质量损失统计表
质量损失率

什么是质量损失率质量损失率是在一定时期企业因内部和企业外部发生的质量损失之和占同期总产值的比重,是显示质量经济性的指标。
企业要在产品设计、工艺技术、材料选择、设备配置、管理措施等方面进行不断改进、完善、创新和提高,以保证和提高产品质量,减少不合格品或废品的发生,从而减少经济损失。
质量损失率的计算: 年度质量损失率=年度总产值年度外部质量损失年度内部质量损失 ×100%内部质量损失是指产品在企业内部从材料入厂验收到产品完工出厂的整个制造过程中因质量问题所产生的损失,包括:● 不合格品的返工、返修处理所产生的损失(材料、人工、设备、能源等消耗)● 材料、零部件甚至产品整体报废所产生的损失● 采购的原材料、零部件或外部单位协作加工、扩散给外部单位制造的零部件,经验收检验发现或用在产品上才发现的不合格所产生的损失● 采购的原材料、零部件在搬运、储存、装配过程中因人为损坏或管理不善所产生的损失● 因设计或工艺错误造成的不合格所产生的损失● 因材料或零部件不合格而进行的质量分析、停工、重新采购和重新检验所产生的损失因材料或零部件不合格而降级或改变用途所产生的损失内部质量损失统计表:内部质量损失统计表XX/XX品质055-2014 填写部门:年月日外部质量损失是指产品交付之后,由于制造未发现或运输、储存等原因造成的产品质量不合格或存在不可接受的缺陷所产生的损失,包括:●在保修期内按合同规定为顾客提供修理或更换零部件服务所产生的损失●赔偿顾客所产生的损失●顾客退货、换货所产生的损失●降价处理所产生的损失●顾客向企业投诉或向司法机关起诉所产生的损失外部质量损失统计表:外部质量损失统计表XX/XX品质055-2014 填写部门:年月日。
质量成本统计分析图表范例

比例 100.0% 80.0% 60.0% 40.0% 20.0% 0.0%
制表:
审核:
核准:
15.00% 1.03% 13.00%
11.00%
预防成本9.00%
鉴定成本7.00%
内部损失5.成00本%
外部损失3.成00本% 1.00%
质量损失率 -1.00%
1损2月失率目月标别
车间
金额
元
比例 %
金额(元)
2020年1月内部损失成本部门分布状态
磨工车间
#DIV/0! 内部损失成本部门分布状态
0.00%
1.05%
0.00%
1.05%
0.00%
1.05%
0.00%
1.05%
质量损失率趋势图 0.00% 0.00% 0.00%
1.05% 1.00% 1.00%
0.00%
1.00%
0.00%
1.00%
0.00%
1.00%
1月
2月
3月
4月
5月
6月
7月
8月
9月
10月
11月
#DIV/0!
0.00%
百分比 1.00%
质量成本统计分析图表
序号
质量成本科 目
单位
1 预防成本
万元
2 鉴定成本
万元
3 内部损失成本 万元
4 外部损失成本 万元
5 工业总产值
万元
6 质量总成本
万元
7 质量成本目标 %
8 质量损失率
%
质量成本结构图
1月
0.00 1.05%
损失 1.00 率目 1.05%
预防成本 鉴定成本 内部损失成本 外部损失成本
16949不良质量成本统计表
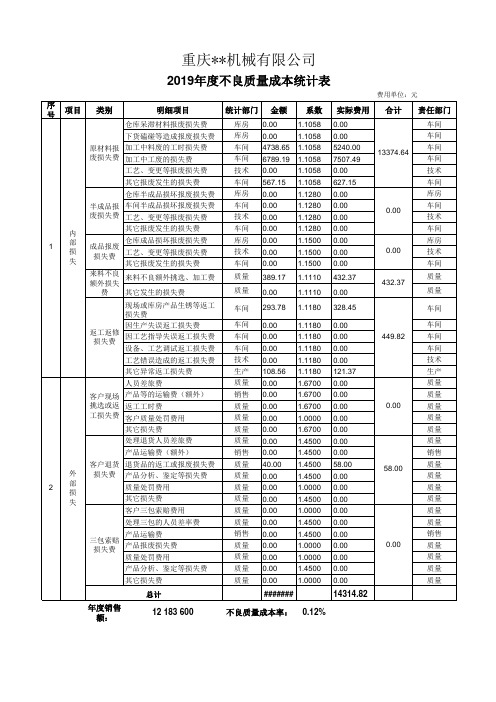
部 2损
质量处罚费用
失
其它损失费
客户三包索赔费用
处理三包的人员差率费
产品运输费 三包索赔
损失费 产品报废损失费 质量处罚费用
产品分析、鉴定等损失费
其它损失费
车间
车间 车间 车间 技术 生产 质量 销售 质量 质量 质量 质量 销售 质量 质量 质量 质量 质量 质量 销售 质量 质量 质量 质量
293.78
库房
半成品报 车间半成品损坏报废损失费 废损失费 工艺、变更等报废损失费
车间 0.00 技术 0.00
1.1280 0.00 1.1280 0.00
车间 0.00
技术
内
其它报废发生的损失费
1
部 损 失
仓库成品损坏报废损失费 成品报废
损失费 工艺、变更等报废损失费 其它报废发生的损失费
车间 0.00 库房 0.00 技术 0.00 车间 0.00
因生产失误返工损失费
返工返修 损失费
因工艺指导失误返工损失费
设备、工艺调试返工损失费
工艺错误造成的返工损失费
其它异常返工损失费
人员差旅费
客户现场 产品等的运输费(额外)
挑选或返 返工工时费 工损失费 客户质量处罚费用ຫໍສະໝຸດ 其它损失费处理退货人员差旅费
产品运输费(额外)
客户退货 退货品的返工或报废损失费
外 损失费 产品分析、鉴定等损失费
总计
#######
14314.82
年度销售 额:
12 183 600
不良质量成本率: 0.12%
制表:
审核:
0.00 0.00 0.00 0.00 108.56 0.00 0.00 0.00 0.00 0.00 0.00 0.00 40.00 0.00 0.00 0.00 0.00 0.00 0.00 0.00 0.00 0.00 0.00
不良质量成本
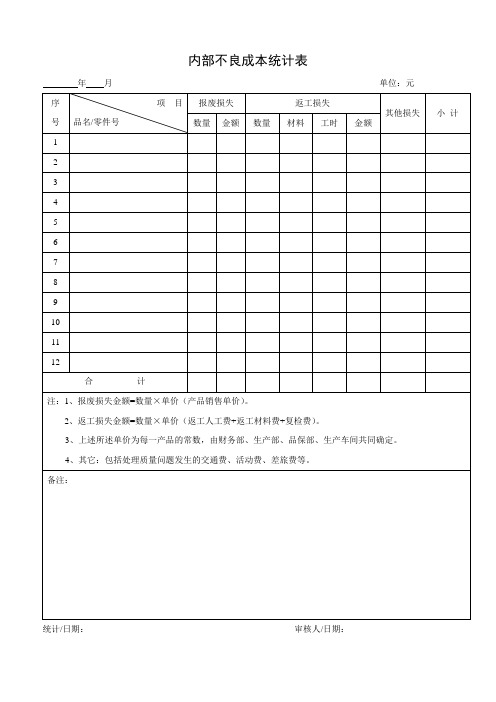
备注:
统计/日期:审核人/日期:
外部不良成本统计表
年月单位:元
序号
项目
品名/零件号
索赔费用
退货损失
其他损失费用
合计
运输费
报废损失返工损失数量金额数量金额1
2
3
4
5
6
7
8
9
10
11
12
合计
注:1、索赔费用=支付给顾客的赔偿金+罚金+索赔处理费(交通费+住宿费+人工费)。
五、(内部损失成本+外部损失成本)/产值
统计/日期:审核/日期:
2、退货中报废损失金额=数量×单价(产品销售单价)。
3、退货中返工金额=数量×单价(返工人工费+材料费+复检费)。
4、上述所述单价为每一产品的常数,由财务部、生产部、品保部、生产车间共同确定。
5、其他损失费用包括客诉、退货、质量事故处理的人员交通费、公关费等。
备注:
统计/日期:审核/日期:
质量成本管理绩效表
内部不良成本统计表
年月单位:元
序
号
项目
品名/零件号
报废损失
返工损失
其他损失
小计
数量
金额
数量
材料
工时
金额
1
2
3
4
5
6
7
8
9
10
11
12
合计
注:1、报废损失金额=数量×单价(产品销售单价)。
2、返工损失金额=数量×单价(返工人工费+返工材料费+复检费)。
3、上述所述单价为每一产品的常数,由财务部、生产部、品保部、生产车间共同确定。
整车厂IATF16949质量目标分解及统计表范例
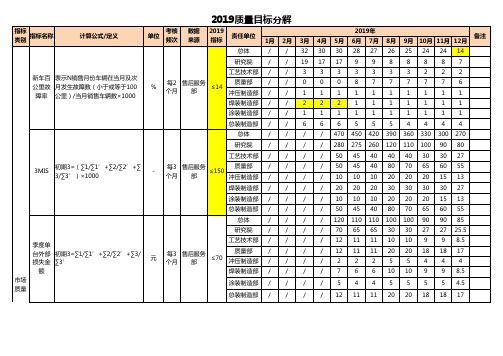
涂装制造部 / / 1 1 1 1 1 1 1 1 1 1
总装制造部 / / 6 6 6 5 5 5 4 4 4 4
总体
/ / / / 470 450 420 390 360 330 300 270
研究院
/
/
/ / 280 275 260 120 110 100 90 80
工艺技术部 / / / / 50 45 40 40 40 30 30 27
每月以在中国质量投诉网站、中
服务质 国汽车质量网、315曝光网站、 量投诉 国家缺陷召回中心等主流媒体收
例
月 质量部 ≤2例 销售中心 ≤2例 ≤2例 ≤2例 ≤2例 ≤2例 ≤2例 ≤2例 ≤2例 ≤2例 ≤2例 ≤2例 ≤2例
集的服务类投诉信息
市场备 当月售后备件采购计划量实际完 件满足 成情况
数量发生400 件以上(含)
月 质量部 0起
总体
0起 0起 0起 0起 0起 0起 0起 0起 0起 0起 0起 0起
投诉信 息处理 及时率
售后投诉信息处理及时率=当月 完成处理数/当月应完成处理数
% 月 销售中心 100% 售后服务部 ### ### 100% 100% 100% 100% 100% 100% 100% 100% 100% 100%
质量 单一问 单一问题关闭率=(实际到期关 改进 题关闭 闭项数/到期应关闭项数)×
%月
自率制冲 1自0制0%冲压件精度合格率=(检具
压件精 测量合格点数/检具测量点数)× % 月
度合格 100%
焊装一 次交付 合格率
一次交付合格率=(合格车辆/报 检车辆)×100%
%
月
焊装单 车不良
点数
焊装单车不良点数=不良点总数/ 下线车辆总数
内部质量损失统计管理办法
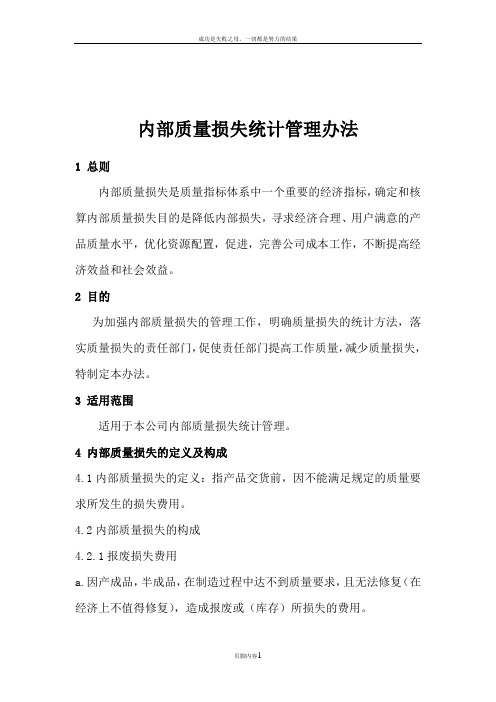
内部质量损失统计管理办法1 总则内部质量损失是质量指标体系中一个重要的经济指标,确定和核算内部质量损失目的是降低内部损失,寻求经济合理、用户满意的产品质量水平,优化资源配置,促进,完善公司成本工作,不断提高经济效益和社会效益。
2 目的为加强内部质量损失的管理工作,明确质量损失的统计方法,落实质量损失的责任部门,促使责任部门提高工作质量,减少质量损失,特制定本办法。
3 适用范围适用于本公司内部质量损失统计管理。
4 内部质量损失的定义及构成4.1内部质量损失的定义:指产品交货前,因不能满足规定的质量要求所发生的损失费用。
4.2内部质量损失的构成4.2.1报废损失费用a.因产成品,半成品,在制造过程中达不到质量要求,且无法修复(在经济上不值得修复),造成报废或(库存)所损失的费用。
b.外购元器件、零部件、原材料在搬运、装备等过程中因人为损坏所造成的损失费用。
c.因设计错误、设计改进、工艺错误、工艺改进等造成产成品、半成品、在制造产品及外购元器件、零部件、原材料报废或(库存)所损失的费用。
4.2.2返修损失费为修复不合格品以及因设计错误、设计改进、工艺错误、工艺改进等造成在制品达不到预期要求,进行返修所需支付的费用,包括人工费、材料消耗、更换的零部件、原材料等的费用。
4.3内部质量损失的分类4.3.1制造性质量损失类:指产品在生产制造过程中,由于管理不善操作不当发生的损失费用。
4.3.2技术性质量损失类:指产品因设计错误、设计改进、工艺错误、工艺改进等发生的损失费用。
5 内部质量损失的计算方法5.1报废品损失费用的计算自制报废品损失费=材料费+制造成本-废铁处理价格;外购损失费=采购价格+运输价格+延期损失费;外协、扩散件损失费=材料+运输+延期损失费。
(注:材料价格、外购、扩散延期损失费(由采购部提供);废铁处理价格、运输价格、外协损失费(由计划物控部提供);制造成本(由工艺部提供)。
)5.2返修品损失费用的计算自制返修损失费用=工时费+材料损失费+能耗+运输5.3焊接一次合格率、探伤一次合格率损失费用的计算焊接一次合格率损失费用=返修数×(目标值-实现率)×单价探伤一次合格率损失费=返修数×(目标值-实现率)×单价6 内部质量损失统计规定内部质量损失的统计,按不同类别发生的报废品、返修品,分别由相关部门收集、计算、填报。
质量事故规定
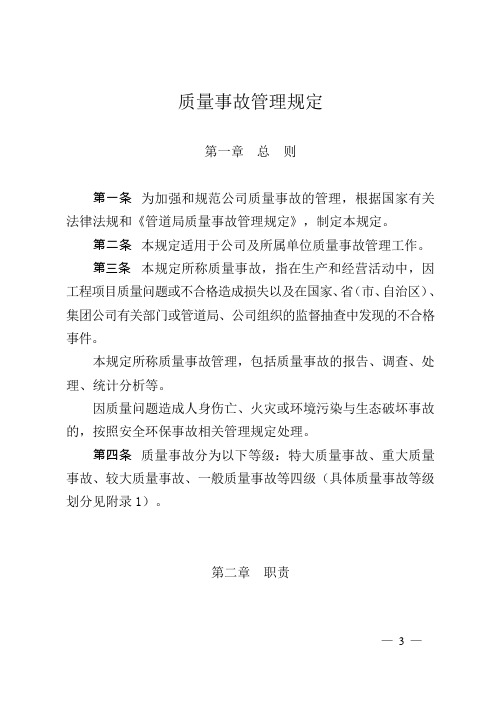
质量事故管理规定第一章总则第一条为加强和规范公司质量事故的管理,根据国家有关法律法规和《管道局质量事故管理规定》,制定本规定。
第二条本规定适用于公司及所属单位质量事故管理工作。
第三条本规定所称质量事故,指在生产和经营活动中,因工程项目质量问题或不合格造成损失以及在国家、省(市、自治区)、集团公司有关部门或管道局、公司组织的监督抽查中发现的不合格事件。
本规定所称质量事故管理,包括质量事故的报告、调查、处理、统计分析等。
因质量问题造成人身伤亡、火灾或环境污染与生态破坏事故的,按照安全环保事故相关管理规定处理。
第四条质量事故分为以下等级:特大质量事故、重大质量事故、较大质量事故、一般质量事故等四级(具体质量事故等级划分见附录1)。
第二章职责第五条公司质量管理部门主要职责是:(一)协助、配合上级单位组织重、特大质量事故的调查处理;(二)组织对较大质量事故以及涉及两个或两个以上的一般质量事故进行事故的调查协调;(三)对质量事故进行统计分析,组织研究预防对策;(四)对基层单位、项目工程一般质量事故的调查、处理情况进行监督检查;(五)按管道局要求上报质量事故有关材料。
第六条公司相关职能部门的职责是:根据职责分工参与质量事故的调查处理等工作。
第七条基层单位、项目部的主要职责:(一)组织调查处理本单位、项目的一般质量事故,进行事故原因分析;(二)积极配合管道局或公司对较大、重大、特大质量事故进行事故的调查处理;(三)进行事故原因分析,制定纠正和预防措施,避免类似事故再次发生;(四)记录事故发生时的影像、图像资料,并妥善保存;(五)组织制定质量事故应急预案,并开展演练,发生质量事故时,按应急预案进行应急处置;(六)按要求上报质量事故有关材料。
第八条质量事故调查组的主要职责是:(一)查明质量事故发生的经过、原因,质量事故发生后应急处置情况;(二)核定或评定质量事故造成的直接经济损失、社会负面影响等;(三)认定质量事故的性质和质量事故责任;(四)总结质量事故教训,提出防范和整改措施;(五)提交质量事故调查报告。
质量损失统计报表范例
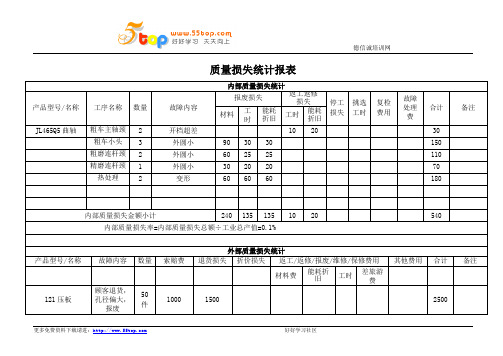
德信诚培训网质量损失统计报表
内部质量损失统计
产品型号/名称工序名称数量故障内容
报废损失
返工返修
损失停工
损失
挑选
工时
复检
费用
故障
处理
费
合计备注材料
工
时
能耗
折旧工时
能耗
折旧
JL465Q5曲轴粗车主轴颈 2 开档超差10 20 30 粗车小头 3 外圆小90 30 30 150
粗磨连杆颈 2 外圆小60 25 25 110
精磨连杆颈 1 外圆小30 20 20 70 热处理 2 变形60 60 60 180
内部质量损失金额小计240 135 135 10 20 540 内部质量损失率=内部质量损失总额÷工业总产值=0.1%
外部质量损失统计
产品型号/名称故障内容数量索赔费退货损失折价损失返工/返修/报废/维修/保修费用其他费用合计备注
材料费能耗折
旧工时
差旅游
费
121压板顾客退货,
孔径偏大,
报废
50
件
1000 1500 2500
125压板顾客退货,
孔径偏小,
退回返工
50
件
200 50 50 100 400
外部质量损失金额小计1200 1500 50 50 100 2900
外部质量损失率=外部质量损失总额÷总产值=0.56%
内外部质量损失金额合计
内外部质量损失率=内外部质量损失总额÷工业总产值=0.66%
简要分析
改进项目责任部门
统计:审核:。