PID控制外文翻译
PID控制中英文对照翻译

外文资料与翻译PID Contro lIntroductionThe PID controller is the most common form of feedback. It was an essential element of early governors and it became the standard tool when process control emerged in the 1940s. In process control today, more than 95% of the control loops are of PID type, most loops are actually PI control. PID controllers are today found in all areas where control is used. The controllers come in many different forms. There are standalone systems in boxes for one or a few loops, which are manufactured by the hundred thousands yearly. PID control is an important ingredient of a distributed control system. The controllers are also embedded in many special purpose control systems. PID control is often combined with logic, sequential functions, selectors, and simple function blocks to build the complicated automation systems used for energy production, transportation, and manufacturing. Many sophisticated control strategies, such as model predictive control, are also organized hierarchically. PID control is used at the lowest level; the multivariable controller gives the set points to the controllers at the lower level. The PID controller can thus be said to be the “bread and butter of control engineering. It is an important component in every co ntrol engineer’s tool box.PID controllers have survived many changes in technology, from mechanics and pneumatics to microprocessors via electronic tubes, transistors, integrated circuits. The microprocessor has had a dramatic influence the PID controller. Practically all PID controllers made today are based on microprocessors. This has given opportunities to provide additional features like automatic tuning, gain scheduling, and continuous adaptation.6.2 The AlgorithmWe will start by summarizing the key features of the PID controller. The “textbook” version of the PID algorithm is described by:()()()()⎪⎪⎭⎫ ⎝⎛++=⎰dt t de d e t e K t u T T d t i 01ττ 6.1 where y is the measured process variable, r the reference variable, u is the control signal and e is the control error (e =sp y − y ). The reference variable is often calledthe set point. The control signal is thus a sum of three terms: the P-term (which is proportional to the error), the I-term (which is proportional to the integral of the error), and the D-term (which is proportional to the derivative of the error). The controller parameters are proportional gain K, integral time T i, and derivative time T d. The integral, proportional and derivative part can be interpreted as control actions based on the past, the present and the future as is illustrated in Figure 2.2. The derivative part can also be interpreted as prediction by linear extrapolation as is illustrated in Figure 2.2. The action of the different terms can be illustrated by the following figures which show the response to step changes in the reference value in a typical case.Effects of Proportional, Integral and Derivative ActionProportional control is illustrated in Figure 6.1. The controller is given by D6.1E with T i= and T d=0. The figure shows that there is always a steady state error in proportional control. The error will decrease with increasing gain, but the tendency towards oscillation will also increase.Figure 6.2 illustrates the effects of adding integral. It follows from D6.1E that the strength of integral action increases with decreasing integral time T i. The figure shows that the steady state error disappears when integral action is used. Compare with the discussion of the “magic of integral action” in Sec tion 2.2. The tendency for oscillation also increases with decreasing T i. The properties of derivative action are illustrated in Figure 6.3.Figure 6.3 illustrates the effects of adding derivative action. The parameters K and T i are chosen so that the closed loop system is oscillatory. Damping increases with increasing derivative time, but decreases again when derivative time becomes too large. Recall that derivative action can be interpreted as providing prediction by linear extrapolation over the time T d. Using this interpretation it is easy to understand that derivative action does not help if the prediction time T d is too large. In Figure 6.3 the period of oscillation is about 6 s for the system without derivative Chapter 6. PID ControlFigure 6.1Figure 6.2Derivative actions cease to be effective when T d is larger than a 1 s (one sixth of the period). Also notice that the period of oscillation increases when derivative time is increased.A PerspectiveThere is much more to PID than is revealed by (6.1). A faithful implementation of the equation will actually not result in a good controller. To obtain a good PID controller it is also necessary to consider。
PID控制简介中英文翻译word版
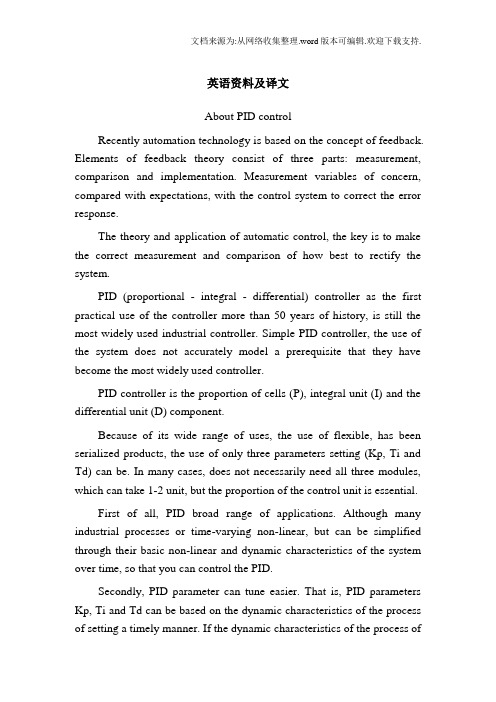
英语资料及译文About PID controlRecently automation technology is based on the concept of feedback. Elements of feedback theory consist of three parts: measurement, comparison and implementation. Measurement variables of concern, compared with expectations, with the control system to correct the error response.The theory and application of automatic control, the key is to make the correct measurement and comparison of how best to rectify the system.PID (proportional - integral - differential) controller as the first practical use of the controller more than 50 years of history, is still the most widely used industrial controller. Simple PID controller, the use of the system does not accurately model a prerequisite that they have become the most widely used controller.PID controller is the proportion of cells (P), integral unit (I) and the differential unit (D) component.Because of its wide range of uses, the use of flexible, has been serialized products, the use of only three parameters setting (Kp, Ti and Td) can be. In many cases, does not necessarily need all three modules, which can take 1-2 unit, but the proportion of the control unit is essential.First of all, PID broad range of applications. Although many industrial processes or time-varying non-linear, but can be simplified through their basic non-linear and dynamic characteristics of the system over time, so that you can control the PID.Secondly, PID parameter can tune easier. That is, PID parameters Kp, Ti and Td can be based on the dynamic characteristics of the process of setting a timely manner. If the dynamic characteristics of the process ofchange, for example, changes may be caused by the load dynamic characteristics of the system changes, PID parameters can be re-tuning.Third, PID controller in practice is to be improved continuously, the following are two examples of improvements.In factories, we always see a lot of loops are in manual, and because of the difficulty of the course so that the "automatic" mode, a smooth working. As a result of these deficiencies, the use of the industrial control system PID is always subject to product quality, safety, waste production and energy problems. PID parameter self-tuning PID parameters in order to deal with this problem setting generated. Now, the auto-tuning or self-tuning of PID controller is a business single-loop controllers and distributed control system of a standard.In some cases the system-specific design of PID controller to control very well, but they are there are still some problems to be solved: If self-tuning should be based on the model, in order to re-PID tuning parameters online to find and maintain a good process model is more difficult. When closed-loop works, the requirements in the process of inserting must have a test signal. This method will cause disturbance, so model-based PID parameter self-tuning is not too good in the industrial applications.If self-tuning control law based on the often difficult to load disturbance caused by the impact and dynamic characteristics of the process of the impact of changes in the distinction between the effects of so disturbed overshoot controller will have to create a self-adaptive unnecessary conversion. In addition, since the control law based on the maturity of the system is not the stability of analytical methods, the reliability of parameter tuning, there are many problems.Therefore, many self-tuning PID controller parameters work in the auto-tuning mode and not in the self-tuning mode. Auto-tuning is oftenused to describe the state of open-loop based on a simple process model to determine automatic calculation of PID parameters.PID in controlling nonlinear, time-varying, coupling and parameter uncertainty and structural complexity of the process, the work is not very good. The most important thing is, if the PID controller can not control the complexity of the process, regardless of how not to use transfer parameters.Despite these shortcomings, PID controller is sometimes the most simple is the best controller.At present, the level of industrial automation has become a measure of the level of modernization in all walks of life an important sign. At the same time, the development of control theory has also experienced a classical control theory, modern control theory and intelligent control theory of three stages. Classic example of intelligent control is ambiguous, such as full-automatic washing machine. Automatic control system can be divided into open-loop control systems and closed-loop control system.A control system, including controllers, sensors, transmitters, implementing agencies, input and output interfaces. Controller's output after the output interface, the implementing agencies, added to the system was charged with; control system charged with the amount, after the sensor, transmitter, through the input interface to the controller. Different control system, the sensor, transmitter, the executing agency is not the same. For example pressure sensors need to be used in pressure control system. Electric heating control system is the sensor temperature sensor. At present, PID control and PID controller or a smart controller (instrument) has a lot of products have been in practice in engineering is widely used, there are a wide range of PID controller products, major companies have developed with PID parameter self-tuning regulator function smart (intelligent regulator), which the PID controller parameters are automatically adjusted through the intelligent or self-tuning, adaptivealgorithms to achieve. PID control are achieved using pressure, temperature, flow, liquid level controller, PID control functions to achieve the programmable logic controller (PLC), also enables the PC system, PID control and so on. Programmable Logic Controller (PLC) is the use of its closed-loop control module to achieve PID control, and programmable logic controller (PLC) can be connected directly with the ControlNet, such as Rockwell's PLC-5 and so on. There can be the controller PID control functions, such as Rockwell's Logix product line, it can be connected directly with the ControlNet, using the Internet to achieve its long-range control functions.1, Open-loop control systemOpen-loop control system is the object of the output (volume control) on the controller does not affect the output. In this control system, do not rely on volume will be charged back to the formation of anti-any closed-loop circuit.2, Closed-loop control systemClosed-loop control system is characterized by the output of the system object (volume control) will be sent back to the impact of anti-output controller to form one or more of the closed-loop. Closed-loop control system has positive feedback and negative feedback, if the feedback signal and the system to set the value of the signal the other hand, is referred to as negative feedback, if the same polarity is called positive feedback, the general closed-loop control system using negative feedback, also known as negative feedback control system. Closed-loop control system has many examples. For example, people with negative feedback is a closed-loop control system, the eye is the sensor to act as a feedback, the human body system through the constant variety of the right to make amendments to the final action. If there are no eyes, there is no feedback loops, it became an open-loop control system. Another example, when a full-automatic washing machine with a realcontinuously check whether the washed clothing, and wash off automatically after the power supply, it is a closed-loop control system.3, Step responseStep response refers to a step input (step function) when added to the system, the system output. Steady-state error is the system response into the steady-state, the system's desired output and actual output of the difference. The performance of control system can be stable, accurate and fast three words to describe. Stability is the stability of the system, a system must be able to work, first of all must be stable, from the step response should be a convergence point of view; quasi-control system refers to the accuracy, control precision, stability is usually state error description, it said the system output steady-state value and the difference between expectations; fast control system refers to the rapid response, and usually to a quantitative description of the rise time.4, Theory and the characteristics of PID controlIn engineering practice, the most widely used control laws regulate the proportional, integral, differential control, referred to as PID control, also known as PID regulator. PID controller has been available for nearly 70 years of history, which in its simple structure, stable, reliable, easy to adjust and become the main industrial control technologies. When charged with the structure and parameters of the object can not completely grasp, or lack of accurate mathematical model, control theory it is difficult using other techniques, the system controller structure and parameters have to rely on experience and on-site testing to determine when the application PID control of the most convenient technology. That is, when we do not fully understand the system and charged with an object, or can not be an effective means of measuring system parameters to obtain the most suitable PID control technology. PID control, in practice there are PI and PD control. PID controller is the error of the system, using proportional, integral, differential calculationfor the control of the volume control.The ratio of (P) controlProportional control is one of the most simple control methods. The controller's output and input error signal proportional to the relationship. The output has the existence of steady-state error when there is only a proportional control system.Integral (I) controlIn integral control, the controller's output and input error signal is proportional to the integral relationship. For an automatic control system, if steady-state error exists after entering the steady-state, the control system is referred to as steady-state error or having a poor system. In order to eliminate steady-state error, the controller must be the introduction of the "key points." Points of error depend on the time of the points of the increase over time, will increase the integral term. In this way, even if the error is very small, integral term will increase as time increases, it increased to promote the output of the controller so that steady-state error further reduced until zero. Therefore, the proportional + integral (PI) controller, you can make the system after entering the steady-state non-steady-state error.Differential (D) controlIn the differential control, the controller's output and input of the differential error signal (the rate of change of error) is directly proportional to the relationship. Automatic control system to overcome the errors in the adjustment process may be unstable or even oscillation. The reason is because of greater inertial components (links) or there is lag components, can inhibit the role of error, the changes always lag behind changes in error. The solution is to inhibit the changes in the role of error "in advance", that is close to zero in the error and suppress the role of error should be zero. This means that the controller only the introduction of the "proportion" of often is not enough, the proportion of the role isonly to enlarge the amplitude error, the current need to increase the "differential item" that can change the trend of prediction error, In this way, with the proportion of + differential controller, will be able to advance so that the role of inhibitory control error equal to zero or even negative, thus avoiding the amount charged with a serious overshoot. Therefore, greater inertia of the charged object or lag, the proportion of + differential (PD) controller to improve the system in the regulation of the dynamic characteristics of the process.PID控制简介当今的自动控制技术都是基于反馈的概念。
比例积分微分控制器外文翻译

原文:A proportional–integral–derivative controller (PID controller) is a generic .control loop feedback mechanism widely used in industrial control systems. A PID controller attempts to correct the error between a measured process variable and a desired setpoint by calculating and then outputting a corrective action that can adjust the process accordingly.The PID controller calculation (algorithm) involves three separate parameters; the Proportional, the Integral and Derivative values. The Proportional value determines the reaction to the current error, the Integral determines the reaction based on the sum of recent errors and the Derivative determines the reaction to the rate at which the error has been changing. The weightedsum of these three actions is used to adjust the process via a control element such as the position of a control valve or the power supply of a heating element.By "tuning" the three constants in the PID controller algorithm the PID can provide control action designed for specific process requirements. The response of the controller can be described in terms of the responsiveness of the controller to an error, the degree to which the controller overshoots the setpoint and the degree of system oscillation. Note that the use of the PID algorithm for control does not guarantee optimal control of the system or system stability.Some applications may require using only one or two modes to provide the appropriate system control. This is achieved by setting the gain of undesired control outputs to zero. A PID controller will be called a PI, PD, P or I controller in the absence of the respective control actions. PI controllers are particularly common, since derivative action is very sensitive to measurement noise, and the absence of an integral value may prevent the system from reaching its target value due to the control action.Note: Due to the diversity of the field of control theory and application, many naming conventions for the relevant variables are in common use.1.Control loop basicsA familiar example of a control loop is the action taken to keep one's shower water at the ideal temperature, which typically involves the mixing of two process streams, cold and hot water. The person feels the water to estimate its temperature. Based on thismeasurement they perform a control action: use the cold water tap to adjust the process. The person would repeat this input-output control loop, adjusting the hot water flow until the process temperature stabilized at the desired value.Feeling the water temperature is taking a measurement of the process value or process variable (PV). The desired temperature is called the setpoint (SP). The output from the controller and input to the process (the tap position) is called the manipulated variable (MV). The difference between the measurement and the setpoint is the error (e), too hot or too cold and by how much.As a controller, one decides roughly how much to change the tap position (MV) after one determines the temperature (PV), and therefore the error. This first estimate is the equivalent of the proportional action of a PID controller. The integral action of a PID controller can be thought of as gradually adjusting the temperature when it is almost right. Derivative action can be thought of as noticing the water temperature is getting hotter or colder, and how fast, and taking that into account when deciding how to adjust the tap.Making a change that is too large when the error is small is equivalent to a high gain controller and will lead to overshoot. If the controller were to repeatedly make changes that were too large and repeatedly overshoot the target, this control loop would be termed unstable and the output would oscillate around the setpoint in either a constant, growing, or decaying sinusoid. A human would not do this because we are adaptive controllers, learning from the process history, but PID controllers do not have the ability to learn and must be set up correctly. Selecting the correct gains for effective control is known as tuning the controller.If a controller starts from a stable state at zero error (PV = SP), then further changes by the controller will be in response to changes in other measured or unmeasured inputs to the process that impact on the process, and hence on the PV. Variables that impact on the process other than the MV are known as disturbances and generally controllers are used to reject disturbances and/or implement setpoint changes. Changes in feed water temperature constitute a disturbance to the shower process.In theory, a controller can be used to control any process which has a measurable output (PV), a known ideal value for that output (SP) and an input to the process (MV) thatwill affect the relevant PV. Controllers are used in industry to regulate temperature, pressure, flow rate, chemical composition, speed and practically every other variable for which a measurement exists. Automobile cruise control is an example of a process which utilizes automated control.Due to their long history, simplicity, well grounded theory and simple setup and maintenance requirements, PID controllers are the controllers of choice for many of these applications.While PID controllers are applicable to many control problems, they can perform poorly in some applications.PID controllers, when used alone, can give poor performance when the PID loop gains must be reduced so that the control system does not overshoot, oscillate or "hunt" about the control setpoint value. The control system performance can be improved by combining the feedback (or closed-loop) control of a PID controller with feed-forward (or open-loop) control. Knowledge about the system (such as the desired acceleration and inertia) can be "fed forward" and combined with the PID output to improve the overall system performance. The feed-forward value alone can often provide the major portion of the controller output. The PID controller can then be used primarily to respond to whatever difference or "error" remains between the setpoint (SP) and the actual value of the process variable (PV). Since the feed-forward output is not affected by the process feedback, it can never cause the control system to oscillate, thus improving the system response and stability.For example, in most motion control systems, in order to accelerate a mechanical load under control, more force or torque is required from the prime mover, motor, or actuator. If a velocity loop PID controller is being used to control the speed of the load and command the force or torque being applied by the prime mover, then it is beneficial to take the instantaneous acceleration desired for the load, scale that value appropriately and add it to the output of the PID velocity loop controller. This means that whenever the load is being accelerated or decelerated, a proportional amount of force is commanded from the prime mover regardless of the feedback value. The PID loop in this situation uses the feedback information to effect any increase or decrease of the combined output in order toreduce the remaining difference between the process setpoint and the feedback value. Working together, the combined open-loop feed-forward controller and closed-loop PID controller can provide a more responsive, stable and reliable control system.Another problem faced with PID controllers is that they are linear. Thus, performance of PID controllers in non-linear systems (such as HVAC systems) is variable.Along with the development of Fuzzy Mathematics, control engineers gradually pay much attention to the idea of Fuzzy Control, thus promoting the invention of fuzzy controllers. However, simple fuzzy controller has its own defect, where control effect is quite coarse and the control precision can not reach the expected level. Therefore, the Fuzzy Adaptive PID Controller is created by taking advantage of the superiority of PID Controller and Fuzzy Controller. Taken this controller in use, the corresponding error and its differential error of the control system can be feed backed to the Fuzzy Logic Controller. Moreover, the three parameters of PID Controller is determined online through fuzzification, fuzzy reasoning and defuzzification of the fuzzy system to maintain better working condition than the traditional PID controller.Meanwhile,the design method and general steps are introduced of the Parameter self-setting Fuzzy PID Controller. Eventually, the Fuzzy Inference Systems Toolbox and SIMULINK toolbox are used to simulate Control System. The results of the simulation show that Self-organizing Fuzzy Control System can get a better effect than the Classical PID controlled evidently.Keywords:Classic PID control; Fuzzy Control; Parameters tuning; the Fuzzy Adaptive PID Controller; MA TLAB simulation译文:比例积分微分控制器(PID调节器)是一个控制环,广泛地应用于工业控制系统里的反馈机制。
PID控制中英文对照翻译

外文资料与翻译PID Contro l6.1 IntroductionThe PID controller is the most common form of feedback. It was an essential element of early governors and it became the standard tool when process control emerged in the 1940s. In process control today, more than 95% of the control loops are of PID type, most loops are actually PI control. PID controllers are today found in all areas where control is used. The controllers come in many different forms. There are standalone systems in boxes for one or a few loops, which are manufactured by the hundred thousands yearly. PID control is an important ingredient of a distributed control system. The controllers are also embedded in many special purpose control systems. PID control is often combined with logic, sequential functions, selectors, and simple function blocks to build the complicated automation systems used for energy production, transportation, and manufacturing. Many sophisticated control strategies, such as model predictive control, are also organized hierarchically. PID control is used at the lowest level; the multivariable controller gives the set points to the controllers at the lower level. The PID controller can thus be said to be the “bread and butter of control engineering. It is an important component in every control engineer’s tool box.PID controllers have survived many changes in technology, from mechanics and pneumatics to microprocessors via electronic tubes, transistors, integrated circuits. The microprocessor has had a dramatic influence the PID controller. Practically all PID controllers made today are based on microprocessors. This has given opportunities to provide additional features like automatic tuning, gain scheduling, and continuous adaptation.6.2 AlgorithmWe will start by summarizing the key features of the PID controller. The “textbook” version of the PID algorithm is described by:()()()()⎪⎪⎭⎫ ⎝⎛++=⎰dt t de d e t e K t u T T d t i 01ττ 6.1 where y is the measured process variable, r the reference variable, u is the control signal and e is the control error (e =sp y − y ). The reference variable is often calledthe set point. The control signal is thus a sum of three terms: the P-term (which is proportional to the error), the I-term (which is proportional to the integral of the error), and the D-term (which is proportional to the derivative of the error). The controller parameters are proportional gain K, integral time T i, and derivative time T d. The integral, proportional and derivative part can be interpreted as control actions based on the past, the present and the future as is illustrated in Figure 2.2. The derivative part can also be interpreted as prediction by linear extrapolation as is illustrated in Figure 2.2. The action of the different terms can be illustrated by the following figures which show the response to step changes in the reference value in a typical case.Effects of Proportional, Integral and Derivative ActionProportional control is illustrated in Figure 6.1. The controller is given by D6.1E with T i= and T d=0. The figure shows that there is always a steady state error in proportional control. The error will decrease with increasing gain, but the tendency towards oscillation will also increase.Figure 6.2 illustrates the effects of adding integral. It follows from D6.1E that the strength of integral action increases with decreasing integral time T i. The figure shows that the steady state error disappears when integral action is used. Compare with the discussion of the “magic of integral action” in Section 2.2. The tendency for oscillation also increases with decreasing T i. The properties of derivative action are illustrated in Figure 6.3.Figure 6.3 illustrates the effects of adding derivative action. The parameters K and T i are chosen so that the closed loop system is oscillatory. Damping increases with increasing derivative time, but decreases again when derivative time becomes too large. Recall that derivative action can be interpreted as providing prediction by linear extrapolation over the time T d. Using this interpretation it is easy to understand that derivative action does not help if the prediction time T d is too large. In Figure 6.3 the period of oscillation is about 6 s for the system without derivative Chapter 6. PID ControlFigure 6.1Figure 6.2Derivative actions cease to be effective when T d is larger than a 1 s (one sixth of the period). Also notice that the period of oscillation increases when derivative time is increased.A PerspectiveThere is much more to PID than is revealed by (6.1). A faithful implementation of the equation will actually not result in a good controller. To obtain a good PID controller it is also necessary to consider。
【系统】PID中英文对照翻译

【关键字】系统PID ControlIntroductionThe PID controller is the most common form of feedback. It was an essential element of early governors and it became the standard tool when process control emerged in the 1940s. In process control today, more than 95% of the control loops are of PID type, most loops are actually PI control. PID controllers are today found in all areas where control is used. The controllers come in many different forms. There are standalone systems in boxes for one or a few loops, which are manufactured by the hundred thousands yearly. PID control is an important ingredient of a distributed control system. The controllers are also embedded in many special purpose control systems. PID control is often combined with logic, sequential functions, selectors, and simple function blocks to build the complicated automation systems used for energy production, transportation, and manufacturing. Many sophisticated control strategies, such as model predictive control, are also organized hierarchically. PID control is used at the lowest level; the multivariable controller gives the set points to the controllers at the lower level. The PID controller can thus be said to be the “bread a nd butter of control engineering. It is an important component in every control engineer’s tool box.PID controllers have survived many changes in technology, from mechanics and pneumatics to microprocessors via electronic tubes, transistors, integrated circuits. The microprocessor has had a dramatic influence the PID controller. Practically all PID controllers made today are based on microprocessors. This has given opportunities to provide additional features like automatic tuning, gain scheduling, and continuous adaptation.6.2 The AlgorithmWe will start by summarizing the key features of the PID controller. The “textbook” version of the PID algorithm is described by:6.1where y is the measured process variable, r the reference variable, u is the control signal and e is the control error(e = − y). The reference variable is often called the set point. The control signal is thus a sum of three terms: the P-term (which is proportional to the error), the I-term (which is proportional to the integral of the error), and the D-term (which is proportional to the derivative of the error). Thecontroller parameters are proportional gain K, integral time Ti, and derivative time Td. The integral, proportional and derivative part can be interpreted as control actions based on the past, the present and the future as is illustrated in Figure 2.2. The derivative part can also be interpreted as prediction by linear extrapolation as is illustrated in Figure 2.2. The action of the different terms can be illustrated by the following figures which show the response to step changes in the reference value in a typical case.Effects of Proportional, Integral and Derivative ActionProportional control is illustrated in Figure 6.1. The controller is given by D6.1E with Ti = and Td=0. The figure shows that there is always a steady state error in proportional control. The error will decrease with increasing gain, but the tendency towards oscillation will also increase.Figure 6.2 illustrates the effects of adding integral. It follows from D6.1E that the strength of integral action increases with decreasing integral time Ti. The figure shows that the steady state error disappears when integral action is used. Compare with the discussion of the “magic of integral action” in Section 2.2. The tendency for oscillation also increases with decreasing Ti. The properties of derivative action are illustrated in Figure 6.3.Figure 6.3 illustrates the effects of adding derivative action. The parameters K and Ti are chosen so that the closed loop system is oscillatory. Damping increases with increasing derivative time, but decreases again when derivative time becomes too large. Recall that derivative action can be interpreted as providing prediction by linear extrapolation over the time Td. Using this interpretation it is easy to understand that derivative action does not help if the prediction time Td is too large. In Figure 6.3 the period of oscillation is about 6 s for the system without derivative Chapter 6. PID ControlFigure 6.1Figure 6.2Derivative actions cease to be effective when Td is larger than a 1 s (one sixth of the period). Also notice that the period of oscillation increases when derivative time is increased.A PerspectiveThere is much more to PID than is revealed by (6.1). A faithful implementation of the equation will actually not result in a good controller. To obtain a good PID controller it is also necessary to consider。
PID名词定义
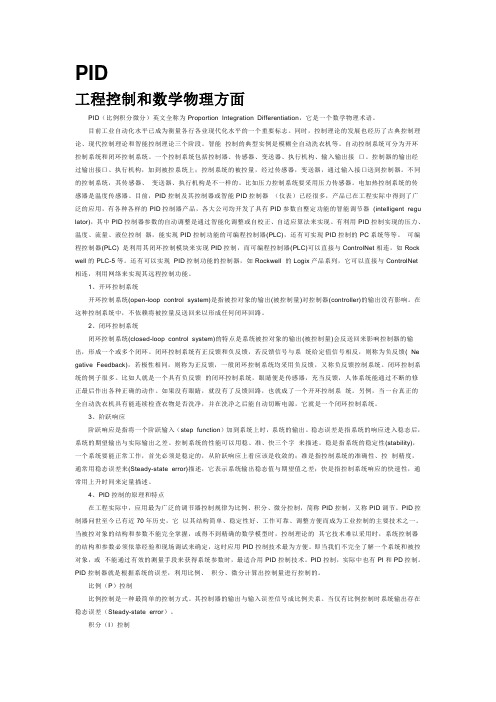
PID工程控制和数学物理方面PID(比例积分微分)英文全称为Proportion Integration Differentiation,它是一个数学物理术语。
目前工业自动化水平已成为衡量各行各业现代化水平的一个重要标志。
同时,控制理论的发展也经历了古典控制理论、现代控制理论和智能控制理论三个阶段。
智能控制的典型实例是模糊全自动洗衣机等。
自动控制系统可分为开环控制系统和闭环控制系统。
一个控制系统包括控制器、传感器、变送器、执行机构、输入输出接口。
控制器的输出经过输出接口、执行机构,加到被控系统上;控制系统的被控量,经过传感器,变送器,通过输入接口送到控制器。
不同的控制系统,其传感器、变送器、执行机构是不一样的。
比如压力控制系统要采用压力传感器。
电加热控制系统的传感器是温度传感器。
目前,PID控制及其控制器或智能PID控制器(仪表)已经很多,产品已在工程实际中得到了广泛的应用,有各种各样的PID控制器产品,各大公司均开发了具有PID参数自整定功能的智能调节器(intelligent regu lator),其中PID控制器参数的自动调整是通过智能化调整或自校正、自适应算法来实现。
有利用PID控制实现的压力、温度、流量、液位控制器,能实现PID控制功能的可编程控制器(PLC),还有可实现PID控制的PC系统等等。
可编程控制器(PLC) 是利用其闭环控制模块来实现PID控制,而可编程控制器(PLC)可以直接与ControlNet相连,如Rock well的PLC-5等。
还有可以实现PID控制功能的控制器,如Rockwell 的Logix产品系列,它可以直接与ControlNet 相连,利用网络来实现其远程控制功能。
1、开环控制系统开环控制系统(open-loop control system)是指被控对象的输出(被控制量)对控制器(controller)的输出没有影响。
在这种控制系统中,不依赖将被控量反送回来以形成任何闭环回路。
外文翻译---PID控制算法

附录附件1:英文资料及中文翻译英文资料PID control algorithm1, PID is a closed loop control algorithm. Therefore, to achieve the PID algorithm, you must have the hardware loop control, that is, must have feedback. Such as controlling a motor speed, you have to have a measurement of speed sensor, and the results fed back to the control line, the following will also be speed control, for example.2, PID is the proportional (P), integral (I), Derivative (D) control algorithms. But not must have these three algorithms, it can be PD, PI, or even only the P-control algorithm. I used for closed-loop control of one of the most simple idea only P control, the current results fed back, and then subtract the target, is positive, then slow down, then it is negative acceleration. Now know that this is just the simplest closed-loop control algorithms.3, the ratio (P), integral (I), differential (D) control algorithms have effect:?????Proportion of the reaction system, the basic (current) deviation e (t), coefficient, can speed up the regulation, reduce errors, but the system is too large proportion decreased stability, or even cause system instability;?????Integral, the cumulative deviation of the reaction system, allowing the system to eliminate the steady state error, no gradient to improve, because there is an error, integral control will be carried out until no error;?????Differential, reflecting the rate of change of the system deviation signal e (t)-e (t-1), is foreseen to anticipate trends deviation generated ahead of the control action, the deviation is not formed, has been the differential regulation of remove, so you can improve the dynamic performance. However, differential interference to noise amplification role in strengthening differential interference detrimental to the system.Integral and differential can not work alone and must be proportional control cooperation.4, the controller of the P, I, D item selection.The following rules will be used to control various control features briefly summarized here: 1, the proportional control law P: P control law used to quickly overcome the disturbances, which act on the output value of the fast, but not very stable at a desired value, compared with a negative result is to effectively overcome the disturbances, but more than a difference appears. It is suitable for the control channel lag is small, little change in the load control is less demanding, controlled parameters within a certain range to allow more than poor occasions. Such as: Jin Biao under the Ministry of Public Works pump house cold, heat pool water level control; pump room intermediate tank oil level control. 2, proportional integral control law (PI): in engineering proportional integral control law is the most widely used control law. Points that can be eliminated on the basis of the proportion of residual error, which applies to the control channel lag is small, little change in load, was charged with parameters do not allow more than a poor occasions. Eg: In the main chamber kiln heavy commutation No. F1419 F1401 to heavy gun flow control system; pump room for the pipeline flow control system; annealing furnace temperature control system, etc. districts. 3, proportional and differential control law (PD): Differential effects has advanced, with capacity for hysteresis control channel, the introduction of differential involved in the control, the derivative term is set properly in the case, for improving the system's dynamic performance indicators, have a significant effect. Therefore, for the time constant of the control channel or capacity lags larger occasions, in order to improve the stability of the system, reducing the dynamic deviation proportional derivative control law can be used. Such as: heated temperature control, composition control. It should be noted that, for those pure lag larger area, the derivative term is powerless, and in the measured signal is noisy or periodic vibration system, you should not use derivative control. Such as: large kiln glass level control. 4, for example, integral derivative control laws (PID): PID control law is an ideal control law, it is based on the introduction of proportional integral, can eliminate residual error, then add the derivative action, but also improve system stability. Itis suitable for the control channel or capacity lag time constant is large, the control requirements of the occasion. Such as temperature control, composition control.????Given D role of the law, we must also understand the concept of time lag, the time lag including capacity lag and pure lag. Capacity in which they lag usually include: measurement and transmission lag lag. Measurement hysteresis is detecting element in the detection need to establish a balance, such as thermocouples, RTD, pressure, etc. resulting from a slow response lag. The transmission lag is in the sensors, transmitters, actuators and other devices produce a control delay. Pure delay is measured relative lag in industry, most of the time delay caused due to material transport, such as: large kiln glass level, feeding maneuver done in the nuclear level gauge detection requires a very long period of time.????In short, the choice of control law according to the process characteristics and process requirements to select, and never say PID control law in any case, has better control performance, regardless of the occasion are used is unwise. If you do so, it will only add complexity to the other work and give parameter tuning difficult. When using PID controller has not yet reached technological requirements, you need to consider other control scheme. If cascade control, feedforward control, large hysteresis control.5the problem. Kp, Ti, Td setting the three parameters of the PID control algorithm key issues. Generally they can only be set when programming the approximate value and the system is running through repeated testing to determine the best value. Therefore, the program must apply for the commissioning phase and memory can be modified at any of these three parameters.6 the parameter self-tuning. In some applications, such as generic instrumentation industry, systems work object is uncertain, different objects have different parameter values, can not set parameters for the user, on the introduction of the concept of self-tuning parameters . Essence is the first time, through the N measurements is looking for a new job object parameters, andremembered as a basis for future work.中文翻译PID控制算法1,PID是一个闭环控制算法。
PID翻译

编程- PID控制PID控制一个比例积分微分控制器(PID控制器)是一种常见的方法控制机器人。
PID理论将帮助你为你的机器人设计一个更好的控制方程。
这里显示的是基本的(一个完整的周期)闭环控制框图:控制系统的一个方面是让机器人驱动器(或其他真正的机器人)做你想做的不受你的控制而自动运行。
传感器(编码器通常是一个执行机构)将确定什么改变,你写的程序定义的最终结果应该是什么,和执行机构的实际变化。
另一个传感器可以感知的环境,给机器人一个人更高层次感觉决定去哪里。
错误 -错误的金额在您的设备没有做正确的事情。
例如,如果你的机器人会3英里每小时,但你想让它去2英里每小时,错误是3英里每小时-2英里每小时1英里每小时。
或假设你的机器人在位于X = 5,但你想让它在x = 7,则误差为2。
控制系统不能做任何事情,如果没有错误 - 想想看,如果你的机器人正在做你想要什么,难道需要控制!比例(P) -比例来看,通常是错误的。
这通常是你想要的机器人前往距离,或者你想要的东西是在一个温度。
机器人是在A位置,但要在B,P项是A - B衍生工具(四) -衍生的长期变化超过设定的时间(T)是错误的。
例如,错误的是C,以前和现在的D,t时刻已经过去了,然后衍生的术语是(CD)/吨。
使用单片机的定时器,以确定通过时间定时器(见教程)。
积分(I) -积分项是累计超过设定的时间(t)期间所作的错误。
例如,你的机器人不断是由一定量的平均水平,所有的时间,我的任期将抓住它。
让在T1说错误是,T2为B,在T3 C.积分项会A/t1 + B/t2 + C/t3。
调整常数(增益) - (,P,I,D)的每学期将需要在您的代码调整了。
有很多东西,这是非常困难的数学模型(地面摩擦,电机电感,质量中心,ducktape一起握着你的机器人,等)有关机器人。
所以往往是更好的,只是建立机器人的时代,实施控制方程,然后调整方程式,直到它正常工作。
只是一个调整常数1猜到的数量多,你每学期。
- 1、下载文档前请自行甄别文档内容的完整性,平台不提供额外的编辑、内容补充、找答案等附加服务。
- 2、"仅部分预览"的文档,不可在线预览部分如存在完整性等问题,可反馈申请退款(可完整预览的文档不适用该条件!)。
- 3、如文档侵犯您的权益,请联系客服反馈,我们会尽快为您处理(人工客服工作时间:9:00-18:30)。
PID controllerA proportional–integral–derivative controller (PID controller) is a generic .control loop feedback mechanism widely used in industrial control systems. A PID controller attempts to correct the error between a measured process variable and a desired setpoint by calculating and then outputting a corrective action that can adjust the process accordingly.The PID controller calculation (algorithm) involves three separate parameters; the Proportional, the Integral and Derivative values. The Proportional value determines the reaction to the current error, the Integral determines the reaction based on the sum of recent errors and the Derivative determines the reaction to the rate at which the error has been changing. The weightedsum of these three actions is used to adjust the process via a control element such as the position of a control valve or the power supply of a heating element. By "tuning" the three constants in the PID controller algorithm the PID can provide control action designed for specific process requirements. The response of the controller can be described in terms of the responsiveness of the controller to an error, the degree to which the controller overshoots the setpoint and the degree of system oscillation. Some applications may require using only one or two modes to provide the appropriate system control. This is achieved by setting the gain of undesired control outputs to zero. A PID controller will be called a PI, PD, P or I controller in the absence of the respective control actions. PI controllers are particularly common, since derivative action is very sensitive to measurement noise, and the absence of an integral value may prevent the system from reaching its target value due to the control action.1.Control loop basicsA familiar example of a control loop is the action taken to keep one's shower water at the ideal temperature, which typically involves the mixing of two process streams, cold and hot water. The person feels the water to estimate its temperature. Based on this measurement they perform a control action: use the cold water tap to adjust the process. The person would repeat this input-output control loop, adjusting the hot water flow until the process temperature stabilized at the desired value.Feeling the water temperature is taking a measurement of the process value or process variable (PV). The desired temperature is called the setpoint (SP). The output from the controller and input to the process (the tap position) is called the manipulated variable (MV). The difference between the measurement and the setpoint is the error (e), too hot or too cold and by how much. As a controller, one decides roughly how much to change the tap position (MV) after one determines the temperature (PV), and therefore the error. This first estimate is the equivalent of the proportional action of a PID controller. The integral action of a PIDcontroller can be thought of as gradually adjusting the temperature when it is almost right. Derivative action can be thought of as noticing the water temperature is getting hotter or colder, and how fast, and taking that into account when deciding how to adjust the tap. Making a change that is too large when the error is small is equivalent to a high gain controller and will lead to overshoot. If the controller were to repeatedly make changes that were too large and repeatedly overshoot the target, this control loop would be termed unstable and the output would oscillate around the setpoint in either a constant, growing, or decaying sinusoid. A human would not do this because we are adaptive controllers, learning from the process history, but PID controllers do not have the ability to learn and must be set up correctly. Selecting the correct gains for effective control is known as tuning the controller.If a controller starts from a stable state at zero error (PV = SP), then further changes by the controller will be in response to changes in other measured or unmeasured inputs to the process that impact on the process, and hence on the PV. Variables that impact on the process other than the MV are known as disturbances and generally controllers are used to reject disturbances and/or implement setpoint changes. Changes in feed water temperature constitute a disturbance to the shower process.In theory, a controller can be used to control any process which has a measurable output (PV), a known ideal value for that output (SP) and an input to the process (MV) that will affect the relevant PV. Controllers are used in industry to regulate temperature, pressure, flow rate, chemical composition, speed and practically every other variable for which a measurement exists. Automobile cruise control is an example of a process which utilizes automated control.Due to their long history, simplicity, well grounded theory and simple setup and maintenance requirements, PID controllers are the controllers of choice for many of these applications.2.PID controller theoryThe PID control scheme is named after its three correcting terms, whose sum constitutes the manipulated variable (MV). Hence:where Pout, Iout, and Dout are the contributions to the output from the PID controller from each of the three terms, as defined below.2.1. Proportional termThe proportional term makes a change to the output that is proportional to the current error value. The proportional response can be adjusted by multiplying the error by a constantKp, called the proportional gain.The proportional term is given by:WherePout: Proportional outputKp: Proportional Gain, a tuning parametere: Error = SP − PVt: Time or instantaneous time (the present)A high proportional gain results in a large change in the output for a given change in the error. If the proportional gain is too high, the system can become unstable (See the section on Loop Tuning). In contrast, a small gain results in a small output response to a large input error, and a less responsive (or sensitive) controller. If the proportional gain is too low, the control action may be too small when responding to system disturbances.In the absence of disturbances, pure proportional control will not settle at its target value, but will retain a steady state error that is a function of the proportional gain and the process gain. Despite the steady-state offset, both tuning theory and industrial practice indicate that it is the proportional term that should contribute the bulk of the output change.2.2.Integral termThe contribution from the integral term is proportional to both the magnitude of the error and the duration of the error. Summing the instantaneous error over time (integrating the error) gives the accumulated offset that should have been corrected previously. The accumulated error is then multiplied by the integral gain and added to the controller output. The magnitude of the contribution of the integral term to the overall control action is determined by the integral gain, Ki.The integral term is given by:Iout: Integral outputKi: Integral Gain, a tuning parametere: Error = SP − PVτ: Time in the past contributing to the integral responseThe integral term (when added to the proportional term) accelerates the movement of the process towards setpoint and eliminates the residual steady-state error that occurs with a proportional only controller. However, since the integral term is responding to accumulatederrors from the past, it can cause the present value to overshoot the setpoint value (cross over the setpoint and then create a deviation in the other direction). For further notes regarding integral gain tuning and controller stability, see the section on loop tuning.2.3 Derivative termThe rate of change of the process error is calculated by determining the slope of the error over time (i.e. its first derivative with respect to time) and multiplying this rate of change by the derivative gain Kd. The magnitude of the contribution of the derivative term to the overall control action is termed the derivative gain, Kd.The derivative term is given by:Dout: Derivative outputKd: Derivative Gain, a tuning parametere: Error = SP − PVt: Time or instantaneous time (the present)The derivative term slows the rate of change of the controller output and this effect is most noticeable close to the controller setpoint. Hence, derivative control is used to reduce the magnitude of the overshoot produced by the integral component and improve the combined controller-process stability. However, differentiation of a signal amplifies noise and thus this term in the controller is highly sensitive to noise in the error term, and can cause a process to become unstable if the noise and the derivative gain are sufficiently large.2.4 SummaryThe output from the three terms, the proportional, the integral and the derivative terms are summed to calculate the output of the PID controller. Defining u(t) as the controller output, the final form of the PID algorithm is:and the tuning parameters areKp: Proportional Gain - Larger Kp typically means faster response since thelarger the error, the larger the Proportional term compensation. An excessively large proportional gain will lead to process instability and oscillation.Ki: Integral Gain - Larger Ki implies steady state errors are eliminated quicker. The trade-off is larger overshoot: any negative error integrated during transient response must be integrated away by positive error before we reach steady state.Kd: Derivative Gain - Larger Kd decreases overshoot, but slows down transient response and may lead to instability due to signal noise amplification in the differentiation of the error.3. Loop tuningIf the PID controller parameters (the gains of the proportional, integral and derivative terms) are chosen incorrectly, the controlled process input can be unstable, i.e. its output diverges, with or without oscillation, and is limited only by saturation or mechanical breakage. Tuning a control loop is the adjustment of its control parameters (gain/proportional band, integral gain/reset, derivative gain/rate) to the optimum values for the desired control response.The optimum behavior on a process change or setpoint change varies depending on the application. Some processes must not allow an overshoot of the process variable beyond the setpoint if, for example, this would be unsafe. Other processes must minimize the energy expended in reaching a new setpoint. Generally, stability of response (the reverse of instability) is required and the process must not oscillate for any combination of process conditions and setpoints. Some processes have a degree of non-linearity and so parameters that work well at full-load conditions don't work when the process is starting up from no-load. This section describes some traditional manual methods for loop tuning.There are several methods for tuning a PID loop. The most effective methods generally involve the development of some form of process model, then choosing P, I, and D based on the dynamic model parameters. Manual tuning methods can be relatively inefficient.The choice of method will depend largely on whether or not the loop can be taken "offline" for tuning, and the response time of the system. If the system can be taken offline, the best tuning method often involves subjecting the system to a step change in input, measuring the output as a function of time, and using this response to determine the control parameters.3.1 Manual tuningIf the system must remain online, one tuning method is to first set the I and D values to zero. Increase the P until the output of the loop oscillates, then the P should be left set to be approximately half of that value for a "quarter amplitude decay" type response. Then increase D until any offset is correct in sufficient time for the process. However, too much D will cause instability. Finally, increase I, if required, until the loop is acceptably quick to reach its reference after a load disturbance. However, too much I will cause excessive response and overshoot. A fast PID loop tuning usually overshoots slightly to reach the setpoint more quickly; however, some systems cannot accept overshoot, in which case an "over-damped" closed-loop system is required, which will require a P setting significantly less than half thatof the P setting causing oscillation.3.2 PID tuning softwareMost modern industrial facilities no longer tune loops using the manual calculation methods shown above. Instead, PID tuning and loop optimization software are used to ensure consistent results. These software packages will gather the data, develop process models, and suggest optimal tuning. Some software packages can even develop tuning by gathering data from reference changes.Mathematical PID loop tuning induces an impulse in the system, and then uses the controlled system's frequency response to design the PID loop values. In loops with response times of several minutes, mathematical loop tuning is recommended, because trial and error can literally take days just to find a stable set of loop values. Optimal values are harder to find. Some digital loop controllers offer a self-tuning feature in which very small setpoint changes are sent to the process, allowing the controller itself to calculate optimal tuning values.4. Limitations of PID controlWhile PID controllers are applicable to many control problems, they can perform poorly in some applications.PID controllers, when used alone, can give poor performance when the PID loop gains must be reduced so that the control system does not overshoot, oscillate or "hunt" about the control setpoint value. The control system performance can be improved by combining the feedback (or closed-loop) control of a PID controller with feed-forward (or open-loop) control. Knowledge about the system (such as the desired acceleration and inertia) can be "fed forward" and combined with the PID output to improve the overall system performance. The feed-forward value alone can often provide the major portion of the controller output. The PID controller can then be used primarily to respond to whatever difference or "error" remains between the setpoint (SP) and the actual value of the process variable (PV). Since the feed-forward output is not affected by the process feedback, it can never cause the control system to oscillate, thus improving the system response and stability.For example, in most motion control systems, in order to accelerate a mechanical load under control, more force or torque is required from the prime mover, motor, or actuator. If a velocity loop PID controller is being used to control the speed of the load and command the force or torque being applied by the prime mover, then it is beneficial to take the instantaneous acceleration desired for the load, scale that value appropriately and add it to the output of the PID velocity loop controller. This means that whenever the load is being accelerated or decelerated, a proportional amount of force is commanded from the prime mover regardless of the feedback value. The PID loop in this situation uses the feedback information to effect any increase or decrease of the combined output in order to reduce theremaining difference between the process setpoint and the feedback value. Working together, the combined open-loop feed-forward controller and closed-loop PID controller can provide a more responsive, stable and reliable control system.Another problem faced with PID controllers is that they are linear. Thus, performance of PID controllers in non-linear systems (such as HV AC systems) is variable. Often PID controllers are enhanced through methods such as PID gain scheduling or fuzzy logic. Further practical application issues can arise from instrumentation connected to the controller. A high enough sampling rate, measurement precision, and measurement accuracy are required to achieve adequate control performance.A problem with the Derivative term is that small amounts of measurement or process noise can cause large amounts of change in the output. It is often helpful to filter the measurements with a low-pass filter in order to remove higher-frequency noise components. However, low-pass filtering and derivative control can cancel each other out, so reducing noise by instrumentation means is a much better choice. Alternatively, the differential band can be turned off in many systems with little loss of control. This is equivalent to using the PID controller as a PI controller.5. Cascade controlOne distinctive advantage of PID controllers is that two PID controllers can be used together to yield better dynamic performance. This is called cascaded PID control. In cascade control there are two PIDs arranged with one PID controlling the set point of another. A PID controller acts as outer loop controller, which controls the primary physical parameter, such as fluid level or velocity. The other controller acts as inner loop controller, which reads the output of outer loop controller as set point, usually controlling a more rapid changing parameter, flowrate or accelleration. It can be mathematically proved that the working frequency of the controller is increased and the time constant of the object is reduced by using cascaded PID controller.[vague]6. Physical implementation of PID controlIn the early history of automatic process control the PID controller was implemented as a mechanical device. These mechanical controllers used a lever, spring and a mass and were often energized by compressed air. These pneumatic controllers were once the industry standard. Electronic analog controllers can be made from a solid-state or tube amplifier, a capacitor and a resistance. Electronic analog PID control loops were often found within more complex electronic systems, for example, the head positioning of a disk drive, the power conditioning of a power supply, or even the movement-detection circuit of a modern seismometer. Nowadays, electronic controllers have largely been replaced by digitalcontrollers implemented with microcontrollers or FPGAs.Most modern PID controllers in industry are implemented in software in programmable logic controllers (PLCs) or as a panel-mounted digital controller. Software implementations have the advantages that they are relatively cheap and are flexible with respect to the implementation of the PID algorithm.PID控制器比例积分微分控制器(PID调节器)是一个控制环,广泛地应用于工业控制系统里的反馈机制。