微小深孔加工综述
小直径深孔管件加工

心 产 生 的 振 动 ,否 则 会 导 致 加 工 条 件 恶 化 。如 果 对 加 长 扩 孔钻进行技术改造,则有 3 个不利因素:
据悉, 全球车铣复合车床市场由日本主导,其 中仅 M A ZA K 一家便占全球市场一半份额。韩国斗 山 也 已 开 发 出 多 款 车 铣 复 合 车 床 。至 于 台 制 车 铣 复 合车床,则尤其需要加强铣削能力。之前台湾机床 业者曾组成联盟,共同开发出线性马达机床。
台 湾 业 界 将 组 成 车 铣 复 合 车 床 的 研 发 联 盟
面的工作。
收 稿 日 期 :2006- 01- 05
由台湾工业技术研究院机械与系统研究所整 合多 家 台 湾 整 机 厂 、零 部 件 厂 共 同 组 成 的“ 知 慧 型 车 铣 复 合 工 具 机 研 发 联 盟 ”,即 将 正 式 成 立 。
据台湾媒体报导,工研院机械所计划向台湾经 济部科专计划办公室提出完整研发计划,预计涉资 2.45 亿元新台币, 其中 40% 来自科专计划经费,余 下由业者自行筹措。新产品预计可于 2 年后完成。
度,形成化学性润滑油膜,提高润滑效果,降低铰刀和支
承套与零件的摩擦,大大地提高了零件表面的质量。
4 结束语
零件的深孔加工, 都不宜采用高速切削, 一般采用
中 、低 速 切 削 。在 切 削 过 程 中 的 排 屑 是 否 流 畅 与 切 屑 的 形
状 有 关 。如 果 在 切 削 过 程 中 出 现 带 状 和 螺 旋 卷 状 切 屑 ,将
机械加工深孔加工技术

机械加工深孔加工技术汇报人:2024-01-02•深孔加工技术概述•深孔加工的工艺流程•深孔加工的刀具与设备目录•深孔加工的质量控制•深孔加工的难点与解决方案•深孔加工的应用实例01深孔加工技术概述深孔加工技术是指对深度大于孔径的孔进行加工的技术。
定义深孔加工具有加工难度大、技术要求高、需要特殊的加工设备和工艺方法等特点。
特点定义与特点深孔加工在许多领域中都有广泛应用,如航空航天、能源、化工等,是满足产品性能要求的重要手段。
满足产品性能要求采用深孔加工技术可以大大提高生产效率,减少加工时间和成本。
提高生产效率深孔加工技术的精度和表面质量要求高,能够保证产品的质量和可靠性。
保证产品质量深孔加工的重要性深孔加工技术起源于20世纪初,随着工业的发展和技术的不断进步,深孔加工技术也在不断改进和完善。
现代深孔加工技术正朝着高精度、高效率、自动化和智能化的方向发展,未来将会有更多的新材料、新工艺和新设备出现。
深孔加工技术的历史与发展发展趋势历史回顾02深孔加工的工艺流程1 2 3钻孔是深孔加工的起始阶段,主要使用钻头在工件上打孔。
钻孔时需要控制切削速度和进给量,以获得良好的切削效果和孔径精度。
钻孔过程中需要使用冷却液来降低切削温度和润滑钻头。
扩孔是对已钻孔进行扩大直径的加工,以修正孔径偏差或得到所需直径。
扩孔可以使用多种刀具,如扩孔钻、锪钻和车刀等,根据需要选择合适的刀具。
扩孔过程中需要控制切削速度和进给量,以确保孔径精度和表面质量。
01铰孔是对已钻孔进行精加工,以提高孔径精度和表面质量。
02铰孔使用的刀具有多种,如机铰刀、手铰刀和锥铰刀等,根据需要选择合适的刀具。
03铰孔过程中需要控制切削速度和进给量,以确保孔径精度和表面质量。
镗孔可以使用多种刀具,如镗杆、车刀和铣刀等,根据需要选择合适的刀具。
镗孔过程中需要控制切削速度和进给量,以确保孔的形状精度和表面质量。
镗孔是对已钻孔进行进一步加工,以修正孔的轴线偏差和提高孔的形状精度。
机械加工深孔加工技术

02
深孔加工技术分类
枪钻技术
01
02
03
原理
枪钻是利用后角刀刃和切 削部分同时进行切削,实 现钻孔的加工。
特点பைடு நூலகம்
枪钻的刚性和导向性较好 ,可以加工小直径、深孔 和精密孔。
应用
广泛应用于汽车、航空航 天、机床等领域。
BTA深孔钻技术
原理
BTA深孔钻是利用切削液 通过钻头内部通道从钻头 喷出,将切屑从钻头外部 排出,实现深孔加工。
排屑问题
总结词
深孔加工中的排屑问题通常是由于切削过程中产生的切屑堆积、堵塞或排出不畅所引起的。
详细描述
为了解决排屑问题,可以采取多种措施,如优化刀具形状和切削参数、选择合适的冷却液和润滑剂、 使用振动器或超声波装置等。此外,还可以通过改变加工方式或使用专门的排屑装置来避免切屑堵塞 或排出不畅的问题。
加工要求
高精度、高强度、高耐热性
加工过程
应用效果
使用深孔钻进行粗加工和精加工,保证孔 的直径、圆度和表面粗糙度符合要求,并 进行热处理提高零件强度和耐热性
提高发动机性能和安全性,降低维护成本
案例三:某医疗器械零件深孔加工
零件名称
医疗器械微针头
加工要求
高精度、高表面质量、高一致性,微米级 尺寸
加工过程
应用
广泛应用于机械、航空航天等领域 。
挤压钻技术
原理
挤压钻是利用钻头挤压孔壁,使 材料发生塑性变形,实现深孔加
工。
特点
挤压钻具有加工硬化层浅、工件 表面质量好等优点,但需要较大
压力和较强的刚性支撑。
应用
广泛应用于机械、航空航天等领 域。
03
深孔加工机床与工具
深孔加工技术研究综述
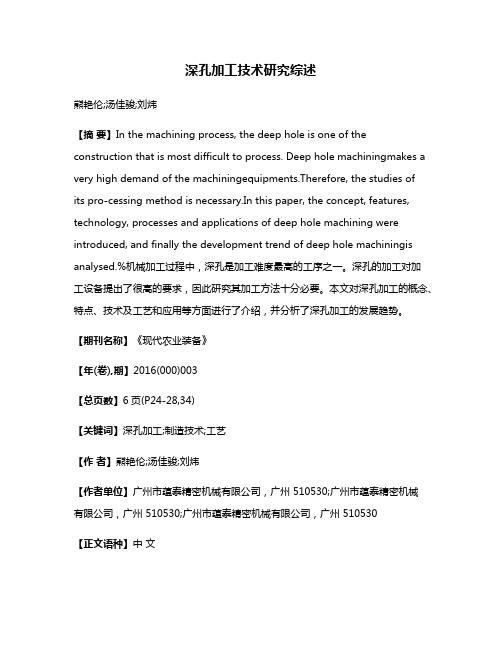
深孔加工技术研究综述熊艳伦;汤佳骏;刘炜【摘要】In the machining process, the deep hole is one of the construction that is most difficult to process. Deep hole machiningmakes a very high demand of the machiningequipments.Therefore, the studies ofits pro-cessing method is necessary.In this paper, the concept, features, technology, processes and applications of deep hole machining were introduced, and finally the development trend of deep hole machiningis analysed.%机械加工过程中,深孔是加工难度最高的工序之一。
深孔的加工对加工设备提出了很高的要求,因此研究其加工方法十分必要。
本文对深孔加工的概念、特点、技术及工艺和应用等方面进行了介绍,并分析了深孔加工的发展趋势。
【期刊名称】《现代农业装备》【年(卷),期】2016(000)003【总页数】6页(P24-28,34)【关键词】深孔加工;制造技术;工艺【作者】熊艳伦;汤佳骏;刘炜【作者单位】广州市蕴泰精密机械有限公司,广州 510530;广州市蕴泰精密机械有限公司,广州 510530;广州市蕴泰精密机械有限公司,广州 510530【正文语种】中文机械加工中的深孔,一般指零件内孔的长度与直径之比大于5的孔,其几何特征决定了它是机械加工中难度最高的加工过程之一。
深孔加工对刀具提出了很高的要求,一般刀具很难同时保证孔的长度和精度要求。
另外,近年来难加工材料(例如高强度合金材料)的运用给深孔加工提出了更高的要求。
小直径深孔加工的探讨

小直径深孔加工的探讨徐良清【摘要】针对小直径深孔加工时常见的棘手现象,通过对切削速度、切削力和走刀量等因素的分析,结合生产实际,提出了预钻锥形孔、定位孔、改善刃形、选取合适的切削速度和走刀量等方法,以解决小直径深孔加工困难的问题.【期刊名称】《现代制造技术与装备》【年(卷),期】2011(000)001【总页数】2页(P51-52)【关键词】深孔加工;偏摆;烧伤【作者】徐良清【作者单位】广东省第二农机厂,乐昌,512219【正文语种】中文目前,钻孔加工一般分钻削和镗削两种方法,对于一般直径比较大、孔深比较浅的孔来说比较适合采用镗削加工,而对于直径较小、孔深较深的孔(直径小于等于4mm、深径比大于等于10mm)较适合钻削加工。
钻削加工过程是半封闭的,钻头工作部分大多处在已加工表面的包围中,冷却条件差,因此加工较困难。
由于钻头工作的部位处于已加工面的包围之中,不容易散热,会使钻头的磨损很快,影响加工质量和钻头寿命。
尤其是小直径深孔的加工更为突出,主要表现在以下几个方面:(1)钻头易被折断或卡死;(2)钻头偏摆,不易定心;(3)钻头烧伤,加工表面质量差。
钻头被折断或卡死是这类加工中常见的现象。
这是因为加工小孔时,要求主轴转速较高,钻头承受的切削力(尤其是径向力)很大,即钻头承受的扭矩过大。
同时,由于钻头小,其两个主切削刃在刃磨时很难保证绝对对称,因此加工的钻头承受的径向切削力不均匀,极易造成钻头折断。
另外,钻头越小,刚度和强度越低,抗扭矩能力越差,并且钻头的螺旋槽越窄,铁屑很容易将螺旋槽堵塞,阻碍加工。
同时钻头较细,深入工件内部长度过长,两侧主切削刃很难保证绝对对称,钻头在加工过程中承受的径向切削力不对称,致使钻头受到的径向力不对称,会引起钻头被卡死,甚至折断。
在加工中,我们通常采取以下措施减缓以上问题。
卡死是这类加工中最主要的现象,这是因为钻头承受的扭力过大,即径向力过大。
钻头所受径向力来自两方面,一方面是钻尖部分的切削力,另一方面来自于钻头棱边与孔壁的摩擦。
微小深孔加工技术

电火花加工
基于高速主轴深小孔电火花加工技术研究 李震 - 哈尔滨工业大学 - 2013
基于3R高速主轴的微细电火花机床实物图
电火花加工
优势: (1)可以加工任何导电材料,不受工件材料的强度和 硬度限制。 (2)可在斜面上加工盲孔、深孔、斜孔及异型孔等。 (3)加工过程中切削力很小,对工具的强度和刚度要 求较低, 可加工直径小于等于10μm的微孔。 存在问题: 电火花穿孔加工的深度有限,这是因为加工的蚀 除物排除困难,丛而引起拉弧阻碍了加工的正常进行 。随着孔的加工深度的增加,拉弧的频率越来越高, 最终使加工无法进行而被迫中断。
微小深孔简介
(a) 、(b)燃气轮机叶片气模微孔; (c)光纤布拉格光栅传感器微孔; (d)用于惯性约 束聚变的靶球微孔; (e)发动机喷油嘴微孔; (f)马赫-曾德尔干涉仪传感器小孔主要的加工方法
微小孔的机械加工主要采用钻削的形式, 特种 加工主要有:电解加工、电火花加工、激光加工、 超声加工、电子束加工等。
电解加工
盐溶液管电极电解加工钛合金深小孔 曾永彬,张玉冬,房晓龙,... - 《电加工与模具》 - 2014
管电极为外径1.2mm、 内径0.8mm、长100mm的 不锈钢管,绝缘层单边 厚度为 0.025 mm 。阳极 工件为厚度 20mm 的钛合 金块(TC4),电解液为 质 量 分 数 10% 的 NaCl 与 10%的NaNO3混合中性盐 溶液,工作温度保持在 35℃ 。电压 24 V ,占空 比 0.3 , 电 解 液 压 力 0.6MPa , 进 给 速 度 0.6mm/min ,加工的小孔 见 左 图 , 其 孔 径 为 1.69mm,深径比为11.8
电解加工
微小孔的电解加工工艺研究 陈辉,王玉魁,王振龙 - 《电加工与模具》 - 2010
浅析镗床加工小直径深孔方法

浅析镗床加工小直径深孔方法作者:常松来源:《中国科技纵横》2019年第07期摘要:通过对普通卧式镗床加工方法的比较,结合各切削方法的优劣点,并针对小直径深孔的具体状况,制定出合理的加工工艺方法,文中通过对具体实例的加工,提供了一种在普通卧式镗床加工出较高精度的小直径深孔的方法。
关键词:深孔加工;普通镗床;工艺方法中圖分类号:TG53 文献标识码:A 文章编号:1671-2064(2019)07-0100-020 前言深孔是指孔的长度与孔的直径比大于5的孔,深孔加工中普通深孔大多数情况下深径比会超过100,如常见的油缸孔、主轴的轴向油孔等。
这些深孔中,有些要求加工尺寸精度和表面质量较高,有些被加工材料的切削加工性能较差,成为了生产加工中一个常见的难题。
深孔的加工有很多的不利因素,比如孔深不能看到加工时的状况,只能凭操作者的经验来判断具体情况,看断屑大小及颜色、听刀具切削时的杂音变化、手摸感觉工件局部升温等手段不好具体把控加工精度,还有就是孔深排屑的问题,如果不能控制断屑的形状和长度,就会造成切屑堵塞,损伤刀具和孔壁,还有就是刀杆直径的选用受加工孔径的限制较大,刀杆的直径越小,长度越长,刀杆刚性和强度就越差,加工时会造成刀杆发颤、加工孔壁有波纹等状况,使深孔的尺寸精度、形位公差及表面粗糙度难以保证。
因此深孔的深径比比值越大,加工精度要求越高,深孔加工难度就越大。
1 镗床加工的工艺特点比较在机械加工制造企业中,普通卧式镗床是一种比较常见的多功能机床。
下面就普通卧式镗床加工小直径深孔的工艺方案做些简单分析。
对镗床来说,有多种切削手段来完成深孔加工,但最主要是钻削、扩孔、镗削、铰削等,在生产加工中,这几种切削方法都有其各自的特点:1.1 钻削普通镗床钻削多使用麻花钻,麻花钻是制造业中最常用的钻孔工具,在其钻孔时,一次连续进给可钻出的孔深,一般不超过孔径的3-5倍就必须退刀排屑,避免切削刃升温、切屑阻塞而损伤钻头和工件。
微小深孔加工技术

电解加工
微小孔的电解加工工艺研究 陈辉,王玉魁,王振龙 - 《电加工与模具》 - 2010
微小孔电解及电极加工装置示意图
电解加工
微小孔的电解加工工艺研究 陈辉,王玉魁,王振龙 - 《电加工与模具》 - 2010
电解加工的微细电极
分别在H2SO4 和NaClO3+EDTA 溶液加工的孔
分别在NaCl 和NaClO3 溶液中加工的孔
激光加工
存在问题: 与电火花、超声、电解加工相比,激光加工设备 价格较贵,加工出的小孔粗糙度大,易形成喇叭口, 圆度较差,精度较低。
超声加工
超声波发生器 产生的超声通过超 声换能器产生高频 的纵向振动,并借 助变幅杆将振幅放 大,驱动工具电极 作超声振动,使得 工作液中悬浮的磨 粒以很大的速度和 加速度不断的撞击 加工区,使该处材 料变形,直至击碎 成微粒和粉末。
(a)高速飞秒激光单脉冲打孔示意图;(b)加工结果原子力显微镜图
激光加工
飞秒激光微孔加工 夏博,姜澜,王素梅,... - 《中国激光》 - 2013 需要多个脉冲的连续作用使得微孔深度不断增 加,以达到所需深度,即所谓的叩击式加工。
不同脉冲个数的激光(150fs,800nm,3.0J/cm2)对聚碳酸酯材料微孔加工的SEM图
5mm 深小孔整体剖面图
电解加工
用高转速微电极电解钻削深小孔 刘勇,曾永彬 - 《光学精密工程》 - 2014
当螺旋电极 绕轴心作高速旋 转时,由于高速 转动螺旋沟槽的 带动作用,电极 周围区的水流迅 速形成轴对称立 轴旋涡流。
加工原理图
电解加工
用高转速微电极电解钻削深小孔 刘勇,曾永彬 - 《光学精密工程》 - 2014
电火花加工
基于高速主轴深小孔电火花加工技术研究 李震 - 哈尔滨工业大学 - 2013
- 1、下载文档前请自行甄别文档内容的完整性,平台不提供额外的编辑、内容补充、找答案等附加服务。
- 2、"仅部分预览"的文档,不可在线预览部分如存在完整性等问题,可反馈申请退款(可完整预览的文档不适用该条件!)。
- 3、如文档侵犯您的权益,请联系客服反馈,我们会尽快为您处理(人工客服工作时间:9:00-18:30)。
na of tool breakage often occurred in the drilling process, and to some difficult-to-machinematerials, traditional drilling tools
had low efficiency or
lasermachining combined machining
在 机 械 制 造 行 业 众 多 零 件 的 加 工 中 ,深孔 及微 小深孔加工历来是被人们广泛关注的问题之一。对 小孔、微小孔、微小深孔的定义一般为:小孔的孔径 为 0. 1!3. 0 mm;微小孔的孔径<0. 1 mm;深孔定
even
was
useless at
all.
Aimed at th esh ortcom in gsof traditionalm achiningm ethods, sp
ning methods were developed , such as electric discharge machining , electrochemical machining , uItrasonic machining , laser
Abstract: tt has always been one of
the
concerns of the manufacturing industry for the
micro deep
hol
chanical drilling was the most effective method in traditional machining, bu tw ith the development of the material science,
综述
歡小深孔加工综述"
刘 泽 祥 ,张 斌
( 泰 州 职 业 技 术 学 院 机 电 技 术 分 院 ,江 苏 泰 州 225300)
摘 要 :微 小 深 孔 加 工 一 直 是 制 造 业 所 关 注 的 问 题 之 一 。传 统 加 工 方 法 中 最 为 有 效 的 是 机 械 钻 削 加
工 ,但 随 着 材 料 科 学 的 发 展 ,微 小 深 孔 钻 削 过 程 中 出 现 了 瓶 颈 ,如 刀 具 难 以 冷 却 、排 屑 困 难 等 问 题 ,致使微 小 深 孔 加 工 的 深 径 比 小 ,加 工 质 量 差 ,在 钻 削 过 程 中 常 出 现 断 刀 的 现 象 ,而 对 于 一 些 难 加 工 材 料 ,采用传
义为孔深与孔径之比(深 径 比 )> 1 0 的孔[12],在生 产 实 践 中 ,按 照 深 孔 直 径 的 大 小 分 为 特 大 深 孔 (200 m 以上)、大深孔(65〜?2〇0 mm) 、普 通 深 孔 (20 〜多65 mm) 、小 深 孔 〜 多 65 mm)和微小深孔 mm以下)。一 般 而 言 ,微 小 深 孔 和 特 大 深 孔 比 中 、
the problems appeared in the
process of
the
cro-deep holes, such
as the difficulty of
cutting
culty of chip removal and so on, which led to the small ratio of depth to diameter, poor machining quality and the phenome
machining and elec tron beam machining , and the machining principle , machining characteristics and existing short comings
were also summarized. Basedon these, the characteristics of some compos ite machining technology were analyzed. As the
足 进 行 了 综 述 ,在 此 基 础 上 ,分 析 了 各 类 复 合 加 工 技 术 的 特 点 ,在 加 工 技 术 上 取 长 补 短 ,弥补各自所存 在
的不 足 。复合加工技术将在未来制造业 中得 到广 泛应用 。
关 键 词 :微 小 深 孔 ;钻 削 ;电 火 花 加 工 ;电 解 加 工 ;超 声 加 工 ;激 光 加 工 ;复合加工
中 图 分 类 号 :T H 16 文 献 标 志 码 :A
Summary of Micro Deep Holes Machining
LIU Zexiang, ZH A N G Bin
(School of Mechanical and Electrical Technology, Taizhou Polytechnic College, Taizhou 225300, China)
shortcomings were madeup with each other , combined maching will be widely used in the future manufacturing industry.
Keywords :microdeep holes , drilling , electric discharge machining , electrochemical machining , ultrasonic machining ,
统 刀 具 加 工 效 率 低 或 者 根 本 无 法 加 工 。针 对 传 统 加 工 方 法 所 存 在 的 不 足 ,开 发 了 各 类 特 种 加 工 方 法 ,如
电 火 花加工 、电 解加 工 、超 声 加 工 、激 光 加 工 以 及 电 子 束 加 工 等 ,对 其 加 工 原 理 、加 工特 点以 及 所存 在的 不
小直径深孔的加工难度更大(]。 微 小 深 孔 广 泛 应 用 于 航 空 航 天 、军 工 生 产 、液压