半导体刻蚀
半导体刻蚀

九.颗粒沾污
等离子体带来的硅片损伤有时也由 硅片表面附近的等离子体产生的颗粒沾 污而引起。研究表明,由于电势的差异, 颗粒产生在等离子体和壳层的界面处。 当没有了等离子体时,这些颗粒就会掉 到硅片表面。颗粒沾污的控制可通过优 化刻蚀设备,合适的操作和关机,对被 刻蚀的膜层选用合适的化学气体来达到。
对于亚微米尺寸的图形来说,希望刻
蚀剖面是各向异性的,即刻蚀只在垂直于 硅片表面的方向进行(见图12.4),只有 很少的横向刻蚀。这种垂直的侧壁使得在 芯片上可制作高密度的刻蚀图形。各向异 性刻蚀对于小线宽图形亚微米器件的制作 来说非常关键。先进集成电路应用上通常 需要88到89º垂直度的侧壁。各向异性刻 蚀大部分是通过干法等离子体刻蚀来实现 的。
七.聚合物
聚合物的形成有时是有意的,是为 了在刻蚀图形的侧壁上形成抗腐蚀膜从 而防止横向刻蚀(见图12.8),这样做 能形成高的各向异性图形,因为聚合物 能阻挡对侧壁的刻蚀,增强刻蚀的方向 性,从而实现对图形关键尺寸的良好控 制。能否形成侧壁聚合物取决于所使用 的刻蚀气体类型。
八.等离子体诱导损伤
12.2 干法刻蚀
在半导体生产中,干法刻蚀是最主 要的用来去除表面材料的刻蚀方法。干 法刻蚀的主要目的是完整的把掩膜图形 复制到硅片表面上。硅片的等离子体刻 蚀过程见图12.9。
干法刻蚀相比与湿法腐蚀的优点是:
1. 刻蚀剖面是各向异性,具有非常 好的侧壁剖面控制;
干法刻蚀根据被刻蚀的材料类型来 分类。按材料来分,刻蚀主要分成三种: 金属刻蚀、介质刻蚀和硅刻蚀。
1. 介质刻蚀是用于介质材料的刻 蚀,如二氧化硅。
2. 硅刻蚀(包括多晶硅)应用于 需要去除硅的场合,如刻蚀多晶硅晶 体管栅和硅槽电容。
3. 金属刻蚀主要是在金属层上去 掉铝合金复合层,制作出互连线。
半导体八大工艺顺序
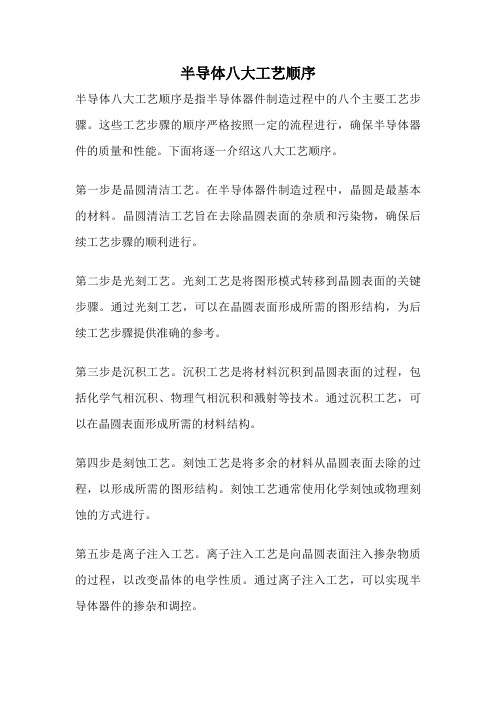
半导体八大工艺顺序半导体八大工艺顺序是指半导体器件制造过程中的八个主要工艺步骤。
这些工艺步骤的顺序严格按照一定的流程进行,确保半导体器件的质量和性能。
下面将逐一介绍这八大工艺顺序。
第一步是晶圆清洁工艺。
在半导体器件制造过程中,晶圆是最基本的材料。
晶圆清洁工艺旨在去除晶圆表面的杂质和污染物,确保后续工艺步骤的顺利进行。
第二步是光刻工艺。
光刻工艺是将图形模式转移到晶圆表面的关键步骤。
通过光刻工艺,可以在晶圆表面形成所需的图形结构,为后续工艺步骤提供准确的参考。
第三步是沉积工艺。
沉积工艺是将材料沉积到晶圆表面的过程,包括化学气相沉积、物理气相沉积和溅射等技术。
通过沉积工艺,可以在晶圆表面形成所需的材料结构。
第四步是刻蚀工艺。
刻蚀工艺是将多余的材料从晶圆表面去除的过程,以形成所需的图形结构。
刻蚀工艺通常使用化学刻蚀或物理刻蚀的方式进行。
第五步是离子注入工艺。
离子注入工艺是向晶圆表面注入掺杂物质的过程,以改变晶体的电学性质。
通过离子注入工艺,可以实现半导体器件的掺杂和调控。
第六步是热处理工艺。
热处理工艺是将晶圆置于高温环境中进行退火、烘烤或氧化等处理的过程。
通过热处理工艺,可以改善晶体的结晶质量和电学性能。
第七步是清洗工艺。
清洗工艺是在制造过程中对晶圆进行清洗和去除残留污染物的过程,以确保半导体器件的质量和可靠性。
第八步是封装测试工艺。
封装测试工艺是将完成的半导体器件封装成最终产品,并进行性能测试和质量检验的过程。
通过封装测试工艺,可以确保半导体器件符合规格要求,并具有稳定可靠的性能。
总的来说,半导体八大工艺顺序是半导体器件制造过程中的关键步骤,每个工艺步骤都至关重要,任何一环节的不慎都可能影响整个制造过程的质量和性能。
通过严格按照八大工艺顺序进行制造,可以确保半导体器件具有优良的性能和可靠性,从而满足现代电子产品对半导体器件的高要求。
半导体si刻蚀

borsh刻蚀结果前几天就已经出来了,找了您好几次,办公室都没人。
borsh1,2,3,分别对应RF=10W,30W,50W,ICP=150W;
borsh1,4,5,分别对应ICP=150W,225W,300W,RF=10W。
pressure=5,为之前一半。
时间为1.5min。
刻蚀气体仅为SF6。
RF的增大,导致SF6物理轰击加强,参与的化学反应明显降低。
ICP增大,相当于变相的降低RF,纵向刻蚀有些变化,但已经趋于饱和,
横向刻蚀相对于改变RF无明显变化。
看borsh1图片,可以很好的将线条下面硅去掉,不知这个是否满足工艺的需要?
图片见附近。
此外,关于ICP刻蚀机载片器,无论是2吋还是不规则的,牛津仪器均没有相关货品,他们也无法定做。
后来跟您说,将1/4硅片直接放在4吋硅片直接传送至反应腔体,1/4硅片在刻蚀的时候也不会移动。
但问题是将
1/4硅片放在整片硅片上于传送腔,传送腔抽真空时,两片之间会有空气,这样1/4硅片会发生明显位移至整片边缘。
所以此方案也是行不通的。
压力变大半导体刻蚀速率

压力变大半导体刻蚀速率引言半导体制造是现代电子产业中至关重要的一项技术。
在半导体制造的过程中,刻蚀是一种常用的工艺,用于在半导体材料上制作微细结构。
刻蚀速率是刻蚀过程中的一个重要参数,它决定了最终制作出的半导体器件的性能和质量。
然而,在实际制造过程中,压力的变化可能会对半导体刻蚀速率产生影响。
本文将对压力变化对半导体刻蚀速率的影响进行探讨。
压力对刻蚀速率的影响在半导体刻蚀过程中,刻蚀速率受到多种因素的影响,包括气体浓度、功率密度、温度等。
而压力则被认为是这些因素中最为重要的影响因素之一。
压力与气体浓度之间的关系压力对刻蚀速率的影响可以通过其与气体浓度之间的关系来理解。
根据气体动力学理论,当压力增大时,气体分子的平均自由程减小,分子之间的碰撞频率增加。
这使得更多的气体分子在单位时间内与半导体表面发生反应,从而增加了刻蚀速率。
压力与碰撞概率之间的关系压力的增大还会增加半导体表面受到气体分子碰撞的机会。
这种碰撞使得半导体表面的原子或分子从固态转移到气态,进而参与刻蚀过程。
因此,压力的增大可以增加碰撞概率,加速刻蚀速率的提高。
压力与副反应之间的关系此外,压力的变化还可能引起一些副反应的发生,从而对刻蚀速率产生影响。
例如,高压下,气体分子之间的相互作用增加,可能导致反应产物在表面发生吸附,并降低刻蚀速率。
不同的气体和反应体系对压力的敏感性也不同。
实验研究为了验证压力对半导体刻蚀速率的影响,研究者进行了一系列实验。
实验中,他们采用了不同的刻蚀系统,并通过调节压力的方法来模拟不同的工艺条件。
实验结果表明,在相同的刻蚀参数下,随着压力的增加,半导体刻蚀速率呈现出明显的增加趋势。
同时,通过对刻蚀后的半导体样品进行表征,发现刻蚀深度的增加与刻蚀速率的增加是一致的。
此外,实验还发现,不同的半导体材料对压力的敏感性存在差异。
不同工艺条件下,压力的增加对刻蚀速率的影响程度也有所不同。
结论压力的变化对半导体刻蚀速率有着明显的影响。
半导体制造工艺刻蚀
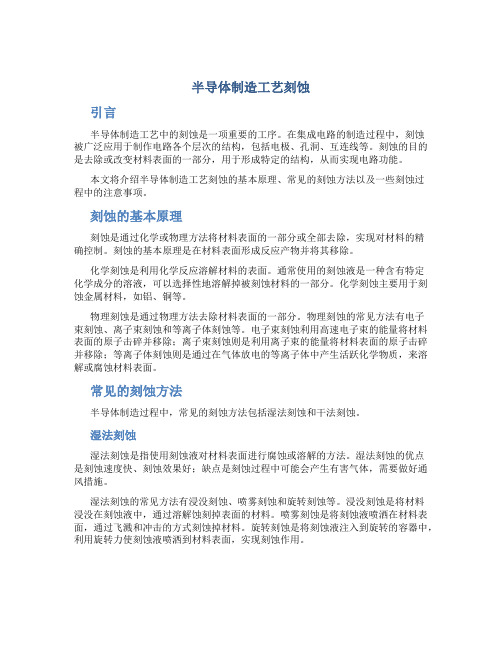
半导体制造工艺刻蚀引言半导体制造工艺中的刻蚀是一项重要的工序。
在集成电路的制造过程中,刻蚀被广泛应用于制作电路各个层次的结构,包括电极、孔洞、互连线等。
刻蚀的目的是去除或改变材料表面的一部分,用于形成特定的结构,从而实现电路功能。
本文将介绍半导体制造工艺刻蚀的基本原理、常见的刻蚀方法以及一些刻蚀过程中的注意事项。
刻蚀的基本原理刻蚀是通过化学或物理方法将材料表面的一部分或全部去除,实现对材料的精确控制。
刻蚀的基本原理是在材料表面形成反应产物并将其移除。
化学刻蚀是利用化学反应溶解材料的表面。
通常使用的刻蚀液是一种含有特定化学成分的溶液,可以选择性地溶解掉被刻蚀材料的一部分。
化学刻蚀主要用于刻蚀金属材料,如铝、铜等。
物理刻蚀是通过物理方法去除材料表面的一部分。
物理刻蚀的常见方法有电子束刻蚀、离子束刻蚀和等离子体刻蚀等。
电子束刻蚀利用高速电子束的能量将材料表面的原子击碎并移除;离子束刻蚀则是利用离子束的能量将材料表面的原子击碎并移除;等离子体刻蚀则是通过在气体放电的等离子体中产生活跃化学物质,来溶解或腐蚀材料表面。
常见的刻蚀方法半导体制造过程中,常见的刻蚀方法包括湿法刻蚀和干法刻蚀。
湿法刻蚀湿法刻蚀是指使用刻蚀液对材料表面进行腐蚀或溶解的方法。
湿法刻蚀的优点是刻蚀速度快、刻蚀效果好;缺点是刻蚀过程中可能会产生有害气体,需要做好通风措施。
湿法刻蚀的常见方法有浸没刻蚀、喷雾刻蚀和旋转刻蚀等。
浸没刻蚀是将材料浸没在刻蚀液中,通过溶解蚀刻掉表面的材料。
喷雾刻蚀是将刻蚀液喷洒在材料表面,通过飞溅和冲击的方式刻蚀掉材料。
旋转刻蚀是将刻蚀液注入到旋转的容器中,利用旋转力使刻蚀液喷洒到材料表面,实现刻蚀作用。
干法刻蚀干法刻蚀是指利用气体等离子体或物理方法对材料表面进行刻蚀的方法。
干法刻蚀的优点是刻蚀过程中不产生液体,可以避免污染问题;缺点是刻蚀速度较慢。
干法刻蚀的常见方法有等离子体刻蚀、离子束刻蚀和电子束刻蚀等。
等离子体刻蚀是通过在气体放电的等离子体中产生活跃化学物质,来溶解或腐蚀材料表面。
半导体刻蚀技术简介终稿

一、等离子体刻蚀技术的产生:在积体电路制造过程中,常需要在晶圆上定义出极细微尺寸的图案,这些图案主要的形成方式,乃是藉由刻蚀技术,将微光刻后所产生的光阻图案忠实地转印至光阻下的材质上,以形成积体电路的复杂架构。
因此蚀刻技术在半导体制造过程中占有极重要的地位。
广义而言,所谓的蚀刻技术,包含了将材质整面均匀移除及图案选择性部份去除的技术。
而其中大略可分为湿式蚀刻与干式蚀刻两种技术。
早期半导体制程中所采用的蚀刻方式为湿式蚀刻,即利用特定的化学溶液将待蚀刻薄膜未被光阻覆盖的部分分解,并转成可溶于此溶液的化合物后加以排除,而达到蚀刻的目的。
湿式蚀刻的进行主要是藉由溶液与待蚀刻材质间的化学反应,因此可藉由调配与选取适当的化学溶液,得到所需的蚀刻速率,以及待蚀刻材料与光阻及下层材质良好的蚀刻选择比(选择性)。
然而,随着积体电路中的元件尺寸越做越小,由于化学反应没有方向性,因而湿式蚀刻是各向同性的,此时,当蚀刻溶液做纵向蚀刻时,侧向的蚀刻将同时发生,进而造成咬边现象,导致图案线宽失真。
因此湿式蚀刻在次微米元件的制程中已被干式蚀刻所取代。
干式蚀刻通常指利用辉光放电方式,产生包含离子,电子等带电粒子及具有高度化学活性的中性原子与分子及自由基的电浆来进行图案转印的蚀刻技术。
由部份解离的气体及等量的带正,负电荷粒子所组成的等离子体被称为电浆。
蚀刻用的电浆中,气体的解离程度很低,其中所含的气体具高度的活性,它是利用外加电场的驱动而形成,并且会产生辉光放电现象。
自1970年代以来元件制造首先开始采用电浆蚀刻技术,对于电浆化学新的了解与认知也就蕴育而生。
在现今的积体电路制造过程中,必须精确的控制各种材料尺寸至次微米大小且具有极高的再制性,而由于电浆蚀刻是现今技术中唯一能极有效率地将此工作在高良率下完成,因此电浆蚀刻便成为积体电路制造过程中的主要技术之一。
影响电浆蚀刻特性好坏的因素包括了:1)电浆蚀刻系统的型态,2)电浆蚀刻的参数; 3)前制程相关参数,如光阻,待蚀刻薄膜之沉积参数条件,待蚀刻薄膜下层薄膜的型态及表面的平整度等。
半导体制造工艺刻蚀
半导体制造工艺刻蚀简介半导体制造工艺刻蚀是一种重要的半导体加工工艺,用于在半导体材料表面上制造出所需的结构和形状。
它通过使用化学溶液(湿刻蚀)或者物理干涉(干刻蚀)的方法,将半导体材料上的一部分材料予以去除,从而达到所需要的目的。
本文将介绍半导体制造工艺中的刻蚀过程、刻蚀方法以及常用的刻蚀设备。
刻蚀过程刻蚀是在半导体加工的各个阶段都会出现的过程,它的主要目的是在半导体材料上制造出所需的结构和形状。
刻蚀过程可分为湿刻蚀和干刻蚀两种主要方式。
湿刻蚀湿刻蚀是通过将半导体材料浸泡在特定的化学溶液中,利用化学反应将材料表面的一部分溶解掉的方法。
湿刻蚀的优点是刻蚀速度快,且刻蚀的方向性较好。
常用的湿刻蚀液有氢氟酸(HF)、氢氧化钠(NaOH)等。
干刻蚀干刻蚀是通过使用高能粒子束或者等离子体将半导体材料表面的一部分物质物理去除的方法。
干刻蚀可以分为离子束刻蚀(IBE)、反应离子束刻蚀(RIBE)、电子束刻蚀等。
与湿刻蚀相比,干刻蚀不需要使用化学溶液,刻蚀速度可调控,同时可以实现更高的精度和较好的控制。
刻蚀方法根据刻蚀的目的和要求,半导体制造过程中可用到多种刻蚀方法。
正式刻蚀正式刻蚀是通过在光刻胶层上涂覆光刻胶,利用光刻胶层的光学反应性将图案转移到光刻胶层上,再通过刻蚀工艺将光刻胶层中不需要的部分去除,形成所需的图形。
常用的正式刻蚀技术有湿法刻蚀和干法刻蚀。
刻蚀深度和形状受光刻胶特性、刻蚀时间和刻蚀条件等影响。
选择性刻蚀选择性刻蚀是通过针对不同材料的耐蚀性差异,选择合适的化学溶液或者物理干涉方式刻蚀特定的材料。
利用选择性刻蚀,可以在半导体制造过程中实现特定材料的去除或者保留,从而形成所需的结构。
深刻蚀深刻蚀是通过较长时间的刻蚀过程,将半导体材料的一部分刻蚀掉,形成较深的结构。
深刻蚀一般需要使用干刻蚀技术,并且需要较长的刻蚀时间和更高的功率,以确保刻蚀的深度和准确性。
刻蚀设备半导体刻蚀设备是用于实施刻蚀工艺的专用设备。
半导体工艺(第8章)刻蚀
典型的氧化去胶是H2SO4 :H2O2=3:1;
优点:
洗涤过程十分简单,即用去离子水冲洗即 可;
但要注意,氧化剂对衬底表面也有腐蚀作 用(十分轻微);
等离子体去胶
一种近几年发展起来的一种新工艺; 不需要化学试剂,也不需要加温,因此,
器件的结构性和金属铝层都不受影响; 这对提高产品质量和可靠性有好处;
干法刻蚀是指以气体为主要媒体的刻蚀技 术,晶圆不需要液体化学品或冲洗,刻蚀 过程在干燥的状态进出系统;
干法刻蚀种类
等离子体刻蚀(以化学反应为主,较少采
用)
物理刻蚀(物理溅射作用) 反应离子刻蚀(既有化学反应,又有物理
溅射)
等离子体概念:
当对一个低压强的容器内的气体施加电压 时,这些原本中性的气体分子将被激发或 离解成各种不同的带电粒子(离子、原子 团、分子及电子)。这些离子便称为等离 子体;
如果用CF4或其他含氟的气体来进行刻蚀, 则选择性较差;
以CF3为例, 对SiO2与Si的刻蚀选择性在 10以上,但是对Si3N4与Si的刻蚀选择性仅 在3~5之间,对Si3N4与SiO2的选择性仅在 2~4之间。故近期改用NF3的等离子体进行 刻蚀,结果比较理想;
多晶硅的刻蚀
多晶硅的刻蚀比Si3N4和SiO2要复杂得多; 多晶硅栅极本身由两层不同材料组成(多
原理:
系统中通入氧气,在外加高频电磁场作用 下,氧气电离,形成等离子区;
其中活化的原子态氧约占10%~20%,他们 活性活泼,氧化能力强,与光刻胶发生反 应;
一些易于氧化的材料,用湿法清洗很容易 被氧化,如果改用干法洗,就可以避免这 一缺陷;
目前用得最多的是干法刻蚀的反应室,可 以与淀积金属的薄膜反应实相连接,经干 法清洗以去除硅片表面氧化层后,可以保 持在真空状态下,再进行表面镀膜;
半导体器件工艺学之刻蚀
下游式刻蚀系统
离子束铣( Ion Milling) 是近年来发展较快的一种离 子剥离技术。该技术主要利用携带能量的离子轰 击靶材料所产生的物理溅射刻蚀效应
离子刻蚀速率表示如下: dh( H) / dt = R( H) / cos(H) = R( H) [ 1 + tan2( H) ]1/2
当离子束入射的角度较大时, 材料表面反射的离子束也增 多。因此, 随着角度H的增大 , 越来越少的离子渗入到材 料的有效表面。为保证离子 的有效渗入, 定义临界角Hc 。 离子束的溅射场与靶材料的 原子数Z 有关, 材料的原子数 Z 越高, 刻蚀速率越高; 反之 则越低。
本产品通过物理与化学相结合的方法,对很细的线条(亚微米以下)进行刻 蚀以形成精细的图形。 主要用于微电子、光电子、通讯、微机械、新材料、能源等领域的器件 研发和制造。
深层反应离子刻蚀(DRIE)
系统己经足以刻蚀深宽比超过50 的深槽硅结构,对于光阻的刻蚀 选择比己超过100:1,刻蚀深度均 匀度也可以控制在±3%以内。
中微发布Primo D-RIE刻蚀设备,面向22 纳米及以下工艺
中微半导体设备(上海)有限公司(以下简称“ 中微”)日前发布面向22纳米及以下芯片生产 的第二代300毫米甚高频去耦合反应离子刻 蚀设备--Primo AD-RIE。 2011年7月
Primo AD-RIE在促进中微第一代刻蚀设备技术创 新的同时,又大大扩大了其自身的加工领域。 该设备的主要部分是一组创新的少量反应台反应 器的簇架构,可以灵活地装置多达三个双反应台 反应器,以达到最佳芯片加工输出量。每个反应 器都可以实现单芯片或双芯片加工。独特的反应 器腔体设计融合了中微专有的等离子体聚焦和喷 淋头技术,确保了芯片加工的质量。Primo ADRIE的一些基本特征使其更具备28纳米以下关键刻 蚀加工的能力
半导体工艺干法刻蚀铝刻蚀
干法刻蚀之铝刻蚀在集成电路的制造过程中,刻蚀就是利用化学或物理方法有选择性地从硅片表面去除不需要的材料的过程。
从工艺上区分,刻蚀可以分为湿法刻蚀和干法刻蚀。
前者的主要特点是各向同性刻蚀;后者是利用等离子体来进行各向异性刻蚀,可以严格控制纵向和横向刻蚀。
干法的各向异性刻蚀,可以用表面损伤和侧壁钝化两种机制来解释。
表面损伤机制是指,与硅片平行的待刻蚀物质的图形底部,表面的原子键被破坏,扩散至此的自由基很容易与其发生反应,使得这个方向的刻蚀得以持续进行。
与硅片垂直的图形侧壁则因为表面原子键完整,从而形态得到保护。
侧壁钝化机制是指,刻蚀反应产生的非挥发性的副产物,光刻胶刻蚀产生的聚合物,以及侧壁表面的氧化物或氮化物会在待刻蚀物质表面形成钝化层。
图形底部受到离子的轰击,钝化层会被击穿,露出里面的待刻蚀物质继续反应,而图形侧壁钝化层受到较少的离子轰击,阻止了这个方向刻蚀的进一步进行。
在半导体干法刻蚀工艺中,根据待刻蚀材料的不同,可分为金属刻蚀、介质刻蚀和硅刻蚀。
金属刻蚀又可以分为金属铝刻蚀、金属钨刻蚀和氮化钛刻蚀等。
目前,金属铝作为连线材料,仍然广泛用于DRAM和flash等存储器,以及以上的逻辑产品中。
本文着重介绍金属铝的刻蚀工艺。
金属铝刻蚀通常用到以下气体:Cl2、BCl3、Ar、 N2、CHF3和C2H4等。
Cl2作为主要的刻蚀气体,与铝发生化学反应,生成的可挥发的副产物AlCl3被气流带出反应腔。
BCl3一方面提供BCl3+,垂直轰击硅片表面,达到各向异性的刻蚀。
另一方面,由于铝表面极易氧化成氧化铝,这层自生氧化铝在刻蚀的初期阻隔了Cl2和铝的接触,阻碍了刻蚀的进一步进行。
添加BCl3 则利于将这层氧化层还原(如方程式1),促进刻蚀过程的继续进行。
Al2O3 + 3BCl3→ 2AlCl3 + 3BOCl (1)Ar电离生成Ar+,主要是对硅片表面提供物理性的垂直轰击。
N2、CHF3和C2H4是主要的钝化气体,N2与金属侧壁氮化产生的AlxNy,CHF3和C2H4与光刻胶反应生成的聚合物会沉积在金属侧壁,形成阻止进一步反应的钝化层。
- 1、下载文档前请自行甄别文档内容的完整性,平台不提供额外的编辑、内容补充、找答案等附加服务。
- 2、"仅部分预览"的文档,不可在线预览部分如存在完整性等问题,可反馈申请退款(可完整预览的文档不适用该条件!)。
- 3、如文档侵犯您的权益,请联系客服反馈,我们会尽快为您处理(人工客服工作时间:9:00-18:30)。
2.氮化硅
在硅片制造过程中用到两种基本的 氮 化 硅 。 一 种 是 在 700~800℃ 下 用 LPCVD淀积的,另一种是在低于350℃ 下用PECVD淀积的。后一种氮化硅膜 的刻蚀速率较快。刻蚀氮化硅常用的主 要气体是CF4。
二.硅的干法刻蚀
1.多晶硅栅刻蚀 在MOS器件中,掺杂的LPCVD多晶 硅是用作栅极的导电材料。掺杂多晶硅线 宽决定了有源器件的栅长,并会影响晶体 管的性能(见图12.17)。多晶硅栅的刻蚀 工艺必须对下层栅氧化层有高的选择比并 具有非常好的均匀性和重复性。同时也要 求高度的各向异性,因为多晶硅栅在源/ 漏的注入过程中起阻挡层的作用。倾斜的 侧壁会引起多晶硅栅结构下面部分的掺杂
1. 介质刻蚀是用于介质材料的刻 蚀,如二氧化硅。 2. 硅刻蚀(包括多晶硅)应用于 需要去除硅的场合,如刻蚀多晶硅晶 体管栅和硅槽电容。 3. 金属刻蚀主要是在金属层上去 掉铝合金复合层,制作出互连线。
刻蚀可以分成有图形刻蚀和无图形 刻蚀。有图形的刻蚀采用掩蔽层(有图 形的光刻胶)来定义要刻蚀掉的表面材 料区域,只有硅片上被选择的这一部分 在刻蚀过程中刻掉。
12.2 干法刻蚀
在半导体生产中,干法刻蚀是最主 要的用来去除表面材料的刻蚀方法。干 法刻蚀的主要目的是完整的把掩膜图形 复制到硅片表面上。硅片的等离子体刻 蚀过程见图12.9。
干法刻蚀相比与湿法腐蚀的优点是: 1. 刻蚀剖面是各向异性,具有非常 好的侧壁剖面控制; 2. 好的特征尺寸(CD)控制; 3. 最小的光刻胶脱落或粘附问题; 4. 好的片内、片间、批次间的刻蚀 均匀性; 5. 较低的化学制品使用和处理费用
刻蚀多晶硅(或硅)通常是一个三 步工艺过程: 1)预刻蚀,用于去除自然氧化层、 硬的掩蔽层和表面污染物来获得均匀的 刻蚀; 2)接下来是刻至终点的主刻蚀。 这一步用来刻蚀掉大部分的多晶硅膜, 并不损伤栅氧化层和获得理想的各向异 性的侧壁剖面;
3)最后是过刻蚀,用于去除刻蚀残 留物和剩余多晶硅,并保证对栅氧化层 的高选择比。
干法等离子体反应器有下面不同的 类型: 一.圆筒式等离子体刻式机 (图12.10) 化学刻蚀,各向同性。 二.平板(平面)反应器 (图12.11) 物理和化学刻蚀,各向异性和各向 同性。 三.顺流刻式系统 (图12.12) 化学刻蚀,各向同性。
四.三极平面反应器(图12.13) 物理刻蚀,各向异性。 五.离子铣 (图12.14) 物理和化学刻蚀,各向异性。 六.反应离子刻蚀 (图12.15) 物理刻蚀,各向异性。 七.高密度等离子体刻蚀机 物理刻蚀,各向异性。
包含带能离子、电子和激发分子的等 离子体可引起对硅片上的敏感器件引起 等离子体诱导损伤。一种主要的损伤是 非均匀等离子体在晶体管栅电极产生陷 阱电荷,引起薄栅氧化硅的击穿。差的 设备或在优化的工艺窗口之外进行刻蚀 工艺会使等离子体变得不均匀。另一种 器件损伤是能量离子对曝露的栅氧化层 的轰击。等离子体损伤有时可以通过退 火或湿法化学腐蚀消除。
高密度等离子体刻蚀机中等离子体 通常处于磁场中。在等离子体刻蚀中采 用磁场的理由是: 1)产生的等离子体能更有效地获得 进入高深宽比窗口的高方向性低能离子 以及较少的硅片损伤; 2)等离子体密度较大,有更多的反 应基和带电粒子以增大刻蚀速率; 3)能减小硅片上的直流偏置电压, 从而可减少粒子轰击(或损伤)。
12.2.4 干法刻蚀的应用
一个成功的干法刻蚀要求: 1. 对不需要刻蚀的材料(主要是光 刻胶和下层材料)的高选择比; 2.获得可接受的产能的刻蚀速率; 3.好的侧壁剖面控制; 4.好的片内均匀性; 5.低的器件损伤; 6. 宽的工艺制造窗口。
一.介质的干法刻蚀
1.氧化物 刻蚀氧化物通常是为了制作接触 孔和通孔。氧化物等离子体刻蚀工艺 通常采用氟碳化合物化学气体。加入 缓冲气体用于稀释刻蚀气体的浓度可 以增加刻蚀的均匀性。
目前有以下几种高密度等离子体技术:
■ 电子回旋加速振荡(ECR)
■ 电感耦合等离子体(ICP)
■ 双等离子体源(DPห้องสมุดไป่ตู้)
■ 磁增强反应离子刻蚀(MERIE)
12.2.3 终点检测
干法刻蚀不同于湿法腐蚀之处在于它 对下面的材料没有好的选择比。基于此 原因,需要终点检测来监测刻蚀工艺并 停止刻蚀以减小对下面材料的过渡刻蚀 。终点检测系统测量一些不同的参数, 如刻蚀速率的变化、在刻蚀中被去除的 腐蚀产物的类型或在气体放电中活性反 应剂的变化(见图12.16)。用于终点检 测的一种方法是光发射谱。这一测量方 法集成在刻蚀腔体中以便进行实时监测
对于亚微米尺寸的图形来说,希望刻 蚀剖面是各向异性的,即刻蚀只在垂直于 硅片表面的方向进行(见图12.4),只有 很少的横向刻蚀。这种垂直的侧壁使得在 芯片上可制作高密度的刻蚀图形。各向异 性刻蚀对于小线宽图形亚微米器件的制作 来说非常关键。先进集成电路应用上通常 需要88到89º 垂直度的侧壁。各向异性刻 蚀大部分是通过干法等离子体刻蚀来实现 的。
六.残留物
刻蚀残留物是刻蚀以后留在硅片表面 不想要的材料。它常常覆盖在腔体内壁或 被刻蚀图形的底部。它的产生有多种原因, 例如被刻蚀膜层中的污染物、选择了不合 适的化学刻蚀剂(如刻蚀太快)、腔体中 的污染物、膜层中不均匀的杂质分布。刻 蚀残留物是IC制造过程中的硅片污染源, 为了去除刻蚀残留物,有时在刻蚀完成后 会进行过刻蚀。刻蚀残留物可以在去除光 刻胶的过程中或用湿法化学腐蚀去掉。
12.2.2 等离子体刻蚀反应器
一个等离子体干法刻蚀系统的基本 部件包括:发生刻蚀反应的反应腔、一 个产生等离子体的射频电源、气体流量 控制系统、去除刻蚀生成物和气体的真 空系统。刻蚀系统包括传感器、气体流 量控制单元和终点触发探测器。
在干法等离子体刻蚀中不同的控制参 数有:真空度、气体混合组份、气流流速、 温度、射频功率和硅片相对于等离子体的 位置。这些不同的参数之间的互作用是干 法刻蚀工艺控制器的功能。
三.金属的干法刻蚀
金属刻蚀的要求主要有以下几点:
1)高刻蚀速率(大于1000nm/min);
2)对下面层的高选择比,对掩蔽层 (大于4:1)和层间介质层(大于20:1); 3)高的均匀性,且CD控制很好,没 有微负载效应;
七.聚合物
聚合物的形成有时是有意的,是为 了在刻蚀图形的侧壁上形成抗腐蚀膜从 而防止横向刻蚀(见图12.8),这样做 能形成高的各向异性图形,因为聚合物 能阻挡对侧壁的刻蚀,增强刻蚀的方向 性,从而实现对图形关键尺寸的良好控 制。能否形成侧壁聚合物取决于所使用 的刻蚀气体类型。
八.等离子体诱导损伤
三.刻蚀偏差
刻蚀偏差是指刻蚀以后线宽或关键 尺寸间距的变化(见图12.5)。它通常 是由于横向钻蚀引起的(见图12.6), 但也能由刻蚀剖面引起。当刻蚀中要去 除掩膜下过量的材料时,会引起被刻蚀 材料的上表面向光刻胶边缘凹进去,这 样就会产生横向钻蚀。
计算刻蚀偏差的公式如下:
刻蚀偏差 = Wb ― Wa
其中,Wb =刻蚀前光刻胶的线宽, Wa =光刻胶去掉后被刻蚀材料 的线宽。
四.选择比
选择比指的是在同一刻蚀条件下一 种材料与另一种材料相比刻蚀速率快多 少。它定义为被刻蚀材料的刻蚀速率与 另一种材料的刻蚀速率的比(见图 12.7)。高选择比意味着只刻除想要刻 去的那一层材料。
对于被刻蚀材料和掩蔽层材料的选 择比SR可以通过下式计算:
12.1 刻蚀工艺
12.1.1 刻蚀工艺
在半导体制造中有两种基本的刻蚀 工艺:干法刻蚀和湿法腐蚀。在湿法腐 蚀中,液体化学试剂(如酸、碱和溶剂 等)以化学方式去除硅片表面的材料。
干法刻蚀是把硅片表面曝露于气态 中产生的等离子体,等离子体通过光刻 胶中开出的窗口,与硅片发生物理或化 学反应(或这两种反应),从而去掉曝 露的表面材料。 干法刻蚀根据被刻蚀的材料类型来 分类。按材料来分,刻蚀主要分成三种: 金属刻蚀、介质刻蚀和硅刻蚀。
九.颗粒沾污
等离子体带来的硅片损伤有时也由 硅片表面附近的等离子体产生的颗粒沾 污而引起。研究表明,由于电势的差异, 颗粒产生在等离子体和壳层的界面处。 当没有了等离子体时,这些颗粒就会掉 到硅片表面。颗粒沾污的控制可通过优 化刻蚀设备,合适的操作和关机,对被 刻蚀的膜层选用合适的化学气体来达到。
多晶硅刻蚀气体传统上是氟基气体, 在刻蚀硅的过程中氟原子起作用。采用 氯或溴化学气体可以产生各向异性刻蚀 和对氧化硅有好的选择比。
2.单晶硅的刻蚀
单晶硅刻蚀主要用于制作沟槽,如 器件隔离沟槽或垂直电容的制作。硅槽 的刻蚀要求对每一个沟槽都进行精确的 控制,要求有一致的光洁度、接近的垂 直侧壁、正确的深度和圆滑的沟槽顶角 和底角,因此需采用多步工艺,并对最 后一步进行优化。浅槽的刻蚀气体多用 氟气,深槽常使用氯基或溴基气体。
使用干法刻蚀也有一些缺点。主 要的缺点是对下层材料的差的刻蚀选 择比、等离子体带来的器件损伤和昂 贵的设备。
12.2.1 刻蚀作用
干法刻蚀系统中,刻蚀作用是通过 化学作用或物理作用,或者是化学和物 理的共同作用来实现的。在纯化学机理 中,等离子体产生的反应元素与硅片表 面的物质发生反应. 为了获得物理机理的刻蚀,等离子 体产生的带能离子(轰击的正离子)在 强电场下朝硅片表面加速,这些离子通 过溅射刻蚀作用去除未被保护的硅片
表面材料。这种机械刻蚀的好处在于 它很强的刻蚀方向性,从而可以获得高 的各向异性刻蚀剖面,以达到好的线宽 控制目的。这种溅射刻蚀速率高,然而 选择比差。另一个问题是被溅射作用去 除的元素是非挥发性的,可能会重新淀 积到硅片表面,带来颗粒和化学污染。
还有一种是物理和化学混合作用机 理,其中离子轰击改善化学刻蚀作用。刻 蚀剖面可以通过调节等离子体条件和气体 组分从各向同性向各向异性改变。这种物 理和化学混合作用机理刻蚀能获得好的线 宽控制并有不错的选择比,因而在大多数 干法刻蚀工艺中被采用。表12.2总结了化 学作用、物理作用和化学/物理结合作用 刻蚀中的不同刻蚀参数。