攻丝技术的发展与应用
钳工螺纹攻丝技术要点

钳工螺纹攻丝技术要点论文摘要:螺纹加工有机床加工和手动加工两种方式,加工螺纹时必须加工正确的螺纹底孔,选择正确的丝攻,攻丝前对丝攻进行检查或修磨改进。
关键词:螺纹底孔丝攻修磨一、钳工加工螺纹底孔时需要注意的几点事项(1)加工前,需严格遵照《机械工人切削手册》进行相应的计算和查表,按照工件要求选择加工螺纹底孔的钻头及扩孔钻头,注意钻头的切削要锋利,刃要带不得有毛刺和磨损等,保持光滑,以免产生锥度及底孔刮伤等缺陷情况发生。
(2)加工钻孔时,应选择合适的转速和进给量,并根据不同材料选择合理的冷却液和润滑液,以防止切削热过高使得加工孔的冷硬层加厚,从而导致后续攻丝加工时变得困难。
(3)当加工的工件底径大于10mm时,应先钻一个相对小的小孔,然后再进行扩孔操作,这样可以使螺纹底孔达到理想的直径和粗糙度要求,通常底孔的粗糙度不得小于3.2√, 同时可避免操作时有弯曲和倾斜发生,导致螺纹倾斜和螺纹牙型缺失不完整。
(4)加工完工件后,要注意螺纹底孔的孔口要进行倒角工序,通孔螺纹两端都倒角。
倒角的大小为大于所攻丝螺距的尺寸,如M3的螺距是0.5,那么倒角用90度钻头倒角C0.5以上就可以,避免攻丝以后毛刺翻于零件表面,影响表面质量。
(5)工件夹具的位置应正确,螺纹孔的中心线应尽量放在水平或垂直位置,以便于攻丝操作时,较容易判断出丝锥轴线是否与工件平面垂直。
(6)钻孔时可以用废料或者钻0.5mm--1mm深,及时测量底孔直径,避免底孔钻大而导致螺纹小径变大。
二在加工时,钳工丝攻本身的质量将直接影响螺纹孔的加工质量,因而加工前选用丝攻时,要注意观察以下几点:(1)观察丝攻的螺纹表面与容屑槽是否光滑。
如果出现切屑瘤、粘屑或铁锈腐蚀,应予以清除,以免妨碍加工工件时切屑的排出。
丝攻的齿形和切屑部分应锋利,不得有刃部裂痕、毛刺、碳损伤等。
否则,在加工切削过程中,切屑会粘附上面并损坏螺孔的表面粗糙度。
(2)注意手用丝攻的方头夹紧部位磨损后,应打磨至较小尺寸,以防止在攻丝过程中夹紧失败,发生打滑情况。
螺纹滚压加工技术研究张美玲

螺纹滚压加工技术研究张美玲发布时间:2021-09-10T09:23:18.433Z 来源:《中国科技人才》2021年第17期作者:张美玲谢保光[导读] 目前,随着个性化的不断发展和市场需求的多样化,塑料成型与磨削加工的结合将取代大部分中小型零件的切削加工,将成为本世纪的发展趋势。
推动了制造业和加工业向着精密、低能耗、无污染的方向发展,已成为绿色制造的重要组成部分。
螺纹加工有多种加工方法,包括螺纹加工、螺纹铣削、滚压、攻丝、螺纹加工等。
螺纹铣削、攻丝等工艺方法是一种切削加工,效率不高,但对工人的技术要求很高,不利于大批量生产。
滚压工艺操作简单,生产率高,加工范围广。
本文对螺纹滚压加工技术进行了深入的研究。
沈阳飞机工业(集团)有限公司辽宁沈阳 110034摘要目前,随着个性化的不断发展和市场需求的多样化,塑料成型与磨削加工的结合将取代大部分中小型零件的切削加工,将成为本世纪的发展趋势。
推动了制造业和加工业向着精密、低能耗、无污染的方向发展,已成为绿色制造的重要组成部分。
螺纹加工有多种加工方法,包括螺纹加工、螺纹铣削、滚压、攻丝、螺纹加工等。
螺纹铣削、攻丝等工艺方法是一种切削加工,效率不高,但对工人的技术要求很高,不利于大批量生产。
滚压工艺操作简单,生产率高,加工范围广。
本文对螺纹滚压加工技术进行了深入的研究。
关键词螺纹滚压;加工技术;研究引言作为塑料成型的一种加工方法,越来越多的紧固件厂家采用螺纹滚压加工技术,本文介绍了螺纹滚压加工技术的原理、优点、影响因素、参数确定以及加工过程中的缺陷表现,为相应的工作人员提供参考。
一、螺纹滚压加工技术的原理工件毛坯的金属基体首先被滚轮的力压缩,发生塑性屈服,最后在工件毛坯上形成螺纹形状。
滚压通常在带有自动开合滚丝头的螺纹铣床、螺纹铣床或自动车床上进行,适用于大批量生产标准紧固件和其他螺纹接头的外螺纹。
滚压螺纹的外径通常在25mm以下,长度在100mm以下,螺纹精度可以达到最大。
钳工技师论文

装配钳工技师论文钻床·钻头·丝攻的改进方法【内容摘要】钻床在夹持钻头、丝攻工作中会出现钻头或丝攻尾部打滑现象,把钻头或丝攻尾部磨成正六棱柱形;在打沉孔时,可以把大钻头磨成组合钻,以便一次性解决;用台钻攻丝时,可以做一个钻头润滑、冷却可调节供油系统装置。
【关键词】正六棱柱形、组合钻、自动供液装置【前言】以前我专门从事过钻床操作,主要是在小胶印机底板上打孔、攻丝.一块底板上有九种规格的孔,有近一半的孔都要攻丝,还有八个沉孔;一天下来要不停地换钻头、丝攻.而且在用直径大的钻头打数量多的孔时,尾部会出现打滑的现象,一旦出现打滑现象时,都要用钥匙把钻夹紧一下,来防止其松动.攻丝时情况也一样.在打沉孔时,上部的大空有时会出现中心偏移的现象,且深度也不均匀;在攻丝时:用毛刷往底板孔内加润滑液,效率极低且浪费还容易遗漏,再则,没有加到润滑液的孔,在攻丝时也容易断丝攻。
【正文】经过长期的摸索、研究和实践,最终总结出一些经验。
如下:一、从事过钻床工作的师傅应该都知道:在加工大批工件上的大孔(直径在6mm 以上)时,钻头尾部夹持部分经常会出现打滑的现象。
一旦出现打滑现象,一般钻夹都会把钻头尾部的标记磨掉,甚至出现几圈拉伤的痕迹。
这样的话,如果下次使用钻头时,在没有卡尺去测量其直径,就不能确切知道大小,从而降低效率;而最重要的是:在下次夹持钻头时,在工作中会造成钻心不稳、打出的孔不圆,直径偏大、中心位置偏移等不良现象.经过长期思考、研究发现:风动工具(风枪)的内六角枪头在工作时,即使打不动也不会出现打滑现象.在此基础上我联想到钻头,如果把钻头尾部也加工成对角线和尾部直径一样的正六棱柱行,也肯定不会产生打滑的现象。
于是我就找了一个φ12的钻头尾部加工成正六棱柱形(见附件图一)。
放入钻夹中随便紧一下就好了,连续打了20多个孔没有一次打滑现象。
后来想了想φ小于6 的钻头,工作是与工件的接触面小(切销面)少,产生的摩擦力也小,容易用钥匙夹紧,所以6个以下的钻头不必磨成六棱柱形.尾部φ14以上的钻头尾部一般都做成扁的,大都在铣床上用,所以也不用磨.对于钻头尾部磨成正六棱柱的长度要根据实际情况而定,以不磨去钻头尾部的标记且又能夹紧为宜.在实际操作中往往只磨出三个面就够了,因为钻夹都是三个脚的。
螺纹铣削技术与攻丝的对比

螺纹铣削技术与攻丝的对比在一般生产加工中,螺纹的加工方式多采用攻丝这种传统工艺,随着数控技术的发展、软件的创新、控制精度的提高、三轴联动或多轴联动数控系统的产生及其在生产领域的广泛应用,相应的先进加工工艺——螺纹铣削逐渐得以实现,其加工精度、光洁度以及柔性是攻丝无法比拟的,另外其经济性在某种情况下也更优于传统工艺。
螺纹铣削是通过主轴高速旋转并做圆弧插补的方式加工螺纹。
只要通过改变程序就可以实现不同直径的螺纹、左右螺纹及内外螺纹的加工,其柔性非常理想,见图1。
另外,螺纹铣削还有线速度高、受力小、排屑好、加工精度高、光洁度好等优点。
图1螺纹铣削相对攻丝的优势通过各个方面的对比,可以发现螺纹铣削存在很多优势:1) 一把螺纹铣刀可以加工直径不同、牙型相同的螺纹。
如图2所示:M15x1.0、M18x1.0、M20x1.0的螺纹用一把螺纹铣刀通过改变插补半径来加工,可减少刀具数量,节省换刀时间,提高效率,方便刀具管理。
图22) 螺纹精度及光洁度提高。
因螺纹铣削是通过刀具高速旋转、主轴插补的方式加工完成。
其切削方式是铣削,切削速度高,加工出来的螺纹漂亮;而丝锥切削速度低,并且切屑长,容易损坏内孔表面。
3) 内螺纹排屑方便。
铣螺纹属于断屑切削,切屑短小,另外加工刀具直径比加工螺纹孔小,所以排屑通畅;而丝锥属于成型连续切削,切屑很长,并且丝锥直径和加工孔一样大,因此排屑困难。
4) 可以避免丝锥反转形成的回转线(在密封要求高的情况下是不允许的)。
因为加工原理不同,螺纹铣刀根本不存在回转线,而丝锥无法避免。
5) 不易形成粘屑的现象。
对于比较软的材料在加工过程中容易产生粘屑现象,但螺纹铣削高速旋转,并且断屑切削;而丝锥切削速度低,全螺纹与加工表面作用,容易造成粘屑。
6) 要求机床功率低。
因为螺纹铣削是断屑切削,刀具局部接触,受切削力小,而丝锥是全螺纹接触,作用力大,要求机床很大的功率。
7) 刀具折损容易处理。
首先螺纹铣刀作用力小,很少发生折损现象,如果发生了,因为加工孔径比刀具大,折断部分很容易取出;而丝锥受力大、排屑不畅,容易折断,折断后大孔处理起来稍微容易些,如果是小孔就非常麻烦,如图3所示。
数控技术历史发展趋势及新技术论文3000字
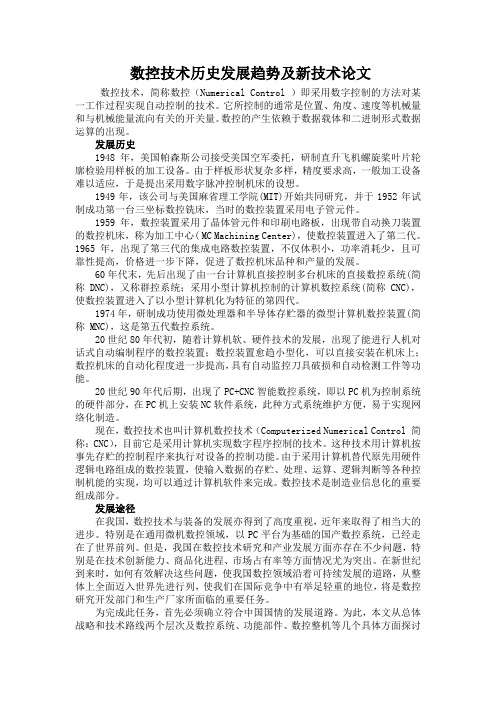
数控技术历史发展趋势及新技术论文数控技术,简称数控(Numerical Control )即采用数字控制的方法对某一工作过程实现自动控制的技术。
它所控制的通常是位置、角度、速度等机械量和与机械能量流向有关的开关量。
数控的产生依赖于数据载体和二进制形式数据运算的出现。
发展历史1948年,美国帕森斯公司接受美国空军委托,研制直升飞机螺旋桨叶片轮廓检验用样板的加工设备。
由于样板形状复杂多样,精度要求高,一般加工设备难以适应,于是提出采用数字脉冲控制机床的设想。
1949年,该公司与美国麻省理工学院(MIT)开始共同研究,并于1952年试制成功第一台三坐标数控铣床,当时的数控装置采用电子管元件。
1959年,数控装置采用了晶体管元件和印刷电路板,出现带自动换刀装置的数控机床,称为加工中心( MC Machining Center),使数控装置进入了第二代。
1965年,出现了第三代的集成电路数控装置,不仅体积小,功率消耗少,且可靠性提高,价格进一步下降,促进了数控机床品种和产量的发展。
60年代末,先后出现了由一台计算机直接控制多台机床的直接数控系统(简称 DNC),又称群控系统;采用小型计算机控制的计算机数控系统(简称 CNC),使数控装置进入了以小型计算机化为特征的第四代。
1974年,研制成功使用微处理器和半导体存贮器的微型计算机数控装置(简称 MNC),这是第五代数控系统。
20世纪80年代初,随着计算机软、硬件技术的发展,出现了能进行人机对话式自动编制程序的数控装置;数控装置愈趋小型化,可以直接安装在机床上;数控机床的自动化程度进一步提高,具有自动监控刀具破损和自动检测工件等功能。
20世纪90年代后期,出现了PC+CNC智能数控系统,即以PC机为控制系统的硬件部分,在PC机上安装NC软件系统,此种方式系统维护方便,易于实现网络化制造。
现在,数控技术也叫计算机数控技术(Computerized Numerical Control 简称:CNC),目前它是采用计算机实现数字程序控制的技术。
钳工螺纹加工技术

1 攻螺纹加工技术研究1.1 攻螺纹的工具攻螺纹主要利用丝锥进行加工。
丝锥主要分为手用、机用、有管螺纹丝锥。
当需要制作一般螺纹时,常用手用或者机用丝锥。
一般M6以下的丝锥强度差、易折断,通常将三支作为一套。
它的大、中、小径一样,当头锥被破坏时,可以把二锥、三锥改为头锥接着用。
攻螺纹使用大丝锥比较费劲,可以通过多次切削来完成。
同时,要根据头锥、二锥和三锥的不同特点,合理分配工作环节,提高工作效率。
另外,丝锥工作时需要借助铰杠来固定。
铰杠有普通型和丁字型两种,而不同类型的铰杠又有各自固定的样式和可调的样式。
若工件在台阶处或者是箱体中,采用丁字型的铰杠操作更方便。
1.2 攻螺纹的操作方法攻螺纹分为手攻和机攻两种方式。
手攻的难度更大,需要确保丝锥轴线与螺纹底部轴线相垂直,而这个过程很容易出现偏差。
因而,攻螺纹时,装夹是关键的一步。
(1)攻螺纹是首先把丝锥摆正,一手扶着铰杠上方沿丝锥竖直方向向下压,另一只手协助转动铰杠。
一两圈后,即从正入的两个方向检查丝锥与加工件平面是否垂直。
若有倾斜,则利用90°角尺进行校准。
若是垂直度不正,则将头锥旋出,用二锥进行校准。
达标后,再用头锥进行。
(2)最初的攻螺纹既是重点也是难点。
直径小的工件用工具夹持不方便,也不便于校准,可以借助攻螺纹套具来完成;直径大的工件可以用专制样板或者光面螺母来校准。
(3)攻螺纹时,铰杠顺时针旋转半圈到一圈时,就要逆时针旋转1/4到1/2圈。
M5以下的丝锥旋转一次进度小于1/2圈就可以保证切屑彻底切断,避免切屑堵塞损坏丝锥。
深孔螺纹进行切削时,要相应加大倒旋转幅度,并多重复几次。
铰杠的旋转速度要符合工件的材质,脆性材质的工件相比塑性材质的工件转动速度快。
(4)手动旋转铰杠时,一定要均匀使劲,不能用力太大。
有阻碍时,要先倒着旋转钻削再攻丝,切忌蛮力攻进。
若是攻螺纹时发现有咯咯的声音,要立刻停止进度并反向旋转丝锥查明原因,否则可能会发生断裂。
钳工教案(攻丝和套丝)
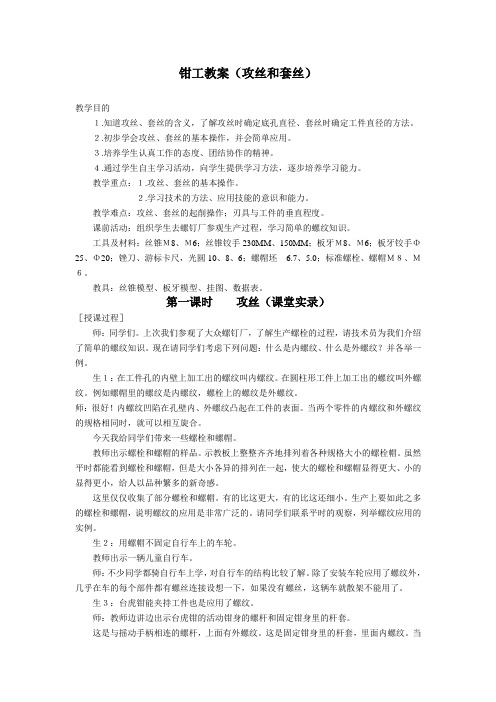
钳工教案(攻丝和套丝)教学目的1.知道攻丝、套丝的含义,了解攻丝时确定底孔直径、套丝时确定工件直径的方法。
2.初步学会攻丝、套丝的基本操作,并会简单应用。
3.培养学生认真工作的态度、团结协作的精神。
4.通过学生自主学习活动,向学生提供学习方法,逐步培养学习能力。
教学重点:1.攻丝、套丝的基本操作。
2.学习技术的方法、应用技能的意识和能力。
教学难点:攻丝、套丝的起削操作;刃具与工件的垂直程度。
课前活动:组织学生去螺钉厂参观生产过程,学习简单的螺纹知识。
工具及材料:丝锥Μ8、Μ6;丝锥铰手230MM、150MM;板牙Μ8、Μ6;板牙铰手Φ25、Φ20;锉刀、游标卡尺,光圆10、8、6;螺帽坯 6.7、5.0;标准螺栓、螺帽M8、M6。
教具:丝锥模型、板牙模型、挂图、数据表。
第一课时攻丝(课堂实录)[授课过程]师:同学们。
上次我们参观了大众螺钉厂,了解生产螺栓的过程,请技术员为我们介绍了简单的螺纹知识。
现在请同学们考虑下列问题:什么是内螺纹、什么是外螺纹?并各举一例。
生1:在工件孔的内壁上加工出的螺纹叫内螺纹。
在圆柱形工件上加工出的螺纹叫外螺纹。
例如螺帽里的螺纹是内螺纹,螺栓上的螺纹是外螺纹。
师:很好!内螺纹凹陷在孔壁内、外螺纹凸起在工件的表面。
当两个零件的内螺纹和外螺纹的规格相同时,就可以相互旋合。
今天我给同学们带来一些螺栓和螺帽。
教师出示螺栓和螺帽的样品。
示教板上整整齐齐地排列着各种规格大小的螺栓帽。
虽然平时都能看到螺栓和螺帽,但是大小各异的排列在一起,使大的螺栓和螺帽显得更大、小的显得更小,给人以品种繁多的新奇感。
这里仅仅收集了部分螺栓和螺帽。
有的比这更大,有的比这还细小。
生产上要如此之多的螺栓和螺帽,说明螺纹的应用是非常广泛的。
请同学们联系平时的观察,列举螺纹应用的实例。
生2:用螺帽不固定自行车上的车轮。
教师出示一辆儿童自行车。
师:不少同学都骑自行车上学,对自行车的结构比较了解。
除了安装车轮应用了螺纹外,几乎在车的每个部件都有螺丝连接设想一下,如果没有螺丝,这辆车就散架不能用了。
攻丝编程技术在实际加工中的应用

目前在 C C机床上 ,攻丝 已经成 为 内螺纹 孔 的 N
加工基本方法之一 ,但 是 由于攻丝编程与普通轮廓编
2 1 丝锥 螺 旋槽 的几何 尺 寸 . 编写攻丝加工程序时 ,丝锥螺旋槽 的效 率依赖 于 主轴 的转速 ,丝锥导程 ( 螺距 )会 限制攻 丝进给率 , 但是其主轴转速选择范 围较大 。工件材料和丝锥螺旋 槽 的几何 尺寸同时影 响主轴转速 ,实际编程时 ,应该 根据刀具商提供的刀具 目录得到技术数 据 ,从 而得到 C C程序 的原始数据 。 N
攻 丝编 程 技术 在 实 际加 工 中 的应 用
.
夏 天 ,陈乃峰
( 四平职 业 大学机械 工程 学院 ,吉林 四平 16 0 ) 30 2
摘 要 :由于攻丝 编程 与普 通轮廓编程存在明显的差异 ,以及机床控制器 本身也对攻 丝编程有一定 的制约 ,因此 编程员
在 实际操 作中往 往会遇到各种问题 。通过理论研究并结合实际应用 ,给 出在 C C机床上应用攻丝技术加工螺纹孑 时的一些 N L 关 键性问题的具体解决方法 。
2 2 丝锥 倒 角 的几何 尺寸 . 丝锥 的倒 角几 何 尺 寸 与 丝 锥 的 末 端形 状 有 关 ,
程存在一些差异 ,编程员 往往会 遇 到各种 实际 问题 。 作者将对攻丝编程技 术在实 际 中的应 用作 一些探 讨 , 希望能给读者一些有益 的帮助 。
1 攻 丝 的原 则
攻丝的主要原则是保证主轴转速和丝锥进给速率
同步 。
1 1 柔性 攻 丝 ( 准攻 丝 ) . 标 由于柔性攻丝时采用 了浮动攻丝刀套 ,尽管它可
- 1、下载文档前请自行甄别文档内容的完整性,平台不提供额外的编辑、内容补充、找答案等附加服务。
- 2、"仅部分预览"的文档,不可在线预览部分如存在完整性等问题,可反馈申请退款(可完整预览的文档不适用该条件!)。
- 3、如文档侵犯您的权益,请联系客服反馈,我们会尽快为您处理(人工客服工作时间:9:00-18:30)。
攻丝技术的发展与应用
攻丝属于比较困难的加工工序,因为丝锥几乎是被埋在工件中进
行切削,其每齿的加工负荷比其它刀具都要大,并且丝锥沿着螺纹与工件接触面非常大,切削螺纹时它必须容纳并排除切屑,因此,可以说丝锥是在很恶劣的条件下工作的。
为了使攻丝顺利进行,应事先考虑可能出现的各种问题。
如工件材料的性能、选择什么样的刀具及机床、选用多高的切削速度、进给量等。
(1)在特殊工件材料上攻丝
工件材料的可加工性是攻丝难易的关键。
针对这些特殊材料的性能,改变丝锥切削部分的几何形状,特别是它的前角和下凹量。
对于高强度的工件材料,丝锥的前角和下凹量通常较小,以增加切削刃强度。
下凹量较大的丝锥则用在切削扭矩较大的场合。
但下凹量过大,切削刃可能会产生崩刃并嵌入螺纹。
一般情况下,长屑材料需较大的前角和下凹量,以便卷屑和断屑。
另一方面,太锋利的角度会使切削刃过于薄弱。
另一个受工件材料可加工性影响较大的丝锥角度是后角。
加工较硬的工件材料需要较大的后角,以减小摩擦和便于冷却液到达切削刃,但过大的后角又会减小丝锥切入工件时的自定心能力。
加工软材料时,太大的后角会导致螺孔扩大。
对于加工硬度、强度都很高的工件材料,丝锥应选择起始于切削刃的偏心后角;而对易加工材料,则选择带复合偏心后角的丝锥,其特点是在切削刃下面无后角刃带之后再磨出后角。
螺旋槽丝锥主要用于盲孔的螺纹加工。
加工硬度、强度高的工件材料,所用的螺旋槽丝锥螺旋角较小,这可改善其结构强度。
此外,对于强韧的加工材料,要选用螺纹长度较短的螺旋槽丝锥,以减小切削时的扭矩。
丝锥不同于大多数金属切削工具,因为它与工件孔壁接触面积非常大,所以冷却至关重要。
如果高速钢丝锥过热,则丝锥会折断、烧损。
上述丝锥的几何形状,再配以特殊的涂层表面(如TiN、TiCN、CrN或TiAlN),可大大提高丝锥的寿命。
这些耐热的、光滑的涂层,减小了切削力并允许在更高的切削速度下攻丝。
实际上,较新的高性能丝锥的开发,极大地促进了机床主轴速度和功率的提高。
像车削中硬质合金刀具逐渐替代高速钢刀具一样,硬质合金丝锥也开始更多地用于螺纹孔加工,与高速钢相比,硬质合金硬度高、脆性大,用硬质合金丝锥攻丝,存在切屑处理的问题。
虽然如此,硬质合金丝锥对于加工铸铁和铝合金材料,其使用效果很好,丝锥的破损形式主要是机械磨损。