直接还原铁海绵铁AC工艺
直接还原铁技术
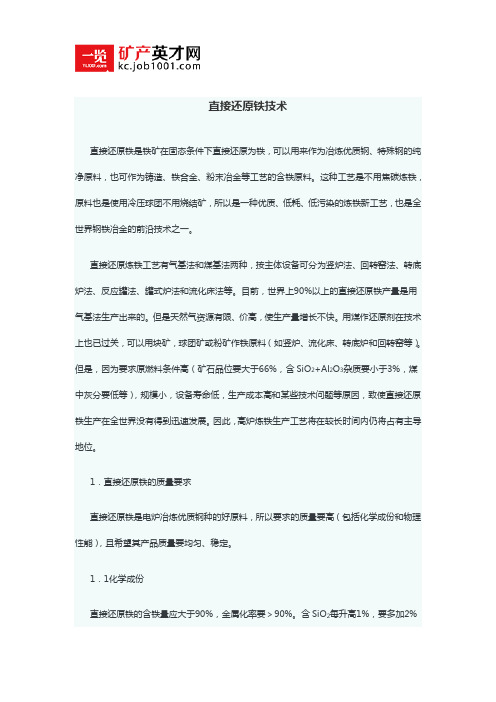
直接还原铁技术直接还原铁是铁矿在固态条件下直接还原为铁,可以用来作为冶炼优质钢、特殊钢的纯净原料,也可作为铸造、铁合金、粉末冶金等工艺的含铁原料。
这种工艺是不用焦碳炼铁,原料也是使用冷压球团不用烧结矿,所以是一种优质、低耗、低污染的炼铁新工艺,也是全世界钢铁冶金的前沿技术之一。
直接还原炼铁工艺有气基法和煤基法两种,按主体设备可分为竖炉法、回转窑法、转底炉法、反应罐法、罐式炉法和流化床法等。
目前,世界上90%以上的直接还原铁产量是用气基法生产出来的。
但是天然气资源有限、价高,使生产量增长不快。
用煤作还原剂在技术上也已过关,可以用块矿,球团矿或粉矿作铁原料(如竖炉、流化床、转底炉和回转窑等)。
但是,因为要求原燃料条件高(矿石品位要大于66%,含SiO2+Al2O3杂质要小于3%,煤中灰分要低等),规模小,设备寿命低,生产成本高和某些技术问题等原因,致使直接还原铁生产在全世界没有得到迅速发展。
因此,高炉炼铁生产工艺将在较长时间内仍将占有主导地位。
1.直接还原铁的质量要求直接还原铁是电炉冶炼优质钢种的好原料,所以要求的质量要高(包括化学成份和物理性能),且希望其产品质量要均匀、稳定。
1.1化学成份直接还原铁的含铁量应大于90%,金属化率要>90%。
含SiO2每升高1%,要多加2%的石灰,渣量增加30Kg/t,电炉多耗电18.5kwh。
所以,要求直接还原铁所用原料含铁品位要高:赤铁矿应>66.5%,磁铁矿>67.5%,脉石(SiO2+Al2O3)量<3%~5%。
直接还原铁的金属化率每提高1%,可以节约能耗8~10度电/t。
直接还原铁含C<0.3%,P<0.03%,S<0.03%,Pb、Sn、As、Sb、Bi等有害元素是微量。
1.2物理性能回转窑、竖炉、旋转床等工艺生产的直接还原铁是以球团矿为原料,要求粒度在5~30mm。
隧道窑工艺生产的还原铁大多数是瓦片状或棒状,长度为250~380mm,堆密度在1.7~2.0t/m3。
无罐还原海绵铁生产线工艺简介
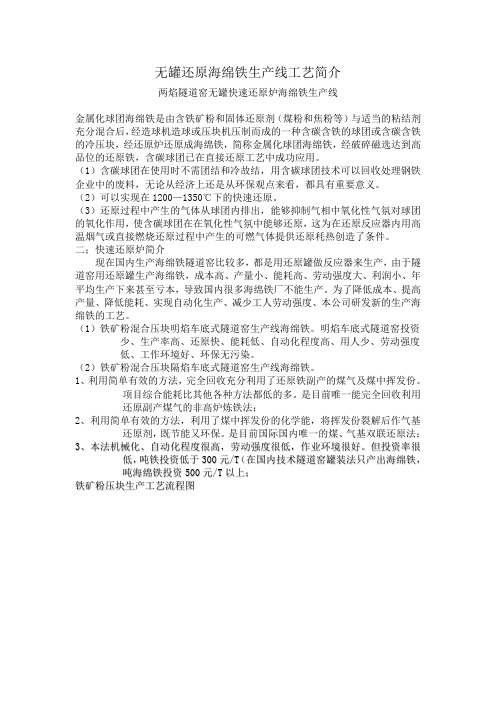
无罐还原海绵铁生产线工艺简介两焰隧道窑无罐快速还原炉海绵铁生产线金属化球团海绵铁是由含铁矿粉和固体还原剂(煤粉和焦粉等)与适当的粘结剂充分混合后,经造球机造球或压块机压制而成的一种含碳含铁的球团或含碳含铁的冷压块,经还原炉还原成海绵铁,简称金属化球团海绵铁,经破碎磁选达到高品位的还原铁,含碳球团已在直接还原工艺中成功应用。
(1)含碳球团在使用时不需团结和冷故结,用含碳球团技术可以回收处理钢铁企业中的废料,无论从经济上还是从环保观点来看,都具有重要意义。
(2)可以实现在1200—1350℃下的快速还原。
(3)还原过程中产生的气体从球团内排出,能够抑制气相中氧化性气氛对球团的氧化作用,使含碳球团在在氧化性气氛中能够还原,这为在还原反应器内用高温烟气或直接燃烧还原过程中产生的可燃气体提供还原秏热创造了条件。
二;快速还原炉简介现在国内生产海绵铁隧道窑比较多,都是用还原罐做反应器来生产,由于隧道窑用还原罐生产海绵铁,成本高、产量小、能耗高、劳动强度大、利润小、年平均生产下来甚至亏本,导致国内很多海绵铁厂不能生产。
为了降低成本、提高产量、降低能耗、实现自动化生产、减少工人劳动强度、本公司研发新的生产海绵铁的工艺。
(1)铁矿粉混合压块明焰车底式隧道窑生产线海绵铁。
明焰车底式隧道窑投资少、生产率高、还原快、能耗低、自动化程度高、用人少、劳动强度低、工作环境好、环保无污染。
(2)铁矿粉混合压块隔焰车底式隧道窑生产线海绵铁。
1、利用简单有效的方法,完全回收充分利用了还原铁副产的煤气及煤中挥发份。
项目综合能耗比其他各种方法都低的多。
是目前唯一能完全回收利用还原副产煤气的非高炉炼铁法;2、利用简单有效的方法,利用了煤中挥发份的化学能,将挥发份裂解后作气基还原剂,既节能又环保。
是目前国际国内唯一的煤、气基双联还原法;3、本法机械化、自动化程度很高,劳动强度很低,作业环境很好。
但投资率很低,吨铁投资低于300元/T(在国内技术隧道窑罐装法只产出海绵铁,吨海绵铁投资500元/T以上;铁矿粉压块生产工艺流程图三.主要工段设备功能简述3.1 隧道车底式快速还原炉还原生产工艺由以下工段组成:1,原料制备及配料系统.2,混料系统.3,压块系统.4,烘干系统.5,隧道式还原炉快速还原系统.6,卸料系统.7,破碎系统8,磁选系统.9,压块工段3.2. 金属化球团海绵铁的配料金属化球团的配料包括四个部分:铁矿粉(铁矿石)、煤粉、脱硫剂和粘结剂。
隧道窑装法生产直接还原铁工艺介绍

隧道窑装法生产直接还原铁工艺介绍隧道窑罐装法生产直接还原铁(海绵铁)是瑞典人在1911年首先用于工业生产直接还原铁(海绵铁)的方法,经过多年的技术发展,已经是一种有效的生产直接还原铁(海绵铁)的方法。
一九九二年河北东瀛有限责任公司在此基础上进行了大量的技术改进和创新,研制开发了新型的隧道窑直接还原铁(海绵铁)生产法。
开创了在我国使用隧道窑生产海绵铁的新纪元,在此后经过不断的改进和完善,形成了无论从投资规模的大与小、无论自动化程度的高与低的系列海绵铁生产工艺,它能满足各种环境、各个区域、各种投资人群的要求,河北东瀛有限责任公司所研制开发的各种工艺无论从投资比例还是投资效益、无论从产品成本还是对原料要求、无论从产品质量还是工艺的成熟性、设备运行的可靠性、稳定性,无论从节能还是环保在我国都是唯一可信赖的、也是遥遥领先的。
它是将精矿粉、煤粉、石灰石粉,按照一定的比例和装料方法,分别装入还原罐中,然后把罐放在罐车上,推入条形隧道窑中或把罐直接放到环形轮窑中,料罐经预热1150℃加热焙烧和冷却之后,使精矿粉还原,得到直接还原铁(海绵铁)的方法。
使用隧道窑直接还原铁(海绵铁)生产工艺已有几十条生产线建成投产。
当精矿粉含铁67%以上时,此法生产的直接还原铁(海绵铁)实物分析结果是:C≥0.04%, S<0.01%, P<0.02%, SiO2<3%, MFe≥86%, TFe≥92% M≥94%。
1.隧道窑生产工艺的特点:(1)原料、还原剂、燃料容易解决此方法所用的原料是精矿粉或品位≥60%的赤铁矿或褐铁矿,这远比富铁块矿好解决,同时,生产中不需要把精矿粉先变成氧化球团,生产费用也低,而且生产中不添加任何粘结剂,这样避免了原料的污染;还原剂是普通无烟煤粉或焦碳末,煤中灰分熔点也不要求很高;供热的燃料是普通动力煤或煤粉,有多余高炉煤气、焦炉煤气、转炉煤气、混和煤气、石油气的地方也可用这些气体做热源,还可使用发生炉煤气或重油作为热源,使用范围十分广阔。
海绵铁新工艺介绍

书山有路勤为径,学海无涯苦作舟
海绵铁新工艺介绍
1. 工艺流程实现全自动化控制,机械化装卸料,采用快速还原炉进行还原、最后形成冷压块铁的直接还原铁(海绵铁)生产工艺方法。
该工艺的工艺流程可分为如下六个工序:
1.1 原料准备及其烘干破碎工序将脱硫剂、还原剂两种物料装入定量料斗,定量料斗按两种物料的重量比,通过输送机将物料送到烘干室内对两物料进行烘干、混合。
烘干后的物料含水量小于3%,烘干后的物料,通过输送机送到还原剂破碎机内进行粉碎,粉碎粒度为1.5mm 以下。
破碎后的物料,经输送机提升到高位料仓,然后再由输送机送到储存料仓。
精矿粉由输送机直接送入烘干机组进行烘干,烘干后含水量小于3%,烘干后的精矿粉由输送机送入高位料仓,然后再由输送机送至储存料仓。
1.2 自动装料工序本工艺根据需要可生产球状、柱状或瓦片状直接还原铁(海绵铁),从保证产品质量,减少生产环节和有利于实现自动装卸料角度考虑,以生产瓦片状为最好。
本工艺采用瓦片状形式。
装料系统由料仓、定量管和装料头三部分组成,精矿粉和还原剂,经过储存料仓,将料卸到布料仓内,再由装料头装入每个还原坩埚,实现向坩埚布料。
1.3 还原焙烧工序此工序在快速还原炉内完成。
适宜稳定的炉温和还原时间是决定直接还原铁(海绵铁)质量的关键,此工序包括预热、还原、冷却三个阶段。
首先,载车经过传动机构,将载车送入快速还原炉内的预热段,在此间,物料中的水分完全蒸发,脱硫剂分解,温度升至还原温度,进入高温还原段,在此间,氧化铁被充分还原,形成单质铁,然后进入冷却段进行冷却,冷却到200℃以下后出炉。
1.4 自动卸料工序物料出炉后在常温中降到100℃~50℃后进入卸料系统进行。
一种基于氨气直接还原铁生产热态海绵铁的方法

一种基于氨气直接还原铁生产热态海绵铁的方法基于氨气直接还原铁生产热态海绵铁的方法热态海绵铁是一种重要的铁素体材料,具有优良的力学性能和物理特性,广泛应用于各个领域。
其中,基于氨气直接还原铁的方法是一种常用的制备热态海绵铁的工艺。
本文将介绍这种方法的原理、步骤和相关工艺参数,以及其在实际应用中的优势和不足之处。
1. 原理:氨气直接还原铁的方法是利用氨气对铁矿石进行还原,生成热态海绵铁。
氨气可以在较低的温度下,与铁矿石中的氧化铁发生反应,产生铁和氮气。
该反应在一定温度范围内进行,且反应速率较快。
2. 步骤:(1)原料准备:将铁矿石粉末和适量氨气载体混合均匀,制备成还原剂。
(2)还原反应:在高温下将还原剂加入反应釜中,同时通入氨气。
随着温度的升高,氨气和还原剂反应,产生铁和氮气。
(3)冷却和分离:将反应产物进行冷却,然后进行分离和筛分,得到热态海绵铁。
3. 工艺参数:(1)反应温度:氨气直接还原铁的反应温度通常在900°C到1200°C之间,具体温度取决于反应物的性质和压力。
(2)氨气流量:氨气的流量对反应的速率和产物的质量也有较大影响,一般选择适宜的流量以获得最佳的反应效果。
(3)反应时间:反应时间是指反应过程的持续时间,可以通过对不同反应时间下得到的产物进行分析和比较来确定最佳反应时间。
4. 优势和不足之处:氨气直接还原铁的方法具有以下优势:(1)反应速率快:由于氨气的强还原性质,反应速率相对较快,可以在相对较短的时间内获得大量的热态海绵铁。
(2)操作简便:方法步骤简单,操作过程相对简便,对设备和人力需求较低。
(3)产品质量高:由于反应温度和氨气流量控制比较容易,可以获得较高质量的热态海绵铁。
然而,氨气直接还原铁的方法也存在一些不足之处:(1)产氮气:反应中会产生大量的氮气,需要进行处理和处理,增加了能源和成本的消耗。
(2)对设备要求高:高温和高压环境对设备的耐受性要求较高,需要相应的设备进行反应。
低污染的无焦炼铁新工艺海绵铁-3页文档资料
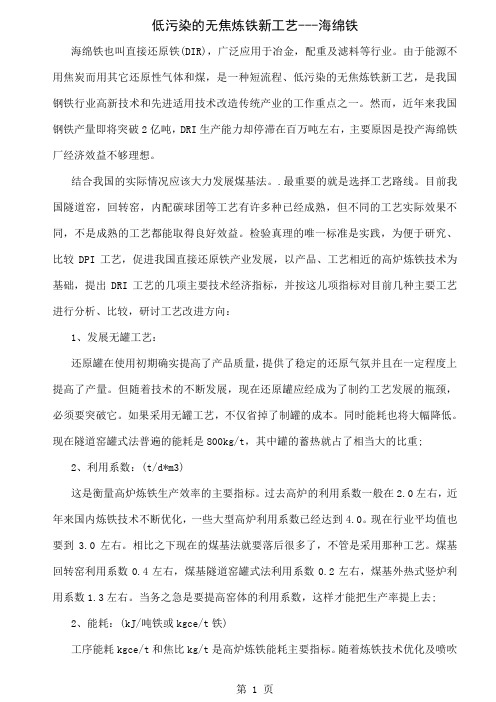
低污染的无焦炼铁新工艺---海绵铁海绵铁也叫直接还原铁(DIR),广泛应用于冶金,配重及滤料等行业。
由于能源不用焦炭而用其它还原性气体和煤,是一种短流程、低污染的无焦炼铁新工艺,是我国钢铁行业高新技术和先进适用技术改造传统产业的工作重点之一。
然而,近年来我国钢铁产量即将突破2亿吨,DRI生产能力却停滞在百万吨左右,主要原因是投产海绵铁厂经济效益不够理想。
结合我国的实际情况应该大力发展煤基法。
.最重要的就是选择工艺路线。
目前我国隧道窑,回转窑,内配碳球团等工艺有许多种已经成熟,但不同的工艺实际效果不同,不是成熟的工艺都能取得良好效益。
检验真理的唯一标准是实践,为便于研究、比较DPI工艺,促进我国直接还原铁产业发展,以产品、工艺相近的高炉炼铁技术为基础,提出DRI工艺的几项主要技术经济指标,并按这儿项指标对目前几种主要工艺进行分析、比较,研讨工艺改进方向:1、发展无罐工艺:还原罐在使用初期确实提高了产品质量,提供了稳定的还原气氛并且在一定程度上提高了产量。
但随着技术的不断发展,现在还原罐应经成为了制约工艺发展的瓶颈,必须要突破它。
如果采用无罐工艺,不仅省掉了制罐的成本。
同时能耗也将大幅降低。
现在隧道窑罐式法普遍的能耗是800kg/t,其中罐的蓄热就占了相当大的比重;2、利用系数:(t/d*m3)这是衡量高炉炼铁生产效率的主要指标。
过去高炉的利用系数一般在2.0左右,近年来国内炼铁技术不断优化,一些大型高炉利用系数已经达到4.0。
现在行业平均值也要到3.0左右。
相比之下现在的煤基法就要落后很多了,不管是采用那种工艺。
煤基回转窑利用系数0.4左右,煤基隧道窑罐式法利用系数0.2左右,煤基外热式竖炉利用系数1.3左右。
当务之急是要提高窑体的利用系数,这样才能把生产率提上去;2、能耗:(kJ/吨铁或kgce/t铁)工序能耗kgce/t和焦比kg/t是高炉炼铁能耗主要指标。
随着炼铁技术优化及喷吹煤粉技术的发展这个指标逐年降低,目前焦比大概是460kg,工序能耗13GJ/t。
直接还原铁生产工艺及发展方向

直接还原铁(海绵铁)生产工艺及发展方向习惯上,我们把铁矿石在高炉中先还原冶炼成含碳高的生铁,而后在炼钢炉内氧化,降低含碳量并精炼成钢,这项传统工艺,称作间接炼钢方法;在低于矿石熔化温度下,通过固态还原,把铁矿石炼制成铁的工艺,称作直接炼铁(钢)法或者直接还原法,用这种方法生产出的铁也就称作直接还原铁(即DRI)。
由于这种铁保留了失氧时形成的大量微气孔,在显微镜下观察形似海绵,所以直接还原铁也称之为海绵铁。
一、直接还原铁(海绵铁)的用途直接还原铁是精铁粉在炉内经低温还原形式的低碳多孔状物质,其化学成分稳定,杂质含量少(碳、硅含量低),主要用作电炉炼钢的原料,也可作为转炉炼钢的冷却剂,如果经二次还原还可供粉末冶金用。
一次还原铁粉(海绵铁)的主要用途有:①作为粉末冶金制品的原料,耗用量约占铁粉总耗用量的60~80%;②作为电焊条的原料,在药皮中加入10~70%铁粉可改进焊条的焊接工艺并显著提高熔敷效率;③作为火焰切割的喷射剂,在切割钢制品时,向氧-乙炔焰中喷射铁粉,可改善切割性能,扩大切割钢种的范围,提高可切割厚度;④还可作为有机化学合成中的还原剂、复印机油墨载体等。
近年来由于钢铁产品朝小型轻量化、功能高级化、复合化方向发展,故钢材中非金属材料和有色金属使用比例增加,致使废钢质量不断下降。
废钢作为电炉钢原料,由于其来源不同,化学成分波动很大,而且很难掌握、控制,这给电炉炼钢作业带来了极大的困难。
如果用一定比例的直接还原铁(30~50%)作为稀释剂与废钢搭配不仅可增加钢材的均匀性,还可以改善和提高钢的物理性质,从而达到生产优质钢的目的。
因此,直接还原铁(海绵铁)不仅仅是优质废钢的替代物,还是生产优质钢材必不可少的高级原料(天津无缝钢管公司国外设计中就明确要求必须配50%的直接还原铁(海绵铁))。
根据国外报导,高功率电炉冶炼时,炉料搭配30~50%直接还原铁,生产率提高10~25%,作业率提高25~30%。
最新低污染的无焦炼铁新工艺海绵铁

低污染的无焦炼铁新工艺海绵铁低污染的无焦炼铁新工艺---海绵铁海绵铁也叫直接还原铁(DIR),广泛应用于冶金,配重及滤料等行业。
由于能源不用焦炭而用其它还原性气体和煤,是一种短流程、低污染的无焦炼铁新工艺,是我国钢铁行业高新技术和先进适用技术改造传统产业的工作重点之一。
然而,近年来我国钢铁产量即将突破2亿吨,DRI生产能力却停滞在百万吨左右,主要原因是投产海绵铁厂经济效益不够理想。
结合我国的实际情况应该大力发展煤基法。
.最重要的就是选择工艺路线。
目前我国隧道窑,回转窑,内配碳球团等工艺有许多种已经成熟,但不同的工艺实际效果不同,不是成熟的工艺都能取得良好效益。
检验真理的唯一标准是实践,为便于研究、比较DPI工艺,促进我国直接还原铁产业发展,以产品、工艺相近的高炉炼铁技术为基础,提出DRI工艺的几项主要技术经济指标,并按这儿项指标对目前几种主要工艺进行分析、比较,研讨工艺改进方向:1、发展无罐工艺:还原罐在使用初期确实提高了产品质量,提供了稳定的还原气氛并且在一定程度上提高了产量。
但随着技术的不断发展,现在还原罐应经成为了制约工艺发展的瓶颈,必须要突破它。
如果采用无罐工艺,不仅省掉了制罐的成本。
同时能耗也将大幅降低。
现在隧道窑罐式法普遍的能耗是800kg/t,其中罐的蓄热就占了相当大的比重;2、利用系数:(t/d*m3)这是衡量高炉炼铁生产效率的主要指标。
过去高炉的利用系数一般在2.0左右,近年来国内炼铁技术不断优化,一些大型高炉利用系数已经达到4.0。
现在行业平均值也要到3.0左右。
相比之下现在的煤基法就要落后很多了,不管是采用那种工艺。
煤基回转窑利用系数0.4左右,煤基隧道窑罐式法利用系数0.2左右,煤基外热式竖炉利用系数1.3左右。
当务之急是要提高窑体的利用系数,这样才能把生产率提上去;2、能耗:(kJ/吨铁或kgce/t铁)工序能耗kgce/t和焦比kg/t是高炉炼铁能耗主要指标。
随着炼铁技术优化及喷吹煤粉技术的发展这个指标逐年降低,目前焦比大概是460kg,工序能耗13GJ/t。
- 1、下载文档前请自行甄别文档内容的完整性,平台不提供额外的编辑、内容补充、找答案等附加服务。
- 2、"仅部分预览"的文档,不可在线预览部分如存在完整性等问题,可反馈申请退款(可完整预览的文档不适用该条件!)。
- 3、如文档侵犯您的权益,请联系客服反馈,我们会尽快为您处理(人工客服工作时间:9:00-18:30)。
直接还原铁(海绵铁)A--C工艺(二)
工艺特点2.1原料、还原剂,燃料容易解决
A—C工艺所用的原料是精矿粉或品位≥60%的赤铁矿或褐铁矿,远比富铁块矿好解决,同时生产中不需要先把精矿粉先变化氧化球团。
生产费用也低,还原剂是普通无烟煤粉或焦碳末,煤中的灰份熔点也不要求很高,供热的热源可为普通动力煤或煤粉,有多余的高炉煤气、转炉煤气,焦炉煤气、混和煤气、石油气的地方也可用这些气体作为热源或用发生炉煤气作热源,还可使用重油作燃料。
2.2工艺稳定
本工艺吸取了各直接还原铁(海绵铁)工艺的优点,并加以改进和创新形成了一种更稳定可靠的新工艺,由于采用封闭式坩埚在还原炉内还原的方法,使坩埚内还原性气氛的浓度和压力都高,并采用计算机控制炉温,温差小,且还原气氛易保持,故很容易保证还原工艺的要求,产品质量稳定。
2.3工艺实用性强
A—C工艺对精矿粉、还原煤的要求不高,实用性强,工艺制度易于控制,操作简单,能较快的稳定产品质量,工人经过培训即可掌握。
2.4成本低、质量稳定
用A—C工艺生产的直接还原铁(海绵铁),每吨铁成本在1600元~2000元之间,吨铁成本较回转窑低50%左右,具有很强的成本优势。
用A—C直接还原铁(海绵铁)生产工艺的工序环节少,每个装料坩埚都经过预热、加热还原、冷却相同的过程,在同样的气氛下,同样容器内,经过同等的时间,出来的产品质量必然是均匀的。
2.5机械化程度高
本工艺选用了机械装卸料系统,替代了传统的人工装卸料,从而减轻了工人的劳动强度,改善了劳动环境,提高了产品质量,降低了产品消耗及产品成本,同时减少用工量,年产10万吨直接还原铁的工厂,全厂劳动定员只有150人,年产30万吨直接还原铁(海绵铁)的工厂,全厂劳动定员只有260人。
2.6自动化程度、生产效率高
本工艺采用了计算机控制系统,自动控制、调节炉温,保证了直接还原铁(海绵铁)的还原工艺要求。
装卸料系统和压块系统的自动控制,提高了工作效率及设备运行的准确性。
2.7采用了机械化的燃烧系统,温度容易控制
用煤气或煤粉做燃料,自动化程度高,便于温度控制,有利于保证产品的质量。
2.8本工艺环保条件好,环保容易达标
本工艺选用了先进的脱硫除尘器、高效率的反吹式扁袋除尘器以及国内先进的节能、低噪声设备,经过采取该措施使尘≤60mg/m3,S02≤480mg/m3,噪声≤65分贝等各项环保指标,均能达到国家环保要求。
另外本工艺没有污水,工作环境干净卫生。
2.9选用碳化硅材质的还原坩埚或金属坩埚,使节用寿命长:
这种坩埚导热性能好,从而缩短了还原时间,提高了产品的质量和产量。
它的使用寿命长达120次以上,且可回收再用:一是可以重新制坩埚,另外还可以破碎作为耐火骨料,所以降低了成本,金属坩埚可用150次以上。
由于这种坩埚强度大、不变形,还有利于实现自动化卸陷料。
2.10采取了对直接还原铁(海绵铁)的钝化处理措施—冷压块:
为了防止产品的再氧化,本工艺对产品进行了钝化处理冷压块。
将密度1.9g/cm3直接还原铁(海绵铁)压制成4.5g/cm3以上的冷压块,作为终产品。
冷压块的实现有效地改善了直接还原铁(海绵铁)的抗氧化性能。
降低了直接还原铁(海绵铁)的吸水性,缩小了体积,有利于直接还原铁(海绵铁)的长期存储和长途运输,同时也提高了钢水的收得率,因此倍受炼钢企业的欢迎,在市场竞争中具有很强的生命力和竞争力。
2.11选用了烟气余热回收系统,提高了热效率:
将炉体烟气余热引至原料烘干机内,进行原材料的烘干,它避免了另设热源的投资,节省了热能的消耗,仅此一项,每年可节能折合标煤11088吨(年产10万吨直接还原铁(海绵铁)规模)。
另外,用烟气余热预热空气(用换热器)到炉内助燃,它不仅带进了大量的物理热,而用改善了炉内燃烧环境,降低了消耗,此项每年可节能折合标煤5760吨(年产10万吨直接还原铁(海绵铁)规模)。
使每吨直接还原铁(海绵铁)工序能耗仅为350公斤标煤。
2.12本工艺采用了自动封闭式装卸料系统,控制了污染,改善了工人的操作环境,使环保能达到国家环保要求。
A—C工艺根据不同的地形、不同的产量布局灵活。
另外装坩埚方式灵活多样,可柱状、球状、也可块状等多种形状。
2.13固定资产投资少
配两座回转窑,年产直接还原铁(海绵铁)30万吨,总投资为十几亿人民币,折合每吨直接还原铁(海绵铁)的投资为4000多元。
唐钢上1260立方米高炉和配套的烧结、焦化,折合吨铁投资又比直接还原铁(海绵铁)的吨投资高10%,而年产10万吨以上的直接还原铁(海绵铁)厂用A—C工艺,直接还原铁(海绵铁)的吨铁投资仅为800元左右,年产30万吨以上的直接还原铁(海绵铁)厂用A—C工艺,直接还原铁(海绵铁)的吨铁投资仅为600元左右。
规模加大投资会更少。
2.14对原料要求低,产品质量好
精矿粉要求:TFe≥67%Si02≤3%S≤0.02%P≤0.05%还原剂要求:灰分≤15%挥发份≤10%固定碳≥75%脱硫剂要求:Ca0≥53%Si02+AL2O3≤3%P2O5≤0.22%S03≤0.5%所有原材料一般均能当地解决。
用该工艺所生产的产品质量为TFe≥92%MFe≥89%M≥94%S≤0.02%P≤0.05%C≥0.04%
2.15产品适用范围广
用该工艺生产的直接还原铁(海绵铁)除可作为生产优质钢的原料外,还可以给粉末冶金厂提供原料,
其产品的金属化率可达99%,而S、P和其它元素都很低。
2.16产品的金属化程度可控制
由于本工艺在物料配比、炉温制度及还原时间上都可以灵活调整,所以根据不同用途或需要,可通过调整生产出不同金属化率的直接还原铁(海绵铁)产品。
2.17产品不易二次氧化
由于物料整个还原过程一直在一个封闭的坩埚内进行,完成还原后,物料随坩埚出炉,在常温环境下冷却,隔绝了直接还原铁与空气的接触。
另外,因罐内有过量的还原剂存在,在冷却初期,还原反应仍在进行,可保持罐内的还原气氛,并呈微正压,同样可阻止外界空气进入罐内,保证了产品的质量,不易被二次氧化。
2.18填充系数高(一般在35%以上)
(注:素材和资料部分来自网络,供参考。
请预览后才下载,期待你的好评与关注!)。