼夜间温差使焊带每天都要经历热胀冷缩的弯折运动;恶劣气候对光伏组件的破坏:昼夜、东西温差、风沙、雪荷载等。
电机算法合集(梯形整流换向、正弦整流换向、AC电机控制算法……)

电机算法合集(梯形整流换向、正弦整流换向、AC电机控制算法……)BLDC电机控制算法无刷电机属于自換流型(自我方向轉換),因此控制起来更加复杂。
BLDC电机控制要求了解电机进行整流转向的转子位置和机制。
对于闭环速度控制,有两个附加要求,即对于转子速度/或电机电流以及PWM信号进行测量,以控制电机速度功率。
BLDC电机可以根据应用要求采用边排列或中心排列PWM信号。
大多数应用仅要求速度变化操作,将采用6个独立的边排列PWM信号。
这就提供了最高的分辨率。
如果应用要求服务器定位、能耗制动或动力倒转,推荐使用补充的中心排列PWM信号。
为了感应转子位置,BLDC电机采用霍尔效应传感器来提供绝对定位感应。
这就导致了更多线的使用和更高的成本。
无传感器BLDC控制省去了对于霍尔传感器的需要,而是采用电机的反电动势(电动势)来预测转子位置。
无传感器控制对于像风扇和泵这样的低成本变速应用至关重要。
在采有BLDC电机时,冰箱和空调压缩机也需要无传感器控制。
空载时间的插入和补充大多数BLDC电机不需要互补的PWM、空载时间插入或空载时间补偿。
可能会要求这些特性的BLDC应用仅为高性能BLDC伺服电动机、正弦波激励式BLDC电机、无刷AC、或PC同步电机。
控制算法许多不同的控制算法都被用以提供对于BLDC电机的控制。
典型地,将功率晶体管用作线性稳压器来控制电机电压。
当驱动高功率电机时,这种方法并不实用。
高功率电机必须采用PWM控制,并要求一个微控制器来提供起动和控制功能。
控制算法必须提供下列三项功能:•用于控制电机速度的PWM电压•用于对电机进整流换向的机制•利用反电动势或霍尔传感器来预测转子位置的方法脉冲宽度调制仅用于将可变电压应用到电机绕组。
有效电压与PWM占空度成正比。
当得到适当的整流换向时,BLDC的扭矩速度特性与一下直流电机相同。
可以用可变电压来控制电机的速度和可变转矩。
功率晶体管的换向实现了定子中的适当绕组,可根据转子位置生成最佳的转矩。
基于FPGA的SpTa自适应电机控制算法

DOI:10.16661/ki.1672-3791.2018.25.011基于FPGA的SpTa自适应电机控制算法王岩(桂林电子科技大学计算机科学与工程学院 广西桂林 541004)摘 要:针对现有步进电机控制器的不足,设计一种基于FPGA(Field-Programmable Gate Array)的SpTa自适应电机控制算法。
本算法通过简单的数学运算和极低的资源占用、利用FPGA并行执行的特点,实现了多轴同步运动、加减速过程加速度可调的自适应电机控制。
使用SpTa算法实现加速度自适应的电机加减速运动,具有很好的实用性。
关键词:FPGA 电机控制算法 SpTa 多轴同步控制器中图分类号:TP18 文献标识码:A 文章编号:1672-3791(2018)09(a)-0011-02医疗设备、工业设备的运动控制系统中,需要多个步进电机同步多角度的运动,以实现复杂的多方位控制。
步进电机的驱动控制常用的有PLC、MUC、FPGA等方式,其中PLC控制成本较高,不适合在低成本的方案中使用,单一MUC无法实现多电机的同步运动,FPGA的并行执行及低成本的特点能很好地实现在低成本方案中多电机的同步运动。
现有的电机控制技术主要通过加减速算法实现步进电机的平滑运动,加减速算法常用的有梯形加减速、S型加减速。
梯形加减速算法加速和减速过程中加速度为一个常数,在FPGA上实现该算法的原理比较简单,但是该算法加速不平稳,冲量比较大,运行精度低。
S型加减速算法加速和减速过程中加速度按照加加速、匀加速、减加速的过程完成整个变速过程,该算法加速平稳,冲量小,但是加速度时间比较长,在FPGA上实时计算加速过程的加速度计算量大,占用的FPGA资源比较大,耗时比较长,进而影响实时性。
根据FPGA芯片的特点及现有技术的不足,提出一种用于控制步进电机的基于FPGA的SpTa自适应控制算法。
该算法在FPGA上使用简单的加、减、移位运算,使用很少的资源实现多个步进电机的同步平稳运动。
电机功率因数控制器的控制算法
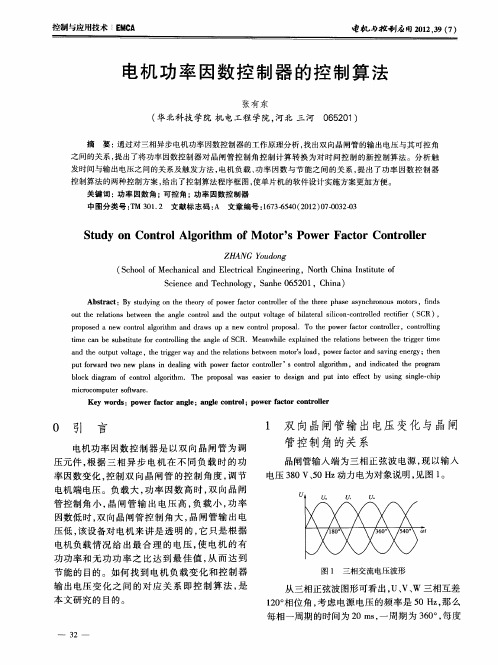
从三 相正 弦波 图形可看 出 , V、 三相 互差 u、 W 10相 位 角 , 2。 考虑 电源 电压 的频 率 是 5 z 那 么 0H , 每 相一 周期 的时 间为 2 , 周 期 为 3 0 , 度 0ms一 6 。每
~
3 一 2
迫 札 与粒 制 应 闭 21 , 7 023 ) 9(
控制算法的两种控制方案 , 给出了控制算法程序框图 , 使单片机的软件设计 实施方案更加方便 。
关 键 词 : 率 因数 角 ; 控 角 ; 率 因数 控 制 器 功 可 功 中 图分 类 号 :M 3 12 文献 标 志 码 : 文章 编 号 :6 364 (0 2 0 -0 2 3 T 0 . A 17 - 0 2 1 ) 7 3 - 5 0 0
p o o e e o to a g rtm n r wsu e o t lp o o a .T h o r fco o t l r o tol g r p s d a n w c n r l lo i h a d d a p a n w c n r r p s 1 o t e p we a tr c n r l ,c n r l n o oe i t a e s b t u ef rc n rl n e a g e o C i c n b u si t o o t l g t n l f R. Me n h l x li e h eai n ewe n t e tig rt me t oi h S a w i e p an d t e r lt s b t e h r e i e o g me a d t e o t u ot g n h up tv l e,te t g e a n h eai n ewe n moo ’ la a h i g rw y a d t e r lt sb t e tr d,p we a t r n a i g e e g r o so o r co d s v n n ry;t e f a hn p t o wa d t e ln n d aig wi o e a tr c n r l r S c n r lag r h ,a d i d c td t e p o r m u r r wo n w p a s i e l t p w r fco o tol ’ o to lo i m f n h e t n n iae h r g a b o k d a r m fc n r l ag r h lc ig a o o t lo i m. T e p o o a a a i r t e in a d p t it f c y u i g s ge c i o t h r p s l w s e se o d sg n u n o ef t b sn i l 。h p e n
智能自适应控制算法在电机控制中的应用探索

智能自适应控制算法在电机控制中的应用探索随着科技发展和智能化进步的不断加速,越来越多的电机控制系统正在转向智能自适应化。
这种控制方式可以根据不同的工况环境动态调节系统参数,主要用于提高系统自适应能力、优化控制效果、降低能耗浪费等方面,能够有效推动电机系统的高效运行。
一般而言,电机是由转子和定子两部分组成的。
我们可以用基本的控制方法,例如PI控制、模型预测控制、PID等,在转速、转矩、位置和跟踪方面实现电机的控制。
但是,这些控制技术的缺点是针对不同的工况环境而调整的参数相对固定。
这就使得既有的控制方式无法完全满足电机控制的需要,因为不同的工况环境下,电机的特性和响应是不同的,也就要求控制策略在不同的工况下进行动态调整。
这时,就要用到智能自适应控制算法。
一、智能自适应控制算法概述智能自适应控制算法是指基于计算机和人工智能控制技术,对电机控制系统进行监测、识别和调整,实现动态优化控制。
这类算法可以根据实际控制效果和系统响应情况进行反馈调整,实现实时控制。
在智能自适应控制算法中,其建模部分包含了多种不同的技术,例如人工神经网络、遗传算法、模糊逻辑和支持向量机等。
通过这些技术的结合,使得系统能够更加准确地感应到现实控制环境的变化,以应对不断变化的外部干扰,从而进行实时调整。
二、智能自适应控制算法在电机驱动系统中的应用从理论角度来说,使用智能自适应控制算法可提高电机驱动系统的运行效率,提高工作质量和生产效率。
在电机调速、电机轴向、转子参数等方面,可以通过智能自适应控制算法实现更好的控制。
电机控制是一个典型的非线性控制问题,而智能自适应控制算法则在设计之初就考虑了这种非线性因素。
这种算法通过对电机的自适应纠正,并以电机行为和环境变化为条件,实现系统参数的调整。
如此一来,系统便能够适应各种不同的工况。
此外,智能自适应控制算法还可以实现在线控制,因为它可以通过实时反馈,使得系统能够及时感知到环境变化,并对系统进行快速调整,从而保证系统在任何情况下都能够有效地运行。
伺服系统的一些公式
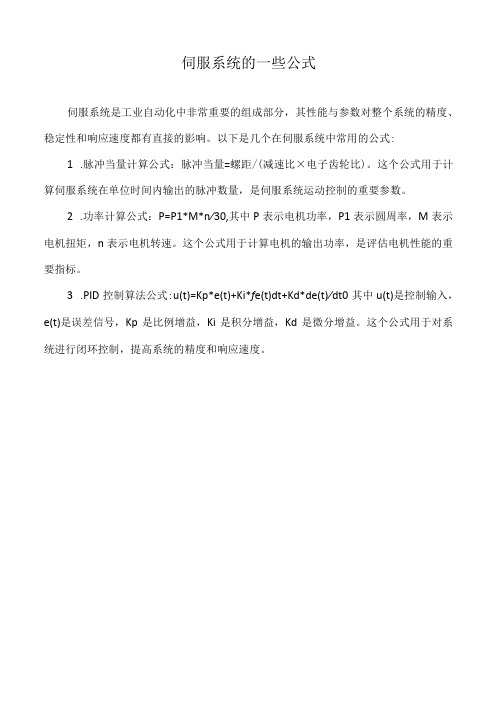
伺服系统的一些公式
伺服系统是工业自动化中非常重要的组成部分,其性能与参数对整个系统的精度、稳定性和响应速度都有直接的影响。
以下是几个在伺服系统中常用的公式:
1.脉冲当量计算公式:脉冲当量=螺距/(减速比×电子齿轮比)。
这个公式用于计算伺服系统在单位时间内输出的脉冲数量,是伺服系统运动控制的重要参数。
2.功率计算公式:P=P1*M*n∕30,其中P表示电机功率,P1表示圆周率,M表示电机扭矩,n表示电机转速。
这个公式用于计算电机的输出功率,是评估电机性能的重要指标。
3.PID控制算法公式:u(t)=Kp*e(t)+Ki*f e(t)dt+Kd*de(t)∕dt0其中u(t)是控制输入,e(t)是误差信号,Kp是比例增益,Ki是积分增益,Kd是微分增益。
这个公式用于对系统进行闭环控制,提高系统的精度和响应速度。
电机SpTA控制算法 (2)

电机SpTA控制算法SpTA即Steps per Time algorithm,它与步进电机S形曲线控制算不同,S形曲线控制算法思想就是根据电机的步数来计算时间,即所谓的Time per Steps,该控制算法先计算电机每一步运行频率,再根据运动曲线计算得到时间参数,而SpTA算法则就是以时间计算为中心,根据时间来计算运动步数相关参数,它的做法就是将电机的运动时间分割成若干个合适的小时间片,在每个时间片内它都将速度参数加到位置参数上,如果位置参数溢出,它就会输出一个脉冲,速度参数根据加速度参数与时间而改变,随着时间推移,速度参数越来越大,位置参数溢出频率越来越高,则电机的运行频率也越来越高错误!未找到引用源。
为了实现根据速度参数控制脉冲输出频率,需要定义以下变量:PosAccumulator 位置累加器PosAdd 位置增加值ActualPosition 实际位置TargetPosition 目标位置,用户输入步进电机运动的步数在时间片到来后进行如下计算:PosAccumulator += ActualVelocity; //位置累加器+实际速度PosAdd = PosAccumulator >> 17; //移位,判断速度累加器就是否溢出PosAccumulator -= PosAdd << 17; //位置累加器去掉溢出部分if(PosAdd!=0) //位置累加器溢出,产生一个不进脉冲{ActualPosition+=1;产生一个步进脉冲;}这样控制器输出的脉冲频率就随着实际速度的增大而增高,随着实际速度减小而降低。
为了根据时间实现实际速度的变化,需要定义以下变量:VelAccumulator 速度累加器ActualAcceleration 实际加速度,用户设定的加速度数值VelAdd 速度增加值ActualVelocity 实际速度TargetVelocity 目标速度在时间片到来后进行如下计算:if(ActualVelocity!=TargetVelocity){//如果实际速度!=目标速度VelAccumulator+=ActualAcceleration; //速度累加器+实际加速度VelAdd = VelAccumulator >> 17; //移位,判断速度累加器就是否溢出VelAccumulator-=VelAdd << 17; //速度累加器去掉溢出部分if(ActualVelocity<TargetVelocity){//如果实际速度<目标速度ActualVelocity=MIN(ActualVelocity+VelAdd, TargetVelocity); //实际速度为两者中小者}else if(ActualVelocity>TargetVelocity){//如果实际速度>大于目标速度ActualVelocity=MAX(ActualVelocity-VelAdd, TargetVelocity);//实际速度为两者中大者}}else{//实际速度=目标速度,不需要执行加加速算法VelAccumulator=0;VelAdd=0;}这样,就实现了通过时间与目标速度改变电机实际速度参数,进而间接改变控制器输出脉冲的频率,时间参数就是随着电机运行而递增的,目标速度参数数值就是使用一个状态机根据当前的运行状态来确定的,该状态机具有四种状态:0: RAMP_IDLE-空闲状态1: RAMP_ACCELERATE-加速状态2: RAMP_DRIVING -匀速状态3: RAMP_DECELERATE-减速状态状态状态切换及其条件如图3-11所示:))图3-11 SpTA控制算法状态机状态切换图SpTA算法同样就是通过定时器来实现的,与S形曲线算法不同的就是它没有使用定时器的PWM功能,仅仅就是通过定时器定时中断来产生一个时间片,在定时器中断服务子程序中完成上述算法,在需要时,通过控制GPIO产生一个步进脉冲。
电机SpTA控制算法
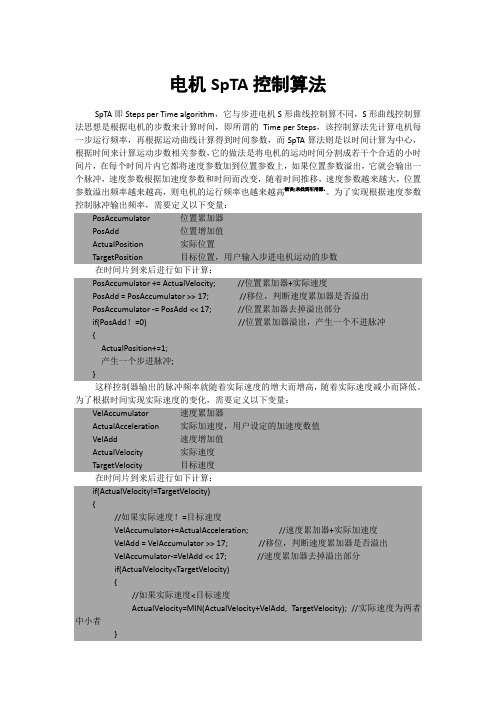
电机SpTA控制算法SpTA即Steps per Time algorithm,它与步进电机S形曲线控制算不同,S形曲线控制算法思想是根据电机的步数来计算时间,即所谓的Time per Steps,该控制算法先计算电机每一步运行频率,再根据运动曲线计算得到时间参数,而SpTA算法则是以时间计算为中心,根据时间来计算运动步数相关参数,它的做法是将电机的运动时间分割成若干个合适的小时间片,在每个时间片内它都将速度参数加到位置参数上,如果位置参数溢出,它就会输出一个脉冲,速度参数根据加速度参数和时间而改变,随着时间推移,速度参数越来越大,位置参数溢出频率越来越高,则电机的运行频率也越来越高错误!未找到引用源。
为了实现根据速度参数控制脉冲输出频率,需要定义以下变量:PosAccumulator 位置累加器PosAdd 位置增加值ActualPosition实际位置TargetPosition目标位置,用户输入步进电机运动的步数在时间片到来后进行如下计算:PosAccumulator += ActualVelocity; //位置累加器+实际速度PosAdd = PosAccumulator >> 17; //移位,判断速度累加器是否溢出PosAccumulator -= PosAdd << 17; //位置累加器去掉溢出部分if(PosAdd!=0) //位置累加器溢出,产生一个不进脉冲{ActualPosition+=1;产生一个步进脉冲;}这样控制器输出的脉冲频率就随着实际速度的增大而增高,随着实际速度减小而降低。
为了根据时间实现实际速度的变化,需要定义以下变量:VelAccumulator 速度累加器ActualAcceleration实际加速度,用户设定的加速度数值VelAdd 速度增加值ActualVelocity实际速度TargetVelocity目标速度在时间片到来后进行如下计算:if(ActualVelocity!=TargetVelocity){//如果实际速度!=目标速度VelAccumulator+=ActualAcceleration; //速度累加器+实际加速度VelAdd = VelAccumulator >> 17; //移位,判断速度累加器是否溢出VelAccumulator-=VelAdd << 17; //速度累加器去掉溢出部分if(ActualVelocity<TargetVelocity){//如果实际速度<目标速度ActualVelocity=MIN(ActualVelocity+VelAdd, TargetVelocity); //实际速度为两者中小者}else if(ActualVelocity>TargetVelocity) {//如果实际速度>大于目标速度ActualVelocity=MAX(ActualVelocity -VelAdd, TargetVelocity);//实际速度为两者中大者} } else {//实际速度=目标速度,不需要执行加加速算法 VelAccumulator=0; VelAdd=0;}这样,就实现了通过时间和目标速度改变电机实际速度参数,进而间接改变控制器输出脉冲的频率,时间参数是随着电机运行而递增的,目标速度参数数值是使用一个状态机根据当前的运行状态来确定的,该状态机具有四种状态:0: RAMP_IDLE -空闲状态1: RAMP_ACCELERATE -加速状态 2: RAMP_DRIVING -匀速状态 3: RAMP_DECELERATE -减速状态状态状态切换及其条件如图3-11所示:))图3-11 SpTA 控制算法状态机状态切换图SpTA 算法同样是通过定时器来实现的,与S 形曲线算法不同的是它没有使用定时器的PWM 功能,仅仅是通过定时器定时中断来产生一个时间片,在定时器中断服务子程序中完成上述算法,在需要时,通过控制GPIO 产生一个步进脉冲。
- 1、下载文档前请自行甄别文档内容的完整性,平台不提供额外的编辑、内容补充、找答案等附加服务。
- 2、"仅部分预览"的文档,不可在线预览部分如存在完整性等问题,可反馈申请退款(可完整预览的文档不适用该条件!)。
- 3、如文档侵犯您的权益,请联系客服反馈,我们会尽快为您处理(人工客服工作时间:9:00-18:30)。
电机SpTA控制算法
SpTA即Steps per Time algorithm,它与步进电机S形曲线控制算不同,S形曲线控制算法思想是根据电机的步数来计算时间,即所谓的Time per Steps,该控制算法先计算电机每一步运行频率,再根据运动曲线计算得到时间参数,而SpTA算法则是以时间计算为中心,根据时间来计算运动步数相关参数,它的做法是将电机的运动时间分割成若干个合适的小时间片,在每个时间片内它都将速度参数加到位置参数上,如果位置参数溢出,它就会输出一个脉冲,速度参数根据加速度参数和时间而改变,随着时间推移,速度参数越来越大,位置参数溢出频率越来越高,则电机的运行频率也越来越高错误!未找到引用源。
为了实现根据速度参数控制脉冲输出频率,需要定义以下变量:
PosAccumulator 位置累加器
PosAdd 位置增加值
ActualPosition 实际位置
TargetPosition 目标位置,用户输入步进电机运动的步数
在时间片到来后进行如下计算:
PosAccumulator += ActualVelocity; //位置累加器+实际速度
PosAdd = PosAccumulator >> 17; //移位,判断速度累加器是否溢出
PosAccumulator -= PosAdd << 17; //位置累加器去掉溢出部分
if(PosAdd!=0) //位置累加器溢出,产生一个不进脉冲
{
ActualPosition+=1;
产生一个步进脉冲;
}
这样控制器输出的脉冲频率就随着实际速度的增大而增高,随着实际速度减小而降低。
为了根据时间实现实际速度的变化,需要定义以下变量:
VelAccumulator 速度累加器
ActualAcceleration 实际加速度,用户设定的加速度数值
VelAdd 速度增加值
ActualVelocity 实际速度
TargetVelocity 目标速度
在时间片到来后进行如下计算:
if(ActualVelocity!=TargetVelocity)
{
//如果实际速度!=目标速度
VelAccumulator+=ActualAcceleration; //速度累加器+实际加速度
VelAdd = VelAccumulator >> 17; //移位,判断速度累加器是否溢出
VelAccumulator-=VelAdd << 17; //速度累加器去掉溢出部分
if(ActualVelocity<TargetVelocity)
{
//如果实际速度<目标速度
ActualVelocity=MIN(ActualVelocity+VelAdd, TargetVelocity); //实际速度为两者中小者
}
else if(ActualVelocity>TargetVelocity)
{
//如果实际速度>大于目标速度
ActualVelocity=MAX(ActualVelocity-VelAdd, TargetVelocity);//实际速度为两者中大者
}
}
else
{
//实际速度=目标速度,不需要执行加加速算法
VelAccumulator=0;
VelAdd=0;
}
这样,就实现了通过时间和目标速度改变电机实际速度参数,进而间接改变控制器输出脉冲的频率,时间参数是随着电机运行而递增的,目标速度参数数值是使用一个状态机根据当前的运行状态来确定的,该状态机具有四种状态:
0: RAMP_IDLE-空闲状态
1: RAMP_ACCELERATE-加速状态
2: RAMP_DRIVING -匀速状态
3: RAMP_DECELERATE-减速状态
状态状态切换及其条件如图3-11所示:
)
)
图3-11 SpTA控制算法状态机状态切换图
SpTA算法同样是通过定时器来实现的,与S形曲线算法不同的是它没有使用定时器的PWM功能,仅仅是通过定时器定时中断来产生一个时间片,在定时器中断服务子程序中完
成上述算法,在需要时,通过控制GPIO产生一个步进脉冲。
SpTA与S型算法的比较:
从上面的两种算法可以看出,传统的S形曲线控制算法实现比较简单,但是它将要输出的脉冲频率(周期)和脉冲个数存储在RAM里,占用了一定的内存,且要想实现更好的控制效果,S形曲线的离散化程度越高,占用的RAM越大,如果要改变电机的运行速度曲线,需要重新计算每个阶段脉冲频率和脉冲个数,计算时使用了浮点数,运算量较大。
SpTA算法是根据用户输入的加速度和目标速度以及设定的总脉冲数,自行决定如何输出达到最佳运动效果的脉冲,它不需要占用额外的RAM来存储每个阶段脉冲频率和脉冲个数,算法实现基本上都是MCU“拿手”的加减法和移位运算,算法效率高,但是该算法为了达到较好的运动控制,需要一个时间片很小的定时中断来调整数据,这样在输出一个脉冲期间要频繁产生中断,尤其是在电机起步和停止的时候,脉冲频率低,但是定时器中断的次数很高,这样CPU的效率就会被定时器中断拉低。
从算法计算量、占用RAM大小、控制效果和CPU效率上,两种控制算法对比分析如表3.2所示,综合考虑二者的优缺点,本系统中对于试剂盘、样本盘、反应盘等负载较大的电机使用SpTA控制算法,其它负载使用S形曲线控制算法。
表3.2 步进电机S形曲线控制算法与SpTA控制算法比较分析
比较项S形曲线控制算法SpTA控制算法
算法计算量大且使用了浮点数小且使用的是整形数
占用RAM大小较多,与控制效果相关很少,与控制效果无关
控制效果由离散化程度决定自适应,效果较好
CPU效率中断次数=步进数,CPU效率
较高中断次数>>步进数,CPU效
率较低。