铸钢件生产时采用的几种自硬砂的
铸钢件生产型砂工艺的选用

铸钢件生产型砂工艺的选用
臧周恒;徐尔灵;王海;孟宪伟;陈晓华
【期刊名称】《铸造工程》
【年(卷),期】2008(032)003
【摘要】造型制芯工艺在铸件生产中占有十分重要的地位,它直接影响铸件的质量、生产成本、生产效率及环境,而传统水玻璃砂工艺劳动强度大、生产效率低.采用新
型水玻璃自硬砂工艺和碱性酚醛树脂自硬砂工艺可以满足铸钢件生产要求,考虑生
产成本选用水玻璃自硬砂工艺,在有特殊要求时采用碱性酚醛树脂自硬砂.
【总页数】3页(P6-8)
【作者】臧周恒;徐尔灵;王海;孟宪伟;陈晓华
【作者单位】广东省韶关市韶铸集团有限公司,广东,韶关,512031;广东省韶关市韶
铸集团有限公司,广东,韶关,512031;广东省韶关市韶铸集团有限公司,广东,韶
关,512031;广东省韶关市韶铸集团有限公司,广东,韶关,512031;广东省韶关市韶铸
集团有限公司,广东,韶关,512031
【正文语种】中文
【中图分类】TG221+.2
【相关文献】
1.厚壁大型铸钢件型砂工艺的探讨 [J], 夏作正
2.大型铸钢件生产型砂粘结剂选择与应用 [J], 唐贤其
3.用湿型砂冲击造型生产铸钢件 [J], 陈其刚;王志刚
4.消失模铸造生产技术第四讲:消失模工艺生产铸钢件工艺原则 [J], 刘立中;刘凯
5.用湿型砂冲击造型生产铸钢件 [J], 陈其刚;王志刚
因版权原因,仅展示原文概要,查看原文内容请购买。
铸钢件生产时采用的几种自硬砂的

铸钢件生产时采用的几种自硬砂的工艺性能的对比分析一.前言50多年来造型、制芯材料和工艺.在国内外有了长足的发展.特别是在生产铸铁件时.采用呋喃树脂砂取代粘土砂方面.显示了许多优越性.它已成为铸铁厂家进行技术改造的首选方案。
在铸钢件生产中.从20世纪50年代开始采用水玻璃砂.到20世纪70年代.由于采用水玻璃砂生产的铸钢件的尺寸精度和表面质量都差.尤其是型、芯砂的溃散性不好.清砂十分困难.旧砂不能再生回用等问题.没有得到较好的解决.于是.在某些重机厂、水泵厂和机车厂等的一些铸钢件改用了呋喃树脂砂。
到20世纪90年代末.又由于呋喃树脂砂生产的铸钢件易产生热裂等缺陷.以及磺酸固化剂热分解时产生的气体.导致铸钢件表面渗碳、渗硫.以及呋喃树脂砂环境污染等问题.使一些铸钢厂又开始采用酯硬化碱性酚醛树脂砂。
不过.直到今天.水玻璃砂造型、制芯工艺.还是铸钢件生产中最基本、用量最多的一种造型、制芯方法。
由于这三种自硬砂各有其优缺点.目前在我国这三种工艺并存.各厂都是根据本厂铸钢件生产的特点和批量.生产的现状和未来的要求等多方面进行综合考虑.而确定本厂的造型、制芯工艺。
例如.二重厂、广重厂等生产中使用了酯硬化碱性酚醛树脂砂.大重厂、沈重厂和一重厂等采用无氮呋喃树脂砂.其余的.包括铁道部下属的20多个机车车辆厂.还是采用水玻璃砂。
总之.人们总是希望能以较高的生产效率、较低的制造成本、较好的作业环境.生产出优质的铸钢件来.可是.到目前国内外还没有一种造型、制芯工艺能同时满足上述的全部要求.为此.下面将从生产效率、铸件质量、环境污染和制造成本等四个方面.对水玻璃砂、呋喃树脂砂和碱性酚醛树脂砂等三种自硬砂的工艺性能进行对比分析.以供参考。
二.生产效率目前在铸造生产中得到广泛应用的造型、制芯工艺有三大类:热硬砂(如热芯盒、覆膜砂等)、气硬冷芯盒砂(如三乙胺聚脲烷、CO2水玻璃砂、SO2呋喃树脂砂等)和自硬砂(如酯硬化碱性酚醛树脂砂、酸固化呋喃树脂砂、酯硬化水玻璃砂和胺固化聚脲烷砂等)。
新型水玻璃自硬砂在铸钢生产中的应用

新型水玻璃自硬砂工艺在铸钢生产中的应用一.前言目前国内外冷凝自硬砂工艺主要分为二大类-无机类粘结剂以水玻璃砂工艺为主,有机类粘结剂以呋喃和碱性酚醛树脂砂工艺为主。
以上二大类自硬砂工艺在二十世纪下半期至今在全世界铸造业应用并不断成熟完善。
但此二种工艺在性能上各有特点,也存在问题。
特别在铸钢、合金钢件的铸造时有明显工艺上的不足。
CO2硬化水玻璃加入量高(一般为7%~8%),砂的残留强度高,溃散性差,旧砂再生回用困难。
有机粘结剂树脂砂工艺的出现,在一定程度上解决了CO2水玻璃砂的固有缺陷,但碱性酚醛树脂成本高,呋喃树脂砂易出现铸件裂纹、气孔等缺陷。
水玻璃“新三法”(VRH、微波烘硬、有机脂)的问世,使水玻璃的加入量降低了一半,溃散性大有改善,但新“三法”在工艺上存在着一定的缺陷,VRH法因设备投资大及铸件尺寸受真空室限制;微波烘硬法因铸型吸湿性强及电微波转化率低;回用砂率综合性能差等缺点,严重制约了水玻璃砂的发展。
随着水玻璃基础理论研究的不断进展,水玻璃砂溃散性差和旧砂再生困难等缺点并非水玻璃的固有特性。
它来源于对水玻璃化学和胶体化学认识不足和使用不当(1)。
目前国内以沈阳汇亚通铸造材料有限责任公司等单位在这方面的研究取得了领先。
他对普通水玻璃进行一系列化学和物理改性及电离子架接,研制开发了新型水玻璃和专用酯类固化剂自硬砂工艺,为水玻璃砂的第三次中兴产生了质的飞跃。
二.新型水玻璃酯硬砂工艺的应用我公司年产阀门承压铸钢件2000余吨,产品以单价小批量为主,壳体主要壁厚10~60mm,且薄件居多。
材质牌号有普通碳素钢,耐热耐高温铬钼钢、铬钼钡钢及各种耐酸不锈钢。
其中有30%是电站阀门铸件,有20%左右是出口阀门配套铸件。
因此,对造型工艺及材料要求相当苛刻。
我们于2000年下半年开始对原粘土砂工艺进行技术改造,要求采用新工艺、新材料,以低成本高质量满足当前生产及市场竞争的需要,在选择工艺方案阶段,我们对普通水玻璃自硬砂,呋喃树脂自硬砂及新型水玻璃自硬砂三种砂型工艺,分别在不同材质、不同品种的阀门铸钢件上进行了工艺试验,试验用原砂为福建平潭优质擦洗硅砂,粒度为40/70目,SiO2含量≥96%,含泥量和含水量分别≤0.5%,角形系数≤1.25%,试验及技术经济分析结果如表1所示。
铸钢件生产时采用的几种自硬砂的

铸钢件生产时采用的几种自硬砂的工艺性能的对比分析一.前言50多年来造型、制芯材料和工艺,在国内外有了长足的发展,特别是在生产铸铁件时,采用呋喃树脂砂取代粘土砂方面,显示了许多优越性,它已成为铸铁厂家进行技术改造的首选方案。
在铸钢件生产中,从20世纪50年代开始采用水玻璃砂,到20世纪70年代,由于采用水玻璃砂生产的铸钢件的尺寸精度和表面质量都差,尤其是型、芯砂的溃散性不好,清砂十分困难,旧砂不能再生回用等问题,没有得到较好的解决,于是,在某些重机厂、水泵厂和机车厂等的一些铸钢件改用了呋喃树脂砂。
到20世纪90年代末,又由于呋喃树脂砂生产的铸钢件易产生热裂等缺陷,以及磺酸固化剂热分解时产生的气体,导致铸钢件表面渗碳、渗硫,以及呋喃树脂砂环境污染等问题,使一些铸钢厂又开始采用酯硬化碱性酚醛树脂砂。
不过,直到今天,水玻璃砂造型、制芯工艺,还是铸钢件生产中最基本、用量最多的一种造型、制芯方法。
由于这三种自硬砂各有其优缺点,目前在我国这三种工艺并存,各厂都是根据本厂铸钢件生产的特点和批量,生产的现状和未来的要求等多方面进行综合考虑,而确定本厂的造型、制芯工艺。
例如,二重厂、广重厂等生产中使用了酯硬化碱性酚醛树脂砂,大重厂、沈重厂和一重厂等采用无氮呋喃树脂砂,其余的,包括铁道部下属的20多个机车车辆厂,还是采用水玻璃砂。
总之,人们总是希望能以较高的生产效率、较低的制造成本、较好的作业环境,生产出优质的铸钢件来,可是,到目前国内外还没有一种造型、制芯工艺能同时满足上述的全部要求,为此,下面将从生产效率、铸件质量、环境污染和制造成本等四个方面,对水玻璃砂、呋喃树脂砂和碱性酚醛树脂砂等三种自硬砂的工艺性能进行对比分析,以供参考。
二.生产效率目前在铸造生产中得到广泛应用的造型、制芯工艺有三大类:热硬砂(如热芯盒、覆膜砂等)、气硬冷芯盒砂(如三乙胺聚脲烷、CO2水玻璃砂、SO2呋喃树脂砂等)和自硬砂(如酯硬化碱性酚醛树脂砂、酸固化呋喃树脂砂、酯硬化水玻璃砂和胺固化聚脲烷砂等)。
铸钢常用自硬砂的选用
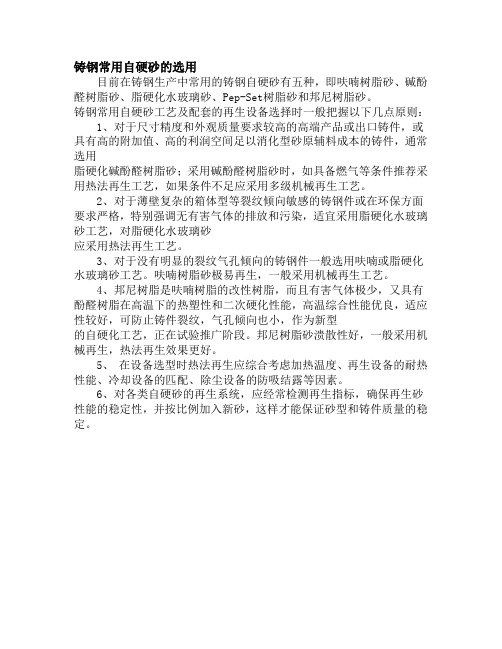
铸钢常用自硬砂的选用
目前在铸钢生产中常用的铸钢自硬砂有五种,即呋喃树脂砂、碱酚醛树脂砂、脂硬化水玻璃砂、Pep-Set树脂砂和邦尼树脂砂。
铸钢常用自硬砂工艺及配套的再生设备选择时一般把握以下几点原则:
1、对于尺寸精度和外观质量要求较高的高端产品或出口铸件,或具有高的附加值、高的利润空间足以消化型砂原辅料成本的铸件,通常选用
脂硬化碱酚醛树脂砂;采用碱酚醛树脂砂时,如具备燃气等条件推荐采用热法再生工艺,如果条件不足应采用多级机械再生工艺。
2、对于薄壁复杂的箱体型等裂纹倾向敏感的铸钢件或在环保方面要求严格,特别强调无有害气体的排放和污染,适宜采用脂硬化水玻璃砂工艺,对脂硬化水玻璃砂
应采用热法再生工艺。
3、对于没有明显的裂纹气孔倾向的铸钢件一般选用呋喃或脂硬化水玻璃砂工艺。
呋喃树脂砂极易再生,一般采用机械再生工艺。
4、邦尼树脂是呋喃树脂的改性树脂,而且有害气体极少,又具有酚醛树脂在高温下的热塑性和二次硬化性能,高温综合性能优良,适应性较好,可防止铸件裂纹,气孔倾向也小,作为新型
的自硬化工艺,正在试验推广阶段。
邦尼树脂砂溃散性好,一般采用机械再生,热法再生效果更好。
5、在设备选型时热法再生应综合考虑加热温度、再生设备的耐热性能、冷却设备的匹配、除尘设备的防吸结露等因素。
6、对各类自硬砂的再生系统,应经常检测再生指标,确保再生砂性能的稳定性,并按比例加入新砂,这样才能保证砂型和铸件质量的稳定。
铸造砂文档

铸造砂1. 引言铸造砂是金属铸造中不可或缺的一种材料。
它在铸造过程中用于制造铸型和芯子,起到支撑金属熔液和保持形状的作用。
铸造砂的品质直接影响到最终铸件的质量和性能。
本文将介绍铸造砂的种类、生产工艺、应用以及相关的质量控制方法。
2. 铸造砂的种类铸造砂可以根据其主要成分的不同分为几种不同的种类:2.1 石英砂石英砂是一种采用天然石英矿石经过破碎、筛分和洗选而得到的铸造砂。
它具有化学稳定性高、热膨胀系数低、耐高温和耐腐蚀等特点,常用于铸造高温合金。
2.2 绿砂绿砂是一种以砂轮废料为主要原料制造的铸造砂。
它具有较高的可塑性和粘度,能够制造出复杂形状的铸型和芯子。
绿砂还可以在高温下迅速脱水,减少铸件中的气孔和夹杂。
2.3 粘土砂粘土砂是一种以粘土为主要原料制造的铸造砂。
它具有良好的可塑性和粘结性,适用于制造较大尺寸和复杂形状的铸型。
粘土砂在高温下能够固化,形成坚硬的铸件。
2.4 耐火砂耐火砂是一种由耐火材料破碎和粉碎而得到的铸造砂。
它具有较高的耐高温性能和耐磨性,常用于制造耐火铸件,如炉内衬板和炉窑砖等。
3. 铸造砂的生产工艺铸造砂的生产工艺包括原料处理、砂浆制备、砂芯制造和铸型制作等环节。
3.1 原料处理根据铸造砂的种类和要求,原料需要进行破碎、筛分和粉碎等处理。
这些处理能够使原料颗粒的大小、含量和分布符合铸造需要。
3.2 砂浆制备将经过处理的原料与粘结剂、水和其他添加剂混合,形成砂浆。
砂浆的稠度和流动性要根据具体的铸造要求进行调整,以确保铸造砂在铸造过程中能够顺利流动,并保持良好的可塑性。
3.3 砂芯制造砂芯是用于形成铸件内部空腔或复杂内部结构的一种铸造砂制品。
砂芯的制造一般通过将砂浆注入芯盒中,然后在适当的温度和湿度条件下进行固化。
固化后的砂芯需要具有一定的强度和耐热性,以保证在浇铸过程中不发生变形或破裂。
3.4 铸型制作铸型是铸造砂制品中最常见的形式,它用于形成铸件的外形和表面。
铸型的制作一般通过将砂浆填充到具有铸件形状的模具中,然后等待砂浆固化。
呋喃树脂自硬砂生产大型铸钢件
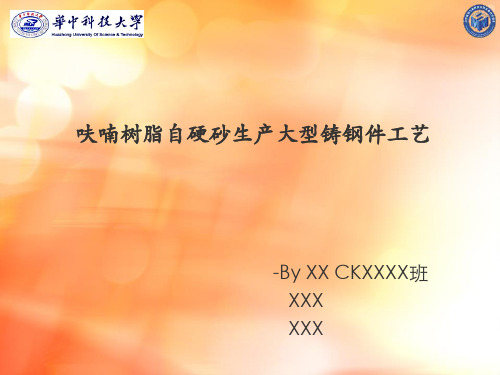
铬铁矿砂
Cr2O3>46% 粒度40/70目 细粉含量≤1.0% 酸耗值≤5ml 水分含量≤0.2% 灼减量≤0.5%
当然,再生砂性能指标与铸件质量也有直接关系!
呋喃树脂自硬砂生产大型铸钢件工艺▪树脂和固化剂的选择
树脂:无氮高糠醇呋喃树脂
固化剂:对甲苯磺酸或二甲苯磺酸
呋喃树脂自硬砂生产大型铸钢件工艺▪砂温控制
20℃~30℃
呋喃树脂自硬砂生产大型铸钢件工艺▪砂型强度
一般要求: 型砂终强度:0.6MPa~0.8MPa 芯砂终强度:0.8MPa~1.0MPa 复杂芯砂终强度:1.6~2.0MPa
呋喃树脂自硬砂生产大型铸钢件工艺▪树脂和固化剂加入量
实际树脂加入量:1.0%~1.2% 固化剂加入量:树脂加入量的30%~50%
参考文献
参考文献: [ 1 ]李远才 . 铸型材料基础 [M]. 北京:化学工业出版社, 2009 [ 2 ]于洪岩,周俊珍 . 呋喃树脂自硬砂生产大型铸钢件工 艺控制要点[J].铸造设备与工艺,2011(3):22-24 [ 3 ]李小军,江国栋,等 . 一种快速测定铸造用自硬呋喃 树脂含氮量的方法[J].铸造,2014,63(4):360-362
呋喃树脂自硬砂生产大型铸钢件工艺▪工艺设计原则
多组芯造型 朝铸件表面填砂 铬铁矿面砂
慎重铸造缩尺
冒口树脂自硬砂生产大型铸钢件工艺▪生产操作注意事项
严控生产操作
举措
型芯紧实
涂料涂刷
型芯排气
砂型芯退让
结论
合格大型铸 有毒气体 发气量大 钢件
不利因素 增碳
热裂倾向 大 退让性差
疏漏之处,恳请指正!
谢谢!
材控XXXX班 XX XXX XXX
铸钢用几种自硬砂综述

生产薄壁类铸钢件用几种自硬砂工艺综述生产铸钢件可供选择的型砂工艺有:呋喃树脂自硬砂工艺、碱性树脂自硬砂工艺、pepset 法自硬砂工艺、新型水玻璃自硬砂工艺。
这四种自硬砂工艺的基本情况如下:一、四种自硬砂工艺的概述(一)呋喃树脂自硬砂工艺1、工艺主要优势(1)铸件表面质量和尺寸精度高。
(2)型芯溃散性好,铸件落砂清理容易。
(3)旧砂干法再生回用容易,回用率高(≥90%)。
这些优点使该工艺在铸件生产中得到大面积推广应用,尤其是铸铁件的生产。
2、工艺缺点多年的理论研究和生产实践表明,用呋喃树脂砂工艺生产铸钢件有难以解决的技术难题。
(1)呋喃树脂砂热膨胀系数大,高温退让性差,铸件易产生裂纹,尤其是薄壁、壁厚差较大,结构复杂的铸钢件。
(2)粘结剂系统含S、N等有害元素,易造成铸件表面渗硫,造成表面微裂纹,以及N导致的气孔或皮下气孔。
(3)型砂发气量较大,铸件易出现气孔缺陷。
(4)混砂、造型、浇注、落砂、清理过程中产生SO2、CO等有害气体,污染作业环境。
正是由于上述一些原因,导致某些工厂不能把所有产品都使用呋喃树脂砂生产,而保持呋喃树脂砂、水玻璃砂(粘土砂、碱性树脂砂)并行的状态,造型管理、生产上的诸多不便。
呋喃树脂砂生产线有的因铸件废品率多、生产成本高已闲置,有的生产线已改造成新型水玻璃自硬砂生产线或碱性树脂砂生产线。
针对呋喃树脂砂工艺的不足,国内外专家进行了多年研究,推出改性呋喃树脂,并在生产过程中采取多项工艺措施(如冷铁等),但未收到明显实效。
综上所述,呋喃树脂砂工艺用于铸钢件的生产不是一种好的选择,生产薄壁、结构复杂、易产生裂纹、气孔类缺陷的泵、阀、机车类铸钢件则更不可取。
(二)碱性树脂自硬砂工艺1、工艺优势(1)铸件表面质量和尺寸精度高,铸件综合质量优良。
(2)粘结剂系统不含S、P、N等有害元素,可防止因这些元素引起的铸件缺陷。
(3)具有独特的高温硬化特性,可显著减少铸钢件的热裂缺陷。
(4)固化剂参与硬化反应,型砂硬化性能好,可调性强。
- 1、下载文档前请自行甄别文档内容的完整性,平台不提供额外的编辑、内容补充、找答案等附加服务。
- 2、"仅部分预览"的文档,不可在线预览部分如存在完整性等问题,可反馈申请退款(可完整预览的文档不适用该条件!)。
- 3、如文档侵犯您的权益,请联系客服反馈,我们会尽快为您处理(人工客服工作时间:9:00-18:30)。
铸钢件生产时采用的几种自硬砂的工艺性能的对比分析一.前言50多年来造型、制芯材料和工艺,在国内外有了长足的发展,特别是在生产铸铁件时,采用呋喃树脂砂取代粘土砂方面,显示了许多优越性,它已成为铸铁厂家进行技术改造的首选方案。
在铸钢件生产中,从20世纪50年代开始采用水玻璃砂,到20世纪70年代,由于采用水玻璃砂生产的铸钢件的尺寸精度和表面质量都差,尤其是型、芯砂的溃散性不好,清砂十分困难,旧砂不能再生回用等问题,没有得到较好的解决,于是,在某些重机厂、水泵厂和机车厂等的一些铸钢件改用了呋喃树脂砂。
到20世纪90年代末,又由于呋喃树脂砂生产的铸钢件易产生热裂等缺陷,以及磺酸固化剂热分解时产生的气体,导致铸钢件表面渗碳、渗硫,以及呋喃树脂砂环境污染等问题,使一些铸钢厂又开始采用酯硬化碱性酚醛树脂砂。
不过,直到今天,水玻璃砂造型、制芯工艺,还是铸钢件生产中最基本、用量最多的一种造型、制芯方法。
由于这三种自硬砂各有其优缺点,目前在我国这三种工艺并存,各厂都是根据本厂铸钢件生产的特点和批量,生产的现状和未来的要求等多方面进行综合考虑,而确定本厂的造型、制芯工艺。
例如,二重厂、广重厂等生产中使用了酯硬化碱性酚醛树脂砂,大重厂、沈重厂和一重厂等采用无氮呋喃树脂砂,其余的,包括铁道部下属的20多个机车车辆厂,还是采用水玻璃砂。
总之,人们总是希望能以较高的生产效率、较低的制造成本、较好的作业环境,生产出优质的铸钢件来,可是,到目前国内外还没有一种造型、制芯工艺能同时满足上述的全部要求,为此,下面将从生产效率、铸件质量、环境污染和制造成本等四个方面,对水玻璃砂、呋喃树脂砂和碱性酚醛树脂砂等三种自硬砂的工艺性能进行对比分析,以供参考。
二.生产效率目前在铸造生产中得到广泛应用的造型、制芯工艺有三大类:热硬砂(如热芯盒、覆膜砂等)、气硬冷芯盒砂(如三乙胺聚脲烷、CO2水玻璃砂、SO2呋喃树脂砂等)和自硬砂(如酯硬化碱性酚醛树脂砂、酸固化呋喃树脂砂、酯硬化水玻璃砂和胺固化聚脲烷砂等)。
而对铸钢件生产来说,特别是生产中、大型铸钢件时,前两种工艺均不适用,目前主要是采用自硬砂为主。
所谓自硬砂系指一种粘结剂,通过加入一种液体固化剂,使之在室温下在一定时间内,型、芯砂能在砂箱中,或芯盒内自行硬化成型的一种造型、制芯工艺。
这种工艺最大的特点是,生产效率低,所以,自硬砂的造型、制芯效率就成为衡量该自硬砂工艺性能的重要指标。
作为衡量自硬砂生产效率大小的量度,一般采用型、芯砂的可使用时间与其起模时间的比值来表示,即其比值的大小表示在型、芯起模时间一定时,型、芯砂可使用时间的长短的一个标志,一般取值范围在0~1之间,接近1的高比值的自硬砂,表示它具有较高的造型、制芯的生产效率,从而,模具、工装的周转率也可加快,表1列出四种自硬砂的比值。
从表中的比值对比可知,酯硬化碱性酚醛树脂砂排在第二位,表示它的硬化速度较快,生产效率较高。
酸硬化呋喃树脂砂排在第三,而酯表1 四种自硬砂的比值。
硬化水玻璃砂排在最后,表示它的硬化速度最慢,造型、制芯效率最低。
由此可知,采用酯硬化水玻璃砂工艺时,工装、模具要求较多,特别是制造大型型、芯时,起模太早,型芯易变形,甚至出现断裂等问题,这点必须引起足够的重视。
三.铸件质量随着装备制造业的发展,特别是外贸出口的需要,对铸钢件的表面质量和尺寸精度都提出了更为严格的要求,而这些都与造型材料的合理选用密切相关,现就以下几个方面的工艺性能,进行比较。
3.1自硬砂的强度。
呋喃树脂砂的最大特点就是粘结强度高、耐热性好;其次是碱性酚醛树脂自硬砂,粘结强度最小的是水玻璃砂,表2列出三种自硬砂的24小时的抗拉强度对比。
表2 三种自硬砂的常温抗拉强度的对比3.2 自硬砂的抗湿性。
型、芯砂的抗湿性差,表示它的表面强度低,铸钢件易产生掉砂、冲砂、粘砂等表面缺陷。
抗湿性的试验方法是;将待测的砂样放入湿度100%密闭容器中,停放24小时后,测定其强度,再分别计算它的抗湿率,表3列出三种自硬砂的抗湿性的对比数据。
从表中的数据可见,酯硬化碱性酚醛树脂砂的抗湿性最好,用它制得的型、芯可长期在高湿度下存放。
而水玻璃砂的抗湿性最差,它的表面安定性表3 三种自硬砂的抗湿性的对比自硬砂种类碱性树脂砂呋喃树脂砂水玻璃砂抗湿性(%)20~30 50~55 80~90不好,因此,水玻璃砂生产的铸钢件上的表面缺陷最多,如掉砂、冲砂、粘砂等铸造缺陷造成的废品率可达总废品率的50%以上,增加了铸钢件的焊补率3.2 自硬砂的高温热变形。
铸钢件的尺寸精度差,超重、超差常与型、芯砂中的粘结剂紧密相关,图1表示四种自硬砂的高温热变形曲线。
从图可看出。
水玻璃砂的热变形最大,这是因为水玻璃在550℃左右会出现低熔点液相的缘故。
从图还可见,呋喃树脂砂在高温下无塑性,热变形很小,仅为水玻璃砂的1/5,但其热膨胀很大,比水玻璃砂大一倍。
而碱性酚醛树脂砂的热膨胀速度慢,膨胀量液小,这是它存在“二次硬化”现象的原故。
由此可看出,呋喃树脂砂的热变形小,铸钢件的尺寸精度高,由于它的耐热性好,却增加了铸钢件在凝固时的收缩阻力,从而,明显增大了铸钢件的热裂缺陷的倾向。
水玻璃砂的高温热变形最大,铸钢件的热烈倾向小,而碱性酚醛树脂砂则居中,它兼顾了呋喃树脂砂的高温强度和水玻璃砂的高温塑性的一种抗裂性较好的造型、制芯材料,不过,它存在二次硬化的现象,对于薄壁、箱形的铸钢件,也还可能存在产生热裂缺陷的可能。
3.4 自硬砂的残留强度。
现今人们总是将型、芯砂在1000℃加热后冷却到室温的砂样的残留抗压强度,作为衡量一种自硬砂清砂难易的标志,表4列出三种自硬砂在1000℃加热、冷却后的残留抗压强度的对比。
从表4 三种自硬砂1000℃加热、冷却后的残留抗压强度的对比表中的数据可知,尽管水玻璃通过化学改性和用有机酯作硬化剂,使其加入量降低到3.0%以下,但其残留强度还是比树脂砂高很多,清砂还是不如树脂砂容易。
3.5 浇注时产生的气体对比。
浇注时产生的气体数量和成分,及其对铸钢件质量的影响,都与所采用的型、芯砂的粘结剂的种类有关。
从发气速度和发气量来看,水玻璃砂都很小,而碱性酚醛树脂砂的发气量又是所有树脂砂中最小的,图2表示几种自硬砂的发气量。
从浇注时产生的气体成分来看,呋喃树脂中含氮(0.5~7.0%),它是导致铸钢件产生气孔的主要原因;另外,呋喃树脂的热分解可使铸钢件的表面渗碳,磺酸固化剂的热分解也能使它的表面增硫,一般来说,表层渗碳量可达2~3mm,渗硫量可达1~2mm,这都能引起合金材质成分的改变及其力学性能的下降,而采用碱性酚醛树脂砂和水玻璃砂均没有这种困扰。
图2 几种自硬砂的发气量3.6 铸钢件的尺寸精度和表面粗糙度。
呋喃树脂砂和碱性酚醛树脂砂这两种工艺是目前铸造行业能实现能源消耗少、劳动强度低、生产效率较高、铸件尺寸精度高、表面质量好的有效途径,已成为我国铸造行业生产高质量铸钢件和外贸出口铸件的一条重要手段,但是,水玻璃砂在这些方面还不如树脂砂好,表5列出树脂自硬砂和酯硬化水玻璃砂生产的铸钢件的尺寸精度和表面粗糙度的对比。
由表可知,树脂砂生产的铸钢件的质量均比水玻璃砂高1~2级。
表5 几种自硬砂生产的铸钢件的尺寸精度和表面粗糙度的对比自硬砂种类碱性树脂砂呋喃树脂砂酯-水玻璃砂铸件尺寸精度(CT,级) 8~10 7~9 10~12铸件表面粗糙度(Ra,µΜ)50 50 50~100 四.生产成本造型、制芯的生产成本包括原、辅材料的成本和旧砂再生的成本等两部分,表6列出了造型、制芯用的原、辅材料的成本。
从表中数据可看出,酯硬化碱性酚醛树脂砂的原、辅材料的成本最高,而酯硬化水玻璃表6 几种自硬砂用原、辅材料的成本砂和呋喃树脂砂的原、辅材料的成本都较低,仅为碱性酚醛树脂砂的55%左右,因此,减少碱性酚醛树脂和有机酯的加入量及其降低它们的生产成本,是当前推广酯硬化碱性酚醛树脂的关键之一。
其次是旧砂再生的成本。
旧砂是否容易再生,再生砂的质量是否接近新砂的水平,是决定一种自硬砂是否有发展应用前景的大问题,因为,它不仅能降低生产成本,节约原砂资源,而且,还可减少固体废弃物的排放,减轻环境污染,因此,在人们环保和成本等意识不断增强的21世纪,旧砂再生显得更为重要。
众所周知,呋喃树脂旧砂的再生性能最好,可采用干法机械再生,再生率可达90%以上,因为,呋喃树脂粘结剂膜属于脆性的缘故。
水玻璃旧砂和碱性酚醛树脂旧砂等粘结剂膜都属于韧性,吸湿性又大,特别是用有机酯作固化剂的场合,旧砂再生更为困难。
目前国内推出的水玻璃旧砂再生线都较复杂,一次性投资较多,一般中、小铸造厂无法采用。
若采用简易再生的方法,再生砂的质量太差,只能作背砂用,大部分旧砂被排放,所以,水玻璃旧砂和碱性酚醛树脂旧砂的再生问题,尚没有得到满意的解决。
五.环境污染在人们环保意识不断增强,国家环保法规日益实施的今天,在选用造型、制芯的自硬砂时,必须清醒地考虑这一点。
表7列出呋喃树脂砂在混砂、造型、浇注和清砂等工序中释放出来的有毒气体的情况。
表7列表7 呋喃树脂砂在造型和浇注时析出的有毒气体量出了呋喃树脂自硬砂在造型和浇注两个工部释放出来的各种有毒气体的情况。
从表中数据清楚地表明,在造型、制芯工部释放出来的有毒气体主要是甲醛和糠醇;而在浇注和清砂工部折出的有毒气体主要是一氧化碳、硫化氢和二氧化硫等,其中浇注工部空气中的一氧化碳、硫化氢等有毒气体的含量均严重超过我国环保法规定的允许浓度,减少呋喃树脂砂的有毒、有害气体对人体的危害,是关系到呋喃树脂砂发展的关键技术之一。
而水玻璃砂和碱性酚醛树脂砂对环境污染都很小,这是它们的优势所在。