半导体晶圆切割
半导体晶圆切割工艺
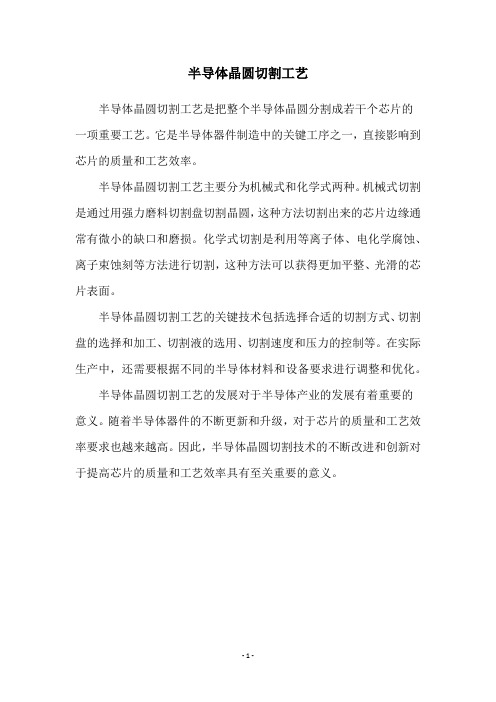
半导体晶圆切割工艺
半导体晶圆切割工艺是把整个半导体晶圆分割成若干个芯片的
一项重要工艺。
它是半导体器件制造中的关键工序之一,直接影响到芯片的质量和工艺效率。
半导体晶圆切割工艺主要分为机械式和化学式两种。
机械式切割是通过用强力磨料切割盘切割晶圆,这种方法切割出来的芯片边缘通常有微小的缺口和磨损。
化学式切割是利用等离子体、电化学腐蚀、离子束蚀刻等方法进行切割,这种方法可以获得更加平整、光滑的芯片表面。
半导体晶圆切割工艺的关键技术包括选择合适的切割方式、切割盘的选择和加工、切割液的选用、切割速度和压力的控制等。
在实际生产中,还需要根据不同的半导体材料和设备要求进行调整和优化。
半导体晶圆切割工艺的发展对于半导体产业的发展有着重要的
意义。
随着半导体器件的不断更新和升级,对于芯片的质量和工艺效率要求也越来越高。
因此,半导体晶圆切割技术的不断改进和创新对于提高芯片的质量和工艺效率具有至关重要的意义。
- 1 -。
半导体元件生产的简易流程
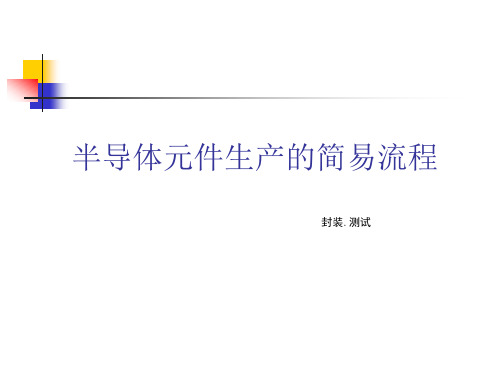
滴有凝胶(solder)的框架 wafer
日本 NEC
Die bond完成品
3 连线(Wire bond)
用金线.铜线或铝线做导线把chip上的线路与框架的管脚进行连接,从而行 成元件的各个电极。 金线稳定性最好,但做大功率管时需要线数多,成本较高,所以 现在不少产品改为铝线和铜线。
阳极 阴极 控制极 门极gate 源极source
1 晶圆切割(sawing)
把整片晶片切割成一个独立的单元 Chip ; Die。 首先要进行贴膜,把晶圆贴在蓝色的膜(wafer tube)上,以膜为载体, 以便切割。 通过自动切片机按照要求的尺寸来进行切割。有的产品在切片之前还要进 行晶圆背面的打磨。使其厚度达到要求,晶圆不能太薄以免在运输过程中 破碎。常用全自动切片机日本的 Disco。 晶圆材料主要用的模具
待注模产品
5 镀锡(Planting)
用镀锡机对元件的裸铜管脚进行镀锡。 主要目的是防止管脚氧化而影响元件性能。
裸铜框架
框架镀锡
6 切筋(tram form)
分割成独立的元件,对剩余部分进行加工形成元件的管脚。 T/F所用设备多以PLC为控制单元,通过电磁阀的通.断来控制汽缸的动作, 完成工作。
晶圆
经贴膜.切割后的晶片 (wafer)
Die
2 贴片(Die bond )
把chip 粘贴到铜框架上. 切好的晶圆放到贴片机上,通过真空(collect)把晶片吸起然后粘贴在滴有凝胶的铜 框架上。常用的凝胶有两种:Epoxy,solder。Solder产品贴片后可直接进行下一 工序焊线;Epoxy产品需要加热凝固后才可进行焊线。 目前大芯片贴片机常用瑞士的 ESEC; 小芯片.LED等贴片常用新加坡的 ASM. 日本的佳能(Canon)
半导体晶圆切割工艺
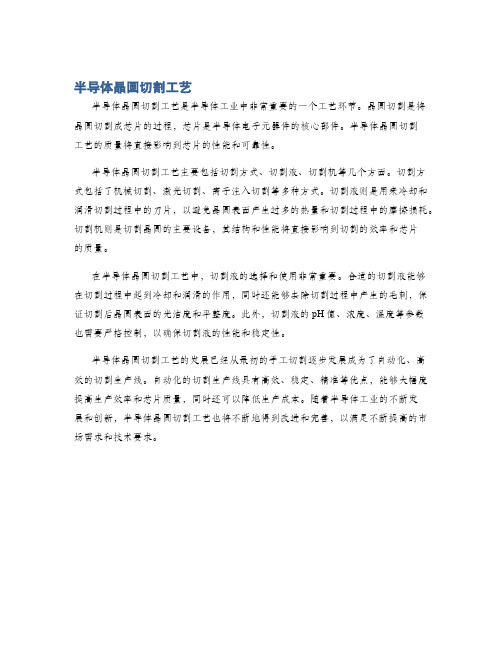
半导体晶圆切割工艺
半导体晶圆切割工艺是半导体工业中非常重要的一个工艺环节。
晶圆切割是将晶圆切割成芯片的过程,芯片是半导体电子元器件的核心部件。
半导体晶圆切割
工艺的质量将直接影响到芯片的性能和可靠性。
半导体晶圆切割工艺主要包括切割方式、切割液、切割机等几个方面。
切割方式包括了机械切割、激光切割、离子注入切割等多种方式。
切割液则是用来冷却和润滑切割过程中的刀片,以避免晶圆表面产生过多的热量和切割过程中的摩擦损耗。
切割机则是切割晶圆的主要设备,其结构和性能将直接影响到切割的效率和芯片
的质量。
在半导体晶圆切割工艺中,切割液的选择和使用非常重要。
合适的切割液能够在切割过程中起到冷却和润滑的作用,同时还能够去除切割过程中产生的毛刺,保证切割后晶圆表面的光洁度和平整度。
此外,切割液的pH值、浓度、温度等参数
也需要严格控制,以确保切割液的性能和稳定性。
半导体晶圆切割工艺的发展已经从最初的手工切割逐步发展成为了自动化、高效的切割生产线。
自动化的切割生产线具有高效、稳定、精准等优点,能够大幅度提高生产效率和芯片质量,同时还可以降低生产成本。
随着半导体工业的不断发
展和创新,半导体晶圆切割工艺也将不断地得到改进和完善,以满足不断提高的市场需求和技术要求。
晶圆切割die数dpw计算公式

晶圆切割Die数DPW计算公式引言概述:在半导体制造中,晶圆是半导体芯片的基础,而晶圆上的小块区域被称为Die。
DPW(Dies Per Wafer)是一个关键的性能指标,它表示在一个晶圆上能切割出的Die的数量。
本文将详细介绍晶圆切割Die数DPW的计算公式,以及与该公式相关的重要参数。
正文:1. 晶圆切割Die数DPW的计算公式1.1 晶圆面积与Die数关系:晶圆直径与面积计算:解释晶圆直径与面积的关系,介绍常用的晶圆面积计算公式。
Die的尺寸与面积关系:阐述Die的尺寸如何影响Die的面积计算,说明在制造中常见的Die尺寸标准。
1.2 有效利用晶圆面积:排列方式的选择:探讨晶圆上Die的排列方式,以及不同排列方式对DPW的影响。
晶圆边缘效应:解释晶圆边缘部分的效应,以及在计算DPW时如何考虑晶圆边缘的影响。
1.3 其他因素的考虑:切割误差的补偿:介绍在实际切割过程中可能出现的误差,以及如何在计算DPW时进行补偿。
晶圆上的保留区域:讨论晶圆上可能需要保留的区域,以及这些区域如何影响DPW的计算。
2. 与DPW计算公式相关的重要参数2.1 晶圆直径(Diameter):直径的测量与影响:介绍晶圆直径的测量方法,以及晶圆直径对DPW的影响。
常见晶圆直径尺寸:提供常见的晶圆直径尺寸,说明它们在不同制造环境中的应用。
2.2 Die的尺寸(Die Size):Die尺寸的标准:解释Die尺寸的标准化,以及标准尺寸对DPW 的计算的重要性。
尺寸的测量与控制:介绍如何测量Die的尺寸,并控制制造过程中的尺寸变化。
2.3 晶圆的形状(Wafer Shape):不同形状的晶圆:探讨不同形状晶圆的特点,以及这些形状对DPW计算的影响。
形状的变化与制程:说明晶圆形状可能因制程变化而引起的影响。
3. DPW计算的应用与优化策略3.1 制造成本的考虑:DPW与成本关系:分析DPW与制造成本的关系,讨论如何在提高DPW的同时降低制造成本。
半导体晶圆切割的重要意义
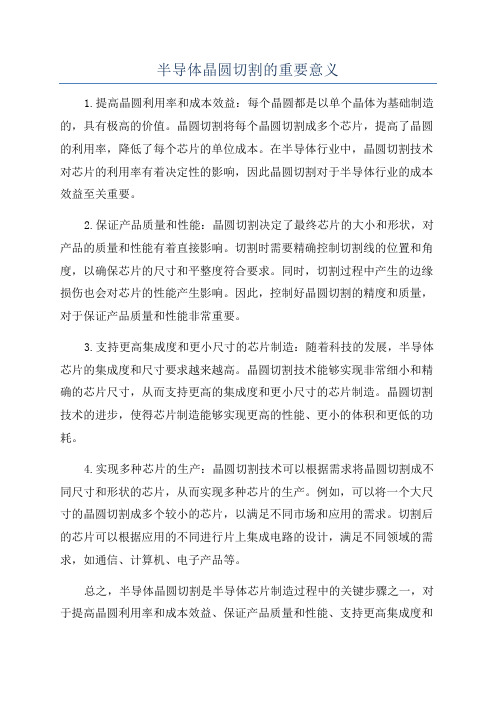
半导体晶圆切割的重要意义
1.提高晶圆利用率和成本效益:每个晶圆都是以单个晶体为基础制造的,具有极高的价值。
晶圆切割将每个晶圆切割成多个芯片,提高了晶圆的利用率,降低了每个芯片的单位成本。
在半导体行业中,晶圆切割技术对芯片的利用率有着决定性的影响,因此晶圆切割对于半导体行业的成本效益至关重要。
2.保证产品质量和性能:晶圆切割决定了最终芯片的大小和形状,对产品的质量和性能有着直接影响。
切割时需要精确控制切割线的位置和角度,以确保芯片的尺寸和平整度符合要求。
同时,切割过程中产生的边缘损伤也会对芯片的性能产生影响。
因此,控制好晶圆切割的精度和质量,对于保证产品质量和性能非常重要。
3.支持更高集成度和更小尺寸的芯片制造:随着科技的发展,半导体芯片的集成度和尺寸要求越来越高。
晶圆切割技术能够实现非常细小和精确的芯片尺寸,从而支持更高的集成度和更小尺寸的芯片制造。
晶圆切割技术的进步,使得芯片制造能够实现更高的性能、更小的体积和更低的功耗。
4.实现多种芯片的生产:晶圆切割技术可以根据需求将晶圆切割成不同尺寸和形状的芯片,从而实现多种芯片的生产。
例如,可以将一个大尺寸的晶圆切割成多个较小的芯片,以满足不同市场和应用的需求。
切割后的芯片可以根据应用的不同进行片上集成电路的设计,满足不同领域的需求,如通信、计算机、电子产品等。
总之,半导体晶圆切割是半导体芯片制造过程中的关键步骤之一,对于提高晶圆利用率和成本效益、保证产品质量和性能、支持更高集成度和
更小尺寸的芯片制造以及实现多种芯片的生产都具有重要意义。
随着技术的不断进步,晶圆切割技术也将继续发展,为半导体行业的发展提供更好的支撑。
晶圆工艺的切割方法
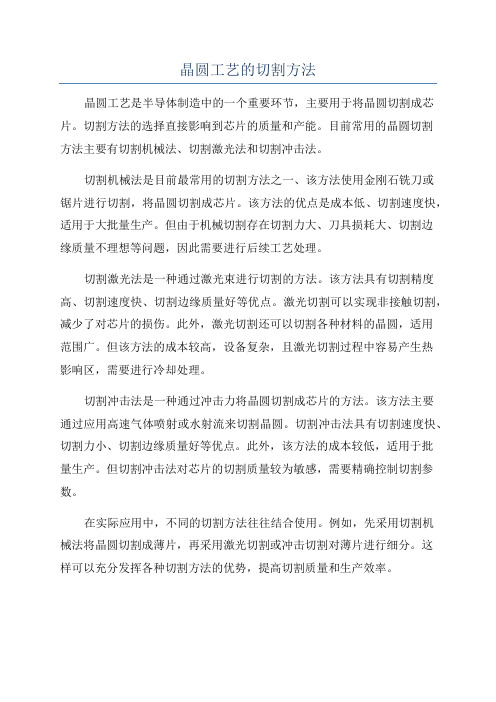
晶圆工艺的切割方法晶圆工艺是半导体制造中的一个重要环节,主要用于将晶圆切割成芯片。
切割方法的选择直接影响到芯片的质量和产能。
目前常用的晶圆切割方法主要有切割机械法、切割激光法和切割冲击法。
切割机械法是目前最常用的切割方法之一、该方法使用金刚石铣刀或锯片进行切割,将晶圆切割成芯片。
该方法的优点是成本低、切割速度快,适用于大批量生产。
但由于机械切割存在切割力大、刀具损耗大、切割边缘质量不理想等问题,因此需要进行后续工艺处理。
切割激光法是一种通过激光束进行切割的方法。
该方法具有切割精度高、切割速度快、切割边缘质量好等优点。
激光切割可以实现非接触切割,减少了对芯片的损伤。
此外,激光切割还可以切割各种材料的晶圆,适用范围广。
但该方法的成本较高,设备复杂,且激光切割过程中容易产生热影响区,需要进行冷却处理。
切割冲击法是一种通过冲击力将晶圆切割成芯片的方法。
该方法主要通过应用高速气体喷射或水射流来切割晶圆。
切割冲击法具有切割速度快、切割力小、切割边缘质量好等优点。
此外,该方法的成本较低,适用于批量生产。
但切割冲击法对芯片的切割质量较为敏感,需要精确控制切割参数。
在实际应用中,不同的切割方法往往结合使用。
例如,先采用切割机械法将晶圆切割成薄片,再采用激光切割或冲击切割对薄片进行细分。
这样可以充分发挥各种切割方法的优势,提高切割质量和生产效率。
总之,晶圆工艺的切割方法是半导体制造中的重要环节,不同的切割方法各有优劣。
通过合理选择切割方法,并结合其他工艺步骤,可以实现高质量和高产能的芯片生产。
【半导体切片】半导体晶圆切割 - 副本
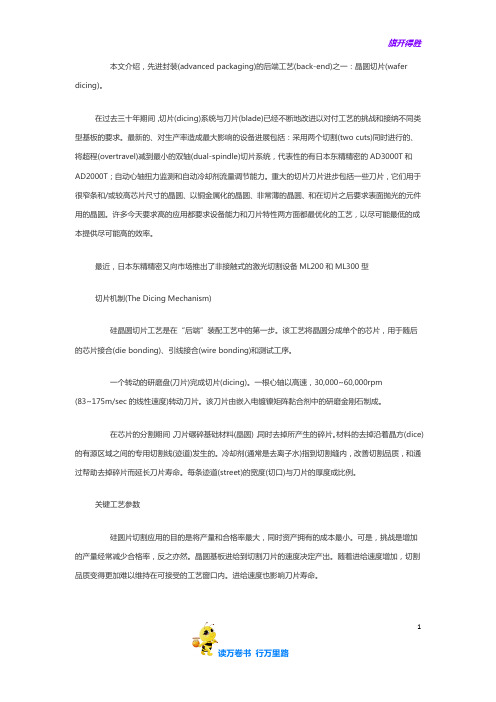
本文介绍,先进封装(advanced packaging)的后端工艺(back-end)之一:晶圆切片(wafer dicing)。
在过去三十年期间,切片(dicing)系统与刀片(blade)已经不断地改进以对付工艺的挑战和接纳不同类型基板的要求。
最新的、对生产率造成最大影响的设备进展包括:采用两个切割(two cuts)同时进行的、将超程(overtravel)减到最小的双轴(dual-spindle)切片系统,代表性的有日本东精精密的AD3000T和AD2000T;自动心轴扭力监测和自动冷却剂流量调节能力。
重大的切片刀片进步包括一些刀片,它们用于很窄条和/或较高芯片尺寸的晶圆、以铜金属化的晶圆、非常薄的晶圆、和在切片之后要求表面抛光的元件用的晶圆。
许多今天要求高的应用都要求设备能力和刀片特性两方面都最优化的工艺,以尽可能最低的成本提供尽可能高的效率。
最近,日本东精精密又向市场推出了非接触式的激光切割设备ML200和ML300型切片机制(The Dicing Mechanism)硅晶圆切片工艺是在“后端”装配工艺中的第一步。
该工艺将晶圆分成单个的芯片,用于随后的芯片接合(die bonding)、引线接合(wire bonding)和测试工序。
一个转动的研磨盘(刀片)完成切片(dicing)。
一根心轴以高速,30,000~60,000rpm(83~175m/sec的线性速度)转动刀片。
该刀片由嵌入电镀镍矩阵黏合剂中的研磨金刚石制成。
在芯片的分割期间,刀片碾碎基础材料(晶圆),同时去掉所产生的碎片。
材料的去掉沿着晶方(dice)的有源区域之间的专用切割线(迹道)发生的。
冷却剂(通常是去离子水)指到切割缝内,改善切割品质,和通过帮助去掉碎片而延长刀片寿命。
每条迹道(street)的宽度(切口)与刀片的厚度成比例。
关键工艺参数硅圆片切割应用的目的是将产量和合格率最大,同时资产拥有的成本最小。
可是,挑战是增加的产量经常减少合格率,反之亦然。
半导体晶圆切割工艺
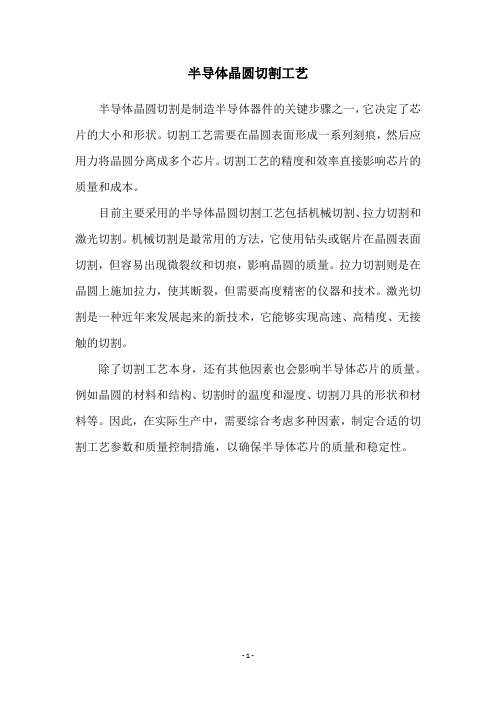
半导体晶圆切割工艺
半导体晶圆切割是制造半导体器件的关键步骤之一,它决定了芯片的大小和形状。
切割工艺需要在晶圆表面形成一系列刻痕,然后应用力将晶圆分离成多个芯片。
切割工艺的精度和效率直接影响芯片的质量和成本。
目前主要采用的半导体晶圆切割工艺包括机械切割、拉力切割和激光切割。
机械切割是最常用的方法,它使用钻头或锯片在晶圆表面切割,但容易出现微裂纹和切痕,影响晶圆的质量。
拉力切割则是在晶圆上施加拉力,使其断裂,但需要高度精密的仪器和技术。
激光切割是一种近年来发展起来的新技术,它能够实现高速、高精度、无接触的切割。
除了切割工艺本身,还有其他因素也会影响半导体芯片的质量。
例如晶圆的材料和结构、切割时的温度和湿度、切割刀具的形状和材料等。
因此,在实际生产中,需要综合考虑多种因素,制定合适的切割工艺参数和质量控制措施,以确保半导体芯片的质量和稳定性。
- 1 -。
- 1、下载文档前请自行甄别文档内容的完整性,平台不提供额外的编辑、内容补充、找答案等附加服务。
- 2、"仅部分预览"的文档,不可在线预览部分如存在完整性等问题,可反馈申请退款(可完整预览的文档不适用该条件!)。
- 3、如文档侵犯您的权益,请联系客服反馈,我们会尽快为您处理(人工客服工作时间:9:00-18:30)。
By Dianne Shi and Ilan Weisshas本文介绍,先进圭寸装(advaneed packaging的后端工艺(back-end)之一:xx 圆切片(wafer dicing)。
在过去三十年期间,切片(dieing)系统与刀片(blade)已经不断地改进以对付工艺的挑战和接纳不同类型基板的要求。
最新的、对生产率造成最大影响的设备进展包括:采用两个切割(two cuts)同时进行的、将超程(overtravel)减到最小的双轴(dual-spindle)切片系统,代表性的有日本东精精密的AD3000T和AD2000T;自动心轴扭力监测和自动冷却剂流量调节能力。
重大的切片刀片进步包括一些刀片,它们用于很窄条和/或较高芯片尺寸的晶圆、以铜金属化的晶圆、非常薄的晶圆、和在切片之后要求表面抛光的元件用的晶圆。
许多今天要求高的应用都要求设备能力和刀片特性两方面都最优化的工艺,以尽可能最低的成本提供尽可能高的效率。
最近,日本东精精密又向市场推出了非接触式的激光切割设备ML200和ML300 型切片机制(The Dicing Mechanism)硅晶圆切片工艺是在“后端”装配工艺中的第一步。
该工艺将晶圆分成单个的芯片,用于随后的芯片接合(die bon di ng)、弓I线接合(wire bonding)和测试工序。
一个转动的研磨盘(刀片)完成切片(dicing)。
一根心轴以高速,30,000~60,000rpm (83~175m/sec的线性速度)转动刀片。
该刀片由嵌入电镀镍矩阵黏合剂中的研磨金刚石制成。
在芯片的分割期间,刀片碾碎基础材料(晶圆),同时去掉所产生的碎片。
材料的去掉沿着晶方(dice)的有源区域之间的专用切割线(迹道)发生的。
冷却剂(通常是去离子水)指到切割缝内,改善切割品质,和通过帮助去掉碎片而延长刀片寿命。
每条迹道(street)的宽度(切口)与刀片的厚度成比例。
关键工艺参数硅圆片切割应用的目的是将产量和合格率最大,同时资产拥有的成本最小。
可是,挑战是增加的产量经常减少合格率,反之亦然。
晶圆基板进给到切割刀片的速度决定产出。
随着进给速度增加,切割品质变得更加难以维持在可接受的工艺窗口内。
进给速度也影响刀片寿命。
在许多晶圆的切割期间经常遇到的较窄迹道(street)宽度,要求将每一次切割放在迹道中心几微米范围内的能力。
这就要求使用具有高分度轴精度、高光学放大和先进对准运算的设备。
当用窄迹道切割晶圆时的一个常见的推荐是,选择尽可能最薄的刀片。
可是,很薄的刀片(20卩m是非常脆弱的,更容易过早破裂和磨损。
结果,其寿命期望和工艺稳定性都比较厚的刀片差。
对于50~76^m迹道的刀片推荐厚度应该是20~30 ^m。
碎片(Chipping)顶面碎片(TSC, top-side chipping,) 它发生晶圆的顶面,变成一个合格率问题,当切片接近芯片的有源区域时,主要依靠刀片磨砂粒度、冷却剂流量和进给速度(图1a)。
背面碎片(BSC, back-side chippin发生在晶圆的底面,当大的、不规则微小裂纹从切割的底面扩散开并汇合到一起的时候(图1b)。
当这些微小裂纹足够长而引起不可接受的大颗粒从切口除掉的时候,BSC变成一个合格率问题。
通常,切割的硅晶圆的质量标准是:如果背面碎片的尺寸在10“以下,忽略不计。
另一方面,当尺寸大于25 ^m时,可以看作是潜在的受损。
可是,50 ^m的平均大小可以接受,示晶圆的厚度而定。
现在可用来控制背面碎片的工具和技术是刀片的优化,接着工艺参数的优化。
刀片优化(Blade Optimization)为了接收今天新的切片挑战,切片系统与刀片之间的协作是必要的。
对于高端(high-e nd)应用特别如此。
刀片在工艺优化中起主要的作用。
为了接纳所有来自于迅速的技术发展的新的切片要求,今天可以买到各种各样的刀片。
这使得为正确的工艺选择正确的刀片成为一个比以前更加复杂的任务。
除了尺寸,三个关键参数决定刀片特性:金刚石(磨料)尺寸、金刚石含量和粘结剂的类型。
结合物是各种金属和/或其中分布有金刚石磨料的基体。
这些元素的结合效果决定刀片的寿命和切削质量(TSC与BSC)改变任何一个这些参数都将直接影响刀片特性与性能。
为一个给定的切片工艺选择最佳的刀片可能要求在刀片寿命与切削质量之间作出平衡。
其它因素,诸如进给率和心轴速度,也可能影响刀片选择。
切割参数对材料清除率有直接关系,它反过来影响刀片的性能和工艺效率。
对于一个工艺为了优化刀片,设计试验方法(DOE, designedexperiment可减少所需试验的次数,并提供刀片特性与工艺参数的结合效果。
另外,设计试验方法(DOE的统计分析使得可以对有用信息的推断,以建议达到甚至更高产出和/或更低资产拥有成本的进一步工艺优化。
图二显示在以30,000rpm 心轴速度进行的硅晶圆切片期间,进给率、刀片磨料尺寸和刀片寿命的结合效果。
图三详细显示相应得切削品质。
正如所料,在某个工艺窗口之内,随着磨料尺寸的增加,刀片寿命增加(或磨损率下降),而切削品质(在这种情况中TSC下降。
越细的磨料尺寸提供在以适当的进给率时更高的顶面切削质量,虽然刀片寿命减少很多。
如所提及的,增加产出是在晶圆切片中的减少成本的主要问题。
更高的进给率和/或心轴速度是最常考虑到的影响参数。
可是,取决于三个关键的刀片参数、晶圆的特性和厚度、和在迹道中的金属化程度,在一套工艺条件下的“完美刀片”可能在条件改变时不适合。
如图二和三所示,随着进给速率的增加,刀片寿命和切削质量两者都会变化,不管磨料尺寸如何。
当优化一个工艺时,重要的是并行地考虑各种主要工艺和刀片的参数,以使产出达到最大,同时保持足够的刀片寿命和可接受的切削质量。
在选择刀片类型来最大减少资产拥有成本的时候,可能要求一个折中。
与那些可能常见的东西相反,较慢的进给速度不总是保证更好的切削品质。
差劣的切削品质可能在太慢的进给率时产生,由于产生更高的热量(图三)。
达到可接受的切削品质的最小进给速度应是指对于一个给定的切片应用。
这是一个可应用于各种晶圆切片的一般结论。
当使用很慢的进给速度时,在切片铜(Cu)晶圆时可观察到较高的BSC1当以很慢的转速切片时观察到相同的效果。
三个关键的刀片元素(金刚石尺寸、浓度和结合物硬度)的相对重要性取决于刀片磨料尺寸和工艺参数。
为了给一个特定应用选择最适合的刀片,对这些关系的理解是必要的。
图四是对由于或者刀片金刚石浓度增加或者粘合物硬度增加而使刀片磨损百分率下降的一个DOE评估。
一般来说,粘结硬度对刀片寿命的影响对于较细金刚砂更为显著。
随着磨料尺寸增加,粘结硬度的影响变得越来越不重要。
可是,对于所有磨料尺寸,金刚石浓度的影响似乎比粘结硬度更为重要。
取决于磨料尺寸变化的程度,其对刀片寿命的影响可能是所有三个刀片参数中最重要的。
作为一般规则,较细金刚砂的刀片对刀片和/或工艺参数变化更加敏感。
当BSC需要改进时,较软的粘结和/或较低的金刚砂浓度经常是必须的。
或者粘结硬度或者金刚砂浓度的改变可降低刀片的寿命。
为了选择一个刀片,重要的还要理解刀片的外表硬度的影响(经常叫做基体硬度)。
这是刀片的硬度的抽象测量,它反映在切割晶圆时刀片的“感觉”方式。
基体硬度通过金刚砂磨料尺寸、浓度和粘结硬度的结合影响来决定。
通常,较细的磨料尺寸、较高的金刚砂浓度和较硬的粘合物将得到增加的基体硬度。
通常建议,与其它考虑因素一起,较硬的材料要求较软的(基体)刀片来切片,反之亦然。
例如,砷化镓(GaAs晶圆一般要求较细的金刚砂尺寸(较硬的刀片),而钽酸锂(LiTaO3晶圆最适合于较粗的金刚砂尺寸和较低的金刚石浓度(较软的刀片)。
随着非硅(non-Si)材料使用的进步,将达到对这些类型的先进晶圆切片应用的更深理解。
刀片负载监测(Blade Load Monitering)在切片或任何其它磨削过程中,在不超出可接受的切削质量参数时,新一代的切片系统可以自动监测施加在刀片上的负载,或扭矩。
对于每一套工艺参数,都有一个切片质量下降和BSC出现的极限扭矩值。
切削质量与刀片基板相互作用力的相互关系,和其变量的测量使得可以决定工艺偏差和损伤的形成。
工艺参数可以实时调整,使得不超过扭矩极限和获得最大的进给速度。
切片工序的关键部分是切割刀片的修整(dressing)。
在非监测的切片系统中,修整工序是通过一套反复试验来建立的。
在刀片负载受监测的系统中,修整的终点是通过测量的力量数据来发现的,它建立最佳的修整程序。
这个方法有两个优点:不需要限时来保证最佳的刀片性能,和没有合格率损失,该损失是由于用部分修整的刀片切片所造成的质量差。
冷却剂流量稳定(Coolant Flow Stabilization)以稳定的扭矩运转的系统要求进给率、心轴速度和冷却剂流量的稳定。
冷却剂在刀片上施加阻力,它造成扭力。
最新一代的切片系统通过控制冷却剂流量来保持稳定的流速和阻力,从而保持冷却剂扭矩影响稳定。
当切片机有稳定的冷却剂流量和所有其它参数都受控制时,维持一个稳定的扭矩。
如果记录,从稳定扭矩的任何偏离都是由于不受控的因素。
这些包括由于喷嘴堵塞的冷却剂流量变化、喷嘴调整的变化、刀片对刀片的变化、刀片情况和操作员错误。
总结切片工艺变得越来越且要求高。
切割迹道变得越窄,可能充满测试用衰耗器(test pad),并且刀片可能需要切割由不同材料制成的各种涂敷层。
在这些条件下达到最大的切片工艺合格率和生产率要求认真的刀片选择和先进的工艺控制能力。