浅析自由曲面数控加工中刀具路径规划
CNC机床加工中的刀具路径规划与优化技术研究

CNC机床加工中的刀具路径规划与优化技术研究CNC(Computer Numerical Control)机床是一种自动控制的精密加工设备,广泛应用于工业制造领域。
在CNC机床的加工过程中,刀具路径的规划和优化是一个关键的技术,它直接影响加工效率和加工质量。
本文将探讨CNC机床加工中的刀具路径规划与优化技术,并研究其在实际应用中的效果。
一、刀具路径规划的重要性刀具路径规划是将产品的CAD模型转化为机床加工程序的过程。
在刀具路径规划中,需要确定工件上每一段加工路径的轮廓、深度和切削方式等参数,以确保加工过程的准确性和高效性。
一个有效的刀具路径规划方案可以减少加工时间、降低能耗,并保证加工质量和表面光洁度。
二、刀具路径规划的方法1. 基于几何模型的方法基于几何模型的刀具路径规划方法是使用几何学原理和算法,根据零件的几何特征进行路径规划。
其中,最常用的方法包括直线路径规划、圆弧路径规划和多边形路径规划。
这些方法具有简单易用和计算效率高的特点,适用于简单形状的零件加工。
2. 基于优化算法的方法基于优化算法的刀具路径规划方法是利用数学优化理论,通过寻找最优解来确定刀具路径。
最常用的优化算法包括遗传算法、模拟退火算法和粒子群算法等。
这些算法能够在考虑多种约束条件的情况下,得到较优的刀具路径规划结果。
三、刀具路径优化的策略刀具路径优化是指对已生成的刀具路径进行进一步改进,以达到更好的加工效果。
以下是几种常用的刀具路径优化策略:1. 最短路径策略最短路径策略是通过优化刀具路径的长度,减少刀具在空转过程中的时间,从而提高加工效率。
该策略可以采用动态规划算法或启发式搜索算法来求解最短路径。
2. 避免退刀策略避免退刀策略是通过合理设置刀具路径,避免刀具在加工过程中频繁退回到机床原点,从而减少加工时间。
常用的方法包括使用切割联接路径和合理调整刀具的进给方向等。
3. 平滑路径策略平滑路径策略是通过优化刀具路径的转角和曲率,减少刀具在加工过程中的冲击和振动,从而提高加工质量和表面光洁度。
数控加工中基于自由曲面表面特性的刀具路径安排
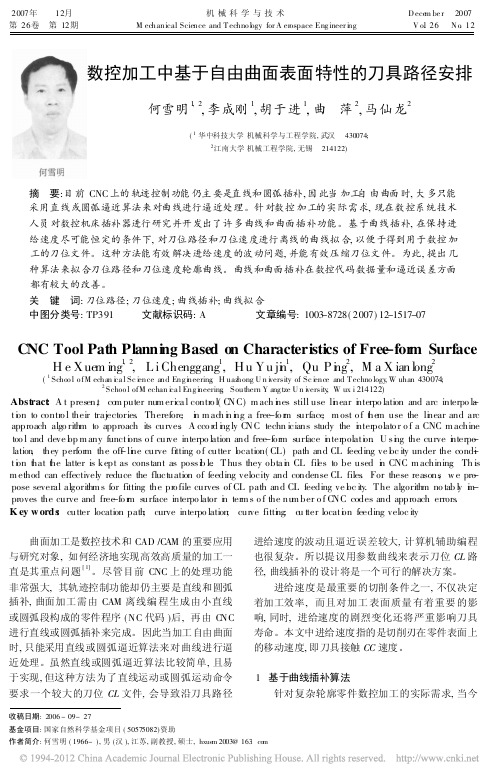
2007年第26卷12月第12期机械科学与技术M echanical Science and T echno l ogy for A erospace Eng ineer i ng D ece m be r V o.l 262007N o .12收稿日期:2006-09-27基金项目:国家自然科学基金项目(50575082)资助作者简介:何雪明(1966-),男(汉),江苏,副教授,硕士,hxue m 2003@163.co m数控加工中基于自由曲面表面特性的刀具路径安排何雪明1,2,李成刚1,胡于进1,曲 萍2,马仙龙2(1华中科技大学机械科学与工程学院,武汉 430074;2江南大学机械工程学院,无锡 214122)摘 要:目前CNC 上的轨迹控制功能仍主要是直线和圆弧插补,因此当加工自由曲面时,大多只能采用直线或圆弧逼近算法来对曲线进行逼近处理。
针对数控加工的实际需求,现在数控系统技术人员对数控机床插补器进行研究并开发出了许多曲线和曲面插补功能。
基于曲线插补,在保持进给速度尽可能恒定的条件下,对刀位路径和刀位速度进行离线的曲线拟合,以便于得到用于数控加工的刀位文件。
这种方法能有效解决进给速度的波动问题,并能有效压缩刀位文件。
为此,提出几种算法来拟合刀位路径和刀位速度轮廓曲线。
曲线和曲面插补在数控代码数据量和逼近误差方面都有较大的改善。
关 键 词:刀位路径;刀位速度;曲线插补;曲线拟合中图分类号:TP391 文献标识码:A 文章编号:1003-8728(2007)12-1517-07CNC Tool Path Planni ng Base d on Characteristics of Free -for m SurfaceH e X ue m i ng 1,2,L i Chenggang 1,H u Y u ji n 1,Qu P i n g 2,M a X ian l ong2(1Schoo l o fM echan i ca l Sc i ence and Eng i neering ,H uaz hong U n i versity of Sc i ence and T echno logy ,W uhan 430074;2Schoo l ofM echan i ca l Eng i neering ,Southern Y ang tze U n i versity ,W ux i 214122)Abst ract :A t presen,t co m puter num erica l contr o l(C NC)m ach i n es still use li n ear i n terpo lation and arc interpo la -ti o n to contr o l their trajectories .Therefore ,i n m ac h i n i n g a free -fo r m surface ,m ost o f t h e m use the li n ear and arcapproach algo rithm to approach its curves .A cco r d i n g ly C NC techn icians study the i n ter polato r o f a CNC m achine too l and deve l o p m any functi o ns o f cur ve interpo lation and free -for m surface i n ter polati o n .U si n g the curve i n terpo -lation ,they perfor m the of-f li n e curve fitting o f cutter l o cation(CL)path and CL feeding ve l o c ity under the cond-i ti o n t h at t h e latter is kept as constant as possi b le .Thus they obta i n CL fil e s to be used i n CNC m achining .Th is m ethod can effectively reduce the fluctuation of feeding velocity and condense CL files .For these reasons ,w e pro -pose several algorithm s for fitting the pr o file curves of CL path and CL feeding ve l o c ity .The algorithm no tab l y i m -proves the curve and free -fo r m surface interpo lator i n ter m s o f the nu m ber o f C NC codes and approach errors .K ey w ords :cutter location path ;curve interpo lation ;cur ve fitti n g ;c u tter locati o n feeding veloc ity 曲面加工是数控技术和CAD /C AM 的重要应用与研究对象,如何经济地实现高效高质量的加工一直是其重点问题[1]。
数控加工刀具路径拟定

2. 3数控加工刀具路径拟定CNC加工的刀具路径指,加工过程中,刀具刀位点相对于工件进给运动的轨迹和方向。
刀具路径一般包括:从起始点快速接近工件加工部位,然后以工进速度加工工件结构,完成加工任务后,快速离开工件,回到某一设定的终点。
可归纳为两种典型的运动:点到点的快速定位运动一一空行程;工作进给速度的切削加工运动一一切削行程。
确定刀具走刀路线的原则主要有以下几点:⑴规划安全的刀具路径,保证刀具切削加工的正常进行。
⑵规划适当的刀具路径,保证加工零件满足加工质量要求。
⑶规划最短的刀具路径,减少走刀的时间,提高加工效益。
2. 3. 1规划安全的刀具路径在数控加工拟定刀具路径时,把安全考虑放在首要地位更切BI荷坏叨刨电域实际。
规划刀具路时,最值得注意的安全问题就是刀具在快速的点定位过程中与障碍物的碰撞。
为了节省时间,刀具加工前接近工件加工部位,完成加工任务后,快速离开工件,常用快速—' ----- ----------- ~点定位路线。
快速点定位时,刀具以最快的设定速图2-3-1车削加工X、Z向安全间隙设计度移动,一旦发生碰撞后果不堪设想。
1 .快速的点定位路线起点、终点的安全设定工艺编程时,对刀具快速接近工件加工部位路线的终点和刀具快速离开工件路线的起点的位置应精心设计,应保证刀具在该点与工件的轮廓应有足够的安全间隙,避免刀具与工件的碰撞。
在拟定刀具快速趋近工件的定位路径时,趋向点与工件实体表面的安全间隙大小应有谨慎的考虑。
如图2-3-1,刀具相对工件在Z向或X向的趋近点的安全间隙设置多少为宜呢?间隙量小可缩短加工时间,但间隙量太小对操作工来说却是不太安全和方便,容易带来潜在的撞刀危险。
对间隙量大小设定时,应考虑到Z0的加工面是否已经加工到位,若没有加工,还应考虑可能的最大的毛坯余量。
若程序控制是批量生产,还应考虑更换新工件后Z向尺寸带来的新变化,以及操作员是否有足够的经验。
在铳削工艺编程,刀具从 X 、Y 向快速趋于工件轮廓时的情况,与Z 向趋近相比较,同 样应精心设计安全间隙,但情况又有所不同,因为刀具X 、Y 向刀位点在圆心,始终与刀具 切削工件的点相差一个半径, 刀具快速趋近的同时, 又需建立半径补偿, 因此设计刀具趋近工件点与工件的安全间隙时,除了要考虑毛坯余量的大小,又应考虑刀具半径值的大小。
数控机床的刀具路径规划与动态优化

数控机床的刀具路径规划与动态优化数控机床是一种以数字信号为基础的自动化机械设备,广泛应用于各个制造行业。
在数控机床的加工过程中,刀具路径规划与动态优化是非常重要的环节。
本文将介绍数控机床的刀具路径规划和动态优化的原理与应用。
一、刀具路径规划的原理与方法刀具路径规划是指根据零件的几何形状、加工工艺和机床的运动特性等参数,在数控机床上规划出合理的刀具运动路径。
刀具路径规划主要包括以下几个方面的内容:1.零件轮廓重构在数控机床的刀具路径规划中,首先需要对零件的几何轮廓进行重构。
这通常通过数字化扫描、CAD软件建模等方式完成。
重构后的零件轮廓数据可以用于后续的路径规划和优化。
2.切削力分析在进行刀具路径规划时,需要考虑零件材料的性质和机床切削力的影响。
通过对切削力的分析,可以调整刀具路径和切削参数,以确保加工过程的稳定性和效率。
3.路径生成路径生成是刀具路径规划的核心环节。
常用的路径生成方法包括直线插补、圆弧插补、螺旋插补等。
在路径生成的过程中,需要考虑刀具的运动轨迹、切削力的方向和大小等因素,以实现高精度的加工效果。
4.切削参数优化切削参数优化是指通过调整切削速度、进给速度、切削深度等参数,以求得刀具路径规划的最佳效果。
切削参数的优化可以提高加工质量、降低切削力和能耗等。
二、刀具路径规划的应用与挑战刀具路径规划在数控机床加工过程中具有重要的应用价值,可以有效提高加工效率和产品质量。
以下是几个刀具路径规划的应用实例:1.零件加工在数控机床的零件加工中,刀具路径规划可以帮助确定切削轨迹、减少加工误差、提高加工速度等。
通过合理地规划刀具路径,可以实现高精度的零件加工。
2.刀具磨损监测刀具磨损是数控机床加工中常见的问题,磨损过度会导致加工质量下降和刀具寿命缩短。
刀具路径规划可以结合刀具磨损监测系统,实时监测刀具磨损情况,并根据监测结果进行动态优化。
刀具路径规划在实际应用中也面临一些挑战。
首先,不同零件的几何形状和加工工艺要求千差万别,如何选择合适的路径生成方法成为一个难点。
数控加工刀位轨迹生成的算法分析
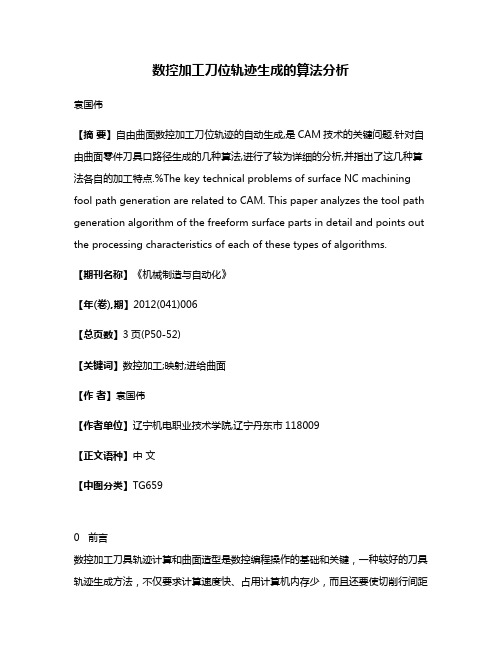
数控加工刀位轨迹生成的算法分析袁国伟【摘要】自由曲面数控加工刀位轨迹的自动生成,是CAM技术的关键问题.针对自由曲面零件刀具口路径生成的几种算法,进行了较为详细的分析,并指出了这几种算法各自的加工特点.%The key technical problems of surface NC machining fool path generation are related to CAM. This paper analyzes the tool path generation algorithm of the freeform surface parts in detail and points out the processing characteristics of each of these types of algorithms.【期刊名称】《机械制造与自动化》【年(卷),期】2012(041)006【总页数】3页(P50-52)【关键词】数控加工;映射;进给曲面【作者】袁国伟【作者单位】辽宁机电职业技术学院,辽宁丹东市118009【正文语种】中文【中图分类】TG6590 前言数控加工刀具轨迹计算和曲面造型是数控编程操作的基础和关键,一种较好的刀具轨迹生成方法,不仅要求计算速度快、占用计算机内存少,而且还要使切削行间距分布均匀、加工误差小、走刀步长分布合理、加工效率高等。
随着CAD/CAM技术的快速发展,出现了多种自由曲面造型理论和数控加工刀具轨迹的算法,其中比较常用的方法有:等参数法、笛卡儿法和APT法。
本文着重谈这三种加工方法的算法分析。
基于刀触点的刀具路径生成方法首先在被加工曲面上采样一系列刀触点,然后再将刀触点转化为刀位点,进而生成刀具路径。
如图1所示,路径规划主要有三种娄型:参数线、导向平面、驱动曲面,分别对应于三种刀具路径生成方法:等参数法、笛卡儿法和APT法。
图1 基于刀触点的刀具路径生成1 等参数法图2等参数法采用环底刀加工凸曲面,其基本参数见表1。
数控加工中的边界特征提取与刀具轨迹规划

数控加工中的边界特征提取与刀具轨迹规划随着科技的进步和制造业的发展,数控加工已经成为现代工业中不可或缺的一部分。
在数控加工中,边界特征提取和刀具轨迹规划是两个重要的环节,对于加工质量和效率具有重要影响。
边界特征提取是指在数控加工中,从设计模型中提取出需要进行加工的特征边界。
这些特征边界可以是直线、曲线、圆弧等形状,也可以是复杂的曲面。
边界特征提取的目的是将设计模型转化为数控机床可以理解和加工的形式。
在传统的加工中,工人需要根据设计图纸进行手工测量和标记,然后根据标记进行加工。
而在数控加工中,边界特征提取可以通过计算机软件自动完成,大大提高了加工的效率。
在边界特征提取的过程中,常用的方法包括几何特征提取和曲线拟合。
几何特征提取是通过计算机算法,从设计模型中提取出直线、曲线等基本几何元素。
曲线拟合则是将设计模型中的复杂曲线拟合成一系列简单的曲线段。
这些方法可以根据设计模型的不同特点进行选择和组合,以提取出最准确的边界特征。
在边界特征提取完成后,接下来就是刀具轨迹规划。
刀具轨迹规划是指确定刀具在加工过程中的运动轨迹,以保证加工的准确性和效率。
在数控加工中,刀具轨迹规划需要考虑多个因素,包括切削力、切削速度、切削深度等。
同时,还需要考虑加工过程中的约束条件,如刀具与工件的碰撞避免和刀具路径的平滑性。
刀具轨迹规划的方法有很多种,常用的包括直线插补、圆弧插补和曲线插补等。
直线插补是指刀具沿直线路径进行加工,适用于直线边界特征。
圆弧插补则是刀具沿圆弧路径进行加工,适用于圆弧边界特征。
曲线插补是将复杂的曲线边界特征转化为一系列简单的直线和圆弧插补,以实现加工。
这些方法可以根据加工要求和机床的性能进行选择和优化,以达到最佳的加工效果。
除了边界特征提取和刀具轨迹规划,数控加工中还有其他一些重要的环节。
例如,切削参数的选择和刀具路径的优化。
切削参数的选择包括切削速度、进给速度和切削深度等参数的确定。
刀具路径的优化则是通过计算机算法,对刀具路径进行优化,以减少加工时间和提高加工质量。
刀具路径规划在CNC机床加工中的应用
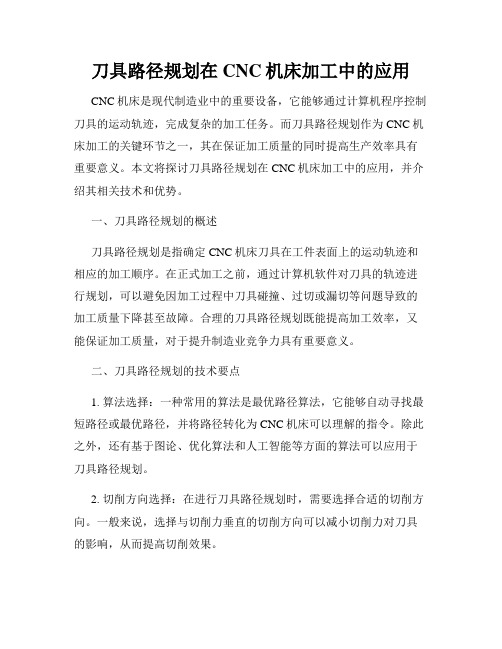
刀具路径规划在CNC机床加工中的应用CNC机床是现代制造业中的重要设备,它能够通过计算机程序控制刀具的运动轨迹,完成复杂的加工任务。
而刀具路径规划作为CNC机床加工的关键环节之一,其在保证加工质量的同时提高生产效率具有重要意义。
本文将探讨刀具路径规划在CNC机床加工中的应用,并介绍其相关技术和优势。
一、刀具路径规划的概述刀具路径规划是指确定CNC机床刀具在工件表面上的运动轨迹和相应的加工顺序。
在正式加工之前,通过计算机软件对刀具的轨迹进行规划,可以避免因加工过程中刀具碰撞、过切或漏切等问题导致的加工质量下降甚至故障。
合理的刀具路径规划既能提高加工效率,又能保证加工质量,对于提升制造业竞争力具有重要意义。
二、刀具路径规划的技术要点1. 算法选择:一种常用的算法是最优路径算法,它能够自动寻找最短路径或最优路径,并将路径转化为CNC机床可以理解的指令。
除此之外,还有基于图论、优化算法和人工智能等方面的算法可以应用于刀具路径规划。
2. 切削方向选择:在进行刀具路径规划时,需要选择合适的切削方向。
一般来说,选择与切削力垂直的切削方向可以减小切削力对刀具的影响,从而提高切削效果。
3. 切削参数优化:切削参数优化是刀具路径规划的重要环节,通过合理设定切削速度、进给速度和进给深度等参数,可以最大程度地提高加工效率和加工质量。
4. 轨迹平滑处理:在刀具路径规划中,为了避免刀具在加工过程中出现不连续或抖动的情况,需要对刀具路径进行平滑处理。
常用的方法是施加加速、减速、插值等操作,使得刀具运动更加平稳。
三、刀具路径规划的应用案例1. 铣削加工:在CNC铣床中,刀具路径规划可以对工件进行平面铣削、轮廓铣削等加工操作。
通过合理的路径规划,可以减少切削次数,提高加工效率,并保证加工表面的质量。
2. 钻孔加工:对于多孔工件的加工,刀具路径规划可以确定钻孔的顺序和深度,避免钻孔过程中产生不必要的干涉和误差,提高钻孔的准确性和一致性。
等残留高度算法应用于自由曲面五轴刀路规划研究

等残留高度算法应用于自由曲面五轴刀路规划研究肖善华【摘要】针对五轴零件加工过程中自由曲面生成的刀具路径代码冗余,加工效率较低和加工表面质量不高等问题,对自由曲面加工中的常用刀具路径算法进行了分类,提出了等残留高度相关算法模型.计算了等残留高度点及在自由曲面的投影点,并对角度值β进行了迭代计算,对自由曲面加工中的五轴刀轴倾角λq值进行了推导计算;以螺旋桨叶片复杂自由曲面模型为刀路加工载体,生成了五轴刀路轨迹,与Mastercam软件的高速动态铣削(旋转五轴)模块功能生成五轴一般刀路进行了对比分析.研究结果表明:等残留高度算法能缩短五轴自由曲面的刀路长度,提高加工效率及零件表面质量.【期刊名称】《机电工程》【年(卷),期】2019(036)007【总页数】5页(P722-726)【关键词】等残留高度模型;刀轴倾角;Mastercam;螺旋桨叶片【作者】肖善华【作者单位】宜宾职业技术学院现代制造工程系,四川宜宾644003【正文语种】中文【中图分类】TH1640 引言复杂的自由曲面路径生成算法,目前主要有等截面算法、等参数线算法、等残留高度算法。
前两类方法刀具轨迹计算比较简单,而等残留高度算法以其加工时的刀具路径轨迹短、加工时效率更高、残余高度均匀并且一致、零件加工表面质量最高而得到广泛的应用。
该算法是美国的SURESH和YANG[1]提出的一种数控加工刀具路径优化方法,针对等残留高度法,国内外学者进行了深入研究。
文献[2]提出了改进的等残留高度轨迹规划的数学建模,从而使刀具轨迹的计算更加简单高效;文献[3]提出了改进的等残留高度法生成五轴的NC刀位轨迹,刀具轨迹沿特定的方向走刀时,加工时间会比刀轨沿其他方向时更短;文献[4]研究了网格曲面等残留高度路径规划算法,曲面分割加工中的一种耦合效应,能减少曲面分割的误差并提高曲面分割的加工效率;文献[5]研究了三角网格表面的刀轨长度较长、加工表面残留高度不均匀的问题,提出了一种改进截平面法的等残留高度刀轨生成算法。
- 1、下载文档前请自行甄别文档内容的完整性,平台不提供额外的编辑、内容补充、找答案等附加服务。
- 2、"仅部分预览"的文档,不可在线预览部分如存在完整性等问题,可反馈申请退款(可完整预览的文档不适用该条件!)。
- 3、如文档侵犯您的权益,请联系客服反馈,我们会尽快为您处理(人工客服工作时间:9:00-18:30)。
由刀位点和刀位点所表示的刀具路径的形状特征设定为
n+1;节点矢量 T 可以由近似弧长参数化方法得到。
控制顶点优化的目的,是使刀位点与拟合曲线之间的偏
差最小。各刀位点与拟合曲线之间的偏差,可以用各刀位点到
曲线上相应的点的距离之和来表示:δj = Pj - P (uj ) 。 由于 k 阶 NURBS 曲线的每个控制顶点的调整,都会影响
刀具所对应的段曲线的变化,因此对各控制顶点位置的优化,
就涉及到所有刀位点所对应的偏差。以所有刀位点所对应的
偏差的平方之和作为目标函数,则优化问题的目标函数可以
表示为
m
Σ f (C0 ,C1 ,…,Cn ) =
2
Pj - P (uj )
j=0
m
n
2
Σ Σ =
Pj - Ni,k (uj )·Ci
j=0
i=0
笛卡尔坐标空间规划方法的步骤是:先在笛卡尔坐标系 的 XY 平面中规划刀具的路径,一般是 XY 平面中的一列平行 直线;然后将这些直线反投影到曲面上,得到曲面上的刀具路 径。这种方法的缺点是:要求在整个零件表面搜索可能与刀具 相干涉的点,计算量较大。 1.3 参数空间路径规划方法
参数空间路径规划方法有两种:等参数步长法和参数筛 选法。
(1)等参数步长法:沿着 u 参数线或 v 参数线,以等参数 步长计算刀具路径点位信息,为了满足加工精度,步长通常取 的很小。这种方法由于没有用曲面的曲率来估计步长,因此没 有考虑曲面的局部平坦性在平坦区域只需较少的点位信息, 所得到的点位信息较多;优点是计算比较简单。
(2)参数筛选法。首先按预设的等参数步长离散 u 或 v 参 数线,计算出零件表面对应的点列和每一点处的法矢,然后按 曲面的曲率和加工精度,从点列中筛选出点位信息。这种方法 中运用了过滤算法和细化算法,过滤算法用于依据曲率变化 合并一些间隔,以减少数据量;细化算法则依加工误差的要 求,在一些间隔较大的区间里添加路径点。这种方法的优点是 克服了等参数步长法的缺点,缺点是过滤算法和细化算法都 非常费时。
由于通过直线插补大量刀位点来进行数控加工,存在很
多缺陷,利用 NURBS 刀具路径进行数控加工,已受到更加广
泛的重视。为了将有序刀位点表示的刀具路径,转化为
NURBS 形式表示的刀具路径,必须对刀位点数据进行 NURBS
曲线的拟合处理。由于刀位点数据特殊性的存在,特别是刀位
点数据量大的特点,使前面介绍的数据拟合方法在应用于刀
中图分类号:TH164
文献标识码:A
文章编号:1672- 545X(2009)07- 0057- 03
计算机数控技术集传统的机械制造、计算机、自动控制、 电气传动、传感检测和信息处理等技术于一体,是现代制造技 术的基础。它的诞生和使用,给机械制造的生产方式、产品结 构、产业结构等方面带来深刻的变革。如今,数控技术作为制 造业实现自动化、柔性化、集成化生产的基础,已成为先进制 造技术的重要组成部分,是发展现代集成制造和智能制造的 主体技术,是当今各种先进制造系统的基础和前提条件。
随着制造业的迅速发展,越来越多的复杂曲面被应用于 航空、汽车、造船及电子产品等行业之中,如空气动力学的飞 机轮廓、汽车车身、涡轮机桨叶和手机外壳等。如何提高这些 特殊产品加工的效率和精确度,已成为亟待解决的问题,越来 越多的人投入到这项研究中[2~3]。刀具路径规划是复杂曲面加 工过程中需要解决的关键技术之一,刀具路径规划是否合理, 直接关系到能否在误差允许范围内获得最大的加工效率。本 课题的主要目的,是对自由曲面数控加工过程中的刀具路径 进行合理规划,力争做到保证被加工曲面表面质量的同时,提 高加工效率。
由于 NURBS 刀具路径,无法从以 NURBS 表示的自由曲 线曲面零件轮廓中直接得到,往往需要首先根据零件的几何 模型和加工工艺,生成以刀位点表示的刀具路径,再将此有序 刀位点表示的刀具路径,转化为 NURBS 刀具路径。因此,如何 以更加精确简洁的方式,将刀位点数据表示成刀具路径,是实 现对自由曲线曲面零件用 NURBS 刀具路径进行高速、高精度 加工的关键。
位点的 NURBS 曲线拟合时,往往不能满足 NURBS 刀具路径生成的需求。
2.4 优化算法
设有 m+1 个有序刀位点 Pj ( j = 0,1,…,n),对这些刀位点
进行 NURBS 曲线拟合,就是要构造一条 k 阶 NURBS 曲面
n
Σ r(u)= Ri,k (u)Ci (其中 Ri,k (u)为有理 B 样条基函数), Ci ( i = i=0
2 刀具路径规划技术分析
在常规的数控加工中,自由曲面零件的切削刀具路径,是 由许多较小的直线段组成的,这种刀具路径我们常称之为线 性插补刀具路径,也称直线插补刀具路径。线性插补刀具路径 虽然具有表达简单、计算快捷等优点,但也有很多缺点。随着
收稿日期:2009- 04- 20 作者简介:王 博(1981-),男,山东泰安人,教师,主攻方向:数控加工。
在基于 ATP 的路径规划方法中,刀具的移动路线由一系 列称之为导动面 DS(drive surface)的曲面来定义。其主要思想 是在加工过程中,通过控制刀具的运动,使之同时与导动面和 零件面保持接触,使刀具按照正确的运动轨迹运动。这种方法
的缺点是:为了控制加工误差,每一刀步中均要进行反复的迭 代运算,以确定正确的刀位,迭代计算费时且在不规则的曲面 情况下不能保证迭代收敛;其优点是:刀具的路径完全由零件 面和导动面决定,因此可以沿着任何方向来规划刀具的路径, 同时可以保证不产生干涉现象。 1.2 笛卡尔坐标空间规划方法
对于插值方法,拟合的目的是要求构造曲线 r(u)严格通过 刀位点 P,此时新构造的曲线 r(u)必须满足条件:
r(uj ) = Pj ( j = 0,1,…,m) 而对于逼近方法,拟合的目的则是要求构造曲线 r(u)在规
定的精度内逼近各刀位点,此时新构造的曲线 r(u)必须满足条
件:
max dist Pj ,r (uj ) ≤ε
曲线拟合的目标,就是通过调整控制顶点的位置使此偏
差达到最小。每个控制顶点由其笛卡儿坐标系中的三个坐标
分量来表示。由前面的分析可知,当控制顶点数目较多时,此
优化问题就成为一个设计变量较多的非线性优化问题,不宜
58
采用解析法求解。通过对目标函数的分析,本研究采用修正 Newton 方法进行迭代求解。修正 Newton 方法将传统 Newton 迭代方法中的迭代步长设为一个可变因子,实现了每一次迭 代都能够在 Newton 方向上进行一维寻优,避免了迭代后目标 函数值上升的现象,从而保持了优化算法的收敛性。其中各分 量为目标函数对坐标轴的求偏导,经过对曲线求偏导并化简 得到。
修正 Newton 方法的迭代计算,需要对初始控制顶点进行 设置,在对刀位点数据进行 NURBS 拟合中,理论上初始控制 顶点可以设定为比刀位点数据少的任意值,控制顶点位置的 迭代初始值,也可以任意指定,但任意给定的控制顶点迭代初 始值,往往会使迭代计算次数太多,降低计算效率,甚至出现 迭代计算不收敛的情况。本优化方法针对刀位点数据分布的 特点,设定初始控制顶点数目为 n=round((1/10~1/2)m),将最接 近的刀位点设为初始控制顶点。这样设定初始控制顶点,避免 了任意初始顶点的不稳定性,减少迭代计算次数,在通过初始 控制顶点条件完成节点矢量的计算后,就可以利用优化方法 寻找最优的控制顶点。
在使用 NURBS 刀具路径进行数控加工时的 NC 程序指 令中,只有三类定义 NURBS 刀具路径的数值,没有必要使用 大量的微小直线段的指令。NURBS 刀具路径由 CNC 系统的 NURBS 插补器来实现内部的曲线运算,对于曲线曲面的加 工,可以得到光滑的加工形状,从根本上解决了直线插补所带 来的问题。 2.2 NURBS 曲线拟合
0,1,…,n)为曲线的控制多边形顶点),使之到各刀位点的偏差
满足一定的精度要求。
根据上节对各控制顶点权重初始值设置的描述,曲线拟
合初期可以将各控制顶点权重均设为 1,这时,Ri,k (u)=Ni,k (u)。 为了使生成的 NURBS 曲线至少二阶连续,以获得具有一定光
顺性的曲线,设定曲线的阶数 k=4。初始控制顶点数目,可以
式中,Dist 表示刀位点至曲线的距离函数;ε 为规定的拟
合精度。
由上述两个拟合的条件式可以看出,无论是插值还是逼
近,要计算满足条件的 NURBS 曲线的数据,拟合条件中与每
个刀位点相对应的 uj 巧参数的选取方法、拟合误差的计算和 采用的拟合方法等技术,均是能否正确计算拟合的关键。
2.3 NURBS 曲线拟合及刀具路径生成
在自由曲面加工的刀具路径规划中,进行 NURBS 曲线拟 合的主要任务,是拟合已知的刀位点。将大量有序的刀位点, 直接拟合成 NURBS 曲线刀具路径,便可以直接传输给数控系 统进行 NURBS 刀具路径的数控加工。在自由曲面的加工中, 为保持刀具路径和被加工曲面的二阶几何(G2)连续性,常使用 三次(阶数 k=4) NURBS 曲线。这样,对于一个给定数目的刀位 点序列 P j ( j= 0,1,2,…m),要求构造出一条合适的 NURBS 曲 线 r(u)来拟合刀位点,主要任务是通过己知的刀位点,来反求 曲线控制顶点、权重因子和节点矢量,这个过程称之为拟合。 拟合分为插值和逼近。
1 刀具路径规划技术的发展概况
自由曲面数控加工中,刀具路径的规划问题较为复杂。近 年来,业界学者对此展开了深入的研究,探讨了多种具有自身 的优点和适用场合的方法。这些方法,为优质高效地完成自由 曲面的数控加工奠定了理论基础和技术基础。传统的数控加工 中的刀具路径规划,是在数控编程中完成的,当前数控编程广 泛采用计算机辅助自动编程方式。在自动编程系统中,针对复 杂曲面零件,刀具路径的规划方法主要有基于 ATP 的路径规 划方法、笛卡尔坐标空间规划方法、参数空间规划方法、多面体 法、等参数线加工方法、截面线加工方法、等残留高度法等。 1.1 基于 ATP 的路径规划方法