压力—位移曲线在压装工艺中的应用研究
压力-位移曲线在压装工艺中的应用研究
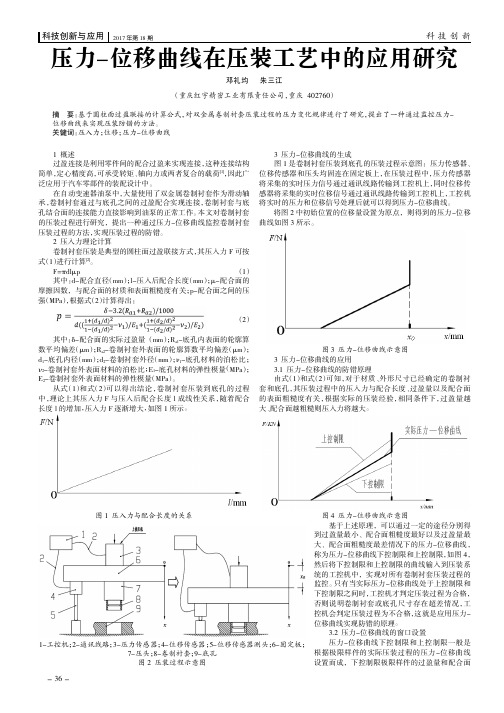
作为一种同时拥有电力架空相线和光通信双重能效的新型和特种
光纤复合架空相线(OPPC)担负着变电站无人值班和全局信息
光缆,拥有很大的技术优势和应用前景。传统的光纤通信以光导纤 网通道传输的重要任务,是电力网重要的组成部分。在 OPPC 技术
维为传输媒介,光波为载波的光纤信道,具有耗损低、频带宽、高速 标准应用实施过程中,为了更好的进行科学化管理,系统规范地将
长度 l 的增加,压入力 F 逐渐增大,如图 1 所示。
大、配合面越粗糙则压入力将越大。
图 1 压入力与配合长度的关系
图 4 压力-位移曲线示意图
基于上述原理,可以通过一定的途径分别得
到过盈量最小、配合面粗糙度最好以及过盈量最
大、配合面粗糙度最差情况下的压力-位移曲线,
称为压力-位移曲线下控制限和上控制限,如图 4,
3.1 压力-位移曲线的防错原理
E2-卷制衬套外表面材料的弹性模量(MPa)。
由式(1)和式(2)可知,对于材质、外形尺寸已经 确定的卷制衬
从式(1)和式(2)可以得出结论,卷制衬套压装到底孔的过程 套和底孔,其压装过程中的压入力与配合长度、过盈量以及配合面
中,理论上其压入力 F 与压入后配合长度 l 成线性关系,随着配合 的表面粗糙度有关,根据实际的压装经验,相同条件下,过盈量越
OPPC 实际应用中的管理方案与效益分析
徐巍峰 刘缙军 朱利锋 凌 军 刘亚民 陈新安 闫小芳 (国网浙江青田县供电公司,浙江 青田 323900)
摘 要:OPPC 在传统相线中嵌入光纤单元,是电力通信中的一种新型光缆。与 OPGW 和 ADSS 相比,OPPC 具有电能传输和光信 号传输完美融合,无附加额外载荷,良好的腐蚀性,热稳定性和高使用寿命等优点。国网浙江省电力公司丽水供电公司结合输电 线路改造,对 10kV 输电线路中 OPPC 的应用开展相关研究并在实际中进行应用,总结了具体管理方案,并对 OPPC 在低电压等 级网络中的相关效益进行分析。 关键词:OPPC;智能电网;管理方案
压装过程最终位置控制线的确定方法
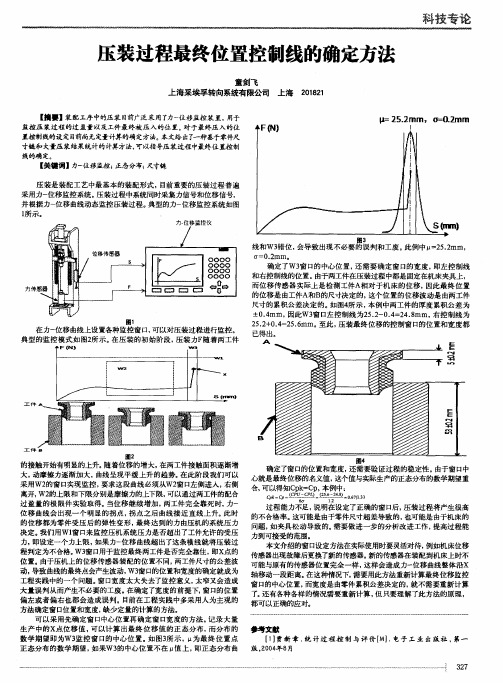
.
圈4
6 7 ( 1 3 3
过程能 力不足 , 说 明在 设定 了正确 的窗 1 : 1 后, 压 装过程 将产生很 高 的不合格 率。 这可能是 由于零 件尺寸超 差 导致 的, 也可能是 由于机 床 的 问题 , 如 夹具 松动导 致的 。 需要 做进 一步 的分 析改进 工作 , 提 高过程 能
w l
确定 了W3 窗口 的 中心 位 置, 还 需要 确定 窗 口的 宽度 , 即左 控制 线 和右控制 线的位置 。 由于两工件在压装 过程 中都是 固定在机 床夹 具上, 而位 移传 感器 实际上 是检 测工件At t H 对于 机床 的位 移 , 因此 最终 位 置 的位移 是 由工件A和B 的尺寸决定 的 , 这个位 置的位 移波动 是 由两 工件 尺寸 的累积 公差决 定 的。 如图4 所示 , 本 例中两 工件 的厚度 累积 公差 为 士0 . 4 am, r 因此 W3 窗 口左 控制 线为2 5 . 2 - 0 . 4 = 2 4 . 8 am, r 右 控制 线为 2 5 . 2 + 0 . 4 = 2 5 . 6 am。 r 至此 , 压装最 终位 移 的控制窗 H的位 置和 宽度都
离开 , W2 的上 限和下限 分别是摩擦 力的上下限 , 可以通 过两工件 的配合 过 盈量 的极 限件 实验取 得。 当位移 继 续增加 , 两工件 完全靠 死时 , 力一 位 移 曲线会 出现一 个 明显 的拐点 , 拐 点之 后 曲线接 近 直线 上升 。 此 时 的位移 都为零 件受压 后 的弹性 变形 , 最终 达到 的力 由压机 的系统 压力 决定 。 我们用 W1 窗口来监 控 压机系统 压 力是否超 出了工件允许 的受压 力, 即设 定一 个力上限 , 如果 力一 位移 曲线超 出了这条横 线就 将压 装过 程判 定为不合格 。 W3 窗口 用于监 控最终两 工件是否完 全靠住 , 即x 点的 位 置。 由于压机上 的位移 传感器装 配的位 置不同, 两 工件尺寸 的公差波 动, 导 致 曲线的最终点会产生波动 , W3 窗 口的位置和宽 度的确定就 成为 工程 实践 中的一 个 问题 。 窗口 宽 度太大 失去了监 控意 义, 太窄 又会 造成
轮对压装过程中几个关键工艺参数的分析

轮对压装过程中几个关键工艺参数的分析摘要:铁路客车轮对承受着车辆的全部载荷,并在负重的条件下沿轨道作高速运转,轮对压装作为重要工序之一,其参数直接影响着行车安全。
本文分析了轮对压装的工艺过程中的几个关键参数,阐述了压装过程中易产生的问题,分析了产生这些问题的原因。
关键词:轮对;工艺;参数轮对是铁路客车最主要的零部件之一,而轮对组装的质量是保证车辆在高速运行中安全的至关重要的环节,车轴、车轮经过几道工序的加工,最后冷压组装,轮轴的加工质量好坏直接影响到轮轴压装环节的合格与否。
通过对压装环节主要质量问题的分析,我们找到了引起这些问题的原因,并在相应生产工序中采取措施,加强了工艺管理。
1. 影响轮对一次压装合格率的因素轮轴压装合格与否是用压装曲线来判别的,所以压装曲线记录仪的灵敏度也直接影响着轮对一次压装合格率。
同时,为了保证所需的联接强度及防止轮对联接部分的应力过高,必须正确选择过盈量。
但在实践中只满足过盈量的选取值,并不能取得理想的压力曲线和终止压装力,它还受到配合表面几何形状误差等因素的制约。
1.1 轮座、轮毂孔锥度对压装合格率的影响通常,在车轮轮毂孔上加工0.04的正向锥度,车轴轮座上加工0.10的正向锥度,以保证曲线形状及终止压装力合格。
在轮对压装过程中,由于轮座、轮毂孔锥度不一致,轮轴配合表面各部位的尺寸(沿径向方向)都不相等,因而沿轴向方向每一横截面的过盈量也不相等。
如果轮座与轮毂孔圆锥度较大且方向一致时,在开始压装时,会出现压力小或没压力,而压装一定量的长度时随过盈量的增加压力迅速增大,造成曲线的长度不够。
1.2 测量误差对轮对压装合格率的影响由于外径干分尺和百分表本身的不确定度(外径千分±0.006 mm,百分表±0.O25mm),再加上选配时测量部位和测量温度及湿度的影响,对过盈量的选取值形成累积误差,不能反映轮轴尺寸的真实值,直接影响过盈量选取的准确性,导致轮对一次压装合格率下降。
导管压装过程及压装力影响因素探析

导管压装过程及压装力影响因素探析作者:熊强强孙庆柳佳琛雷冲来源:《汽车科技》2019年第01期摘要:用伺服压机进行缸盖导管阀座压装,可以采集整个压装过程中的压装力-位移曲线。
压装力是导管压装工序中重要监控参数,在压装过程中,异常情况都会伴随出现压装力过大或者过小的现象,所以利用压装力位移曲线监控压装过程中压装力变化是保证导管压装质量的关键。
本论文结合压力位移曲线对导管压装过程中各阶段进行分析,并通过在不同条件下进行导管压装实验,得出不同条件下最大压装力变化情况,总结出过盈量、压装前润滑、压装速度对导管压装的影响。
关键词:导管;压装力;压力位移曲线;过盈量;压装前润滑;压装速度中图分类号:U466 文献标识码:A 文章编号:1005-2550(2019)01-0096-04Abstract: The pressure-displacement curve of cylinder head guide-pipe can be acquired by using servo press during the whole pressure-mounting process. Pressing force is an important monitoring parameter in the pipe pressing process, abnormal conditions will be accompanied by excessive or small pressure loading force, so the use of pressure loading displacement curve to monitor the pressure change in the process of pressure loading is the key to ensure the quality of pipe pressure loading. In this paper, the pressure-displacement curves are used to analyze the different stages of the pressure-fitting process of the pipe, and the maximum pressure-force under different conditions is obtained through the pressure-fitting experiments. The influence of interference,lubrication before pressure-fitting and pressure-loading speed on the pressure-fitting of the pipe is summarized.Key Words: Guide-pipe; Pressure; Pressure-displacement curve; interference;Lubrication; pressure-loading speed引言在氣缸盖总成加工过程中,导管阀座压装是非常关键的一道工序。
铁路货车轮轴组装工艺改进研究

铁路货车轮轴组装工艺改进研究摘要:随着铁路货车重载、高速的发展需要,对轮轴的制造水平要求越来越高,以进一步提升车辆的运行品质。
铁路货车轮轴主要由车轴、车轮、轴承及前盖后挡等附件组成,车轴与车轮加工后采用过盈配合冷压装装配形成轮对,轴承及附件与轮对装配后成为轮轴。
基于此,本文主要对铁路货车轮轴组装工艺改进进行分析探讨。
关键词:铁路货车;轮轴组装;工艺改进1轮对组装工艺及改进研究轮对组装须符合TB/T1718《铁道车辆轮对组装技术条件》相关要求,目前我国主要铁路货车以准轨为主,设计时速小于120km/h,要求同一轮对的两车轮直径差不大于1mm,同一车轮相互垂直的直径差不大于0.5mm,轮对内侧距离为(1353±2)mm,且轮对内侧距任意三处相差不大于1mm,轮位差不大于3mm。
1.1轮对压装工艺轮对压装工艺设计时,车轴与车轮采用过盈配合,采用自动化压装设备进行压装,其装配过盈量为车轴轮座直径的0.8‰~1.5‰,轮对压装最终压装力根据轮毂孔直径进行计算,轮对压装后,通过轮对尺寸检测及压装位移—压力曲线综合判断车轮车轴的装配质量。
车轴车轮及轮对尺寸检测项目较多,配置有内径外径千分尺、轮径尺、内侧距尺、深度尺、圆弧样板、踏面全形样板、三孔位置度检具、轮位差尺、轮轴偏心检测仪、样板轮对等成套量具检具,用于控制轮对的组装尺寸及组装质量。
轮对压装为特殊过程工序,车轮与车轴的装配质量难以用肉眼观察,需通过压装实物质量与压装曲线综合判断轮对组装质量,其组装尺寸及形位公差满足产品图纸及技术条件相关要求,压装曲线要求光滑并均匀上升,不得有跳动;压装压力曲线长度不小于理论长度的80%;曲线起点陡升时,陡升值不超过98kN;曲线中部不得有下降,平直长度不超过该曲线投影长度的10%;压力曲线末端平直线长度不超过该曲线投影长度的15%;压力曲线开始上升点与终点连成一直线,曲线应全部在此直线之上。
轮对压装曲线可直观判断轮对的装配质量,压装过程中装配不良、损伤拉伤等质量缺陷可通过压装曲线的平直、陡升、降吨、异常凸起等缺陷进行判断,车轮与车轴的压装位移通过位移-压力曲线长度进行判断。
压力—位移曲线在压装工艺中的应用研究
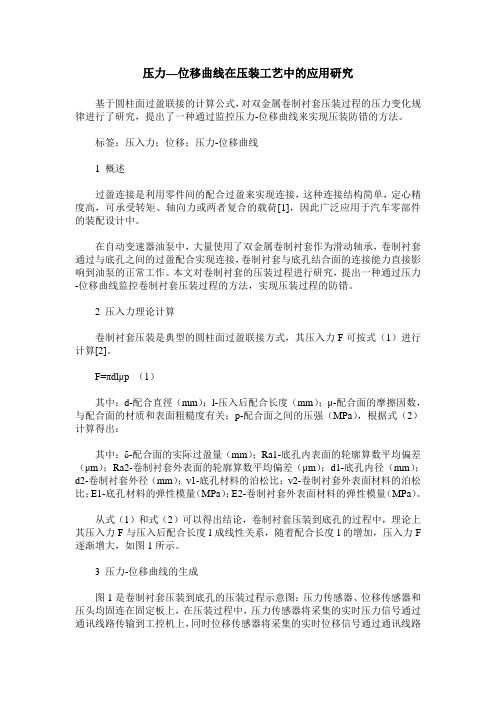
压力—位移曲线在压装工艺中的应用研究基于圆柱面过盈联接的计算公式,对双金属卷制衬套压装过程的压力变化规律进行了研究,提出了一种通过监控压力-位移曲线来实现压装防错的方法。
标签:压入力;位移;压力-位移曲线1 概述过盈连接是利用零件间的配合过盈来实现连接,这种连接结构简单,定心精度高,可承受转矩、轴向力或两者复合的载荷[1],因此广泛应用于汽车零部件的装配设计中。
在自动变速器油泵中,大量使用了双金属卷制衬套作为滑动轴承,卷制衬套通过与底孔之间的过盈配合实现连接,卷制衬套与底孔结合面的连接能力直接影响到油泵的正常工作。
本文对卷制衬套的压装过程进行研究,提出一种通过压力-位移曲线监控卷制衬套压装过程的方法,实现压装过程的防错。
2 压入力理论计算卷制衬套压装是典型的圆柱面过盈联接方式,其压入力F可按式(1)进行计算[2]。
F=πdlμp (1)其中:d-配合直徑(mm);l-压入后配合长度(mm);μ-配合面的摩擦因数,与配合面的材质和表面粗糙度有关;p-配合面之间的压强(MPa),根据式(2)计算得出:其中:δ-配合面的实际过盈量(mm);Ra1-底孔内表面的轮廓算数平均偏差(μm);Ra2-卷制衬套外表面的轮廓算数平均偏差(μm);d1-底孔内径(mm);d2-卷制衬套外径(mm);ν1-底孔材料的泊松比;ν2-卷制衬套外表面材料的泊松比;E1-底孔材料的弹性模量(MPa);E2-卷制衬套外表面材料的弹性模量(MPa)。
从式(1)和式(2)可以得出结论,卷制衬套压装到底孔的过程中,理论上其压入力F与压入后配合长度l成线性关系,随着配合长度l的增加,压入力F 逐渐增大,如图1所示。
3 压力-位移曲线的生成图1是卷制衬套压装到底孔的压装过程示意图:压力传感器、位移传感器和压头均固连在固定板上,在压装过程中,压力传感器将采集的实时压力信号通过通讯线路传输到工控机上,同时位移传感器将采集的实时位移信号通过通讯线路传输到工控机上,工控机将实时的压力和位移信号处理后就可以得到压力-位移曲线。
位移压力曲线

位移压力曲线
位移压力曲线是压装过程中,压装力和压装行程之间的关系曲线。
这种曲线可以用来表示工件在压装过程中的受力情况以及位移变化。
通过对曲线的分析,可以得出压装过程的力和位移监控结果,并对压装结果进行评估。
在压装过程中,如果对位移要求比较高的话,工艺需要考虑结构形变对位移产生的影响能不能抵消或者补偿到最终位移当中。
在这种情况下,可以用到奇石乐伺服压机系统中的一个功能:形变补偿功能。
其最广泛应用的领域为发动机缸盖导管座圈中导管的压装。
奇石乐导管压装对位移控制是有较高要求的。
设备结构受力时多多少少有形变。
压座圈时设备结构会承受2-3T的力在上边,机构发生了形变。
在工程上,任何一个过程的焓变化量都和温度变化相同的定容过程的焓变化量相等。
因此,定压过程中由于压力不变,其技术功值为零,表明工质定压稳定流过诸如换热器等设备时,不对外作技术功,即热能转化来的机械能全部用来维持工质流动。
浅谈缸盖导管、座圈压装

发动机缸盖加工过程中导管座圈压装是生产线中关键辅机工序,压装质量的好坏对后序导管、座圈精加工存在直接影响,根据压装工艺,对导管压装深度及进排气导管、座圈压装一致性有很高的要求,由于导管、座圈压装精度较高,需要采用一面两销定位,如出现定位销受力情况,就会损伤缸盖销孔,影响后续定位销孔的使用,因此在选择导管、座圈压装工艺及机床结构时尤为重要。
1导管、座圈压装机组成①缸盖输送系统:通过机动滚或摆杆到将工件输送到压装工位,压装完成后再通过机动滚道或摆杆将工件输送到下一工位;②缸盖喷油系统:通过喷油装置将润滑油雾化后喷到缸盖导管底孔内壁或导管外壁;③压装系统:一般采用两个工位进行压装,一个工位压装进气导管、座圈,一个工位压装排气导管、座圈;④导管、座圈上料机构:导管、座圈上料形式多种多样,其中最常见的几种上料形式有A:手动上料;B :采用弹夹加料道形式上料;C:采用震动料斗加料道形式上料;⑤阀座冷却系统:通过液氮对座圈冷却后进行压装,目前不少发动机厂家已经采用常温压装,无需液氮冷却。
2C 型结构压装机压装特点2.1以往的压装机多采用油缸驱动,机床结构为四角立柱型结构(如图1),此压装方式在压装导管、座圈过程中存在较大弊端:①首先在压装过程中存在剪切力,定位销孔受力,易变形,容易造成座圈压偏,导管啃伤导管底孔,影响后序加工精度;②设备采用液压驱动,并且多个压头同时压装,在压装过程中由于难以控制多个压头压力长期保持一致,存在压力不稳现象,容易造成压入深度一致性差;③对位移无法有效监测;④设备本体采用螺栓固定,精度易走失。
2.2目前的压装机多采用伺服电缸驱动,C 型压装结构(如图2):①平衡压装,减少缸盖在压装过程中的变形;②整体铸造而成,精度不易走失;③有效地避免工件在压装过程中承受剪切力,避免定位销受力压伤;④伺服电缸驱动可实现位移监控和压力监控。
图1图23C 型结构压装机压装原理(如图3)工步1:机床处于复位状态,工件上料;工步2:伺服电缸带动导向套向下运动与工件接触;工步3:由于反作用力带动座圈压头向上运动与工件接触;工步4:当上下压头都与工件接触后,气液增压抱死系统进行抱死;工步5:开始进行座圈压装;工步6:伺服电缸通过导管压壁进行导管压装;工步7:压装完成,导管压臂退回;工步8:导向套退回;工步9:复位弹簧带动C型框架复位。
- 1、下载文档前请自行甄别文档内容的完整性,平台不提供额外的编辑、内容补充、找答案等附加服务。
- 2、"仅部分预览"的文档,不可在线预览部分如存在完整性等问题,可反馈申请退款(可完整预览的文档不适用该条件!)。
- 3、如文档侵犯您的权益,请联系客服反馈,我们会尽快为您处理(人工客服工作时间:9:00-18:30)。
压力—位移曲线在压装工艺中的应用研究
基于圆柱面过盈联接的计算公式,对双金属卷制衬套压装过程的压力变化规律进行了研究,提出了一种通过监控压力-位移曲线来实现压装防错的方法。
标签:压入力;位移;压力-位移曲线
1 概述
过盈连接是利用零件间的配合过盈来实现连接,这种连接结构简单,定心精度高,可承受转矩、轴向力或两者复合的载荷[1],因此广泛应用于汽车零部件的装配设计中。
在自动变速器油泵中,大量使用了双金属卷制衬套作为滑动轴承,卷制衬套通过与底孔之间的过盈配合实现连接,卷制衬套与底孔结合面的连接能力直接影响到油泵的正常工作。
本文对卷制衬套的压装过程进行研究,提出一种通过压力-位移曲线监控卷制衬套压装过程的方法,实现压装过程的防错。
2 压入力理论计算
卷制衬套压装是典型的圆柱面过盈联接方式,其压入力F可按式(1)进行计算[2]。
F=πdlμp (1)
其中:d-配合直徑(mm);l-压入后配合长度(mm);μ-配合面的摩擦因数,与配合面的材质和表面粗糙度有关;p-配合面之间的压强(MPa),根据式(2)计算得出:
其中:δ-配合面的实际过盈量(mm);Ra1-底孔内表面的轮廓算数平均偏差(μm);Ra2-卷制衬套外表面的轮廓算数平均偏差(μm);d1-底孔内径(mm);d2-卷制衬套外径(mm);ν1-底孔材料的泊松比;ν2-卷制衬套外表面材料的泊松比;E1-底孔材料的弹性模量(MPa);E2-卷制衬套外表面材料的弹性模量(MPa)。
从式(1)和式(2)可以得出结论,卷制衬套压装到底孔的过程中,理论上其压入力F与压入后配合长度l成线性关系,随着配合长度l的增加,压入力F 逐渐增大,如图1所示。
3 压力-位移曲线的生成
图1是卷制衬套压装到底孔的压装过程示意图:压力传感器、位移传感器和压头均固连在固定板上,在压装过程中,压力传感器将采集的实时压力信号通过通讯线路传输到工控机上,同时位移传感器将采集的实时位移信号通过通讯线路
传输到工控机上,工控机将实时的压力和位移信号处理后就可以得到压力-位移曲线。
将图2中初始位置的位移量设置为原点,则得到的压力-位移曲线如图3所示。
3 压力-位移曲线的应用
3.1 压力-位移曲线的防错原理
由式(1)和式(2)可知,对于材质、外形尺寸已经确定的卷制衬套和底孔,其压装过程中的压入力与配合长度、过盈量以及配合面的表面粗糙度有关,根据实际的压装经验,相同条件下,过盈量越大、配合面越粗糙则压入力将越大。
基于上述原理,可以通过一定的途径分别得到过盈量最小、配合面粗糙度最好以及过盈量最大、配合面粗糙度最差情况下的压力-位移曲线,称为压力-位移曲线下控制限和上控制限,如图4,然后将下控制限和上控制限的曲线输入到压装系统的工控机中,实现对所有卷制衬套压装过程的监控。
只有当实际压力-位移曲线处于上控制限和下控制限之间时,工控机才判定压装过程为合格,否则说明卷制衬套或底孔尺寸存在超差情况,工控机会判定压装过程为不合格,这就是应用压力-位移曲线实现防错的原理。
3.2 压力-位移曲线的窗口设置
压力-位移曲线下控制限和上控制限一般是根据极限样件的实际压装过程的压力-位移曲线设置而成,下控制限极限样件的过盈量和配合面粗糙度均按最小值为目标进行制造,上控制限极限样件的过盈量和配合面粗糙度均按最大值为目标进行制造,为了避免制造误差的影响,下控制限极限样件和上控制限极限样件的数量一般为各20~30套。
将所有下控制限极限样件的实际压力-位移曲线取平均值作为最终的下控制限曲线,将所有上控制限极限样件的实际压力-位移曲线取平均值作为最终的上控制限曲线。
在实际的应用中,一般设置三个窗口对压装的压力和位移进行控制,如图5所示,其中压力控制窗口1和压力控制窗口2是根据上控制限和下控制限绘制的,窗口宽度为0.5~1mm,位移控制窗口是根据压装相关的轴向尺寸公差计算得出。
如图6是实际压装过程的压力-位移曲线,只有当实际的曲线从左端穿入壓力控制窗口、从右端穿出压力控制窗口,并且从下端穿入位移控制窗口、从上端穿出位移控制窗口时,压力-位移曲线才是合格,否则判定为压装不合格,这就实现了压装过程的防错。
5 结束语
本文基于圆柱面过盈联接方式压入力的理论计算,对双金属卷制衬套压装过
程的压力变化规律进行了研究,提出了一种通过监控压力-位移曲线来实现压装防错的方法,确保了大规模生产时双金属卷制衬套压装的可靠性。
参考文献
[1]王文斌,等.机械设计手册/第2卷[M].北京:机械工业出版社,2004.
[2]王贤刚,孙美丽,夏成勇.径向滑动轴承过盈装配变形的研究[J].润滑与密封,2008(4).。