金属表面处理工艺技术指标
电镀级别氯化镍的技术参数项目指标

电镀级别氯化镍的技术参数项目指标一、电镀级别氯化镍的概述电镀级别氯化镍是一种常见的金属表面处理技术,可以提高金属表面的硬度、耐磨性、耐腐蚀性等性能。
其工艺流程包括清洗、酸洗、钝化、电镀等步骤,其中电镀是关键环节。
二、电镀级别氯化镍的主要技术参数1. 电解液成分:电解液是影响电镀质量和效率的重要因素之一。
通常采用氯化镍为主体,加入适量的酸性盐类和助剂等。
其中,氯化镍浓度应在150~200g/L之间。
2. 电解液温度:温度对于反应速率和沉积速率都有很大影响。
通常控制在40~60℃之间。
3. 电流密度:是指单位面积上通过的电流量,也称为“密度”。
其大小直接影响到沉积速率和沉积质量。
一般控制在2~10A/dm²之间。
4. 镀层厚度:不同工件需要的厚度不同,但通常控制在5~25μm之间。
5. 镀层硬度:硬度是衡量电镀质量的重要指标,一般应达到500~700HV之间。
6. 镀层耐腐蚀性:氯化镍电镀层具有较好的耐腐蚀性,但其抗蚀性能也受到其他因素的影响,如电解液成分、温度、电流密度等。
7. 镀层外观:外观包括光泽度、颜色等方面,应符合客户要求。
三、影响电镀级别氯化镍质量的因素1. 金属基材表面处理:金属表面必须经过适当的清洗和钝化等处理,以保证电镀质量。
2. 电解液配方和控制:电解液成分和控制对于沉积速率和沉积质量都有很大影响。
3. 电流密度控制:过高或过低的电流密度都会影响到沉积速率和质量。
4. 温度控制:温度过高会导致气泡产生,温度过低则会影响到沉积速率。
5. 气泡问题:气泡是常见的问题,会导致镀层质量下降。
6. 机械因素:如搅拌、气流等,也会影响到电镀质量。
四、电镀级别氯化镍的应用领域1. 机械制造业:氯化镍电镀层具有较好的耐磨性和耐腐蚀性,广泛应用于机械制造业中。
2. 汽车制造业:汽车零部件表面处理中常用氯化镍电镀技术,以提高其耐腐蚀性和硬度。
3. 航空航天工业:氯化镍电镀技术在航空航天工业中也得到了广泛应用,以提高金属表面的抗磨损性能和抗腐蚀性能。
铝合金表面处理技术规范-艾默生

拉丝+喷砂+阳极氧化质量要求拉丝定義拉丝:是一种砂带磨削加工,通过砂带对金属表面进行磨削加工,去除金属表面缺陷,并形成具有一定粗糙度、纹路均匀的装饰表面。
外觀拉丝表面纹路均匀,无划痕、污染、烧伤和腐蚀现象粗糙度按GB10610-89的方法测试其粗糙度Ra应在2.2~3.4um范围以内(垂直于纹路方向上进行测量)喷砂定義喷砂:使制件表面受到喷射砂粒的冲击而进行清理、除锈或粗化的过程。
外觀 喷砂表面文理均匀,无划痕、污染、大理石花纹、腐蚀痕迹或疏松粉末粗糙度按 GB10610-89的方法测试其粗糙度Ra应在 1.5~1.8 m 范围以内。
工艺參數注:推荐的干喷砂工艺如下:材料 --------------------------- 玻璃珠材料规格 --------------------- 100~140 目空气压力 -------------------- 500~700 KPa喷嘴移动速度 -------------- 约 100 mm/s工件表面与喷枪距离 ---- 约 200 mm工件表面与喷枪角度 ---- 约 30°无色化学氧化膜定義无色化学氧化:指氧化膜呈无色状的化学氧化工艺。
外观 1.所有零件都应进行外观检查。
2.氧化膜必须连续、均匀。
完整。
零件表面不允许有划伤、污染、腐蚀痕迹或疏松粉末;3.允许有轻微的夹具印。
焊缝及焊点处不允许膜层发黑。
4.无色化学氧化膜应是铝基底颜色。
耐蚀性无色化学氧化膜按 GB/T 10125-1997 进行100小时的中性盐雾试验;试验后,在每一试片边缘以外的表面上直径不大于0.8 mm的腐蚀点不能多于3个。
接触电阻要求在1kg/mm2的电极压力下,其接触电阻不大于0.9 Ω/mm2。
喷砂光亮无色化学氧化膜定義喷砂光亮无色化学氧化:指经喷砂处理后再进行化学抛光和无色化学氧化的表面处理工艺。
粗糙度按GB10610-89 方法测试其粗糙度 Ra 应在 1.5~1.8um 范围以内。
金属表面处理国家标准
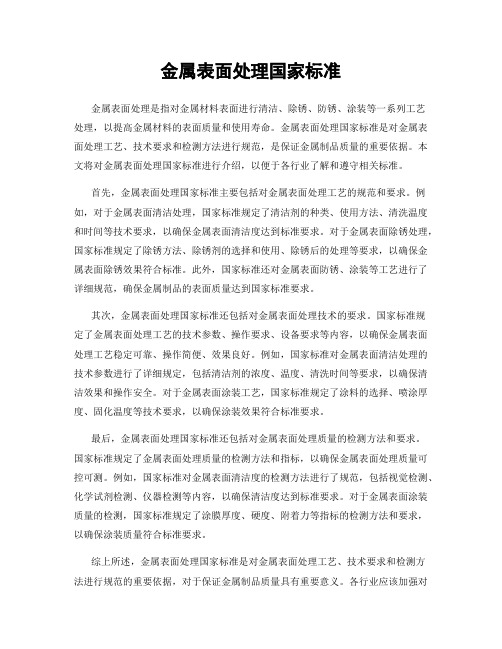
金属表面处理国家标准金属表面处理是指对金属材料表面进行清洁、除锈、防锈、涂装等一系列工艺处理,以提高金属材料的表面质量和使用寿命。
金属表面处理国家标准是对金属表面处理工艺、技术要求和检测方法进行规范,是保证金属制品质量的重要依据。
本文将对金属表面处理国家标准进行介绍,以便于各行业了解和遵守相关标准。
首先,金属表面处理国家标准主要包括对金属表面处理工艺的规范和要求。
例如,对于金属表面清洁处理,国家标准规定了清洁剂的种类、使用方法、清洗温度和时间等技术要求,以确保金属表面清洁度达到标准要求。
对于金属表面除锈处理,国家标准规定了除锈方法、除锈剂的选择和使用、除锈后的处理等要求,以确保金属表面除锈效果符合标准。
此外,国家标准还对金属表面防锈、涂装等工艺进行了详细规范,确保金属制品的表面质量达到国家标准要求。
其次,金属表面处理国家标准还包括对金属表面处理技术的要求。
国家标准规定了金属表面处理工艺的技术参数、操作要求、设备要求等内容,以确保金属表面处理工艺稳定可靠、操作简便、效果良好。
例如,国家标准对金属表面清洁处理的技术参数进行了详细规定,包括清洁剂的浓度、温度、清洗时间等要求,以确保清洁效果和操作安全。
对于金属表面涂装工艺,国家标准规定了涂料的选择、喷涂厚度、固化温度等技术要求,以确保涂装效果符合标准要求。
最后,金属表面处理国家标准还包括对金属表面处理质量的检测方法和要求。
国家标准规定了金属表面处理质量的检测方法和指标,以确保金属表面处理质量可控可测。
例如,国家标准对金属表面清洁度的检测方法进行了规范,包括视觉检测、化学试剂检测、仪器检测等内容,以确保清洁度达到标准要求。
对于金属表面涂装质量的检测,国家标准规定了涂膜厚度、硬度、附着力等指标的检测方法和要求,以确保涂装质量符合标准要求。
综上所述,金属表面处理国家标准是对金属表面处理工艺、技术要求和检测方法进行规范的重要依据,对于保证金属制品质量具有重要意义。
金属表面处理工艺及技术
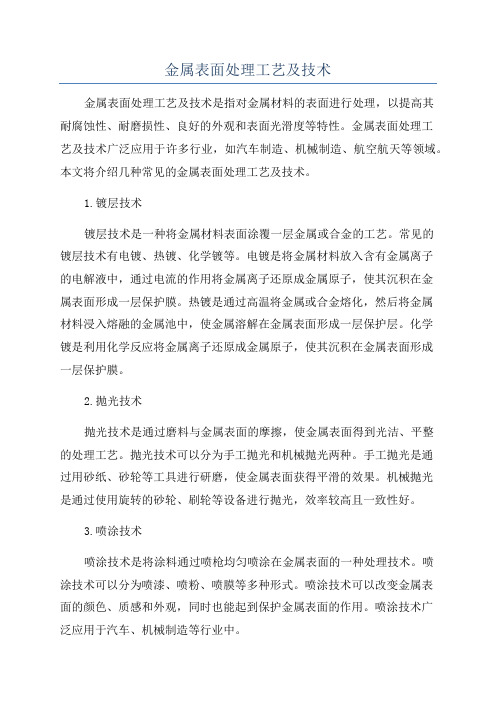
金属表面处理工艺及技术金属表面处理工艺及技术是指对金属材料的表面进行处理,以提高其耐腐蚀性、耐磨损性、良好的外观和表面光滑度等特性。
金属表面处理工艺及技术广泛应用于许多行业,如汽车制造、机械制造、航空航天等领域。
本文将介绍几种常见的金属表面处理工艺及技术。
1.镀层技术镀层技术是一种将金属材料表面涂覆一层金属或合金的工艺。
常见的镀层技术有电镀、热镀、化学镀等。
电镀是将金属材料放入含有金属离子的电解液中,通过电流的作用将金属离子还原成金属原子,使其沉积在金属表面形成一层保护膜。
热镀是通过高温将金属或合金熔化,然后将金属材料浸入熔融的金属池中,使金属溶解在金属表面形成一层保护层。
化学镀是利用化学反应将金属离子还原成金属原子,使其沉积在金属表面形成一层保护膜。
2.抛光技术抛光技术是通过磨料与金属表面的摩擦,使金属表面得到光洁、平整的处理工艺。
抛光技术可以分为手工抛光和机械抛光两种。
手工抛光是通过用砂纸、砂轮等工具进行研磨,使金属表面获得平滑的效果。
机械抛光是通过使用旋转的砂轮、刷轮等设备进行抛光,效率较高且一致性好。
3.喷涂技术喷涂技术是将涂料通过喷枪均匀喷涂在金属表面的一种处理技术。
喷涂技术可以分为喷漆、喷粉、喷膜等多种形式。
喷涂技术可以改变金属表面的颜色、质感和外观,同时也能起到保护金属表面的作用。
喷涂技术广泛应用于汽车、机械制造等行业中。
4.钝化技术钝化技术是通过在金属表面形成一层钝化膜,使金属材料具有较好的耐腐蚀性能。
钝化技术可以分为化学钝化和电化学钝化两种形式。
化学钝化利用化学反应在金属表面形成一层钝化膜,电化学钝化则通过电流的作用,在金属表面形成一层保护层。
5.涂层技术涂层技术是将一层涂料覆盖在金属表面,以提高金属的耐磨、耐腐蚀等性能。
涂层技术可以分为喷涂、涂装、热喷涂等多种形式。
喷涂是通过喷枪将涂料均匀喷涂在金属表面。
涂装是通过涂刷或滚涂等形式将涂料覆盖在金属表面。
热喷涂是将金属或陶瓷等材料加热至熔融状态,然后通过喷枪将其喷射在金属表面,形成一层保护层。
金属漆工艺 技术要求

金属漆工艺技术要求一、表面处理1.表面应平整、清洁,无油污、尘土、锈迹和其他杂质。
2.对于有涂层的表面,应确保涂层完好,无破损、起泡、变色等现象。
3.对于粗糙的表面,应进行打磨处理,以增加涂层的附着力。
二、涂装环境1.涂装环境应保持清洁、干燥、通风良好。
2.温度和湿度应符合涂料产品的要求。
3.在涂装过程中,应避免灰尘、烟雾、水蒸气等对涂装质量产生影响。
三、涂装设备1.涂装设备应完好无损,使用前应进行检修和清洗。
2.涂装设备的运行速度和压力应符合工艺要求。
3.涂装设备应定期维护和保养,以保证其正常运行。
四、涂料选择1.涂料应符合设计要求,选用优质涂料,以保证涂装质量。
2.根据被涂装表面的材质和用途,选择合适的涂料类型和品牌。
3.在选择涂料时,应考虑涂料的干燥速度、耐磨性、耐候性等因素。
五、涂装工艺1.涂装前应对被涂装表面进行预处理,如打磨、除尘等。
2.根据涂料产品的要求,制定合理的涂装工艺流程。
3.在涂装过程中,应对每一道工序进行质量检查,确保涂装质量。
4.涂装完成后,应对涂层进行养护,以保证其使用寿命。
六、涂层质量1.涂层表面应平整、光滑,无气泡、裂纹等现象。
2.涂层的厚度应符合设计要求,涂层均匀、完整。
3.涂层的附着力应符合要求,无脱落现象。
4.涂层的耐磨性、耐候性等性能应符合设计要求。
七、涂层保护1.在涂层未完全干燥之前,应避免水蒸气、雨雪等对涂层产生影响。
2.在使用过程中,应避免硬物刮擦、碰撞等对涂层造成损伤。
3.对于需要长时间暴露在外的涂层,应定期进行清洁和维护,以延长其使用寿命。
八、安全与环保1.在涂装过程中,应遵守安全操作规程,佩戴防护用品,避免涂料泄漏、溅出等对人员和环境造成危害。
2.涂装设备应配置环保设施,如废气处理装置、废水处理装置等,确保涂装过程中的废气、废水等符合环保标准。
3.对于使用过的涂料包装物、废料等应进行分类收集,并按照相关规定进行处置,避免对环境造成污染。
九、质量检测与控制1.在涂装过程中,应按照相关标准和设计要求对涂层进行质量检测,如涂层厚度测量、附着力测试等。
金属表面处理标准工艺有哪些常见金属表面处理方法
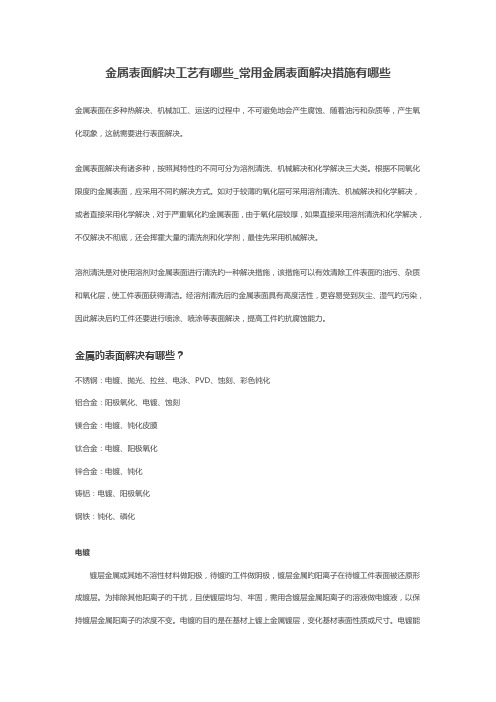
金属表面解决工艺有哪些_常用金属表面解决措施有哪些金属表面在多种热解决、机械加工、运送旳过程中,不可避免地会产生腐蚀、随着油污和杂质等,产生氧化现象,这就需要进行表面解决。
金属表面解决有诸多种,按照其特性旳不同可分为溶剂清洗、机械解决和化学解决三大类。
根据不同氧化限度旳金属表面,应采用不同旳解决方式。
如对于较薄旳氧化层可采用溶剂清洗、机械解决和化学解决,或者直接采用化学解决,对于严重氧化旳金属表面,由于氧化层较厚,如果直接采用溶剂清洗和化学解决,不仅解决不彻底,还会挥霍大量旳清洗剂和化学剂,最佳先采用机械解决。
溶剂清洗是对使用溶剂对金属表面进行清洗旳一种解决措施,该措施可以有效清除工件表面旳油污、杂质和氧化层,使工件表面获得清洁。
经溶剂清洗后旳金属表面具有高度活性,更容易受到灰尘、湿气旳污染,因此解决后旳工件还要进行喷涂、喷涂等表面解决,提高工件旳抗腐蚀能力。
金属旳表面解决有哪些?不锈钢:电镀、抛光、拉丝、电泳、PVD、蚀刻、彩色钝化铝合金:阳极氧化、电镀、蚀刻镁合金:电镀、钝化皮膜钛合金:电镀、阳极氧化锌合金:电镀、钝化铸铝:电镀、阳极氧化钢铁:钝化、磷化电镀镀层金属或其她不溶性材料做阳极,待镀旳工件做阴极,镀层金属旳阳离子在待镀工件表面被还原形成镀层。
为排除其他阳离子旳干扰,且使镀层均匀、牢固,需用含镀层金属阳离子旳溶液做电镀液,以保持镀层金属阳离子旳浓度不变。
电镀旳目旳是在基材上镀上金属镀层,变化基材表面性质或尺寸。
电镀能增强金属旳抗腐蚀性(镀层金属多采用耐腐蚀旳金属)、增长硬度、避免磨耗、提高导电性、润滑性、耐热性、和表面美观。
电泳电泳是电泳涂料在阴阳两极,施加于电压作用下,带电荷涂料离子移动到阴极,并与阴极表面所产生之碱性作用形成不溶解物,沉积于工件表面。
电泳表面解决工艺旳特点:电泳漆膜具有涂层丰满、均匀、平整、光滑旳长处,电泳漆膜旳硬度、附着力、耐腐、冲击性能、渗入性能明显优于其他涂装工艺。
铝合金表面处理技术规范标准
铝合金表面处理技术规艾默生网络能源修订信息表目录目录 (3)前言 (5)一、铝合金化学氧化技术规 (6)1目的 (6)2 适用围 (6)3 关键词 (6)4引用/参考标准或资料 (6)5 规容 (6)5.1 术语 (6)5.2 工艺鉴定要求 (7)5.2.1 总则 (7)5.2.2 设计要求 (7)5.2.3 鉴定程序 (7)5.2.4 试验及试片要求 (7)5.2.5 试验方法及质量指标 (8)5.2.6 鉴定状态的保持 (8)5.3 产品质量检验要求 (8)5.3.1 外观 (8)5.3.2 耐蚀性 (8)二、铝合金喷砂光亮阳极化技术规 (9)1目的 (9)2 适用围 (9)3 关键词 (9)4 引用/参考标准或资料 (9)5 规容 (10)5.1 术语 (10)5.2 工艺鉴定要求 (10)5.2.1 总则 (10)5.2.2 设计要求 (10)5.2.3 鉴定程序 (10)5.2.4 试验及试片要求 (10)5.2.5 试验方法及质量指标 (11)5.2.6 鉴定状态的保持 (11)5.3 产品质量检验要求 (11)5.4 备注 (12)6 附录1 (12)三、喷砂及拉丝技术规 (12)1目的 (12)2 适用围 (13)3 关键词 (13)4引用/参考标准或资料 (13)5 规容 (13)5.1 术语 (13)5.2工艺鉴定要求 (13)5.2.1 总则 (13)5.2.2 设计要求 (14)5.2.3 鉴定程序纪律 (14)5.2.4 试验及试片要求 (14)5.2.5 试验方法及质量指标 (15)5.2.6 鉴定状态的保持 (15)5.3 产品质量检验要求 (15)5.3.1 拉丝件 (15)5.3.2 喷砂件: (15)前言本规由艾默生网络能源研发部发布实施,适用于本公司的产品设计开发及相关活动。
本规由结构造型设计中心部门遵照执行。
本规拟制部门:结构造型设计中心;本规拟制人:士杰;本规批准人:运清;一、铝合金化学氧化技术规1目的本规规定了铝合金化学氧化的工艺要求及其质量要求。
金属表面喷涂处理工艺【详解】
金属表面涂装一般分为两部份:一是涂装前金属的表面处理,也叫前处理技术;二是涂装的施工工艺。
表面处理是通过化学反应的方式进行除油、除锈、清洁的过程,表面处理得好与坏直接影响涂装的质量,金属工件的防锈能力和寿命,是一个不可忽视的重要环节。
涂装施工是把油漆喷涂、刷涂、滚涂等方式附着在金属表面的过程,对金属进行保护和装饰。
金属表面涂装工艺如下1.准备工作,准备好要涂装的金属工件,检查其表面是否有毛刺,如有应进行打磨毛刺。
2. 脱脂处理,又称除油,指把润滑油、防锈油、泥土等杂物从金属表面除掉的过程。
一般采用隔油池和除油池。
脱脂的方法有:有机溶剂脱脂、化学脱脂、电化学脱脂。
3. 热水洗,把金属表面的碱性溶液用热水清洗干净。
4. 冷水洗5. 酸洗,又称除锈,利用酸溶液去除金属表面上的氧化皮和锈蚀物的方法称为酸洗。
氧化皮、铁锈等铁的氧化物(Fe3o4,Fe2o3,Feo等)与酸溶液发生化学反应,形成盐类溶于酸溶液中而被除去。
酸洗常用的酸为:盐酸、硫酸、硝酸、磷酸、氢氟酸。
在酸洗时务必加入酸洗缓蚀剂,防止酸对金属的腐蚀。
6. 冷水洗7. 中和,如果偏碱性,就用强酸调节pH=7,如果偏酸性就用强碱调节PH=7。
8. 冷水洗9. 磷化处理,磷化工艺过程是一种化学与电化学反应形成磷酸盐化学转化膜的过程,所形成的磷酸盐转化膜称之为磷化膜。
10. 冷水洗11. 热水洗12. 干燥13. 喷涂前检查,喷涂前应检查金属工件表面是否有凹凼、批挂,如有应进行补腻子和打磨。
14. 底漆的调配,准备好调缸,底漆先充分搅拌均匀,加入一定数量的底漆到调缸,再按比例加入固化剂搅拌均匀,最后进入稀释剂调整粘度,用180目过滤布过滤,静止10min后即可喷涂。
15. 面漆喷涂前检查,查看底漆是否平整光滑,如果表面粗糙,应用600目的砂纸打磨平整。
16. 面漆的调配,准备好干净的调缸,充分搅拌面漆,加入一定数量的底漆到调缸,再按比例加入固化剂搅拌均匀,最后进入稀释剂调整粘度,用200目过滤布过滤,静止15min后即可喷涂。
金属表面处理项目简介
金属表面处理项目简介立项备案是指在进行一个项目之前,需要经过立项审核,并将项目的基本情况和申请理由写成备案材料,提交给上级部门进行审批。
在金属表面处理项目的立项备案申请中,需要详细描述项目的背景、目标和计划,并提供相关的技术和经济分析,以便上级部门能够评估项目的可行性和必要性。
以下是一个金属表面处理项目的立项备案申请的简介,供参考。
一、项目背景和意义金属表面处理是一项用于提高金属材料表面性能的技术,包括清洗、涂覆、电镀等工艺。
在当前经济发展和工业制造中,金属材料广泛应用于各个领域,而金属材料的表面性能往往决定了其整体品质和使用寿命。
因此,开展金属表面处理项目具有重要的意义和巨大的市场需求。
当前,我市的金属表面处理工艺落后,无法满足市场需求和企业发展的需要,存在着质量不稳定、成本高昂、环境污染等问题。
为了解决这些问题,提高企业的竞争力和产品质量,推动我市金属制造业的升级和发展,本项目拟在我市投资兴建一条先进的金属表面处理生产线,以满足市场需求和企业发展的需要。
二、项目目标和计划本项目的目标是建设一条年处理金属材料1000吨的金属表面处理生产线。
该生产线将采用先进的清洗、涂覆和电镀工艺,并引进先进的设备和技术,以提高金属材料的表面质量和性能。
通过项目的实施,预计可以提高金属材料的质量稳定性、降低生产成本、减少环境污染,为企业提供高品质、低成本的金属表面处理服务。
项目计划分为四个阶段进行:1.前期准备阶段:完成项目方案的策划、技术准备、市场调研和资金筹集等工作,预计耗时3个月;2.设备安装与调试阶段:选购所需设备和技术,并进行安装、调试和培训工作,预计耗时6个月;3.试生产和改进阶段:进行试生产,并持续改进技术和工艺,以提高产品质量和生产效率,预计耗时9个月;4.正式生产阶段:正式投入生产,对产品进行大规模生产,并持续改进和优化,预计耗时36个月。
三、技术和经济分析本项目采用先进的金属表面处理技术和设备,可以提高金属材料的表面质量和性能,并降低生产成本。
金属表面处理标准说明及各种标准比较
金属表面处理标准说明及各种标准比较编写:审核:1.金属的表面处理标准GB8923-88 中国国家标准ISO8501-1:1988 国际标准化组织标准SIS055900-1967 瑞典标准SSPC-SP2,3,5,6,7和10 美国钢结构涂装协会表面处理标准 BS4232 英国标准DIN55928 德国标准JSRA SPSS 日本造船研究协会标准2.各种金属表面处理标准说明2.1 金属表面处理中影响最大的标准是瑞典标准SIS 05 5900 1967,该标准最早由瑞典腐蚀研究所、美国测试和材料协会(ASTM)和钢结构涂装协会(SSPC)联合制定。
其它国家的标准,比如德国DIN 55928、丹麦DS 2019 等都是在此基础上建立起来的。
瑞典标准现在已经与国际标准ISO 8501-1:1988合并且由后者取代。
2.2 ISO8501则是现在普遍采用的国际标准。
美国由于科技力量的强大,SSPC/NACE是他们使用的主要标准而不使用ISO国际标准,并且随着NACE 在全球推广涂装检查培训认证,以及很多钢结构设计机构也使用这一标准,因此在中国也经常会遇到并使用SSPC/NACE标准。
2.3 中国的国家标准GB8923等效采用于ISO8501-1:1988。
3.国标GB8923-88 的除锈等级3.1 喷射或抛射除锈以字母“Sa”表示。
本标准订有四个除锈等级:3.1.1 Sa1 轻度的喷射或抛射除锈钢材表面应无可见的油脂和污垢,并且没有附着不牢的氧化皮,铁锈和油漆涂层等附着物。
Sa2 彻底的喷射或抛射除锈钢材表面应无可见的油脂和污垢,并且氧化皮,铁锈和油漆涂层等附着物已基本清除,其残留物应该是附着牢固的。
3.1.2 Sa2.5 非常彻底的喷射或抛射除锈钢材表面应无可见的油脂,污垢,氧化皮,铁锈和油漆涂层等附着物,任何残留的痕迹应仅是点状或条纹状的轻微色斑。
3.1.3 Sa3 钢材表面外观洁净的喷射或抛射除锈钢材表面应无可见的油脂,污垢,氧化皮,铁锈和油漆涂层等附着物,该表面应显示均匀的金属色泽。
- 1、下载文档前请自行甄别文档内容的完整性,平台不提供额外的编辑、内容补充、找答案等附加服务。
- 2、"仅部分预览"的文档,不可在线预览部分如存在完整性等问题,可反馈申请退款(可完整预览的文档不适用该条件!)。
- 3、如文档侵犯您的权益,请联系客服反馈,我们会尽快为您处理(人工客服工作时间:9:00-18:30)。
金属表面处理技术统计
,喷丸,渗碳,渗氮,镀膜
常用电镀技术指标
电镀技术常用术语
电镀层种类
硬铬在严格控制温度与电流密度(较装饰镀铬高)的条件下,从镀铬液中获得的硬度较高、耐磨性好的硬铬层。
乳色铬
通过改变镀铬溶液的工作条件,获得的孔隙少、具有较高抗蚀能力、而硬度较低的乳白色铬镀层。
氧化及钝化
阳极氧化
通常指铝或铝合金制品或零件,在一定的电解液中和特定的工作条件下作为阳极,通过直流电流的作用,使其表面生成一层抗腐蚀的氧化膜的处理过程。
磷化钢铁零件在含有磷酸盐的溶液中进行化学处理,使其表面生成一层难溶于水的磷酸盐保护膜的处理过程。
发蓝钢铁零件在一定的氧化介质中进行化学处理,使其表面生成一层蓝黑色的保护性氧化膜的处理过程。
化学氧化在没有外电流作用下,金属零件与电解质溶液作用,使其表面上生成一层氧化膜的处理过程。
电化学氧化以浸入一定的电解质溶液中的金属零件作为阳极,在直流电作用下,使其表面生成氧化膜的电化学处理过程。
化学钝化在没有外电流作用下,金属零件与电解质溶液作用,使其表面上生成一层钝化膜的处理过程。
电化学钝化以浸入一定电解质溶液中的金属零件作为阳极,在直流电作用下,使其表面生成一层钝化膜的处理过程。
电解
电解在外电流通过电解液时,在阳极和阴极上分别进行氧化和还原反应,将电能变为化学能的过程。
阳极电解以零件作为阳极的电解过程。
阴极电解以零件作为阴极的电解过程。
镀前处理
化学除油在含碱的溶液中,借助皂化和乳化作用,除去零件或制品表面油垢的过程。
有机溶剂除油利用有机溶剂对油垢的溶解作用,除去零件或制品表面油垢的过程。
电化学除油(即电解除油)在含有碱的溶液中,以零件作为阳极或阴极,在电流作用下,除去零件或制品表面油垢的过程。
化学酸洗在含酸的溶液中,除去金属零件表面的锈蚀物和氧化物的过程。
化学抛光金属零件在一定组成的溶液中和特定条件下,进行短时间的浸蚀,从而将零件表面整平,获得比较光亮的表面的过程。
磨光利用磨轮来磨削零件表面上的粗糙不平处,从而提高零件表面的平整程度的过程。
机械抛光借助于粘有精细磨料和抛光膏的高速抛光轮,对零件进行轻微磨削和整平,从而获得光亮表面的机械加工过程。
喷砂利用净化的压缩空气,将干砂流强烈的喷射到金属零件表面以进行清理或粗化的加工过程。
电镀
电流密度一般指电极(如电镀零件)单位面积表面通过的电流值,通常用A/dm2作为度量单位。
极化通常指直流电流通过电极时,电极电位偏离其平衡电位的现象。
在电流作用下,阳极的电极电位向正的方向偏移,称为阳极极化;阴极的电极电位向负的方向偏移,称为阴极极化。
氢脆零件在电化学除油、强侵蚀、电镀等过程中,由于被还原后的部分氢以原子氢的状态渗入基体金属或镀层中形成应力,使基体金属及镀层的韧性下降而产生脆性的现象。
镀层粗糙由于主盐浓度、镀液pH值、温度与电流密度等控制不当,以及固体杂质过多,所造成的镀层结晶粗大、细微不平的现象
电镀镀层要求
多孔性镀铬(也称松孔镀铬黑铬铬镀层的质量要求
装饰铬镀层:要求外观呈略带蓝色的镜面光亮镀层,结合牢固,镀层完整,亮度基本均匀,允许在不严重影响外观的区域有轻微的夹具印迹,由于材料的表面状态不同,对某此零件允许在同一零件上有稍不均匀的颜色和光泽差别,镀层厚度为0.3~0.5μm。
耐磨铬镀层:要求其镀层厚度应达到图纸要求,结合牢固,镀层基本均匀,颜色和光泽呈稍带蓝色的银白色至亮灰色。
对于复杂件和大型零件允许锐边和棱边有轻微粗糙,但不影响装配质量。
对镀铬后需加工(精磨)的零件,允许镀层有轻微粒子、针孔等经过加工能排除的缺陷。
不允许有严重椭圆度、锥度缺陷。
镀层经精磨后起皮或脱落,需全部磨去铬镀层后重新镀铬。
银
银的性质和银镀层的用途
性质:银是一种容易抛光具有银白色光泽的贵重金属。
导热、导电和光线反射性能极好,同时还有好的耐腐蚀性和焊接性。
用途:银在金属中导电性最好,广泛应用于电子电器、航空、仪器仪表等工业中
银的反光能力强,用于按照灯的反光镜镀银。
银具有银白色美丽光泽而应用于装饰性镀银。
各种化学器皿及仪器也采用镀银,防止其在碱溶液中不受腐蚀。
镀银工艺中,光亮镀银、镀硬银、光亮镀硬银及镀厚银,应用广泛。
镀银工艺分类镀银分为氰化镀银和无氰镀银两类。
镀层的质量要求
银镀层厚度应符合技术条件要求;
银镀层呈银白色,或钝化后呈稍带微黄色,均匀细致,结合力好;银镀层不允许有粗糙、斑点、起泡、脱落、发暗、漏镀和明显条纹;
电镀镀层要求银镀层允许有轻微水迹和夹具印。
铜锡合金
铜锡合金镀层的性质和用途铜锡合金镀层俗称青铜镀层。
按含锡量的多少,可分为低锡青铜镀层(含锡量为2%~15%)、中锡青铜镀层(含锡量为16%~23%)、高锡青铜镀层(含锡量为40%~50%)这三类青铜镀层有其不同的性能和用途。
低锡青铜镀层中,随着含锡量的增加,镀层的色泽由粉红色向金黄。
它的硬度和孔隙率低,具有较高的防蚀性能和抛光性能。
但在空气中易氧化变色,含锡量越低越易变色,所以镀层表面必须套铬。
它作为防护装饰性低镍底层,被广泛用于轻工、手工、机械、仪表和其他工业中。
中锡青铜镀层呈金黄色,它的硬度和抗氧化性比低锡青铜镀层高。
但由于镀层的含锡量较高,作为防护装饰性镀层的底层在套铬后容易发花,所以在生产中应用较少。
高锡青铜镀层,又称白青铜镀层,也称镜铜,呈银白色。
它不易氧化变色,有较高的硬度和耐磨性,经过抛光后有良好的反光性能,能耐有机酸、弱酸、弱碱和硫化物的腐蚀,同时具有良好的钎焊和导电性能。
一般可用来代银代铬作为反光器械、电器零件的接触点、仪器仪表、日用商品等防护装饰镀层。
但由于镀层有细小的裂纹和孔隙,它的抗蚀性能较差,不宜作为在恶劣环境下工作零件的镀层。
另外,镀层的性质较脆。
铜锡合金镀层的质量要求镀层均匀细致,结合力好;镀层不允许有粗糙、斑点、起泡、脱落、海绵状或暗灰色现象;镀层允许零件边缘有轻微的粗糙现象和水迹夹具印。
镍铁合金
镍铁合金镀层的性质与用途镍铁合金镀层呈白色,含铁量一般为10%~30%左右。
镀层具有硬度、光亮度高,延展性、耐蚀性好,内应力低等特性。
镍铁合金镀层还是一种良好的磁性镀层,在电子工业特别是电子计算机工业中有着特殊的用途。
光亮镍铁合金镀层,可以代替光亮镍作为基体的装饰防护性镀层而得到广泛地应用电镀镀层要求采用双层或三层镍铁合金/铬,代替常规的铜/镍/铬装饰性镀层,效果很好,广泛应用于机械、五金、轻工及家电产品中。
镍铁合金电镀的特点
装饰性光亮镍铁合金电镀有如下特点:
镀层中含有30%左右的铁,以廉价的铁代替金属镍,可降低成本。
镀液中金属离子浓度为光亮镀镍液的1/3,既降低了配槽成本,又减少了零件带出损失,同时还减轻了电镀废水的处理量。
不需铜作底层或其他中间层,可以在钢铁件基体上直接电镀,减少了工序。
镀液的整平性、分散能力、覆盖能力、抗杂质离子干扰能力,镀层结合力大,内应力低,硬度、光亮度高,延展性、耐蚀性优良。
工艺范围宽,镀液性能稳定,操作维护方便。
套铬容易。
光亮镀镍液容易转化为镍铁合金镀液。
可代替镀亮镍,消除了因镀液中铁杂质所产生的镀层不良现象。
镍铁合金镀层延展性极好,优于镍镀层,适用于管状零件、深孔零件和其他需要镀后变形加工的零件。
镍铁合金镀层的质量要求
镀层厚度符合技术条件要求;
镀层呈白色、光亮、细致、均匀、结合力好;
镀层不允许有粗糙、斑点、发雾、针孔、桔皮、毛刺、漏镀和明显条纹镀层允许有轻微水迹和夹具印。