半导体制造工艺_12薄膜沉积(上)
刻蚀工艺和薄膜工艺(一)

刻蚀工艺和薄膜工艺(一)
刻蚀工艺和薄膜工艺
简介
•刻蚀工艺是一种常用的微纳加工技术,用于在半导体材料上制造微细结构。
•薄膜工艺是根据特定的要求在材料表面制备一层薄膜的技术。
刻蚀工艺
定义
•刻蚀工艺是通过化学反应或物理作用,将特定区域的材料制成所需形状或深度的工艺。
常见方法
1.干法刻蚀:使用高能离子束或高温等干燥条件进行刻蚀。
2.湿法刻蚀:利用酸碱溶液进行刻蚀,有较高的选择性和均匀性。
薄膜工艺
定义
•薄膜工艺是在材料表面制备一层具有特定功能的薄膜的工艺。
常见方法
1.物理气相沉积(PVD):利用物理方式将原子或分子沉积在基底
上。
2.化学气相沉积(CVD):利用化学反应在基底上生成薄膜。
刻蚀工艺和薄膜工艺的联系和区别
•刻蚀工艺和薄膜工艺都是微电子制造中常用的工艺。
•刻蚀工艺主要用于制造微细结构,而薄膜工艺主要用于制备功能性薄膜。
•刻蚀工艺和薄膜工艺可以结合使用,以实现更精确的微纳加工。
结论
•刻蚀工艺和薄膜工艺都是微电子制造中极为重要的工艺。
•了解刻蚀工艺和薄膜工艺的原理和方法,可以帮助提高微细结构制备和薄膜制备的技术水平。
脚标:该文章以一个资深创作者的视角,简要介绍了刻蚀工艺和薄膜工艺的定义、常见方法以及二者的联系和区别。
通过用标题和副标题的方式进行排版,提供了清晰易读的文章结构。
文章内容符合markdown格式的要求,没有出现html字符、网址、图片、电话号码等内容。
薄膜沉积工艺
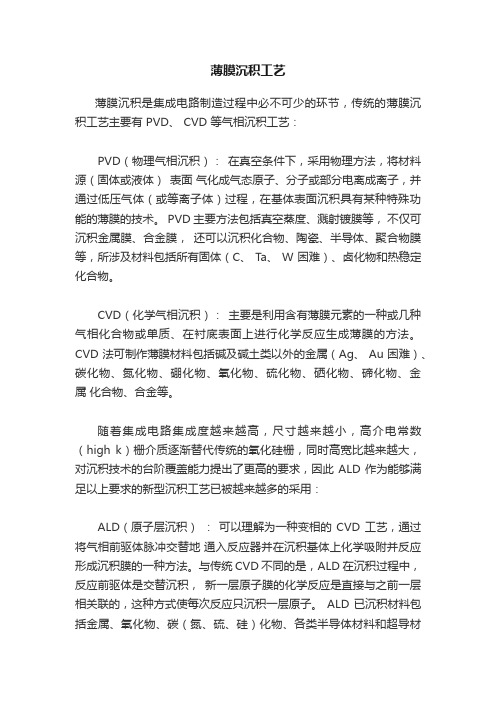
薄膜沉积工艺薄膜沉积是集成电路制造过程中必不可少的环节,传统的薄膜沉积工艺主要有 PVD、 CVD 等气相沉积工艺:PVD(物理气相沉积):在真空条件下,采用物理方法,将材料源(固体或液体)表面气化成气态原子、分子或部分电离成离子,并通过低压气体(或等离子体)过程,在基体表面沉积具有某种特殊功能的薄膜的技术。
PVD 主要方法包括真空蒸度、溅射镀膜等,不仅可沉积金属膜、合金膜,还可以沉积化合物、陶瓷、半导体、聚合物膜等,所涉及材料包括所有固体(C、 Ta、 W 困难)、卤化物和热稳定化合物。
CVD(化学气相沉积):主要是利用含有薄膜元素的一种或几种气相化合物或单质、在衬底表面上进行化学反应生成薄膜的方法。
CVD 法可制作薄膜材料包括碱及碱土类以外的金属(Ag、 Au 困难)、碳化物、氮化物、硼化物、氧化物、硫化物、硒化物、碲化物、金属化合物、合金等。
随着集成电路集成度越来越高,尺寸越来越小,高介电常数(high k)栅介质逐渐替代传统的氧化硅栅,同时高宽比越来越大,对沉积技术的台阶覆盖能力提出了更高的要求,因此 ALD 作为能够满足以上要求的新型沉积工艺已被越来越多的采用:ALD(原子层沉积):可以理解为一种变相的 CVD 工艺,通过将气相前驱体脉冲交替地通入反应器并在沉积基体上化学吸附并反应形成沉积膜的一种方法。
与传统 CVD 不同的是,ALD 在沉积过程中,反应前驱体是交替沉积,新一层原子膜的化学反应是直接与之前一层相关联的,这种方式使每次反应只沉积一层原子。
ALD 已沉积材料包括金属、氧化物、碳(氮、硫、硅)化物、各类半导体材料和超导材料等。
ALD沉积材料ALD 相比传统的 PVD 和 CVD 等淀积工艺,充分利用表面饱和反应,天生具备厚度控制和高度的稳定性能,对温度和反应物通量的变化不太敏感。
因此 ALD 法沉积的薄膜兼具高纯度和高密度,既平整又具有高度的保型性,即使对于纵宽比高达100:1 的结构也可实现良好的阶梯覆盖。
半导体制造技术—第四讲:淀积工艺

提供反应物质:反应气体是淀积过程中形成薄膜的主要物质来源 控制反应速率:反应气体的浓度和流量可以控制反应速率从而影响薄膜的厚度和质量 影响薄膜性质:反应气体的种类和比例可以影响薄膜的性质如导电性、光学性能等 参与化学反应:反应气体在淀积过程中参与化学反应形成所需的薄膜材料
半导体制造技术之淀 积工艺
汇报人:
目录
添加目录标题
淀积工艺概述
淀积工艺的原理
淀积工艺的应用
淀积工艺的优缺点
淀积工艺的未来展 望
添加章节标题
淀积工艺概述
淀积工艺是半导体制造过程中的关键步骤之一 主要目的是在硅晶圆上沉积一层或多层薄膜 薄膜可以是金属、氧化物、氮化物等 淀积工艺包括化学气相淀积(CVD)、物理气相淀积(PVD)等方法
研究方向:新型材料、新工艺、新设备 技术挑战:提高性能、降低成本、提高可靠性 研发目标:实现更高性能、更低成本、更可靠的淀积工艺 研发成果:新型材料、新工艺、新设备的研发和应用
太阳能电池:利用淀积工艺制造高效太阳能电池提高光电转换效率 燃料电池:利用淀积工艺制造高性能燃料电池提高能源转换效率 储能设备:利用淀积工艺制造高性能储能设备提高储能效率和稳定性 电动汽车:利用淀积工艺制造高性能电动汽车电池提高续航里程和充电速度
物理淀积的优 点是沉积速度 快沉积层厚度 均匀沉积层质
量高
化学淀积是一种通过化学反应在半导体 表面形成薄膜的过程
化学淀积可以分为气相化学淀积和液相 化学淀积两种类型
气相化学淀积是通过化学反应在半导体 表面形成薄膜的过程
液相化学淀积是通过化学反应在半导体 表面形成薄膜的过程
化学淀积工艺可以应用于半导体制造中的各 种薄膜制备如氧化物、氮化物、金属等
芯片制造薄膜沉积工艺
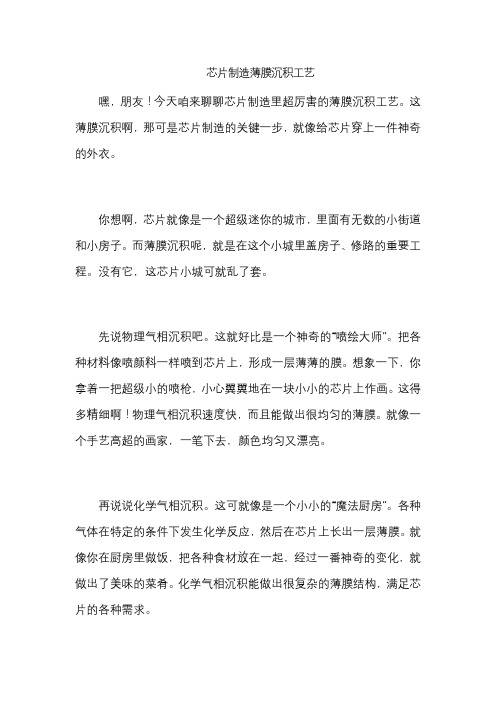
芯片制造薄膜沉积工艺嘿,朋友!今天咱来聊聊芯片制造里超厉害的薄膜沉积工艺。
这薄膜沉积啊,那可是芯片制造的关键一步,就像给芯片穿上一件神奇的外衣。
你想啊,芯片就像是一个超级迷你的城市,里面有无数的小街道和小房子。
而薄膜沉积呢,就是在这个小城里盖房子、修路的重要工程。
没有它,这芯片小城可就乱了套。
先说物理气相沉积吧。
这就好比是一个神奇的“喷绘大师”。
把各种材料像喷颜料一样喷到芯片上,形成一层薄薄的膜。
想象一下,你拿着一把超级小的喷枪,小心翼翼地在一块小小的芯片上作画。
这得多精细啊!物理气相沉积速度快,而且能做出很均匀的薄膜。
就像一个手艺高超的画家,一笔下去,颜色均匀又漂亮。
再说说化学气相沉积。
这可就像是一个小小的“魔法厨房”。
各种气体在特定的条件下发生化学反应,然后在芯片上长出一层薄膜。
就像你在厨房里做饭,把各种食材放在一起,经过一番神奇的变化,就做出了美味的菜肴。
化学气相沉积能做出很复杂的薄膜结构,满足芯片的各种需求。
那原子层沉积呢?这简直就是一个“超级精细的裁缝”。
一层一层地给芯片披上最合身的衣服。
它能精确控制薄膜的厚度,就像裁缝给你量身定制衣服一样,分毫不差。
如果把芯片比作一个高贵的公主或王子,那原子层沉积就是给他们做最美的华服。
在芯片制造的过程中,薄膜沉积可不能马虎。
就像盖房子,地基不打好,房子就会摇摇晃晃。
薄膜沉积不好,芯片的性能就会大打折扣。
所以啊,工程师们就像细心的工匠,一点一点地把这薄膜沉积做好。
你说,这薄膜沉积是不是很神奇?它就像是芯片制造的魔法,让小小的芯片拥有强大的功能。
咱中国的芯片产业要崛起,就得把这薄膜沉积工艺掌握得牢牢的。
让我们的芯片穿上最棒的外衣,在科技的舞台上闪闪发光。
加油,中国芯片!加油,薄膜沉积工艺!。
半导体八大工艺名称

半导体八大工艺名称1. 硅晶圆制备工艺硅晶圆制备是半导体制造过程的第一步,也是最为关键的一步。
它是指将高纯度的硅材料通过一系列的工艺步骤转化为薄而平整的硅晶圆。
硅晶圆制备工艺主要包括以下几个步骤:(1) 单晶生长单晶生长是将高纯度的硅材料通过熔融和凝固的过程,使其在特定的条件下形成单晶结构。
常用的单晶生长方法包括Czochralski法和区熔法。
(2) 切割切割是将生长好的硅单晶材料切割成薄片的过程。
常用的切割方法是采用金刚石刀片进行切割。
(3) 研磨和抛光研磨和抛光是将切割好的硅片进行表面处理,使其变得平整光滑的过程。
研磨通常使用研磨机进行,而抛光则使用化学机械抛光(CMP)工艺。
(4) 清洗清洗是将研磨和抛光后的硅片进行清洁处理,去除表面的污染物和杂质。
清洗过程通常采用酸洗和溶剂清洗的方法。
2. 光刻工艺光刻工艺是半导体制造中的一项关键工艺,用于将设计好的电路图案转移到硅晶圆上。
光刻工艺主要包括以下几个步骤:(1) 涂覆光刻胶涂覆光刻胶是将光刻胶涂覆在硅晶圆表面的过程。
光刻胶是一种敏感于紫外光的物质,可以通过紫外光的照射来改变其化学性质。
(2) 曝光曝光是将硅晶圆上的光刻胶通过光刻机上的光源进行照射,使其在特定区域发生化学反应。
曝光过程需要使用掩模板来控制光刻胶的曝光区域。
(3) 显影显影是将曝光后的光刻胶进行处理,使其在曝光区域发生溶解或固化的过程。
显影过程通常使用显影液进行。
(4) 清洗清洗是将显影后的硅晶圆进行清洁处理,去除残留的光刻胶和显影液。
3. 离子注入工艺离子注入工艺是将特定的离子注入到硅晶圆中,以改变其电学性质的过程。
离子注入工艺主要包括以下几个步骤:(1) 选择离子种类和能量选择合适的离子种类和能量是离子注入工艺的第一步。
不同的离子种类和能量可以改变硅晶圆的导电性质。
(2) 离子注入离子注入是将选择好的离子通过离子注入机进行注入的过程。
离子注入机通过加速器将离子加速到一定的能量,并将其注入到硅晶圆中。
半导体制造详细流程介绍
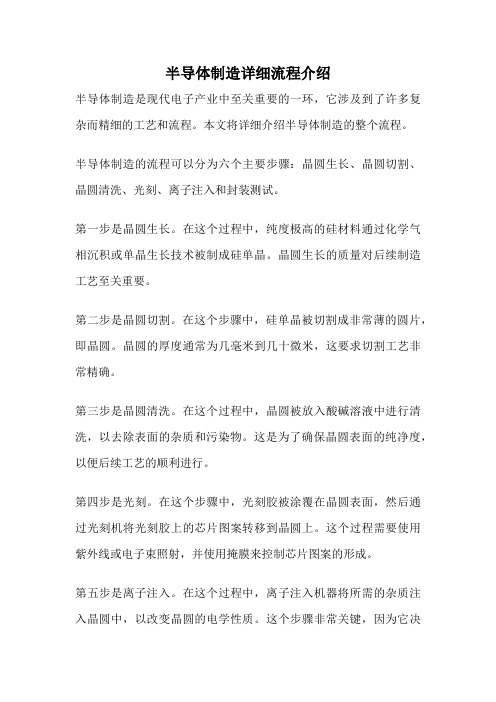
半导体制造详细流程介绍半导体制造是现代电子产业中至关重要的一环,它涉及到了许多复杂而精细的工艺和流程。
本文将详细介绍半导体制造的整个流程。
半导体制造的流程可以分为六个主要步骤:晶圆生长、晶圆切割、晶圆清洗、光刻、离子注入和封装测试。
第一步是晶圆生长。
在这个过程中,纯度极高的硅材料通过化学气相沉积或单晶生长技术被制成硅单晶。
晶圆生长的质量对后续制造工艺至关重要。
第二步是晶圆切割。
在这个步骤中,硅单晶被切割成非常薄的圆片,即晶圆。
晶圆的厚度通常为几毫米到几十微米,这要求切割工艺非常精确。
第三步是晶圆清洗。
在这个过程中,晶圆被放入酸碱溶液中进行清洗,以去除表面的杂质和污染物。
这是为了确保晶圆表面的纯净度,以便后续工艺的顺利进行。
第四步是光刻。
在这个步骤中,光刻胶被涂覆在晶圆表面,然后通过光刻机将光刻胶上的芯片图案转移到晶圆上。
这个过程需要使用紫外线或电子束照射,并使用掩膜来控制芯片图案的形成。
第五步是离子注入。
在这个过程中,离子注入机器将所需的杂质注入晶圆中,以改变晶圆的电学性质。
这个步骤非常关键,因为它决定了晶圆上芯片的导电性能。
最后一步是封装测试。
在这个步骤中,晶圆上的芯片被切割成单个芯片,并封装到芯片包装中。
然后,芯片将被连接到电路板上,并进行各种测试,以确保其正常工作。
整个半导体制造过程需要非常严格的控制和监测,以确保每个步骤都能达到所需的质量标准。
同时,制造过程中的设备和环境条件也需要精确控制,以避免对晶圆的污染或损坏。
除了上述主要步骤外,半导体制造还涉及到许多其他辅助工艺和步骤,如薄膜沉积、化学机械研磨、电镀和退火等。
这些步骤都是为了改善芯片的性能和可靠性。
总结起来,半导体制造是一个高度复杂和精细的过程,涉及到多个步骤和工艺。
每个步骤都需要严格的控制和监测,以确保最终芯片的质量和性能。
随着科技的不断进步,半导体制造也在不断演进和改进,以满足电子产品对于更高性能和更小尺寸的需求。
揭秘半导体制造全流程(上篇)
为帮助大家了解和认识半导体及相关工艺,我们将以三期文章推送,为大家逐一介绍每个步骤。
当听到“半导体”这个词时,你会想到什么?它听起来复杂且遥远,但其实已经渗透到我们生活的各个方面:从智能手机、笔记本电脑、信用卡到地铁,我们日常生活所依赖的各种物品都用到了半导体。
每个半导体产品的制造都需要数百个工艺,泛林集团将整个制造过程分为八个步骤:晶圆加工-氧化-光刻-刻蚀-薄膜沉积-互连-测试-封装。
为帮助大家了解和认识半导体及相关工艺,我们将以三期微信推送,为大家逐一介绍上述每个步骤。
第一步晶圆加工所有半导体工艺都始于一粒沙子!因为沙子所含的硅是生产晶圆所需要的原材料。
晶圆是将硅(Si)或砷化镓(GaAs)制成的单晶柱体切割形成的圆薄片。
要提取高纯度的硅材料需要用到硅砂,一种二氧化硅含量高达95%的特殊材料,也是制作晶圆的主要原材料。
晶圆加工就是制作获取上述晶圆的过程。
①铸锭首先需将沙子加热,分离其中的一氧化碳和硅,并不断重复该过程直至获得超高纯度的电子级硅(EG-Si)。
高纯硅熔化成液体,进而再凝固成单晶固体形式,称为“锭”,这就是半导体制造的第一步。
硅锭(硅柱)的制作精度要求很高,达到纳米级,其广泛应用的制造方法是提拉法。
②锭切割前一个步骤完成后,需要用金刚石锯切掉铸锭的两端,再将其切割成一定厚度的薄片。
锭薄片直径决定了晶圆的尺寸,更大更薄的晶圆能被分割成更多的可用单元,有助于降低生产成本。
切割硅锭后需在薄片上加入“平坦区”或“凹痕”标记,方便在后续步骤中以其为标准设置加工方向。
③晶圆表面抛光通过上述切割过程获得的薄片被称为“裸片”,即未经加工的“原料晶圆”。
裸片的表面凹凸不平,无法直接在上面印制电路图形。
因此,需要先通过研磨和化学刻蚀工艺去除表面瑕疵,然后通过抛光形成光洁的表面,再通过清洗去除残留污染物,即可获得表面整洁的成品晶圆。
第二步氧化氧化过程的作用是在晶圆表面形成保护膜。
它可以保护晶圆不受化学杂质影响、避免漏电流进入电路、预防离子植入过程中的扩散以及防止晶圆在刻蚀时滑脱。
实验十二真空镀膜
实验十二真空镀膜引言在真空中使固体表面(基片)上沉积一层金属、半导体或介质薄膜的工艺通常称为真空镀膜。
早在19世纪,英国的Grove和德国的Plücker接踵在气体放电实验的辉光放电壁上观察到了溅射的金属薄膜,这就是真空镀膜的萌芽。
后于1877年将金属溅射用于镜子的生产;1930年左右将它用于Edison唱机录音蜡主盘上的导电金属。
以后的30年,高真空蒸发镀膜又取得了飞速发展,这时已能在实验室中制造单层反射膜、单层减反膜和单层分光膜,而且在1939年由德国的Schott等人镀制出金属的FabryPerot干与滤波片,1952年又做出了顶峰值、窄宽度的全介质干与滤波片。
真空镀膜技术历经一个多世纪的发展,目前已普遍用于电子、光学、磁学、半导体、无线电及材料科学等领域,成为一种不可缺少的新技术、新手腕、新方式。
实验目的1.了解真空镀膜机的结构和利用方式。
2.掌握真空镀膜的工艺原理及在基片上蒸镀光学金属、介质薄膜的工艺进程。
3.了解金属、介质薄膜的光学特性及用光度法测量膜层折射率和膜厚的原理。
实验原理从镀膜系统的结构和工作机理上来讲,真空镀膜技术大体上可分为“真空热蒸镀”、“真空离子镀”及“真空阴极溅射”三类。
真空热蒸镀是一种发展较早、应用普遍的镀膜方式。
加热方式主要有电阻加热、电子束加热、高频感应加热和激光加热等。
1.真空热蒸镀的沉积条件(1)真空度由气体分子运动论知,处在无规则热运动中的气体分子要彼此发生碰撞,任意两次持续碰撞间一个分子自由运动的平均路程称为平均自由程,用λ表示,它的大小反映了分子间碰撞的频繁程度。
P d kT22πλ=(8.2-1)式中:d为分子直径,T为环境温度(单位为K),P为气体压强。
在常温下,平均自由程可近似表示为:)(1055m P -⨯≈λ (8.2-2)式中:P 为气体平均压强(单位为Torr)。
表8.2-1列出了各类真空度(气体平均压强)下的平均自由程λ及其它几个典型参量。
半导体全面分析:制造三大工艺,晶圆四大工艺!
半导体全⾯分析:制造三⼤⼯艺,晶圆四⼤⼯艺!技术:设计流程 100 亿个晶体管在指甲盖⼤⼩的地⽅组成电路,想想就头⽪发⿇!⼀个路⼝红绿灯设置不合理,就可能导致⼤⽚堵车,电⼦在芯⽚上跑来跑去,稍微有个 PN 结出问题,电⼦同样会堵车,所以芯⽚的设计异常重要 芯⽚制造的过程就如同⽤乐⾼盖房⼦⼀样,先有晶圆作为地基,再层层往上叠的芯⽚制造流程后,就可产出必要的芯⽚(后⾯会介绍),然⽽,没有设计图,拥有再强制造能⼒都没有⽤1. 规格制定在 IC 设计中,最重要的步骤就是规格制定,这个步骤就像是在设计建筑前,先决定要⼏间房间、浴室,有什么建筑法规需要遵守,在确定好所有的功能之后在进⾏设计,这样才不⽤再花额外的时间进⾏后续修改第⼀步:确定 IC 的⽬的、效能为何,对⼤⽅向做设定第⼆步:察看需要何种协议,否则芯⽚将⽆法和市⾯上的产品相容第三步:确⽴ IC 的实作⽅法,将不同功能分配成不同的单元,并确⽴不同单元间连结的⽅法,如此便完成规格的制定 2. 设计芯⽚细节这个步骤就像初步记下建筑的规画,将整体轮廓描绘出来,⽅便后续制图。
在 IC 芯⽚中,便是使⽤硬体描述语⾔(HDL)将电路描写出来。
常使⽤的 HDL 有Verilog、VHDL等,藉由程式码便可轻易地将⼀颗 IC 功能表达出来。
接着就是检查程式功能的正确性并持续修改,直到它满⾜期望的功能为⽌ 3. 设计蓝图在 IC 设计中,逻辑合成这个步骤便是将确定⽆误的 HDL code,放⼊电⼦设计⾃动化⼯具(EDA tool),让电脑将 HDL code 转换成逻辑电路,产⽣如下的电路图,之后,反复的确定此逻辑闸设计图是否符合规格并修改,直到功能正确为⽌ 4. 电路布局与绕线将合成完的程式码再放⼊另⼀套EDA tool,进⾏电路布局与绕线(Place And Route)。
在经过不断的检测后,便会形成如下的电路图。
图中可以看到蓝、红、绿、黄等不同颜⾊,每种不同的颜⾊就代表着⼀张光罩 ▲常⽤的演算芯⽚- FFT 芯⽚,完成电路布局与绕线的结果 5.光罩⼀颗IC 会产⽣多张的光罩,这些光罩有上下层的分别,每层有各⾃的任务。
纳米集成电路制造工艺-电介质薄膜沉积工艺
纳米集成电路制造工艺-电介质薄膜沉积工艺前言电介质在集成电路中主要提供器件、栅极和金属互连间的绝缘,选择的材料主要是氧化硅和氮化硅等,沉积方法主要是化学气相沉积(CVD)。
随着技术节点的不断演进,目前主流产品已经进入65/45nm的世代,32/28nm产品的技术也已经出现,为了应对先进制程带来的挑战,电介质薄膜必须不断引入新的材料和新的工艺。
电介质是能够被电极化的绝缘体。
电介质的带电粒子是被原子、分子的内力或分子间的力紧密束缚着,因此这些粒子的电荷为束缚电荷。
在外电场作用下,这些电荷也只能在微观范围内移动,产生极化。
在静电场中,电介质内部可以存在电场,这是电介质与导体的基本区别。
在电磁学里,当给电介质施加一个电场时,由于电介质内部正负电荷的相对位移,会产生电偶极子,这现象称为电极化。
施加的电场可能是外电场,也可能是嵌入电介质内部的自由电荷所产生的电场。
因为电极化而产生的电偶极子称为“感应电偶极子”,其电偶极矩称为“感应电偶极矩”。
在栅极电介质的沉积方面,为了在降低电介质EOT(等效氧化物厚度)的同时,解决栅极漏电的问题,必须提高材料的k值。
在130/90/65nm乃至45nm的世代,对传统热氧化生成的氧化硅进行氮化,生成氮氧化硅是提高k值的一种有效方法。
而且氮氧化硅在提高材料k值和降低栅极漏电的同时,还可以阻挡来自多晶硅栅内硼对器件的不利影响,工艺的整合也相对简单。
到45/32nm以后,即使采用氮氧化硅也无法满足器件对漏电的要求,高k介质的引入已经成为必然。
Intel公司在45nm已经采用了高k的栅极介质(主要是氧化铪基的材料,k值约为25),器件的漏电大幅降低一个数量级。
在后端的互连方面,主要的挑战来自RC延迟。
为了降低RC延迟,电介质的k值必须随着技术节点不断降低。
从180/130nm采用掺氟的氧化硅(FSG)到90/65/45nm采用致密掺碳的氧化硅(SiCOH),再到32nm以后的多孔的掺碳氧化硅(p-SiCOH),材料的k值从3.5到3.0~2.7,再到小于2.5。
- 1、下载文档前请自行甄别文档内容的完整性,平台不提供额外的编辑、内容补充、找答案等附加服务。
- 2、"仅部分预览"的文档,不可在线预览部分如存在完整性等问题,可反馈申请退款(可完整预览的文档不适用该条件!)。
- 3、如文档侵犯您的权益,请联系客服反馈,我们会尽快为您处理(人工客服工作时间:9:00-18:30)。
13
CT v k sY N
Ea k s k0 exp kT
表面(反应)控制,对温度 特别敏感
2、如果hG<<ks,则CS≈0,这是质量传输控制过程
有
CT v hGY N
质量输运控制,对温度不敏感
半导体制造工艺基础
第八章 薄膜淀积 (上)
生长速率和温度的关系
T对ks的影响较hG 大许多,因此: hG<<ks质量传 输控制过程出现 斜率与激活能 在高温
hG≈constant Ea成正比
14
hG>>ks表面控制 过程在较低温度 出现
硅外延:Ea=1.6 eV
半导体制造工艺基础
第八章 薄膜淀积 (上)
以硅外延为例(1 atm,APCVD)
15
hG 常数
外延硅淀积往往是 在高温下进行,以 确保所有硅原子淀 积时排列整齐,形 成单晶层。为质量 输运控制过程。此 时对温度控制要求 不是很高,但是对 气流要求高。
化学气相淀积的基淀积 (上)
生长动力学
从简单的生长模型出发,用 动力学方法研究化学气相淀 积推导出生长速率的表达式 及其两种极限情况
与热氧化生长稍有 不同的是,没有了 在SiO2中的扩散流
10
F1是反应剂分子的粒子流密度 F2代表在衬底表面化学反应消耗的反应剂分子流密度
半导体制造工艺基础
第八章 薄膜淀积 (上)
单晶硅外延要采用图中的卧式反应设备, 放置硅片的石墨舟为什么要有倾斜?
17
半导体制造工艺基础
第八章 薄膜淀积 (上)
18
这里界面层厚度s是x方向平板长度的函数。
hG
DG
为气体粘度 为气体密度
s
U为气体速度
x s ( x) U
随着x的增加,s(x)增加,hG下降。如果淀 积受质量传输控制,则淀积速度会下降 沿支座方向反应气体浓度的减少, 同样导致 淀积速度会下降
8
半导体制造工艺基础
第八章 薄膜淀积 (上)
(1)反应剂被携带气体引入反应器 后,在衬底表面附近形成“滞留 层”,然后,在主气流中的反应剂 越过边界层扩散到硅片表面 (2)反应剂被吸附在硅片表面,并 进行化学反应
9
(3)化学反应生成的固态物质, 即所需要的淀积物,在硅片表 面成核、生长成薄膜 (4)反应后的气相副产物,离 开衬底表面,扩散回边界层, 并随输运气体排出反应室
表面反应控制:温度 质量输运控制:反应器形状, 硅片放置
的单晶层,晶向取决于衬底
半导体制造工艺基础
第八章 薄膜淀积 (上)
5
多晶硅薄膜的应用
CMOS栅电极材料;多层金属化电极的导电材料
半导体制造工艺基础
第八章 薄膜淀积 (上)
6
Chemical Vapor Deposition (CVD)
Epitaxy Substrate
Single crystal (epitaxy)
半导体制造工艺基础
第八章 薄膜淀积 (上)
因此,支座倾斜可以促使s(x)沿x变化减小 原理:由于支座倾斜后,气流的流过的截面积 下降,导致气流速度的增加,进而导致s(x)沿x 减小和hG的增加。从而用加大hG的方法来补偿 沿支座长度方向的气源的耗尽而产生的淀积速 率的下降。尤其对质量传输控制的淀积至关重 要,如APCVD法外延硅。
则生长速率
k s hG CG k s hG CT F v Y N k s hG N k s hG N
N是形成薄膜的单位体积中的原子数。对硅外延N为5×1022 cm-3
半导体制造工艺基础
第八章 薄膜淀积 (上)
Y一定时, v 由hG和ks中较小者决定
1、如果hG>>ks,则Cs≈CG,这种情况为表面反应控制过程
2
半导体制造工艺基础
第八章 薄膜淀积 (上)
除了CVD和PVD外,制备薄膜的方法还有:
3
旋涂Spin-on 镀/电镀electroless plating/electroplating
铜互连是由电镀工艺制作
半导体制造工艺基础
第八章 薄膜淀积 (上)
外延硅应用举例
4
外延:在单晶衬底上生长一层新
7
半导体制造工艺基础
第八章 薄膜淀积 (上)
化学气相淀积(CVD)
单晶 (外延)、多晶、非晶(无定型)薄膜 半导体、介质、金属薄膜 常压化学气相淀积(APCVD),低压CVD (LPCVD),等离子体增强淀积(PECVD)等 CVD反应必须满足三个挥发性标准
在淀积温度下,反应剂必须具备足够高的蒸汽压 除淀积物质外,反应产物必须是挥发性的 淀积物本身必须具有足够低的蒸气压
19
半导体制造工艺基础
第八章 薄膜淀积 (上)
本节课主要内容
20
常用的淀积薄膜有哪些? 举例说明其用途。 什么是CVD?描述它的 工艺过程。 CVD的控制有哪两种 极限状态?分别控制什 么参数是关键?
单晶硅(外延)—器件;多晶 硅—栅电极;SiO2—互连介质; Si3N4—钝化。金属… 化学气相淀积:反应剂被激活 后在衬底表面发生化学反应成 膜。1)主气流中的反应剂越过 边界层扩散到硅片表面;2)反 应剂被吸附在硅片表面;3)反 应成核生长;4)副产物挥发。
1
半导体制造工艺基础
第八章 薄膜淀积 (上)
设
12
CG Y CT
这里 Y 为在气体中反应剂分子的摩尔比值, CG为每cm3中反应剂分子数,这里CT为在 气体中每cm3的所有分子总数
CG PG PG Y CT PTotal PG PG1 PG 2 ....
PG 是反应剂分子的分压,PG1, PG1 PG2 PG3…..等是系统中其它气体的分压
半导体制造工艺基础
第八章 薄膜淀积 (上)
F1 hG (CG C S )
hG 是质量输运系数(cm/sec)
11
F2 ksCS
ks 是表面化学反应系数(cm/sec) 在稳态,两类粒子流密度应相等。这样得到
F F1 F2
可得:
ks CS CG 1 hG
1)化学气相淀积 — Chemical Vapor Deposition (CVD) 一种或数种物质的气体,以某种方式激活后,在衬底表面发生 两 化学反应,并淀积出所需固体薄膜的生长技术。 类 例如:APCVD, LPCVD, PECVD, HDPCVD 主 要 2)物理气相淀积 — Physical Vapor Deposition (PVD) 的 淀 利用某种物理过程实现物质的转移,即将原子或分子转移到衬 积 底(硅)表面上,并淀积成薄膜的技术。 方 例如:蒸发 evaporation,溅射sputtering 式
多晶硅生长是在低 温进行,是表面反 应控制,对温度要 求控制精度高。
Ea 值相同
半导体制造工艺基础
第八章 薄膜淀积 (上) 当工作在高温区,质量控制为主导,hG是常数, 此时反应气体通过边界层的扩散很重要,即反 应腔的设计和晶片如何放置显得很重要。
16
记住关键两点:
ks 控制的淀积 主要和温度有关 hG 控制的淀积 主要和反应腔体几何形状有关
Courtesy Johan Pejnefors, 2001
Polycrystalline
半导体制造工艺基础
第八章 薄膜淀积 (上)
对薄膜的要求
1. 组分正确,玷污少,电学和机械性能好
2. 片内及片间(每一硅片和硅片之间)均匀性好 3. 台阶覆盖性好(conformal coverage — 保角覆盖) 4. 填充性好 5. 平整性好
半导体制造工艺基础
第八章 薄膜淀积 (上)
在集成电路制 备中,很多薄 膜材料由淀积 工艺形成
Deposition
1
半导体薄膜:Si 介质薄膜:SiO2,Si3N4,
BPSG,… 多晶薄膜:poly-Si 金属薄膜:Al,Cu,W,Ti,…
单晶薄膜:Si, SiGe(外延)
半导体制造工艺基础
第八章 薄膜淀积 (上)