异型材挤出成型-重点难点
异型材挤出成型资料

2020/7/2
异型材挤出成型设备
• 孔板式机头
• 2号口模板是成型零 件,更换口模板便可 得到不同形状的制品。 机颈座是过渡部分, 它的内孔尺寸由挤出 机的内径逐步过渡到 与口模板成型部分接 近的尺寸。
2020/7/2
异型材挤出成型设备
异型材机头种类
1).流线型机头 由螺杆出口的圆形过渡到近似制品外形的流道
是缓慢变化的流道形式(包括整体式和分段式)。
2).多级式机头、孔板式机头 多级式与板式机头由螺杆出口的圆形过渡到近
似制品外形的流道是有急剧变化的流道形式。
2020/7/2
异型材挤出成型设备
• 整体式流线型机头
2020/7/2
2020/7/2
生产线实物图
2020/7/2
PE木塑扶手挤出实图
2020/7/2
2020/7/2
2020/7/2
2020/7/2
2)、波纹板滑移式定型装置
定型模 异型材
先挤成管坯,剖切 展平后进入定型模
成型。
定型模
2020/7/2
3)、折弯异型材滑移式定型装置
先挤成板材,再经滑移式定 型模中折弯成异型材并冷却 定型。
2020/7/2
特点:可以用形状简单的模 具成型极为复杂的大型异 型材。
4.牵引装置
可采用生产管材所用牵引装置——履带式牵引装 置。如将履带上的橡胶块外形与牵引的异型材轮廓 加工成一致,则牵引效果会更好些。
混合
双螺杆挤出成型
真空定型
冷却
牵引
型材挤出中的异常现象、原因、解决方法

1型材弯曲挤出型材直线度是检验塑料门窗异型材产品品质的一个重要指标,它直接影响门窗焊接、组装质量以及五金配件的安装。
GB/T8814-1998规定,当门窗主要异型材(诸如:扇、框、梃)弯曲量大于2mm/m时为不合格。
造成挤出制品弯曲的因素很多,最常见的有以下几个方面:1.1口模出料不均匀口模出料均匀性包括“出料速度差异”和“型坯壁厚差异”两个要素。
判断口模出料是否均匀,只需在口模出口处用专用铲刀迅速截取长约20mm、塑化良好的型坯4~5片进行测量,若型坯纵向各侧面的长度误差(取各片的平均值)不超过10%,且外壁、内筋等各处的厚度(因有离模膨胀效应,故此厚度并不等同于制品壁厚)对应关系符合产品截面图纸要求则视为合格。
口模出料不均匀造成的弯曲,其弯曲方向在定型系统对型坯冷却充分、牵引阻力平衡的前提下向出料慢的一侧弯曲(冷却效果和牵引阻力的影响在后面讨论)。
调整口模出料均匀性的措施如下:(1)检查口模定型段型腔主间隙的均匀性,间隙差不大于0.02mm;(2)检查流道内有无死角、台阶或糊料现象,将型腔抛光至镜面(Ra≤0.02μm);(3)检查尾锥分流中心是否合理并予以调整;(4)调整口模局部出料速度还可在压缩段、分流段或发散段采取“阻流”或“疏流”两种不同的方式(严禁改变口模定型段间隙)。
对出料快的区域可通过设置阻尼块或采用与模体相同的材料对型腔进行堆焊以达到“限流”的目的;对出料慢的区域可通过局部延长压缩段长度(即缩短定型段长度)、加大分流段型腔尺寸或调整尾锥分流角度以达到“疏流”的目的。
1.2型坯通过定型冷却系统时的牵引阻力不平衡PVC-U异〖BF〗型材定型冷却系统通常采用干-湿结合定型装置。
在干定型段(普遍采用数段定型模安装在同一底板上的串联结构)通过抽真空使高弹态的型坯被吸附在型腔壁上定型冷却,并在牵引机的作用下滑移。
由于多数异型材结构相对复杂,且在沿型腔滑移的过程中逐渐收缩,因此牵引阻力不平衡很常见,主要应从以下几方面分析:(1)因阻力不平衡造成的弯曲(主要发生在非对称型材),往往向阻力大的一侧弯;(2)真空吸附力越大,则型坯与型腔间的摩擦阻力越大,可通过调整真空吸附强度来改变局部牵引阻力;(3)检查易产生较大牵引阻力的沟槽、凸台的结构尺寸设计是否合理。
异型材挤出成型—异型材成型辅机(塑料挤出成型课件)

异型材机头分类
异型材机头分类
思考:板式机头和流线型机头各自优缺点?
1. 板式机头
• 特点:结构简单,成本低,口模更换容易,适合多品种、小批量生产 • 缺点:横截面急剧变化,易形成局部滞料和死角,型材尺寸准确性不高 • 适用:聚烯烃,软聚氯乙烯的生产
2.流线型机头
• 设计要求:机头内流道必须为圆形过渡,各处不得有急剧过渡或死角。 • 特点:能克服流道急剧变化,保证挤出成型质量,适合大批量生产。
为什么?
滚轮式牵引装置
1一型材;2一主动轮;3一调节杆;4一手轮; 5一从动轮
由2~5对上下牵引滚轮组成。滚轮和型材之间面或线接触,牵引力小,只适用于 小型异型材制品的生产。要注意滚轮的形状尺寸应与异型材的形状和尺寸相适应。
由二条或二条以上的履带组成。由于牵 引履带与型材的接触面积大,牵引力也 较大,且不易打滑,特别适用于薄壁或 型材尺寸较大的制楞板时,预先挤出的板材 经波纹形辊筒压成粗波纹,接着通 过上图所示的滑移式定型模,冷却 定型成为所要求的波纹板。
将从平缝模挤出的板材在滑移式 定型模中折弯成需要的截面形状,冷 却定型。此法能用简单的模具制造出 复杂的大型异型材。
定型方法
3. 真空(外)定型
1. 特点:由于采用间接水冷方式,有效抑制了内应力和形变。 2. 方法:定型模周围壁上的细孔或缝口抽真空产生负压区,使型材的外壁与真空
牵引装置
牵引、切割装置
• 作用:克服型材在定型模内的摩擦阻力而均匀地牵引型 材,使挤出过程稳定进行。
• 由于异型材形状复杂,有效面积上摩擦阻力大,要求牵 引力也较大,同时为保证型材壁厚、尺寸公差、性能及 外观要求,必须使型材挤出速度和牵引速度匹配。
• 异型材挤出常用牵引机有辊轮式、履带式和皮带式三种。
硬PVC门窗异型材挤出成型工艺

硬PVC门窗异型材挤出成型工艺一、生产工艺流程硬PVC门窗异型材的生产工艺路线主要有单螺杆挤出成型工艺和双螺杆挤出成型工艺两种,而两种工艺挤出用的原料都是前道工序按一定配方配好的混合粉料。
目前,硬PVC 门窗异型材的挤出大多采用锥形螺杆挤出生产线。
(一)单螺杆挤出成型单螺杆挤出成型工艺特别适用于小批量、小规格异型材的生产。
其工艺流程如下:混合粉料→单螺杆挤出造粒→单螺杆挤出成型→定型→牵引→切割→翻转台→成品(二)双螺杆挤出成型双螺杆挤出成型工艺可用粉料直接成型,生产能力大,特别适用于大批量常规型材和大规格异型材的生产。
其工艺流程如下:混合粉料→双螺杆挤出成型→定型→牵引→切割→翻转台→成品二、双螺杆挤出机挤出硬PVC门窗异型材工艺控制要点硬PVC门窗异型材的挤出过程可简述如下:改性PVC混合料在机筒内经过螺杆混炼,在内磨擦热和电加热的作用下,物料逐渐变成熔融粘流态,物料在旋转螺杆的流动下向机头方向螺旋运动。
进入机头模具后,在高温、高压下经过机头模具型腔进行分流压缩成型,挤出近似制品断面的型坯,再经过定型模具对型坯真空冷却定型,达到制品设计要求。
成型温度、定型冷却、螺杆转速、牵引速度、加料速度等都是影响异型材制品质量的重要因素,现分述如下:(一)温度控制PVC混合粉料进入挤出机后,要完成压实、输送、熔融、均化以及在较低温度下挤出。
为获得高质量、高产量型材,各段的温度需反复调节、准确控制,使物料在挤出成型过程中,始终在熔融温度与分解温度区间进行。
要正确设定温度,则需充分考虑和指导物料成型温度的相关因素。
1影响物料加工温度的因素1)配方及原料质量对加工温度影响最大的是配方,不同原料组成的混合物料其塑化温度不同。
配方确定后,加工温度也就基本确定了,只需视产品质量作小范围的调节;同一配方不同厂家生产的原料,挤出成型温度往往也有差异,只有通过生产实践,依据塑料型坯的质量,适时调整设定温度。
2)挤出速度在正常生产工艺条件下,提高挤出速度会使物料磨擦生热,所以应适当降低加热温度。
cpvc胶粒挤出异形材的解决方法

cpvc胶粒挤出异形材的解决方法
硬质PVC颗粒在挤出异型材时的表面亮度不够原因及解决方法
想增加硬质PVC颗粒在挤出异型材时的表面亮度,可以从以下方面查找原因并做调整:
1.原材料粒度差异较大,使得难以均匀塑化,而光泽不良,对此,应将原材料进行筛分处理。
2.原料中再生料或水口料加入太多,影响熔体的均匀塑化而光泽不良,对此,应减少再生料或水口料加入量。
3.有些原材料在调温时会分解变色导致光泽不良,对此,应选用耐温性较好的原材料。
4.原材料中水分或易挥发物含量过高,受热时挥发成气体,在型腔和熔体中凝缩,导致塑件光泽不良,对此,应对原材料进行预干燥处理。
5.有些添加剂的分散性太差而使塑件光泽不良,对此,应改用流动性能较好的添加剂。
6.原材料中混有异物,杂料等物料,它们不能与其原料均匀混熔在一起而导致光泽不良,对此,应事先严格排除这些杂料。
7、.若润滑剂用量过少,熔体的流动性较差,塑件表面不致密,使得光泽不良,对此,应适当增加润滑剂的用量。
避免 PVC 挤出异型材表面的凹痕和气泡,可以采取以下措施:
1. 调整加工工艺:适当提高加工温度、螺杆转速和模头压力,同时降低螺杆压缩比,以保证原料充分塑化。
2. 优化模具设计:增加模具排气孔数量和尺寸,并在模具表面喷涂脱模剂,以提高制品脱模效率。
3. 定期清洁模具:每隔一段时间就对模具进行一次清洁,以去除残留的原料和污垢。
4. 定期检查设备:每隔一段时间就对设备进行一次检查,以确保设备的正常运行。
5. 控制原材料质量:选择高质量的 PVC 树脂,并在使用前进行适当的干燥处理。
通过以上措施,可以有效避免 PVC 挤出异型材表面的凹痕和气泡。
异型材挤出成型—异型材成型工艺(塑料挤出成型课件)
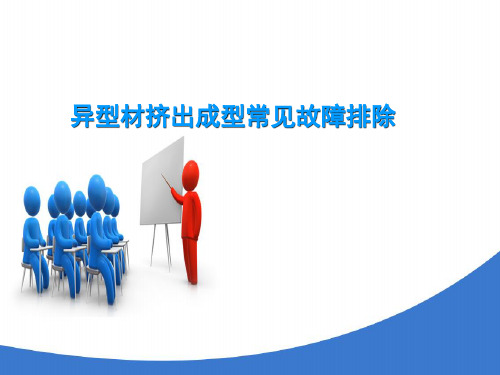
机头 压力 不足
定型段 物料 入机头 配方中 物料 分料筋 挤出 长度 未充分 料流 外润滑性 流动性 处熔体 速度 不足 汇流 偏低 过强 太差 温度偏低 太快
调整 物料 流量
增加 机头 压力
增加 定型段 长度
在模芯 支架后 设置 物料池
增大机头 入口处的 树脂流道
降低 混料的 外润滑性
采用 流动性好 的物料
冷却水对 型材冷却过快
关小冷却水
真空压力过大
定型模与冷却水箱 不在同一直线上
减小真空吸力
调整定型模与水箱 在同一水平直线上
异型材挤出成型工艺规程
异型材挤出工艺规程
1、开机前准备 检查水电供应、辅机是否正常,辅助工具
是否准备齐全,人员是否到位。
2、升温 升温并观察温度变化,打开螺杆油温,开启水阀,
(2)待停机料挤出后,依次关闭定型真空、风机,停止主 机螺杆,关闭螺杆油泵、冷却油泵。牵引机待料条牵引完 毕后关闭;
(3)后退定型台,松动模头紧固螺丝,松开连接法兰螺丝, 整体拆下模头,模具交付模具工清理;
(4)松开定型模底脚紧固丝,关闭主水阀,拔掉水、气管。 (5)关闭总电源,收拾工具,打扫现场卫生。 注:停机清理定型模执行(1)(2),清理模头还需执行
比如850r/min左右,低速排料, 转 速150r/min左右。
(4)混合温度:视冷热混合情况而定。 (5)混合时间:一般为5-15min。
二、异型材成型工艺控制
物料混合包括热混和冷混。
热混的目的是将物料中各个组
分颗粒达到最大程度的分布,使 物料升温,达到预塑化,如PVC 热混温度控制在115~120℃。
挥发物含量过多 产生分解气体
大
增加螺杆压缩比, 使排气完全
异型材成型工艺

异型材成型工艺异型材挤出成型复习资料第一章绪论挤出成型的定义:在挤出机中通过加热、加压而使物料以流动状态通过口模成型的方法称为挤出成型。
或称为挤塑。
挤出成型需要的设备:挤出机;机头口模;冷却装置;定型装置;牵引装置;切割装置;卷曲装置挤出成型的优点:1.设备成本低,制造容易,投资少,见效快。
2.生产效率高。
3.可以连续化生产。
4.生产操作简单,工艺控制容易,易于实现自动化。
5.可以一机多用。
挤出成型主要的产品:薄膜;管材;板材;片材;型材;电线电缆包覆;棒材;丝;网;带;中空容器;泡沫塑料;合材料;挤出成型发展趋势:1.产品向多样化发展。
2.高速化,自动化。
第二章挤出设备挤出设备的组成:1.挤出机2.辅机3.控制系统挤出机的组成:1.挤压系统:主要由螺杆和料筒组成,是挤出机的关键部件。
2.传动系统:其作用是驱动螺杆,保证螺杆在挤出过程中所需要的扭矩和转速。
3.加热系统:用来保证塑料在成型加工中的温度控制要求。
挤出机的分类:1.螺杆的数量:无螺杆挤出机、单螺杆挤出机、双螺杆挤出机、多螺杆挤出机2.螺杆的转速:普通挤出机、高速挤出机、超高速挤出机3.安装位置:卧式挤出机、立式挤出机4.装配结构:整体式挤出机、分开式挤出机5.排气结构:排气式挤出机、非排气式挤出机螺杆技术参数:1.螺杆直径(D) 是指螺杆外径,单位mm2.螺杆长径比(L/D) L为螺杆的工作部分(有效部分)长度(工艺上将L定义为加料口中心线到螺纹末端的长度)3.压缩比:螺杆加料段第一个螺槽容积与均化段最后一个螺槽容积之比。
4.螺杆转速范围5.螺槽深度:6.螺槽螺距:7.螺纹升角:8.螺纹头数:9.螺楞宽度:10.螺杆外径与机筒内壁的间隙。
螺杆各段的作用:1.加料段:对塑料进行预热、压实和输送。
2.熔融段:使塑料进一步压实和塑化使包围在塑料内的空气压回到加料口处排出,并改善塑料的热传导性能,。
3.均化段:塑料进入均化段后进一步塑化和均匀化,并使之定量、定压、定温地从机头挤出。
塑料异型材挤出工艺参数设定、控制依据与标准

塑料异型材挤出工艺参数设定、控制依据与标准绪言塑料异型材是在挤出机一定温度和螺杆摩擦、压延、剪切作用下均衡塑化加工成型的。
挤出机各项工艺参数,即挤出温度,螺杆温度,给料速度,挤出速度,牵引速度,熔体压力,扭矩,口模熔压,型材密实度,口模与定型模真空度,定型冷却温度,牵引压力等项参数技术指标的设定和控制对挤出型材塑化的外观和内在质量十分重要。
正确设定和控制以上工艺参数是每一个型材生产操作者应具备的技术技能。
现根据笔者十几年工作经验,将以什么为基准,正确设定和控制各项工艺参数以及出现一些非常情况的应对措施,谈一点自已的看法和意见,与行业各位行家交流,共勉,以共同促进塑料异型材质量水平提高。
不当之处请批评、指正。
塑料异型材工艺参数设定和控制依据与标准1、挤出温度的设定和控制由于PVC-U物料对温度比较敏感,塑料异型材挤出成型是在塑化温度和降解温度之间相对狭窄的温度区域进行的。
因锥形双螺杆机挤出型材供物料塑化,并抑制物料降解,分别对应有两个热源与冷源:一个热源是电加热圈提供给机筒的外热。
外热温控系统大致由10个温控点组成。
依据物料在挤出过程各个阶段的形态,承担热量供应工作。
因此可归纳为加温、恒温、保温三个区域。
其中加温与恒温区主要在挤出机内进行,以排气孔为界划分为两个相对独立又互为关联的部分。
所供热量由仪表电器进行控制。
依据挤出型材工艺要求,设定温度值,启动机筒各段电加热圈工作,当机筒加热达到设定温度值时,则通过温度传感器给模块数据,自动切断加热电源,加热停止,此时螺筒处于保温状态;当显示温度达不到设定温度指标参数时,加热圈就一直不间断工作。
另一个热源是由螺筒和螺杆产生的摩擦、压延、剪切热(简称剪切热),是不能自控的,主要由给料速度和螺杆结构形式所决定;一个冷源是安装在螺筒熔融段与计量段位置上的风机实施的。
当螺筒加热时,风机不工作,当显示温度达到或超过设定温度指标参数,螺筒加热圈加热停止的同时,温控系统自动启动冷却风机,进行强制冷却;另一个冷源是螺杆内部调温装置,通过预先设定一个温度指标,启动螺杆芯温电机、调温装置的加热器对油箱导热介质(硅油)加热,当螺杆物料温度高于设定温度时,通过温度控制元件控制水冷却装置对油箱内导热介质(硅油)进行冷却。
- 1、下载文档前请自行甄别文档内容的完整性,平台不提供额外的编辑、内容补充、找答案等附加服务。
- 2、"仅部分预览"的文档,不可在线预览部分如存在完整性等问题,可反馈申请退款(可完整预览的文档不适用该条件!)。
- 3、如文档侵犯您的权益,请联系客服反馈,我们会尽快为您处理(人工客服工作时间:9:00-18:30)。
工艺条件控制
6
常见故障排除
常见异型材挤出缺陷的可能原因分析;
型材挤出机的使用与维护
异型材挤出制品缺陷分析及排查
7
硬聚氯乙烯结皮发泡钢塑共挤型材
钢塑异型材的配方、生产工艺、生产设备以及产品结构
结皮微发泡成型工艺过程;
硬聚氯乙烯结皮发泡钢塑共挤机头结构分析
8
双组份异型材
双组分异型材共挤出机头结构分析、共挤出对树脂的流动性能和工艺要求、两种熔融流体的界面
两种熔融流体的界面
双组分异型材机头结构分析
9
木塑异型材
木塑异型材的配方组成;
木塑异型材的加工设备设计要点;
木塑异型材加工工艺控制要点
木塑异型材配方组成
异型材截面设计原则
常见异型材截面分析与改进
成型温度控制
异型材挤出工艺规程
异型材挤出机的使用与维护
常见异型材挤出缺陷及故障排除
项目4异型材挤出——重点难点
序号
单元名称
重点
难点
1
异型材生产整体认识、技术进展
常见异型材简介;
异型材应用;
异型材生产设备以及工艺流程初步认识;
新型异型材机头简介
新型异型材机头结构分析
2
异型材挤出辅线技术
多板式定型、滑移式定型、真空定型以及内芯定型的结构、方法、设计以及应用
各类牵引装置的特点以及适用范围。
各类定型装置的原理;
各类定型装置Байду номын сангаас选择
3
异型材截面设计
异型材截面设计的基本原则;
异型材截面的设计要点;
简单异型材截面设计
表面粗糙度;
截面形状与结构;
界面壁厚;
4
异型材挤出机头
异型材机头分类以及特点;
异型材机头结构;
异型材机头设计原则
机头结构分析
机头结构设计
5
异型材成型工艺
异型材挤出工艺基本流程和工艺参数分析;