100kt_a硫酸装置沸腾炉的设计
1、图1所示为硫酸生产中的沸腾炉

第一章:名称:带控制点工艺流程图(PID)1、图1所示为硫酸生产中的沸腾炉。
试说明图中的位号和图形的意义是:图1 硫酸生产中的沸腾炉带控制点工艺流程图答:(1)仪表位号TI-101、TI-102、TI-103表示第一工序第01、02、03个温度检测回路。
期中:T表示被控变量为温度;I表示仪表具有指示功能;表示该温度指示仪表属于仪表盘正面安装,用于操作员监视用。
(2)仪表位号PI-101表示第一工序第01个压力检测回路。
其中P表示被测变量为压力;I表示仪表具有指示功能;表示该压力表按照在现场。
(3)仪表位号PRC-102表示第一工序第02个压力控制回路。
其中:P表示被测变量为压力;RC表示仪表具有记录、控制功能。
(4)仪表位号AR-101表示第一工序第01个成分分析回路。
其中:A表示被测变量为成分;R表示仪表具有报警功能。
第二章:干燥筒对象特性测试2、为了测量某物料干燥筒的对象特性,在T=0时刻突然将加热蒸汽量从25m3/h增加到28m3/h,物料出口温度记录仪得到的阶跃响应曲线如图3所示。
试求出该对象的特性。
已知流量仪表量程为0~40,温度仪表为0~200℃图3 干燥筒的阶跃响应曲线答:由阶跃响应曲线可以看出该对象具有一阶纯滞后特性。
放大系数为:240/)2528(200/)120150(=--=K 时间常数为T=4 分钟滞后时间为2=τ分钟第三章: 料位测量问题3、流态化粉末状、颗粒状固态介质料位测量的问题。
在石油化工生产中,常遇到流态化粉末状催化剂在反应器内流化床床层高度的测量。
因为流态化的粉末状或颗粒状催化剂具有一般流体的性质,所以在测量它们的床层高度或藏量时,可以把它们看作流体对待。
测量的原理也是将测量床层高度的问题变成测差压的问题。
但是,在进行上述测量时,由于有固体粉末或颗粒的存在,测压点和引压管线很容易被堵塞,因此必须采用反吹风系统,即采用吹气法用差压变送器进行测量。
流化床内测压点的反吹风方式如图2所示,在有反吹风存在的条件下,设被测压力为P ,测量管线引至变送器的压力为2P (即限流孔板后的反吹风压力),反吹管线压降为P ∆,则有P P P ∆+=2,理论上看仪表显示压力2P 较被测压力高P ∆,但实际证明,当采用限流孔板只满足测压点及引压管线不堵的条件时,反吹风气量可以很小,因而P ∆可以忽略不计,即P P =2。
10万吨年硫酸生产工艺设计(硫磺制酸熔硫工序毕业设计
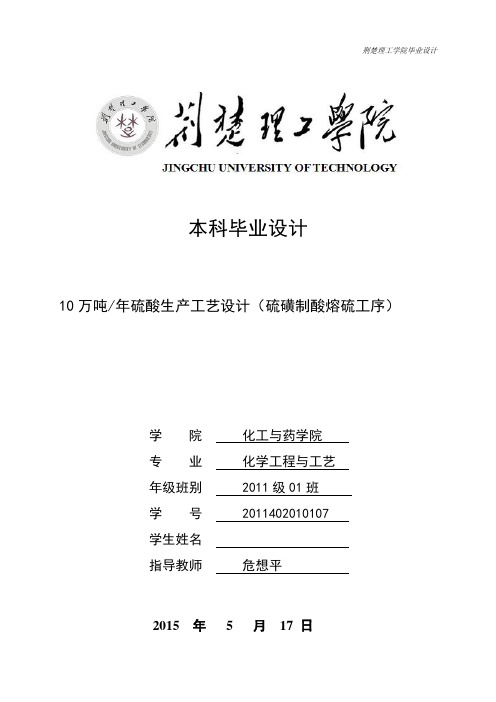
荆楚理工学院毕业设计本科毕业设计10万吨/年硫酸生产工艺设计(硫磺制酸熔硫工序)学院化工与药学院专业化学工程与工艺年级班别 2011级01班学号 2011402010107学生姓名指导教师危想平2015 年 5 月17 日目录前言 (1)1 文献综述 (1)1.1硫磺、硫化物及硫酸的性质 (2)1.1.1 化学性质 (2)1.1.2 物理性质 (3)1.2 硫酸的生产方法 (3)1.2.1 硝化法制造硫酸 (3)1.2.2 接触法制造硫酸 (4)1.3 硫酸生产工艺流程叙述 (5)气体的制取 (5)1.3.1 SO21.3.2 炉气的净化 (6)气体的转化 (6)1.3.3 SO2气体的吸收 (6)1.3.4SO31.3.5尾气的处理 (7)1.4 硫酸的用途 (7)1.4.1 硫酸的工业用途 (7)1.4.2 硫酸的农业用途 (8)2 物料平衡计算 (8)2.1 设计要求 (9)2.2 熔硫部分的物料衡算 (9)2.3熔硫工段的能量衡算 (9)3 主要设备 (10)3.1熔硫釜 (11)3.2焚硫炉 (11)3.3 转化器 (13)3.4 干吸塔 (14)3.5 空气鼓风机 (14)3.6 循环吸泵 (15)3.7 废热锅炉 (15)3.8 过热器和省煤器 (16)4 硫酸的安全生产 (16)4.1 硫酸工业中催化剂的重要作用 (17)4.2 硫酸生产中可能存在的危害 (17)4.3 我国硫酸工业技术概况 (18)4.4安全防护措施及防护用具 (18)4.5环境保护与治理建议 (18)设计小结 (19)参考文献 (20)致谢 (21)10万吨/年硫酸生产工艺设计(硫磺制酸熔硫工序)摘要硫酸作为工业之母,至今还发挥着重要作用。
采用硫磺制硫酸有利于保护环境建清洁文明工厂,且装置上投资为原来的50%,具有很大的经济效益。
硫酸生产工艺主要由五部分组成,包括二氧化硫气体的制取,炉气的净化,二氧化硫气体的转化,三氧化硫气体的吸收以及尾气的处理。
沸腾炉的设计
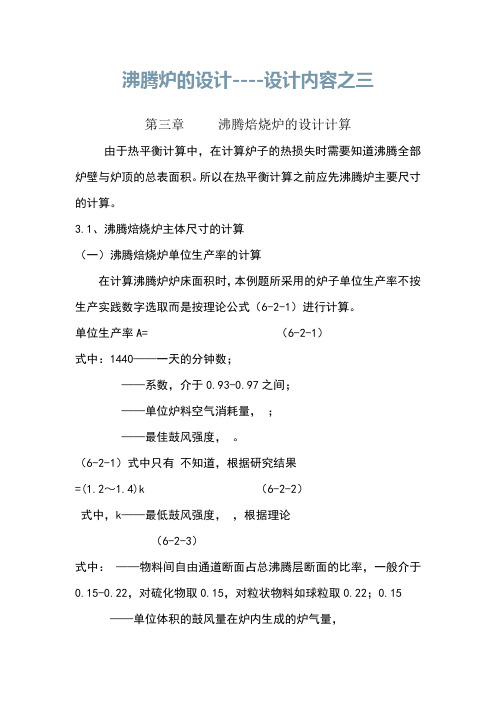
沸腾炉的设计----设计内容之三第三章沸腾焙烧炉的设计计算由于热平衡计算中,在计算炉子的热损失时需要知道沸腾全部炉壁与炉顶的总表面积。
所以在热平衡计算之前应先沸腾炉主要尺寸的计算。
3.1、沸腾焙烧炉主体尺寸的计算(一)沸腾焙烧炉单位生产率的计算在计算沸腾炉炉床面积时,本例题所采用的炉子单位生产率不按生产实践数字选取而是按理论公式(6-2-1)进行计算。
单位生产率A= (6-2-1)式中:1440——一天的分钟数;——系数,介于0.93-0.97之间;——单位炉料空气消耗量,;——最佳鼓风强度,。
(6-2-1)式中只有不知道,根据研究结果=(1.2~1.4)k (6-2-2)式中,k——最低鼓风强度,,根据理论(6-2-3)式中:——物料间自由通道断面占总沸腾层断面的比率,一般介于0.15-0.22,对硫化物取0.15,对粒状物料如球粒取0.22;0.15——单位体积的鼓风量在炉内生成的炉气量,——炉料的比重,4000 ;——炉气重度, = =1.429 ;——通过料层炉气的算术平均温度,= =460℃;——物料粒子平均粒度,米。
根据已知精矿的粒度组成,精矿中大粒部分:粒度 0.323㎜ 10%(33%)0.192㎜ 20%(67%)共计 30%(100%)=0.9=0.9(0.67×0.192+0.33×0.323)=0.212㎜精矿中细粒部分:粒度 0.081㎜ 35%(50%)0.068㎜ 35%(50%)共计 70%(100%)=0.9=0.9(0.50×0.068+0.50×0.081)=0.067㎜对全部精矿:大粒部分 0.212㎜ 30%细粒部分 0.067㎜ 70%= × =0.32物料粒子平均粒度按经验公式计算,对混合料,≤0.415 时,平均粒度根据小粒体积含量按下式计算:=5% +95%=0.05×0.212+0.95×0.067=0.074㎜=74×把上述数字代入(6-2-3)式:=(1.2~1.4)k,选用系数1.2,则最佳鼓风强度 =1.2k=1.2×7.403=8.884现在就可以计算炉子的单位生产率:A= =6.925沸腾炉的单位生产率(床能力)与操作气流速度有关,因此也可按以下公式计算求得:A= (6-2-4)式中:——操作气流速度,米/秒。
浅谈沸腾炉的设计

浅谈沸腾炉的设计、使用要点工业原、燃材料、半成品、成品为了下道工序的更好制备、储存,大多要进行烘干,大规模的工业生产,必然采用烘干设备。
烘干系统使用效果的好坏,不仅体现在本体设计上的周密、统盘考虑,比如较低的热损失、料气的充分交换;还要考虑系统中的众多因素,使之达到最佳结合。
热风炉的选择、设计、使用就是很重要的环节。
一、热风炉的选择热风炉是烘干系统的热量来源。
热风炉热效率高低取决于热烟气的输入量和介质温度,实际应用中热风炉有多种形式。
手烧炉:由人工手动喂煤,可直接燃烧 50mm 以下的粒状煤,需不断的进煤、清渣,工人劳动强度大,大量冷风带入炉内,燃烧过程不稳定、炉内烟气温度低、不完全燃烧损失大,造成煤耗高、热效率低、供热量小。
喷煤炉:对火烟深度控制要求严格,火焰过深,则容易烧坏烘干机内部筒体及扬料板,甚至改变物料的物性;过短,则烟气进入烘干机的温度不足,烘干能力变差。
此外,对煤质及细度要求严格,燃烧不稳定,操作难度大。
燃油(气)炉:利用油、气作为燃料,优点是燃尽率高,易于操作。
缺点是对操作的要求,优其是对安全的要求极高,严禁泄漏,,以防爆炸。
沸腾炉:它介于层燃和悬浮状燃烧之间,燃烧时呈沸腾状态,具有强化燃烧、传热效果好、结构简单、可燃烧劣质燃料等优点。
但传统沸腾炉由于局部结构设计不合理,直角部分多,使用寿命短,炉内易结渣,涡流现象严重,煤耗较高,燃烧温度偏低。
节煤型高温沸腾炉:是我所在传统沸腾炉的基础上进行整体改型和优化设计的一种KF新炉型。
其采用小炉床整体框架结构,炉床容积较常规缩小,炉体结构更加稳固,大大提高了炉体的使用寿命和单位容积热强度;减少了尖锐直角,降低了结渣频率,能够在原有沸腾炉的基础上节煤 40 ~ 60% ,炉温大幅度提升并可自由控制,进一步放宽了对劣质煤的适应程度。
几种炉型的技术经济指标对比见表 1 ,单位容积热强度对比见表 2 。
表 1 不同燃烧方式的技术经济指标比较炉型煤低位热值 /c aγ/ kg燃烧温度℃灰渣含碳量%煤耗kg/t投资 /万元层燃式手烧炉5000 600 18 40 8 喷燃式煤粉炉6000 900 12 30 12 普通沸腾炉4500 700 8 28 16 节煤型沸腾炉3000 1100 4 18 16表 2 几种炉型炉膛容积热强度比较炉型q v ( kW/m 3 )煤粉炉175~233抛煤机炉233~291普通沸腾炉930~1170节煤型沸腾炉1350~1861燃油炉291~349高炉煤气燃气炉233~349节煤型高温沸腾炉因对燃煤的适应性强,能燃烧劣质煤,操作简单,节煤显著而为众多企业所选用。
沸腾炉初步设计方案

沸腾炉初步设计方案沸腾炉是一种常用的热交换设备,通常用于加热或冷却各种流体。
它的工作原理是通过将一定量的流体加热到沸点,使其产生沸腾状态,从而实现传热的目的。
在这篇文章中,将从沸腾炉的工作原理、设计参数、结构设计和安全措施等方面进行详细的介绍,并提出一个初步的设计方案。
沸腾炉的工作原理是利用流体在加热的过程中产生的沸腾现象来传热。
沸腾现象是指当流体受热至其饱和温度以上时,由于压力降低,使流体中的液体部分迅速蒸发形成气泡,并在液体表面聚集形成气泡层。
气泡层具有很高的传热系数,可以快速将热量传递到流体中,从而实现传热的目的。
设计沸腾炉需要考虑的参数包括流体的性质、流量、温度差以及所需的传热量等。
流体的性质决定了其饱和温度和传热系数,不同的流体传热特性也不同,因此在设计过程中需要根据实际情况进行合理选择。
流量是指流体在单位时间内通过沸腾炉的体积或质量,通常需要根据传热需求和设备的承载能力来确定。
温度差是指流体进出口之间的温度差异,通常越大传热效果越好,但也需要根据实际情况进行合理考虑。
传热量则取决于流体的质量、温度差以及传热系数等。
在沸腾炉的结构设计上,主要包括加热区、沸腾区和冷却区。
加热区通常采用电加热器或燃气加热器等方式将流体加热至饱和温度以上,使其进入沸腾区。
沸腾区通常由一组管道和加热板组成,通过液体与加热板的接触来实现沸腾现象。
冷却区则通过冷却介质的流动将加热后的流体冷却至所需温度。
为了确保沸腾炉的安全运行,需要采取一系列的安全措施。
首先,在设计上要确保设备具有足够的强度和稳定性,以承受内部压力和温度的变化。
其次,在操作过程中需要严格控制流体的流量和温度,避免过载运行和温度过高等状况。
同时,设备的维护保养也十分重要,定期检查和清洗设备,确保其正常运行。
基于以上原理和要求,初步的沸腾炉设计方案如下:1.设备结构:沸腾炉采用立式设计,由加热区、沸腾区和冷却区组成,整体结构简单紧凑。
2.材料选择:设备主要采用不锈钢材料,具有良好的耐腐蚀性和高强度,确保设备的长期稳定运行。
图所示为硫酸生产中的沸腾炉

沸腾炉漏料:由于炉体密封不严或物料流动性差,导致物料泄漏
沸腾炉结垢:由于物料中的杂质或水分过多,导致炉内结垢
故障诊断:通过观察、听、闻、摸等方法,确定故障部位和原因
排除故障:根据诊断结果,采取相应的:沸腾炉通过加热炉料,使炉料中的硫磺和空气在高温下反应,生成二氧化硫气体。
促进化学反应:沸腾炉中的高温环境有利于硫磺和空气中的氧发生化学反应,生成二氧化硫气体。
分离固体产物:沸腾炉中的高温环境可以使炉料中的固体产物与气体产物分离,方便后续处理。
提高生产效率:沸腾炉的高温环境可以加快化学反应速度,提高硫酸生产效率。
通知相关部门进行检修和处理
汇报人:
感谢您的观看
确认工艺流程:确认硫酸生产工艺流程,熟悉操作步骤和注意事项。
严格控制温度和压力:沸腾炉的操作过程中,需要严格控制温度和压力,确保生产安全和产品质量。
保持炉内清洁:定期清理炉内杂物,保持炉内清洁,防止杂物对生产过程产生不良影响。
避免过度投料:在投料过程中,要避免过度投料,以免对炉内产生过大的压力和温度波动。
沸腾炉与配料系统:配料系统向沸腾炉提供原料,确保生产顺利进行
沸腾炉与余热回收系统:余热回收系统利用沸腾炉的余热,提高能源利用效率
沸腾炉与酸冷系统:酸冷系统对沸腾炉产生的硫酸进行冷却,保证产品质量
沸腾炉与尾气处理系统:尾气处理系统对沸腾炉产生的尾气进行处理,保护环境
沸腾炉的工作原理
沸腾炉的构造:包括炉体、燃烧器、通风装置等部分
沸腾炉的工作原理:燃料在燃烧器中燃烧产生高温气体,使炉内物料呈沸腾状态,实现传热和化学反应
沸腾炉的特点:具有高效传热、高气速、高生产强度等优点
硫酸装置中焚硫炉的设计

- 11 -第7期硫酸装置中焚硫炉的设计田旭(贵州东华工程股份有限公司, 贵州 贵阳 550002)[摘 要] 对20万吨/年硫酸扩能技改工程项目硫酸装置中焚硫炉的设计,从焚硫炉的工作原理、结构型式和主要尺寸到制造安装应注意的问题进行了阐述和分析。
[关键词] 硫酸装置;焚硫炉;设计;结构特点作者简介:田旭(1984—),男,贵州遵义人,本科,工程师,在贵州东华工程股份有限公司从事化工设备设计校核工作。
20万吨/年硫酸扩能技改工程项目硫酸装置中的焚硫炉,焚烧炉是本项目中的关键设备。
炉子按硫磺的蒸发率不同,分为阶梯式焚硫炉(膜式炉)、池式焚硫炉、喷雾式焚硫炉三种。
使用最普遍的是喷雾式焚硫炉,本文着重对焚硫炉的设计进行阐述和分析。
1 工作原理喷雾式焚硫炉一般为钢制圆筒内衬耐火砖和保温砖的卧式结构。
硫磺经过喷枪喷入炉内,空气由端部进入,经过旋流装置与雾化后的硫磺充分接触进行燃烧。
炉内设有两堵挡墙,使硫磺与空气充分混合。
为了防止燃烧不充分,一般还需要设有二次风入口,用于补充含氧量同时调节炉膛温度,使反应更加完全,以免产生升华硫。
设置两只机械雾化硫磺喷枪,利用泵的高压进行雾化。
为了保证空气与硫磺的充分混合,有利于燃烧更完全,设置了旋流装置。
2 工艺条件表1 焚硫炉的主要工艺参数及特性图1 焚硫炉的结构简图3 焚硫炉的组成3.1 耐火砌体设计耐火砌体是构成焚硫炉的主要结构,设备一般不设置外保温,本设备的炉体隔热保温主要由内部的高铝质耐火砖和高铝质隔热耐火砖。
砌砖前,应对其待衬砖的钢壳内表面进行清污除锈工作并涂刷石墨水玻璃涂料两遍,为了防止钢壳制作完成后到筑炉的这段时间内与大气接触而氧- 12 -论文广场石油和化工设备2019年第22卷化腐蚀,筑炉时,首先衬一层3mm厚硅酸铝纤维板,再用水玻璃粘贴,在钢壳体和砌体之间起到衬垫作用。
然后再砌一层由230mm厚和一层114mm厚的高铝质隔热耐火砖组成的保温层,再砌一层230mm厚的高铝质耐火砖组成的耐火层。
沸腾炉初步设计方案

沸腾炉初步设计方案一、沸腾炉的概述1、沸腾炉的简介沸腾锅炉的工作原理是将破碎到一定粒度的煤末,用风吹起,在炉膛的一定高度上成沸腾状燃烧。
煤在沸腾炉中的燃烧,既不是在炉排上进行的,也不是像煤粉炉那样悬浮在空间燃烧,而是在沸腾炉料床上进行的。
沸腾炉的突出优点是,对煤种适应性广,可燃烧烟煤、无烟煤、褐煤和煤矸石。
它的另一个好处在于使燃料燃烧充分,从而提高燃料的利用率。
沸腾料层的平均温度一般在850一1050℃,料层很厚,相当于一个大蓄热池,其中燃料仅占5%左右,新加入的煤粒进入料层后就和温度高几十倍的灼热颗粒混合,因此能很快燃烧,故可应用煤矸石代替。
生产实践表明,利用含灰分高达70%、发热量仅7.54MJ/kg的煤矸石,锅炉运行正常.40%一50%的热可直接从床层接收。
2、工作原理固体燃料在炉内被向上流动的气流托起,在一定的高度范围内作上下翻滚运动,并以流态化(或称沸腾)状态进行燃烧的炉膛,又称流化床燃烧炉。
沸腾燃烧方式也用于其他的炉窑中。
沸腾燃烧方式的特点既不像在层燃炉中那样将固体燃料静止地放在炉排上燃烧;也不像在室燃炉中那样将液体、气体或磨成细粉状的固体燃料悬浮在炉膛空间中燃烧,而是把固体燃料破碎成一定粒度的粉末,使之在炉内以类似沸腾的状态燃烧。
在中国,沸腾炉用煤的粒度一般为8毫米以下。
3、结构和工作过程常用沸腾炉燃烧室的典型结构包括布风系统、沸腾床、进料和排渣系统3个部分。
①布风系统。
燃烧室底部为布风板,板上直接开孔或装许多带通风小孔的风帽。
布风板的作用是承载料层并使空气上升速度沿炉内截面分布均匀。
②沸腾床。
布风板上放置一定量的床料(包括固体燃料和大量的灰渣或石灰石颗粒)。
运行时,当料层中的空气达到一定上升速度时,沸腾床上的床料便从静止状态转入沸腾状态,这一风速称为临界沸腾风速。
为了保持剧烈的沸腾燃烧工况,沸腾炉正常运行时的风速要比临界沸腾风速大,使料层膨胀到一定高度。
床料沸腾高度约为静止料层的两倍,在此容积的燃料呈沸腾状态,故称为沸腾床,小颗粒则被气流带出炉外。