目视化管理案例
5S及目视化标准案例

5.记录物品现况板的场所号码,要按照搁板标示的 编号的顺序来记录(01-M-01)。
照片
责任人:
23. 储物柜标示标准
23. 储物柜标示标准
办公室5S管理标识
名称:工具柜
17mm
对象
现场及办公室使用的私物柜、更衣柜、鞋柜等。
类别:
目的 使车间现场私物柜标示统一,明确责任人。
第一层:常用办公用品 73mm
15.货架定位标准
15.货架定位标准
货架 货架
对象 目的 标准
对所有不经常移动的物品。如(备品、备件、货架 等)
对所有不经常移动的物品原位置进行标识,确保物 物有归处,使整顿成为习惯化。
1.定位线为黄色线条宽度5cm,规划区域长度 20cm,宽度已实际货架宽度规划,样式为C型定 位线 2.规划原则:货架两侧布置
22.库房货位标示标准
22.库房货位标示标准
对象 原材料、消耗品、备品。
目的 36mm
明确物品的三定:“定品、定位、定量”,来缩短 查找时间和削减库存,谋求有计划的采购物资。
96mm
标准 1.制作物品现况板,单面印刷。
2.大规格:长130mmx宽70mm,小规格:长
96mmx宽36mm。
3.附着在物品前面(搁板下面)。 4.按照部门的编号顺序记录搁板标示(生-M- 01)。
附录一
5S及目视化 标准案例
1.车间标线使用颜色标识标准
1.车间标线使用颜色标识标准
对象 目的 标准
车间涉及到颜色管理物品等
用颜色做目视化管理,一目了然
1.标识方法:物品定位线宽5cm、通道线10cm、 白色斑马线15cm
2.绿色:成品区、任何好的来料、成品、工具柜、 文件柜、指引箭头等。
坚持现场管理标准化案例

坚持现场管理标准化案例坚持现场管理标准化案例一、目视化管理某制造企业通过对现场进行目视化管理,将操作流程、设备状态、安全警示等信息以直观的方式呈现给员工,使员工能够快速了解现场情况,提高工作效率。
例如,在设备上张贴绿色运行指示灯,当设备运行正常时,指示灯亮起,员工可以直观地了解设备状态。
二、标准化操作某医疗机构通过对现场操作进行标准化管理,确保每一步操作都符合规范要求,提高了工作效率和安全性。
例如,在消毒环节中,规定消毒剂的种类、浓度、使用方法等,使每次消毒都能够达到相同的标准,保证了医疗质量。
三、设备维护保养某化工企业通过定期对设备进行维护保养,延长了设备的使用寿命,提高了设备效率。
例如,制定设备的日检、周检、月检计划,对设备进行定期检查和维护,确保设备始终处于良好状态。
四、环境卫生管理某餐饮企业通过对现场环境进行卫生管理,确保食品加工过程的清洁卫生,提高了食品安全质量。
例如,在厨房设置消毒设施和通风系统,对加工区域进行定期消毒,同时保持空气流通,减少细菌滋生。
五、安全措施某建筑工地通过加强现场安全措施,确保员工的人身安全。
例如,在施工现场设置安全围栏、警示标志和安全通道等,对危险区域进行隔离和警示,同时加强员工安全培训,提高员工的安全意识。
六、培训与教育某服务企业通过对员工进行培训和教育,提高员工的专业技能和服务质量。
例如,定期开展礼仪培训、沟通技巧培训等课程,使员工能够更好地与客户沟通交流,提高客户满意度。
同时加强企业文化建设。
七、质量管理体系某电子产品制造企业通过建立完善的质量管理体系,确保产品的质量和可靠性。
例如制定严格的质量检测流程和技术标准对每个生产环节进行控制和监督形成完整的质量检验链条针对每一个生产批次都有明确的质量检测标准和要求所有质量数据都会被详细记录下来并进行分析以便在第一时间发现并解决问题。
八、班组建设与企业文化某制造企业通过加强班组建设和企业文化建设培养团队合作精神和管理理念激发员工的积极性和创造力推动企业发展.例如各班组定期召开班前会进行工作安排和交底让每个员工了解自己的工作内容和要求形成互相帮助、共同进步的良好氛围同时通过开展多样化的文体活动增强员工的凝聚力和归属感让员工更好地融入到企业大家庭中来.此外还通过制定合理的奖惩机制激励员工努力工作并树立良好的企业形象和文化氛围让员工自觉遵守企业规章制度并更好地为企业发展贡献力量.。
3办公区域目视化管理实战案例

3办公区域目视化管理实战案例近年来,随着信息化技术的不断发展,办公区域目视化管理也得到了广泛应用。
目视化管理不仅提高了工作效率,还提升了办公环境的舒适度。
下面将介绍三个办公区域目视化管理的实战案例。
案例一:会议室目视化管理公司的会议室经常因为预约混乱而导致浪费了大量的时间和精力。
为了解决这一问题,公司引入了目视化管理技术。
他们在会议室门口安装了一个数字显示屏,用来显示会议室的预约情况。
每个员工都可以通过这个屏幕查看会议室的预约情况,并且可以直接在屏幕上进行预约操作。
这样一来,员工们就可以很方便地查看会议室的使用情况,并且可以及时地进行预约操作,避免了预约混乱的问题。
此外,公司还在会议室内部放置了一个大屏幕,用来显示会议的议程和相关信息,方便参会人员了解会议的进展情况。
案例二:办公室设备目视化管理公司的办公室拥有大量的设备和办公用品,例如电脑、打印机、文件柜等。
由于设备的数量庞大,很容易发生遗失或损坏的情况,给公司的工作带来了很大的困扰。
为了解决这一问题,公司引入了目视化管理技术。
他们在办公室的墙壁上安装了一块设备管理屏幕,用来显示办公室设备的位置和使用情况。
每个员工都可以通过这个屏幕查询办公设备的位置,并且可以将设备借用信息输入到屏幕上。
这样一来,员工们就可以很方便地找到需要的设备,并且可以对设备的使用情况进行实时记录,避免了设备遗失或损坏的问题。
案例三:员工任务目视化管理公司的员工经常因为任务安排不清晰而导致工作效率低下。
为了解决这一问题,公司引入了目视化管理技术。
他们在办公区域的公共墙上悬挂了一个任务分配屏幕,用来显示员工的任务安排和进度情况。
每个员工都可以通过这个屏幕查询自己的任务,并且可以将任务进度输入到屏幕上。
此外,公司还在员工的工位上放置了一个个人任务看板,用来显示员工的任务安排和重点工作。
这样一来,员工们就可以清晰地了解自己的任务安排和进度情况,并且可以根据任务看板上的信息有针对性地进行工作,提高了工作效率。
目视化管理案例

目视化管理案例目视化管理是一种以视觉化的形式来管理和监控项目进展和绩效的管理方法。
下面是一个目视化管理案例。
在某公司的软件开发项目中,项目经理采用了目视化管理的方法来监控项目进展和绩效。
项目经理在项目会议室的大屏幕上设置了一个任务看板,用来展示项目的各个任务和其进度。
任务看板分为多个列,包括待办、进行中和已完成。
每个任务都用一个卡片来表示,卡片上包括任务名称、责任人、预计完成时间和实际完成时间等信息。
当一个任务还未开始时,它就会被放置在待办列;当一个任务正在进行中时,它就会被移动到进行中列;当一个任务完成时,它就会被移动到已完成列。
每天早上,整个团队都会在会议室里进行每日站会。
在会议室里,项目经理会带领团队成员来更新任务看板。
每个团队成员需要报告自己的任务进展情况,例如完成了多少工作量,是否遇到了问题等等。
项目经理会在任务看板上根据团队成员的报告调整卡片的位置,以反映最新的任务进展。
通过任务看板,项目经理和团队成员可以一目了然地了解项目的整体进展。
如果某个任务拖延,项目经理可以及时发现并采取措施来解决问题,以避免进度延误。
如果某个团队成员遇到了问题,他可以在每日站会上及时报告,并与其他团队成员一起寻找解决方案。
另外,任务看板也可以帮助项目经理进行资源调配和风险管理。
通过观察任务看板,项目经理可以看到哪些任务正在拖延,哪些任务需要更多的资源支持。
项目经理还可以根据任务看板上的信息来识别潜在的风险,并制定相应的应对措施。
总之,通过目视化管理方法,项目经理能够更好地了解和监控项目的进展和绩效。
这不仅有助于提高项目的执行效率,还能够减少项目的风险,并及时发现和解决问题,从而保证项目的顺利进行。
公司目视化管理看板案例

公司目视化管理看板案例
公司目视化管理看板案例
在一家生产性企业中,为了更好地管理生产流程,提高生产效率和质量,引进了目视化管理看板。
该看板分为几个部分,包括生产计划、
生产进度、员工绩效、设备维修保养等内容。
首先,生产计划板块用于汇总生产计划并可随时进行修改。
该板块按日、周、月分别展示生产计划,以供生产部门按计划生产。
其次,生产进度板块用于记录生产进度情况。
这里展示了产品批次、
生产数量、生产时间等信息。
未完成的任务标记为红色,完成的任务
标记为绿色。
工作人员可以很容易地了解生产任务的进度并进行调整。
第三,员工绩效板块用于统计员工绩效并进行考评。
该板块展示了员
工姓名、岗位职责、绩效指标、完成情况等信息。
同时,该板块也是
对员工绩效的激励性考评,并能够对不合格的绩效进行跟踪和改进。
最后,设备维修保养板块用于记录设备的维修保养情况。
在该板块,
工作人员可以了解设备的保养时间、保养内容、保养人员等信息,并
及时安排设备维修保养工作以确保设备工作的稳定性和可靠性。
总体来看,通过引入目视化管理看板,生产部门能够更好地了解生产计划、生产进度和员工绩效,并更能够做到生产计划的有序管理。
同时,设备的维修保养也得到了全面的监控。
目视化管理的案例分析

案例总结:目视 化管理是一种有 效的管理方法, 能够提高生产效 率和质量,降低 成本和浪费。
案例二:某物流公司的目视化管理
案例背景:某物 流公司为了提高 工作效率和降低 成本,实施了目 视化管理。
目视化管理的应 用:通过使用颜 色、标签、标识 等方式,将工作 流程、设备状态 等信息清晰地展 示出来,方便员 工快速了解工作 情况。
提高员工素质
目视化管理有助于提高员工的专业技能 和知识水平,通过直观的展示和培训, 员工能够更好地理解和掌握工作流程和 操作规范。
目视化管理能够促进员工之间的沟通和 协作,通过明确的标识和指示,员工能 够更好地理解彼此的工作内容和进度, 从而更好地协作完成任务。
目视化管理能够提高员工的安全意识,通 过直观的展示和提醒,员工能够更好地注 意安全问题和风险,从而减少事故的发生。
在教育机构的推广和应用
目视化管理在教育机构中的定义和作用 目视化管理在教育机构中的实施步骤和注意事项 目视化管理在教育机构中的成功案例和经验分享 目视化管理在教育机构中的未来发展趋势和前景展望
目视化管理的未来 发展
智能化目视化管理
定义:利用先进的 技术手段,如人工 智能、大数据等, 实现目视化管理的 智能化升级。
案例一:某制造企业的目视化管理
案例背景:某制 造企业通过实施 目视化管理,提 高了生产效率和 质量。
目视化管理实施 过程:该企业通 过制定目视化管 理方案,明确标 识和颜色标准, 将生产现场的各 项信息以直观的 方式呈现出来。
目视化管理效果: 实施目视化管理 后,该企业的生 产效率提高了 20%,质量缺陷 率降低了30%。
设计目视化工具:根据管理标 准,设计相应的目视化工具, 例如看板、标识牌、颜色管理 等。
现场目视化看板案例

现场目视化看板案例
一家生产汽车零部件的公司采用了现场目视化看板来管理其生产线。
该看板由一系列不同颜色的标识牌组成,每个颜色表示不同的信息。
首先,看板的绿色标识牌用于标识目标产量。
在生产线上的每个工位旁边都有一个绿色标识牌,上面写着该工位的目标产量。
这些目标产量是根据产品需求和生产能力进行设定的。
其次,看板的黄色标识牌用于标识实际产量。
每当一个工位完成了一个产品,工人会在黄色标识牌上记录实际产量。
这样,生产线上的每个工位的实际产量都可以清晰地被看到。
另外,看板的红色标识牌用于标识问题和停工原因。
如果一个工位出现了问题导致生产线停工,工人会将红色标识牌放在该工位旁边,并在上面写下停工原因。
这样,管理层可以及时了解到停工原因,并采取相应的措施。
此外,看板还包括蓝色标识牌用于标识工位的位置和名称,以及白色标识牌用于标识其他额外的信息,如质量指标和问题解决进展等。
通过使用现场目视化看板,该公司能够实时监控生产线的运行情况,及时发现和解决问题,提高生产效率和产品质量。
目视化管理标识牌案例
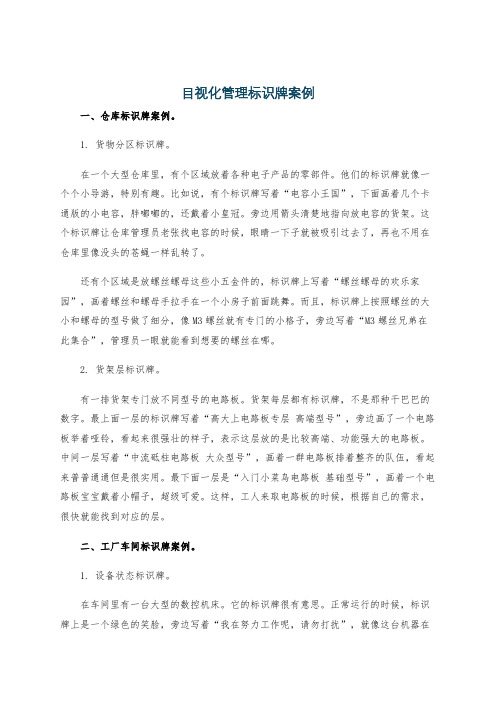
目视化管理标识牌案例一、仓库标识牌案例。
1. 货物分区标识牌。
在一个大型仓库里,有个区域放着各种电子产品的零部件。
他们的标识牌就像一个个小导游,特别有趣。
比如说,有个标识牌写着“电容小王国”,下面画着几个卡通版的小电容,胖嘟嘟的,还戴着小皇冠。
旁边用箭头清楚地指向放电容的货架。
这个标识牌让仓库管理员老张找电容的时候,眼睛一下子就被吸引过去了,再也不用在仓库里像没头的苍蝇一样乱转了。
还有个区域是放螺丝螺母这些小五金件的,标识牌上写着“螺丝螺母的欢乐家园”,画着螺丝和螺母手拉手在一个小房子前面跳舞。
而且,标识牌上按照螺丝的大小和螺母的型号做了细分,像M3螺丝就有专门的小格子,旁边写着“M3螺丝兄弟在此集合”,管理员一眼就能看到想要的螺丝在哪。
2. 货架层标识牌。
有一排货架专门放不同型号的电路板。
货架每层都有标识牌,不是那种干巴巴的数字。
最上面一层的标识牌写着“高大上电路板专层高端型号”,旁边画了一个电路板举着哑铃,看起来很强壮的样子,表示这层放的是比较高端、功能强大的电路板。
中间一层写着“中流砥柱电路板大众型号”,画着一群电路板排着整齐的队伍,看起来普普通通但是很实用。
最下面一层是“入门小菜鸟电路板基础型号”,画着一个电路板宝宝戴着小帽子,超级可爱。
这样,工人来取电路板的时候,根据自己的需求,很快就能找到对应的层。
二、工厂车间标识牌案例。
1. 设备状态标识牌。
在车间里有一台大型的数控机床。
它的标识牌很有意思。
正常运行的时候,标识牌上是一个绿色的笑脸,旁边写着“我在努力工作呢,请勿打扰”,就像这台机器在跟工人们友好地打招呼。
如果设备出故障了,标识牌就变成红色的哭脸,上面写着“我病啦,快叫维修师傅来”,还画了一个小扳手在旁边,特别形象。
工人们老远看到这个标识牌,就知道这台设备能不能用了,节省了很多时间,不用每次都走到设备跟前检查。
还有一个冲压设备,它的标识牌是个可以翻转的小牌子。
一面是“冲压中危险勿靠近”,用黄色的底色,上面画着大大的闪电符号,表示有危险。
- 1、下载文档前请自行甄别文档内容的完整性,平台不提供额外的编辑、内容补充、找答案等附加服务。
- 2、"仅部分预览"的文档,不可在线预览部分如存在完整性等问题,可反馈申请退款(可完整预览的文档不适用该条件!)。
- 3、如文档侵犯您的权益,请联系客服反馈,我们会尽快为您处理(人工客服工作时间:9:00-18:30)。
目视化管理案例
3.5.1车间标识
工厂建筑编号方法
工厂房间命名方法
门把手的标示方法
通道限高标示方法
车间温湿度管理
步行方向标示方法
出入门牌标示方法
门区域线标示方法
房间门管理责任者标示方法
楼梯引导标示方法
抽屉标示方法
文件夹摆放标示方法
电话机原位置标示方法
水杯保管方法
办公文具的保管方法
灯具开关的标示方法
3.5.2看板管理 企业文化宣传看板
目的宣传企业文化,让每个人能够清楚认识和掌握企业文化。
对象进入车间所有人员。
标准
打印板报,张贴在看板上面、及时更新内容。
效果展示
任职资格宣传看板
目的宣传公司最新任职资格体系,营造积极向上的竞争氛围,实力良好的企业形象和管理氛围。
对象进入车间所有人。
标准
打印板报,张贴在看板上面、及时更新内容。
效果展示
高管论坛宣传看板
目的宣传高级管理层最新动态,让一线员工及时了解。
对象进入车间所有人员
标准
打印板报,张贴在看板上面、及时更新内容。
效果展示
荣誉墙
目的评选并展示车间或工序的优秀员工的事迹,让有贡献的员工有成就感和自豪感,营造积极向上的竞争氛围,实力良好的企业形象和管理氛围。
对象生产部所有人员
标准
打印板报,张贴在看板上面、及时更新内容。
效果展示
车间规章制度宣传看板
目的即时宣传车间规章制度,让进入车间人员认识并掌握。
对象进入车间所有人员。
标准打印板报,张贴在看板上面、及时更新内容。
效果展示
精益项目宣传看板
目的宣传精益项目动态,让一线员工即时并了解精益项目。
对象进入车间所有人员。
标准打印板报,张贴在看板上面、及时更新内容。
效果展示
手机最新动态宣传看板
目的宣传公司最新手机动态,让员工有成就感和自豪感。
对象进入车间所有人员。
标准打印板报,张贴在看板上面、及时更新内容。
效果展示
员工关怀宣传看板
目的宣传部门员工关怀事项,让一线员工有归属感。
对象生产部所有员工。
标准打印板报,张贴在看板上面、及时更新内容。
效果展示
3.5.3设备标示
空调风口标示方法
管道流向标示方法
设备铭牌标示方法
电器警示灯标示方法
额定电压示方法
计量器界限范围标示方法
风扇通风口标示方法
开关控制范围标示方法
3.5.4物品材料
零件放置区标示方法
不良品标示方法
物品原位置标示方法
垃圾分类回收标示方法
垃圾分类回收标示方法
垃圾桶定位定量标示方法
台阶型架台保管标示方法
瓶装物品保管标示方法
半成品区标示方法
零件堆放限高线标示方法
私物柜标示方法
3.5.5工具器具
清扫工具保管标示方法
搬运工具保管标示方法
搬运工具保管标示方法
一般工具的标示方法
3.5.6安全警示
消防设施管理标示方法
消防设施位置标示方法
保护性指令标示方法
禁令性标示方法
电力安全标示方法
消防紧急疏散图
危险物品的保管
墙角墩柱标示方法
....................................分隔............................................分隔.............................
目视化管理案例
3.5.1车间标识
工厂建筑编号方法
门把手的标示方法
通道限高标示方法
车间温湿度管理
步行方向标示方法
地面导向标示方法
出入门牌标示方法
树木花草标示方法
门区域线标示方法
房间门管理责任者标示方法
楼梯引导标示方法
抽屉标示方法
文件夹摆放标示方法
电话机原位置标示方法
水杯保管方法
办公文具的保管方法
灯具开关的标示方法
3.5.2看板管理 企业文化宣传看板
目的宣传企业文化,让每个人能够清楚认识和掌握企业文化。
对象进入车间所有人员。
标准
打印板报,张贴在看板上面、及时更新内容。
效果展示
任职资格宣传看板
目的宣传公司最新任职资格体系,营造积极向上的竞争氛围,实力良好的企业形象和管理氛围。
对象进入车间所有人。
标准
打印板报,张贴在看板上面、及时更新内容。
效果展示
高管论坛宣传看板
目的宣传高级管理层最新动态,让一线员工及时了解。
对象进入车间所有人员
标准
打印板报,张贴在看板上面、及时更新内容。
效果展示
荣誉墙
目的评选并展示车间或工序的优秀员工的事迹,让有贡献的员工有成就感和自豪感,营造积极向上的竞争氛围,实力良好的企业形象和管理氛围。
对象生产部所有人员
标准
打印板报,张贴在看板上面、及时更新内容。
效果展示
车间规章制度宣传看板
目的即时宣传车间规章制度,让进入车间人员认识并掌握。
对象进入车间所有人员。
标准打印板报,张贴在看板上面、及时更新内容。
效果展示
精益项目宣传看板
目的宣传精益项目动态,让一线员工即时并了解精益项目。
对象进入车间所有人员。
标准打印板报,张贴在看板上面、及时更新内容。
效果展示
手机最新动态宣传看板
目的宣传公司最新手机动态,让员工有成就感和自豪感。
对象进入车间所有人员。
标准打印板报,张贴在看板上面、及时更新内容。
效果展示
员工关怀宣传看板
目的宣传部门员工关怀事项,让一线员工有归属感。
对象生产部所有员工。
标准打印板报,张贴在看板上面、及时更新内容。
效果展示
3.5.3设备标示
空调风口标示方法
管道流向标示方法。