半导体制造工艺_11刻蚀
半导体工艺光刻+蚀刻 ppt课件
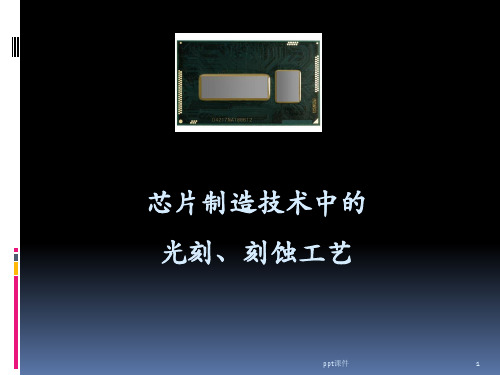
ppt课件
1
▪ 芯片制造工艺 ▪ 光刻工艺
▪ 刻蚀工艺
ppt课件
2
精品资料
ppt课件
4
光刻+蚀刻
最重要
决定着芯片的最小尺寸 制造时间的40-50% 制造成本的30%
ppt课件
5
玻璃模版 光刻胶膜
硅片
光刻 光化学反应
蚀刻
腐蚀
ppt课件
6
ppt课件
7
光刻原理
模版上的铬岛
紫外光
光刻胶的曝光区
光p刻ho胶tor层esist 氧化ox层ide
sil硅ico衬n 底substrate
使光衰弱的被曝光区
光刻胶上的阴影
岛
光刻胶层
窗口
氧化层 硅衬底
光刻胶显影后的最终图形
ppt课件
8
▪ 使用光敏材料(光刻胶)和可控制的曝 光在光刻胶膜层形成三维图形
▪ 在后续工艺(蚀刻)中,保护下面的材料
ppt课件
9
HMDS
清洗+喷涂粘附剂
光刻工艺步骤
紫外光
光刻胶
模版
旋转涂胶
软烘
对准和曝光
曝光后烘焙
显影
坚膜烘焙
显影检查
ppt课件
10
涂胶
模板 曝光
显影
ppt课件
11
Normal under
Incomplete
over
ppt课件
12
光刻工艺 —— 显影后
ppt课件
13
蚀刻工艺
▪ 光刻胶上的IC设计图形
晶圆表面
▪ 腐蚀作用,从Si片表面去除不需要的材料, 如Si、SiO2,金属、光刻胶等
光刻与刻蚀工艺
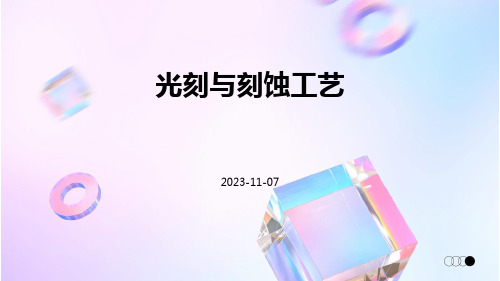
涂胶/显影技术
01
02
03
涂胶
在晶圆表面涂上一层光敏 胶,以保护非曝光区域并 提高图像对比度。
显影
用适当的溶剂去除曝光区 域的光敏胶,以形成所需 的图案。
控制胶厚
保持胶厚均匀,以避免图 像的扭曲和失真。
烘烤与曝光技术
烘烤
通过加热去除晶圆表面的湿气,以提高光敏胶的灵敏度和图像质 量。
曝光
将掩模图像投影到光敏胶上,通过光化学反应将图像转移到晶圆 上。
非接触式光刻
投影式非接触
利用光学系统将掩膜板上的图像投影到光刻胶涂层上,优点是无需直接接触,缺点是难度较高,需要精确的控 制系统。
电子束光刻
利用电子束在光刻胶上直接曝光,优点是分辨率高、无需掩膜板,缺点是生产效率低。
投影式光刻
接触式投影
掩膜板与光刻胶涂层之间保持接触,通过投影系统将图像投影到光刻胶上,优点是操作简单、高效, 缺点是图像质量可能受到掩膜板损伤和光刻胶污染的影响。
要点二
损伤控制
是指在刻蚀过程中避免对材料产生损伤。对于某些特殊 材料,如脆性材料,损伤控制尤为重要。如果刻蚀过程 中产生过多损伤,可能会导致材料性能下降甚至破裂。
感谢您的观看
THANKS
光刻工艺的基本步骤
涂胶
将光刻胶涂敷在硅片表面,以形成 光刻胶层。
烘烤
通过烘烤使光刻胶层干燥并固化。
曝光
将掩膜版上的图形对准硅片上的光 刻胶层,并使用曝光设备将图形转 移到光刻胶上。
显影
使用显影液将曝光后的光刻胶进行 化学处理,使图形更加清晰地展现 出来。
光刻工艺的重要性
光刻工艺是半导体制造中的关键环节,直接影响芯片的制造 质量和性能。
集成电路工艺:刻蚀

1. 引 言
1.1刻蚀的概念
刻蚀:它是半导体制造工艺,微电子IC制造工 艺以及微纳制造工艺中的一种相当重要的步骤。 是与光刻相联系的图形化(pattern)处理的一 种主要工艺。所谓刻蚀,实际上狭义理解就是 光刻腐蚀,先通过光刻将光刻胶进行光刻曝光 处理,然后通过其它方式实现腐蚀处理掉所需 除去的部分。随着微制造工艺的发展;广义上 来讲,刻蚀成了通过溶液、反应离子其它机 械方式来剥离、去除材料的一种统称,成为微 加工制造的一种普适叫法。
4.2常用材料的湿法刻蚀
1.二氧化硅湿法刻蚀 采用氢氟酸溶液加以进行。因为二氧化硅可与室
温的氢氟酸溶液进行反应,但却不会蚀刻硅基材 及多晶硅。反应式如下:
SiO2 + 6HF= H2[SiF6] + 2H2O 由于氢氟酸对二氧化硅的蚀刻速率相当高,在制
程上很难控制,因此在实际应用上都是使用稀释 后的氢氟酸溶液,或是添加氟化铵(NH4F)作 为缓冲剂的混合液,来进行二氧化硅的蚀刻。
下层的Ti ➢ 金属铝的刻蚀步骤多,工艺复杂
4. 湿法刻蚀
4.1 湿法刻蚀的原理
湿法刻蚀是将被刻蚀材料浸泡在腐蚀液内进行腐蚀 的技术
这是各向同性的刻蚀方法,利用化学反应过程去除 待刻蚀区域的薄膜材料
湿法刻蚀,又称湿化学腐蚀法。半导体制造业一开 始,湿法腐蚀就与硅片制造联系在一起。现在湿法 腐蚀大部分被干法刻蚀代替,但在漂去氧化硅、除 去残留物、表层剥离以及大尺寸的图形腐蚀应用方 面起着重要作用。尤其适合将多晶硅、氧化物、氮 化物、金属与Ⅲ-Ⅴ族化合物等作整片的腐蚀。
干法刻蚀是各向异性刻蚀,用物理和化学方法, 能实现图形的精确转移,是集成电路刻蚀工艺的 主流技术。
各向同性刻蚀:侧向与纵向腐蚀速度相同 各向异性刻蚀:侧向腐蚀速度远远小于纵向腐蚀
半导体行业之刻蚀工艺

1.负载效应等离子体图形化刻蚀过程中,刻蚀图形将影响刻蚀速率和刻蚀轮廓,称为负载效应。
负载效应有两种:宏观负载效应和微观负载效应。
宏观负载效应具有较大开口面积的晶圆刻蚀速率与较小开口面积的晶圆刻蚀速率不同,这种晶圆对晶圆的刻蚀速率差异就是宏观负载效应,这主要影响批量刻蚀,但对单片晶圆影响不大。
微观负载效应对于接触窗和金属层间接触窗孔的刻蚀,较小窗孔的刻蚀速率比大窗孔慢。
这就是微观负载效应(见下图(a)),产生该效应的原因是刻蚀等离子体气体难以穿过较小的窗孔,而且刻蚀的副产品也难以扩散出去。
减少工艺压力可以降低微观负载效应。
当压力较低时,平均自由程较长,刻蚀气体较易穿过微小的窗孔而接触到要被刻蚀的薄膜,从而比较容易从微小的窗孔中把刻蚀副产品去除。
由于光刻胶会溅镀沉积在侧壁上,所以图形隔离区域的刻蚀轮廓比密集区域宽,这是由于隔离图形区域缺少由邻近图形散射离子造成的侧壁离子轰击。
下图(b)说明了微观负载效应轮廓。
2.过刻蚀效应当刻蚀薄膜时(包括多晶硅、电介质以及金属刻蚀),晶圆内的刻蚀速率和薄膜厚度并不完全均匀。
因此当大部分薄膜被刻蚀移除后,留下的少部分薄膜必须移除。
移除剩余薄膜的过程称为过刻蚀,过刻蚀前的过程称为主刻蚀。
在过刻蚀中,被刻蚀薄膜和衬底材料之间的选择性要足够高才能避免损失过多的衬底材料。
在主刻蚀中,如果主刻蚀与过刻蚀使用不同的刻蚀条件,则能够改善过刻蚀中被刻薄膜和衬底材料之间的选择性,等离子体刻蚀中的光学终点侦测器可以自动停止主刻蚀而引发过刻蚀,这是因为当主刻蚀中的刻蚀剂开始刻蚀衬底薄膜时,等离子体中的成分就会发生变化。
如在多晶硅栅刻蚀中(见下图),主刻蚀不需要考虑二氧化硅的选择性。
当某些区域的多晶硅被刻蚀时,氯等离子体开始刻蚀二氧化硅,氧的辐射信号强度就会增强,从而发出一个停止主刻蚀而切换到过刻蚀的信号。
下图说明了主刻蚀和过刻蚀过程。
问题:对于一个IC芯片,多晶硅的厚度为3000A,薄膜的非均匀性为1.5%。
半导体制造工艺刻蚀
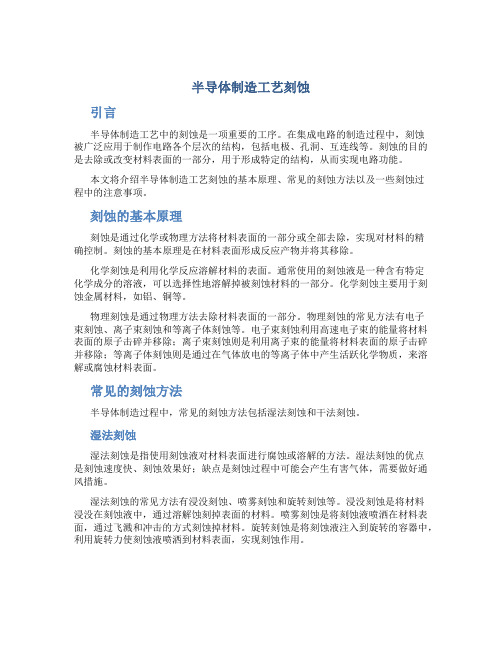
半导体制造工艺刻蚀引言半导体制造工艺中的刻蚀是一项重要的工序。
在集成电路的制造过程中,刻蚀被广泛应用于制作电路各个层次的结构,包括电极、孔洞、互连线等。
刻蚀的目的是去除或改变材料表面的一部分,用于形成特定的结构,从而实现电路功能。
本文将介绍半导体制造工艺刻蚀的基本原理、常见的刻蚀方法以及一些刻蚀过程中的注意事项。
刻蚀的基本原理刻蚀是通过化学或物理方法将材料表面的一部分或全部去除,实现对材料的精确控制。
刻蚀的基本原理是在材料表面形成反应产物并将其移除。
化学刻蚀是利用化学反应溶解材料的表面。
通常使用的刻蚀液是一种含有特定化学成分的溶液,可以选择性地溶解掉被刻蚀材料的一部分。
化学刻蚀主要用于刻蚀金属材料,如铝、铜等。
物理刻蚀是通过物理方法去除材料表面的一部分。
物理刻蚀的常见方法有电子束刻蚀、离子束刻蚀和等离子体刻蚀等。
电子束刻蚀利用高速电子束的能量将材料表面的原子击碎并移除;离子束刻蚀则是利用离子束的能量将材料表面的原子击碎并移除;等离子体刻蚀则是通过在气体放电的等离子体中产生活跃化学物质,来溶解或腐蚀材料表面。
常见的刻蚀方法半导体制造过程中,常见的刻蚀方法包括湿法刻蚀和干法刻蚀。
湿法刻蚀湿法刻蚀是指使用刻蚀液对材料表面进行腐蚀或溶解的方法。
湿法刻蚀的优点是刻蚀速度快、刻蚀效果好;缺点是刻蚀过程中可能会产生有害气体,需要做好通风措施。
湿法刻蚀的常见方法有浸没刻蚀、喷雾刻蚀和旋转刻蚀等。
浸没刻蚀是将材料浸没在刻蚀液中,通过溶解蚀刻掉表面的材料。
喷雾刻蚀是将刻蚀液喷洒在材料表面,通过飞溅和冲击的方式刻蚀掉材料。
旋转刻蚀是将刻蚀液注入到旋转的容器中,利用旋转力使刻蚀液喷洒到材料表面,实现刻蚀作用。
干法刻蚀干法刻蚀是指利用气体等离子体或物理方法对材料表面进行刻蚀的方法。
干法刻蚀的优点是刻蚀过程中不产生液体,可以避免污染问题;缺点是刻蚀速度较慢。
干法刻蚀的常见方法有等离子体刻蚀、离子束刻蚀和电子束刻蚀等。
等离子体刻蚀是通过在气体放电的等离子体中产生活跃化学物质,来溶解或腐蚀材料表面。
半导体制程培训CMP和蚀刻

LOGO
半导体制造工艺流程
干法刻蚀
优点:各向异性好,选择比高,可控性、灵活性、重复性好, 细线条操作安全,易实现自动化,无化学废液,处理过程未引 入污染,洁净度高。
缺点:成本高,设备复杂。
干法刻蚀方式:①溅射与离子束铣蚀 ②等离子刻蚀(Plasma Etching) ③③高压等离子刻蚀 ④高密度等离子体(HDP)刻蚀 ⑤反应离子刻蚀(RIE)
Your site here
LOGO
半导体制造工艺流程
单层金属IC的表面起伏剖面
顶层
氮化硅
Poly
n+
金属化前氧化层 侧墙氧化层 栅氧化层
垫氧 ILD
n+
场氧化层
氧化硅
Metal
氧化硅 Poly Metal
p+
p+
pห้องสมุดไป่ตู้ 外延层
n-阱 Metal
p+ 硅衬底
Your site here
LOGO
半导体制造工艺流程
Your site here
LOGO
半导体制造工艺流程
应用
化学机械抛光主要用于以下几个方面: ①深槽填充的平面化
②接触孔和过孔中的金属接头的平面化
③生产中间步骤中氧化层和金属间电介层的平面化
Your site here
LOGO
半导体制造工艺流程
CMP技术的优点:
1.能获得全局平坦化; 2.各种各样的硅片表面能被平坦化; 3.在同一次抛光过程中对平坦化多层材料有用; 4.允许制造中采用更严格的设计规则并采用更多的互连层; 5.提供制作金属图形的一种方法。 6. 由于减小了表面起伏,从而能改善金属台阶覆盖; 7.能提高亚0.5微米器件和电路的可靠性、速度和成品率; 8.CMP是一种减薄表层材料的工艺并能去除表面缺陷; 9.不使用在干法刻蚀工艺中常用的危险气体。
半导体器件工艺学之刻蚀

下游式刻蚀系统
离子束铣( Ion Milling) 是近年来发展较快的一种离 子剥离技术。该技术主要利用携带能量的离子轰 击靶材料所产生的物理溅射刻蚀效应
离子刻蚀速率表示如下: dh( H) / dt = R( H) / cos(H) = R( H) [ 1 + tan2( H) ]1/2
当离子束入射的角度较大时, 材料表面反射的离子束也增 多。因此, 随着角度H的增大 , 越来越少的离子渗入到材 料的有效表面。为保证离子 的有效渗入, 定义临界角Hc 。 离子束的溅射场与靶材料的 原子数Z 有关, 材料的原子数 Z 越高, 刻蚀速率越高; 反之 则越低。
本产品通过物理与化学相结合的方法,对很细的线条(亚微米以下)进行刻 蚀以形成精细的图形。 主要用于微电子、光电子、通讯、微机械、新材料、能源等领域的器件 研发和制造。
深层反应离子刻蚀(DRIE)
系统己经足以刻蚀深宽比超过50 的深槽硅结构,对于光阻的刻蚀 选择比己超过100:1,刻蚀深度均 匀度也可以控制在±3%以内。
中微发布Primo D-RIE刻蚀设备,面向22 纳米及以下工艺
中微半导体设备(上海)有限公司(以下简称“ 中微”)日前发布面向22纳米及以下芯片生产 的第二代300毫米甚高频去耦合反应离子刻 蚀设备--Primo AD-RIE。 2011年7月
Primo AD-RIE在促进中微第一代刻蚀设备技术创 新的同时,又大大扩大了其自身的加工领域。 该设备的主要部分是一组创新的少量反应台反应 器的簇架构,可以灵活地装置多达三个双反应台 反应器,以达到最佳芯片加工输出量。每个反应 器都可以实现单芯片或双芯片加工。独特的反应 器腔体设计融合了中微专有的等离子体聚焦和喷 淋头技术,确保了芯片加工的质量。Primo ADRIE的一些基本特征使其更具备28纳米以下关键刻 蚀加工的能力
半导体工艺原理--刻蚀工艺
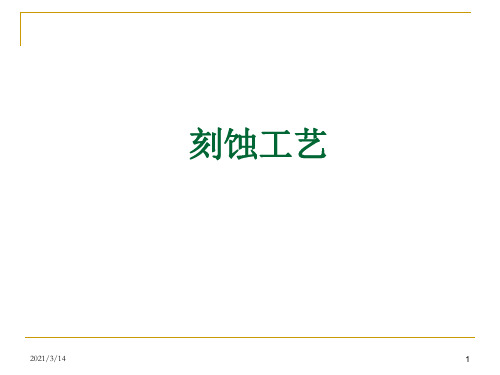
注释
对硅有选择性,对硅腐蚀速率很慢,腐蚀速率依赖于 膜的密度,掺杂等因素
是纯HF腐蚀速率的1/20,腐蚀速率依赖于膜的密度, 掺杂等因素,不像纯HF那样使胶剥离
Si3N4
HF(49%) HPO:HO(沸点:130-150℃)
Al
H3PO4:H2O:HNO3:CH3COOH(16:2:1:
1)
多晶硅 单晶硅
2021/3/14
34
其刻蚀分为两步,首先是要除去未被光刻胶保护 的硅化金属,可以采用CF4、SF6、Cl2、HCl2等都 可以用来作为硅化金属的RIE的反应气体。
对多晶硅的刻蚀采用氟化物将导致等方向性的刻 蚀,而Polycide 的刻蚀必须采用各向异性,因此采 用氯化物较好,有 Si, HCL2, SiCl4等。
2 A l 6 H 3 P O 4 2 A l( H 2 P O 4 ) 3 3 H 2
高锰酸钾腐蚀液的配方为:
K M n O 4 :N a O H :H 2 O 6 g :1 0 g :9 0 m l
高锰酸钾与铝的反应式
N a O H
K M n O 4A l K A lO 2M n O 2
22
湿法刻蚀剖面
2021/3/14
23
SiO2 的腐蚀
SiO24HFSiF42H2O SiF42HFH2(SiF6)
氟化铵在SiO2 腐蚀液中起缓冲剂的作用。这种加有氟化铵 的氢氟酸溶液,习惯上称为HF缓冲液。 常用的配方为:
HF:NH4F:H2O = 3ml:6g:10ml
2021/3/14
24
HNO3:H2O:HF(CH3COOH)(50:20:1)
HNO3:H2O:HF(CH3COOH)(50:20:1) KOH:HO:IPA(23wt%KOH,13wt%IP
- 1、下载文档前请自行甄别文档内容的完整性,平台不提供额外的编辑、内容补充、找答案等附加服务。
- 2、"仅部分预览"的文档,不可在线预览部分如存在完整性等问题,可反馈申请退款(可完整预览的文档不适用该条件!)。
- 3、如文档侵犯您的权益,请联系客服反馈,我们会尽快为您处理(人工客服工作时间:9:00-18:30)。
rlat 方向性 A 1 rvert
干法刻蚀 纯物 理刻 蚀
反应离子刻蚀RIE 增加方向性、选择 性的方法CF4/O2
纯化 学刻 蚀
SiO2——HF
MEMS
半导体制造工艺基础
第五章 刻蚀原理
32
反应等离子体刻蚀技术与设备
一个反应等离子体刻蚀反应器包括一个真空腔、抽气泵系统、电源供应 产生器、压力探测器、流量控制器与终点探测器等。
10%O2可获得最大的Si/SiO2刻蚀比
半导体制造工艺基础
第五入少量H2, 可使CFx:F*的浓度比 增加。 从而使SiO2:Si 及Si3N4:Si的腐蚀速 率比增大
半导体制造工艺基础
第五章 刻蚀原理
29
增加F/C比(加氧气),可以增加刻蚀速率 减少F/C比(加氢气),刻蚀过程倾向于形成高分子膜
20
终点控制
干法刻蚀必须配备一个用来探测刻蚀工艺结束点的监视器,即终点探 测系统。激光干涉度量法用来持续控制晶片表面的刻蚀速率与终止点。 在刻蚀过程中,从晶片表面反射的激光会来回振荡,这个振荡的发生是 因为刻蚀层界面的上界面与下界面的反射光的相位干涉。因此这一层材 料必须透光或半透光才能观测到振荡现象。振荡周期与薄膜厚度的变化 关系为:
半导体制造工艺基础
第五章 刻蚀原理 刻蚀方向性的增加
增加离子轰击(物理刻蚀分量) 侧壁增加抑制物(inhibitor) DRIE
30
半导体制造工艺基础
第五章 刻蚀原理
本节课主要内容 什么是图形转移技术? 刻蚀的两个关键问题? 湿法腐蚀:
Si——HNA各向同性 ——KOH各向异性
31
光刻+刻蚀
半导体制造工艺基础
第五章 刻蚀原理
21
反射系数(任意单位)
硅化物
多晶硅
硅化物/多晶硅刻蚀实验曲线 刻蚀时间(任意单位)
半导体制造工艺基础
第五章 刻蚀原理
22
Sputtering mode:硅 片置于右侧电极,该 电极接地(反应腔体 通常也接地,则增大 该电极有效面积); 右侧暗区电压差小, 通过离子轰击的物理 刻蚀很弱
反应的实质,打破C-F、Si-Si键,形成挥发性的Si-F硅卤化物。
CΘF +Si ΘSi = Si-F + 17kcal/mol
反应需要一个净正能量,CF4本身不会直接刻蚀硅。等离子体高能量
的电子碰撞会使CF4分子分裂生产自由的氟原子和分子团,使得形成 SiF是能量有利的。
等离子刻蚀基本原理 半导体制造工艺基础
半导体制造工艺基础
第五章 刻蚀原理
14
化学刻蚀
物理刻蚀
半导体制造工艺基础
第五章 刻蚀原理
离子增强刻蚀-Ion Enhanced etching
15
无离子,XeF2对Si不刻蚀 纯Ar离子,对Si不刻蚀 Ar离子和XeF2相互作用, 刻蚀速率很快
物理过程(如离子轰 击造成的断键/晶格 损伤、辅助挥发性反 应产物的生成、表面 等离子体刻蚀的化学和物理过 抑制物的去除等)将 有助于表面化学过程 程并不是两个相互独立的过程, /化学反应的进行 而且相互有增强作用
23
SiCl4
TiCl4
等离子刻蚀基本原理 半导体制造工艺基础
第五章 刻蚀原理
刻蚀方程式 为何处在等离子体环境下进行刻蚀
在我们的工艺中,是用CF4和O2来刻蚀扩散后的硅片,其刻蚀原理如下:
24
CF4 = CFx* + (4-x) F* (x≤3) Si + 4 F* = SiF4 ↑
SiO2 + 4 F* = SiF4 + O2↑
半导体制造工艺基础
第五章 刻蚀原理
18
刻蚀机制、等离子体探测与终点的控制
刻蚀机制
刻蚀工艺包括5个步骤: 1、刻蚀过程开始与等离子体刻蚀反应物的产生; 2、反应物通过扩散的方式穿过滞留气体层到达表面; 3、反应物被表面吸收; 4、通过化学反应产生挥发性化合物; 5、化合物离开表面回到等离子体气流中,接着被抽气泵抽出。 基本刻蚀方式为: 物理方式:溅射刻蚀,正离子高速轰击表面; 化学方式:等离子体产生的中性反应物与物质表面相互作用产生挥发性产物。 化学方式有高腐蚀速率、高的选择比与低的离子轰击导致的缺陷,但有各向 同性的刻蚀轮廓。物理方式可以产生各向同性的轮廓,但伴随低的选择比与 高的离子轰击导致的缺陷。将二者结合,如反应离子刻蚀(RIE)。
刻蚀速率R (etch rate) 刻蚀均匀性 (etch uniformity) 选择性S (Selectivity) 各项异性度A (Anisotropy) 掩膜层下刻蚀 (Undercut) 单位时间刻蚀的薄膜厚度。对产 率有较大影响 一个硅片或多个硅片或多批硅片 上刻蚀速率的变化 不同材料之间的刻蚀速率比 刻蚀的方向性 A=0, 各项同性;A=1, 各项异性 横向单边的过腐蚀量
半导体制造工艺基础
第五章 刻蚀原理
例1:SiO2采用HF腐蚀
7
实 BOE:buffered oxide etching 际 用 或BHF: buffered HF 例2:Si采用HNO3和HF腐蚀(HNA)
加入NH4F缓冲液:弥补 F和降低对胶的刻蚀
例3:Si3N4采用热磷酸腐蚀
各 向 同 性
半导体制造工艺基础
第五章 刻蚀原理
氧气的作用
在CF4进气中加入少量氧气会提高硅和二氧化硅的刻蚀 速率。人们认为氧气与碳原子反应生成 CO2 ,这样从等离 子体中去掉一些碳,从而增加F的浓度,这些成为富氟等离 子体。往CF4等离子体中每增加 12%的氧气,F浓度会增加 一个数量级,对硅的刻蚀速率增加一个数量级。
25
半导体制造工艺基础
(2)干法腐蚀能达到高的分辨率,湿法腐蚀较差
(3)湿法腐蚀需大量的腐蚀性化学试剂,对人体 和环境有害 (4)湿法腐蚀需大量的化学试剂去冲洗腐蚀剂剩 余物,不经济
半导体制造工艺基础
第五章 刻蚀原理
13
干法刻蚀
化学刻蚀(各项同性,选择性好) ——等离子体激活的化学反应(等离子体刻蚀)
物理刻蚀(各向异性,选择性差) ——高能离子的轰击 (溅射刻蚀) 离子增强刻蚀(各向异性,选择性较好) ——反应离子刻蚀
半导体制造工艺基础
第五章 刻蚀原理
19
半导体制造工艺基础
第五章 刻蚀原理
等离子体探测
大多数的等离子体工艺中发出的射线范围在红外光到紫外光之间,一 个简单的缝隙方法是利用光学发射光谱仪(OES)来测量这些发射光谱 的强度与波长的关系。利用观测到的光谱波峰与已知的发射光谱比较, 通过可以决定出中性或离子物质的存在。物质相对的密度,也可以通过 观察等离子体参数改变时光强度的改变而得到。这些由主要刻蚀剂或副 产物所引起的发射信号在刻蚀终点开始上升或下降。
大多数的等离子体抗蚀机,除了三极RIE外,都无法提供独立控制等离子 体参数的能力。导致轰击损伤的严重问题。ECR结合微波电源与静电场 来驱使电子沿磁场线作一定角频率的回旋。当此频率等于外加微波频率 时,电子能量与外加磁场产生共振耦合,造成大量的分解与电离。
半导体制造工艺基础
第五章 刻蚀原理
36
其他高密度等离子体刻蚀机
半导体制造工艺基础
第五章 刻蚀原理
HNA各向同性腐蚀
10
自终止
半导体制造工艺基础
第五章 刻蚀原理
利用Si的各向异性湿法腐蚀制作的MEMS (MicroElectroMechanical Systems)结构
11
半导体制造工艺基础
第五章 刻蚀原理
12
湿法腐蚀的缺点
在大规模集成电路制造中,湿法腐蚀正被干法刻蚀 所替代: (1)湿法腐蚀是各向同性,干法可以是各向异性
由于ULSI的线宽持续缩小,逼近传统的RIE系统极限,除了ECR系统外, 其他形式的高密度等离子体源(HDP),如电感耦合等离子体源 (ICP)、变压器耦合等离子体源(TCP)、表面波耦合等离子体源 (SWP)也已开始发展。这些设备拥有高等离子体密度与低工艺压强。 另外,HDP等离子体源对衬底的损伤较小(因为衬底有独立的偏压源与 侧电极电势),并有高的的各向异性(因为在低压下工作但有高活性的 等离子体密度)。 然而,由于其复杂且成本较高,这些系统可能不会使用于非关键性的工 艺,如侧壁间隔与平坦化工艺。
半导体制造工艺基础
第五章 刻蚀原理
33
1000 低压整批RIE 100 单片晶片RIE
10
低于高密度 ECR,ICP
桶状等离 子体刻机
1
1
10
100
1000
半导体制造工艺基础
第五章 刻蚀原理
34
反应离子刻蚀(RIE)
平行板系统
RF
RF
半导体制造工艺基础
第五章 刻蚀原理
35
电子回旋共振(ECR)等离子体刻蚀机
6. 清洁、经济、安全
半导体制造工艺基础
第五章 刻蚀原理
5
刻蚀过程包括三个步骤:
– 反应物质量输运(Mass transport)到要被刻 蚀的表面 – 在反应物和要被刻蚀的膜表面之间的反应 – 反应产物从表面向外扩散的过程
半导体制造工艺基础
第五章 刻蚀原理 湿法刻蚀
6
反应产物必 须溶于水或 是气相
半导体制造工艺基础
第五章 刻蚀原理
介电板 RF
37
等离子体
RF
变压器耦合等离子体反应设备示意图
半导体制造工艺基础
第五章 刻蚀原理
38
集成等离子体工艺
半导体晶片都是在洁净室里加工制作,以减少大气中的尘埃污染。当器 件尺寸缩小,尘埃的污染成为一个严重的问题。为了减少尘粒的污染, 集成等离子体设备利用晶片操作机将晶片置于高真空环境中从一个反应 腔移到另一个反应腔。同时可以增加产率。