某氧化铜矿的选矿工艺
氧化铜浮选工艺
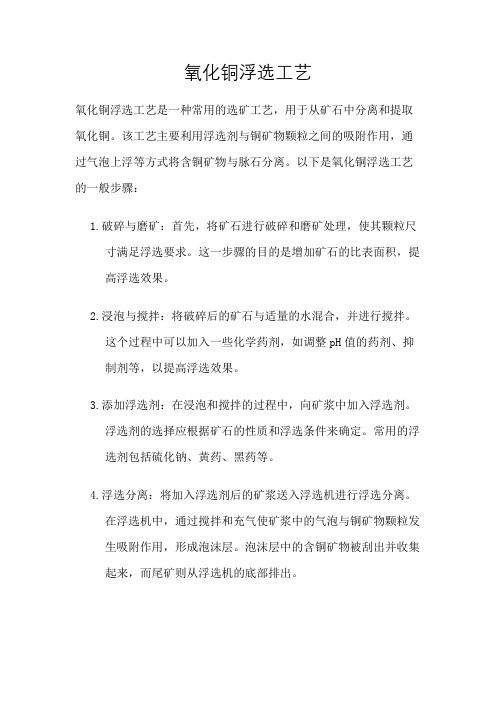
氧化铜浮选工艺
氧化铜浮选工艺是一种常用的选矿工艺,用于从矿石中分离和提取氧化铜。
该工艺主要利用浮选剂与铜矿物颗粒之间的吸附作用,通过气泡上浮等方式将含铜矿物与脉石分离。
以下是氧化铜浮选工艺的一般步骤:
1.破碎与磨矿:首先,将矿石进行破碎和磨矿处理,使其颗粒尺
寸满足浮选要求。
这一步骤的目的是增加矿石的比表面积,提高浮选效果。
2.浸泡与搅拌:将破碎后的矿石与适量的水混合,并进行搅拌。
这个过程中可以加入一些化学药剂,如调整pH值的药剂、抑
制剂等,以提高浮选效果。
3.添加浮选剂:在浸泡和搅拌的过程中,向矿浆中加入浮选剂。
浮选剂的选择应根据矿石的性质和浮选条件来确定。
常用的浮选剂包括硫化钠、黄药、黑药等。
4.浮选分离:将加入浮选剂后的矿浆送入浮选机进行浮选分离。
在浮选机中,通过搅拌和充气使矿浆中的气泡与铜矿物颗粒发生吸附作用,形成泡沫层。
泡沫层中的含铜矿物被刮出并收集起来,而尾矿则从浮选机的底部排出。
5.精矿处理:收集到的含铜泡沫经过进一步的处理,如洗涤、浓
缩和干燥等,最终得到氧化铜精矿。
需要注意的是,氧化铜浮选工艺的具体操作条件和参数应根据矿石的性质、浮选剂的类型以及浮选机的型号等因素进行调整和优化。
此外,为了提高浮选效果,还可以采用一些辅助措施,如添加抑制剂、调整矿浆的pH值等。
西藏某低品位氧化铜矿选矿试验研究报告

西藏某低品位氧化铜矿选矿试验研究报告西藏某低品位氧化铜矿选矿试验研究报告摘要:本试验旨在探究某低品位氧化铜矿选矿技术,选出品质较好的铜精矿。
试验选择的氧化铜矿石含铜量为0.91%,选矿工艺包括粗磨-粗选-二次磨-中选-精选-部分回收铜浸液等步骤。
通过对试验结果的统计和分析,发现该选矿工艺大幅提升了品质,选矿率从原来的5.23%提升至19.73%,铜品位达到23.80%。
关键词:低品位氧化铜矿,选矿试验。
一、选矿原理和工艺流程低品位氧化铜矿选矿试验的原理是通过机械物理和表面化学作用,在矿石表面形成一层带正电的氧化物膜,并利用匝道作用实现氧化铜矿和贫矿物分离。
本试验选择的选矿工艺包括:1. 粗磨-粗选:将矿石通过初级破碎、研磨等工艺,将含铜物质分离出来。
2. 二次磨-中选:在初选后,将结构更加密实的矿石再次进行破碎,将其适当细化。
然后通过中选实现铜和矿细粒子的分离。
中选选择的是机制相同但粒度不同的矿浆。
3. 精选:将经过中选的浮选精矿,进一步提纯铜等金属元素。
4. 部分回收铜浸液:通过回收和再利用浸液,提升铜的含量。
二、实验样品和方法1. 材料和设备试验中用到的样矿来自西藏某采掘区。
选矿设备包括球磨机、筛子、浮选机等。
2. 实验方法(1)粗磨:将样矿粗磨至0.074mm以下(2)粗选:粗磨后通过筛子进行筛选。
(3)二次磨:对筛选后的物料再次进行破碎(4)中选:给矿浆加入中选药剂,使用浮选机将铜精矿从悬浮的矿料中分离。
(5)精选:使用浮选机对铜精矿进行精选,进一步提取铜等金属元素。
(6)部分回收铜浸液:使用铜浸液反应棒将回收的铜浸液加入弱硫酸中进行沉淀和浓缩,得到含铜浸液。
三、实验结果1. 矿石品位原料废石片段不属于选矿过程中的矿物部分,而为矿山中的无用石头部分。
试验中样品含铜量为0.91%。
2. 矿石回收率试验中,对同等重量的样品进行选矿处理,矿石回收率由原来的5.23%提升至19.73%。
3. 铜品位试验中选择的选矿工艺在提纯铜精矿等金属元素上取得了较为显著的提升,铜品位由原来的0.13%提升至23.80%。
低品位难选氧化铜矿化学选矿流程

低品位难选氧化铜矿化学选矿流程引言低品位难选氧化铜矿是一种资源富集程度低、选矿难度较大的铜矿石。
为了充分利用这些矿石资源,科学家们通过研究和实践,深入探索了氧化铜矿的化学选矿流程。
本文将介绍一种适用于低品位难选氧化铜矿的化学选矿流程,并详细分析各个步骤的原理和操作方法。
1.矿石预处理矿石预处理是化学选矿流程的第一步,旨在提高矿石的可选性和选矿效果。
这一步骤通常包括矿石破碎、磨矿和浮选等处理过程。
矿石预处理的重点是将矿石细化到一定的粒度,并去除其中的杂质,以便后续步骤的进行。
2.微细氧化铜矿的浸出微细氧化铜矿的浸出是低品位难选氧化铜矿化学选矿流程的核心步骤之一。
在这一步骤中,我们通常采用酸浸或氨浸的方法,将氧化铜矿中的铜离子溶解出来。
具体的操作方法包括矿石浸出试验、浸出液的准备和浸出反应等。
3.铜离子的还原与沉淀在微细氧化铜矿的浸出过程中,我们得到的是铜的溶液,接下来需要将铜离子还原为固态物质进行沉淀。
这一步骤通常包括还原剂的选择、反应条件的控制和沉淀物的分离等操作。
通过优化还原与沉淀的条件,可以提高铜的回收率和产品质量。
4.沉淀物的浸出与溶解沉淀物的浸出与溶解是将沉淀物中的铜溶解出来的步骤,这一步骤旨在将沉淀物中的有价金属进行回收利用。
通常可使用酸浸、氯化浸或硫酸浸等方法进行。
在这个过程中,需要注意控制酸浸或氯化剂的浓度、温度和反应时间等因素,以获得较高的浸出率和较好的经济效益。
5.铜的电积铜的电积是最后一步,通过此步骤可以得到高纯度的金属铜。
这一步骤通常采用电积槽进行,其中包括阳极和阴极两个电极。
通过控制电流密度、电积时间等参数,可以获得纯度较高的金属铜产品。
结论低品位难选氧化铜矿化学选矿流程是一项难度较大的工作,但通过科学的实践和研究,人们已取得了一定的成果。
本文简要介绍了低品位难选氧化铜矿化学选矿流程的各个步骤和操作方法。
然而,随着科学技术的不断进步,仍然存在着一些问题和挑战。
因此,我们需要进一步深入研究和探索,以优化该选矿流程,并提高矿石资源的综合利用率。
氧化铜矿浮选技术
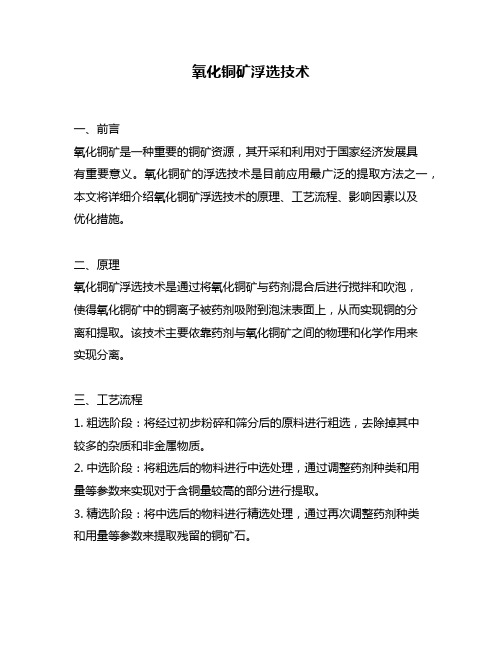
氧化铜矿浮选技术一、前言氧化铜矿是一种重要的铜矿资源,其开采和利用对于国家经济发展具有重要意义。
氧化铜矿的浮选技术是目前应用最广泛的提取方法之一,本文将详细介绍氧化铜矿浮选技术的原理、工艺流程、影响因素以及优化措施。
二、原理氧化铜矿浮选技术是通过将氧化铜矿与药剂混合后进行搅拌和吹泡,使得氧化铜矿中的铜离子被药剂吸附到泡沫表面上,从而实现铜的分离和提取。
该技术主要依靠药剂与氧化铜矿之间的物理和化学作用来实现分离。
三、工艺流程1. 粗选阶段:将经过初步粉碎和筛分后的原料进行粗选,去除掉其中较多的杂质和非金属物质。
2. 中选阶段:将粗选后的物料进行中选处理,通过调整药剂种类和用量等参数来实现对于含铜量较高的部分进行提取。
3. 精选阶段:将中选后的物料进行精选处理,通过再次调整药剂种类和用量等参数来提取残留的铜矿石。
四、影响因素氧化铜矿浮选技术的效果受到多种因素的影响,主要包括以下几个方面:1. 药剂种类和用量:药剂种类和用量是影响氧化铜矿浮选效果最为重要的因素之一。
2. 搅拌速度和时间:搅拌速度和时间对于氧化铜矿浮选过程中泡沫生成和控制起着关键作用。
3. 浮选机型号和规格:不同规格、型号的浮选机对于氧化铜矿浮选效果也会产生不同的影响。
4. 环境条件:环境条件如温度、湿度等也会对于氧化铜矿浮选产生一定影响。
五、优化措施针对以上影响因素,可以采取以下优化措施来提高氧化铜矿浮选技术效率:1. 选择合适的药剂种类和用量,通过实验确定最佳使用方案。
2. 控制搅拌速度和时间,保证泡沫生成和控制的稳定性。
3. 选择合适的浮选机型号和规格,根据生产需求进行合理配置。
4. 优化环境条件,如保持温度、湿度等在合适范围内。
六、总结氧化铜矿浮选技术是一种重要的铜矿提取方法,其原理简单、工艺流程清晰。
但是其效果受到多种因素的影响,需要根据实际情况进行优化措施。
通过对于药剂种类和用量、搅拌速度和时间、浮选机型号和规格以及环境条件等方面进行优化可以提高氧化铜矿浮选技术效率,实现更加高效的铜矿提取。
氧化铜矿的选矿工艺
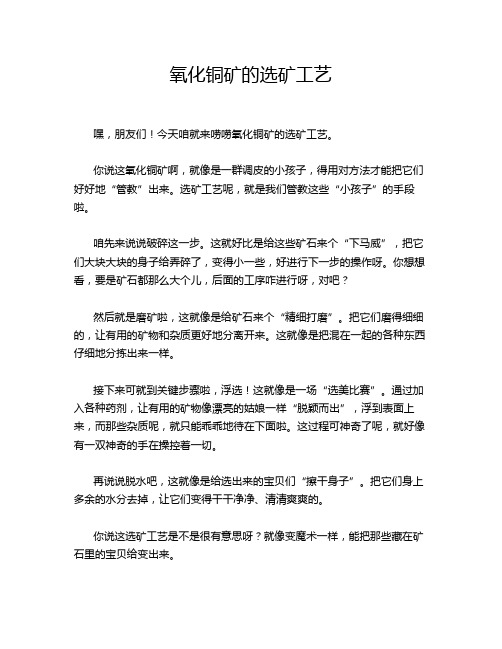
氧化铜矿的选矿工艺嘿,朋友们!今天咱就来唠唠氧化铜矿的选矿工艺。
你说这氧化铜矿啊,就像是一群调皮的小孩子,得用对方法才能把它们好好地“管教”出来。
选矿工艺呢,就是我们管教这些“小孩子”的手段啦。
咱先来说说破碎这一步。
这就好比是给这些矿石来个“下马威”,把它们大块大块的身子给弄碎了,变得小一些,好进行下一步的操作呀。
你想想看,要是矿石都那么大个儿,后面的工序咋进行呀,对吧?然后就是磨矿啦,这就像是给矿石来个“精细打磨”。
把它们磨得细细的,让有用的矿物和杂质更好地分离开来。
这就像是把混在一起的各种东西仔细地分拣出来一样。
接下来可就到关键步骤啦,浮选!这就像是一场“选美比赛”。
通过加入各种药剂,让有用的矿物像漂亮的姑娘一样“脱颖而出”,浮到表面上来,而那些杂质呢,就只能乖乖地待在下面啦。
这过程可神奇了呢,就好像有一双神奇的手在操控着一切。
再说说脱水吧,这就像是给选出来的宝贝们“擦干身子”。
把它们身上多余的水分去掉,让它们变得干干净净、清清爽爽的。
你说这选矿工艺是不是很有意思呀?就像变魔术一样,能把那些藏在矿石里的宝贝给变出来。
可别小看了这每一步哦,要是哪一步没做好,那可就像做饭时盐放多了或者火候没掌握好一样,最后的结果可就不那么完美啦。
而且啊,不同的氧化铜矿还得用不同的方法呢,这就跟每个人都有自己的脾气似的,得顺着来。
在实际操作中,选矿工人就像是一群经验丰富的大厨,精心地烹饪着每一道“菜肴”。
他们要时刻关注着每一个环节,稍有不慎就可能影响到最终的结果。
咱再想想,如果没有这些选矿工艺,那些氧化铜矿不就被白白浪费了吗?那多可惜呀!所以说呀,这选矿工艺可真是太重要啦,它能让那些原本不起眼的矿石变得闪闪发光,为我们的生活带来各种好处呢。
总之呢,氧化铜矿的选矿工艺就是这么神奇又重要,它让我们能更好地利用这些自然资源,为我们的生活增添更多的精彩!原创不易,请尊重原创,谢谢!。
氧化铜矿萃取过程
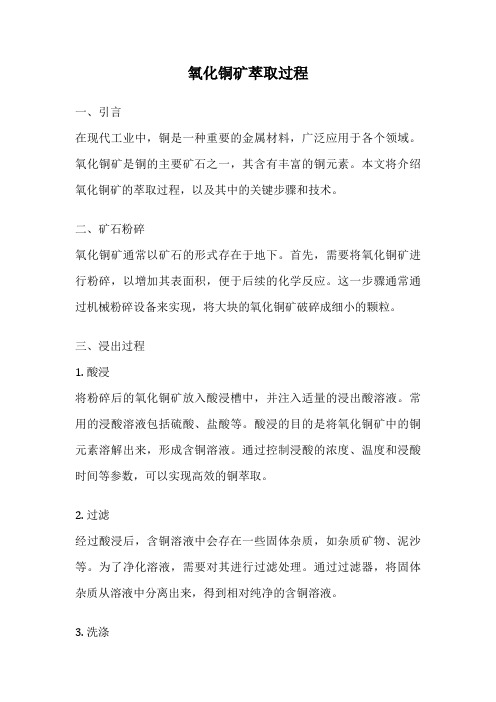
氧化铜矿萃取过程一、引言在现代工业中,铜是一种重要的金属材料,广泛应用于各个领域。
氧化铜矿是铜的主要矿石之一,其含有丰富的铜元素。
本文将介绍氧化铜矿的萃取过程,以及其中的关键步骤和技术。
二、矿石粉碎氧化铜矿通常以矿石的形式存在于地下。
首先,需要将氧化铜矿进行粉碎,以增加其表面积,便于后续的化学反应。
这一步骤通常通过机械粉碎设备来实现,将大块的氧化铜矿破碎成细小的颗粒。
三、浸出过程1. 酸浸将粉碎后的氧化铜矿放入酸浸槽中,并注入适量的浸出酸溶液。
常用的浸酸溶液包括硫酸、盐酸等。
酸浸的目的是将氧化铜矿中的铜元素溶解出来,形成含铜溶液。
通过控制浸酸的浓度、温度和浸酸时间等参数,可以实现高效的铜萃取。
2. 过滤经过酸浸后,含铜溶液中会存在一些固体杂质,如杂质矿物、泥沙等。
为了净化溶液,需要对其进行过滤处理。
通过过滤器,将固体杂质从溶液中分离出来,得到相对纯净的含铜溶液。
3. 洗涤经过过滤后的含铜溶液中仍然可能存在一些酸性物质,需要进行洗涤处理。
洗涤的过程通常是将含铜溶液通过洗涤装置,用水或其他溶液进行冲洗,以去除残留的酸性物质。
四、电积过程1. 电解槽将洗涤后的含铜溶液注入电解槽中。
电解槽通常由两个电极(阳极和阴极)组成,以及一个电解液。
阳极通常由铜金属构成,而阴极则是待积铜的位置。
电解液中包含铜盐和其他添加剂,用于调节电解过程。
2. 电积铜在电解槽中,通入电流,通过电解的方式将铜离子还原成纯铜金属。
铜离子在电流的作用下,从阳极释放出来,然后在阴极上沉积,形成纯铜层。
这一过程被称为电积,也是氧化铜矿萃取过程中的关键步骤。
五、产品处理经过电积过程后,阴极上会沉积一层纯铜金属。
将纯铜从阴极上取下,并进行后续处理。
通常,纯铜会被熔炼成铜块或铜板,以供各种工业应用。
六、结论氧化铜矿萃取过程是一系列复杂的化学反应和物理处理的综合体现。
通过粉碎、浸出、电积等步骤,可以从氧化铜矿中提取出纯铜金属。
这一过程在现代工业中具有重要的意义,有效地利用了资源,同时满足了人们对铜材料的需求。
玻利维亚某氧化铜矿选冶工艺研究
Ke y wo r d s:o x i d i z e d c o p p e r o r e ;f l o t a t i o n ;h e a p l e a c h i n g ;e x t r a c t i o n ;e l e c t r o w i n n i n g
f o r a c i d i c l e a c h i n g d u e t o i t s l o w c o n t e n t o f a l k a l i n e g a n g u e mi n e r a l s .E x p e ime r n t l a r e s u l t s o f l f o t a t i o n - a c i d i c l e a c h i n g ,a g i t a t i o n l e a c h i n g a n d c o l u mn l e a c h i n g s h o w e d t h a t t h e s u i t a b l e i n d u s t i r a l p r o c e s s or f t r e a t i n g t h i s o r e i s h e a p l e a c h i n g - e x t r a c t i o n - s t r i p p i n g - e l e c t r o w i n n i n g wh i c h i s c h ra a c t e r i z e d b y h i g h l e a c h i n g r a t e , h i s h q u li a t y o f e l e c t r o l y t i c c o p p e r a n d l o w c o s t o f i n v e s t me n t a n d i n d u s t ia r l o p e r a t i o n .
氧化铜:氧化铜的浮选方法
氧化铜:氧化铜的浮选方法氧化铜是一种常见的铜矿石,在铜的采矿和冶炼工作中有着重要的地位。
而浮选法是氧化铜矿石的常用选矿方法。
本文将就氧化铜浮选方法进行详细介绍。
氧化铜的性质氧化铜是一种常见的铜矿石,通常呈黑色或深绿色,具有一定的坚硬度。
氧化铜的分子式为CuO,化学性质比较稳定。
氧化铜的浮选方法浮选法是一种选矿方法,可以通过物理化学方法对含有目标矿物的原料进行分离,是氧化铜的主要选矿方法之一。
氧化铜浮选方法主要有以下几个步骤。
矿物粉碎与磨制首先需要将氧化铜矿石进行粉碎和磨制,以便使其尺寸达到浮选的要求。
一般情况下,采用球磨机进行磨制,可以得到粒度较为均匀的氧化铜矿石粉末。
氧化铜的激发在进行氧化铜浮选前,需要对氧化铜进行激发,使其表面带有一定的电荷,并吸附浮选剂。
常用的激发试剂为分子比重较小、挥发性较强的吸附剂,例如丙酮、甲醛等。
氧化铜的捕集在进行浮选时,需要将氧化铜粉末与浮选剂混合,并进行搅拌使其均匀分布。
常用的浮选剂为吸附性较强的十二烷基硫酸钠等有机化合物。
此时,氧化铜会与浮选剂之间产生化学反应,并被浮选剂捕集。
氧化铜的分离与回收为了分离氧化铜和浮选剂,可以采用气泡浮选法。
将气泡通过设备通入混合物中,浮选剂会与氧化铜共同吸附在气泡表面上,然后上升到矿泡顶部,被刮板收集。
收集后的氧化铜可以进一步进行烧结、熔炼等工艺,回收铜元素。
总结通过以上介绍,我们可以了解到氧化铜的浮选方法主要是针对氧化铜矿石进行的,主要包括矿物粉碎与磨制、氧化铜的激发、氧化铜的捕集、氧化铜的分离与回收等步骤。
这些步骤可以分离氧化铜和浮选剂,并回收铜元素,是氧化铜选矿中常用的方法。
氧化铜矿浮选工艺
-
探索试验 表 明 , 随着捕 收 剂 用量 增 加 , 铜精 矿
铜 回 收 率 具 有 增 加 趋 势 ; 收 剂 用 量 在 60 8 0 捕 0 ~ 0 g t , 矿 铜 品 位 和 铜 回 收率 可 以达 到 较 高 指 标 . /时 精
硫 化 后 , 黄 药 或 黑 药 等 捕 收 剂 浮 选 , 法 适 用 于 用 此 处 理 以 孔 雀 石 、 铜 矿 、 铜 矿 为 主 的 矿 石 ; 者 蓝 氯 后
注: 、 Au Ag单 位 为 g t /
表 2 原 矿 的铜 化 学 物 相 分 析 结果
Ta l 2 T e n ls e ut o o p r h mi l b e h a i rs l f p e c e c a y s s c a
氧 化 铜 矿浮 选工 艺
彭 光菊
( 林 矿 产 地 质 研 究 院 , 西 桂 林 5 10 ) 桂 广 4 0 4
摘 要 : 有 效 回收 氧 化 铜 矿 石 中的 铜矿 物 , 用 硫化 ~ 药 浮 选 工 艺对 某 氧 化 铜 矿 石 进 行 浮 选 试 验 研 究 . 为 采 黄 考
金 属 矿 物 铜 矿 物
矿物 /
铁 矿 物
矿 物 /
脉 石矿 物
—
1 原 矿 性 质
1 1 原 矿 主 要 化 学 成 分 和铜 物 相 分 析 . 原矿 的多元 素 和 铜 物 相 分 析结 果 分 别 见 表 1 和 表 2 从 原 矿 的 多 元 素 分 析 结 果 可 知 , 石 中 可 . 矿
第 5 期
彭 光 菊 : 化 铜 矿 浮 选 工 艺 氧
新疆某氧化铜矿的浮选工艺研究
铜蓝 : 矿石 中主要 的硫化 铜 矿物 , 大多 呈 自形 一
半 自形 的板状 、 薄板 状 、 他形 不 规则 粒 状 集合 体 。大
多铜蓝 的周 围有交代残余 的小颗粒的黄铁矿 , 或与 孔雀 石伴 生 , 一起形 成 细脉状 , 或呈 稀 疏浸 染 状 出现 在铁的氧化物赤铁矿、 褐铁矿及脉石 中。与褐铁矿 、
关键词 : 化铜 ; 化铜 ; 硫 氧 活化 剂 ; 浮 性 可
中图分类号 : D 2 T 93
文献标识码 : A
文章编号 :0 3 5 0 2 1 )2—0 0 10 —5 4 (0 2 0 0 9—0 4
铜 是 国民经济 建设 的重要 原 材料 之 一 。 随着 国 民经济 的发 展 , 的需求 量 不 断增 加 , 着铜 矿 的 不 铜 随 断开 采 , 我 国可选 性 相 对 较 好 的单 一 型硫 化 铜 矿 在 石 资 源不 断 减 少 , 因而 加 强对 氧化 铜 一硫 化 铜 混 合
选是 否 适 宜 , 行 了氧 化 铜 浮选 前 的再 磨 细 度 浮选 进
试验 。试验 工艺 流 程 及 药 剂 用 量 如 图 1 示 , 验 所 试 结果 如图 2所示 。
给 矿 药 剂用 置 :g! /
色, 常见其 呈 针 柱 状 、 发状 , 合 体 呈 细 脉 状存 在 毛 集 于 矿石裂 隙 中 , 或呈 他形 粒状 集合 体 充 填 于赤 铁矿 、 褐铁 矿 中 , 与赤铁 矿 、 铁 矿构 成 蜂 窝状 结构 。填 或 褐
第 2 第 2期 8卷
21 0 2年 4月
HUNAN NONF ERROUS M ET S AL
湖 南有 色金 属
9
新疆某氧化铜矿 的浮选工艺研究
- 1、下载文档前请自行甄别文档内容的完整性,平台不提供额外的编辑、内容补充、找答案等附加服务。
- 2、"仅部分预览"的文档,不可在线预览部分如存在完整性等问题,可反馈申请退款(可完整预览的文档不适用该条件!)。
- 3、如文档侵犯您的权益,请联系客服反馈,我们会尽快为您处理(人工客服工作时间:9:00-18:30)。
某氧化铜矿的选矿工艺研究杨树赟(云南迪庆矿业有限公司)1引言随着矿产资源开发利用的强度越来越大,高品位易回收利用的优质矿石逐渐减少,对难处理氧化矿的开展回收利用研究十分必要,也符合国家资源综合利用的产业政策,同时可以带动地区经济发展。
某矿山矿产资源为铜氧化矿,生产工艺流程为:“碎矿为三段一闭路流程,碎矿最终粒度为-12mm;碎矿产品经过两段连续磨矿至-200目占70%,再经一次粗选、一次扫选、两次精选获得铜精矿;选铜作业的尾矿经一次磁粗选获得铁粗精矿,再磨至-200占92%的细度,然后经过两次精选获得铁精矿;精矿脱水为浓密、过滤两段脱水作业,最终产品铜精矿含水14%,铁精矿含水10%”的设计流程,作为一期建设的依据。
2选矿流程2.1单金属矿浮选原则流程单金属矿浮选原则流程的选择,主要取决于矿石中有用矿物的嵌布粒度特性。
一般多为不均嵌布,由于有益矿物和脉石硬度不同,易于泥化,影响回收率,制定选别流程的原则是尽最使有用矿物经粗选、扫选得粗精矿或中矿,然后进行粗精矿或中矿再磨再选,对于嵌布不均的有益矿物在粗磨的条件下能产出部分合格精矿,粗选尾矿进行再磨再选或得粗精矿再磨再选,得到第二部分合格精矿。
处理复杂不均嵌布矿石时,由于该类矿石有用矿物嵌布不均,连生体解离范围较广,有时要用三段磨矿三段选别的流程,才能综合回收不同粒级的有用矿物。
处理含大量原生泥和可溶性盐类矿石时,由于矿泥和矿砂选别工艺不一样,一般采用泥砂分选流程,才能获得比较理想的技术经济指标。
2.2多金属矿浮选原则流程多金属矿浮选是指两种有益矿物以上的金属矿浮选,选别流程一般有优先浮选、混合浮选然后分离浮选和优先、混合浮选兼有的选别流程。
如铅锌矿一般有铅锌依次的优先浮选和铅锌混合浮选得混合精矿,经再磨(或不再磨)后分离浮选得铅精矿和锌精矿。
又如铜、铅锌、硫化铁的多金属矿,其浮选流程一般为先优先浮选铜铅,进行铜铅分离,优先浮选铜铅的尾矿进行锌、硫混合浮选然后分离锌硫或依次优先浮选锌、硫得锌精矿、硫精矿。
某些矿石可利用矿物的可浮性使用选择性捕收剂优先选出已解离的部分矿物,然后再进行混合浮选、分离浮选。
流程中有否再磨工序,视矿物的堪布粒度及解离情况而定。
3氧化铜矿的处理方法3.1浮选法(1)硫化浮选法。
加硫化剂使氧化矿硫化,然后用普通硫化铜浮选的药剂方法进行浮选。
此法适用于处理以孔雀石、蓝铜矿、氯铜矿为主的矿石。
(2)胺类浮选法。
用胺类作捕收剂进行浮选,适用于处理孔雀石、蓝铜矿、氯铜矿等,含矿泥多时应加脉石抑制剂、絮泥剂;如果一般的抑制剂无效时,可选用海藻粉、木素磺酸盐或纤维素木素磺酸盐,聚丙烯酸等作脉石抑制剂。
(3)螯合剂-中性油浮选法。
硅孔雀石可用上述方法回收,但因效果较差,所以选用特殊捕收剂,如辛基取代的碱性染料孔雀绿,辛基氧肪酸钾,苯并三唑及中性油乳化剂,N-取代亚胺二乙酸盐,多元胺和有机卤化物的缩合物,以及季铵盐和季磷盐等进行浮选。
(4)乳浊液浮选法。
氧化铜矿物先经硫化,然后加铜络合剂,造成稳定的亲油性矿物表面,再用中性油乳浊液盖在其表面,造成强疏水的可浮状态,牢固地吸附在气泡上浮。
脉石抑制剂可用丙烯酸聚合物和硅酸钠。
铜络合剂用苯并三唑、甲苯酰三唑、疏基苯并唑、二苯胍等;非极性油浮化剂可用汽油、煤油、柴油等。
3.2化学选矿或与浮选联合处理氧化和混合矿多采用浮选法处理,对于浮选效果较差的氧化矿石,可用化学选矿法处理。
化学选矿法又可分为浸出法(包括酸浸和氨浸),浸出-萃取-电积法;浸出-置换-浮选法(即LPF法);磨矿-浸出-置换-浮选法(即GLPF法);浸出-置换-磁选法(即LCMS法);磨矿-浸出-浮选法,哈尔兰法(即氧化铜矿直接电解法);焙烧(硫酸化焙烧)-浸出-电解法;氯化焙烧-浮选法;离析-浮选法(氯化还原焙烧-浮选法);还原焙烧-氨浸法等。
浸染状铜矿石的浮选一般采用比较简单的流程,经一段磨矿,细度-200目占50~70%,1次粗选,2~3次精选,1~2次扫选,就能达到较为理想的生产技术经济指标。
如铜矿物浸染粒度比较细,可考虑采用阶段磨选流程。
处理斑铜矿的选矿厂,大多采用粗精矿再磨在进行精选的阶段磨选阶段选别流程,其实质是混合-优先浮选流程。
先经一段粗磨、粗选、扫选,再将粗精矿再磨再精选得到高品位铜精矿和硫精矿。
粗磨细度-200目约占45~50%,再磨细度-200目约占90~95%。
致密铜矿石的浮选,致密铜矿石由于黄铜矿和黄铁矿致密共生,黄铁矿往往被次生铜矿物活化,黄铁矿含量较高,难于抑制,分选困难。
分选过程中要求同时得到铜精矿和硫精矿。
通常选铜后的尾矿就是硫精矿。
如果矿石中脉石含量超过20~25%,为得到硫精矿还需再次分选。
处理致密铜矿石,常采用两段磨矿或阶段磨矿,磨矿细度要求较细。
药剂用量也较大,黄药用量100g/t(原矿)以上,石灰8~10kg/t(原矿)以上。
摘要:氧化铜矿石,是一种难以综合回收利用的矿石。
根据氧化铜矿的组成及其特征,提出了氧化铜矿石选矿回收工艺中值得考虑的几个问题,在此基础上通过多方案的对比,来确定较为合理的选矿回收工艺流程。
关键词:氧化铜矿石;综合选矿回收利用工艺;处理技术地质勘测180广东科技2012.12.第23期广东科技2012.12.第23期4某氧化矿选矿的具体工艺流程4.1碎矿工艺流程碎矿工艺设计一般采用三段一闭路流程,如图1所示。
矿山供矿在坑内经过“粗碎”后,从井下经过电机车或胶带运输机输送至碎矿车间的中间贮矿仓,然后经过“中碎”、“细碎”、“筛分”(碎矿与振动筛构成闭路循环),得到粒度为-12mm 的最终碎矿产品,碎矿产品经胶运输机送往磨选车间粉矿仓。
该企业2006年实施“万吨技改”项目,将原用的3台弹簧圆锥破碎机更新为HP500型液压圆锥破碎机,并缩小了分级振动筛的筛孔尺寸,使碎矿最终产品粒度从-12mm 减小为-10mm ,实现了多碎少磨的节能理念,增加了磨矿处理能力,为磨矿作业实现1万t/d 生产能力创造了条件。
4.2磨选工艺流程4.2.11#、2#系列磨选工艺流程原选厂一期建设的磨矿选别工艺,处理矿石2400t/d 的规模是按两个处理矿石1200t/d 系列的方案设计。
因为1#系列选用了选厂闲置的两台3200×3100球磨机,实际生产能力可达1400t/d ,比选用2700×3600球磨机的2#系列高出200t/d ,所以一期建成时实际磨机处理能力可达到2600t/d 。
为了同磨矿能力相匹配,1#系列选铜回路的浮选机总槽数比2#系列多设置了4台(粗扫选2台,精选2台)。
2006年为了提高铜精矿品位,1#系列又增加了一次精选作业,即将原来两次精选改为三次精选。
为了进一步提高铁精矿品位,又在选铁回路新增了立式脉冲振动磁场磁选机和高频振动细筛。
4.2.23#系列磨选工艺流程选厂的二期系统建设,由于磨矿工艺按一段闭路流程设计,选用了两台MQY3600×4500的球磨机,设计处理能力3000t/d 。
2003年12月二期建成以后,选厂设计生产能力为5600t/d 。
一、二期系统投产以后,通过生产优化、技改,碎矿机设备更新等扩产措施,生产能力又逐年提高至1万t/d 的水平。
为了提高精矿品位,3#系列除增加了立式脉冲振动磁选机和高频振动细筛之外,又增加了1台MQY2100×3000的溢流型球磨机,用于高频振动筛筛上产物的进一步细磨。
这些技术措施使铁精矿品位从原先的61%提高到63%以上。
4.3精矿脱水工艺流程(1)一期系统铜精矿和铁精矿的脱水都采用两段脱水工艺。
第一段采用周边传动式浓密机;第二段铜精矿采用折带式真空过滤机,铁精矿采用内滤式圆筒真空过滤机。
由于过滤设备要求的技术参数不同,因此与之匹配的真空过滤系统中配置的辅助设备也有所不同。
(2)二期系统铜精矿和铁精矿的脱水都采用两段脱水工艺。
第一段脱水采用中心传动高效浓缩机;第二段脱水采用TT 系列特种陶瓷过滤机。
4.4尾矿回水工艺流程提高尾矿回水利用率是选厂降低生产水耗和选矿成本的主要措施。
由于尾矿库距离选厂较远,从尾矿库回水不现实,因此,一、二期系统均采用了厂前回水方案,即在生产厂区通过浓密机脱去大量溢流水,返回生产使用以降低“新水”(指从水源地取用的生产用水)消耗量。
脱去了大量水分的高浓度尾矿,从浓密机底部的排矿口流往尾矿输送泵站,再用水隔离泵加压,通过尾矿输送管道、沟渠送往尾矿库或井下充填制备站。
5小结通过以上几种矿石的试验,我们可以得到以下结论:①处理氧化矿时,使用混合捕收剂有利于提高浮选指标,降低药剂消耗,从而达到降低成本、增加经济效益的目的;②多段加药、分段浮选,有利于氧化矿石的浮选;③对氧化铜矿,硫化浮选法优于直接浮选法,可克服直接浮选法精矿品位低,泡沫发粘等缺陷;④流程结构对浮选指标影响颇大,如含泥高的矿石,应采用预先脱泥、泥砂分选工艺流程,并选择合适的中矿返回地点;⑤采用浸出或联合法处理氧化铜矿石,可以说是今后处理贫、细、杂矿石的一个方向,是选矿方法中的一个重要手段。
参考文献:[1]何家良.深部氧化铜铁矿石选矿工艺研究[J].有色金属(选矿部分),1996,(5):43~45.[2]李荣改,宋翔宇,乔江晖,余广学,李志伟,徐靖.含泥难选氧化铜矿石选矿工艺研究[J].矿冶工程,2008,(1):76~78.[3]牛埃生,方伟.某地氧化铜矿选矿工艺研究[J].新疆有色金属,2007,(S2):66~68.[4]徐叶林.氧化铜矿石处理技术[J].新疆有色金属,1994,(1):32~33.!!!!!!!!!!!!!!!!!!!!!!!!!!!!!!!!!!!!!!!!!!!!!!!化,最大接地比压往往是平均接地比压的几倍,在编制吊装方案时不能用平均接地比压代替,否则可能引起因地面承载能力不足而导致起重机倾翻的严重后果。
本文提出的计算方法所需要的参数在起重机使用说明书中都可以查到,因此这种计算方法有一定的实用性。
更准确的计算方法要依赖于履带式起重机的制造厂家提供各项参数,或者由制造厂家直接提供各工况的最大接地比压图表,或相应的计算软件。
参考文献:[1]崔碧海.起重技术.重庆大学出版社.[2]姜建华.履带式起重机支承面的受力分析与计算.电力建设,1997年1期.[3]GBT14560-2011《履带起重机》.(上接第193页)181。