(管理制度)丰田式管理制度培训课程
丰田公司流程管理制度

丰田公司流程管理制度一、公司概况丰田汽车公司是一家知名的全球汽车制造商,总部位于日本。
公司成立于1937年,至今已经有近80年的历史。
丰田公司的产品涵盖了轿车、卡车、SUV等多个领域,在全球范围内享有盛誉。
作为一家先进的汽车制造商,丰田公司一直以来注重流程管理,致力于提高生产效率和产品质量,以满足消费者的需求。
二、流程管理制度的重要性在汽车制造领域,流程管理是至关重要的。
一个高效的流程管理系统可以有效地提高生产效率、降低生产成本,同时还能够提高产品质量和客户满意度。
流程管理制度不仅能够帮助企业实现高效的生产,还可以帮助企业管理人员监控和控制生产过程,确保生产活动按照规定的程序进行,从而避免出现生产故障和质量问题。
三、丰田公司的流程管理制度丰田公司一直以来都非常重视流程管理,并建立了一套完善的流程管理制度,以确保企业的运营顺利进行。
以下是丰田公司流程管理制度的主要内容:1. 流程优化:丰田公司不断优化生产流程,消除不必要的环节和浪费,提高生产效率。
公司定期对生产流程进行评估和优化,确保生产活动尽可能地精简和高效。
2. 流程标准化:丰田公司建立了一套统一的生产标准和操作流程,以确保各个生产环节按照相同的程序进行。
标准化的流程可以帮助员工减少错误,提高工作效率,同时还可以提高产品的一致性和质量。
3. 流程监控:丰田公司建立了一套完善的流程监控系统,用于监测生产过程中的各个环节。
公司管理人员可以随时查看生产数据和报表,以确保生产活动按照规定的程序进行,及时发现和解决问题。
4. 流程改进:丰田公司重视持续改进和创新,不断优化生产流程,提高生产效率和产品质量。
公司鼓励员工提出改进和创新的建议,倡导团队合作,共同推动流程改进。
5. 培训和考核:丰田公司注重员工的培训和考核,以确保员工掌握标准化的流程和操作程序。
公司定期开展培训课程,帮助员工提升技能和业务水平,同时对员工的表现进行考核和评估,激励员工努力工作。
6s管理制度管理制度

6s管理制度管理制度1. 引言在现代企业管理中,持续改进和提高工作效率是至关重要的。
为了达到这个目标,许多公司采用了6s管理制度。
6s是一个综合管理系统,它的目标是通过改进组织和清理工作环境来提高工作效率和员工满意度。
本文将介绍6s管理制度的重要性和实施步骤,以及它对企业的影响。
2. 什么是6s管理制度6s管理制度是源于日本丰田生产方式的管理方法。
在这种管理制度中,6个S代表了6个关键步骤,包括整理(seiri)、整顿(seiton)、清扫(seiso)、清洁(seiketsu)、标准化(seiketsu)和维持(sitsuke)。
- 整理(seiri):这一步骤旨在将工作场所清理出不必要的物品和杂乱的物品。
只留下必要的物品,并将它们适当地存放在易于获取的位置。
- 整顿(seiton):整顿是为了确保所有物品都有固定的位置,并且易于使用。
通过标记和组织工作区域,可以使员工轻松找到所需的工具和材料。
- 清扫(seiso):清扫是指定期清洁工作场所,包括地板、工作台和设备等。
这可以提高工作环境的安全性和美观度,并减少事故和错误的发生。
- 清洁(seiketsu):清洁是指保持工作区域的整洁和有序。
这需要员工定期清理和整理工作区域,并确保不再出现杂乱和脏乱的情况。
- 标准化(seiketsu):标准化是指确立清洁和整理的标准,并将其应用到整个组织。
这可以保持一致的工作环境,并提供一个基准来评估改进和持续改进。
- 维持(sitsuke):维持是指确保6s系统的长期有效性。
维持调查和审计可以确保员工遵守6s规定,并及时解决问题和改善措施。
3. 6s管理制度的实施步骤要实施6s管理制度,企业需要按照以下步骤进行:- 识别并定义目标:企业首先需要明确6s管理制度的目标和期望效果。
这有助于团队明确方向,并集中精力执行。
- 培训和宣传:企业需要对员工进行6s管理制度的培训,并宣传其重要性和好处。
这可以激发员工对改进工作环境的积极性和参与度。
精益5S5S管理培训

通过价值流分析,发现生产流程中的非增值活动,减少或消除浪 费。
优化生产布局
合理规划生产线布局,减少物料搬运距离和时间,提高生产效率。
引入自动化设备
采用自动化设备替代人工操作,提高生产流程的稳定性和效率。
2024/1/25
22
生产计划编排技巧分享
合理安排生产计划
根据市场需求、产能和物料供应情况,制定合理 的生产计划,确保生产顺利进行。
根据设备特性和使用要求,制定相应的维护保养 规程。
确定维护保养周期
根据设备使用频率和重要性,确定合理的维护保 养周期。
3
明确维护保养责任人
指定专门的设备维护保养人员,明确其职责和工 作要求。
2024/1/25
15
设备维护保养计划执行与检查
2024/1/25
制定维护保养计划
01
根据设备维护保养制度和周期,制定相应的维护保养计划。
案例二
某企业通过对生产流程进行价值流分析,发现并消除了多 个浪费环节,成功降低了生产成本20%。
案例三
某企业采用生产管理软件,实现了生产计划的自动化编排 和调整,提高了计划执行效率25%。
24
06 员工培训与素质 提升途径
2024/1/25
25
员工培训需求分析
2024/1/25
确定培训目标
明确培训的目的和预期结果,确保培训内容与组织战略和员工职 业发展相关。
2024/1/25
改善工作环境
通过保持工作场所整洁、有序,精益 5S5S管理可以改善员工的工作环境 ,提高员工满意度和士气。
培养员工素养
通过培养员工的自律性、责任感和团 队合作精神,精益5S5S管理可以提 升员工整体素养和企业形象。
“质量成本”体现了质量和成本的统一,跟着丰田学习质量管理、成本控制

“质量成本”体现了质量和成本的统⼀,跟着丰⽥学习质量管理、成本控制有⼈以为提⾼质量和降低成本是⽭盾的2个⽬标。
其实只要你想明⽩“质量成本”的概念,就会理解质量和成本是统⼀的,并不⽭盾。
如果你为了降低成本⽽选⽤了不符合要求的原材料,导致出现质量事故,客户不但会退货还要索赔,更要命的是砸了企业品牌,降低企业的品位。
员⼯培训的时候需要清除成本的构成,特别是质量成本的构成,把质量成本压缩到零。
丰⽥在2000年重点对“质量成本”进⾏培训,2003年丰⽥重点从市场出发推算成本效益的培训。
当然,质量成本真的到0难度巨⼤,⼀下⼦难以马上实现。
但是,起码可以把质量成本从4%降低到1%作为⼀个追求的⽬标。
丰⽥之所以取得如此骄⼈的业绩,离不开丰⽥全体员⼯执⾏“成本减半”的战略⽬标。
《降低成本50%的实际操作程序》为企业节流的必修课,是管理者的实⽤⼿册。
它不同于传统的成本降低法,从根本上打破了旧框架。
《降低成本50%的实际操作程序》从五⼤⽅法、21个⼩步骤⼈⼿,结合实际案例.为企业如何降低成本指明了⽅向,带给读者⼀种全新的体验。
书中所介绍的步骤具体周详,企业可以按部就班地拿来使⽤。
通过《降低成本50%的实际操作程序》,作者希望读者能够将每⼀个环节的操作应⽤到⼯作中,同时,也希望能够帮助企业真正节约成本。
丰⽥的某位董事兼任⼏家合作公司督导,必须每个⽉有数天在合作公司常驻,针对“问题在哪⾥、什么地⽅需要变⾰”提供指导。
丰⽥公司与合作公司之间保持着“集思⼴益”的关系,这种做法促进了合作公司的合理化。
降低成本,创造利润,⼤家较⽿熟能详的⽇式管理制度,莫过于以“及时⽣产”(Just In Time:JIT)制度为代表的丰⽥式⽣产管理体系。
然⽽,实际上在⽇本国内及欧美各国,⽇本创始的管理会计制度——“成本企划”所受到的重视并不亚于JIT,近年来更有⽇益重要的趋势,甚⽽有超越JIT的说法;那是因JIT仅为⽣产阶段之⼀的⽣产管理制度,⽽成本企划则是进⼊⽣产阶段前的各阶段降低成本与利润管理的综合性经营管理制度。
5S管理培训教材

1 宁波宜科旭阳纺织品有限公司――整理整顿清扫清洁素养――一、5S概述5S活动是日本企业普遍采用的一种现场方法,现已在世界许多国家得到推广应用;5S最早是丰田公司的现场管理实践中总结出来,随后,在其他企业中得到广泛普及。
5S是指整理(Seiri)、整顿(Seiton)、清扫(Seiso)、清洁(Seiketsu)和素养(Shitsuke);这 5个日语单词用罗马字拼时其第一个字母都是“S”,所以简称5S。
二、5S活动的目标(1)保证质量,提高工效;(2)降低消耗,降低成本;(3)保证机器设备的正常运行;(4)提高所有员工现场改进能力的途径。
三、5S活动的意义(1)提供一个舒适的工作环境;(2)提供一个安全的作业场所;(3)提升全体员工的工作热情;(4)稳定产品的质量水平;(5)提高现场的工作效率;(6)增加设备的使用寿命;1(7)良好的公司形象;(8)创造一个能让用户或亲友参观的厂房。
四、5S活动的功能(1)提升企业形象;(2)提升员工归属感;(3)提升效率;(4)保障品质;(5)减少浪费。
五、5S活动的要点(1)全员参与;(2)勤检查、勤鼓励,勤宣传;(3)各班组互相评比,竞赛;(4)班长要以身作则,做出榜样;(5)确定5S的整理、整顿、清扫、清洁四阶段的具体内容,作为日常管理的组成部分。
(6)贵在坚持,常抓不懈。
六、推行5S的理由实践证明5S推行不良,会产生下列不良后果:(1)影响人们的工作情绪;(2)造成职业伤害,发生各种安全事故;(3)降低设备的精度及使用寿命;2(4)由于标识不清而造成误用;(5)影响工作和产品质量。
七、5S的含义整理(Seiri)――明确区分需要的与不需要的物品,在生产现场保留需要的,消除不必要的物品;(红牌作战)1、整理目的(1)腾出空间,并充分利用;(2)防止误用无关的物品;(3)塑造清爽的工作场所。
2、整理的推行方法(1)深刻领会开展目的,建立共同的认识;a)确认不需要的东西,多余的库存会造成浪费;b)向全体员工宣讲,取得共识;c)下发整理的措施;d)规定整理要求。
丰田企业安全生产管理知识

安全投入资金主要用于:安全技术措施工程,如防火、通风;购置安全设备、器材、装备、仪器仪表及其维护;重大安全课题研究;配备劳动防护用品;安全教育培训;应急救援预案;其他.
3.2安全技术措施计划
生产经营单位为了保证安全资金的有效投入,应编制安全技术措施计划,该计划的核心是安全技术措施.
2. 生产经营单位安全生产的组织保障
2.1 生产经营单位安全生产管理机构的设置矿山、建筑施工单位和危险物品的生产、经营、储存单位,应当设置安全生产管理机构或者配备专职安全生产管理人员.
2.2 生产经营单位安全生产管理人员的设置 其他生产经营单位,从业人员超过300人的,应当设置安全生产管理机构或者配备专职安全生产管理人员;从业人员在300人以下的,应当配备专职或者兼职的安全生产管理人员,或者委托具有国家规定的相关专业技术资格的工程技术人员提供安全生产管理服务,保证安全生产的责任仍由本单位负责.
1.7 事故 是指造成人员死亡、伤害、职业病、财产损失或其他损失的意外事件. 是人们不希望发生的,同时违背人们的意愿后果.
1.8 事故隐患 指生产系统中可导致事故发生的人的不安全行为、物的不安全状态、环境的不安全条件和管理上的缺陷.
1.9 危险 是指系统中存在导致发生不期望后果的可能性超过了人们的承受程度. 注意危险度的概念,危险度用生产系统中事故发生的可能性和严重性给出.
基本要求: 检验应考人员对安全生产管理基本概念的掌握程度;对现代安全生产管理理论的熟悉程度;对我国安全生产工作现状和安全生产管理方针的熟悉程度.
1.安全生产管理的基本概念
1.2 安全生产 为了使生产过程在符合物质条件和工作秩序下进行,防止发生人身伤亡和财产损失等生产事故,消除或控制危险、有害因素,保障人身安全与健康、设备和设施免受损坏、环境免遭破坏的总称.
丰田模式-精益制造的14项管理原则

精益制造的14项管理原则两大支柱:准时化(连续生产)和自働化。
核心原则:单件流和杜绝浪费。
准时生产代表尽可能避免使用库存方式来缓解生产过程中可能出现的问题;单件流作业的理想时以顾客需求的速率或节拍时间,一次处理一件;使用较小的缓冲,代表如质量问题必须立刻浮现,强化自働化。
第一类原则长期理论1.管理决策以长期理念为基础,及时因此牺牲短期财务目标也在所不惜第二类原则正确的流程方能产生正确结果2.建立连续的作业流程以使问题浮现连续流:通过一系列的工序,在生产和运输产品时,尽可能地使工序连续化,即每个步骤只执行下一步骤所必需的工作。
核心是缩短从原材料到产生最终成品(或服务)的消耗时间,有助于促成最佳质量,最低成本,以及最短送货时间。
即使在那些无法实行单件流的环节,必须策略性地建立存货以作为缓冲时,会不断努力减少存货,以改善流程。
实际上,在正确且必要之处建立缓冲存货,将有助于企业整体流程改善。
容易出现的两个错误。
假流程:把设备搬迁在一起,创造出看似单件流作业的小组,然后再每个阶段进行大量生产,完全没有生产节拍时间的概念;发生问题后就退回原路,放弃单件流作业。
3.使用拉动生产方式以避免生产过剩“拉动”意指“准时生产”的理想状态:在顾客(包括生产流程中下一步骤的“内部顾客”)需要时,才提供其所需数量的东西。
当各流程作业相距太远,或是各作业步骤执行的周期时间差异太大,无法做到百分之百的单件流作业时,次佳选择看板制度。
预定进度表的推动式生产方式,他们非常注重实时性与准时性,也就是说,进度表并非只是你尽量遵照的原则,而是你必须竭尽全力达到的截至期限。
4.使工作负荷平均(生产均衡化)3M:Muda浪费,Muri员工或者设备的负荷过重,Mura不均衡为了保护供应商生产流程的平均化,以免需求突然增加而致生产作业吃紧,维持少量的产品存货往往是必要的。
实现多品种搭配生产,快速换模是前提。
服务业的均衡化:1.使顾客需求和均衡的进程表相配合,预约制;2.制定提供不同种类服务所花费的标准时间。
5S管理ppt课件
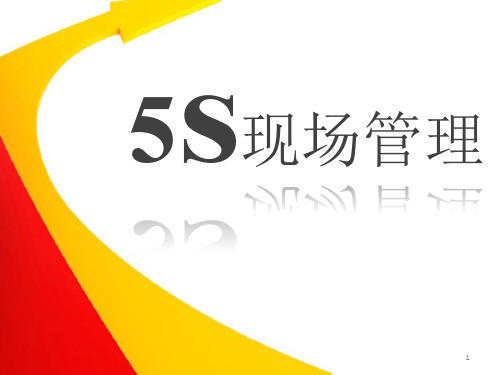
5S管理
如果企业是一棵大树,那么5S是埋在地下的根 根越大,树木也就越大;根越小,树木的生存越受到影响
28
精益求精 追求卓越
3 5S推进步骤 29
精益求精 追求卓越
不同时代的5S推进步骤
传统的5S推进步骤
01-成立组织 02-宣传培训 03-拟定计划 04-分段作业 05-巡检整改 06-稽核考评 07-综合分析
设备底下油污满地,难以清洁,影 响形象,并容易对产品造成污染
整改后
增加接油槽,消除污染源,美化现 场环境,不污染产品
18
精益求精 追求卓越
清洁
SEIKETSU
洁净环境 贯彻到底
定义
将前面的3S实施的做法制度化,规 范化,贯穿日常行为,持续实施
目的
通过制度化来维持成果,并显现” 异常”的所在
推行要领
整理
SEIRI
整顿
SEITON
清扫
SEISO
清洁
SEIKETSU
素养
SHITSUKE
5
精益求精 追求卓越
整理
SEIRI
要与不要 一留一弃
定义 目的
区分要用的和不要用的, 不要用的要清除掉。
节约空间
推行要领
全面检查作业场,包括看得到 的和看不到的
制定需要和不需要的判别基准 清除不需要物品 制定废弃物处理方法 每日自我检查
47
精益求精 追求卓越
原因/解决
04 责任不明
5S只是生产现场员工的事情 开展5S活动主要靠员工自发行为 什么事都要我来做,却一点权力
都不给 这液压车不归我管 责任区域不明确,不清晰
48
精益求精 追求卓越
- 1、下载文档前请自行甄别文档内容的完整性,平台不提供额外的编辑、内容补充、找答案等附加服务。
- 2、"仅部分预览"的文档,不可在线预览部分如存在完整性等问题,可反馈申请退款(可完整预览的文档不适用该条件!)。
- 3、如文档侵犯您的权益,请联系客服反馈,我们会尽快为您处理(人工客服工作时间:9:00-18:30)。
(管理制度)豐田式管理制度培訓課程豐田式管理制度一、前言本課程主要在探討豐田式管理系統,對JIT(及時化作業)的發展、JIT的先決條件,到且到JIT的實施架構等,作一介紹,包括看板系統、自動化、品管圈、少人化等。
最後再導入JIT-Ⅱ的觀念,使JIT像MRP-Ⅱ一樣推展到全公司。
二、目的自1970年代起,豐田式管理系統已在全球製造業掀起了一股風潮,尤其在面臨石油危機發生時,豐田汽車公司的營業成長率不但沒有受到石油危機因素下降,反而逆式成長升高了許多,令許多日本企業及美國企業大為驚訝,紛紛開始研究豐田式管理。
迄今實施JIT成功的廠商,不論中外,成功的實在不多,分析其原因均可歸納於欠缺整體性的規劃、管理階層與執行人員觀念的偏差、流程未落實與檢核未全面化與深入化等四項原因,期望課程的說明可使各級管理人員,瞭解豐田管理的技巧與精神所在,更運用適合各企業的管理方法延伸有效管理活動,來達到提升效率、降低成本的目標。
三、豐田生產管理系統(一)發展過程豐田生產系統是由豐田汽車公司前副社長----大野耐一先生(Ohno)歷經30年的時間首創並推廣的一種生產方式。
直到1973年第一次石油危機時,由於豐田汽車公司尚能在此種環境中獲致龐大的利潤,而引起日本工業界的注目。
此理論的基礎是集合了自動織機發明之王----豐田佐吉翁(豐田紡織廠)及豐田汽車創始者豐田喜一郎的思想(JustInTime),經過大野先生將之推行實施而成的學說。
(二)及時性生產JIT的定義豐田生產系統的基本理念是彈性地適應需求的變化,也就是在必要的時間,生產必要數量的產品。
豐田生產的最終目的是藉著成本的降低以創造利益,為了達此目標,就要排除浪費,如多餘的庫存、搬運‥等,以降低製造成本。
且藉著降庫存而使各種問題顯現,透過解決問題的改善活動及排除浪費的因素實施,而使製造成本降低,達到豐田管理的主要目標。
除了主要目標外,還有三個次要目標:1.能適應每月每日的需要變動,兼顧數量與種類的數量管理。
2.每項工程都能提供後面工程良好的品質保證。
3.為達成降低成本,利用人力資源時,也必須提高對人性的尊重目的。
(三)及時性生產JIT的主要架構生產線的一貫流程,與對市場的數量及種類的需求變化,是藉著「及時化」及「自動化」來完成。
1.及時化(Justintime):必要的物品,必要的時候,生產必要的份量。
2.自動化:能自動檢出製程上異常現象的裝備,且自動停止裝置的機械。
這二個可說是豐田生產的二大支柱。
同樣重要的概念還包括了下列兩項:1.適應需求變化而對作業員人數作理性調整的「少人化」。
2.透過作業員的提案改善活動的「品管圈」。
為了實現這4個概念,豐田公司採用下列幾個方法:1.使用「看板制度」以達成及時生產。
2.採行生產、平穩化的方法以適應需求變化。
3.縮短整備時間以減少生產前置期。
4.實施「操作標準化」以達成生產線的平衡。
5.注意機器設備之安排及運用「多能工」以期能保有增減作業人數之彈性。
6.藉著進行小組「改善活動」和,提案制度,以削減作業人數和提高作業員士氣。
7.藉「目視控制」制度以實現「自動化」概念「功能管理制度」以推進全公司的品質管理。
(四)排除浪費豐田生產方式可以稱為徹底排除浪費的方式。
製造現場通常視浪費為「增加成本負擔之要素」,因此若不重視浪費的問題,將會發生很多不必要的麻煩。
◆常見的浪費有下列七種形式:1.修改不良品的浪費。
2.生產過剩的浪費,生產過剩將導致增設機器設備、材料預支、多餘操作員金錢的損失、倉庫擴大等,百害而無一利。
3.加工的浪費,自己認為最好的方式或工作,其實包含了浪費。
4.搬運的浪費。
5.庫存的浪費。
6.動作的浪費:製造過程中,假如人手、設備、機器之操作而產生找不到物品,不良品等時,這些都是浪費的主因。
7.等待的浪費:機器還在加工,後面的人沒有工作,空手等待稱為等待的浪費。
◆改善浪費的順序:l.表格標準作業:正確記錄,對於日常作業要求必定按照事實寫出來。
2.發現浪費:根據步驟1的確實記錄與標準作業做比較找出問題點。
3.改善:針對浪費的地方找出解決之道(五)看板制度(Kanban)看板制度是對各製程的生產量進行控制的一種資訊系統。
這種生產管理,可稱為及時生產,但看板制度並不等於豐田生產體系。
1.看板種類(1)常用的看板有二種:取用看板及生產訂購看板,取用看板是記載後製程應該向前製程領取的零組件種類和數量。
生產訂購看板又被稱為生產看板,則記載前製程必須生產或訂購的零組件的種類和數量(2)供應商看板:向零件供應商提取零取件。
供應商看板則一律使用條碼。
(3)信號看板:用來載明壓鑄機,或是鍛造工程等批量生產。
2.看板功能(1)避免生產過剩的浪費。
(2)索取情報、生產指示情報。
(3)目視的管理、道具。
(4)改善的道具一看板太多反而沒有效果。
3.看板的使用技術(1)後工程的運貨人員,要將必要領取的數量與貨櫃,裝在叉式起重機或台車上,而搬到前工程的倉庫(零件倉庫)A。
(2)後工程的搬運工,於倉庫A領取零件之後,須拿開裝載貨架內的零件生產指示看板,放入已領取的地方。
(3)搬運人員,於自己所拿開的每一張生產指示看板後,要再掛上一張領取看板(4)在後工程作業一開始時,領取看板放置在收容領取看板的地方。
(5)前工程裏,在一定時間或生產一定數量的零件時,從看板領取處搜集而來的生產指示看板,須按倉庫拿走的順序,將這些生產指示看板放在其收容處才行。
(6)按照放在收容處的生產指示看板順序,來生產零件。
(7)進行加工零件時,這些零件與其看板,要成對的移動。
(8)在此工程中,每完成零件加工後,其零件的生產指示看板須放置倉庫,讓後工程的搬運工隨時領走。
4.達成看板的五個原則:(1)後製程祇有在必要的時候,向前製程領取必要數量的必要零組件。
(2)前製程應該只生產足夠的量,以補充被後製程提取的零件。
(3)不良品決不送往後製程。
(4)看板的使用數目應儘量減少。
(5)應該使用看板以適應小幅度的需求變動。
5.違反看板規則的影響(1)看板會發生狀況(2)易產生不良品(3)增加看板數量(4)庫存增加(5)不易發現問題點(6)不需改善以上的不良結果產生,對於JustInTime實施上的搬運無法運作,當然對生產現場之活性化沒有幫助。
(六)自動化豐田的自動化牽涉到品質管制,因為它使不良品無法通過生產線,並且它也有降低成本,具有因應彈性的生產及對人性更進一層的重要等等的效果。
2.達成自動化的具體技術:(1)發生異常的時候,停止生產線所使用的特殊設計法。
A.接觸式的安全系統B.整體式的安全系統C.行動步驟式的安全系統(2)使作業員習於「自動化」生產的技術A.防止盲目操作裝置:關閉型式、警示式B.防呆裝置(3)監視生產及當異常發生的時候,加以修正的手段。
A.視覺控制:標準操作表、看板、數字顯示板和貯存處及倉庫的顯示板。
3.自動化前必要的注意事項(1)定期更換機器的配件(2)定期檢查品質(3)定期補給機油(4)定期除去粉屑等等(5)防止異常停止再發生。
以上的維護作業,需靠各維修人員定期並加以注意維修,使有好的設備,才能製造優良的產品。
(七)及時生產「及時化」就是在必要的時間,把必要的東西(產品)送到需要的地方。
要實現及時化,必須完成下列三項準備:1.生產平準化2.作業標準化3.製程設計。
而看板的任務,則是作為情報傳遞的資訊系統。
◆生產平準化所謂生產平準化就是每一個單位製程時間,不管在數量或種類方面都處於平均化的狀態。
平準化生產的優缺點:1.優點:(1)零件的使用量會安定化。
(2)各工程以及承包企業的生產負荷量會安定化。
(3)可降低製品或工程進行間半製品的庫存量。
(4)依據小批量的生產與搬運,單位製品的平均生產佔用時間,可以縮減。
2.缺點:(1)由於各製品的種類大不相同,反而需要有事前的訓練,但實際上其作業的情形,常有延誤或零件裝置錯誤的現象。
(2)必須具備能適用各種製品作業的夾具和製造系統。
如:彈性製造系統(FMS)、群組技術(GT)。
(3)對於前工程作業,需要以小批量且頻繁的領料,而為要縮短庫存與佔用時間,有必要縮短調換機件的時間。
(4)當市場需要有大幅度變動時,就會有生產量難以配合的情形。
◆作業標準化使生產現場有提高生產效率的依據,有管理者管理自己的過程的基礎,便是標準作業。
標準作業由下列三個因素所成立。
1.週期時間:指一件物品必須以多少時間來裝配或製造公式為:一天必需數量=一個月的必需數量/實際工作日數週期時間=實際工作時間/一天的必需數量2.作業順序:是指作業人員在加工物品時,由材料至製品的次序變化過程。
3.在製品標準存量:乃指作業過程內最低需要量的半成品,也包括裝在機器上的在內。
◆製程設計1.把單功能作業員變成多功能作業員。
如:一人多機、工作輪調、U型生產線2.縮短特定製品的生產時間。
3.排除各製程間不必要的庫存。
4.多功能作業員觀念,減少所需的作業員人數。
5.參與工廠整體生產體系的籌劃,因而對自己的工作更為滿意。
6.每個作業員能從事團隊合作而彼此互相協助。
(八)品管圈(QCC)是指為了解決作業現場存在的問題,而由作業員組成的小團體,自發性並且繼續不斷地研讀品質管理的觀念和技術。
其最終目標是要增進作業員的責任感,提供作業員達成生產目標的方法,並使得作業員的技能得以提高成長。
其研究範圍包括品質管制、成本降低、設備保養、工廠安全、產業公害等。
三、JIT執行步驟(一)豐田生產方式的特徵1.和經營直接有關的公司IE活動:(1)生產計劃予以平準化(2)生產批量愈小愈佳(3)徹底做到必需的物料,在必需時才製造必要的數量2.更重視事實的科學態度(1)反覆的問5次「why」(2)使問題一目了然(3)使解決問題的目的明朗化(4)即使只有一個不良品,也要想出對策3.能切身實踐的工數減低活動(1)從作業的改善設備改善(2)工數與人數、省力化與省人化(3)所謂的檢查就是反省4.「經濟性」為一切的判斷基準(1)設備的稼動率,視生產需要量而定(2)有餘力就練習調換機件(3)生產現場才是主角(4)重視應變能力(二)JIT製造的先決條件1.使生產排程穩定2.使工廠集中3.製造中心的生產產能增加4.改善生產品質5.培養多能工6.透過預防保養,以減少設備故障(三)改革程序:1.意識改革一教育訓練2.現場改善之基礎:5S5S---整理、整頓、清掃、清潔、紀律3.JIT的縱面改革生產現狀分析---P、Q分析、標準流程、U型生產線、平準化、標準作業4.橫面推展,由一個部門,推展到全公司(四)JIT成功的七個步驟catinandleadership教育和領導力panyassessmentofJITelements實行JIT的評估3.Implementationplan執行JIT的計劃4.Pilotimplementation政策執行5.Smallgroupimprovementorgamization小團體的改善組織6.performanceevaluation績效評估panywidetransitionandinternalization小組擴大實施,不斷轉變和內部化四、JIT-ⅡJIT-Ⅱ?什麼是JIT-Ⅱ?它與JIT有什麼關係?我們可說JIT的目的是要降低成本,達到零庫存或減少庫存的生產方法。