半导体工艺干法刻蚀铝刻蚀
半导体八大工艺顺序

半导体八大工艺顺序半导体制造是一个复杂的过程,需要经过八个主要的工艺步骤才能完成。
这些工艺步骤包括晶圆清洗、沉积、光刻、蚀刻、清洗、离子注入、退火和测试。
下面将对这些工艺步骤进行详细介绍。
1. 晶圆清洗晶圆清洗是制造半导体的第一步,目的是去除晶圆表面的杂质和污染物,以确保后续工艺的顺利进行。
晶圆清洗通常使用化学物质和超声波来实现。
首先将晶圆浸泡在去离子水中,然后使用化学物质和超声波来去除表面污染物。
2. 沉积沉积是将材料沉积在晶圆表面的过程。
这个过程通常使用化学气相沉积(CVD)或物理气相沉积(PVD)来实现。
在CVD中,化学反应会产生气体,然后将其放置在晶圆上,在高温下发生反应并形成所需的材料层。
在PVD中,原子或分子会通过真空管道传输到晶圆表面,然后在晶圆表面生成所需的材料层。
3. 光刻光刻是将图案转移到晶圆表面的过程。
这个过程通常使用光刻胶和掩模来实现。
首先,在晶圆表面涂上一层光刻胶,然后将掩模放置在光刻胶上,并使用紫外线照射掩模。
这会使光刻胶在掩模的开口处固化,形成所需的图案。
4. 蚀刻蚀刻是将材料从晶圆表面移除的过程。
这个过程通常使用干法或湿法蚀刻来实现。
在干法蚀刻中,使用等离子体或化学反应来去除不需要的材料层。
在湿法蚀刻中,使用化学物质来溶解不需要的材料层。
5. 清洗清洗是去除蚀刻残留物和其他污染物的过程。
这个过程通常使用酸、碱和有机溶剂来实现。
首先将晶圆浸泡在酸、碱或有机溶剂中,然后用去离子水冲洗干净。
6. 离子注入离子注入是将离子注入晶圆表面的过程。
这个过程通常用于形成掺杂层和修饰材料的电学性质。
在离子注入过程中,使用加速器将离子加速到非常高的速度,然后将它们注入晶圆表面。
7. 退火退火是在高温下加热晶圆以改善其电学性质的过程。
在退火过程中,晶圆被放置在高温炉中,并暴露于高温下一段时间。
这会使掺杂层扩散并形成所需的电学性质。
8. 测试测试是检查芯片是否正常运行的过程。
这个过程通常使用测试设备来实现。
半导体刻蚀工艺技术——ICP.
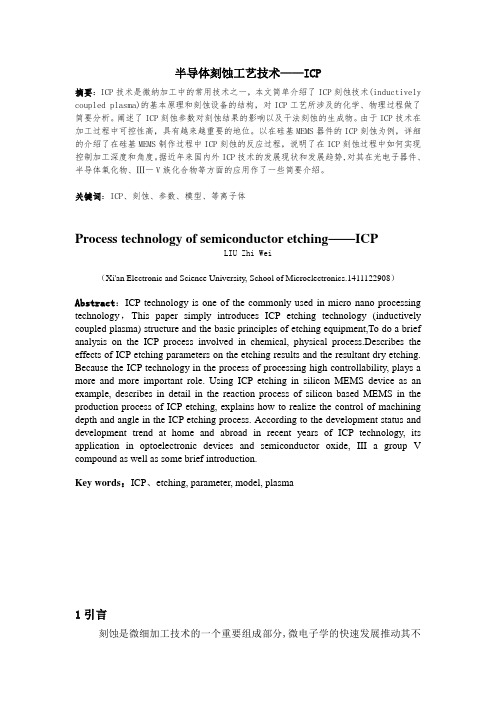
半导体刻蚀工艺技术——ICP摘要:ICP技术是微纳加工中的常用技术之一,本文简单介绍了ICP刻蚀技术(inductively coupled plasma)的基本原理和刻蚀设备的结构,对ICP工艺所涉及的化学、物理过程做了简要分析。
阐述了ICP刻蚀参数对刻蚀结果的影响以及干法刻蚀的生成物。
由于ICP技术在加工过程中可控性高,具有越来越重要的地位。
以在硅基MEMS器件的ICP刻蚀为例,详细的介绍了在硅基MEMS制作过程中ICP刻蚀的反应过程,说明了在ICP刻蚀过程中如何实现控制加工深度和角度。
据近年来国内外ICP技术的发展现状和发展趋势,对其在光电子器件、半导体氧化物、Ⅲ一V族化合物等方面的应用作了一些简要介绍。
关键词:ICP、刻蚀、参数、模型、等离子体Process technology of semiconductor etching——ICPLIU Zhi Wei(Xi'an Electronic and Science University, School of Microelectronics.1411122908)Abstract:ICP technology is one of the commonly used in micro nano processing technology,This paper simply introduces ICP etching technology (inductively coupled plasma) structure and the basic principles of etching equipment,To do a brief analysis on the ICP process involved in chemical, physical process.Describes the effects of ICP etching parameters on the etching results and the resultant dry etching. Because the ICP technology in the process of processing high controllability, plays a more and more important role. Using ICP etching in silicon MEMS device as an example, describes in detail in the reaction process of silicon based MEMS in the production process of ICP etching, explains how to realize the control of machining depth and angle in the ICP etching process. According to the development status and development trend at home and abroad in recent years of ICP technology, its application in optoelectronic devices and semiconductor oxide, III a group V compound as well as some brief introduction.Key words:ICP、etching, parameter, model, plasma1引言刻蚀是微细加工技术的一个重要组成部分,微电子学的快速发展推动其不断向前。
综述报告——刻蚀简介

微加工技术——刻蚀简介自从半导体诞生以来,很大程度上改变了人类的生产和生活。
半导体除了在计算机领域应用之外,还广泛地应用于通信、网络、自动遥控及国防科技领域。
本文主要介绍半导体制造工艺中的刻蚀工艺。
随着半导体制造大规模集成电路技术的发展,图形加工线条越来越细,硅片尺寸越来越大,对刻蚀工艺的要求也越来高。
因此,学习了解刻蚀工艺十分必要。
本文将主要从刻蚀简介、刻蚀参数及现象、干法刻蚀和湿法刻蚀四个方面进行论述。
1、刻蚀简介1.1 刻蚀定义及目的刻蚀就是用化学的、物理的或同时使用化学和物理的方法,有选择地把没有被抗蚀剂掩蔽的那一部分薄膜层除去,从而在薄膜上得到和抗蚀剂膜上完全一致的图形。
刻蚀的基本目的,是在涂光刻胶(或有掩膜)的硅片上正确的复制出掩膜图形[1]。
刻蚀,通常是在光刻工艺之后进行。
通过刻蚀,在光刻工艺之后,将想要的图形留在硅片上。
从这一角度而言,刻蚀可以被称之为最终的和最主要的图形转移工艺步骤。
在通常的刻蚀过程中,有图形的光刻胶层〔或掩膜层)将不受到腐蚀源显著的侵蚀或刻蚀,可作为掩蔽膜,保护硅片上的部分特殊区域,而未被光刻胶保护的区域,则被选择性的刻蚀掉。
其工艺流程示意图如下。
1.2 刻蚀的分类从工艺上分类的话,在半导体制造中有两种基本的刻蚀工艺:干法刻蚀和湿法腐蚀。
干法刻蚀,是利用气态中产生的等离子体,通过经光刻而开出的掩蔽层窗口,与暴露于等离子体中的硅片行物理和化学反应,刻蚀掉硅片上暴露的表面材料的一种工艺技术法[1]。
该工艺技术的突出优点在于,是各向异性刻蚀(侧向腐蚀速度远远小于纵向腐蚀速度,侧向几乎不被腐蚀),因此可以获得极其精确的特征图形。
超大规模集成电路的发展,要求微细化加工工艺能够严格的控制加工尺寸,要求在硅片上完成极其精确的图形转移。
任何偏离工艺要求的图形或尺寸,都可能直接影响产品性能或品质,给生产带来无法弥补的损害。
由于干法刻蚀技术在图形转移上的突出表现,己成为亚微米尺寸下器件刻蚀的最主要工艺方法。
金属铝刻蚀工艺简介

在金属铝中通常会加入少量的硅和铜来提
高电子器件的可靠性。硅和Cl反应生成挥发性的
SiCl ,很容易被带出反应腔。铜与Cl反应生成的 4
CuCl2 挥发性却不高,因此需要加大物理性的离 子轰击把铜原子去掉,一般可以通过加大 Ar 和
AlCl 被气流带出反应腔。BCl 一方面提供BCl +,
3
3
3
垂直轰击硅片表面,达到各向异性的刻蚀。另一
方面,由于铝表面极易氧化成氧化铝,这层自生
氧化铝在刻蚀的初期阻隔了 Cl 和铝的接触,阻 2
碍了刻蚀的进一步进行。添加 BCl 则利于将这 3
层氧化层还原(如方程式 1),促进刻蚀过程的继
续进行。
基础知识 HOW TO MAKE A CHIP
金属铝刻蚀工艺简介
在 集成电路的制造过程中,刻蚀就是利 用化学或物理方法有选择性地从硅片 表面去除不需要的材料的过程。从工
艺上区分,刻蚀可以分为湿法刻蚀和干法刻蚀。
前者的主要特点是各向同性刻蚀;后者是利用等
离子体来进行各向异性刻蚀,可以严格控制纵向
和横向刻蚀。
蚀和氮化钛刻蚀等。目前,金属铝作为连线材
料,仍然广泛用于 DRAM 和 flash 等存储器,以
及 0.13um 以上的逻辑产品中。本文着重介绍金
属铝的刻蚀工艺。
金属铝刻蚀通常用到以下气体:Cl 、BCl 、
2
3
Ar、 N 、CHF 和 C H 等。Cl 作为主要的刻蚀气
2
3
24
2
体,与铝发生化学反应,生成的可挥发的副产物
半导体八大工艺顺序

半导体八大工艺顺序半导体八大工艺顺序,是指半导体制造过程中的八个主要工艺步骤。
这些工艺步骤包括晶圆清洗、光刻、沉积、刻蚀、扩散、离子注入、退火和包封。
下面将逐一介绍这些工艺步骤的顺序及其作用。
1. 晶圆清洗晶圆清洗是半导体制造过程中的第一步。
在这一步骤中,晶圆将被放入化学溶液中进行清洗,以去除表面的杂质和污染物。
这样可以确保后续工艺步骤的顺利进行,同时也可以提高器件的质量和性能。
2. 光刻光刻是半导体制造中的关键工艺步骤之一。
在这一步骤中,将使用光刻胶覆盖在晶圆表面上,并通过光刻机将图形投射到光刻胶上。
然后,利用化学溶液将未曝光的光刻胶去除,从而形成所需的图形。
3. 沉积沉积是指在晶圆表面上沉积一层薄膜的工艺步骤。
这一层薄膜可以用于改变晶圆表面的性质,增加其导电性或绝缘性。
常用的沉积方法包括化学气相沉积和物理气相沉积。
4. 刻蚀刻蚀是将多余的材料从晶圆表面去除的工艺步骤。
在这一步骤中,利用化学溶液或等离子刻蚀机将不需要的材料去除,从而形成所需的图形和结构。
5. 扩散扩散是将杂质或掺杂物diffused 到晶圆中的工艺步骤。
这一步骤可以改变晶圆的电学性质,并形成PN 结等器件结构。
常用的扩散方法包括固体扩散和液相扩散。
6. 离子注入离子注入是将离子注入到晶圆中的工艺步骤。
这可以改变晶圆的导电性和掺杂浓度,从而形成电子器件的结构。
离子注入通常在扩散之前进行。
7. 退火退火是将晶圆加热至一定温度并保持一段时间的工艺步骤。
这可以帮助晶圆中的杂质扩散和掺杂物活化,从而提高器件的性能和稳定性。
8. 包封包封是将晶圆封装在外部保护材料中的工艺步骤。
这可以保护晶圆不受外部环境的影响,同时也可以方便晶圆的安装和使用。
半导体制造过程中的八大工艺顺序是一个复杂而精密的过程。
每个工艺步骤都起着至关重要的作用,只有严格按照顺序进行,才能生产出高质量的半导体器件。
希望通过本文的介绍,读者对半导体制造过程有了更深入的了解。
半导体八大工艺顺序
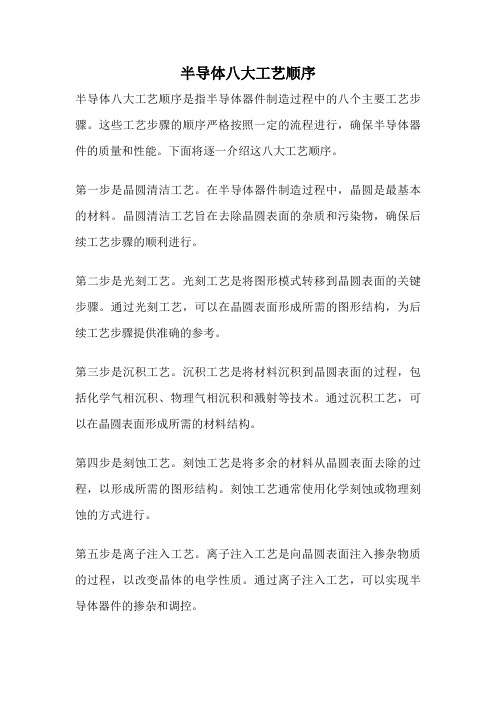
半导体八大工艺顺序半导体八大工艺顺序是指半导体器件制造过程中的八个主要工艺步骤。
这些工艺步骤的顺序严格按照一定的流程进行,确保半导体器件的质量和性能。
下面将逐一介绍这八大工艺顺序。
第一步是晶圆清洁工艺。
在半导体器件制造过程中,晶圆是最基本的材料。
晶圆清洁工艺旨在去除晶圆表面的杂质和污染物,确保后续工艺步骤的顺利进行。
第二步是光刻工艺。
光刻工艺是将图形模式转移到晶圆表面的关键步骤。
通过光刻工艺,可以在晶圆表面形成所需的图形结构,为后续工艺步骤提供准确的参考。
第三步是沉积工艺。
沉积工艺是将材料沉积到晶圆表面的过程,包括化学气相沉积、物理气相沉积和溅射等技术。
通过沉积工艺,可以在晶圆表面形成所需的材料结构。
第四步是刻蚀工艺。
刻蚀工艺是将多余的材料从晶圆表面去除的过程,以形成所需的图形结构。
刻蚀工艺通常使用化学刻蚀或物理刻蚀的方式进行。
第五步是离子注入工艺。
离子注入工艺是向晶圆表面注入掺杂物质的过程,以改变晶体的电学性质。
通过离子注入工艺,可以实现半导体器件的掺杂和调控。
第六步是热处理工艺。
热处理工艺是将晶圆置于高温环境中进行退火、烘烤或氧化等处理的过程。
通过热处理工艺,可以改善晶体的结晶质量和电学性能。
第七步是清洗工艺。
清洗工艺是在制造过程中对晶圆进行清洗和去除残留污染物的过程,以确保半导体器件的质量和可靠性。
第八步是封装测试工艺。
封装测试工艺是将完成的半导体器件封装成最终产品,并进行性能测试和质量检验的过程。
通过封装测试工艺,可以确保半导体器件符合规格要求,并具有稳定可靠的性能。
总的来说,半导体八大工艺顺序是半导体器件制造过程中的关键步骤,每个工艺步骤都至关重要,任何一环节的不慎都可能影响整个制造过程的质量和性能。
通过严格按照八大工艺顺序进行制造,可以确保半导体器件具有优良的性能和可靠性,从而满足现代电子产品对半导体器件的高要求。
半导体干法蚀刻的介绍

半导体干法蚀刻的介绍《半导体干法蚀刻:新兴技术的应用与发展》引言:半导体干法蚀刻是一种关键的制造工艺,在半导体行业中有着广泛的应用。
本文将着重介绍半导体干法蚀刻的原理、特点以及其在新兴技术领域的应用与发展。
正文:一、半导体干法蚀刻的原理半导体干法蚀刻是利用气体或等离子体与半导体表面发生反应来实现物质的去除。
通过将气体或者气体混合物注入到真空环境中,让气体产生等离子体,利用等离子体中的活性粒子或自由基对半导体表面进行化学反应或破坏性物理反应,从而移除半导体表面的一层材料。
二、半导体干法蚀刻的特点1. 制程精度高:通过控制反应气体、温度、时间等参数,可以实现较高的制程精度,满足半导体器件的要求。
2. 制程可控性强:半导体干法蚀刻过程中可以精确控制蚀刻速率和选择性,从而实现对半导体的精确加工。
3. 无需接触:与湿法蚀刻相比,半导体干法蚀刻是一种无需接触半导体表面的加工方式,可以避免因接触引起的损伤和污染。
4. 适用性广:半导体干法蚀刻可以适用于各种材料,包括硅、氮化硅、氮化铝等,可满足不同材料的蚀刻需求。
5. 环保高效:半导体干法蚀刻是一种无废液产生的加工方式,不会对环境造成污染,同时也节约了大量的水资源。
三、半导体干法蚀刻在新兴技术的应用与发展1. 三维芯片制造:随着半导体器件的发展,传统的二维芯片逐渐无法满足需求。
半导体干法蚀刻可以实现对芯片表面的精确加工,为三维芯片制造提供了重要工艺支持。
2. 纳米加工:随着纳米科技的快速发展,半导体干法蚀刻在纳米加工中广泛应用。
通过控制蚀刻参数,可以实现纳米尺寸的结构制造,为纳米电子学和纳米光学等领域的研究提供了有力支持。
3. 新型材料加工:随着新型材料的涌现,传统的湿法蚀刻技术面临挑战。
半导体干法蚀刻可以适用于新型材料的加工,如氮化硅、氮化铝等,为新型材料的应用拓展提供了技术保障。
结论:半导体干法蚀刻是一种重要的制造工艺,具有制程精度高、制程可控性强、适用性广、环保高效等特点。
半导体芯片干法刻蚀工艺
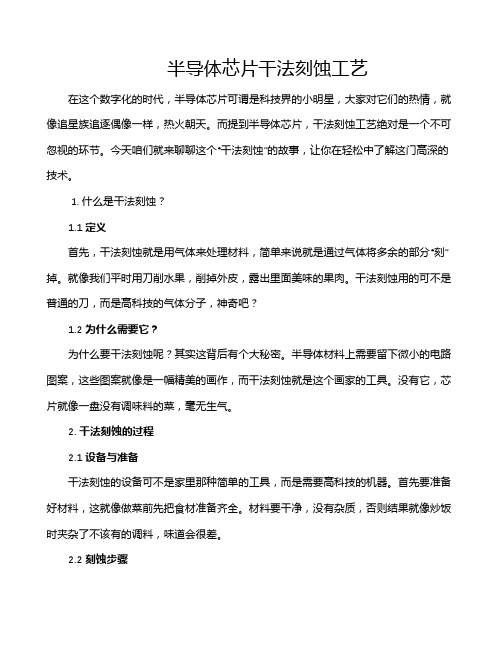
半导体芯片干法刻蚀工艺在这个数字化的时代,半导体芯片可谓是科技界的小明星,大家对它们的热情,就像追星族追逐偶像一样,热火朝天。
而提到半导体芯片,干法刻蚀工艺绝对是一个不可忽视的环节。
今天咱们就来聊聊这个“干法刻蚀”的故事,让你在轻松中了解这门高深的技术。
1. 什么是干法刻蚀?1.1 定义首先,干法刻蚀就是用气体来处理材料,简单来说就是通过气体将多余的部分“刻”掉。
就像我们平时用刀削水果,削掉外皮,露出里面美味的果肉。
干法刻蚀用的可不是普通的刀,而是高科技的气体分子,神奇吧?1.2 为什么需要它?为什么要干法刻蚀呢?其实这背后有个大秘密。
半导体材料上需要留下微小的电路图案,这些图案就像是一幅精美的画作,而干法刻蚀就是这个画家的工具。
没有它,芯片就像一盘没有调味料的菜,毫无生气。
2. 干法刻蚀的过程2.1 设备与准备干法刻蚀的设备可不是家里那种简单的工具,而是需要高科技的机器。
首先要准备好材料,这就像做菜前先把食材准备齐全。
材料要干净,没有杂质,否则结果就像炒饭时夹杂了不该有的调料,味道会很差。
2.2 刻蚀步骤接下来就是真正的“刻蚀”过程。
我们把准备好的材料放入刻蚀机中,然后把气体注入,气体和材料发生反应,把不需要的部分给“消灭”掉。
这一步就像是让一位雕刻家在大理石上精雕细琢,细致入微,最终形成我们想要的图案。
整个过程需要极高的温度和压力,真是热火朝天,紧张又刺激。
3. 干法刻蚀的优势与挑战3.1 优势干法刻蚀的优势可不少。
首先,它能实现高精度的刻蚀,就像精准的手艺人,毫不马虎。
此外,干法刻蚀能处理各种不同的材料,这样一来,适应性强,真是让人赞叹不已。
3.2 挑战不过,挑战也随之而来。
比如,气体的选择、刻蚀的速度等等,都是需要精确把控的,要是稍有差池,就可能导致整个工艺的失败。
这就像是在走钢丝,一不小心就得“摔”下来,真是心惊胆战。
4. 总结干法刻蚀工艺就像一门艺术,既有技术的严谨,也有创意的灵动。
- 1、下载文档前请自行甄别文档内容的完整性,平台不提供额外的编辑、内容补充、找答案等附加服务。
- 2、"仅部分预览"的文档,不可在线预览部分如存在完整性等问题,可反馈申请退款(可完整预览的文档不适用该条件!)。
- 3、如文档侵犯您的权益,请联系客服反馈,我们会尽快为您处理(人工客服工作时间:9:00-18:30)。
干法刻蚀之铝刻蚀
在集成电路的制造过程中,刻蚀就是利用化学或物理方法有选择性地从硅片表面去除不需要的材料的过程。
从工艺上区分,刻蚀可以分为湿法刻蚀和干法刻蚀。
前者的主要特点是各向同性刻蚀;后者是利用等离子体来进行各向异性刻蚀,可以严格控制纵向和横向刻蚀。
干法的各向异性刻蚀,可以用表面损伤和侧壁钝化两种机制来解释。
表面损伤机制是指,与硅片平行的待刻蚀物质的图形底部,表面的原子键被破坏,扩散至此的自由基很容易与其发生反应,使得这个方向的刻蚀得以持续进行。
与硅片垂直的图形侧壁则因为表面原子键完整,从而形态得到保护。
侧壁钝化机制是指,刻蚀反应产生的非挥发性的副产物,光刻胶刻蚀产生的聚合物,以及侧壁表面的氧化物或氮化物会在待刻蚀物质表面形成钝化层。
图形底部受到离子的轰击,钝化层会被击穿,露出里面的待刻蚀物质继续反应,而图形侧壁钝化层受到较少的离子轰击,阻止了这个方向刻蚀的进一步进行。
在半导体干法刻蚀工艺中,根据待刻蚀材料的不同,可分为金属刻蚀、介质刻蚀和硅刻蚀。
金属刻蚀又可以分为金属铝刻蚀、金属钨刻蚀和氮化钛刻蚀等。
目前,金属铝作为连线材料,仍然广泛用于DRAM和flash等存储器,以及0.13um 以上的逻辑产品中。
本文着重介绍金属铝的刻蚀工艺。
金属铝刻蚀通常用到以下气体:Cl2、BCl3、Ar、 N2、CHF3和C2H4等。
Cl2作为主要的刻蚀气体,与铝发生化学反应,生成的可挥发的副产物AlCl3被气流带出反应腔。
BCl3一方面提供BCl3+,垂直轰击硅片表面,达到各向异性的刻蚀。
另一方面,由于铝表面极易氧化成氧化铝,这层自生氧化铝在刻蚀的初期阻隔了Cl2和铝的接触,阻碍了刻蚀的进一步进行。
添加BCl3 则利于将这层氧化层还原(如方程式1),促进刻蚀过程的继续进行。
Al2O3 + 3BCl3→ 2AlCl3 + 3BOCl (1)
Ar电离生成Ar+,主要是对硅片表面提供物理性的垂直轰击。
N2、CHF3和C2H4是主要的钝化气体,N2与金属侧壁氮化产生的AlxNy,CHF3和C2H4与光刻胶反应生成的聚合物会沉积在金属侧壁,形成阻止进一步反应的钝化层。
一般来说,反应腔的工艺压力控制在6-14毫托。
压力越高,在反应腔中的Cl2浓度越高,刻蚀速率越快。
压力越低,分子和离子的碰撞越少,平均自由程增加,离子轰击图形底部的能力增强,这样刻蚀反应速率不会降低甚至于停止于图形的底部。
目前金属刻蚀机台广泛采用双射频功率源设计,如应用材料公司DPS(decouple plasma source)金属刻蚀机台。
偏置功率用来加速正离子,提供垂直的物理轰击,源功率
用来提高反应腔体内的等离子体的浓度。
这种双功率的设计可以实现对离子体的能量和浓度的独立控制,扩大了刻蚀工艺的工艺窗口和性能。
在金属铝的上下通常会淀积金属钛或氮化钛,形成氮化钛/铝/氮化钛/钛的结构。
用来刻蚀铝的Cl2与钛反应生成挥发性相对较低的TiCl4,刻蚀氮化钛的速率只有刻蚀铝的1/3-1/4,因此减少Cl2或是增加BCl3和偏置功率,都有利于提高氮化钛和钛的刻蚀速率。
在金属铝中通常会加入少量的硅和铜来提高电子器件的可靠性。
硅和Cl反应生成挥发性的SiCl4,很容易被带出反应腔。
铜与Cl反应生成的CuCl2挥发性却不高,因此需要加大物理性的离子轰击把铜原子去掉,一般可以通过加大Ar和增加偏置功率来实现。
当铝刻蚀完成之后,硅片表面、图形侧壁和光刻胶表面残留的Cl,会和铝反应生成AlCl3,继而与空气中的水分发生自循环反应(如方程式2),造成对铝的严重侵蚀(corrosion)。
因此,在刻蚀工艺完成后,一般会用H2O和O2的等离子体把氯和光刻胶去除, 并且在铝表面形成氧化铝来保护铝。