液压管道冲洗规范(力士乐内部资料
液压管道循环酸洗、油冲洗技术综述

液压管道循环酸洗、油冲洗技术综述液压管道在长期使用过程中,由于介质的腐蚀、沉积物的积累以及摩擦磨损等原因,往往会导致管道内部出现生锈、结垢等问题,进一步影响管道的正常运行和寿命。
为了解决这些问题,液压工程中常常运用循环酸洗和油冲洗技术。
本文就对液压管道循环酸洗、油冲洗技术进行综述。
液压管道酸洗技术液压管道酸洗原理液压管道通常采用酸洗的方法,其中最常用的是循环酸洗技术。
循环酸洗技术是通过对管道内部使用酸洗液进行旋转强制流动,使酸洗液在管道内能够充分接触管道表面,并能够去除管道内部的氧化铁锈、沉积物等杂质,从而达到对管道进行有效清洗和去腐蚀的目的。
循环酸洗工艺可以除去钢铁表面氧化物和油污等,改善金属表面状况、优化表面质量、加强表面粗糙度,有利于严密联接。
液压管道酸洗过程液压管道酸洗过程包括管道内部酸洗、中和、清洗、漂洗、除锈处理等环节。
在实际应用中,酸洗剂的类型和浓度、流量、流速、反应时间等也会因管道材质、壳体结构、管径大小以及管道使用情况的不同而有所不同。
液压管道酸洗注意事项在进行管道酸洗之前,首先需要根据管道的实际材质、管径大小等情况选择合适的酸洗液浓度和配方。
在酸洗过程中,也需要注意控制酸洗液的浓度和酸洗时间,避免管道因长时间酸洗而出现损坏、变形等问题。
另外,酸洗过后也需及时中和清洗管道内部,避免出现酸碱中和不均衡导致的二次腐蚀问题。
此外,在进行酸洗前还需做好防护措施,戴好防护胶手套,做好防护工作,避免因酸液对皮肤、眼睛等造成的刺激和损伤。
液压管道油冲洗技术液压管道油冲洗原理在液压管道酸洗的基础之上,通常还会采用油冲洗技术,目的是清除管道内残留的杂质以及防止其再次沉积。
油冲洗技术是利用高速旋转的油涡片冲刷管道内壁表面,利用力的热与化学等特性去除管道内的污物或脱落的附着物。
同时通过油的切割作用,也能够有效去除摩擦产生的金属粉屑或铁锈等杂质,从而保证管道内部的清洁度和液压系统的正常运行。
液压管道油冲洗过程液压管道油冲洗过程由串联油箱、泵组、油冲系统和过滤系统组成。
液压和润滑管道的酸洗和油冲洗作业指导书

本作业指导书适用于液压和润滑管道的酸洗和油(液)冲洗。
1. 管道酸洗
1.1管道酸洗一般规定
1.1.1液压、润滑管道的除锈应采用酸洗法。
管道酸洗应在管道配制完成,且具备=冲洗条件后进行。
对涂有油漆的管子,在酸洗前应把油漆除净。
1.2 油库或液压站内的管道,宜采用槽式酸洗法;从油库或液压站至使用点或工作缸的管道,可采用循环酸洗法。
酸洗液的配方,当设计或外商有明确规定时,按规定执行;无明确规定时按表1或表2选用。
槽式酸洗法脱脂、酸洗、中和、钝化液配合比表1
1.1.3酸洗应严格按所选配方、要求进行。
液压、稀油润滑、干油润滑管道脱脂、酸洗、中和、钝化记录(2/4)
酸洗记录
工程名称:工程编号:
工程部位名称:施工单位:
记录人:制表日期:年月日。
液压管清洗流程

液压管路冲洗程序Hydraulic pipes flushing procedure1.目的/Purpose为了保证公司产品的液压系统正常工作,在系统投入使用之前,对系统进行全面、细致的油冲洗,以保证液压系统清洁度---清除系统制作、安装过程中潜伏在系统内部的污染。
In order to the hydraulic system is running smoothly, we need flush the inside of hydraulic pipes and to clean the dirty.2.冲洗的理论依据/ The theories of flushing2.1.层流和紊流概念/ Laminar flow and Turbulent flow层流是各流体微团彼此平行地分层流动,互不干扰与混杂。
此时,液体流速较低,粘性力起主导作用;Laminar flow: the fluid of stratified flow in parallel to each other, each other without mixed. At this point, the liquid flow rate is low, viscous force plays a leading role.紊流是各流体微团间强烈地混合与掺杂、不仅有沿着主流方向的运动,而且还有垂直于主流方向的运动。
此时,液体流速较高,惯性力起主导作用。
Turbulent flow is the fluid between strongly mixed micelle and doping, not only the mainstream direction of movement, but also in the direction perpendicular to the mainstream. At this point, the fluid velocity is higher; the inertial force plays a leading role.2.2.雷诺数概念/Reynolds number雷诺数(Reynolds number)一种可用来表征流体流动情况的无量纲数,以Re表示,Re=ρvd/η,其中v、ρ、η分别为流体的流速、密度与黏性系数,d为一特征长度。
液压润滑管道循环冲洗要点
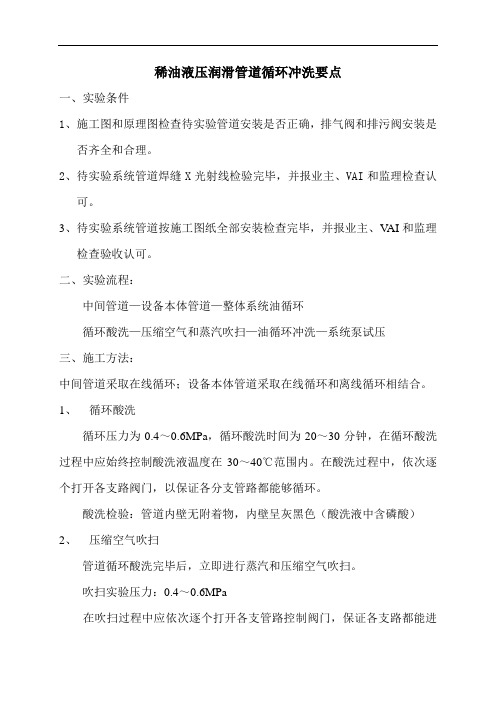
稀油液压润滑管道循环冲洗要点一、实验条件1、施工图和原理图检查待实验管道安装是否正确,排气阀和排污阀安装是否齐全和合理。
2、待实验系统管道焊缝X光射线检验完毕,并报业主、VAI和监理检查认可。
3、待实验系统管道按施工图纸全部安装检查完毕,并报业主、V AI和监理检查验收认可。
二、实验流程:中间管道—设备本体管道—整体系统油循环循环酸洗—压缩空气和蒸汽吹扫—油循环冲洗—系统泵试压三、施工方法:中间管道采取在线循环;设备本体管道采取在线循环和离线循环相结合。
1、循环酸洗循环压力为0.4~0.6MPa,循环酸洗时间为20~30分钟,在循环酸洗过程中应始终控制酸洗液温度在30~40℃范围内。
在酸洗过程中,依次逐个打开各支路阀门,以保证各分支管路都能够循环。
酸洗检验:管道内壁无附着物,内壁呈灰黑色(酸洗液中含磷酸)2、压缩空气吹扫管道循环酸洗完毕后,立即进行蒸汽和压缩空气吹扫。
吹扫实验压力:0.4~0.6MPa在吹扫过程中应依次逐个打开各支管路控制阀门,保证各支路都能进行吹扫。
直到将管道内的残留酸液全部吹出,管道内壁吹干,并在出口处用白布检查目测无可见的污物即可认为吹扫合格。
3、稀油系统油循环冲洗实验管道吹扫实验合格后,应立即进行油循环冲洗实验。
实验介质:N22#机械油(应无杂质和水分)冲洗实验压力:1.0~1.2MPa冲洗流量:400L/min冲洗油温度:40℃~60℃过滤方式:回油过滤检验标准:清洁度NAS7级,检验方法用颗粒计数器进行检查。
拆除实验管道连接的所有阀台阀块的接口法兰,将阀块移走后,开始循环时使用25μ和15μ的滤芯,当冲洗油清洁度达到NAS8级时更换为10μ和5μ滤芯进行循环,直到冲洗油清洁度达到NAS7级要求。
4、液压系统油循环冲洗实验每个液压系统分为液压站到阀台前和阀台后到用户点两部分完成实验。
实验介质:N22#机械油(应无杂质和水分)冲洗实验压力:1.0~1.2MPa冲洗流量:400L/min冲洗油温度:40℃~60℃过滤方式:回油过滤拆除实验管道连接的所有阀台阀块的接口法兰,将阀块移走后,开始循环时使用25μ和15μ的滤芯,当冲洗油清洁度达到NAS8级时更换为10μ和5μ滤芯进行循环,直到冲洗油清洁度达到NAS6级。
液压系统管道的冲洗要领
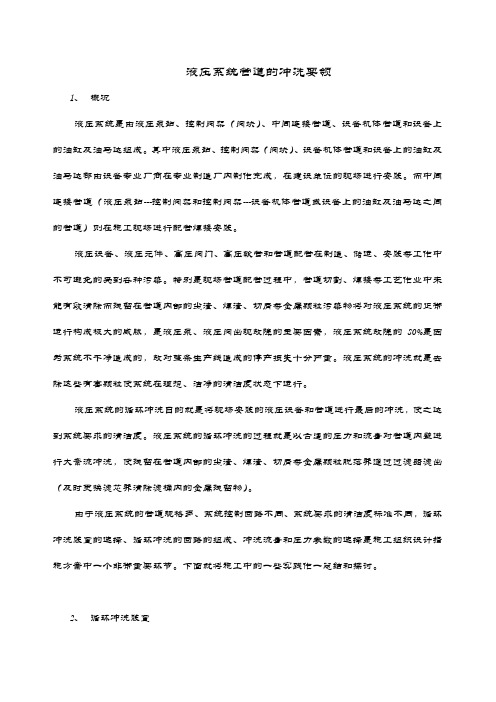
液压系统管道的冲洗要领1、概况液压系统是由液压泵站、控制阀架(阀块)、中间连接管道、设备机体管道和设备上的油缸及油马达组成。
其中液压泵站、控制阀架(阀块)、设备机体管道和设备上的油缸及油马达都由设备专业厂商在专业制造厂内制作完成,在建设单位的现场进行安装。
而中间连接管道(液压泵站---控制阀架和控制阀架---设备机体管道或设备上的油缸及油马达之间的管道)则在施工现场进行配管焊接安装。
液压设备、液压元件、高压阀门、高压软管和管道配管在制造、储运、安装等工作中不可避免的受到各种污染。
特别是现场管道配管过程中,管道切割、焊接等工艺作业中未能有效清除而残留在管道内部的尘渣、焊渣、切屑等金属颗粒污染物将对液压系统的正常运行构成极大的威胁,是液压泵、液压阀出现故障的主要因素,液压系统故障的80%是因为系统不干净造成的,故对整条生产线造成的停产损失十分严重。
液压系统的冲洗就是去除这些有害颗粒使系统在理想、洁净的清洁度状态下运行。
液压系统的循环冲洗目的就是将现场安装的液压设备和管道进行最后的冲洗,使之达到系统要求的清洁度。
液压系统的循环冲洗的过程就是以合适的压力和流量对管道内壁进行大紊流冲洗,使残留在管道内部的尘渣、焊渣、切屑等金属颗粒脱落并通过过滤器滤出(及时更换滤芯并清除滤桶内的金属残留物)。
由于液压系统的管道规格多、系统控制回路不同、系统要求的清洁度标准不同,循环冲洗装置的选择、循环冲洗的回路的组成、冲洗流量和压力参数的选择是施工组织设计措施方案中一个非常重要环节。
下面就将施工中的一些实践作一总结和探讨。
2、循环冲洗装置循环冲洗装置一般采用独立的大流量高压冲洗装置或系统的工作泵站进行管道的循环冲洗作业。
独立的大流量高压冲洗装置的输出流量一般1000升/分以上,应由3-4台高压泵和1台低压泵组成,按照冶金液压系统的参数高压泵(31.5MPa)流量配置以250升/分、160升/分、100升/分、63升/分和低压泵(2.5MPa)400-600升/分可以组成不同的冲洗压力\流量的需要。
液压管路酸洗和循环冲洗的过程控制及检验

液压管路酸洗和循环冲洗的过程控制及检验执行标准∶《机械设备安装工程及验收通用规范》(GB 50231)《重型机械液压系统通用技术条件》(JB/T 6996)一,管路酸洗1.槽式酸洗:脱脂--水冲洗--酸洗--水冲洗--中和--钝化--水冲洗--干燥--喷防锈油(剂)--封口。
一次安装好的管路拆下来,置入酸洗槽,酸洗操作完毕并检验合格后,再将其二次安装。
此方法适用于管径较大的短管,直管,容易拆卸,管路施工量小的场合,液压站或阀站内的管道,法兰接头,短管路等均采用槽式酸洗法。
2.循环酸洗:水试漏--脱脂水冲洗--酸洗--中和--钝化--水冲洗--干燥喷防锈油(剂)。
条件允许,所有外部配管均推荐采用循环酸洗法进行酸洗。
组成回路的管道长度,可根据管径等现场实际情况确定,所有管路可以连成一个或多个回路,但单个回路不宜超过300m。
所选酸洗泵必须保证有足够大的流量,应使所有管道的内壁全部接触酸液且酸液出口呈紊流状态流出。
循环酸洗注意事项:(1)使用一台酸泵输送几种介质,因此操作时应特别注意,不能将几种介质混淆,严重时会造成介质浓度降低,甚至造成介质报废。
(2)循环酸洗应严格遵守工艺流程,统一指挥。
当前一种介质完全排出或用另一种介质顶出时,应及时准确停泵,将回路末端软管从前一种介质槽中移出,放入下一工序的介质槽内。
然后启动酸泵,开始计时。
酸洗完成后,管道内部呈青黑色,具体时间可根据实际酸洗效果适当调整。
二,循环冲洗液压系统的管道在酸洗合格后应尽快采用系统所使用的同品质的工作介质进行冲洗,且宜采用循环方式冲洗,并应符合下列要求:(1)液压系统外部管道采用独立循环泵冲洗。
(2)复杂管路可适当分区对各部分进行冲洗。
(3)保证足够大的冲洗速度,应使液流呈紊流状态且应尽可能高。
(4)冲洗液为液压油时应时油温尽可能高,但不宜超过60°C。
(5)循环冲洗要连续进行,冲洗时间通常在72h以上。
冲洗过程宜采用改变冲洗方向或对管子焊接处反复进行敲打,振动等方法加强冲洗效果。
液压管道冲洗方案

液压管道冲洗方案(总2页)--本页仅作为文档封面,使用时请直接删除即可----内页可以根据需求调整合适字体及大小--液压管道冲洗方案现代化的大型联合制造,加工设备的越来越多采用电液控制。
液压系统中各种精密阀体得到广泛应用。
液压缸和液压马达由于工作推力增大而要求配合更精密,内漏更少,为保证系统安全运行,必须有效的清除液压管道中的污垢,以避免污垢进入阀体,造成阀卡死,液压缸拉伤,执行失误等事故。
液压管道冲洗方案有很多种,根据我们公司多年来的经验,我们一直采用管道油冲洗方案,操作方便,实用,清洗的效果好。
具体措施如下:(一)连接及检验方式:1、油冲洗时用机床动力油箱;并根据现场实际管道的管径及长度采用分组串联方式连接循环管路。
2、油冲洗是为了除去管路系统中的异物,防止管道受污染和使用油变质,导致液压系统工作性能差;并保证液压系统的比例阀及油缸等在系统工作中不致出现机构异常磨损、卡阻现象,以及过滤器堵塞现象。
(二)、冲洗前的准备:1、清除油箱内的杂物、碎片,确保油箱密封,以免污染物进入。
2、检查有无元件损坏,特别是压力表、温度计、液位计、空气滤清器等。
3、检查有无泄漏,如有必须预先处理。
4、油泵电机联轴器连接是否妥当。
(三)、开始冲洗:1、将管道通过软管与钢管短接,构成油洗回路。
沿着循环冲洗方向,管路的管径,由粗到细顺序连接,避免循环回路产生阻力,而且每个回路都要控制流量,以保证每根管内壁完全接触油液。
2、确认冲洗参数,冲洗介质要符合要求(依据GB/T14039-2002,达到NAS7),注意冲洗流量要大,形成紊流状态,保证管道内壁进行充分冲洗。
紊流最小流速V(m/s),V=×(μ/d)3、式中:μ——冲洗油的运动粘度,d——管内径,cm3、循环冲洗过程中定期顺着介质流向敲击管壁,特别是焊口、法兰、变径、三通、弯头等部位,加快冲洗速度,循环冲洗连续进行,并反复调压加强冲洗效果。
让油温在30℃—45℃之间变化,通过升/降温,使管路热胀冷缩,脏物便于脱落。
液压管路临时冲洗具体步骤
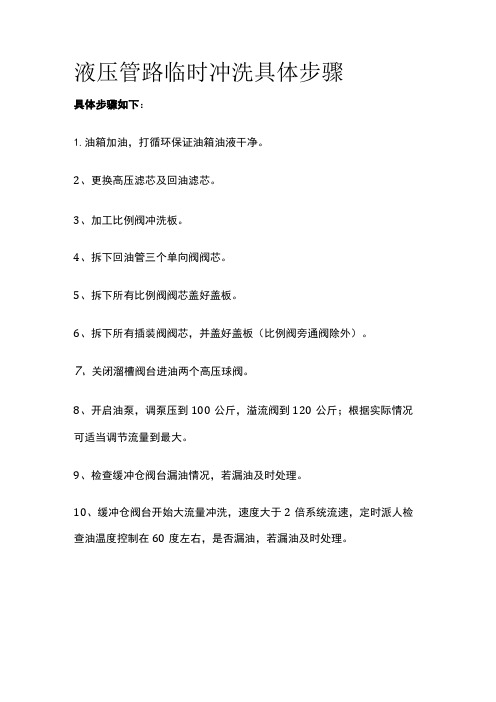
液压管路临时冲洗具体步骤具体步骤如下:1.油箱加油,打循环保证油箱油液干净。
2、更换高压滤芯及回油滤芯。
3、加工比例阀冲洗板。
4、拆下回油管三个单向阀阀芯。
5、拆下所有比例阀阀芯盖好盖板。
6、拆下所有插装阀阀芯,并盖好盖板(比例阀旁通阀除外)。
7、关闭溜槽阀台进油两个高压球阀。
8、开启油泵,调泵压到100公斤,溢流阀到120公斤;根据实际情况可适当调节流量到最大。
9、检查缓冲仓阀台漏油情况,若漏油及时处理。
10、缓冲仓阀台开始大流量冲洗,速度大于2倍系统流速,定时派人检查油温度控制在60度左右,是否漏油,若漏油及时处理。
12、冲洗20小时后关闭油泵,用堵头堵住缓冲仓进油管,必要时检查滤芯破损情况。
13、打开溜槽阀台球阀,开启油泵。
14、检查溜槽阀台漏油情况,若漏油及时处理。
15、溜槽阀台开始大流量冲洗,速度大于2倍系统流速,定时派人检查油温度控制在60度左右,是否漏油,若漏油及时处理。
16、冲洗过程中,派专人对管路用木棒敲击加速冲洗速度,尤其注意管路弯头、接头等位置。
17、冲洗20小时后关闭油泵,用堵头堵住缓冲仓进油管,关闭溜槽阀台进油两个高压球阀,必要时检查滤芯破损情况。
18、蓄能器5个一组开启到泄压状态,开启油泵,注意观察压力、温度,必要时可停泵。
19、检查缓冲仓阀台及蓄能器漏油情况,若漏油及时处理。
20、蓄能器管路开始大流量冲洗,速度大于2倍系统流速,定时派人检查油温度控制在60度左右,是否漏油,若漏油及时处理。
22、切换冲洗20小时后关闭油泵。
23、用煤油清或者柴油清洗好比例阀进行安装,注意保持阀台清洁避免异物掉落。
24、用煤油或者柴油清洗好插装阀进行安装,注意保持阀台清洁避免异物掉落。
25、拆除缓冲仓进油管堵头,注意保持阀台清洁避免异物掉落。
26、检查更换新滤芯,注意保持清洁避免异物掉落。
27、用煤油或者柴油清洗、安装好回油管三个单向阀阀芯,注意保持清洁避免异物掉落。
28、检查球阀及蓄能器泄压阀是否开关到位。
- 1、下载文档前请自行甄别文档内容的完整性,平台不提供额外的编辑、内容补充、找答案等附加服务。
- 2、"仅部分预览"的文档,不可在线预览部分如存在完整性等问题,可反馈申请退款(可完整预览的文档不适用该条件!)。
- 3、如文档侵犯您的权益,请联系客服反馈,我们会尽快为您处理(人工客服工作时间:9:00-18:30)。
FLUSHING HYDRAULIC SYSTEM FLUSHING HYDRAULIC SYSTEM
During the assembly and installation of extensive hydraulic system with many pipe runs ,it is easy possible for dirt and other contamination to find their way into the pipes and other items of equipment. Therefore , it is necessary with such system to flush out all the contamination ,so that it cannot have an adverse effect on the operation and life of the equipment.
Flushing involves circulating hydraulic fluid through the system at high speed. The fast-flowing fluid carries the particles of dirt along with it to where they can eventually be removed in a separate filter circuit.
The duration and intensity of flushing depend on the cleanliness of system required.
1. Preparing the System for Flushing
Any part of the system that could be damaged by the flushing must either be replaced by suitable device or be by-passed using pipes or hoses. If necessary , isolate certain units of the system and flush them individually.
Venting valves must be provided at high points in the pipework system in order to be certain that the pipes and equipment are completely full of fluid.
Drains must be provided at low points an in dead legs so that any dirty fluid can be drained off.
2. Flushing Unit
Flushing unit comprises pumps , heater, filters , tank and the necessary connections. The pumps must be fitted with adjustable pressure relief valves which must be set to a pressure which ensure that the full volumetric flow of the pumps is being passed through the parts being flushed. The capacity of the tank should be at least three times the pump delivery per minute. It should also be at least equal in capacity to the capacity of the installation being flushed.
3. Flushing Velocity and Temperature
Flushing Velocity and temperature should be as high as possible for the quick and effective flushing of the hydraulic system.
Practical experience has shown that the temperature should be higher than the operating temperature if possible. In the case od mineral oils 60 ℃is recommended. The flow velocity should be at least twice that during normal operation of the installation and the flow should be in turbulent range at all points.
The minimun volumetric flow of fluid through a pipe necessary to achieve turbulent flow conditions is defined as :
V ×d
Re = ------------- ≥4000
γ
Q ≥0.9 ×γ×d
Where Re = Reynold ‘s number
V = Flow velocity
Q = V olumetric flow in L / min
d = Insid
e diameter o
f pipe in mm
γ= Viscosity in mm2 / s
4. Flushing Fluid
The type of flushing fluid used must be compatible with the fluid eventually to be used in the system and with the materials used in the system ,especially the seals . Although the same fluid to be used subsequently can be used for flushing , a lower viscosity flushing fluid with no expensive additives can flush a system more quickly and more cheaply.
5. The Flushing Procedure
The flushing fluid should be introduced into the tank of the flushing unit through a filter.
Then heat the fluid to the required temperture and start the flushing pump . Ensure that the hydraulic system is properly vented .
While flushing is in progress keep a close watch on the clogging indicators of the filters . so that the elements can be changed or cleaned at the right time .
It is advisable to reverse the direction of flow after about an hour of flushing . Flushing should be continued untill the filter blockage indicators have been showing nothing for more than an hour . The flow should be reversed again . Take fluid sample from the system and see whether the required cleanliness of fluid has been achieved.
Make sure that all circuits comprising the hydraulic system are flushed .
When flushing is complete ensure that residual fluid is removed from any dead legs .
Obviously ,any by-passes and other auxiliary devices that have been fitted solely for the purposes of flushing must ben removed again afterwards. So that the hydraulic system is then restored to its fully functioning state .
If the system is not to be filled with fluid for some time before the final commissioning is undertaken it might be necessary to flush the system through with an anti-corrosion fluid .。