铸造基本定义
铸造的定义及特点
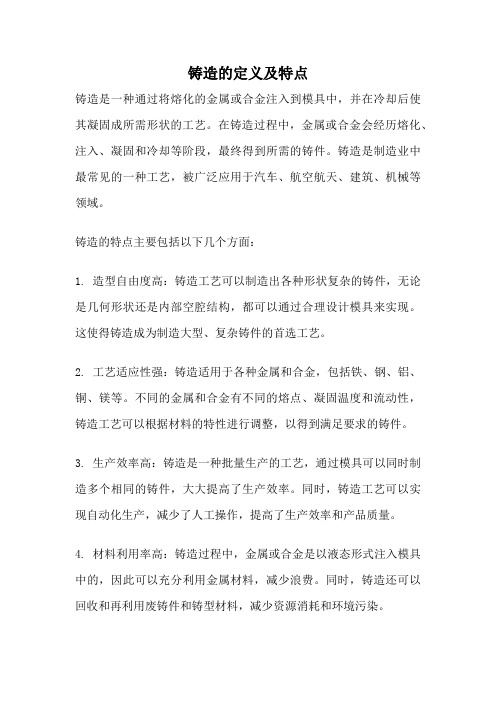
铸造的定义及特点铸造是一种通过将熔化的金属或合金注入到模具中,并在冷却后使其凝固成所需形状的工艺。
在铸造过程中,金属或合金会经历熔化、注入、凝固和冷却等阶段,最终得到所需的铸件。
铸造是制造业中最常见的一种工艺,被广泛应用于汽车、航空航天、建筑、机械等领域。
铸造的特点主要包括以下几个方面:1. 造型自由度高:铸造工艺可以制造出各种形状复杂的铸件,无论是几何形状还是内部空腔结构,都可以通过合理设计模具来实现。
这使得铸造成为制造大型、复杂铸件的首选工艺。
2. 工艺适应性强:铸造适用于各种金属和合金,包括铁、钢、铝、铜、镁等。
不同的金属和合金有不同的熔点、凝固温度和流动性,铸造工艺可以根据材料的特性进行调整,以得到满足要求的铸件。
3. 生产效率高:铸造是一种批量生产的工艺,通过模具可以同时制造多个相同的铸件,大大提高了生产效率。
同时,铸造工艺可以实现自动化生产,减少了人工操作,提高了生产效率和产品质量。
4. 材料利用率高:铸造过程中,金属或合金是以液态形式注入模具中的,因此可以充分利用金属材料,减少浪费。
同时,铸造还可以回收和再利用废铸件和铸型材料,减少资源消耗和环境污染。
5. 产品质量稳定:铸造工艺可以通过控制铸件的组织和性能来满足不同的使用要求。
通过合理的铸造工艺参数和材料选择,可以获得具有一定强度、硬度、耐磨性、耐腐蚀性等特性的铸件。
6. 成本较低:相比其他制造工艺,铸造的设备投资和生产成本较低。
铸造设备简单、易于操作,不需要复杂的加工工艺和设备,可以在较低的成本下完成生产任务。
铸造工艺的发展随着时间的推移和科技的进步,逐渐形成了多种不同的铸造方法和工艺。
例如,根据铸造材料的不同,可以将铸造分为金属铸造、陶瓷铸造和塑料铸造等。
根据铸造方法的不同,可以将铸造分为重力铸造、压力铸造、离心铸造、注射铸造等。
每种铸造方法和工艺都有其适用的范围和特点,可以根据具体的产品要求和生产需求进行选择。
铸造作为一种传统的制造工艺,在现代工业中仍然占据重要地位。
铸造工艺原理和总结

铸造工艺原理和总结一、实质、特点及应用1.铸造定义是指熔炼金属、制造铸型、并将熔融金属浇注入铸型内、凝固后获得一定形状和性能铸件的成形方法。
铸造实质:是利用熔融金属的流动性能实现成形。
铸件:用铸造方法得到的金属零件。
铸型:形成铸件形状的工艺装置。
2.铸造的特点1)成形方便、适应性强•尺寸、形状不受限制长度从几mm-20m;厚度从0.5-500mm;重量从几克-几百吨;•材料的种类和零件形状不受限制。
2)生产成本较低(与锻造比)•设备费用低;•减少加工余量,节省材料;•原材料来源广泛。
3)组织性能较差•晶粒粗大、不均匀;•力学性能差;-工序繁多、易产生铸造缺陷。
4)工作条件差、劳动强度大。
3、铸造的应用1)形状复杂、特别是具有复杂内腔的零件:箱体、缸体和壳体;2)尺寸大、质量大的零件,如床身、重型机械零件;3)力学性能要求不高,或主要承受压应力作用的零件,如底座、支架;4)特殊性能要求的零件,如球磨机的磨球、拖拉机的链轨。
4、铸造成形的基本工序二、金属的铸造性能——是指金属材料铸造成形的难易程度。
评价指标:流动性和收缩性。
(一)流动性——是指熔融金属有流动能力1、表示方法螺旋试样长度L,如L铸钢=20mm,L铸铁=1800mm,铸铁的流动性比铸钢好。
2、影响流动性的因素1)化学成分:共晶合金最好,纯金属差;2)浇注温度:T浇愈高,保温时间愈长,流动性愈好,但收缩性大和浇毁铸型。
经验:“高温出炉,低温浇注”。
3)铸型类别影响铸型蓄热能力和透气性;如、干砂型〉湿砂型>金属型。
4)铸型结构简单、壁厚的铸型〉复杂、壁薄的铸型。
3、流动性对铸件质量的影响流动性好:铸件形状完整、轮廓清晰;利于气体和夹杂物上浮排出和补偿;流动性不好:产生浇不到和冷隔、气孔和夹杂等缺陷。
4、防止流动性不好缺陷方法调整化学成分、提高浇注温度和改善铸型条件。
(二)收缩性——指浇注后熔融金属逐渐冷却至室温时总伴随着体积和尺寸缩小的特性。
制造工艺详解——铸造
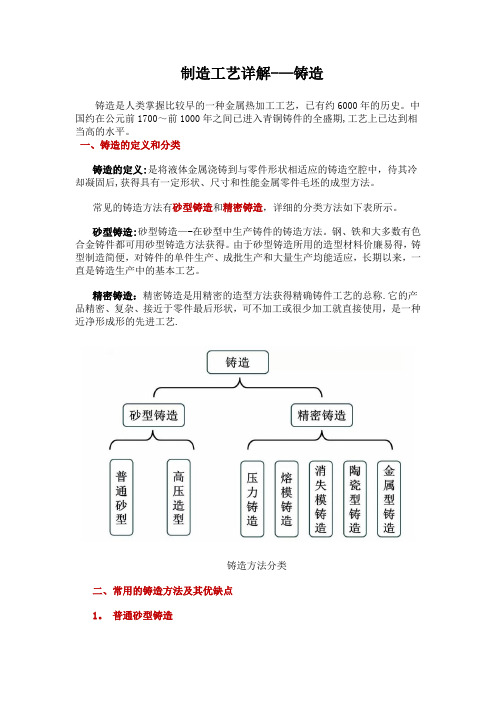
制造工艺详解-—铸造铸造是人类掌握比较早的一种金属热加工工艺,已有约6000年的历史。
中国约在公元前1700~前1000年之间已进入青铜铸件的全盛期,工艺上已达到相当高的水平。
一、铸造的定义和分类铸造的定义:是将液体金属浇铸到与零件形状相适应的铸造空腔中,待其冷却凝固后,获得具有一定形状、尺寸和性能金属零件毛坯的成型方法。
常见的铸造方法有砂型铸造和精密铸造,详细的分类方法如下表所示。
砂型铸造:砂型铸造—-在砂型中生产铸件的铸造方法。
钢、铁和大多数有色合金铸件都可用砂型铸造方法获得。
由于砂型铸造所用的造型材料价廉易得,铸型制造简便,对铸件的单件生产、成批生产和大量生产均能适应,长期以来,一直是铸造生产中的基本工艺。
精密铸造:精密铸造是用精密的造型方法获得精确铸件工艺的总称.它的产品精密、复杂、接近于零件最后形状,可不加工或很少加工就直接使用,是一种近净形成形的先进工艺.铸造方法分类二、常用的铸造方法及其优缺点1。
普通砂型铸造制造砂型的基本原材料是铸造砂和型砂粘结剂。
最常用的铸造砂是硅质砂,硅砂的高温性能不能满足使用要求时则使用锆英砂、铬铁矿砂、刚玉砂等特种砂。
应用最广的型砂粘结剂是粘土,也可采用各种干性油或半干性油、水溶性硅酸盐或磷酸盐和各种合成树脂作型砂粘结剂。
砂型铸造中所用的外砂型按型砂所用的粘结剂及其建立强度的方式不同分为粘土湿砂型、粘土干砂型和化学硬化砂型3种.砂型铸造用的是最流行和最简单类型的铸件已延用几个世纪。
砂型铸造是用来制造大型部件,如灰铸铁,球墨铸铁,不锈钢和其它类型钢材等工序的砂型铸造。
其中主要步骤包括绘画,模具,制芯,造型,熔化及浇注,清洁等.工艺参数的选择加工余量:所谓加工余量,就是铸件上需要切削加工的表面,应预先留出一定的加工余量,其大小取决于铸造合金的种类、造型方法、铸件大小及加工面在铸型中的位置等诸多因素。
起模斜度:为了使模样便于从铸型中取出,垂直于分型面的立壁上所加的斜度称为起模斜度.铸造圆角:为了防止铸件在壁的连接和拐角处产生应力和裂纹,防止铸型的尖角损坏和产生砂眼,在设计铸件时,铸件壁的连接和拐角部分应设计成圆角。
铸造工程基础

铸造工程学一、名词解释1、铸造的定义:铸造就是将熔融的液态金属或合金浇注到与零件的形状(尺寸)相适应的预先制备好的铸型空腔中使之冷却、凝固,而获得毛坯或零件的制造过程称为铸造生产,简称铸造。
2、面砂:特殊配制的在造型时铺覆在模样表面上构成型腔表面层的型砂。
背砂:在模样上覆盖在面砂背后,填充砂箱用的型砂3、模数:钠水玻璃中SiO2和Na2O的摩尔数之比4、浇注位置:浇注时铸件在铸型中的位置。
分型面:两半铸型(上、下型)或多个铸型(多箱铸造)相互接触、配合的表面。
5、压环:在上模样芯头上车削一道半圆凹沟,造型后在上芯座上凸起一环型砂,合型后它能把砂芯压紧,避免液体金属沿间隙钻入芯头,堵塞通气道。
二、判断题三、简答:1、什么是液态金属充型能力?充型是指液态合金填充铸型的过程,是一种运动速度变化的机械过程。
液态金属充满铸型型腔获得形状完整、轮廓清晰铸件的能力称为液态金属的充型能力。
能力不足引起什么缺陷?充型不足易产生浇不足或冷隔等缺陷。
影响因素?①合金的流动性:流动性常以螺旋形试样长度来衡量。
②浇注条件:❶浇注温度❷充型压力③铸型的充型条件:❶铸型的蓄热能力❷铸型温度❸铸型中气体④铸件的结构2、CO2硬化钠水玻璃的硬化机理?P42CO2是一种脱水能力相当强的其气体,从砂粒周围流过,CO2与粘结剂接触面积大,使钠水玻璃部分失水,同时CO2与钠水玻璃中的水作用形成碳酸,从而使钠水玻璃的pH值不断降低,并达到迅速硬化。
3、顺序凝固、定向凝固、均衡凝固、同时凝固的凝固原则?各有什么优缺点?(1)顺序凝固:原则就是在铸件上可能出现缩孔的厚大部位通过安放冒口等工艺措施,使铸件远离冒口的部位先凝固,然后是靠近冒口的部位凝固,最后才是冒口本身凝固。
优点:冒口的补缩作用好,可以防止产生缩孔和缩松,获得致密而合格的铸件。
缺点:因铸铁件各部分有较大温差,使得铸件在凝固期间在过渡部位易产生热裂,凝固后易产生应力和变形,工艺成品率较低,切除冒口耗费大量工时,使成本提高。
铸造基础知识(二)

铸造基础知识铸造的定义——铸造是将通过熔炼的金属液体浇注入铸型内,经冷却凝固获得所需形状和性能的零件的制作过程,是制造业常用的制造方法之一。
铸造是一种古老的制造方法,在我国可以追溯到6000年前。
随着工业技术的发展,铸大型铸件的质量直接影响着产品的质量,因此,铸造在机械制造业中占有重要的地位。
铸造工艺种类:铸造工艺可分为重力铸造、压力铸造、砂型铸造、压铸、熔模铸造和消失模铸造。
铸造方法常用的是砂型铸造,其次是特种铸造方法,如:金属型铸造、熔模铸造、石膏型铸造等。
各种特种铸造方法均有其突出的特点和一定的局限性,对铸件结构也各有各自的特殊要求。
重力铸造重力铸造是指金属液在地球重力作用下注入铸型的工艺,也称浇的重力铸造包括砂型浇铸、金属型浇铸、熔模铸造,泥模铸造等;窄义的重力铸造专指金属型浇铸。
压力铸造压力铸造是指金属液在其他外力(不含重力)的作用下注入铸型的工艺。
广义的压力铸造包括压铸机的压力铸造和真空铸造、低压铸造、离心铸造等;窄义的压力铸造专指压铸机的金属型压力铸造,简称压铸。
这几种铸造工艺是目前有色金属铸造中最常用的、也是相对价格最低的。
砂型铸造砂型铸造是一种以砂作为主要造型材料,制作铸型的传统铸造工艺。
砂型一般采用重力铸造,有特殊要求时也可采用低压铸造、离心铸造等工艺。
砂型铸造的适应性很广,小件、大件,简单件、复杂件,单件、大批量都可采用。
砂型铸造用的模具,以前多用木材制作,通称木模。
木模缺点是易变形、易损坏;除单件生产的砂型铸件外,可以使用尺寸精度较高,并且使用寿命较长的铝合金模具或树脂模具。
虽然价格有所提高,但仍比金属型铸造用的模具便宜得多,在小批量及大件生产中,价格优势尤为突出。
此外,砂型比金属型耐火度更高,因而如铜合金和黑色金属等熔点较高的材料也多采用这种工艺。
但是,砂型铸造也有一些不足之处:因为每个砂质铸型只能浇注一次,获得铸件后铸型即损坏,必须重新造型,所以砂型铸造的生产效率较低;又因为砂的整体性质软而多孔,所以砂型铸造的铸件尺寸精度较低,表面也较粗糙。
铸造知识PPT课件

尺寸精度和表面粗糙度控制方法
尺寸精度控制方法
采用高精度的造型和制芯设备;加强模样和芯盒的制造精度 ;严格控制型砂和芯砂的性能等。
表面粗糙度控制方法
选用细粒度的型砂和芯砂;提高铸型的表面光洁度;优化浇 注系统设计,减少铁液对型壁的冲刷等。
05
特种铸造技术简介
压力铸造(压铸)
定义
压力铸造是利用高压将熔融金属压入金属模具中, 并在压力下快速凝固成型的铸造方法。
冷铁应用
02
在铸件厚大部位放置冷铁,以加快该部位的冷却速度,实现顺
序凝固,防止缩孔和裂纹缺陷。
其他辅助措施
03
根据铸件特点和生产要求,还可采用其他辅助措施,如设置出
气孔、加强型芯的固定和排气等。
04
常见铸造缺陷及防止措施
气孔、夹杂等内部缺陷产生原因及防止方法
气孔产生原因
型砂水分过多或过少;造型操作不当; 浇注系统设计不合理;熔炼过程控制不
准备原材料
选择符合要求的金属原材 料,并进行必要的预处理。
铸造工艺过程
熔炼金属
将金属原材料按照一定比 例配料,通过熔炼设备将 其熔化,获得符合要求的 液态金属。
制造模具
根据铸件的结构和尺寸, 设计并制造相应的模具, 包括型腔、型芯、浇口、 冒口等部分。
浇注
将液态金属倒入模具中, 注意控制浇注温度、速度 和压力等参数。
智能化生产
应用机器人、自动化生产线等智能化设备,实现铸造生产的自动化、 柔性化和智能化,提高生产效率和产品质量。
数字化检测
采用三维扫描、无损检测等数字化检测技术,实现铸件质量的快速、 准确检测,提高产品质量和生产效率。
绿色、环保、可持续发展理念在铸造中体现
机械总结 2

第一章铸造一、铸造的定义及特点。
定义:将液态金属浇注到铸型型腔中,待其冷却凝固后,获得一定形状的毛坯或零件的方法。
优点:1、可以铸造出内腔、外形很复杂的毛坯。
2、工艺灵活性大。
3、铸件成本较低。
缺点:1、铸造组织疏松、晶粒粗大。
2、与锻件比,铸件机械性能低。
3、铸造工序多,精度难以控制,质量不稳定。
4、劳动条件较差。
二、造型方法按照紧实型砂和起模的方法,可分为手工造型和机器造型。
三、铸造工艺通常包括哪些内容?1、铸件的浇注位置和分型面位置;2、加工余量、收缩率和拔模斜度等工艺参数;3、型芯和芯头结构;4、浇注系统、冒口和冷铁的布置等。
四、浇注位置和分型面的选择原则主要有哪些?(结合各图示加以说明)首先应保证铸件质量;其次应使工艺简单、操作方便;还要考虑具体生产条件。
五、型芯在铸造生产中有哪些作用?为什么型芯上应有型芯头?型芯的作用:形成铸件的内腔。
芯头的作用:它是型芯的重要组成部分,起定位和支撑型芯、排除型芯内气体的作用。
六、零件、铸件和模样三者在形状和尺寸上有哪些区别?在尺寸方面:零件尺寸最小,铸件上有加工余量,尺寸比零件大,模样上除了要加加工余量外,还需加上液态金属的收缩率,故尺寸最大。
在形状方面:铸件与零件相比,铸件在垂直于分型面的壁上有起模斜度,且有些小孔、小槽不铸出。
模样与铸件相比,在需铸出的孔处,并无孔,且需加上型芯头。
七、铸造过程中,收缩率、加工余量、拔模斜度都指什么含义?铸件由于凝固、冷却后体积要收缩,其各部分尺寸均小于模样尺寸。
铸造收缩率K=%100-模样铸件铸件LLL加工余量是指在铸件表面上留出的准备切削去的金属层厚度。
拔模斜度-为了便于取模,在平行于出模方向的模样表面上所增加的斜度称为拔模斜度。
八、合金的铸造性能通常用什么来衡量?流动性、收缩性九、什么叫缩孔和缩松?凝固结束后往往在铸件某些部位出现孔洞,大而集中的孔洞称缩孔,细小而分散的孔洞称缩松。
十、铸造应力包括哪两种形式?热应力、机械应力第二章锻压一、锻造与铸造相比有何特点?应用有何不同?锻件内部组织致密、均匀,力学性能优于相同化学成分的铸件,能承受较大的载荷和冲击,因此力学性能要求较高的重要零件一般都采用锻件。
铸造和锻造的定义

铸造和锻造的定义
铸造和锻造是两种不同的工艺,具体定义如下:
铸造是一种将熔融的金属浇铸到模型中获得铸件的过程。
具体来说,是将铁矿石或废铁加热到液态温度区(一般1300度以上)变成铁水,然后灌入预先准备好的特定的模具中,冷却后得到相应的固体件。
铸造专业侧重的是金属熔炼过程,以及浇铸过程中工艺的控制。
锻造是将高温或常温的金属,用锤击或压床加压的方式,使金属物件具有一定的形状和尺寸,并改变它的物理性质的加工法。
具体来说,锻造包括自由锻和模锻,前者用铁榔头手工打,后者则有模具用机床打。
锻造是固态下的塑性成型,有热加工、冷加工之分,像挤压、拉拔、墩粗、冲孔等都属于锻造。
总的来说,铸造是将金属加热熔化后倒入特定模具中,经冷却凝固后获得所需形状的铸件的过程;而锻造则是将金属加热到一定温度后进行打压,用锤击或压床加压的方式使金属具有一定的形状和尺寸。
- 1、下载文档前请自行甄别文档内容的完整性,平台不提供额外的编辑、内容补充、找答案等附加服务。
- 2、"仅部分预览"的文档,不可在线预览部分如存在完整性等问题,可反馈申请退款(可完整预览的文档不适用该条件!)。
- 3、如文档侵犯您的权益,请联系客服反馈,我们会尽快为您处理(人工客服工作时间:9:00-18:30)。
铸造基本定义珠光体――由铁素体和渗碳体片交替组成的共折组织铁素体――即δ组、α组,由碳在铁中形成的间隙固溶体,纬心立方晶格,δ相存在于1392℃~1536℃;α相存在于911℃以下。
奥氏体――即γ相,符号γ或а,由碳在γ铁中形成的间隙固溶体,而心立方晶格,存在于727℃~1483℃石墨――铸铁中以游离状态存在的碳,有折石墨,共晶石墨及共折石墨,共形态可呈片状、蠕虫状、团絮状及球状。
渗碳体――即fe3c,铁与碳形成的间隙化合物,复杂的正交晶格,有一次渗碳体、共晶渗碳体、二次渗碳体和共折渗碳体,开头可呈片状、扳条状及网状。
莱氏体――由奥氏体及其轻变产物和渗碳体组成的混合物。
为共晶组织。
马氏体相变――替换原子经无扩散切变位移而产生的形状改变,形核-长大型的相变马氏体――马氏体相变的产物贝氏体――由铁素体和碳休物组成的针状聚合物,存在于马氏体温度以下珠光体温度以下索氏体――属于珠光体类型,共组织比珠光体细小,具有良好的综合机械性能屈氏体――极细的珠光体组织,比索氏体还细灰铸铁――基体组织和片状石墨组成,断口呈灰口球墨铸铁――基体组织和球状石墨组成,断口呈银白色蠕墨铸铁――基体组织和蠕状石墨组成,也会伴有少量球状石墨,断口呈胶状,断口呈白色可锻铸铁――组织为珠光体和莱氏体组成,退火后组织为基体和团絮状石墨组成,断口呈黑绒状控磨铸铁――基体组织和碳化物组成,断口呈白口耐热铸铁――基体组织和片状或球状石墨组成,断口呈灰口耐腐蚀铸铁――基体组织和片状或球状石墨组成,断口呈灰口碳钢――即碳素钢,指含碳量<2%,并含有少量si、mn、p、s等元素的铁碳合金,工业使用一般含碳量<1。
4%,分为低碳钢、中碳铜和高碳钢合金钢――指钢中除含si、mn作为合金元素外,还含有其它的合金元素,如cr、ni、mo、ti、cu、w、al、co、nb、zr等,也还可含有某些状金属元素。
例如p、n的钢种,分为低合金钢,中合金钢、高合金钢。
不锈钢――含质量分数为13%以下cr元素的钢种,cr在fe中形成固溶体,这种钢的晶粒表面会形成致密的含cr2o3 的氧化膜(印化膜),可以保护晶粒内部免受腐蚀分为铬不锈钢、铬镍不锈钢、铬锰氮不锈钢等耐热钢――在(0.3~0.5)t熔点以上的工作温度具有足够强度且不起皮的钢种高锰钢――典型的抗磨钢,组织为奥氏体和碳化物,其在强烈的冲击、挤压条件下,表层迅速发出加工硬化现象,使其具有在内部保持奥氏体良好韧性和塑性和同时,表面硬休层又具有很好和耐磨性能,其锰含量一般在13%以下现在铸造工厂所采用的造型方法,过去十年间没有大的变化而造型技术有了大的进步。
对湿砂造型、精密砂型、消失模铸造分别叙述如下。
1.湿砂造型法。
Mount公司认为:适用于大部分金属材质、大批量生产的造型法中,粘土湿砂造型是最经济的造型法。
铸造工厂装备有最新技术的控制装置,就应逐步做到,用湿型砂控制技术可以反复得到最佳的性能。
这些控制装置包括,筛分分离金属、回用砂的冷却、回用砂混练时准确释量添加剂等等。
Vulcan 公司认为,现在的粘土湿砂造型机具有优良的性能,能以二年前从未达到过的速度,制造要求严格、允许差别很小时湿砂型。
再加上准确控制效率高的供砂装置,使粘土湿砂型在铁基合金和非铁合金的造型中保持最重要的地位。
Macler Assoc认为,在湿砂造型中,垂直分型与水平分型两种加以比较,对于大批量生产中、小型,灰铁件或球铁件的铸造工厂,重直分型造型都占优势,因其设备费用比较便宜、可以高速造型、所需人员少、紧实度的偏差小等优点。
但采用垂直分型工艺,在浇口方案与昌口与形态上,以及在用复杂的芯子、过滤片、冷铁、套管、舂入芯等方面都受到限制。
此外,用流动性好的合金铸造时,由于金属静压比较高,容易引起金属渗透粘砂。
在制造有色合金铸件方面,已设计了适合这类合金铸件的大批量生产各种特性垂直分型造型法,现正在推广。
但是,具有要求的机械特性的铸件,在用这种造型法达到相当高度的大批量生产之前,作为大批量铝合金铸件的生产方式,金属型铸造法依然占有优势。
Macler Assoc认为,水平分型湿砂型铸造法,对于中、小批量铸造工厂,还是有利的造型法之一,无论是上型、下型方式,或双面模板方式,对复杂铸件的生产都有适应性。
可在一个循环期内更换模样,短时间运行、长时间运行都可以有效的进行生产。
但手工操作需要机械化,为了保证生产表面优良、尺寸精度高的铸件,还需对整套设备进行改造。
温砂造型法的选择,需要考虑以下各点:◆要有能造型出硬度均一的高质量铸型的造型设备。
◆可以迅速更换模板。
◆下芯、铸型的装卸机械化。
Macler Assoc谈到,为使造型度均一,采用了多种技术。
有几种自动双面模板机采用了射砂和压实法,此时,为了取得均一的铸型密度,射砂和压实法,此时,为了取得均一的铸型密度,射砂的方向要是与板垂直的方向。
还有一种上型、下型造型机,为使铸型密度均一,还采了微振击和压实。
另外,为向模样填砂时有强的冲击力,也有用高压缩气体的。
铸造是指将熔炼好的金属浇入铸型,待其凝固后获得一定形状和性能铸件的成形方法。
用铸造方法得到的金属件称为铸件。
铸造的方法很多,主要有砂型铸造、金属型铸造、压力铸造、离心铸造以及熔模铸造等,其中以砂型铸造应用最广泛。
砂型铸造的典型工艺过程包括模样和芯盒的制作、型砂和芯砂配制、造型制芯、合箱、熔炼金属、浇注、落砂、清理及检验。
下图是套筒铸件的铸造生产工艺过程。
套筒砂型铸造工艺过程示意图铸造的优点是可以铸出各种大小规格或形状复杂的铸件,且成本低,材料来源广,所以铸造是机械制造中生产零件或毛坯的主要方法之一。
而铸造的主要缺点是铸件的力学性能及精度较差,使铸造在生产中受到一定的限制。
但在机器设备中,铸件所占的比重还是很大的,如机床、内燃机、轧钢机等机械中,铸件的重量约占机器总重量的75%以上,可见铸造生产在机器制造中的重要性。
铸造(casting)铸造是将金属熔炼成符合一定要求的液体并浇进铸型里,经冷却凝固、清整处理后得到有预定形状、尺寸和性能的铸件的工艺过程。
铸造毛胚因近乎成形,而达到免机械加工或少量加工的目的降低了成本并在一定程度上减少了时间.铸造是现代机械制造工业的基础工艺之一。
铸造种类很多,按造型方法习惯上分为:①普通砂型铸造,包括湿砂型、干砂型和化学硬化砂型3类。
②特种铸造,按造型材料又可分为以天然矿产砂石为主要造型材料的特种铸造(如熔模铸造、泥型铸造、铸造车间壳型铸造、负压铸造、实型铸造、陶瓷型铸造等)和以金属为主要铸型材料的特种铸造(如金属型铸造、压力铸造、连续铸造、低压铸造、离心铸造等)两类。
铸造工艺通常包括:①铸型(使液态金属成为固态铸件的容器)准备,铸型按所用材料可分为砂型、金属型、陶瓷型、泥型、石墨型等,按使用次数可分为一次性型、半永久型和永久型,铸型准备的优劣是影响铸件质量的主要因素;②铸造金属的熔化与浇注,铸造金属(铸造合金)主要有铸铁、铸钢和铸造有色合金;③铸件处理和检验,铸件处理包括清除型芯和铸件表面异物、切除浇冒口、铲磨毛刺和披缝等凸出物以及热处理、整形、防锈处理和粗加工等。
铸造工艺可分为三个基本部分,即铸造金属准备、铸型准备和铸件处理。
铸造金属是指铸造生产中用于浇注铸件的金属材料,它是以一种金属元素为主要成分,并加入其他金属或非金属元素而组成的合金,习惯上称为铸造合金,主要有铸铁、铸钢和铸造有色合金。
金属熔炼不仅仅是单纯的熔化,还包括冶炼过程,使浇进铸型的金属,在温度、化学成分和纯净度方面都符合预期要求。
为此,在熔炼过程中要进行以控制质量为目的的各种检查测试,液态金属在达到各项规定指标后方能允许浇注。
有时,为了达到更高要求,金属液在出炉后还要经炉外处理,如脱硫、真空脱气、炉外精炼、孕育或变质处理等。
熔炼金属常用的设备有冲天炉、电弧炉、感应炉、电阻炉、反射炉等。
不同的铸造方法有不同的铸型准备内容。
以应用最广泛的砂型铸造为例,铸型准备包括造型材料准备和造型造芯两大项工作。
砂型铸造中用来造型造芯的各种原材料,如铸造砂、型砂粘结剂和其他辅料,以及由它们配制成的型砂、芯砂、涂料等统称为造型材料造型材料准备的任务是按照铸件的要求、金属的性质,选择合适的原砂、粘结剂和辅料,然后按一定的比例把它们混合成具有一定性能的型砂和芯砂。
常用的混砂设备有碾轮式混砂机、逆流式混砂机和叶片沟槽式混砂机。
后者是专为混合化学自硬砂设计的,连续混合,速度快。
造型造芯是根据铸造工艺要求,在确定好造型方法,准备好造型材料的基础上进行的。
铸件的精度和全部生产过程的经济效果,主要取决于这道工序。
在很多现代化的铸造车间里,造型造芯都实现了机械化或自动化。
常用的砂型造型造芯设备有高、中、低压造型机、抛砂机、无箱射压造型机、射芯机、冷和热芯盒机等。
铸件自浇注冷却的铸型中取出后,有浇口、冒口及金属毛刺披缝,砂型铸造的铸件还粘附着砂子,因此必须经过清理工序。
进行这种工作的设备有抛丸机、浇口冒口切割机等。
砂型铸件落砂清理是劳动条件较差的一道工序,所以在选择造型方法时,应尽量考虑到为落砂清理创造方便条件。
有些铸件因特殊要求,还要经铸件后处理,如热处理、整形、防锈处理、粗加工等。
铸造是比较经济的毛坯成形方法,对于形状复杂的零件更能显示出它的经济性。
如汽车发动机的缸体和缸盖,船舶螺旋桨以及精致的艺术品等。
有些难以切削的零件,如燃汽轮机的镍基合金零件不用铸造方法无法成形。
另外,铸造的零件尺寸和重量的适应范围很宽,金属种类几乎不受限制;零件在具有一般机械性能的同时,还具有耐磨、耐腐蚀、吸震等综合性能,是其他金属成形方法如锻、轧、焊、冲等所做不到的。
因此在机器制造业中用铸造方法生产的毛坯零件,在数量和吨位上迄今仍是最多的。
铸造生产经常要用的材料有各种金属、焦炭、木材、塑料、气体和液体燃料、造型材料等。
所需设备有冶炼金属用的各种炉子,有混砂用的各种混砂机,有造型造芯用的各种造型机、造芯机,有清理铸件用的落砂机、抛丸机等。
还有供特种铸造用的机器和设备以及许多运输和物料处理的设备。
铸造生产有与其他工艺不同的特点,主要是适应性广、需用材料和设备多、污染环境。
铸造生产会产生粉尘、有害气体和噪声对环境的污染,比起其他机械制造工艺来更为严重,需要采取措施进行控制。
铸造产品发展的趋势是要求铸件有更好的综合性能,更高的精度,更少的余量和更光洁的表面。
此外,节能的要求和社会对恢复自然环境的呼声也越来越高。
为适应这些要求,新的铸造合金将得到开发,冶炼新工艺和新设备将相应出现。
铸造生产的机械化自动化程度在不断提高的同时,将更多地向柔性生产方面发展,以扩大对不同批量和多品种生产的适应性。
节约能源和原材料的新技术将会得到优先发展,少产生或不产生污染的新工艺新设备将首先受到重视。