玻璃钢制品缠绕工艺图文并茂
干货玻璃钢粘接工艺

干货玻璃钢粘接工艺一、玻璃钢件制作玻璃钢简称“FRP”或“GRP”,它是一种玻璃纤维增强塑料,由玻璃纤维毡、玻璃纤维物与合成树脂(如聚酯树脂、环氧树脂)复合而成的非金属材料,在客车上应用最多的是含聚酯树脂的玻璃钢。
玻璃钢件的制作工艺流程如下:在模子上刷涂脱模剂→在模子上铺树脂层(0.5~1.0mm 厚的胶衣) → 胶衣层变硬后,在模子上铺第一层玻璃布→涂树脂和玻璃布→树脂在玻璃钢成型时开始固化→取出玻璃钢件。
二、玻璃钢件的粘接工艺因为聚酯树脂和制作工序的多样性, 在对其进行粘接和密封时就必须有更广泛的工艺范围。
粘接玻璃钢件最常用的胶粘剂一般为聚氨酯胶和硅胶,这些胶粘接玻璃钢件后,形成弹性体,与玻璃钢件粘接牢固,安全可靠。
(1)、时效处理。
刚从模子中取出的玻璃钢件不能马上用于粘接和密封, 必须要经过时效处理, 以便除去在制作玻璃钢件时未反应完全的一些物质, 如单体苯乙烯和其它易挥发的物质。
另外, 时效处理还有助于玻璃钢件内应力的释放和消除。
这里所说的时效处理是指玻璃钢件在 23 摄氏度、相对湿度 50%的条件下, 放置至少两周以上。
在时效处理以前, 还应对玻璃钢件在 60 摄氏度~80 摄氏度的条件下加热 4~6 小时。
(2)、打磨。
经过时效处理过的玻璃钢件, 须用粗砂布一般为80#~120# 在其表面进行打磨处理, 除去时效处理过程中析出的一些化学物质。
(3)、清洁。
清洁剂和胶粘剂应该配套使用。
所用的清洁剂一般有两个用途:① 清洗。
用工业擦拭用纸按住瓶口, 轻轻摇动,确保只有极少量的清洁剂沾上纸巾。
擦拭时, 只能向一个方向擦拭, 不允许来回擦拭。
擦完后, 要立即用干的纸巾将清洁剂擦干(此时纸巾上应没有任何污渍)。
清洁完毕后, 根据温度条件晾置一段时间,以确保清洁剂完全干透。
② 活化。
与胶粘剂配套的清洁剂一般都有活化底材的作用, 使胶粘剂与底材有更好的粘接力。
(4)、底涂。
客车用的玻璃钢件一般是半透明的,有的甚至是透明的。
连续缠绕玻璃钢管道生产工艺与技术

连续缠绕玻璃钢管材技术在我国事一个新兴的玻璃钢管道生产工艺,这种技术设备在国际上也只有意大利、挪威、英国等几个发达国家能够制造。
我国目前有两条从欧洲引进的连续缠绕设备,一条是河南安阳某公司在十年前引进的,另一条是上海某公司在2009年引进的,这两条设备的引进价格都在人民币四千万元以上。
所谓的连续缠绕玻璃钢管就是由钢带的连续前后循环运转,在向前移动的内芯模上连续完成纤维缠绕、复合、加砂、固化等工艺过程。
由于生产的连续性,使设备具有工艺控制便利、劳动强度低、污染小、工作环境好、生产效率高,管材质量稳定等上风。
青岛朗通机器有限公司的连续缠绕玻璃钢管材的国家专利技术,打破了我国以往只有定长断续法生产玻璃钢管的历史,开创了我国运用和赶超国际最先进的玻璃钢管生产技术的先河。
我公司的连续缠绕玻璃钢管技术具备独占的技术工艺和独特的成型专利技术,生产线通过了专家鉴定。
现在设备已经批量生产,在国内外都有销售,市场远景非常乐观。
下面就从以下几个方面具体阐述一下我公司的连续缠绕玻璃钢管道的生产工艺、技术的最新进展:一、连续缠绕玻璃钢管成型技术的研制过程青岛朗通公司的前身是一家从事塑料制品的机械设备制造的专业厂家,公司拥有工艺研发、机械设计、自动化程控、高分子材料分析等多种学科的技术研发中心,有着多年的机械加工制造经验和丰富的管道生产、施工经验。
公司曾经开发了多个在国内十分具有影响利的产品:有PVC塑料芯层发泡管技术、铝塑复合管技术、大口径中空壁缠绕管技术、PPR管技术、供水/燃气管技术等管道项目。
值得一提的是大口径中空壁缠绕管技术,可生产直径200-3000mm的管道,其技术是采用方管连续缠绕成型的原理完成的,这种成型技术在国内首家成功推出后很快被国家建设部列为重点推广项目,在国内广泛地推广普及。
大口径塑料管道的成功研制打破了我国在排水、输水管网一直延续使用的混凝土管的历史,加快了以塑代钢、以塑取代混凝土管的步伐。
在大口径的环保管道推出的背景之下,玻璃钢管道技术在排水、输水管网的应用在国内迅猛崛起,发展势态很可观。
玻璃钢制品穿纱作业指导书

玻璃钢制品穿纱作业指导书
一、目的
规范操作流程,保证后续工艺正常。
二、适用范围
纱穿过树脂盒、预成型器、模具的过程。
三、工作流程
1.确认型材型号及相应排纱图。
2.先穿树脂盒,纱在一根细铜丝的帮助下,每孔穿两根纱,
除非是规定只有1根的穿
1根,穿的时候从最下层里侧开始,依次穿完每一孔,同时纱架上要求每穿一层保留相邻的一层备用,例如通常穿三层,在纱架上就是1、3、5层的纱穿过树脂盒,保留2、4层不动。
3.穿过树脂盒的纱再用铜丝穿过3块预成型板,顺序依
然是从最下层里侧开始,依次
穿完每一孔。
4.穿过预成型板的纱在一根铁片的帮助下穿过模具,注
意铁片始终是通过模具中较平
坦的位置,纱通过后再移动到正确的位置;先穿角落位置的纱,再穿较平坦位置,最后铁片不能通过时,余下的纱用已经穿过的纱带过去,每次只带一个孔的纱,带出一根再带另一根,具体做法是找一根较接近的纱,缠绕在这根纱上,一起拉过去。
用铁片穿纱时每次最好只穿一个孔的纱。
5.拉纱时几根纱一起拉,以免只拉一根与其它的纱摩擦
起毛,在穿过模具的纱上打一
个结,剪掉过长的纱,用铁链将拉具和粗纱连接起来,启动拉具,注意当拉具到头复位后将铁链重新固定,拉纱到正确
位置停止。
6.全面检查一下纱的位置,将不在位置的纱通过拉纱的
过程调整到正确的位置,穿纱
的原则是避免交叉,使每根纱都能保持顺畅的通过,而不会因为交叉、摩擦起毛。
五、质量要求
1、粗纱位于正确的位置。
2、粗纱没有交叉,膨体纱进模角度正确。
六、注意事项
遵守01520型拉挤机安全操作规程。
玻璃钢贮罐螺旋缠绕新工艺
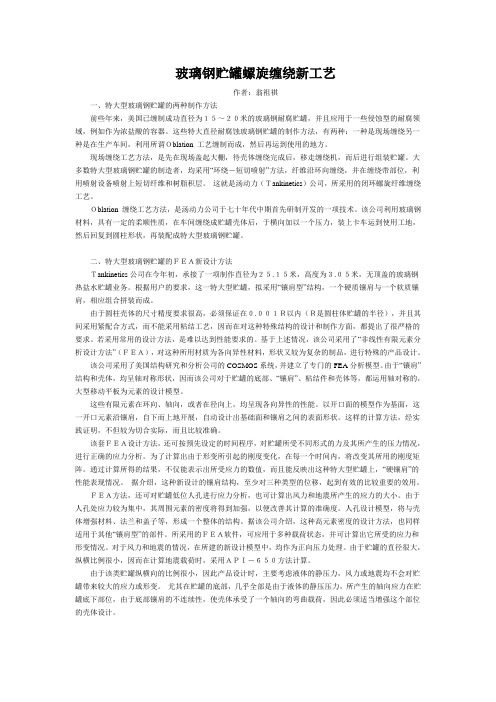
玻璃钢贮罐螺旋缠绕新工艺作者:翁祖祺一、特大型玻璃钢贮罐的两种制作方法前些年来,美国已缠制成功直径为15~20米的玻璃钢耐腐贮罐,并且应用于一些侵蚀型的耐腐领域,例如作为浓盐酸的容器。
这些特大直径耐腐蚀玻璃钢贮罐的制作方法,有两种:一种是现场缠绕另一种是在生产车间,利用所谓Oblation 工艺缠制而成,然后再运到使用的地方。
现场缠绕工艺方法,是先在现场盖起大棚,待壳体缠绕完成后,移走缠绕机,而后进行组装贮罐。
大多数特大型玻璃钢贮罐的制造者,均采用“环绕-短切喷射”方法,纤维沿环向缠绕,并在缠绕带部位,利用喷射设备喷射上短切纤维和树脂积层。
这就是汤动力(Tankinetics)公司,所采用的闭环螺旋纤维缠绕工艺。
Oblation 缠绕工艺方法,是汤动力公司于七十年代中期首先研制开发的一项技术。
该公司利用玻璃钢材料,具有一定的柔顺性质,在车间缠绕成贮罐壳体后,于横向加以一个压力,装上卡车运到使用工地,然后回复到圆柱形状,再装配成特大型玻璃钢贮罐。
二、特大型玻璃钢贮罐的FEA新设计方法Tankinetics公司在今年初,承接了一项制作直径为25.15米,高度为3.05米,无顶盖的玻璃钢热盐水贮罐业务。
根据用户的要求,这一特大型贮罐,拟采用“镶肩型”结构,一个硬质镶肩与一个软质镶肩,相应组合拼装而成。
由于圆柱壳体的尺寸精度要求很高,必须保证在0.001R以内(R是圆柱体贮罐的半径),并且其间采用紧配合方式,而不能采用粘结工艺,因而在对这种特殊结构的设计和制作方面,都提出了很严格的要求。
若采用常用的设计方法,是难以达到性能要求的。
基于上述情况,该公司采用了“非线性有限元素分析设计方法”(FEA),对这种所用材质为各向异性材料,形状又较为复杂的制品,进行特殊的产品设计。
该公司采用了美国结构研究和分析公司的COSMOS系统,并建立了专门的FEA分析模型。
由于“镶肩”结构和壳体,均呈轴对称形状,因而该公司对于贮罐的底部、“镶肩”、粘结件和壳体等,都运用轴对称的,大型移动平板为元素的设计模型。
玻璃钢制品缠绕形式的确定
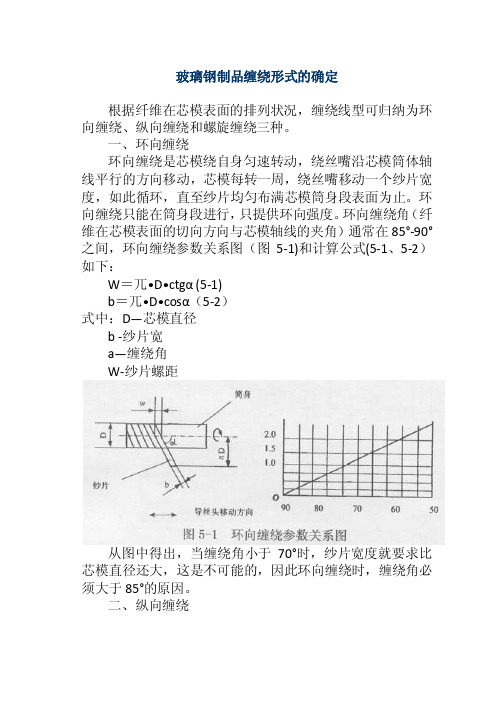
玻璃钢制品缠绕形式的确定根据纤维在芯模表面的排列状况,缠绕线型可归纳为环向缠绕、纵向缠绕和螺旋缠绕三种。
一、环向缠绕环向缠绕是芯模绕自身匀速转动,绕丝嘴沿芯模筒体轴线平行的方向移动,芯模每转一周,绕丝嘴移动一个纱片宽度,如此循环,直至纱片均匀布满芯模筒身段表面为止。
环向缠绕只能在筒身段进行,只提供环向强度。
环向缠绕角(纤维在芯模表面的切向方向与芯模轴线的夹角)通常在85°-90°之间,环向缠绕参数关系图(图5-1)和计算公式(5-1、5-2)如下:W=兀•D•ctgα (5-1)b=兀•D•cosα(5-2)式中:D—芯模直径b -纱片宽a—缠绕角W-纱片螺距从图中得出,当缠绕角小于70°时,纱片宽度就要求比芯模直径还大,这是不可能的,因此环向缠绕时,缠绕角必须大于85°的原因。
二、纵向缠绕纵向缠绕又称平面缠绕,图5-2a。
缠绕过程中,绕丝嘴在固定平面内作匀速圆周运动,芯模绕自身慢速旋转。
绕丝嘴每转一周,芯模转动一个微小角度,反映在芯模表面等于一个纱片的宽度。
纱片与芯模轴线的夹角称为缠绕角,其值小于25°。
纱片依次连续缠绕到芯模上,各纱片均与极孔相切,相互间紧挨着而不交叉。
纤维缠绕轨迹近似为一个平面单圆封闭曲线。
平面缠绕基本线型图5-2b。
式中:r1、r2-----两封头的极孔半径Lc------筒身段长度Le1、Le2------两封头高度若两封头极孔相同(即r1=r2=r),封头高度相等(即Le1=Le2=Le)则平面缠绕的速比i为芯模转速Zm和单位时间绕丝嘴绕芯模旋转次数n的比值,若纱片的宽度为b,缠绕解为α,则速比为平面缠绕适用于球形、椭球形及长径比小于1的短粗筒形容器的生产。
平面缠绕容器封头上(极孔处)纤维有严重架空现象,为了减少纤维架空对制品质量的影响,一般在缠绕不同层次时,使缠绕角α值在一定范围内变化,以分散纤维在端头部的堆积。
环向缠绕和纵向缠绕在一定条件下,可以看作螺旋缠绕的特例。
玻璃钢缠绕管道的基本工艺及性能

玻璃钢缠绕管道的基本工艺及性能一、管壁基本构造管壁结构在玻璃钢中,由拉伸强度很高的玻璃纤维起着骨架增强作用,而耐压耐磨性较强的合成树脂则作为基本材料粘结纤维,使其起共同的成型和承载作用。
内衬层、外保护层——管壁的内、外表面,由玻璃纤维毡、表面毡和耐腐蚀性高强的树脂组成,其中纤维重量约占10%,树脂重量约占90%,内衬层使管道形成一层密实、光滑、坚硬的外壳,以增加管道的防渗性、耐久性和耐腐性。
结构层——由交叉缠绕的玻璃纤维粗纱作为增强骨架,以聚酯树内衬层 缠绕 层 缠绕 层 外保护 层表面内衬层 次内 衬 层 环 向 层 交叉缠绕 层 交叉缠绕 层 环 向 层 防老化树脂 层脂作为粘结基体。
二、先进的制作工艺目前我公司采用的是往复式定长缠绕工艺,使用目前比较先进的二轴纤维缠绕机。
同时可以生产两件同样规格的玻璃钢管道。
缠绕控制采用计算机实时自动控制可以完成环向-交叉-环向等全自动控制。
生产过程中可以不需人工操作,大大提高产品质量。
接口部份采用我公司专利快速接头连接。
密封性能优良,安装方便可满足5Mpa以下压力管道的使用。
三、基本性能一):性能概述高强度:环向强度:500Mpa,轴向拉伸强度320Mpa,纤维增强,强度可设计性。
高刚度:树脂-缠绕纱结构层。
1250、2500、3750、5000、7500、10000N/m2及以上.防渗漏:富树脂内衬层和高致密度结构层,里外防漏。
重量轻:一般只有同口径钢管的1/4,水泥管的1/10,安装费用低。
耐腐蚀:耐腐性能特别优异,可输送腐蚀介质和任何污水。
输水性能好:采用食品级树脂,水质优良、无任何异味,且长期使用不结垢,避光条件下不产生微生物。
内壁光滑:水力摩阻系数小且长期稳定,具有可观的节能效益。
抗冻性能好:水结冰后不冻裂。
保温性能好:导热系数值为钢管的1/233。
阻燃性好:阻燃指数大于30。
使用寿命长:按50年设计,唯一将使用寿命写进国内外标准的产品。
二):玻璃钢管道的优点与其他材质的管道比较,玻璃管道具有以下一些显著的优点:1.耐腐蚀性。
玻璃钢管(定长缠绕、离心浇铸、连续缠绕)工艺比较
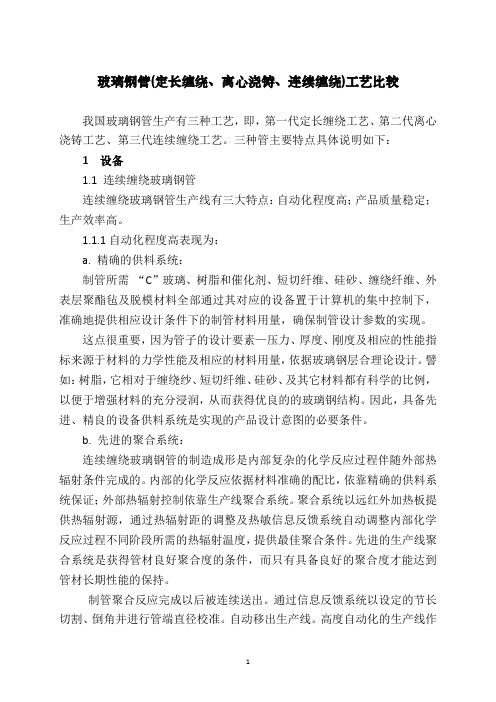
玻璃钢管(定长缠绕、离心浇铸、连续缠绕)工艺比较我国玻璃钢管生产有三种工艺,即,第一代定长缠绕工艺、第二代离心浇铸工艺、第三代连续缠绕工艺。
三种管主要特点具体说明如下:1 设备1.1 连续缠绕玻璃钢管连续缠绕玻璃钢管生产线有三大特点:自动化程度高;产品质量稳定;生产效率高。
1.1.1自动化程度高表现为:a. 精确的供料系统:制管所需“C”玻璃、树脂和催化剂、短切纤维、硅砂、缠绕纤维、外表层聚酯毡及脱模材料全部通过其对应的设备置于计算机的集中控制下,准确地提供相应设计条件下的制管材料用量,确保制管设计参数的实现。
这点很重要,因为管子的设计要素—压力、厚度、刚度及相应的性能指标来源于材料的力学性能及相应的材料用量,依据玻璃钢层合理论设计。
譬如:树脂,它相对于缠绕纱、短切纤维、硅砂、及其它材料都有科学的比例,以便于增强材料的充分浸润,从而获得优良的的玻璃钢结构。
因此,具备先进、精良的设备供料系统是实现的产品设计意图的必要条件。
b. 先进的聚合系统:连续缠绕玻璃钢管的制造成形是内部复杂的化学反应过程伴随外部热辐射条件完成的。
内部的化学反应依据材料准确的配比,依靠精确的供料系统保证;外部热辐射控制依靠生产线聚合系统。
聚合系统以远红外加热板提供热辐射源,通过热辐射距的调整及热敏信息反馈系统自动调整内部化学反应过程不同阶段所需的热辐射温度,提供最佳聚合条件。
先进的生产线聚合系统是获得管材良好聚合度的条件,而只有具备良好的聚合度才能达到管材长期性能的保持。
制管聚合反应完成以后被连续送出。
通过信息反馈系统以设定的节长切割、倒角并进行管端直径校准。
自动移出生产线。
高度自动化的生产线作为客观条件,造就了高品质的连续缠绕玻璃钢管。
1.1.2产品质量稳定:高度的生产线自动化排除了人为因素的干扰。
生产线只须经最初的参数调整,便进入正常工作状态,以恒定的速度、设计的配方、设计的运行参数运行,连续不间断工作,直至最后一件产品的完成。
玻璃钢缠绕成型工艺

具有高强度、轻质、耐腐蚀、绝缘等 优点,广泛应用于航空、航天、汽车、 建筑等领域。
历史与发展
起源
起源于20世纪40年代,最初用于制造飞机 零部件。
发展历程
经过多年的研究和技术改进,玻璃钢缠绕成型工艺 逐渐完善,应用领域不断扩大。
发展趋势
随着环保意识的提高和新型材料的出现,玻 璃钢缠绕成型工艺将进一步向绿色化、智能 化方向发展。
应用领域
航空航天
用于制造飞机零部件、卫星结构件等。
建筑领域
用于制造建筑模板、装饰材料等。
汽车工业
用于制造汽车车身、发动机罩等部件。
管道防腐
用于制造防腐管道、化工设备等。
02 玻璃钢缠绕成型工艺流程
材料准备
玻璃纤维
选择适合的玻璃纤维类型,如E-glass、S-glass等, 根据产品性能要求进行选择。
温度与压力控制
要点一
温度控制
在缠绕过程中,控制温度以保证树脂的固化速度和产品质 量。
要点二
压力控制
在缠绕和固化过程中,控制压力以保证纤维与树脂的紧密 结合和管件密实度。
04 玻璃钢缠绕成型工艺的质 量控制
材料质量控制
01
02
03
树脂
纤维增强材料
辅助材料
选择高品质的树脂,确保其具有 良好的粘结性、耐久性和稳定性。
后期处理
修整
对产品表面进行修整,去除毛刺、气泡等缺陷。
涂装
根据产品用途和外观要求,进行涂装处理,提高产品美观度和耐腐蚀性。
03 玻璃钢缠绕成型工艺的关 键技术
纤维选择与处理
纤维选择
根据产品性能要求,选择合适的纤维材料, 如玻璃纤维、碳纤维、芳纶纤维等。
- 1、下载文档前请自行甄别文档内容的完整性,平台不提供额外的编辑、内容补充、找答案等附加服务。
- 2、"仅部分预览"的文档,不可在线预览部分如存在完整性等问题,可反馈申请退款(可完整预览的文档不适用该条件!)。
- 3、如文档侵犯您的权益,请联系客服反馈,我们会尽快为您处理(人工客服工作时间:9:00-18:30)。
玻璃钢制品缠绕工艺(图文并茂)
纤维缠绕工艺是树脂基复合材料的主要制造工艺之一。
是一种在控制张力和预定线型的条件下,应用专门的缠绕设备将连续纤维或布带浸渍树脂胶液后连续、均匀且有规律地缠绕在芯模或内衬上,然后在一定温度环境下使之固化,成为一定形状制品的复合材料成型方法。
纤维缠绕成型工艺示意图1-1。
缠绕的主要形式有三种(图1-2 ):环向缠绕、平面缠绕及螺旋缠绕。
环向缠绕的增强材料与芯模轴线以接近90度角(通常为85-89度)的方向连续缠绕在芯模上,平面缠绕的增强材料以与芯模两端极孔相切并在平面内的方向连续缠绕在芯模上,螺旋缠绕的增强材料也与芯模两端相切,但是在芯模上呈螺旋状态连续缠绕在芯模上。
纤维缠绕技术的发展与增强材料、树脂体系的发展和工艺发明息息相关。
尽管在汉代就有在长木杆外加纵向竹丝及环向蚕丝后浸渍大漆制造戈、戟等长兵器杆的工艺,但直到20世纪50年代纤维缠绕工艺才真正成为一种复合材料制造技术。
1945年首次应用纤维缠绕技术成功制造了无弹簧的车轮悬挂装置,1947年第一台纤维缠绕机被发明。
随着碳纤维、芳纶纤维等高性能纤维的开发和微机控制缠绕机的出现,纤维缠绕工艺作为一种机械化生产程度很高的复合材料制造技术,得到迅速的发展,20世纪60年代开始在几乎所有可能的领域都得到了应用。
根据缠绕时树脂基体所处的化学、物理状态不同,缠绕工艺可分为干法、湿法及半干法三种。
1.干法
干法缠绕采用经过事先浸胶而处于B阶段的预浸纱带。
预浸纱带是在专门的工厂或车间制造与提供的。
干法缠绕时,
在缠绕机上需先对预浸纱带进行加热软化处理后再缠绕到芯模上。
由于可以在缠绕前对预浸纱带的含胶量、胶带尺寸及质量进行检测和筛选,因而可以较准确地控制制品质量。
干法缠绕的生产效率较高,缠绕速度可达100-200m/min,工作环境也较清洁。
但干法缠绕设备比较复杂且造价很高,缠绕制品的层间剪切强度也较低。
2.湿法
湿法缠绕是将纤维经集束、浸胶后,在张力控制下直接缠绕在芯模上,然后再固化成型。
湿法缠绕的设备比较简单,但由于纱带浸胶后立即缠绕,在缠绕过程中对制品含胶量不易控制和检验,同时胶液中的溶剂固化时易在制品中形成气泡、孔隙等缺陷,缠绕时张力也不易控制。
同时,工人在溶剂挥发气氛和纤维短毛飞扬的环境中操作,劳动条件较差。
3.半干法
与湿法工艺相比,半干法是在纤维浸胶到缠绕至芯模的途中增加一套烘干设备,将纱带胶液中的溶剂基本上驱赶掉。
与干法相比较,半干法不依赖一整套复杂的预浸渍工艺设备。
虽然制品的含胶量在工艺过程中与湿法一样不易精确控制且比湿法多一套中间烘干设备,工人的劳动强度更大,但制品中的气泡、孔隙等缺陷大为降低。
三种方法各有特点,湿法缠绕方式因其对设备的要求相对简单和制造成本较低而应用最为广泛。
三种缠绕工艺方法的优缺点比较见表1-1。