尿素的工艺和职业危害
合成氨及尿素生产危险有害因素分析

合成氨及尿素生产危险有害因素分析1、造气工段造气工段转动设备多、操作上控制点多、受人为因素影响较大、工艺条件相互制约、操作难度大。
介质具有腐蚀、有毒、易燃、易爆的性质(氢气、一氧化碳、甲烷、硫化氢等),并具有引爆的火种;由于机械设备易磨损、易腐蚀、易发生容器的损坏、可燃物质的泄漏等;制气周期短,操作程序要求较严等,极易发生煤气发生炉爆炸、气柜抽瘪和爆炸、人员中毒、伤亡等,它是小氮肥厂中发生事故最多的一个工序。
该工段曾发生过“7.22”夹套爆炸事故。
2、脱硫工段由于半水煤气中的H2、CO、CH4、H2S等都是易燃、易爆、有毒气体。
在生产过程中常会因设备管道泄漏发生着火爆炸,造成人员中毒。
据统计,该工段发生的火灾爆炸中毒事故占小氮肥厂的30%左右。
该工段曾发生过多起着火爆炸事故。
3、变换工段由于半水煤气转化为变换气后,气体中的氢气含量显著增加,高温气体一旦泄漏,遇空气很容易引起燃烧、爆炸;如果设备或系统形成负压,空气被吸入,与煤气混合,形成爆炸性气体,在高温、摩擦、静电等作用下,也会发生爆炸;特别是在检修过程中,如不能对系统有效地隔绝,也极易发生爆炸事故。
该工段曾发生过“4.16”热水饱和塔爆炸事故。
4、碳化工段碳化过程是合成氨原料气净化处理的中间过程,也是生产碳酸氢铵产品的最后工序。
由于碳化反应在常温下进行,压力又不太高,因此安全易被人忽视。
特别是氨水槽、贫液槽,既是常温又是常压,且又与大气相通,一旦遇上火源就会发生爆炸。
此工段的碳化塔检修多,由于不好置换,碳化塔爆炸事故也是小氮肥厂多发事故之一。
该工段曾发生过“8.8”“4.7”爆炸事故。
5、压缩工段在压缩工段由于存在着氢气、一氧化碳、甲烷等易燃易爆气体,它们经压缩加压后,压力和温度都大大提高,其火灾和爆炸的危险性增大了;再加上压缩机在高压状况下长周期运转,易发生机械故障;由于压缩工段在整个合成氨系统中,分别与脱硫、变换、脱碳(碳化)、甲醇、醇烷化(精炼)、合成等工段有密切联系,外工段操作不当,会直接影响压缩机的正常工作,严重时会损坏压缩机。
尿素技术总结1500字
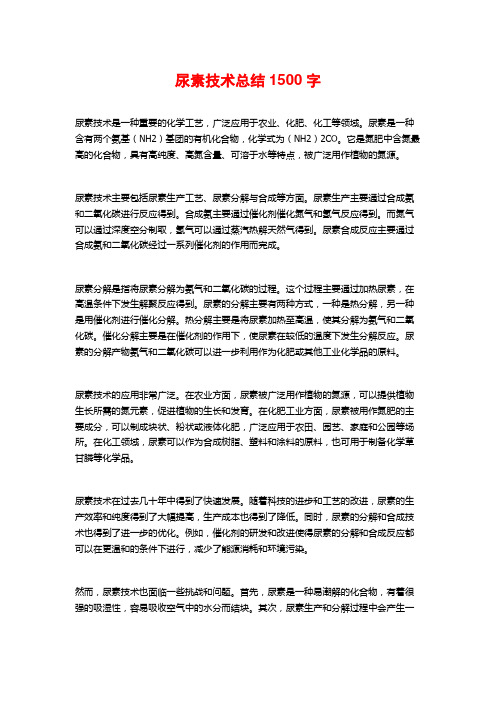
尿素技术总结1500字尿素技术是一种重要的化学工艺,广泛应用于农业、化肥、化工等领域。
尿素是一种含有两个氨基(NH2)基团的有机化合物,化学式为(NH2)2CO。
它是氮肥中含氮最高的化合物,具有高纯度、高氮含量、可溶于水等特点,被广泛用作植物的氮源。
尿素技术主要包括尿素生产工艺、尿素分解与合成等方面。
尿素生产主要通过合成氨和二氧化碳进行反应得到。
合成氨主要通过催化剂催化氮气和氢气反应得到。
而氮气可以通过深度空分制取,氢气可以通过蒸汽热解天然气得到。
尿素合成反应主要通过合成氨和二氧化碳经过一系列催化剂的作用而完成。
尿素分解是指将尿素分解为氨气和二氧化碳的过程。
这个过程主要通过加热尿素,在高温条件下发生解聚反应得到。
尿素的分解主要有两种方式,一种是热分解,另一种是用催化剂进行催化分解。
热分解主要是将尿素加热至高温,使其分解为氨气和二氧化碳。
催化分解主要是在催化剂的作用下,使尿素在较低的温度下发生分解反应。
尿素的分解产物氨气和二氧化碳可以进一步利用作为化肥或其他工业化学品的原料。
尿素技术的应用非常广泛。
在农业方面,尿素被广泛用作植物的氮源,可以提供植物生长所需的氮元素,促进植物的生长和发育。
在化肥工业方面,尿素被用作氮肥的主要成分,可以制成块状、粉状或液体化肥,广泛应用于农田、园艺、家庭和公园等场所。
在化工领域,尿素可以作为合成树脂、塑料和涂料的原料,也可用于制备化学草甘膦等化学品。
尿素技术在过去几十年中得到了快速发展。
随着科技的进步和工艺的改进,尿素的生产效率和纯度得到了大幅提高,生产成本也得到了降低。
同时,尿素的分解和合成技术也得到了进一步的优化。
例如,催化剂的研发和改进使得尿素的分解和合成反应都可以在更温和的条件下进行,减少了能源消耗和环境污染。
然而,尿素技术也面临一些挑战和问题。
首先,尿素是一种易潮解的化合物,有着很强的吸湿性,容易吸收空气中的水分而结块。
其次,尿素生产和分解过程中会产生一些副产物,如二甲基胺、氨基甲酸等,对环境和健康造成一定影响。
尿素生产安全技术
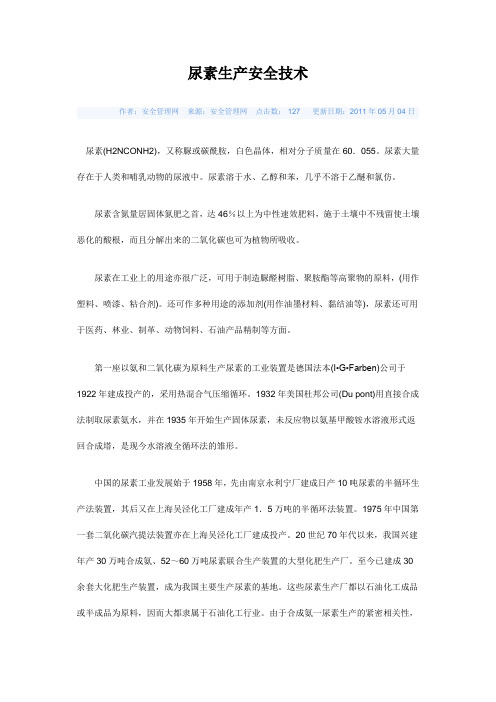
尿素生产安全技术作者:安全管理网来源:安全管理网点击数: 127 更新日期:2011年05月04日尿素(H2NCONH2),又称脲或碳酰胺,白色晶体,相对分子质量在60.055。
尿素大量存在于人类和哺乳动物的尿液中。
尿素溶于水、乙醇和苯,几乎不溶于乙醚和氯仿。
尿素含氮量居固体氮肥之首,达46%以上为中性速效肥料,施于土壤中不残留使土壤恶化的酸根,而且分解出来的二氧化碳也可为植物所吸收。
尿素在工业上的用途亦很广泛,可用于制造脲醛树脂、聚胺酯等高聚物的原料,(用作塑料、喷漆、粘合剂)。
还可作多种用途的添加剂(用作油墨材料、黏结油等),尿素还可用于医药、林业、制革、动物饲料、石油产品精制等方面。
第一座以氨和二氧化碳为原料生产尿素的工业装置是德国法本(I•G•Farben)公司于1922年建成投产的,采用热混合气压缩循环。
1932年美国杜邦公司(Du pont)用直接合成法制取尿素氨水,并在1935年开始生产固体尿素,未反应物以氨基甲酸铵水溶液形式返回合成塔,是现今水溶液全循环法的雏形。
中国的尿素工业发展始于1958年,先由南京永利宁厂建成日产10吨尿素的半循环生产法装置,其后又在上海吴泾化工厂建成年产1.5万吨的半循环法装置。
1975年中国第一套二氧化碳汽提法装置亦在上海吴泾化工厂建成投产。
20世纪70年代以来,我国兴建年产30万吨合成氨、52~60万吨尿素联合生产装置的大型化肥生产厂。
至今已建成30余套大化肥生产装置,成为我国主要生产尿素的基地。
这些尿素生产厂都以石油化工成品或半成品为原料,因而大都隶属于石油化工行业。
由于合成氨一尿素生产的紧密相关性,其生产工艺过程分别介绍如下。
1.合成氨生产氮肥生产的主要过程主要环节是制取氢,而合成氨所需要的氮则直接或间接地来源于空气。
目前世界上大多数的氮肥厂均采用石化原料或其副产品来制取氢或一氧化碳,只有少数厂家采用电解水法制取氢,由于此法受电力成本制约,难以形成大规模的工业化生产。
合成氨及尿素生产危险有害因素分析

合成氨及尿素生产危险有害因素分析首先,合成氨及尿素生产过程中常用的原料是天然气和空气。
天然气是一种易爆易燃气体,一旦发生泄漏或过压现象,可能引发火灾或爆炸事故。
此外,天然气中还含有硫化氢等有毒气体,其高浓度会对人体造成严重伤害。
其次,合成氨的生产过程中需要使用氨合成催化剂。
这种催化剂通常含有一定的金属活性物质,如铑和铱等。
这些金属具有较高的毒性,一旦接触到皮肤、眼睛或吸入到肺部,会引发中毒反应,并对身体造成严重损害。
此外,合成氨的生产过程中也会产生大量的废气和废水。
这些废气中常常含有一些有害物质,如一氧化碳、氮氧化物等。
而排放到大气中的废气会对环境和人体健康造成危害。
废水中可能含有氨氮、氨基酸等物质,若未经处理直接排放,会对水体生态环境造成污染。
此外,合成氨和尿素的生产过程中还会产生大量的粉尘和噪声。
粉尘不仅会影响生产工艺的稳定性,还会对工人的健康产生负面影响。
噪声超过一定的强度,会造成听力损伤并影响工人的工作效率。
在工作环境方面,合成氨和尿素的生产过程中,需要采用高温高压的条件进行反应。
这种条件下,工作环境的温度和压力都较高,容易导致热中暑和中暑等问题,对工人的身体健康造成危害。
此外,由于合成氨和尿素的生产工艺复杂,涉及许多设备和管道,一旦出现设备故障或管道泄漏,可能引发化学物质的泄漏事故。
化学物质的泄漏会对工人和周边环境造成危害,并可能引发火灾、爆炸等严重事故。
综上所述,合成氨和尿素生产过程中存在许多危险有害因素,包括易燃易爆的原料、有毒催化剂、有害气体的排放、废水废气的污染、粉尘噪声的危害、高温高压的工作环境和化学物质泄漏等。
因此,在生产过程中需要采取各种措施,如加强设备的维护和管理、提供个人防护装备、加强环保设施建设和管理等,以减少危害和确保生产过程的安全性。
尿素生产安全技术

尿素生产安全技术前言尿素是一种重要的化学品,广泛应用于化肥、塑料、医药等多个领域。
然而,尿素生产过程中存在着很多的安全风险,例如:化学反应中的火灾爆炸、气体泄漏、跑冒滴漏、粉尘爆炸等。
因此,尿素生产企业应当不断提升自身安全生产能力,以确保生产过程中的安全和稳定。
尿素生产的流程和原理尿素的制备流程一般包括以下几个步骤:1.合成氨生产2.氨气与二氧化碳反应生成尿素3.尿素脱水4.晶体化其中,合成氨生产主要是通过气体反应,使空气中的氮气与天然气中的氢气反应生成氨气。
氨气与二氧化碳反应生成尿素的反应式如下:N2 + 3H2 -> 2NH3NH3 + CO2 -> NH2COONH4尿素脱水一般采用真空蒸发或压力脱水的方法,将尿素水溶液中多余的水分去除。
晶体化是将脱水后的尿素蒸发结晶而成。
尿素生产中的安全隐患和对策火灾爆炸尿素生产过程中,常常涉及到高温高压条件下的各种化学反应。
因此,火灾爆炸是一个常见的安全隐患。
此时,企业应当采取以下的措施:1.设计合理的防火防爆措施:如安装消防设施,建立消防管道系统等。
2.采取必要的安全措施:对于含有易燃、易爆等物质的设备采用特殊的防爆设施,确保操作人员的人身安全。
3.加强员工培训:提高员工的安全意识和应急处理能力,切实做好安全防范工作。
气体泄漏尿素生产中,各种气体的泄漏是另一个值得关注的问题。
如氨气、二氧化碳等气体都具有毒性和易燃爆的特性。
以下是针对气体泄漏的安全措施:1.设置气体检测器:安装气体检测器可以及时发现气体泄漏的存在,避免大规模的事故发生。
2.加强气体管道的维护:保持气体管道的完整性,防止管道老化、腐蚀等导致泄漏的情况发生。
3.做好危险化学品的储存和运输:对危险化学品的储存和运输要求严格,防止针对危险品的严重事故发生。
跑冒滴漏和粉尘爆炸尿素生产过程中,跑冒滴漏和粉尘爆炸也是两个需要特别注意的安全隐患。
以下是对应的预防措施:1.对管道、阀门进行定期检查:在生产运营过程中,检查各管道、阀门、连接件等设备是否完好,做好必要的维修保养,优化设备运作效率,防止跑冒滴漏。
脲安全周知卡、职业危害告知卡、理化特性表
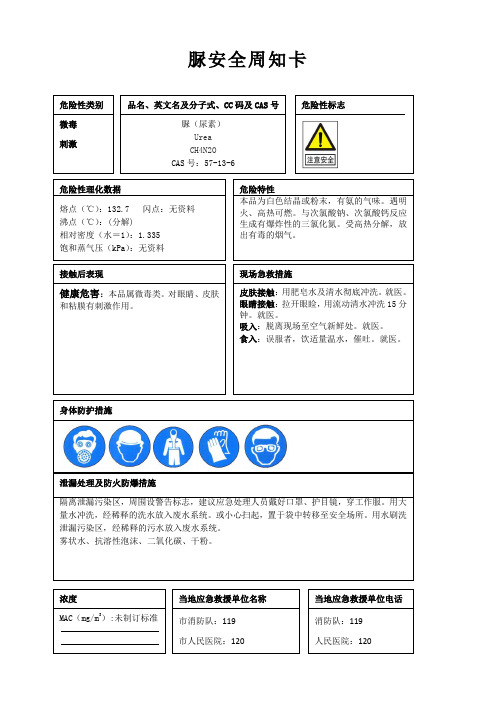
脲安全周知卡危险性类别微毒刺激品名、英文名及分子式、CC码及CAS号脲(尿素)UreaCH4N2OCAS号:57-13-6危险性理化数据熔点(℃):132.7 闪点:无资料沸点(℃):(分解)相对密度(水=1):1.335饱和蒸气压(kPa):无资料危险特性本品为白色结晶或粉末,有氨的气味。
遇明火、高热可燃。
与次氯酸钠、次氯酸钙反应生成有爆炸性的三氯化氮。
受高热分解,放出有毒的烟气。
接触后表现健康危害:本品属微毒类。
对眼睛、皮肤和粘膜有刺激作用。
现场急救措施皮肤接触:用肥皂水及清水彻底冲洗。
就医。
眼睛接触:拉开眼睑,用流动清水冲洗15分钟。
就医。
吸入:脱离现场至空气新鲜处。
就医。
食入:误服者,饮适量温水,催吐。
就医。
身体防护措施泄漏处理及防火防爆措施隔离泄漏污染区,周围设警告标志,建议应急处理人员戴好口罩、护目镜,穿工作服。
用大量水冲洗,经稀释的洗水放入废水系统。
或小心扫起,置于袋中转移至安全场所。
用水刷洗泄漏污染区,经稀释的污水放入废水系统。
雾状水、抗溶性泡沫、二氧化碳、干粉。
浓度MAC(mg/m3):未制订标准当地应急救援单位名称市消防队:119市人民医院:120当地应急救援单位电话消防队:119人民医院:120危险性标志脲职业病危害告知卡作业场所存在脲,对人体有损害,请注意防护脲Urea健康危害理化特性本品属微毒类。
对眼睛、皮肤和粘膜有刺激作用。
溶于水、甲醇、乙醇,微溶于乙醚、氯仿、苯。
遇明火、高热可燃。
与次氯酸钠、次氯酸钙反应生成有爆炸性的三氯化氮。
受高热分解,放出有毒的烟气。
应急处理皮肤接触:用肥皂水及清水彻底冲洗。
就医。
眼睛接触:拉开眼睑,用流动清水冲洗15分钟。
就医。
吸入:脱离现场至空气新鲜处。
就医。
食入:误服者,饮适量温水,催吐。
就医。
灭火方法:雾状水、抗溶性泡沫、二氧化碳、干粉。
注意防护急救电话:120 消防电话:119。
尿素工艺工作总结
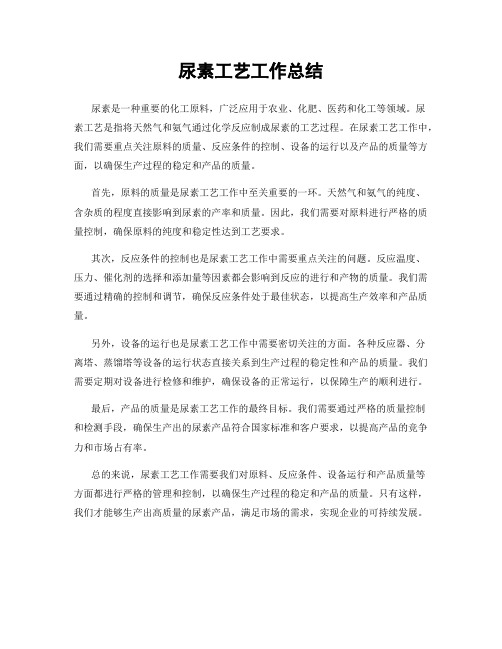
尿素工艺工作总结
尿素是一种重要的化工原料,广泛应用于农业、化肥、医药和化工等领域。
尿
素工艺是指将天然气和氨气通过化学反应制成尿素的工艺过程。
在尿素工艺工作中,我们需要重点关注原料的质量、反应条件的控制、设备的运行以及产品的质量等方面,以确保生产过程的稳定和产品的质量。
首先,原料的质量是尿素工艺工作中至关重要的一环。
天然气和氨气的纯度、
含杂质的程度直接影响到尿素的产率和质量。
因此,我们需要对原料进行严格的质量控制,确保原料的纯度和稳定性达到工艺要求。
其次,反应条件的控制也是尿素工艺工作中需要重点关注的问题。
反应温度、
压力、催化剂的选择和添加量等因素都会影响到反应的进行和产物的质量。
我们需要通过精确的控制和调节,确保反应条件处于最佳状态,以提高生产效率和产品质量。
另外,设备的运行也是尿素工艺工作中需要密切关注的方面。
各种反应器、分
离塔、蒸馏塔等设备的运行状态直接关系到生产过程的稳定性和产品的质量。
我们需要定期对设备进行检修和维护,确保设备的正常运行,以保障生产的顺利进行。
最后,产品的质量是尿素工艺工作的最终目标。
我们需要通过严格的质量控制
和检测手段,确保生产出的尿素产品符合国家标准和客户要求,以提高产品的竞争力和市场占有率。
总的来说,尿素工艺工作需要我们对原料、反应条件、设备运行和产品质量等
方面都进行严格的管理和控制,以确保生产过程的稳定和产品的质量。
只有这样,我们才能够生产出高质量的尿素产品,满足市场的需求,实现企业的可持续发展。
尿素技术总结1500字

尿素技术总结1500字尿素是一种主要用途广泛的化工产品,在农业和工业领域都有重要的应用。
尿素技术是指生产尿素的工艺和方法,主要包括合成尿素的反应过程和相关设备、控制系统等方面。
本文将对尿素技术进行总结,主要包括尿素的生产过程、合成反应、设备与控制等方面。
尿素的生产过程主要分为合成氨和合成尿素两个步骤。
合成氨的生产通常采用哈柏过程或者A进化过程,其中哈柏过程是利用天然气或石油为原料,进行重整反应产生氢气,然后通过催化剂使氢气和氮气生成合成氨。
合成尿素的反应过程主要分为碳酰化反应和胺化反应两个步骤。
碳酰化反应是将合成氨和二氧化碳在高温高压下反应生成尿素酸,然后通过脱水反应生成尿素。
胺化反应是将尿素酸与氨在碱性条件下反应生成尿素。
整个尿素生产过程需要考虑反应条件、原料质量、催化剂选择等因素,以满足产品质量和产量的要求。
尿素的合成反应是碳-氮化合物的一个重要反应,通过将氨与二氧化碳反应,生成了一个稳定的化学键,从而形成了尿素。
这个反应具有一些特点,首先是反应条件的选择对反应速率和产品质量有很大影响。
例如,反应温度、压力、催化剂种类和浓度等都会影响反应的进行。
其次,催化剂对反应速率和选择性起着重要作用。
常用的催化剂有金属铁和金属铁酸盐等。
此外,反应过程中还需要考虑溶剂的选择、搅拌速度和气体的供应等因素,以确保反应的进行和产品的质量。
尿素生产中的设备主要包括反应器、分离器和传热器等。
反应器是进行尿素合成反应的主要设备,通常采用高压容器,有固定床反应器和流化床反应器等。
分离器是将反应混合物中的尿素和未反应的气体分离开的设备,常用的分离器有吸收塔、再吸收塔和闪蒸器等。
传热器用于提供反应过程中所需的热量,通常采用换热器和蒸发器等设备。
此外,尿素生产还需要相应的控制系统,用于监测和调节反应过程中的温度、压力、流量等参数。
总之,尿素技术是一种重要的化工生产技术,其生产过程包括合成氨和合成尿素两个步骤。
合成尿素的反应过程主要包括碳酰化反应和胺化反应。
- 1、下载文档前请自行甄别文档内容的完整性,平台不提供额外的编辑、内容补充、找答案等附加服务。
- 2、"仅部分预览"的文档,不可在线预览部分如存在完整性等问题,可反馈申请退款(可完整预览的文档不适用该条件!)。
- 3、如文档侵犯您的权益,请联系客服反馈,我们会尽快为您处理(人工客服工作时间:9:00-18:30)。
尿素的工艺和职业危害一、尿素的制造工艺:尿素生产工艺流程简介新建项目以无烟煤为主要生产原料,首先合成氨和CO2,然后二者再合成尿素。
原料煤经过造气炉造气,形成原料气,原料气经过压缩,进入变换炉进行变换后生成变换气,变换气经过脱硫、脱碳、精脱硫后成为合成气,脱碳后的合成气中的CO2被溶剂吸收后生成的CO2气体作为合成尿素的原料。
合成气经过压缩后送入双甲精制制备甲醇,从双甲精制后出来的合成气经过压缩后作为氨合成的原料气,原料气经过氨合成塔后合成液态氨,作为合成尿素的原料。
液氨进入尿素合成塔,与合成装置来的CO2气体在尿素合成塔中合成尿液,尿液经过蒸发去除水分后,进入尿素造粒系统,形成大颗粒尿素成品。
1、原料煤贮运系统原料煤由汽车运入干煤棚,再由抓斗桥式起重机抓入受煤坑或由汽车直接倒入受煤坑,通过电振给料机给至带式输送机运至筛分厂房,通过园振动筛进行筛分,筛上原煤通过带式输送机送至造气炉炉顶的卸料小车,卸入汽化炉煤仓供汽化炉造气使用,筛下煤通过带式输送机进入热电站的燃料煤系统。
2、燃料煤贮运系统汽车运来的燃料煤人工卸入干煤棚内贮存,上煤时由抓斗桥式起重机送入受煤斗,受煤斗的出料口设有电机振动给料机,将燃料煤按需要输送量给进备1带式输送机,经过备2带式输送机转运至筛分破碎厂房,由圆振筛进行筛分,筛上大于8mm的块煤进入破碎机,破碎后的煤给进备3带式输送机上;筛下小于8mm的合格煤也进入备3带式输送机上,再经过备4带式输送机转运至锅炉房上煤层,由备5带式输送机分别给进锅炉的贮煤斗中。
造气系统生产工艺流程及其职业病危害因素的分布3、造气系统生产工艺(1)造气造气过程由吹风、上吹制气、下吹制气、空气吹净五个阶段组成。
粒度合格的原料块煤,经皮带运至各造气炉料仓,由自动加煤装置将煤连续均匀地加入造气炉内,与鼓风机鼓入的空气混合进行燃烧,同时将混有少量空气的过热蒸汽分别从炉底和炉上部通入炉内,与炽热的炭层发生反应,在造气炉内发生的主要化学反应有:以上反应产生的混合气分别称为上行煤气和下行煤气,上、下行煤气进入造气余热回收器回收热量后,进入煤气冷却器,洗涤冷却至常温后送气柜。
造气炉产生的吹风气经炉上部进入旋风除尘器除尘后去吹风气回收系统。
(2)原料气压缩工艺原料气压缩系统压缩机分为四级压缩系统来自加压炉气柜的0.004Mpa(g)、40℃半水煤气经原料气压缩机的三个一级进气缓冲器后分别进入三个一级气缸进行压缩,从三个一级气缸排出的0.25 Mpa(g)、153℃气体通过三个一级排气缓冲器后依次进入一级冷却器和一级分离器,温度降到40℃并分离冷凝液后经二级进气缓冲器分别进入二级气缸进行压缩。
经二级气缸压缩至0.73 Mpa(g)、122℃的气体依次经二级排气缓冲器、二级冷却器和二级分离器后通过三级进气缓冲器进入三级气缸进行压缩。
经三级气缸压缩1.8 Mpa(g)、131℃的气体依次经三级排气缓冲器、三级冷却器和三级分离器后通过四级进气缓冲器进入四级气缸进行压缩。
经四级气缸压缩的 3.55Mpa(g)、131℃的气体依次经四级排气缓冲器、四级冷却器和四级分离器温度降到40℃并分离冷凝液后送至变换工序。
(3 )吹风气回收吹风气回收是合成氨达到蒸汽自给必须实施的一项节能措施。
吹风气主要收集自造气炉,由造气炉来的吹风气以及氢氨回收等回收来的吹风气与热空气充分混合后,于燃烧炉中燃烧,产生高温(800~950℃)烟气,烟气从燃烧炉下部出口经高温空气余热器、高压蒸汽过热器吸收部分余热后到余热锅炉加热汽包内的软水产生饱和蒸汽,最后由引风机引至主烟囱排出。
余热锅炉产生的饱和蒸汽,经高压蒸汽过热器加热升温后,送至高压蒸汽管网共发电使用。
4、变换系统生产工艺(1)变换来自原料气压缩的压力3.55 Mpa(g),温度40℃的半水煤气进入气气换热器换热后进入第一混合器,与中压蒸汽混合升温至反应温度,进入第一变换炉进行变换反应,主要化学方程式为:出第一变换炉的变换气经中压废热锅炉回收热量产生中压蒸汽,然后再经气气换热器进一步降低温度,进入第二混合器配入一定量的蒸汽后进入第二变换炉。
出第二变换炉的变换气中CO降至2%,温度265℃,变换气再经过中压废热锅炉、气气换热器、混合器回收热量,经水冷器将温度降至40℃,经分离器分离冷凝液后进入变换气脱硫工序。
(2)变换气脱硫来自变换工段的变换气,进入脱硫塔的下部,与塔顶喷淋而下的脱硫贫液逆流接触,变换气中的H2S被吸收。
出塔变脱气中的H2S含量约20mg/Nm3,温度40℃,经变脱气分离器分离掉夹带的栲胶溶液后,进干法脱硫塔进一步脱硫后,变脱气中的H2S≤2ppm后,送往脱碳装置。
从脱硫塔顶进入的脱硫贫液吸收了变换气中的H2S后,富液从塔底排出,首先经过涡轮机回收静压能后进入喷射氧化再生槽顶的喷射器口,与自吸的空气在喷射器混合,形成一股射流,进行强化氧化反应,然后进入喷射氧化再生槽,这时硫泡沫及溶液从喷射再生槽底迅速返上。
在喷射氧化再生槽内,氧化浮选出的硫泡沫自流入硫泡沫槽,由硫泡沫泵加压送入熔硫釜连续熔硫,熔硫釜排出的清液进入溶液缓冲槽降温后返回贫液槽,经贫液泵加压到4.0 Mpa后分别送入脱硫塔循环喷淋脱硫。
熔硫釜底部排出物为硫磺,凝固后即为硫膏,硫膏外卖销售。
各排出点排出的溶液均收集于低位槽。
(3)NHD脱碳来自变换气脱硫工段的变脱气首先进入气体换热器使其温度降至17℃,经原料气分离器进入脱碳塔底部。
变脱气由下而上与从塔顶下来的NHD溶液逆流接触,气体中的CO2被溶剂吸收。
从塔顶出来的脱碳气含CO2<0.38%,温度-2℃。
经脱碳气分离器除去少量夹带的NHD雾沫后,脱碳气进入气体换热器换热,温度升至30℃,送入精脱硫工段。
从脱碳塔顶进入的贫液在塔内吸收CO2后,富液由脱碳塔底部引出,进入水力透平回收静压能。
回收能量后的富液进入高压闪蒸槽,部分溶解的CO2和大部分H2在此解吸出来,即高压闪蒸气,送回原料气压缩机三段入口,作原料气。
从高压闪蒸槽底部出来的溶液减压进入低压闪蒸槽。
此时,大部分溶解的CO2气被解吸出来,经气体换热器回收冷量后大部分送往尿素工段作为尿素原料,其余就地放空。
从低压闪蒸槽底部出来的溶液经富液泵提压后,其中一少部分溶液流经溶液过滤器滤除固体杂质。
大部分溶液送入气提塔。
溶液自上而下与塔底送入的气提空气逆流接触进行传质传热,此时溶液中所吸收的CO2被空气气提出来。
解吸气从塔顶引出,经空气换热器换热后,引至塔顶约50m高度放空。
气提空气由空气鼓风机经空气过滤器从大气吸入。
先通过空气冷却器冷却并在空气水分离器中将冷凝下来的水分离掉,进入气提塔底部去气提含CO2的富液。
最后从气提塔顶部由空气鼓风机引出。
NHD溶液具有吸水性,它将原料气和气提空气中的水份吸收而使溶液中水含量积累增高,当NHD溶液含水超过3%(wt)就会降低其吸收CO2性能。
因此需要抽出部分溶液进行脱水。
从富液泵出口引出部分溶液,经过溶液换热器换热后进入脱水塔。
出脱水塔顶部气相经脱水塔水冷器冷凝,进入冷凝液贮槽后,不凝气放空,冷凝液用泵打至水处理系统。
从脱水塔底部引出的溶液已脱水,经过溶液换热器换热降低温度后送至地下槽。
脱水所需热源由脱水搭内的蒸汽盘管提供。
系统中各排液导淋回收的NHD溶液经过排液总管流入地下槽,存入溶液贮槽,并通过补液泵补入气提塔,保持系统各处的正常液位。
脱碳工艺流程见图3-9。
(4)精脱硫来自脱碳装置的脱碳气,首先进入气液分离器,分离掉夹带的液滴后,进入精脱硫塔,在该塔脱除H2S。
然后气体进入合成气压缩工段。
(5)合成气压缩来自精脱硫工序的温度40℃、压力3.0 Mpa的精脱气与来自氢氨回收工序的氢气一起进入本工序,经一段进气分离器分离出夹带的液滴后进入合成气压缩机低压缸。
精脱气经一段压缩后,送往双甲精制工序。
来自双甲工序的温度6℃、压力7.7 Mpa的精制气,进入合成气压缩机的高压缸,经七级压缩后在缸内与氨合成工序来的循环气混合加压至14.3Mpa,75℃后,送至氨合成工序。
5 、甲醇合成系统(1)双甲精制来自精脱硫装置的精脱气,其总硫小于0.1ppm,补入氢回收装置来的氢回收气,与分子筛再生气一并进入合成气压缩机低压缸,压缩至7.9MPa,出口温度约为168℃,进入双甲精制装置。
新鲜合成气首先进入第一进出口换气器预热至230℃,再进入等温列管式第一甲醇塔.合成塔壳侧副产2.7MPa的中压饱和蒸汽,并入中压蒸汽管网。
出第一甲醇塔的合成气进入第一进出口换热器,再进入脱盐水预热器回收热量后,进入第一水冷器进一步冷却至40℃,进甲醇分离器分离出液体粗甲醇。
甲醇分离器出口的合成气进入第二进出口换热器壳侧,预热后进入第一蒸汽加热器加热至220℃后,进入绝热式固定床第二甲醇塔。
出第二甲醇塔的气体经过第二进出口换热器冷却至75℃后,进入第二水冷器进一步冷却至40℃后,在甲醇水洗塔塔底分离出粗甲醇。
从甲醇精馏装置常压塔底来的废水或界外来的脱盐水经废水加压泵加压后送入甲醇水洗塔。
出甲醇水洗塔的合成气进入甲烷化进出口换热器,预热至280℃,进入第二蒸汽加热器加热至310℃,入绝热式固定床甲烷化塔。
出甲烷化塔的合成气进入甲烷化进出口换热器壳侧冷却至88℃,再进入最终水冷器进一步冷却至40℃后,经氨冷器冷至8℃,进入气液分离器分离出液相水。
出气液分离器的气体进入分子筛干燥净化系统。
甲醇分离器和甲醇水洗塔来的粗甲醇合并后减压送入粗甲醇闪蒸槽,闪蒸后粗甲醇送精馏装置制得产品精甲醇。
闪蒸气并入可燃料气管网送吹风回收装置。
(2)分子筛干燥来自双甲合成含有H2、N2、CH4、Ar及微量H2O、CO、CO2,温度为8℃得新鲜合成气进入分子筛干燥净化系统。
用于分子筛干燥系统再生的气体取自净化后的新鲜合成气,其量为总新鲜气的4%。
再生气经调节阀减压后并由再生气加热器加热至250℃后,进入分子筛干燥器,对其进行再生。
再生后的气体经再生气水冷器冷至40℃后返回合成气压缩机低压缸入口加以回收利用。
(3 )甲醇精馏从甲醇合成工段来的粗甲醇,与闪蒸槽来的蒸汽冷凝液在粗甲醇换热器中换热,达到70℃左右进入预精馏塔(简称预塔)中上部进行蒸馏反应。
而冷凝液温度降至84℃,与加压塔预热器来的蒸汽冷凝液汇合,一起进入冷凝液冷却器冷却至60℃后,进入冷凝液槽,经冷凝液泵加压返回脱盐水站。
从预塔塔顶出来的馏分经预塔冷凝器Ⅰ冷凝后,用预塔回流泵加压后送至预塔塔顶回流。
未冷凝的轻组分及不凝气体经气液分离器分离后至吹分气回收系统或高空排放,气液分离器回收的甲醇液自流入地下槽。
从预塔塔底出来即为脱除轻组分后的预后甲醇,温度为85℃,用预后甲醇泵抽出,送至加压塔预热器加热至110℃后送入加压塔中下部,塔底有再沸器加热。
加压塔上部侧线采出精甲醇,经加压塔冷却器冷却后送至精甲醇中间槽。