圆柱蜗杆传动设计计算
蜗杆传动设计

14
3.34
15
3.22
16
3.07
17
2.96
18
2.89
19
2.82
20
2.76
22
2.66
24
2.57
26
2.51
Z2 YF2
28 2.48
30 2.44
35 2.36
40 2.32
45 2.27
50 2.24
60 2.20
70 2.17
80 2.14
90 2.12
100 2.10
150 2.07
Fnc = K Fn
载荷系数K=l~1.4
3、蜗轮齿面的接触强度计算
校核公式: 设计公式:
H 500
KT2 KT 500 2 2 2 [ H ] d1d2 2 m d1 z2
2
500 2 m d1 KT2 z2 [ H ]
4、蜗轮轮齿齿根弯曲强度计算
1.53KT2 cos YF 2 F 校核公式: F d1d 2 m 1.53KT2 cos 设计公式: m2 d1 YF 2 z2 F
表2-9-6 蜗轮的齿形系数YF2(α=20°,ha*=1)
Z2
YF2
10
4.55
11
4.14
12
3.70
13
3.55
(a)圆柱蜗杆传动
(b)圆环面蜗杆传动
(c)锥面蜗杆传动
阿基米德蜗杆
渐开线蜗杆
法向直廓蜗杆 圆弧圆柱蜗杆
(2)按蜗杆旋向不同来分类,蜗杆传动可以分成左旋和右旋蜗杆 传动两种类型 。 (3)按工作条件不同分类蜗杆传动可以分为闭式蜗杆传动和开式 蜗杆传动两种类型。 2、蜗杆传动的特点 (1)蜗杆传动的最大特点是结构紧凑、传动比大。i=10~40,最 大可达80。若只传递运动(分度运动),其传动比可达1000。 (2)传动平稳、噪声小 (3)可制成具有自锁性的蜗杆 (4)传动效率低 (5)制造成本高 二、蜗杆传动的主要参数和几何尺寸 中间平面:通过蜗杆轴线并垂直于蜗轮轴线的平面称为中间平面。 在中间平面上蜗轮与蜗杆的啮合相当于渐开线齿轮与齿条的啮合。 因此蜗杆传动的设计计算都以中间平面上的参数和几何关系为准。
蜗杆外径计算公式
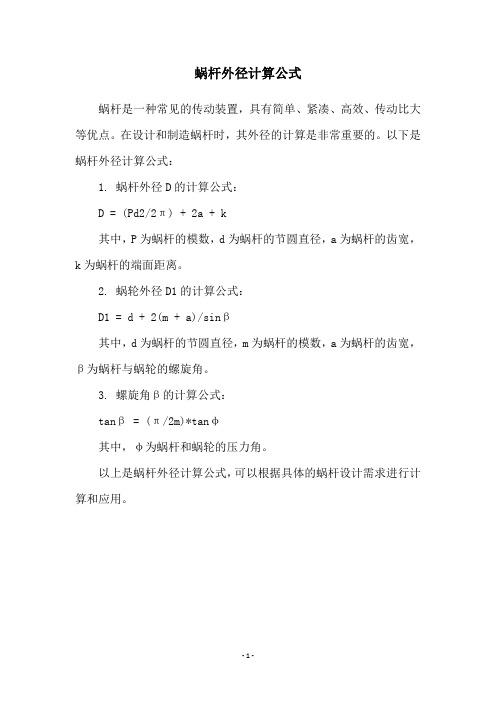
蜗杆外径计算公式
蜗杆是一种常见的传动装置,具有简单、紧凑、高效、传动比大等优点。
在设计和制造蜗杆时,其外径的计算是非常重要的。
以下是蜗杆外径计算公式:
1. 蜗杆外径D的计算公式:
D = (Pd2/2π) + 2a + k
其中,P为蜗杆的模数,d为蜗杆的节圆直径,a为蜗杆的齿宽,k为蜗杆的端面距离。
2. 蜗轮外径D1的计算公式:
D1 = d + 2(m + a)/sinβ
其中,d为蜗杆的节圆直径,m为蜗杆的模数,a为蜗杆的齿宽,β为蜗杆与蜗轮的螺旋角。
3. 螺旋角β的计算公式:
tanβ = (π/2m)*tanφ
其中,φ为蜗杆和蜗轮的压力角。
以上是蜗杆外径计算公式,可以根据具体的蜗杆设计需求进行计算和应用。
- 1 -。
蜗轮蜗杆设计参数
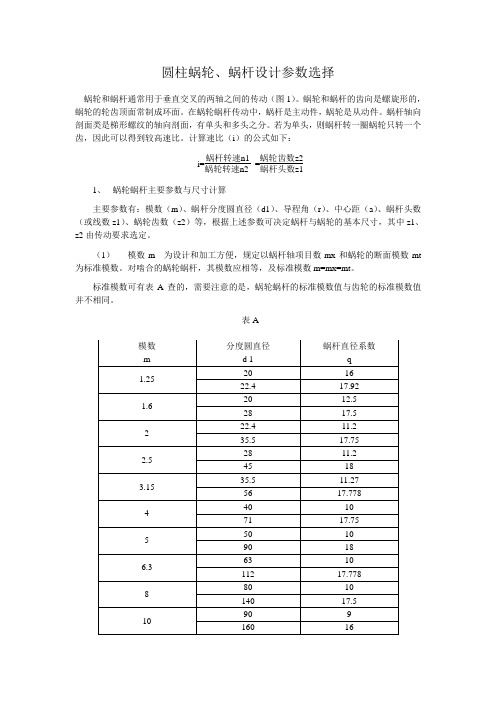
圆柱蜗轮、蜗杆设计参数选择蜗轮和蜗杆通常用于垂直交叉的两轴之间的传动(图1)。
蜗轮和蜗杆的齿向是螺旋形的,蜗轮的轮齿顶面常制成环面。
在蜗轮蜗杆传动中,蜗杆是主动件,蜗轮是从动件。
蜗杆轴向剖面类是梯形螺纹的轴向剖面,有单头和多头之分。
若为单头,则蜗杆转一圈蜗轮只转一个齿,因此可以得到较高速比。
计算速比(i)的公式如下:i=蜗杆转速n1蜗轮转速n2=蜗轮齿数z2蜗杆头数z11、蜗轮蜗杆主要参数与尺寸计算主要参数有:模数(m)、蜗杆分度圆直径(d1)、导程角(r)、中心距(a)、蜗杆头数(或线数z1)、蜗轮齿数(z2)等,根据上述参数可决定蜗杆与蜗轮的基本尺寸,其中z1、z2由传动要求选定。
(1)模数m 为设计和加工方便,规定以蜗杆轴项目数mx和蜗轮的断面模数mt 为标准模数。
对啮合的蜗轮蜗杆,其模数应相等,及标准模数m=mx=mt。
标准模数可有表A查的,需要注意的是,蜗轮蜗杆的标准模数值与齿轮的标准模数值并不相同。
表A图1图2(2)蜗杆分度圆直径d1 再制造蜗轮时,最理想的是用尺寸、形状与蜗杆完全相同的蜗轮滚刀来进行切削加工。
但由于同一模数蜗杆,其直径可以各不相同,这就要求每一种模数对应有相当数量直径不同的滚刀,才能满足蜗轮加工需求。
为了减少蜗轮滚刀数目,在规定标准模数的同时,对蜗杆分度圆直径亦实行了标准化,且与m 有一定的匹配。
蜗杆分度圆直径d1与轴向模数mx之比为一标准值,称蜗杆的直径系数。
即q=蜗杆分度圆直径模数=d1m d1=mq有关标准模数m 与标准分度圆直径d1的搭配值及对应的蜗杆直径系数参照表A (3) 蜗杆导程角r 当蜗杆的q 和z1选定后,在蜗杆圆柱上的导程角即被确定。
为导程角、导程和分度圆直径的关系。
tan r=导程分度圆周长 = 蜗杆头数x 轴向齿距分度圆周长 =z1px d1π =z1πm πm q =z1q相互啮合的蜗轮蜗杆,其导程角的大小与方向应相同。
(4) 中心距a 蜗轮与蜗杆两轴中心距a 与模数m 、蜗杆直径系数q 以及蜗轮齿数z2间的关系式如下:a=d1+d22 =m q(q+z2)蜗杆各部尺寸如表B蜗轮各部尺寸如表C2、 蜗轮蜗杆的画法(1) 蜗杆的规定画法 参照图1图2 (2)蜗轮的规定画法 参照图1图2 (3)蜗轮蜗杆啮合画法 参照图1图2.。
机械设计(7.2.1)--圆柱蜗杆传动主要参数和几何尺寸计算
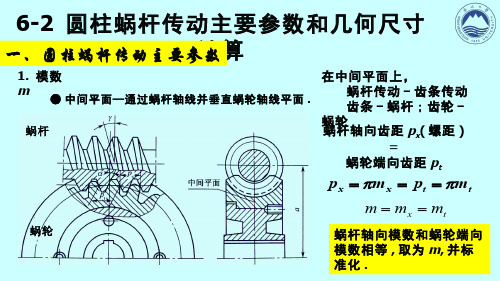
变 圆分离 ;
位 : 蜗杆分度线与蜗轮分度
中心距较标准值改 变;
位 , 减小 .
正变位 , 增大 ; 负变
(4) 变位后 , 蜗轮分度圆仍然与其节圆重 合,
但轮尺尺寸有变化 .
负变位 x2<0
标准 x2=0
正变位 x2>0 变位系数 , 过小 ,
( 变位后的 ) 实际中心距
a
a
a
1 2
(d1
● 蜗杆径向尺寸: d1= 按标准或自定 齿全高 , 齿顶高 , 齿根高及顶圆、
根圆同标准齿轮 , 无关变位 .
da1 d1 2ha1;ha1 ha*m d f 1 d1 2hf 1;hf 1 (ha* c* )m
ha* 1.0,0.8(短);c* 0.2,0.15,0.25
与链传动不同
7. 蜗轮齿数 表z26-3 给出了 z2 荐用值 ( 结合传动比和 蜗杆头数, z1=1,2,4,6) 。
为避免根切:
z1=1 , z2>17~18
z1=2 , z2>27
动力传动时,
z2<80, 根强度
避免尺寸过大 , 削弱齿
6-2 圆柱蜗杆传动主要参数和几何尺寸计算 一、圆柱蜗杆传动主要参 数
6-2 圆柱蜗杆传动主要参数和几何尺寸计算 一、圆柱蜗杆传动主要参 数
一、圆柱蜗杆传动主要参数
4. 蜗杆分度圆直径 d1(1) 为保证正确啮合,用蜗杆尺寸基
本相同的滚刀来加工蜗轮 .
(2) 为减少滚刀的数量和使之标准化 ,每个标准模数的规定了一定数量 的滚刀直径 ( 即蜗杆直径 ).
(3) 表 6-2 列出了 m 和 d1 常用标准 值.
蜗杆传动的强度计算

三、蜗杆传动的强度计算1、蜗轮齿面接触疲劳强度计算,由赫其公式(Hertz )按主平面内斜齿轮与齿条啮合进行强度计算H n E H L KF Z ][σρσ≤=∑Fn ——法向载荷(N );L ——接触线长度(注意蜗杆蜗轮接触线是倾斜的,并计入重合度);∑ρ——综合曲率半径;Z E ——材料弹性线数,对钢蜗杆↔配青铜蜗轮αMP Z E 160=,代入蜗杆传动有关参数,并化简得 校核公式:H P E H a KT Z Z ][/32σσ≤⋅= Mpa式中,Z E ——材料的弹性系数,钢蜗杆配青铜蜗轮αMP Z E 160=Z P ——接触系数,Z P 为反映蜗杆传动接触线长度和曲率半径对接触强度的影响系数 βK K K K V A ⋅⋅=——载荷系数K A ——工况系数βK ——齿面载荷分布系数:1=βK ——载荷平稳6.1~3.1=βK ——载荷变化较大,或有冲击、振动时 K V ——动载荷系数 s m V K V /3,1.1~0.12≤=——精制蜗杆s m V K V /3,2.1~1.12>=——一般蜗杆设计公式:322][⎪⎪⎭⎫ ⎝⎛≥H P E Z Z KT a σmm ⇒定m,q ,H ][σ——蜗轮齿面许用接触应力(1)当蜗轮材料为铸铁或高强度青铜,ασMP B 300≥——失效形式为胶合(不属于疲劳失效),∴许用应力H ][σ与应力循环次数N 无关。
(2)若蜗轮材料ασMP B 300<(锡青铜)——失效形式为点蚀,H ][σ与应力循环次数N 有关。
OH HN H K ][][σσ=OH ][σ——基本许用接触应力HN K ——接触强度寿命系数,8710NK HN =,N 为应力循环次数,h L jn N 260=,n 2为蜗轮转速(r/min ),L h 为蜗轮总工作时数h ,j 为每转一圈每个轮齿啮合次数。
2、蜗轮齿根弯曲疲劳强度计算齿根折断一般发生在Z 2>90,及开式传动中,∴在闭式传动中弯曲强度计算作为校核计算对于重载传动,通过计算还可差别由于轮齿的弯曲变形量引起的轮齿弹性变形量是否过大而影响蜗杆传动的平稳性。
普通圆柱蜗杆传动基本几何尺寸计算关系式
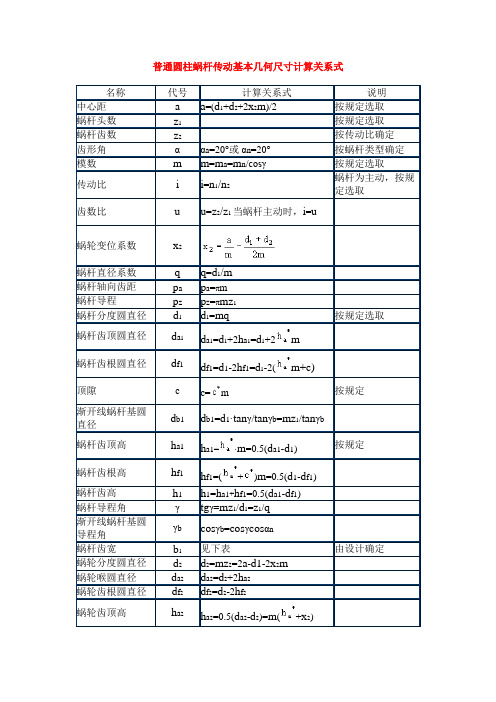
名称
代号
计算关系式
说明
中心距
a
a=(d1+d2+2x2m)/2
按规定选取
蜗杆头数
z1
按规定选取
蜗杆齿数
z2
按传动比确定
齿形角
α
αa=20°或αn=20°
按蜗杆类型确定
模数
m
m=ma=mn/cosγ
按规定选取
传动比
i
i=n1/n2
蜗杆为主动,按规定选取
齿数比
u
u=z2/z1当蜗杆主动时,i=u
经磨削的蜗杆,按左式所求的长度应再增加下列值:
当m<10mm时,增加25mm;
当m=10~16mm时,增加35~40mm;
当m>16mm时,增加50mm;
2
≤da2+1.5m
4
≤0.67da1
≤da2+m
0
-0.5
-1.0
0.5
1.0
≥(12.5+0.09z2)m
≥(9.5+0.09z2)m
≥(10.5+z1)m
蜗轮咽喉母圆半径
rg2
rg2=a-0.5da2
蜗轮齿宽
b2
由设计确定
蜗轮齿宽角
θ
θ=2arcsin(b2/d1)
蜗杆轴向齿厚
sa
sa=0.5πm
蜗杆法向齿厚
sn
sn=sa·cosγ
蜗轮齿厚
st
按蜗杆节圆处轴向齿槽宽ea'确定
蜗杆节圆直径
d1'
d1'=d1+2x2m=m(q+2x2)
双头蜗杆设计计算书与齿轮齿条设计计算书

双头蜗杆设计计算书
机械设计手册化学工业出版社第二版(修订)中册
第六章蜗杆传动
二、圆柱蜗杆传动
(二)圆柱蜗杆传动的设计计算(p559表232)
齿轮齿条设计计算书
机械设计手册化学工业出版社
第二版(修订)中册
第三章、渐开线圆柱齿轮传动
(一)精度等级和齿轮副侧隙:
齿轮的精度等级和加工方法及使用范围(p403表8-127)
选择9级(低精度级)齿面表面粗糙度(花4)
9GL为9级G齿厚(或公法线长度)上偏差,L齿厚(或公法线长度)下偏差
机械设计手册第五版化学工业出版社第3卷第14篇齿轮传动
第1章渐开线圆柱齿轮传动
2、渐开线圆柱齿轮传动的参数选择p14-18 表14-1-6
4
6.1.1 GB/T10095-1988。
普通圆柱讲义蜗轮蜗杆传动设计计算

力的方向判断例题
2 蜗杆传动的计算载荷
计算载荷=K*名义载荷
KKAKK
式中KA—工作情况系数 K—动载荷系数 K—齿向载荷分布系数
二、蜗轮齿面接触疲劳强度计算
校核公式为:
HZE
9 dK 1d2 2 2TZE
9K2T[ m 2d1Z2 2
]H
MPa
设计公式为:
m2d1 9KT 2(Z2Z[E]H)2 mm3
中间平面上的参数作为设计基准
一、普通圆柱蜗杆传动的主要参数及其选择
1 、蜗杆传动的正确啮合条件及模数m和压力角
m a1 m t2 m
a1 t2 2
旋向相同
2 、蜗杆分度圆直径d1和导程角
为了限制蜗轮滚刀的 数目并便于滚刀的标 准化,因此对每一标 准模数规定了一定数 量的蜗杆分度圆直径 d1(表9-1)
a'
1 2
d1 mz'2 2mx
a
1 2
d1
mz2
一般取 ∣x∣≤ 1
z '2 z2 2 x
x
z2
z
' 2
2
5 相对滑动速度S
s
2 1
2 2
1 co s
d 1n1
60 1000 cos
m/s
式中:
d1--蜗杆分度圆直径,mm n1--蜗杆的转速,r/min
--蜗杆分度圆上的导程角, 度
精品
普通圆柱蜗轮蜗杆传动设计计算
一、蜗杆传动的特点和应用
1、特点:
单级传动比大; 结构紧凑; 传动平稳,无噪音; 可自锁; 传动效率低; 成本高。
2、应用:
机床:数控工作台、分度 汽车:转向器 冶金:材料运输 矿山:开采设备 起重运输:提升设备、电梯、 自动扶梯
- 1、下载文档前请自行甄别文档内容的完整性,平台不提供额外的编辑、内容补充、找答案等附加服务。
- 2、"仅部分预览"的文档,不可在线预览部分如存在完整性等问题,可反馈申请退款(可完整预览的文档不适用该条件!)。
- 3、如文档侵犯您的权益,请联系客服反馈,我们会尽快为您处理(人工客服工作时间:9:00-18:30)。
23.368 24.556 0.158 0.158
23.526 24.714
53
1200
r/min
22.6415 r/min
1.979 m/s
( 非 双 导 程 法 向 弦 齿 厚
4.923 )
( 非 双 导 程 法 向 弦 齿 高
3.152 )
0.8148
0.33
0.8253
0.33
0.8044
0.32
普通
圆柱蜗杆传动设计
计算 说明:本计算程序适用于圆柱蜗杆传
动(ZA、数Z的N、计Z算K1、型几)何设特计性计的算验(算包
、受力分6析、和7、承8载级能,力分计度算圆。直还径可8根00
毫米以下另,外模,数设1定至蜗1轮0材毫料米为)锡和青侧
铜 引,用离标心准浇:铸圆,柱蜗蜗杆杆为基淬本火齿钢廓;工作
G主B要1参00考87书--目88:,《圆机柱床蜗设杆计、手蜗册轮》 2
小模数齿面:
齿面法向力
蜗杆圆周力 Ft1 = - 蜗轮轴向力 Fx2 蜗杆轴向力 Fx1 = - 蜗轮圆周力 Ft2
蜗杆径向力 Fr1 = - 蜗轮径向力 Fr2
承载能力计算:
v2 v1大 v1小 v2大 v2小 v12 v12
f' η大 η小 T1 P1 P2 T2 Fn
Fn
0.198 m/s 1.874 m/s 2.084 m/s 0.308 m/s 0.304 m/s 7.733 m/s 7.733 m/s
0.322254602 弧度,
0.377028128 弧度, 158.35605 155.22391
3.15 48.925 3.78 -41.995 6.93
5.710593 度, 5.767316 度, 5.653859 度, 6.087731 度, 5.370995 度, 20.09363 度, 20.08997 度,
B: 设定螺牙原始截面处为标准齿厚 πm /2
da1
37.8
df1
23.94
da2
264.8
de2
271.1
df2
250.94
r2
19.53
rg2
12.6
b20
20.895
θ0
1.4505 弧度, 83.11 度
B20
19.5
θ 1.047197551 弧度,
L大1
12.35
60 度
L小1
7.18
L大2
蜗杆原始截面处法向弦齿高 蜗杆原始截面处法向弦齿厚设定值 蜗杆原始截面处法向弦齿高 上述设定值情况下标准齿厚至薄齿端 距离 蜗杆厚齿端最小齿槽底法向宽度 蜗杆薄齿端最小齿顶法向宽度 蜗轮滚切时不根切的最少齿数 蜗杆齿面名义导圆柱半径 蜗杆大模数齿面导圆柱半径 蜗杆小模数齿面导圆柱半径 螺旋线母线与端截面间的名义夹角 大齿螺旋线母线与端截面间的夹角 小齿螺旋线母线与端截面间的夹角 蜗轮滚切时是否面切或装配干涉 说明:当A≥A'时,则不面切或干涉 重合度计算: 大模数齿面端面重合度 小模数齿面端面重合度 大模数齿面轴向重合度 小模数齿面轴向重合度 大模数齿面总重合度 小模数齿面总重合度 速度计算: 传动比 蜗杆转速 蜗轮转速 蜗杆名义分度圆线速度
蜗轮齿宽角
蜗轮滚切时是否发生面切或装配干 涉?
蜗杆厚齿端最小齿槽底法向宽度
蜗杆薄齿端最小齿顶法向宽度
sn1
bmin samin
θ
bmin samin
蜗轮滚切时是否根切?
蜗轮齿顶是否变尖?
总重合度
ε大
ε小
蜗杆转速(不验算承载能力不输入)
n1
蜗杆输入转矩
T1
蜗杆名义分度圆线速度 齿面相对滑动速度 蜗轮材料的许用接触应力
FPk
蜗轮齿距极限偏差
±f Pt
260.16953 256.83053 29.8305 33.1695 14.38787 14.67853 9.89602 9.99498 9.79706 0.099668652 弧度, 0.100658653 弧度, 0.098678456 弧度, 0.106250942 弧度, 0.093741542 弧度, 0.350699986 弧度, 0.350636101 弧度,
18.46383 度,
21.60212 度,
5゜ 5゜ 5゜ 6゜ 5゜ 20 ゜ 20 ゜
18 ゜
21 ゜
42 ′ 46 ′ 39 ′ 5′ 22 ′ 5′ 5′
27 ′
36 ′
蜗杆齿顶圆直径 蜗杆齿根圆直径 蜗轮喉圆直径 蜗轮顶圆直径参考值 蜗轮齿根圆直径 蜗轮齿根圆环面半径 蜗轮咽喉母圆半径 蜗轮齿宽(蜗轮轮齿的计算宽度) 蜗轮计算齿宽角 蜗轮轮缘宽度最小值 蜗轮齿宽角选取值
0.02
0.02
顶隙系数
c
蜗轮轮齿的计算宽度
b20
蜗轮计算齿宽角(按 b20 计算) θ0
蜗轮齿宽角选取值
蜗轮轮缘宽度最小值(按θ计算)
原始截面至薄齿端的计算长度 原始截面至薄齿端的实际长度 蜗杆螺牙计算总长 蜗杆螺牙实际总长
θ B2min Lg0
Lg L0 L
0.2 20.895 83.11
60 19.5 92.05 30 133.79 74
30
0.67
mm
mm 注: 如不 输 入, 则默 认上 面的 sn1a 数值 。
按 L/2 处 轴向齿厚为 标准齿厚计 算
按原始截面 轴向齿厚为 标准齿厚计 算
mm
mm
mm 度
mm
mm 注:按滚刀 齿顶高增加 0.1 模数考
r/min
N·m
P 3.77 kW
T m/s m/s
N/mm2 蜗轮齿面强
N/mm2 度不足!
比较 L大2与 L小1,大者为 La' 比较 L小2与 L大1,大者为 La" 啮合线长度 调整长度 工艺长度 原始截面至薄齿端的计算长度 原始截面至薄齿端的实际长度 蜗杆螺牙计算总长 蜗杆螺牙实际总长 A: 设定螺牙长度一半处为标准齿厚 πm /2 蜗杆原始截面处齿厚 蜗杆原始截面处法向弦齿厚 蜗杆原始截面处法向弦齿高
19.89654 度, 19 ゜
19.89448 度, 19 ゜
19.89858 度, 19 ゜
53 ′ 53 ′ 53 ′
蜗轮名义分度圆线速度
蜗杆大模数齿面节圆线速度
蜗杆小模数齿面节圆线速度
蜗轮大模数齿面节圆线速度
蜗轮小模数齿面节圆线速度
大模数齿面齿面相对滑动速度
大模数齿面齿面相对滑动速度
大模数齿面速度比
蜗轮材料的许用接触应力
[σ]H 202.61 N/mm2
K1' 1 K2' 0.9 K3'
蜗轮齿面接触应力 法向模数 蜗轮齿根的弯曲应力
σH
349.75 N/mm2
mn
3.1344
σb
45.1
N/mm2
K5' 0.77 K6' 0.86 K7'
K 0.42 Km 1 ZE KV
' 0.97 KN 0.83
v1大
/v2大
小模数齿面速度比
v1小
/v2小
传动效率计算:
齿面磨擦系数
大模数齿面传动效率
小模数齿面传动效率
受力分析:
蜗杆输入转矩
蜗杆输入功率
蜗轮输出功率
蜗轮输出转矩
大模数齿面:
齿面法向力
蜗杆圆周力 Ft1 = - 蜗轮轴向力 Fx2 蜗杆轴向力 Fx1 = - 蜗轮圆周力 Ft2
蜗杆径向力 Fr1 = - 蜗轮径向力 Fr2
sn1b
hn1b sn1 hn1
bmin samin
Z2min
rZ r Z大 r Z小 αT α T大 α T小 A' A
εt大 εt小 εx大 εx小 ε大 ε小
i12 n1 n2 v1
4.923
3.152
4.784 3.152
37.01 1.54 1.89 24 0.3252 0.326 0.3244 0.347260128 弧度, 0.34722412 弧度, 0.347295788 弧度, 0.117 1.508
编 号: 12
蜗杆直径系数
q0
蜗杆名义分度圆直径理论值
d10 在下行输入
蜗杆名义分度圆直径实际值
d1
31.5
mm
蜗杆直径系数(按d1计算所得)
q
10
蜗轮名义分度圆直径
d2
a0
99.225 mm
蜗轮变位系数初值
x20
0.2
蜗杆传动副计算中心距(按X20计算) a0'
6.084
6.855
0.018 0.83 0.828
N·
30000 mm
3.77
kW
3.129 Nk·W
1319700 mm
10879.46 N 1278.92 N 10144.93 N 3720.99 N
11004.4 N 1165.15 N 10276.81 N 3763.73 N
0.018 *
蜗轮齿面接触应力 蜗轮齿根的弯曲应力 蜗轮齿根的极限弯曲应力
v1 v12 [σ]H
σH σσb
bmax
蜗轮齿根弯曲强度的安全系数
Sb
4.784
4.923
37.01 1.54 1.89 83.11
否 1.54 1.89
否 否 23.526 24.714 1200 30
1.979 7.733 202.61 349.75 45.1
注:一般为 0. 2
度 注:动力传 动70—110 度,运动传 动45—60度