尿素工艺流程简述(副本)
尿素 生产工艺

尿素生产工艺
尿素是一种最常用的氮肥,也是农田中使用最广泛的肥料之一。
它是在压缩空气和氨的存在下制造的。
下面是尿素生产的工艺流程。
首先,通过空气分离装置将空气中的氮气和氧气分离出来。
这样纯净的氮气就可以用作后续的制氨过程。
然后,在制氨装置中,将氮气与纯氢气经过高温高压条件下的反应,生成氨气。
这个反应通常使用铁-钼催化剂来加速反应
速度。
制氨反应可以分为低温反应和高温反应两个阶段,低温反应通常在200-300°C下进行,生成的氨气含量在15-20%;
而高温反应则在高温下进行,将氮气和未反应的氢气继续反应,使氨气的含量达到25-35%。
接下来,通过氨合成器将制得的氨气与二氧化碳反应,生成尿素。
氨合成器中采用铁-钼催化剂,条件为200-220°C,压力为150-200 atm。
尿素反应生成的热量通过蒸汽汽化剂来排出。
尿素的反应方程式为:
2NH3 + CO2 → NH2CONH2 + H2O
尿素生成之后,需要通过冷却、脱水和干燥的过程来提高尿素的纯度。
这些过程通常通过旋转蒸发器、冷却器和离心机来完成。
最后,尿素需要进行粉碎和筛分处理,以获得所需的颗粒大小
和均匀度。
粉碎过程通常使用球磨机或者研磨机来完成,而筛分则使用振动筛或者离心筛来分离不同颗粒大小的尿素。
总的来说,尿素的生产过程包括氨的制备、尿素的合成、尿素的精制和颗粒的粉碎筛分等步骤。
这些步骤通过控制温度、压力和催化剂的选择来实现高效的生产。
尿素的工艺流程不仅提高了氮肥的产量,而且还减少了对环境的污染。
尿素工艺流程图

尿素工艺流程图
尿素工艺是一种制备尿素的化学工程过程。
下面是一个简洁的尿素工艺流程图的描述,其中包括主要步骤和反应条件。
尿素工艺流程图
1. 吸收剂制备
氨气(NH3)和二氧化碳(CO2)从化合物气体进料中分离出来。
氨气先通过冷凝器冷却,然后通过压缩机加压。
二氧化碳通过压缩机进一步压缩。
2. 合成反应
吸收剂和尿素制备物的反应在压力脱除过程中进行,其中合成反应采用尿素合成反应器。
在合成反应器中,通过加热吸收剂混合物至一个特定温度,以促进反应。
3. 真空脱除
合成反应后,产生的混合物进入真空脱除装置。
通过降低压力,将未反应的氨气和其他轻质组分从反应物中除去。
4. 还原反应
从真空脱除装置中得到的尿素混合物进入还原反应器。
在还原反应器中,使用脱水剂,如甲醇(CH3OH),对尿素进行脱水反应。
5. 结晶
还原反应得到的尿素溶液通过降低温度来促进结晶。
结晶过
程中,尿素分离出来,并通过过滤或离心等方式得到尿素晶体。
6. 精制
结晶得到的尿素晶体进行洗涤,以去除杂质。
然后经过干燥,将尿素晶体转化为尿素颗粒。
7. 包装和储存
精制后的尿素颗粒通过包装装入袋子或容器中,并存放在干
燥的仓库中,等待出厂或运输。
该工艺流程图简要描述了从吸收剂制备到尿素包装和储存的主要步骤。
这是一种典型的尿素工艺流程,具体的条件和设备设计可能会根据不同工厂的要求有所变化。
尿素流程叙述稿

上升,与由液氨缓冲槽2来的回流液氨逆流接触,未吸收的 CO2完全从气相中除去,而纯的气态氨离开吸收塔进入氨冷 器12,借助氨冷将气氨冷凝为液氨,被冷凝的液氨进入氨缓 冲槽2。
在氨冷凝器12中未冷凝的惰性气体进入惰性气体洗涤器13,
气体中的氨用来自二段蒸发冷凝器28的冷凝液来吸收。氨水 在洗涤器中蒸浓,然后流入一段吸收塔10顶。13中未被吸 收的含氨惰性气体经尾气吸收塔16回收氨后放空。10中 的大部分吸收剂来自二段吸收塔14的稀甲铵液。
来自二段吸收塔14的甲铵液经二段甲铵泵15 送入一段吸收
塔10下部。浓的甲铵液由一段吸收塔10底部出来经一段 甲铵泵11送入合成塔底部。
由一段分解塔7出来的溶液减压至0.3~0.4 MPa,进入二段
分解塔8进行加热分解。分解出来的液体送入闪蒸槽18,气 体则进入二段吸收塔底部,由加入塔顶的来自28的二段蒸
②二氧化碳经压缩机 1加压至20 MPa 左 右,温度约125℃, 进入尿素合成塔5底 部的预反应器。
③从一段吸收塔10来 的甲铵溶液,由一段 甲铵泵11加压后亦同 样送入合成塔5底部 的预反应器。在预反 应器中大约90%的 NH3和CO2生成甲胺
⒒由二段分 解塔8底出 来的溶液, 减压后进入 闪蒸槽18中, 在41 KPa Hg 真空下 气化,除去 部分水和溶 液的氨等, 使尿素不含 溶解的经二段甲铵泵15 送入
一段吸收塔10下部。浓的甲铵液由一段吸收塔1 0底部出来经一段甲铵泵11送入合成塔底部。
Stamicarbon 水溶液全循环法流程叙述 : 二氧化碳经压缩机1加压至20 MPa 左右,温度约125℃,进入 尿素合成塔5底部。来自液氨缓冲槽2的液氨经高压泵3加压, 并经液氨预热器4预热到温度约90℃的液氨,配成氨碳比为4 左右进入合成塔底部。 从一段吸收塔10来的甲铵溶液,由一 段甲铵泵11加压后亦同样送入合成塔底部。上述三种物料在 合成塔内充分混合并反应生成甲铵和甲铵脱水为尿素。与CO2 气提法不同的是,甲铵的生成与脱水为尿素均在合成塔中完 成。 合成压力19.62~21.58 MPa、温度185~190℃、 NH3/CO2比4~4.5、H2O/CO2比0.6~0.7,二氧化碳约有62% 转化为尿素。 含有尿素、未转化的甲铵、过剩氨和水的混合溶液, 从合成 塔顶出来,通过减压阀减至1.7~1.8 MPa,进入预分离器 6, 在此进入气液分离。由预分离器出来的溶液,因膨胀气化, 温度有所下降,进入一段分解塔7进入加热分解。 把一段分解塔分出的气体也引入预分离器6后, 将气体一并
尿素生产工艺流程
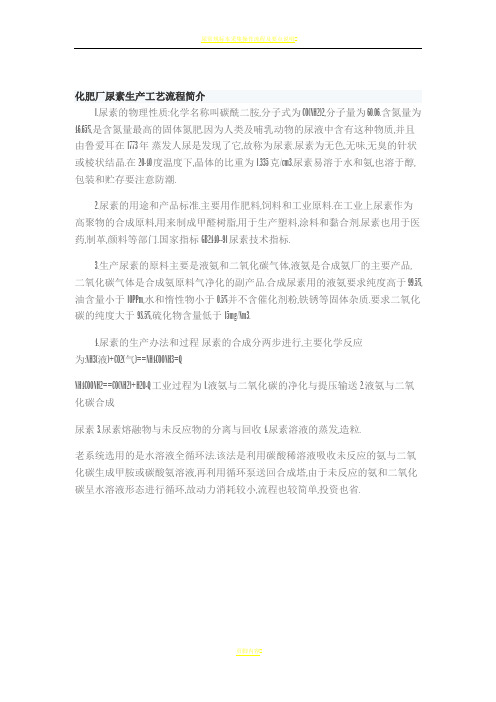
化肥厂尿素生产工艺流程简介
1.尿素的物理性质:化学名称叫碳酰二胺,分子式为CO(NH2)2,分子量为60.06.含氮量为46.65%,是含氮量最高的固体氮肥.因为人类及哺乳动物的尿液中含有这种物质,并且由鲁爱耳在1773年蒸发人尿是发现了它,故称为尿素.尿素为无色,无味,无臭的针状或棱状结晶.在20-40度温度下,晶体的比重为1.335克/cm3.尿素易溶于水和氨,也溶于醇,包装和贮存要注意防潮.
2.尿素的用途和产品标准.主要用作肥料,饲料和工业原料.在工业上尿素作为高聚物的合成原料,用来制成甲醛树脂,用于生产塑料,涂料和黏合剂.尿素也用于医药,制革,颜料等部门.国家指标GB2440--91尿素技术指标.
3.生产尿素的原料主要是液氨和二氧化碳气体,液氨是合成氨厂的主要产品,二氧化碳气体是合成氨原料气净化的副产品.合成尿素用的液氨要求纯度高于99.5%,油含量小于10PPm,水和惰性物小于0.5%并不含催化剂粉,铁锈等固体杂质.要求二氧化碳的纯度大于98.5%,硫化物含量低于15mg/Nm3.
4.尿素的生产办法和过程尿素的合成分两步进行,主要化学反应
为:NH3(液)+CO2(气)==NH4COONH3=Q
NH4COONH2==CO(NH2)+H2O-Q工业过程为1.液氨与二氧化碳的净化与提压输送2.液氨与二氧化碳合成
尿素3.尿素熔融物与未反应物的分离与回收4.尿素溶液的蒸发,造粒.
老系统选用的是水溶液全循环法.该法是利用碳酸稀溶液吸收未反应的氨与二氧化碳生成甲胺或碳酸氨溶液,再利用循环泵送回合成塔,由于未反应的氨和二氧化碳呈水溶液形态进行循环,故动力消耗较小,流程也较简单,投资也省.。
尿素生产工艺流程简介
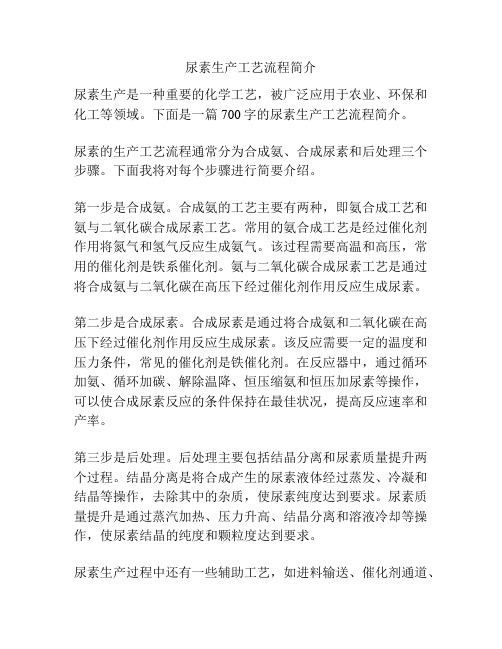
尿素生产工艺流程简介尿素生产是一种重要的化学工艺,被广泛应用于农业、环保和化工等领域。
下面是一篇700字的尿素生产工艺流程简介。
尿素的生产工艺流程通常分为合成氨、合成尿素和后处理三个步骤。
下面我将对每个步骤进行简要介绍。
第一步是合成氨。
合成氨的工艺主要有两种,即氨合成工艺和氨与二氧化碳合成尿素工艺。
常用的氨合成工艺是经过催化剂作用将氮气和氢气反应生成氨气。
该过程需要高温和高压,常用的催化剂是铁系催化剂。
氨与二氧化碳合成尿素工艺是通过将合成氨与二氧化碳在高压下经过催化剂作用反应生成尿素。
第二步是合成尿素。
合成尿素是通过将合成氨和二氧化碳在高压下经过催化剂作用反应生成尿素。
该反应需要一定的温度和压力条件,常见的催化剂是铁催化剂。
在反应器中,通过循环加氨、循环加碳、解除温降、恒压缩氨和恒压加尿素等操作,可以使合成尿素反应的条件保持在最佳状况,提高反应速率和产率。
第三步是后处理。
后处理主要包括结晶分离和尿素质量提升两个过程。
结晶分离是将合成产生的尿素液体经过蒸发、冷凝和结晶等操作,去除其中的杂质,使尿素纯度达到要求。
尿素质量提升是通过蒸汽加热、压力升高、结晶分离和溶液冷却等操作,使尿素结晶的纯度和颗粒度达到要求。
尿素生产过程中还有一些辅助工艺,如进料输送、催化剂通道、废水处理和废气处理等。
进料输送是指将原料通过输送带、皮带输送机和螺旋输送机等装置转移到反应器中。
催化剂通道是指将催化剂从储存罐中转移到反应器中。
废水处理是指将生产过程中产生的废水进行处理,以达到环境保护的要求。
废气处理是指将生产过程中产生的废气进行净化,避免对环境造成污染。
综上所述,尿素的生产工艺流程包括合成氨、合成尿素和后处理三个步骤,其中合成氨和合成尿素是尿素生产的核心步骤,后处理是保证尿素质量的关键环节。
在整个生产过程中,还需要对原料和产品进行输送、催化剂进行通道,以及处理产生的废水和废气等辅助工艺。
这些工艺的运行与控制直接关系到尿素生产的效率和质量。
尿素生产简图(彩色工艺流程图)

1
同一段差不多
3.
去常压吸收塔
氨水来自氨水槽
6.氨水解吸
解吸废水
去界区
中压蒸汽来自外管250℃2.4Mpa
流程说明
1、液氨加压
来自界区的液氨在取样分析后由高压泵加压到14Mpa送往高压喷射器
2、反应阶段
液氨作为喷射动力,将来自高压洗涤器的甲铵液一起带入高压甲铵冷凝器,在其中生成甲铵CO2+2NH3 ⇌NH4•COONH2反应放热,回收一部分热量让反应平衡向正反应偏移;反应后的气体跟液体直接通往合成塔底部,在合成塔(14Mpa 183℃)中生成尿素NH4•COONH2 ⇌CO (NH2)2+H2O 反应吸热,而气体CO2+2NH3 ⇌NH4•COONH2反应放热,所以合成塔中自热平衡,且合成塔中设有多层塔板,防止返混;反应生成的尿素-甲铵液体从合成塔底部取样分析后去汽提塔顶部,与下层来的高压CO2逆流接触,在高温以及CO2气体带动下,甲铵液被进一步分解,尿素及甲铵液从汽提塔底部取样分析后去往精馏塔,在精馏塔中循环加热,促进甲铵液进一步分解,出来的尿素溶液浓度大约为68%,取样分析后进入闪蒸罐(常压),闪蒸出CO2/NH3/H20,尿素溶液流进尿素贮罐。
3、尿素造粒
尿素贮罐的尿素溶液取样后打到一段蒸发加热器(0.03Mpa 13 0℃)尿素溶液中的气体水分充分分解、蒸发,出一段加热器的尿素溶液浓度大约为95%,然后流进二段蒸发加热器(0.003MPa 140℃)
. 继续加热浓缩,出来的尿素为熔融状态(99.7%),取样后送到造粒系统直接做成颗粒状,包装存储。
4、其他说明
过程中产生的气体回收利用,或者去排气筒,用过程中产生的溶液吸收后返回氨水槽,不能吸收的气体排大气。
.;。
尿素合成工艺流程
尿素合成工艺流程尿素合成工艺流程尿素是一种重要的化肥,广泛用于农业生产。
它由两种主要原料—氨和二氧化碳合成而成。
下面是尿素合成的工艺流程。
第一步:制备氨气将天然气或者其他石油化工产品作为原料,经过脱硫、脱水等处理,得到高纯度的氢气。
然后将氢气和氮气以一定比例混合,经过压缩、冷却和吸附等操作,制备得到高纯度的氨气。
第二步:制备尿素溶液将氨气和液态二氧化碳按照一定的比例同时进入反应器,反应温度通常在160-200摄氏度之间。
经过反应,氨气和二氧化碳发生彼此的反应,生成尿素溶液。
此时,尿素溶液中还含有一定量的氨化物、卡尔氏氮化碳和少量的铵盐。
第三步:尿素结晶将尿素溶液经过蒸发和降温的过程,使得尿素逐渐结晶出来。
通过调节温度和压力,使得产生合适大小的尿素结晶颗粒,方便后续的分离和提纯。
第四步:尿素过滤将产生的尿素结晶颗粒经过过滤分离,去除其中的杂质和溶液。
此过程也可以通过离心、真空过滤等方式进行,得到高纯度的尿素颗粒。
第五步:尿素干燥将过滤得到的湿尿素颗粒进行干燥处理,去除其中的水分。
通常可以使用流化床干燥器或者气流干燥器等设备,将湿尿素颗粒在一定的温度下,通过热风吹干,使得尿素颗粒的水分含量降到一定的标准,以利于后续的包装和储存。
第六步:尿素包装将干燥后的尿素颗粒进行包装,通常采用编织袋或者塑料袋装填,以便于运输和销售。
尿素合成工艺流程主要包括氨气制备、尿素溶液制备、尿素结晶、尿素过滤、尿素干燥和尿素包装等环节。
这个流程既简单又高效,可以使得尿素生产达到规模化和工业化的要求,并且可以保证产品的质量和纯度。
同时,这个工艺流程也具备一定的环保性,能够有效地处理和循环利用一些废水、废气和废渣,减少对环境的污染。
尿素合成工艺流程的不断改进和优化,不仅提高了尿素合成的产量和质量,也降低了生产成本。
同时,也为农业生产提供了高效、可靠的化肥产品,促进了农业的发展和粮食的丰收。
尿素合成工艺的研究和应用将继续推进农业的可持续发展,为保障粮食安全和农业生态环境的改善做出贡献。
尿素生产工艺流程简介
尿素生产工艺流程简介
尿素是一种理想的氮肥,广泛应用于农业生产中。
下面简要介绍尿素的生产工艺流程。
尿素的生产主要包括合成氨和合成尿素两个过程。
合成氨的工艺流程如下:
1. 获取天然气:天然气是合成氨生产的主要原料。
首先,从地下的天然气田或油田提取天然气。
2. 脱硫:天然气中含有硫化氢和二硫化碳等杂质,需要将其脱除。
一般采用吸收剂法进行脱硫。
3. 脱水:将脱硫后的天然气进行脱水处理,以减少水蒸气对后续反应的干扰。
4. 压缩:将脱水后的天然气进行压缩,提高反应过程的产物浓度。
5. 进料催化:将压缩后的天然气与氛围空气混合,进入反应器进行催化反应,生成合成氨。
6. 分离:将反应器产物进行冷却和分离,得到合成氨。
合成尿素的工艺流程如下:
1. 进料处理:将合成氨与二氧化碳按一定比例混合。
2. 反应器反应:将混合物进入反应器进行加热反应,生成尿素。
3. 分离:将反应器产物进行分离,得到尿素和一些杂质产物。
4. 精制:对分离得到的尿素进行精制和净化处理,以提高产品质量。
5. 包装:将精制的尿素包装成所需的不同规格。
以上是尿素生产的主要工艺流程。
需要注意的是,尿素生产过程中需要控制反应温度、压力和催化剂的使用量等参数,以确保反应的高效和产品质量的稳定。
同时,也需要对生产设备进行合理的维护和清洁,以确保生产过程的安全和正常运行。
尿素的生产工艺流程
尿素的生产工艺流程尿素是一种重要的化学品,广泛应用于农业、化工、医药等领域。
尿素的生产工艺流程有以下几个主要步骤:1. 合成氨的制备:尿素的生产首先需要制备氨气。
通常采用合成氨工艺流程,即将气体混合物(通常为自然气和蒸汽的混合物)通过压缩、解冷、采用催化转化反应等方式,将气体转化为含有高浓度氨气的气体。
2. 尿素合成:尿素的合成一般采用哈伦斯过程,即将合成氨与二氧化碳反应生成尿素。
这一步骤通常在高压和高温下进行,并且需要使用催化剂催化反应。
具体的反应方程式为:2NH3+ CO2 → NH2CONH2 + H2O3. 尿素结晶:尿素合成后是以液体状态存在的,需要通过结晶过程将其转化为固体尿素。
通常采用蒸发结晶法或压滤除溶法进行尿素的结晶。
具体的过程一般包括加热、浓缩、结晶分离、干燥等步骤。
4. 尿素粒化:经过结晶后的尿素通常需要进行粒化处理,以改善其性能和外观。
粒化过程通常采用旋转粒化机,将固体尿素与适量的液体尿素混合后,通过旋转机械的作用使尿素逐渐成为颗粒状。
粒化后的尿素质量更均匀,便于搬运和应用。
5. 产品包装和储运:尿素粒化后,需要进行适当的包装和储运以保证产品质量和安全性。
一般采用塑料袋或编织袋等包装尿素,并以集装箱或散装的形式进行储运。
同时,根据不同的应用需求,也可以对尿素进行进一步的混合、掺杂等处理,以调整其化学成分和性能。
尿素的生产工艺流程需要采用先进的设备和控制技术,以确保产品质量和生产效率。
同时,对废气、废水等产生的副产品也需要进行适当的处理和回收,以避免对环境造成污染。
因此,尿素的生产需要综合考虑技术、环保和经济等多个方面因素的综合优化。
尿素工艺流程
一、原料的压缩和净化1、二氧化碳(CO2)的压缩和净化二氧化碳来自脱碳,其浓度为65.7%(V),含氧量0. 5 %(V),硫化物<15mg/M3,CO2通过一分离器后进入CO2压缩机一段,由二段出口去脱硫槽,降低CO2气中的含量至10 mg/M3以下,回到压缩机三段出入,再经三、四、五段压缩达到20.7Mpa,送到尿素合成塔。
2、液体的净化和输送原料液氨从合成车间氨冷冻岗位氨贮槽送来,温度≤30℃,压力≥2.05Mpa,先进入液氨过滤器,除去固体杂质和油类,再进入液氨缓冲槽,进入尿素系统的氨由调节阀开度的大小来控制流量。
二、尿素的合成CO2压缩机出口气体压力约为Mpa,温度约125℃,进入两尿素合成塔,进入尿塔的CO2量决定整个系统的生产负荷大小。
从一吸塔来的氨基甲酸溶液约85—90℃,经一甲泵加压至20.69Mpa,送入尿素合成塔。
从液氨缓冲槽来液氨进入氨泵入口加压至20.7Mpa,经氨预热器加热至45℃左右,送入尿塔。
入尿塔的氨量根据塔顶部温度决定,其顶部温度控制在188—190℃;尿素合成塔的压力由塔出口的调节阀自行控制,一般维持在19.6Mpa。
三、循环回收1、一段分解合成塔出来的合成液中含有尿素、氨基甲酸铵(甲胺)、过剩氨和水。
通过压力调节阀减压至1.7Mpa,进入一段分解塔及一分加热器,由1.10Mpa 的蒸汽加热至155—160℃,使甲胺的分解率达到88%以上,总氨蒸出率达90%,在分离段进行气液分离后通过一减压调节阀后送至二段加热分离器(二分塔)。
2、二段分解出一段分解塔的流体经减压至0.4Mpa后,进入二分塔,在上部闪蒸,经填料精馏段,二段加热器加热至135—140后进行气液分离,气相进入二段吸收,液相经一减压调节阀进入蒸发系统的闪蒸槽。
3、一段循环系统从一分塔气相出来的气体约120℃,是NH3、CO2 、H2O的混合物,经热能利用段换热降温至100℃,进入一吸冷却器,由循环脱盐水冷却,然后进入一吸塔下部,利用塔顶部加入的液氨和氨水进行吸收,控制出一吸塔气相温度≤50℃,CO2含量≤100PPM。
- 1、下载文档前请自行甄别文档内容的完整性,平台不提供额外的编辑、内容补充、找答案等附加服务。
- 2、"仅部分预览"的文档,不可在线预览部分如存在完整性等问题,可反馈申请退款(可完整预览的文档不适用该条件!)。
- 3、如文档侵犯您的权益,请联系客服反馈,我们会尽快为您处理(人工客服工作时间:9:00-18:30)。
尿素工艺流程简述
1、尿素的合成
CO压缩机五段出口CO气体压力约20.69MPa(绝),温度约125C,进入尿素
合成塔的量决定系统生产负荷。
从一吸塔来的氨基甲酸铵溶液温度约90 C左右,经一甲泵加压至约20.69MPa (绝)进入尿素合成塔,一般维持进料"O/CO (摩尔比)0.65〜0.70。
从氨泵来的液氨经预热器预热至40〜70C进入尿素合成塔,液氨用量根据生产负荷决定,塔顶温度控制在186〜190C,进料NH/CC2分子比控制3.8〜4.2。
尿塔压力由塔顶减压阀PIC204 (自调阀)自动控制,一般维持19.6MPa(表)物料在塔内停留时间为40分钟,CO转化率》65% 为防止尿塔停车时管路堵塞,设置高压冲洗泵,将蒸汽冷凝液加压到19.6〜25.0MPa送到合成塔进出口物料管线进行冲洗置换。
2、中压分解
出合成塔气液混合物减压至1.77MPa(绝)进入预分离器,合成液中的氨大部分被分离闪蒸出来,通过气相管道进入一吸外冷却器,液相进入预蒸馏塔上部,在此分离出闪蒸气后溶液自流至中部蒸馏段,与一分加热器来的热气逆流接触,进
行传质、传热,使液相中的部分甲铵与过剩氨分解、蒸出进入气相,同时,气相中的水蒸汽部分冷凝降低了出塔气相带水量。
出预蒸馏塔中部的液体进入一分加热器,经饱和蒸汽加热后,出一分加热器温度控制在155〜160C,保证氨基甲酸铵的分解率达到88%总氨蒸出率达到90% 加热后物料进入预蒸馏塔下部的分离段进行气液分离,分离段液位由LICA302
摇控控制,物料减压后送至二分塔。
在一分加热器液相入口用空压机补加空气,防止一段分解系统设备管道的腐蚀, 加入空气量由流量计指示(约2m i/TUr)通过旁路放空阀调节流量。
3、二段分解(低压分解)
出预蒸馏塔的液体经LRC302减压至0.29〜0.39MPa (绝),进入二分塔上部进行闪蒸,液体在填料精馏段与塔下分离段来的气体进行传质、传热,以降低出塔气体温度和提高进二分塔加热器的液体温度。
出二分塔加热物料温度为135〜145C,该温度由TRC303自动控制,物料被加热后进入二分塔分离段进行气液分离,二分塔液位由LIC303自动控制。
4、闪蒸
出二分塔液体经减压阀后进入闪蒸槽,出闪蒸槽的气相与一段蒸发气相汇合后去尿素回收塔,再进入一蒸冷凝器通过闪蒸槽气相管线上的阀门控制闪蒸槽的操作压力为340〜400mmHg绝),温度95〜100C,在闪蒸槽液相中残余的氨和二氧化碳大部分逸入气相,尿液则进入一段蒸发器。
5、一段吸收
来自预蒸馏塔的一段分解气与二甲泵送来的二甲液,在一段蒸发器热能回收段混合,产生部分冷凝,放出的热量用于加热尿素溶液,出热能回收段的气液混合物与预分离器气相混合后进入一吸外冷却器底部,被循环脱盐水冷却,气体进一步
冷凝,出一吸冷却器的气液混合物进入一吸塔鼓泡段,气体经鼓泡段吸收后,未吸收的部分进入精洗段,被来自惰洗器的浓氨水及来自液氨缓冲槽的回流氨进一步精洗回收,保证一吸塔出口气相温度小于50C,含CO小于100PPm(体积比)的气氨进入两个串联的氨冷器,首先进入第一个氨冷器(A),部分气氨在此冷
凝下来流往液氨缓冲槽,出氨冷器(A)的气体经惰洗器的防爆空间后进入氨冷凝器(B),在此冷凝的液氨也流往液氨缓冲槽,未冷凝的气体进入惰洗器,气体中氨被氨水泵送来的氨水吸收,出惰洗器的气体由PIC301 (中压压力自调阀)送入尾吸塔。
一吸冷却器所需脱盐水由循环水泵加压后,进入一吸外冷却器顶部与气液混合物逆向进行热交换,吸收热量后,经脱盐水冷却器用循环冷却水冷却后,回到循环水泵进口,构成冷却脱盐水循环系统。
一吸塔底部液相温度在90〜95C,由回流氨及一吸冷却器等配合调节控制,一甲液加压到20.69MPa后送入尿素合成塔,一吸塔液位主要通过改变二甲泵转速调节,即进一吸塔二甲液量来控制(结合尿塔的HO/CO摩尔比,配合二甲泵和
一甲泵的转速来调节)。
6. 二段吸收
二分塔顶部出口气体与来自解吸塔的气体混合后进入二循一冷却器,在一冷中被蒸发冷凝液泵送来的二段蒸发冷凝液吸收生成二甲液并由二甲泵送入一段蒸发热能利用段,二循一冷凝器液位通过改变加水量进行控制,未被吸收的气体由二循一冷凝器顶部出来进入二循二冷凝器底部,被蒸发冷凝液泵送来的蒸发冷凝液吸收,生成的氨水由氨水泵送往惰洗器,二循二冷凝器液位也是通过改变加水量进行控制,二循二冷凝器尾气经(低压压力调节阀)PIC302送往尾吸塔,二段循环吸收剂所用的蒸发冷凝液,是由二段蒸发冷凝液排往二表槽贮存。
7 •尾气吸收
二循二冷出气与惰洗器减压后的尾气分别进入尾吸塔底部,来自一表槽的蒸发冷凝液经尾吸泵送往尾吸冷却器冷却到40C后进入尾吸塔顶部,经填料层吸收尾气后,尾吸塔排出液体流至碳铵液槽,气体经放空管放空。
8•解吸
碳铵液贮槽来的碳铵液,由解吸泵经自调阀由流量计计量后,进入解吸换热器与从解吸塔底来的解吸废液(温度约143C)换热后,进入解吸塔上部喷淋至填料层和从解吸塔底部上升的气体传质、传热进行解吸,气体进入解吸冷凝器,用一吸冷却器来的脱盐水冷却,控制解吸冷气相出口温度w 112C,冷却下来的液体
进入解吸塔顶部作顶部回流,控制解吸塔顶部温度w 120C,解吸冷却器的气相
通过自调阀控制其压力在0.3MPa左右后送入二循一冷气相进口,出解吸冷凝器的脱盐水经电导仪,由自调阀调节其流量后送至锅炉房,解吸废液经解吸换热器换热后外送,解吸塔液位由LC701控制。
解吸塔热量由解吸塔底部加入1.3MPa(绝)蒸汽直接加热,蒸汽加入量根据解吸塔工艺状况由TIC701控制,保证解吸废液NH w0.07%。
合成氨
氨是重要的无机化工产品之一,在国民经济中占有重要地位。
除液氨可直接作为肥料外,农业上使用的氮肥,例如尿素、硝酸铵、磷酸铵、氯化铵以及各种含氮复合肥,都是以氨为原料的。
合成氨是大宗化工产品之一,世界每年合成氨产量已达到1亿吨以上,其中约有80%勺氨用来生产化学肥料,20%乍为其它化工产品的原料。
德国化学家哈伯1909年提出了工业氨合成方法,即“循环法”,这是目前工业普遍采用的直接合成法。
反应过程中为解决氢气和氮气合成转化率低的问题,将氨产品从合成反应后的气体中分离出来,未反应气和新鲜氢氮气混合重新参与合成反应。
合成氨反应式如下:
N2+3H牟2NH3
合成氨的主要原料可分为固体原料、液体原料和气体原料。
经过近百年的发展,合成氨技术趋于成熟,形成了一大批各有特色的工艺流程,但都是由三个基本部分组成,即原料气制备过程、净化过程以及氨合成过程。
1.合成氨的工艺流程
(1) 原料气制备将煤和天然气等原料制成含氢和氮的粗原料气。
对于固体原料煤和焦炭,通常采用气化的方法制取合成气;渣油可采用非催化部分氧化的方法获得合成气;对气态烃类和石脑油,工业中利用二段蒸汽转化法制取合成气。
(2) 净化对粗原料气进行净化处理,除去氢气和氮气以外的杂质,主要包括变换过程、脱硫脱碳过程以及气体精制过程。
①一氧化碳变换过程
在合成氨生产中,各种方法制取的原料气都含有CO其体积分数一般为12%~40% 合成氨需要的两种组分是H2和N2,因此需要除去合成气中的CO变换反应如下:
CO+H2OH2+CO2 =41.2kJ/mol 0298H △
由于CO变换过程是强放热过程,必须分段进行以利于回收反应热,并控制变换段出口残余CO含量。
第一步是高温变换,使大部分CO转变为CO2和H2;第二步是低温变换,将CC含量降至0.3%左右。
因此,CO变换反应既是原料气制造的继续,又是净化的过程,为后续脱碳过程创造条件。
②脱硫脱碳过程。