PC聚碳酸酯的应力开裂
聚碳酸酯(PC)的各种性能及其成型特性(个人总结含图表)

聚碳酸酯(PC)的各种性能及其成型特性(个⼈总结含图表)聚碳酸酯(PC)的性能聚碳酸酯(PC)是⼀种线型碳酸聚酯,分⼦中碳酸基团与另⼀些基团交替排列,这些基团可以是芳⾹族,可以是脂肪族,也可以两者皆有。
双酚A型PC是最重要的⼯业产品。
双酚A型PC是⼀种⽆定形的⼯程塑料,具有良好的韧性、透明性和耐热性。
碳酸酯基团赋予韧性和耐⽤性,双酚A基团赋予⾼的耐热性。
⽽PC的⼀些主要应⽤⾄少同时要求这两种性能。
表2-30列出了通⽤级聚碳酸酯的性能。
表2-30 通⽤级聚碳酸酯的性能⼒学性能聚碳酸酯的缺点是耐疲劳强度较低,耐磨性较差,摩擦因数⼤。
聚碳酸酯制品容易产⽣应⼒开裂,内应⼒产⽣的原因主要是由于强迫取向的⼤分⼦间相互作⽤造成的。
如果将聚碳酸酯的弯曲试样进⾏挠曲并放置⼀定时间,当超过其极限应⼒时便会发⽣微观撕裂。
在⼀定应变下发⽣微观撕裂时间与应⼒之间的关系依赖于聚碳酸酯的平均相对分⼦质量。
如果聚碳酸酯制品在成型加⼯过程中因温度过⾼等原因发⽣分解⽼化,或者制品本⾝存在缺⼝或熔接缝,以及制品在化学⽓体中使⽤,那么,发⽣微观撕裂的时间将会⼤⼤缩短,其极限应⼒值也将⼤幅度下降。
热性能聚碳酸酯的耐热性较好,未填充聚碳酸酯的热变形温度⼤约为130℃,玻璃纤维增强后可使这个数值再增加10℃。
长期使⽤温度可达120℃,同时⼜具有优良的耐寒性,脆化温度为-100℃。
低于100℃时,在负载下的蠕变率很低。
聚碳酸酯没有明显的熔点,在220-230℃呈熔融状态。
由于其分⼦链刚性⼤,所以它的熔体粘度较⾼。
电性能聚碳酸酯由于极性⼩,玻璃化转变温度⾼,吸⽔率低,因此具有优良的电性能。
表2-31列出了通⽤级聚碳酸酯的电性能。
表2-31 通⽤级聚碳酸酯的电性能耐化学药品性能聚碳酸酯对酸性及油类介质稳定,但不耐碱,溶于氯代烃。
PC有较好的耐⽔解性,但长期浸⼊沸⽔中易引起⽔解和开裂,不能应⽤于重复经受⾼压蒸汽的制品。
PC易受某些有机溶剂的侵蚀,虽然它可以耐弱酸、脂肪烃、醇的⽔溶液,但可以溶解在含氯的有机溶剂中。
聚碳酸酯应力开裂分析
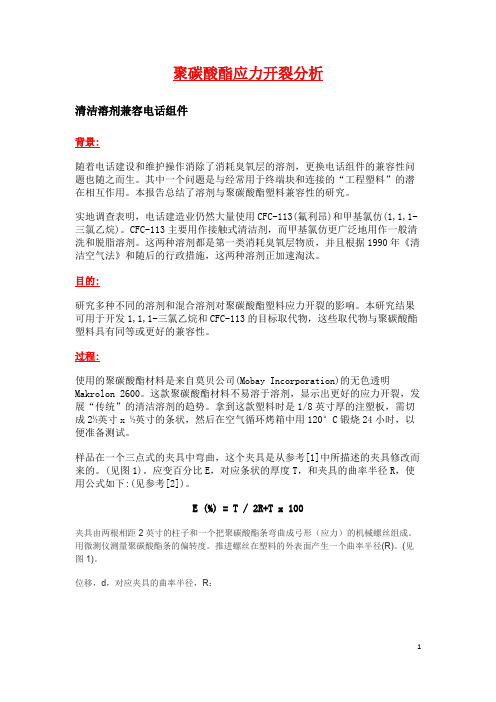
聚碳酸酯应力开裂分析清洁溶剂兼容电话组件背景:随着电话建设和维护操作消除了消耗臭氧层的溶剂,更换电话组件的兼容性问题也随之而生。
其中一个问题是与经常用于终端块和连接的“工程塑料”的潜在相互作用。
本报告总结了溶剂与聚碳酸酯塑料兼容性的研究。
实地调查表明,电话建造业仍然大量使用CFC-113(氟利昂)和甲基氯仿(1,1,1-三氯乙烷)。
CFC-113主要用作接触式清洁剂,而甲基氯仿更广泛地用作一般清洗和脱脂溶剂。
这两种溶剂都是第一类消耗臭氧层物质,并且根据1990年《清洁空气法》和随后的行政措施,这两种溶剂正加速淘汰。
目的:研究多种不同的溶剂和混合溶剂对聚碳酸酯塑料应力开裂的影响。
本研究结果可用于开发1,1,1-三氯乙烷和CFC-113的目标取代物,这些取代物与聚碳酸酯塑料具有同等或更好的兼容性。
过程:使用的聚碳酸酯材料是来自莫贝公司(Mobay Incorporation)的无色透明Makrolon 2600。
这款聚碳酸酯材料不易溶于溶剂,显示出更好的应力开裂,发展“传统”的清洁溶剂的趋势。
拿到这款塑料时是1/8英寸厚的注塑板,需切成2½英寸x ½英寸的条状,然后在空气循环烤箱中用120°C锻烧24小时,以便准备测试。
样品在一个三点式的夹具中弯曲,这个夹具是从参考[1]中所描述的夹具修改而来的。
(见图1)。
应变百分比E,对应条状的厚度T,和夹具的曲率半径R,使用公式如下:(见参考[2])。
E (%) = T / 2R+T x 100夹具由两根相距2英寸的柱子和一个把聚碳酸酯条弯曲成弓形(应力)的机械螺丝组成。
用微测仪测量聚碳酸酯条的偏转度。
推进螺丝在塑料的外表面产生一个曲率半径(R)。
(见图1)。
位移,d,对应夹具的曲率半径,R:图 #1三点式弯曲夹具使聚碳酸酯条形成弓形(应力)不同位移,d的应变计算如下介绍几种不同的方法来评定聚碳酸酯对溶剂的化学抗性,或者反过来说,评定溶剂对聚碳酸酯的作用。
PC聚碳酸酯中空阳光板开裂原因分析

PC中空板是一种质量很好的建筑资料,能够用作隔热、隔音等等。
但是在我们现实使用的时候,会发现PC中空板很轻易发生因为力气过度而开裂的情况,这究竟是怎么回事呢?有甚么办法能够解决呢?
PC中空阳光板会呈现应力开裂的原因主要还是因为PC中空板的原材料的布局和机能决议的。
因为咱们在共挤成型PC中空板时,份子链会自愿取向,而因为聚碳酸酯份子链上又具备苯环,解取向又会变得比较困难。
以是在成型之后,被取向的链照样有能够会回复到原本的状况,然则因为全部份子链曾经被解冻和大份子链之间的互相阁下,从而会使成品存在残留应力,终极形成中空板产物呈现应力开裂的可能性。
然则,这也不是绝对的,因为聚碳酸酯板外部另有许多分歧的力存在,好比抗开裂力。
而份子链的是非、链间的缠结数量、份子敛之间的作用力都是决议这个力大小的症结身分链。
以是咱们只需包管抗开裂才能和内应力到达均衡,PC中空板的开裂征象就不会呈现。
那如何才能使抗开裂才能和内应力到达均衡呢?就是要进步中空板的模具温度,因为模具温度越高,份子链才越轻易活动,从而有利于聚碳酸酯中取向份子的松懈。
颠末实验,中空板模具的最好温度是节制在一百到一百二十度阁下。
可见PC中空板会呈现应力开裂也不是一个完全不能避免的成绩,只需在誉耐PC中空板的制造过程当中,尽量控制几种作用力之间的干系就能够了。
PC制件内应力表征及内应力开裂因素与改善措施分析

ofmoldtemperaturecouldgiveamorethan30 %influenceonthenumbersofstresscrackofPC. ThestresscrackingproblemofPCpartscouldbesolvedeffectivelybyannealingat110 ℃for2h, andmeanwhile,theirstrengthwasnotreducedsignificantly. 犓犲狔狑狅狉犱狊:polycarbonate;internalstress;crack;solventsoaking
冻结导致在某些应用条件下出现应力开裂的问题[1]。
師 師
師 師
熿燀 O 帩 CC HH33 帩 O CO 燄燅狀
(1)
由于 PC制件在实际使用过程中,交变温度、高能
射线、特 定 油 脂、溶 剂 等 等 促 发 应 力 开 裂 的 因 素 很
多[23],这些因素变化的量值及每个因素作用的程度又
针对 PC材料应力开裂问题,国内外很多学者阐述 了银 纹 扩 展、密 度 梯 度 微 区 等 应 力 开 裂 机 理[47],提 供 了恒定应力、恒 定 应 变、溶 剂 法 等 表 征 方 法[810]表 征 内 应力的大小,并从产品的结构设计、用料、注塑工艺、后 处理、使用环 境 等 方 面 提 出 改 善 应 力 开 裂 的 措 施 和 进 行措施有效性探讨 ,本 [23,1112] 文采用溶剂浸泡法进行 应力开裂的 机 理 分 析、内 应 力 表 征 及 改 善 应 力 措 施 的 效果评价。
如何处理聚碳酸酯(PC)环境应力

如何处理聚碳酸酯(PC)环境应力开裂性能的影响聚碳酸酯(PC)产品的应力开裂和解决方案我们在研究一个材料时,应该注意一个问题就是:材料的结构决定材料的性能,材料的性能反映材料的结构。
在成型聚碳酸酯时,分子链被迫取向,但是由于聚碳酸酯分子链上具有苯环,所以解取向比较困难,而在成型后,被取向的链有恢复自然状态的趋势,但是由于整个分子链已经被冻结和大分子链之间的相互左右,从而造成制品存在残留应力,而残余应力的存在,就造成产品可能出现应力开裂,注意,这里说的是可能,为什么是可能呢?这是因为聚碳酸酯内部还存在很多力,而其中比较重要的是:抗开裂力,这个力的大小取决分子链的长短,链间的缠结数目,分子敛之间的作用力。
当抗开裂能力和内应力平衡时,产品不会出现开裂现象,而当抗开裂能力小于内应力时,就会出现:为什么我的产品成型时还好好的,而存放一段时间后就开裂了?难道是上天的魔法?其实不是魔法,而是内应力和抗开裂力作用的结果,好了,我们将这个简单话:分子链上苯环——成型取向——制品成型后出现内应力——当内应力和抗开裂能力平衡——好制品——当内应力大于抗开裂能力——产品开裂。
出现这样的问题,大家都不愿意看见,我们不能一出问题就找供应商麻烦吧,而是找供应商共同解决问题,对,有这样的态度就好了,现在我们共同来探讨如何解决问题,我们先从工艺上去解决吧:首先,我们看看模具温度。
从上面那些难懂的理论我们知道,内应力是因为成型时候分子链被冻结引起的,成型吗,当然是用模具成型的,我想你大概已经想到了,对,模具的温度对冻结和分子链的解取向有很大影响,很明显的吗,模具温度越高,分子链肯定容易运动吗,就如同水分子在100度时会“飞”的道理(烧开水的气泡吗,经常做家务哦),所以,提高模具温度,不仅对冲模有利,并且课题调整制品冷却速度,使其变得更均匀,从而有利于聚碳酸酯中取向分子的松弛,也就是解取向。
说了半天,到底模具的温度在多少合适呢?不要着急,模具温度假如能控制,在100—120度是成型聚碳酸酯的最佳温度了。
pc的应力应变曲线

pc的应力应变曲线
PC(聚碳酸酯)的应力应变曲线可分为三个阶段:
1. 弹性阶段:在应变小的情况下,PC材料呈现线性弹性行为,应力随应变的增加而线性增加。
此阶段下的应力应变曲线是一条直线。
2. 屈服阶段:当应变达到一定程度时,PC材料进入屈服阶段。
此时应变增加造成的应力增加逐渐变缓,PC材料开始发生塑
性变形。
在此阶段,应力应变曲线呈现出曲线的特征,即曲线开始出现弯曲。
3. 断裂阶段:当应变超过屈服应变极限时,PC材料进入断裂
阶段,应力急剧减小并最终导致断裂。
在这个阶段下,应力应变曲线急剧下降并最终截断。
需要注意的是,PC材料的应力应变曲线受到多种因素的影响,如温度、加载速率等,不同条件下的曲线形状可能会有所不同。
此外,PC材料也具有较高的强度和刚性,具有良好的抗冲击
性能,这使其在许多应用领域中得以广泛应用。
聚碳酸酯耐环境应力开裂性能的研究
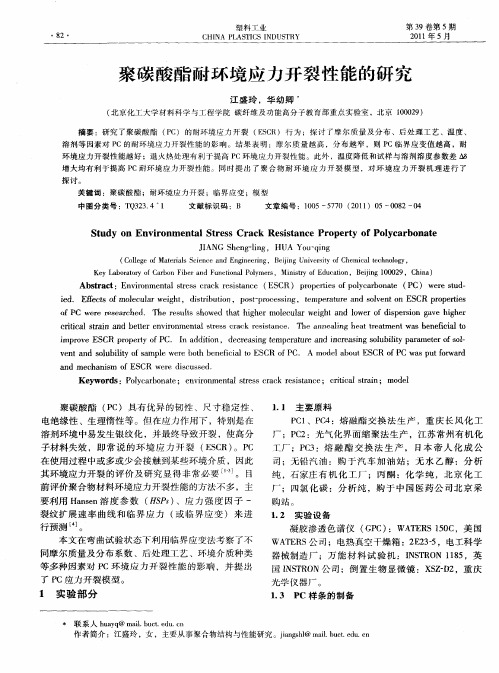
区域 ,从 而形 成微 区 。在 拉 伸作用 力 下 ,一些 微 区连
接处 的薄 弱 点 趋 于 发 生 破 坏 ,从 而 形 成 微 裂 纹 或 银
纹 ,如 图 2 。在 环 境 介 质 中 ,银 纹 的存 在 将 使 材 料 a
与介 质接 触 表面 积大 幅度 增加 ,同时 由于 微 区连接 界 面 的破坏 ,使 得介 质 可 以进一 步渗 人 材料 内部 。 当裂
Abta t E vrn e t t s rc eia c ( S R) poet so p l a oae ( C) w r u — s c : n i m na s escakrs t e E C r o l r sn rp re f oy r n t P i cb ees d t
l d Efe t fmo e ua ih , d srbui n, p s r c s i g, tmp r t r n ov nto CR r p ris e. f cs o l c l rwe g t iti t o o tp o e sn e e a u e a d s l e n ES p o e te
聚碳酸 酯 ( C)具有 优异 的 韧性 、尺 寸稳 定性 、 P
1 1 主 要原料 .
电绝缘 性 、生理惰 性等 。但 在应力 作用 下 ,特 别是 在 溶 剂环 境 中易发生 银纹化 ,并 最终 导致 开裂 ,使 高分 子材 料失 效 ,即 常 说 的环 境 应 力 开 裂 ( S R) C E C 。P 在使 用过 程 中或 多或 少会 接触 到某些 环境介 质 ,因此 其环境 应力 开裂 的评 价及 研 究显 得 非 常必 要 ¨ ] 目 。 前评价 聚合 物材料 环境 应力 开裂 性能 的方法不 多 ,主 要 利用 Hasn溶 度 参 数 ( S s 、应 力 强 度 因子 ~ ne HP) 裂 纹扩 展 速 率 曲线 和 临界 应 力 ( 临界 应 变 )来 进 或
pc 应力开裂测试标准

pc 应力开裂测试标准应力开裂是塑料制品在特定环境条件下因内部应力导致的裂纹形成。
为了确保塑料制品的质量和耐用性,进行应力开裂测试是至关重要的。
以下是PC(聚碳酸酯)应力开裂测试的标准程序和建议。
一、测试前的准备1.样品准备:选择符合要求的PC塑料制品作为测试样品,确保其形状、尺寸和厚度都符合测试标准。
2.环境条件:测试应在恒温恒湿的环境中进行,以确保测试结果的准确性。
通常建议的温度为23℃±2℃,相对湿度为50%±5%。
3.测试设备:准备用于测试的设备和工具,如拉力试验机、显微镜、计时器等。
二、测试步骤1.预处理:将样品置于测试环境中至少24小时,以确保其适应测试环境。
2.施加应力:使用拉力试验机对样品施加一定的拉伸应力,拉伸速度应控制在规定的范围内,通常为50mm/min。
3.观察与记录:在施加应力的过程中,使用显微镜观察样品的表面变化。
一旦发现裂纹,应立即停止施加应力并记录裂纹的位置、长度和宽度。
4.结果判定:根据裂纹的情况判定测试结果。
如果没有裂纹出现,则判定为合格;如果出现裂纹,则判定为不合格。
三、影响因素与注意事项1.温度:温度是影响应力开裂的重要因素。
在高温下,PC材料的分子链运动加剧,容易导致裂纹的产生。
因此,在测试过程中应严格控制温度。
2.湿度:湿度对应力开裂也有一定影响。
高湿度环境下,水分容易渗透到材料内部,增加分子链间的距离,降低材料的强度,从而导致裂纹的产生。
因此,测试时应保持适当的湿度。
3.应力速率:应力速率对应力开裂的影响也很大。
如果应力速率过快,材料来不及发生塑性变形就可能导致裂纹的产生。
因此,在测试过程中应控制应力的施加速度。
4.样品厚度:样品的厚度也会影响测试结果。
厚度较大的样品在受到相同应力时,其内部的应力分布可能不均匀,容易导致裂纹的产生。
因此,在选择测试样品时应注意其厚度。
总结来说,PC应力开裂测试标准需要严格控制测试条件、设备以及操作步骤等多个方面。
- 1、下载文档前请自行甄别文档内容的完整性,平台不提供额外的编辑、内容补充、找答案等附加服务。
- 2、"仅部分预览"的文档,不可在线预览部分如存在完整性等问题,可反馈申请退款(可完整预览的文档不适用该条件!)。
- 3、如文档侵犯您的权益,请联系客服反馈,我们会尽快为您处理(人工客服工作时间:9:00-18:30)。
PC聚碳酸酯的应力开裂塑料内应力是指在塑料熔融加工过程中由于受到大分子链的取向和冷却收缩等因素而响而产生的一种内在应力。
内应力的实质为大分子链在熔融加工过程中形成的不平衡构象,这种不平衡构象在冷却固化时不能立即恢复到与环境条件相适应的平衡构象,这种不平衡构象的实质为一种可逆的高弹形变,而冻结的高弹形变平时以位能形式贮存在塑料制品中,在适宜的条件下,这种被迫的不稳定的构象将向自由的稳定的构象转化,位能转变为动能而释放。
当大分子链间的作用力和相互缠结力承受不住这种动能时,内应力平衡即遭到破坏,塑料制品就会产生应力开裂及翘曲变形等现象。
几乎所有塑料制品都会不同程度地存在内应力,尤其是塑料注射制品的内应力更为明显。
内应力的存在不仅使塑料制品在贮存和使用过程中出现翘曲变形和开裂,也影响塑料制品的力学性能、光学性能、电学性能及外观质量。
为此,必须找出内应力产生的原因及消除内应力的办法,最大程度地降低塑料制品内部的应力,并使残余内应力在塑料制品上尽可能均匀地分布,避免产生应力集中现象,从而改善塑料制品的力学1热学等性能。
产生内应力的原因有很多,如塑料熔体在加工过程中受到较强的剪切作用,加工中存在的取向与结晶作用,熔体各部位冷却速度极难做到均匀一致,熔体塑化不均匀,制品脱模困难等,都会引发内应力的产生。
依引起内应力的原因不同,可将内应力分成如下几类。
(1)取向内应力取向内应力是塑料熔体在流动充模和保压补料过程中,大分子链沿流动方向排列定向构象被冻结而产生的一种内应力。
取向应力产生的具体过程为:*近流道壁的熔体因冷却速度快而造成外层熔体粘度增高,从一而使熔体在型腔中心层流速远高于表层流速,导致熔体内部层与层之间受到剪切应力作用,产生沿流动方向的取向。
取向的大分子链冻结在塑料制品内也就意味着其中存在未松弛的可逆高弹形变,所以说取向应力就是大分子链从取向构象力图过渡到无取向构象的内力。
用热处理的方法,可降低或消除塑料制品内的取向应力。
塑料制品的取向内应力分布为从制品的表层到内层越来越小,并呈抛物线变化。
(2)冷却内应力冷却内应力是塑料制品在熔融加工过程中因冷却定型时收缩不均匀而产生的一种内应力。
尤其是对厚壁塑料制品,塑料制品的外层首先冷却凝固收缩,其内层可能还是热熔体,这徉芯层就会限制表层的收缩,导致芯层处于压应力状态,而表层处于拉应力状态。
塑料制品冷却内应力的分布为从制品的表层到内层越来越大,并也呈抛物线变化.。
另外,带金属嵌件的塑料制品,由于金属与塑料的热胀系数相差较大,容易形成收缩不一均匀的内应力。
除上述两种主要内应力外,还有以下几种内应力:对于结晶塑料制品而言,其制品内部各部位的结晶结构和结晶度不同也会产生内应力。
另外还有构型内应.力及脱模内应力等,只是其内应力听占比重都很小。
(1)分子链的刚性分子链刚性越大,熔体粘度越高,聚合物分子链活动性差,因而对于发生的可逆高弹形变恢复性差,易产生残余内应力口例如,一些分子链中含有苯环的聚合物,如PC、PPO、PPS等,其相应制品的内应力偏大。
(2)分子链的极性一分子链的极性越大,分子间相互吸引的作用力越大,从而使分子间相互移动困难增大,恢复可逆弹性形变的程度减小,导致残余内应力大。
例如,一些分子链中含有羰基、酯基、睛基等极性基团的塑料品种,其相应制品的内应力较大。
(3)取代基团的位阻效应大分子侧基取代基团的体积越大,则妨碍大分子链自由运动导致残余内应力加大。
例如,聚苯乙烯取代基团的苯基体积较大,因而聚苯乙烯制品的内应力较大。
几种常见聚合物的内应力大小顺序如下(1)原料配方设计1)选取分子量大、分子量分布窄的树脂聚合物分子量越大,大分子链间作用力和缠结程度增加,其制品抗应力开裂能力较强;聚合物分子量分布越宽,其中低分子量成分越大,容易首先形成微观撕裂,造成应力集中,便制品开裂。
2)选取杂质含量低的树脂聚合物内的杂质即是应力的集中体,又会降低塑料的原有强度,应将杂质含量减少到最低程度。
3)共混改性易出现应力开裂的树脂与适宜的其它树脂共混,可降低内应力的存在程度。
例如,在PC中混入适量PS,PS呈近似珠粒状分散于PC连续相中,可使内应力沿球面分散缓解并阻止裂纹扩展,从而达到降低内应力的目的。
再如,在PC中混入适量PE , PE球粒外沿可形成封闭的空化区,也可适当降低内应力。
4)增强改性用增强纤维进行增强改性,可以降低制品的内应力,这是因为纤维缠结了很多大分子链,从而提高应力开裂能力。
例如,30%GFPC的耐应力开裂能力比纯PC提高6倍之多。
5)成核改性在结晶性塑料中加入适宜的成核剂,可以在其制品中形成许多小的球晶,使内应力降低并得到分散。
(2)成型加工条件的控制(2)成型加工条件的控制在塑料制品的成型过程中,凡是能减小制品中聚合物分子取向的成型因素都能够降低取向应力;凡是能使制品中聚合物均匀冷却的工艺条件都能降低冷却内应力;凡有助于塑料制品脱模的加工方法都有利于降低脱模内应力。
对内应力影响较大的加工条件主要有如下几种。
①料筒温度较高的料筒温度有利于取向应力的降低,这是因为在较高的料筒温度,熔体塑化均匀,粘度下降,流动性增加,在熔体充满型腔过程中,分子取向作用小,因而取向应力较小。
而在较低料筒温度下,熔体粘度较高,充模过程中分子取向较多,冷却定型后残余内应力则较大。
但是,料筒温度太高也不好,太高容易造成冷却不充分,脱模时易造成变形,虽然取向应力减小,但冷却应力和脱模应力反而增大。
②模具温度模具温度的高低对取向内应力和冷却内应力的影响都很大。
一方面,模具温度过低,会造成冷却加快,易使冷却不均匀而引起收缩上的较大差异,从而增大冷却内应力;另一方面,模具温度过低,熔体进入模其后,温度下降加快,熔体粘度增加迅速,造成在高粘度下充模,形成取向应力的程度明显加大。
模温对塑料结晶影响很大,模温越高,越有利于晶粒堆砌紧密,晶体内部的缺陷减小或消除,从而减少内应力。
另外,对于不同厚度塑料制品,其模温要求不同。
对于厚壁制品其模温要适当高一些。
以PC为例,其内应力大小与模具温度的关系如表5-5所示。
③注射压力注射压力高,熔体充模过程中所受剪切作用力大,产生取向应力的机会也较大。
因此,为了降低取向应力和消除脱模应力,应适当降低注射压力。
.以PC为例,其内应力大小与注射压力的关系如表5-6所示。
.④保压压力保压压力对塑料制品内应力的影响大于注射压力的影响。
在保压阶段,随着熔体温度的降低,熔体粘度迅速增加,此时若施以高压,必然导致分子链的强迫取向,从而形成更大的取向应力。
⑤注射速度注射速度越快,越容易造成分子链的取向程度增加,从而引起更大的取向应力。
但注射速度过低,塑料熔体进入模腔后,可能先后分层而形成熔化痕,产生应力集中线,易产生应力开裂。
所以注射速度以适中为宜。
最好采用变速注射,在速度逐渐减小下结束充模。
⑥保压时间保压时间越长,会增大塑料熔体的剪切作用,从而产生更大的弹性形变,冻结更多的取向应力。
所以,取向应力随保压时间延长和补料量增加而显著增大。
⑦开模残余压力应适当调整注射压力和保压时间,使开模时模内的残余压力接近于大气压力,从而避免产生更大的脱模内应力。
(3)塑料制品的热处理塑料制品的热处理是指将成型制品在一定温度下停留一段时间而消除内应力的方法。
热处理是消除塑料制品内取向应力的最好方法。
对于高聚物分子链的刚性较大、玻璃化温度较高的注塑件;对壁厚较大和带金属嵌件的制件;对使用温度范围较宽和尺寸精度要求较高的制件;时内应力较大而又不易自消的制件以及经过机械加工的制件都必须进行热处理。
对制件进行热处理,可以使高聚物分子由不平衡构象向平衡构象转变,使强迫冻结的处于不稳定的高弹形变获得能量而进行热松弛,从而降低或基本消除内应力。
常采用的热处理温度高于制件使用温度10~20℃或低于热变形温度5~10℃。
热处理时间取决于塑料种类、制件厚度、热处理温度和注塑条件。
一般厚度的制件,热处理1~2小时即可,随着制件厚度增大,热处理时间应适当延长。
提高热处理温度和延长热处理时间具有相似的效果,但温度的效果更明显些。
热处理方法是将制件放入水、甘油、矿物油、乙二醇和液体石蜡等液体介质中,或放入空气循环烘箱中加热到指定温度,并在该温度下停留一定时间,然后缓慢冷却到室温。
实验表明,脱模后的制件立即进行热处理,对降低内应力、改善制件性能的效果更明显。
此外,提高模具温度,延长制件在模内冷却时间,脱模后进行保温处理都有类似热处理的作用。
尽管热处理是降低制件内应力的有效办法之一,但热处理通常只能将内应力降低到制件使用条件允许的范围,很难完全消除内应力。
对PC制件进行较长时间的热处理时,PC分子链有可能进行有序的重排,甚至结晶,从而降低冲击韧性,使缺口冲击强度降低。
因而,不应把热处理作为降低制件内应力的唯一措施。
塑料制品的形状和尺寸在具体设计塑料制品时,为了有效地分散内应力,应遵循这样的原则:制品外形应尽可能保持连续性,避免锐角、直角、缺口及突然扩大或缩小。
对于塑料制品的边缘处应设计成圆角,其中内圆角半径应大于相邻两壁中薄者厚度的70%以上;外圆角半径则根据制品形状而确定。
对于壁厚相差较大的部位,因冷却速度不同,易产生冷却内应力及取向内应力。
因此,应设计成壁厚尽可能均匀的制件,如必须壁厚不均匀,则要进行壁厚差异的渐变过渡。
②合理设计金属嵌件塑料与金属的热膨胀系数相差5~10倍,因而带金属嵌件的塑料制品在冷却时,两者形成的收缩程度不同,因塑料的收缩比较大而紧紧抱住金属嵌件,在嵌件周围的塑料内层受压应力,而外层受拉应力作用,产生应力集中现象。
在具体设汁嵌件时,应注意如下几点,以帮助减小或消除内应力。
a.尽可能选择塑料件作为嵌件。
b.尽可能选择与塑料热膨胀系数相差小的金属材料做嵌件材料,如铝、铝合金及铜等。
c.在金属嵌件上涂覆一层橡胶或聚氨酯弹性缓冲层,并保证成型时涂覆层不熔化,可降低两者收缩差。
d.对金属嵌件进行表面脱脂化处理,可以防止油脂加速制品的应力开裂。
e.金属嵌件进行适当的预热处理。
f.金属嵌件周围塑料的厚度要充足。
例如,嵌件外径为D,嵌件周围塑料厚度为h,则对铝嵌件塑料厚度h≥0.8D;对于铜嵌件,塑料厚度h≥0.9 D。
g.金属嵌件应设计成圆滑形状,最好带精致的滚花纹。
③塑料制品上孔的设计塑料制品上孔的形状、孔数及孔的位置都会对内应力集中程度产生很大的影响。
为避免应力开裂,切忌在塑料制品上开设棱形、矩形、方形或多边形孔。
应尽可能开设圆形孔,其中椭圆形孔的效果最好,并应使椭圆形孔的长轴平行于外力作用方向。
如开设圆孔,可增开等直径的工艺圆孔,并使相邻两圆孔的中心连接线平行于外力作用方向,这样可以取得与椭圆孔相似的效果;还有一种方法,即在圆孔周围开设对称的槽孔,以分散内应力。