铸造车间砂处理工部的通风除尘
铸造车间通风工程节能措施
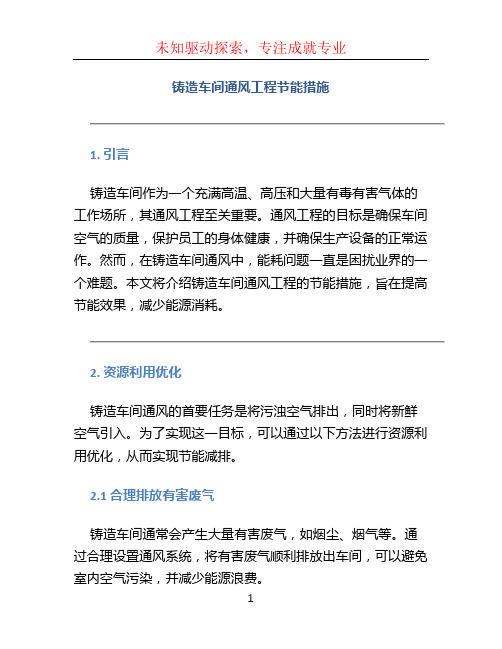
铸造车间通风工程节能措施1. 引言铸造车间作为一个充满高温、高压和大量有毒有害气体的工作场所,其通风工程至关重要。
通风工程的目标是确保车间空气的质量,保护员工的身体健康,并确保生产设备的正常运作。
然而,在铸造车间通风中,能耗问题一直是困扰业界的一个难题。
本文将介绍铸造车间通风工程的节能措施,旨在提高节能效果,减少能源消耗。
2. 资源利用优化铸造车间通风的首要任务是将污浊空气排出,同时将新鲜空气引入。
为了实现这一目标,可以通过以下方法进行资源利用优化,从而实现节能减排。
2.1 合理排放有害废气铸造车间通常会产生大量有害废气,如烟尘、烟气等。
通过合理设置通风系统,将有害废气顺利排放出车间,可以避免室内空气污染,并减少能源浪费。
2.2循环利用余热在铸造车间通风排气中,会伴随着大量的热量的流失。
通过采用余热回收技术,可以将排出的废气中的热能重新回收利用,供车间其他需要热能的装置使用,以实现能源的最大化利用。
2.3 控制通风系统运行时间根据车间的使用情况,合理控制通风系统的运行时间,不仅可以减少用电量,还可以延长通风设备的使用寿命。
可以通过安装定时或传感器控制装置,根据实时的空气质量情况对通风系统进行智能化的控制。
3. 设备优化改造为了实现铸造车间通风工程的节能目标,可以对设备进行优化改造,以提高设备的能效比,从而节约能源消耗。
3.1 更换高效通风设备采用高效的通风设备可以有效地提高通风效率,减少能源消耗。
与传统的通风设备相比,高效通风设备具有更高的风量、更低的能耗以及更好的控制性能。
因此,及时更换老旧的通风设备,采用高效新型设备,是提高通风工程能效的重要手段。
3.2 优化通风系统布局合理的通风系统布局有助于减少风阻损失和能源浪费。
可以通过将通风设备安装在恰当的位置,采用合理的管道布局,减少管道阻力,提高通风效果。
3.3 使用变频控制器通过安装变频控制器,可以根据车间实际需求调整通风设备的运行速度,实现能量的动态调节。
铸造厂除尘方案

铸造厂除尘方案引言铸造厂作为重工业生产的重要环节,其生产过程中会产生大量的粉尘和废气,对环境造成严重污染。
为了保护环境、改善员工的工作环境,铸造厂需要采取有效的除尘方案。
本文将从以下几个方面探讨铸造厂除尘方案的设计和实施。
除尘需求分析铸造厂的除尘需求主要包括两方面:一是对产生的粉尘进行有效的收集和处理,以防止粉尘对环境和人体健康的危害;二是对废气进行治理,以减少对大气环境的污染。
除尘方案需要考虑以下几个因素:1. 铸造工艺特点不同的铸造工艺会产生不同的粉尘和废气,因此除尘方案需要根据具体的工艺特点进行设计。
例如,砂型铸造和金属型铸造产生的粉尘成分和浓度可能会有所不同,因此采取的除尘设备和处理方法也会有所差异。
2. 除尘效果要求除尘效果是评价除尘方案好坏的重要指标之一。
根据国家相关标准和环保要求,对粉尘和废气的排放浓度有明确的要求。
除尘方案需要确保达到相关标准,以保证环境和人体健康的安全。
3. 经济可行性除尘方案的实施需要投入大量的人力、物力和财力。
因此,除尘方案的设计和选择需要考虑经济可行性,综合考虑除尘设备的价格、运行成本和维护费用等因素,以确保除尘方案的可持续发展。
除尘方案设计根据以上需求分析,我们可以设计以下的铸造厂除尘方案:1. 粉尘收集针对铸造工艺产生的粉尘,可以采用以下几种方式进行收集:•机械收尘:通过设置风机和管道系统,将产生的粉尘经过引风装置吸入到集尘器中进行过滤和收集。
常见的集尘器包括布袋除尘器、湿式除尘器等。
•水雾除尘:通过喷雾系统将水雾喷洒到产生粉尘的区域,使粉尘与水雾结合后沉降下来。
这种方法适用于一些无法通过机械收尘处理的粉尘。
2. 废气治理针对铸造工艺产生的废气,可以采用以下几种方式进行治理:•烟气净化:通过设置烟气净化设备,如除尘器、脱硫装置、脱硝装置等,对废气进行净化处理,去除其中的颗粒物、二氧化硫、氮氧化物等有害物质。
•排放控制:合理设计和布置生产设备,通过有效的通风系统和排风罩,将废气排放到合适的位置,避免对周围环境和人体健康造成危害。
铸造厂房通风及粉尘治理方案
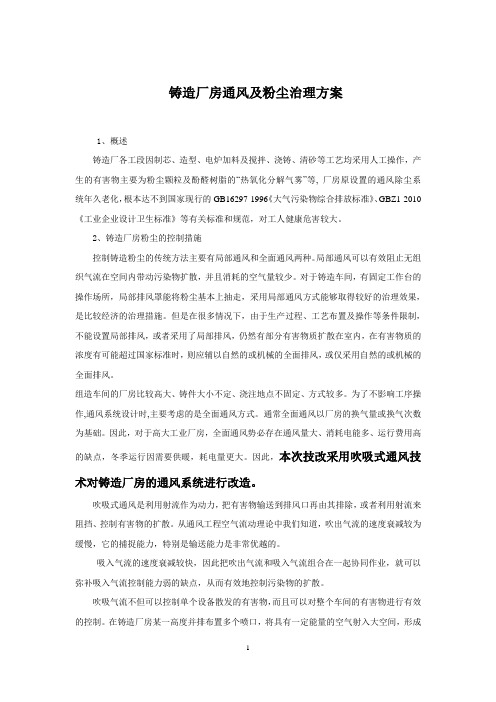
铸造厂房通风及粉尘治理方案1、概述铸造厂各工段因制芯、造型、电炉加料及搅拌、浇铸、清砂等工艺均采用人工操作,产生的有害物主要为粉尘颗粒及酚醛树脂的“热氧化分解气雾”等, 厂房原设置的通风除尘系统年久老化,根本达不到国家现行的GB16297-1996《大气污染物综合排放标准》、GBZ1-2010《工业企业设计卫生标准》等有关标准和规范,对工人健康危害较大。
2、铸造厂房粉尘的控制措施控制铸造粉尘的传统方法主要有局部通风和全面通风两种。
局部通风可以有效阻止无组织气流在空间内带动污染物扩散,并且消耗的空气量较少。
对于铸造车间,有固定工作台的操作场所,局部排风罩能将粉尘基本上抽走,采用局部通风方式能够取得较好的治理效果,是比较经济的治理措施。
但是在很多情况下,由于生产过程、工艺布置及操作等条件限制,不能设置局部排风,或者采用了局部排风,仍然有部分有害物质扩散在室内,在有害物质的浓度有可能超过国家标准时,则应辅以自然的或机械的全面排风,或仅采用自然的或机械的全面排风。
组造车间的厂房比较高大、铸件大小不定、浇注地点不固定、方式较多。
为了不影响工序操作,通风系统设计时,主要考虑的是全面通风方式。
通常全面通风以厂房的换气量或换气次数为基础。
因此,对于高大工业厂房,全面通风势必存在通风量大、消耗电能多、运行费用高的缺点,冬季运行因需要供暖,耗电量更大。
因此,本次技改采用吹吸式通风技术对铸造厂房的通风系统进行改造。
吹吸式通风是利用射流作为动力,把有害物输送到排风口再由其排除,或者利用射流来阻挡、控制有害物的扩散。
从通风工程空气流动理论中我们知道,吹出气流的速度衰减较为缓慢,它的捕捉能力,特别是输送能力是非常优越的。
吸入气流的速度衰减较快,因此把吹出气流和吸入气流组合在一起协同作业,就可以弥补吸入气流控制能力弱的缺点,从而有效地控制污染物的扩散。
吹吸气流不但可以控制单个设备散发的有害物,而且可以对整个车间的有害物进行有效的控制。
铸造除尘(精)

一、砂处理系统除尘该工段工序复杂,物料输送量大,工艺设备多,跨越面积大,故扬尘点造成的危害也大,是铸造车间粉尘治理的重点.因此在结合机械化物料输送的技术改造中,设计配置了一台150m布袋除尘器,风机为4—72一U,8C风机,电机配JO72—2,22kW,该设施风量范围为17920m/h一31000m/h,风压2.52kPa—1.88kPa.主风管为4,680rain,再分上下两路,上风路主风管为20IIlIII和85ITlln,分两支路,一支路主管为00rain蝶阀,当不需要经直线振动筛时,关闭此阀门.另一支路主管为20mm,分至五处犁式卸料器处,此主管采用渐缩式,在每一渐缩处分一支管,其管径为4,200rain,同时配4,200rain蝶阀,用以调节和关闭不启用,卸料处的风量损失.渐缩管为20一70一20一50—4,200(mm).下风路主风管为4,380mm,再分两支路,一路至提升机下部,风管直径为50mm;另一支路主管85mm通至储砂斗下,密封皮带输送机的两处扬尘点风管直径皆为4,200rain配2—4,200mm蝶阀,皮带不运转时关闭两处碟阀以调节风量此除尘经应用理想,不但制止了粉尘外逸,在旧砂回送过程中,将旧砂中的灰分大量吸出,使得型砂质量得以提高.二、落砂机除尘落砂机选用L128惯性冲击式落砂机,传统落砂方式为行车吊运不脱钩落砂,由于落砂机所处位置在车间内的中部,基本上无横向气流,因而采用侧吸罩吸尘方式,这样可不影响工艺操作.为此选用300m袋式除尘器,风机为4—72—1l,10C风机,电机JO2—82—4,40kW,风量范围34800m /h一50150m/h,风压2.39kPa一1.90kPa.主吸风管00mm至侧吸罩,同时分一支路至落砂机下部至皮带输送机的卸料扬尘点.在生产现场,基本上控制住了由于激烈振动、撞击、空气扰动以及高温铸件产生的热上升气流和带尘水汽.三、木型工部除尘系统此工部机械设备集中间隔于厂房一侧,设备现有两台木型车床,截锯一台,圆锯一台,一台压刨和大小平刨各一台.除尘系统设计采用一台XM一6型木工旋风除尘器.配套风机采用排尘离心通风机和lOkW电机,风机前置,将吸人的木屑粉尘排入旋风除尘器再落人封闭的小屋内,吸尘管路主管后分两支路采用集合管形式再分多个小吸口,吸口用蛇皮软管联接至各个设备扬尘点,控制粉尘的外逸.该厂铸造车间的粉尘治理主要抓住了这九处进行治理,其余的粉尘如干型合型前的粉尘和浇注时产生的烟气,由于无法定点而采用加强文明生产管理来减少粉尘的外逸.治理后经市级环保部门检测数据如下;(单位为ms/m)大件造型地段3.0;中部造型1.8;北部小件1.6;混妙机1.4;冲天炉1.5;对芯2.0;清铲15;砂轮机处2.0抛丸滚筒1.5.除大件造型因采用干型造型烘型后的修型合箱过程还有粉尘飞逸超标外,基本上都达到了***规定的标准范围.控制和治理粉尘污染应从工艺改革着手.实现机械化.自动化.密闭化.并配备一定的通风除尘设备.这是最有效的途径.该厂结合铸造车间技术改造的过程中,通过自行设计分段实施,在提出铸造机械化的过程中同步解决了铸造车间的粉尘污染.尤其砂处理工部的粉尘治理,还使得旧砂中所含的灰分得以有效地排出,一举两得,使产品质量相应提高.同时企业的安全生产、劳动保护质量也有了保障.但是相对而言,粉尘治理一次性投入较大,经济效益回报率不显著,应用后的设备保养维护投入也增大,在面临市场经济的大气候环境中,应加强环保意识及法制教育,使上下一致提高此项意识,否则便会导致即使上了的环保项目,如不及时投资进行维护保养,也将使其成为废物,发挥不了应有的作用,这是应当引起高度重视的。
铸造生产中粉尘危害及防尘技术措施

铸造生产中粉尘危害及防尘技术措施参考资料:中国环保网(/trade/supply/index--1000100610011004--.htm)小编导读:本文主要介绍铸造生产中粉尘的危害,铸造生产公益,最后是一些铸造相关的防尘技术措施。
一、粉尘危害铸造生产过程中,在型砂配制、造型、打箱、清砂和砂轮加工等过程中,均可产生粉尘。
由于铸件品种和砂型的制造方法不同,型砂的成分也不一样。
一般型砂粉尘中游离二氧化硅含量约为20%一30%,有的高达70%左右。
产生粉尘的设备有碾砂机、筛砂机、拌砂机、皮带输送机、电弧炉、冲天炉、落砂机、喷抛丸机。
我国铸造工厂(车间)除少数重点企业外,多数工艺操作及装备都比较落后,仍为手工造型,就地浇注,清砂机械化程度低,工人劳动强度大。
据有关资料介绍,每熔炼一吨铁水,散发粉尘6一15kg;在非熔炼的工艺过程中,每生产一吨铸件,散发粉尘约50k8。
1978年的一份调查报告中指出,全国300个铸造车间,作业地点的粉尘浓度基本上不能达到国家卫生标准。
全国农机重点企业的3874个作业点,有80%超过国家卫生标准。
由于铸造生产中粉尘浓度高,粉尘含硅量大,因此铸造工人的矽肺病发病情况比较严重。
二、铸造生产工艺铸造生产的主要工序如下。
(一)造型配砂。
即将砂、粘土或黄土、焦炭粉、煤粉等物料,经碾碎、过筛混料后制成型砂。
(二)造型。
首先根据铸件的规格要求,做好一定形状的木模,然后用型砂在砂箱内或地上制成砂型。
(三)溶化。
将铁块及硒土、焦炭等材料送入冲天炉内溶化成铁水。
(四)浇铸。
将熔融的金属浇入砂型中。
(五)订箱。
砂箱冷却后,用人工或机械的方法,从砂型中打出铸件。
(六)清砂。
用振动、铁棒、手凿、风铲等工具把铸件上的毛刺和砂土清除掉。
(七)旧砂回用。
清砂后的旧砂经过一定处理后仍可回到混砂机中与新砂混合使用。
三、防尘技术(一)工艺措施l。
固定作业工位应处于车间内通风良好和空气相对洁净的地方。
2.污染大与污染小的作业点要分开布局。
铸造通风除尘

a. 炉外排烟: 上部对开式伞形罩——小于或等于5t电弧炉。 炉盖排烟罩——小于或等于10t电弧炉。 钳形排烟罩——小于或等于10t电弧炉。 电极环形罩——小于或等于5t电弧炉。 吹吸罩——小于或等于5t电弧炉。 以上排烟方式适用于炉盖上无加料孔的电弧炉,炉门均应设排风 罩。 大密闭罩、移动式密闭罩--要求冶炼全过程均能控制烟尘、环境要 求严格、机械化自动化程序较高的电弧炉。 b. 炉内排烟: 脱开式炉内排烟——大于或等于10t电弧炉。 c. 炉内处结合排烟——大于或等于10t电弧炉。 d. 屋顶排烟--要求治炼全过程均能控制烟尘,并且环境要求高的 电弧炉。宜与炉内或炉内外排烟方式结合采用。 3.1.1.3 通风除尘系统的设计参数应按冶炼氧化期最大烟气量考 虑。排风量宜按不同冶炼期进行调整,可采取节电的变风量措施。 3.1.1.4 炉处排烟方式的通风除尘系统。当烟气温度低于135℃时, 可不设冷却装置。但采用炉盖排烟罩时,应采用水冷罩或耐热钢罩。 3.1.1.5 炉内排烟方式的通风除尘系统,应设冷却装置(水冷炉顶排 烟管、水冷风管、风冷风管或其他冷却器等)。有条件时,可考虑余热 利用。 3.1.1.6 电弧炉的烟气净化设备宜采用干式高效除尘器,如袋式除 尘器、电除尘器。不宜采用湿式除尘器。 3.1.1.7 炉内或炉内外结合的系统应采取防爆措施。 3.1.1.8 通风除尘系统应有防止过高烟气温度或灼热颗粒直接进入 袋式除尘器措施,当有结露可能时应采取预防措施。 3.1.2 冲天炉 3.1.2.1 冲天炉的排烟净化方式应根据炉型、燃料种类、加料口开 敞情况、水源条件、劳动卫生、环境保护及节能要求与维护管理水平等 条件进行具体分析和综合考虑来决定。 3.1.2.2 排烟净化宜采用下列方式: a. 机械排烟净化设备宜采用: 高效旋风除尘器、颗粒层除尘器——在炉料经过预处理(如废铸件 清砂、焦炭过筛等)后,适用于粉尘排放浓度在200-400mg/m3(标准状 态)的地区采用。 袋式除尘器、电除尘器——适用于粉尘排放浓度在200mg/m3(标准
铸造车间通风除尘设计说明

铸造污染防治措施及要求
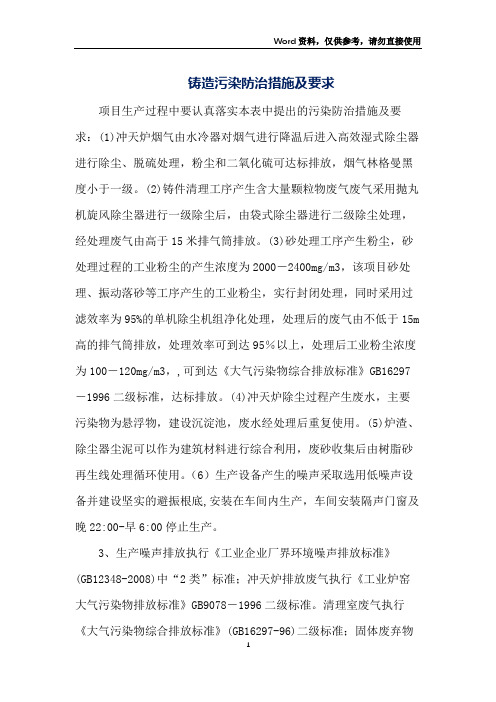
铸造污染防治措施及要求项目生产过程中要认真落实本表中提出的污染防治措施及要求:(1)冲天炉烟气由水冷器对烟气进行降温后进入高效湿式除尘器进行除尘、脱硫处理,粉尘和二氧化硫可达标排放,烟气林格曼黑度小于一级。
(2)铸件清理工序产生含大量颗粒物废气废气采用抛丸机旋风除尘器进行一级除尘后,由袋式除尘器进行二级除尘处理,经处理废气由高于15米排气筒排放。
(3)砂处理工序产生粉尘,砂处理过程的工业粉尘的产生浓度为2000-2400mg/m3,该项目砂处理、振动落砂等工序产生的工业粉尘,实行封闭处理,同时采用过滤效率为95%的单机除尘机组净化处理,处理后的废气由不低于15m 高的排气筒排放,处理效率可到达95%以上,处理后工业粉尘浓度为100-120mg/m3,,可到达《大气污染物综合排放标准》GB16297-1996二级标准,达标排放。
(4)冲天炉除尘过程产生废水,主要污染物为悬浮物,建设沉淀池,废水经处理后重复使用。
(5)炉渣、除尘器尘泥可以作为建筑材料进行综合利用,废砂收集后由树脂砂再生线处理循环使用。
(6)生产设备产生的噪声采取选用低噪声设备并建设坚实的避振根底,安装在车间内生产,车间安装隔声门窗及晚22:00-早6:00停止生产。
3、生产噪声排放执行《工业企业厂界环境噪声排放标准》(GB12348-2008)中“2类”标准;冲天炉排放废气执行《工业炉窑大气污染物排放标准》GB9078-1996二级标准。
清理室废气执行《大气污染物综合排放标准》(GB16297-96)二级标准;固体废弃物执行《中华人民共和国固体废物污染环境防治法》中的有关规定。
需要区域平衡替代消减满足污染物总量控制指标。
4、该项目为补办项目,必须在2011年8月底前完成环保设施的验收工作,否则按有关法律法规进行处理。
1、工程分析结论项目主要污染物为冲天炉除尘器产生的除尘废水;冲天炉熔化过程产生含粉尘、SO2废气;清砂过程产生工业粉尘;各类机械设备等产生的噪声;冲天炉熔化产生的炉渣、落砂清砂产生的废砂及除尘尘泥2、环境影响分析结论废气:(1)冲天炉烟气由水冷器对烟气进行降温后进入高效湿式除尘器进行除尘、脱硫处理,粉尘和二氧化硫可达标排放。
- 1、下载文档前请自行甄别文档内容的完整性,平台不提供额外的编辑、内容补充、找答案等附加服务。
- 2、"仅部分预览"的文档,不可在线预览部分如存在完整性等问题,可反馈申请退款(可完整预览的文档不适用该条件!)。
- 3、如文档侵犯您的权益,请联系客服反馈,我们会尽快为您处理(人工客服工作时间:9:00-18:30)。
在资金允许的情况下尽量采用新工艺、新设备、 新材料,如砂处理工部采用机械化生产线;落砂采用 密封性好的落砂冷却滚筒;煤粉、粘土等干态粉料采 用气力输送装置密闭输送;粘结剂采用无毒无害的动 物蛋白型粘结剂等。
Z=知2,0/2 Pa
(2)
式中 {——局部阻力系数(可查专门的资料获得)。
对于管段①:震动筛面积为1.6m2,按上吸罩的
排风量为每平方米筛板面积2 700 m3/h计算,所需风
量:2 700×1.6=4 320 m3/h,按风速18 rals计,则管
段①风管商径
D。=(4q/3 600r:v,)“2
环保2006,33(4)
通风除尘是目前劳动保护与环境保护的重要手段之一.其中过滤网格式通风除尘是一种占用空间小、除尘效果好、运行成本低、维护检修容易的通风 除尘系统,其风机房的两种设置方式各有优缺点,在工程中要根据实际需要进行选择.
5.会议论文 欧阳金练.欧阳曜.张洁.刘建刚 暖卫通风安装工程若干问题的对策 2000
山东大学(南校区)机械厂
丽百i旷葡瓣
万方数据
铸造车间砂处理工部的通风除尘
作者: 作者单位: 刊名:
英文刊名: 年,卷(期): 引用次数:
张国玲, 陈金宝 山东大学,济南,250061
环境工程 ENVIRONMENTAL ENGINEERING 2003,21(3) 0次
相似文献(10条)
1.会议论文 周让池 抛光车间的两种通风地沟 1985
万方数据
环境工程
2003年6月第21卷第3期
35
速是使粉尘在风管内能移动的最小风速,考虑风管的 损伤、密封不严、风机叶轮的磨损等因素,一般设计风 速要大于输送风速。砂处理工部各设备除尘系统的 风管中设计风速如表1。经净化后的空气,风管风速 可采用8~12 m/s。
衰1砂处理工部除尘臻统风管中的设计风速
2.3通风除尘 通风除尘是保证车间环境、改善劳动条件的主要
环节。根据砂处理工部的生产状况和布置特点,一般 采用就地除尘和分散除尘2种方法。 2.3.1就地除尘
是将除尘器、风机与扬尘设备结合为一体,就地 捕集和回收粉尘,这种方法布置紧凑、简单、维修方 便、节约能源。如目前的砂处理工部设计中,粉料输 送系统中的拆包机上安置就地除尘机组,混砂机上部 都设置插入式布袋除尘器。 2.3.2分散除尘
1个除尘系统的总阻力包括3部分:吸尘罩的入 口阻力,风管及其部件的摩擦阻力、局部阻力以及除 尘器的阻力。
摩擦阻力R(由于空气本身的粘滞性及其与管壁 间的摩擦而产生的阻力) 其计算公式如下:
R=Rn·L
Ro=^"2p/2d
(1)
式中 风——单位长度上的压力损失Palm;
^——摩擦系数;
w——风管内空气的平均流速;
*四川省应用基础项目
降低处理时间,这意味着惰性气体的消耗量也将减 少”。同时,微波加热均匀,微波场中无温度梯度存 在,故热效率高。
微波加热作为一种全新的热能技术,在材料工程 中得到了广泛的应用,在活性炭制备和改性中也产生 了较好的效果”‘41。本实验在此基础上,对活性炭利 用微波等离子体技术进行改性后的s02吸附性能进 行了初步研究,旨在探索一种简便、高效的活性炭脱 硫剂改性技术,现着重对微波功率、辐照时间等因素 对改性活性炭的脱硫效果进行实验分析。 2实验部分 2.1样品的制备
总风量为2个震动筛、2个皮带机转卸点: 0=4 320×2+1 500 X 2=11 640 H13/h 根据上述数据选除尘器:采用2级除尘,第一极 为CLP/A型旋风除尘器(CLP/A一10.6XN),进口风速 17 m/s,处理风量13 900矗/h,阻力损失1 260 Pa为 达到较好的除尘效果,第二级选布袋除尘器,(LMN。.
以下,排放浓度在100~120 mg/m:’以内。 (2)设计人员要多投入精力到环保设备的设计
中。设计出效率更高、效果更好的环保设备。并根据
生产中的问题不断改进。
(3)加强工人的环保意识,做好日常的维护工作, 加强管理,定期检查、专人维修。还要做好粉尘的后
处理工作,防止二次污染。
作者通讯处张国玲250061 电话(0531)8392543
:(4·4 32013 600,r·18)“2:0.29 m
管段①长8.7 nl,其摩擦阻力为:(将D,、”.、^代人公
式(1)得R。=12)
R=R。·L 冠=12×8,7=104.4 Pa
其局部阻力为:Z=∈v2to/29 在管段①中:五节弯头1个:n=90。R=1.5 D∈= 0.25(查表)
由公式(2)Z=0.25-182-1.2/2=48.6 Pa 直流三通1个:口=30。皮带机带宽为500 mm、排 风量为1 500 m3/h(查表),则三通支管直径
在设计多个抽风点的除尘系统时应对并联管路 进行阻力平衡。
4几点体会
(1)改善铸造车间的环境,首先要加大投资力度,
在每一个新建项目中必须考虑环保、通风除尘这一问
题。近年来在铸造车间砂处理工部设计中都是这样
做的,从而使车间环境得到大大的改善。车间操作点
的含尘浓度基本上达到了国家标准规定的10 mg/m3
验法,探讨了擞波功率、辐照时问及样品粒径3种固索对政性后的活性炭脱硫效果的影响。结果表明.微波改性后的
活性炭大大提高了对so:的吸附能力。最高硫吸附量可达109.4 mg/g,微波功率和样品粒径是决定改性活性炭硫容量
的关键素,并通过元素舟析和扫描电镜等手段对其机理进行了讨论。
关键词微波辐照 改性活性炭脱硫
体会与思考 -现代铸铁2006,26(4)
详细介绍了Busch铸造公司、Tweer铸造厂、Baumgarte铸造厂、宝马汽车铸造厂及GF-Singen铸造厂的除尘系统配置情况和实际效果,分析指出德国工 厂环境保护意识强、除尘技术先进可靠、工艺设备密闭性好,并且强调供排风的平衡和重视旧砂再生技术.
4.期刊论文 姜立升.马麒.杜雅兰 过滤网格式通风除尘系统预埋风管风机房设置方式的探讨 -铁道劳动安全卫生与
弋啦域A
1前言 为了制备具有更高脱硫活性的活性炭,通过在惰
性气体中热处理.削减炭表面的某些含氧官能团,以 得到低氧含量、高疏水性和耐老化的炭可以达到这一 目的…。加热的方式可分为普通加热(如电炉加热) 和微波加热,二者的不同点在于热的产生方式。对于 前者,热源位于炭床外,物料中存在温度梯度,直到达 到稳定。用微波加热,微波能量被炭粒子吸收,这种 能量靠偶极子转动和离子传导,转变为粒子自身的 热。相比而言,利用微渡加热主要的优点是能大幅度
D2=(4Q13 600M)” :(4×1 50013 600ד×18)1” =0.172 nl(圆整为170 mm)
则实际口2为4·1 50013 600×Ⅱ×0.172=18.3 m/s 根据"2“.DlID2查表得{=O.4 由公式(2)则三通处Z=0.4×18.33×1.2/2=
80 Pa
该文介绍了中型抛光车间为净化除尘而实施的两种通风地沟,即浅短地沟和深长地沟。并对两种地沟的实际应用,包括使用效果、维修管理、节约 能耗、粉尘污染情况,初投资及长期运行费用作了详细的对比。文后附有两种地沟的平面图示。(本刊录)
2.期刊论文 张文斌.ZHANG Wen-bin 扁袋除尘器在木工车间通风除尘中的应用 -工业安全与环保2007,33(10)
震动筛吸尘罩的局部阻力损失为40 Pa(查表得) 管段①的总压损
H.=ERoL+乏知2p129 =104.4+48.6+80+40=273 Pa
以同样的方法计算出管段②、③、④、⑤、⑥、⑦、⑧、⑨ 的压力损失H2=320、H3=180、风=120、H,=20、H。 =320、日7=281、H8;165、凰=420
环境工程 2003年6月第2l卷第3期
铸造车间砂处理工部的通风除尘
张国玲陈金宝
(山东大学,济南250061)
摘要本文叙述了铸造车问砂处理工部通风除尘的必要性,工部设计中采取的环保措施,具体的设计计算方法及实际
应用中的效果和体会。
关键词 环境保护 通风除尘
X] b
1概述 铸造车间砂处理工部要对旧砂进行破碎、筛分、
总压损为He=∑㈨H=2 099 Pa
万方数据
环境工程 2003年6月第2l卷第3期
徽渡改性活性炭脱磙性能的初步研究’
江霞蒋文举
朱晓帆
(四川大学建筑与环境学院,成都610065) (四川大学分析测试中心,成都610065)
摘要 在此提出了一种利用微渡等离子技术对活性炭进行改性以提高活性炭的s嘎吸附性能的新方法。通过正交实
72)风量5 940~11 880 In3/h,阻力1 200 Pa。 根据风量风压选择风机如下:(计算值风量附加
10%,风压附加15%),则: Q=11 640×110%=12 804 m3/h
Ⅳ=(2 099+l 260+l 200)×115%=5 243 Pa
由此选风机9—19型N。】0风压5 350 Pa 风量13 952 m3/h
据资料,国外先进的大型铸造厂的特点是高度自 动化的流水生产,非常注重劳动条件和环境保护,如 采用密封厂房和双层厂房,加强车间通风除尘。一般 铸造车间的新建工程或老厂改造在环保方面的投资 要占总投资的30%;近年来在国内用在通风除尘上 的投资大部分都提高到总投资的20%~30%,从而 极大的改善了车间环境及工人的劳动条件。 2采取的措施 2.1工艺布置
以我们设计的镇江某器材厂的砂处理工部的一 个分散除尘系统为例,设计计算如下:根据同时运转, 距离较近的原则,我们将混砂机上9 m平台上的2条 旧砂分配皮带,2个震动筛设为1套分散除尘系统。 震动筛采用上吸式吸尘罩。旧砂皮带采用全封闭式 除尘罩,共设4个抽尘口。其布置形式如附图。