发动机结构与设计各类计算与校核
汽车发动机设计课程设计说明书195柴油机连杆设计及连杆螺栓强度校核计算 精品
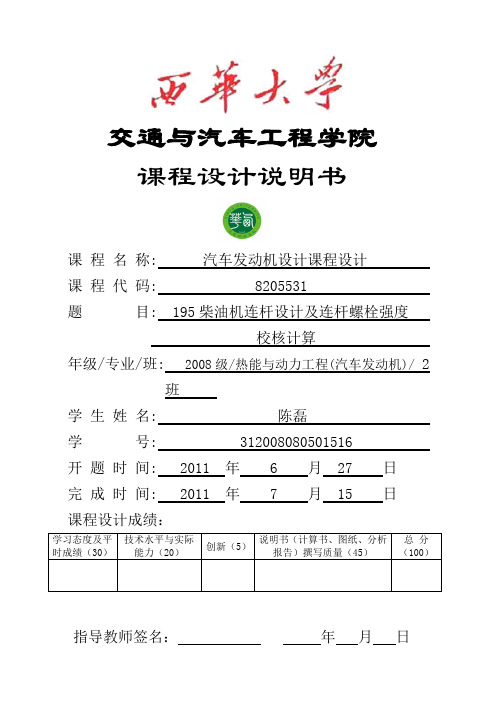
交通与汽车工程学院课程设计说明书课程名称:汽车发动机设计课程设计课程代码: 8205531 题目: 195柴油机连杆设计及连杆螺栓强度校核计算年级/专业/班: 2008级/热能与动力工程(汽车发动机)/ 2班学生姓名: 陈磊学号: 312008********* 开题时间: 2011 年 6 月 27 日完成时间: 2011 年 7 月 15 日课程设计成绩:学习态度及平时成绩(30)技术水平与实际能力(20)创新(5)说明书(计算书、图纸、分析报告)撰写质量(45)总分(100)指导教师签名:年月日目录摘要 (2)1引言 (3)1.1国内外内燃机研究现状 (3)1.2任务与分析 (3)2柴油机工作过程计算 (5)2.1 已知条件 (5)2.2 参数选择 (6)2.3 195柴油机额定工况工作过程计算 (6)3 连杆设计 (9)3.1 连杆结构设计 (9)3.2 连杆材料选择 (11)4 连杆螺钉强度校核 (12)4.1 连杆螺钉的结构设计 (12)4.2 连杆螺钉的强度校核 (13)5 结论 (15)致谢 (17)参考文献 (18)附录:195柴油机额定工况工作过程计算程序 (19)摘要汽车已经在普通民众中得到普及,随着汽车行业的不断发展,越来越多的新技术出现在汽车的心脏——发动机上面。
越来越多的汽车像滚雪球般地形成一股能量强大的冲击波,冲击出一片现代化的肥沃土壤,造就了人类历史上最宏大的物质财富。
据统计,世界上50家最大的公司中,汽车公司就占了近20%,而内燃机作为汽车的核心部件,由于其技术含量高,在国民经济中仍占有较高位置,因此,对内燃机研究人员的培养就显得十分重要。
此次课程设计就是集合这样的时代背景和划时代的教育意义开设的,通过对195柴油机的分析研究,绘制了195柴油机总成纵剖面图,充分认识了195柴油机内部各零部件的结构及装配关系。
此次还设计了连杆,并绘制了所设计的连杆零件图。
并就195柴油机个各设计参数运用Visual Basic 6.0进行工作过程计算,绘制其工作过程的P-V图。
发动机翻转拆装台设计,设计说明书
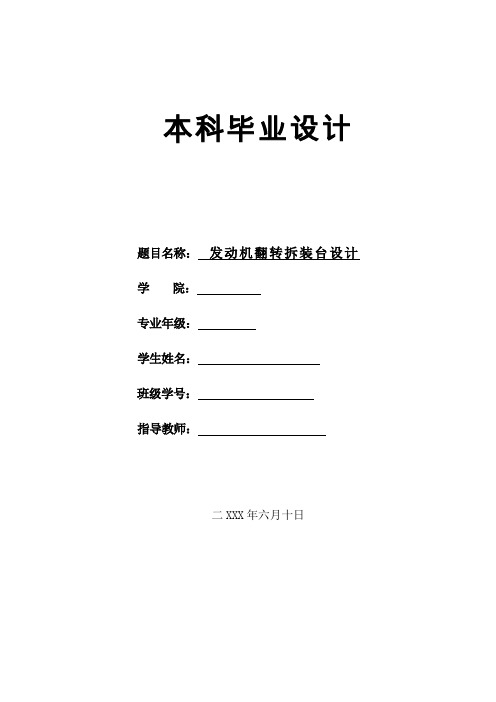
发动机部件计算公式

附录1 发动机部件计算公式1 基础知识1)空气、燃气的焓、熵公式见附录2。
2)气动函数()q λ、()πλ、τλ()、()f λ计算公式见附录3。
2 变循环发动机各部件的计算公式2.1 进气道2.1.1 已知:发动机飞行高度H 、飞行马赫数Ma 。
2.1.2 计算过程1)计算标准大气条件下环境压力0p (静压),环境温度0T (静温)。
当高度H km ≤11时:5.2553001.01325144.308288.15 6.5H p T H ⎧⎛⎫=⨯-⎪ ⎪⎨⎝⎭⎪=-⨯⎩ (2.1) 其中,高度H 的单位为km ,温度的单位为K ,压力的单位为bar 。
2)进气道进口的总温总压:2020 T T Ma p p Ma γγγγ*-*⎧-⎛⎫=+ ⎪⎪⎝⎭⎪⎨-⎪⎛⎫=+ ⎪⎪⎝⎭⎩10112112 (2.2) γ:气体绝热指数,纯空气=1.4γ,燃气=1.33γ。
3)计算进气道总压恢复系数:i 1.35i 1 1.01 1.00.075(1)H H H M M M σσ≤=⎧⎨>=--⎩:: (2.3) 4)计算进气道出口总温总压:iT T p p σ****⎧=⎨=⋅⎩1010(2.4)2.2 压气机双涵道变循环发动机中三个压气机部件,分别是风扇、CDFS 和高压压气机,这三个压气机部件采用同一种计算方法。
2.2.1 已知 压气机进口总温T in *、总压P in *、压气机的压比函数值zz 、物理转速n 、压气机导叶角度α。
2.2.2 计算过程1)计算压气机换算转速:cor n = (2.5)其中,风扇:*,=288.15in d T ,CDFS :*,=428.56862609in d T ,高压压气机:*, 473.603961in d T =。
*inT 为压气机进口总温。
2)计算压气机增压比、效率和换算流量压气机的增压比c pr 、效率c η和换算流量c W 分别是其换算转速和压比函数值及导叶角α的函数。
轮系设计和校核计算(参考)

DA471发动机前端附件驱动系统设计与计算摘要:发动机前端附件传动系统设计的优劣,将直接影响发动机附件的性能及其工作可靠性,进而影响到整机的技术指标。
因此,其设计和开发也越来越引起人们的重视。
附件传动系统是利用带与带轮之间的摩擦力,将发动机的动力传递给附件并使其在合适的转速下运转。
本文结合XXX发动机前端轮系的开发,着重介绍了多楔带的结构及特点。
对发动机多楔带轮系的设计问题进行了探讨,提出了在设计过程中应重点考虑的问题。
关键词: 多楔带、发动机、速比、张紧力、发电机1、多楔带轮系的结构特点传统汽车发动机前端附件传动系多采用V型带传动,但由于其弯曲性能较差,传动的附件较少,已无法满足现代汽车在较小空间内传动多个附件的要求。
两者的主要区别在于多楔带由多个微型三角带组成,传动方式主要包括V 型带传动和多楔带传动。
与V型带相比,多楔带具有以下优点:●传动扭矩大,寿命长;●可以背面传动;●张紧拉力不容易丧失,调整次数少;●传动效率高;●一根带传动轮的数量多,减小了发动机的轴向长度;●可以采用自动张紧机构,无需调整;●带轮直径可尽可能减小。
●2、多楔带的结构多楔带的结构如图1所示。
图1 多楔带的结构它是由楔胶、芯线和顶布三部分构成。
多楔带沿回转方向的楔峰保证了带与带轮良好的接触和摩擦性能, 并使其在整个带宽上受力分布均匀。
楔胶部分的材料一般为氯丁橡胶, 并带有横的沿回转方向的纤维, 使其接触面具有良好的耐磨性、耐油性以及低噪声特性。
芯线为高强度、小延伸率的聚脂绳。
皮带在外力伸长的多少主要与芯线有关,它在整个宽度上以专门的包入技术连续缠绕, 并与楔胶部分牢固结合。
顶布材料也是耐磨的带有增强纤维的氯丁橡胶。
它不仅是芯线的坚固保护层, 而且能够使用背部作为平型带传动。
多楔带分为五种标准断面, PH、PJ、PK、PL、PM 通常根据所要传递的功率大小和速度大小选择多楔带的断面型式。
PK 型带为汽车发动机附件传动通用带型。
汽车发动机的结构设计

汽车发动机的结构设计
汽车发动机的结构设计是汽车制造时必须要经历的一个重要环节,汽车发动机的品质高低关系到了汽车的性能和寿命。
汽车发动机的结构设计可以从以下几个方面来考虑:
1. 气缸数量:汽车发动机的气缸数量通常有四缸、六缸和八缸等多种选择,这个数量的选择会影响到发动机的动力和燃油效率。
2. 吸气方式:汽车发动机可以采用自然吸气或者涡轮增压的方式,自然吸气相对简单,但是涡轮增压可以增加发动机输出功率,提升动力性能。
3. 燃料系统:汽车发动机可以采用汽油或者柴油作为燃料,燃油系统的设计会直接影响到发动机的燃油经济性能。
4. 点火方式:汽车发动机的点火方式有传统的点火和电子点火两种,传统点火相对简单,但是电子点火的响应速度更快,能够提升发动机的性能。
结构设计的目的是优化发动机的性能,提升燃油效率和动力性能,同时保证发动机的可靠性和寿命。
在结构设计时需要注意材料的选择和制造工艺的优化,力求达到最佳的性价比,使汽车发动机在市场上具有竞争力。
发动机做工计算公式

发动机做工计算公式发动机是汽车的心脏,它的性能直接影响着汽车的整体表现。
在汽车工程领域中,对发动机的设计和制造是一个非常重要的课题。
而对于发动机的做工质量的评估,通常会采用一些计算公式来进行分析。
本文将介绍一些常用的发动机做工计算公式,帮助读者了解发动机做工质量的评估方法。
1. 燃烧室压力计算公式。
燃烧室是发动机内部进行燃烧过程的地方,其压力的大小直接关系到发动机的工作效率和性能。
燃烧室压力的计算公式为:P = (ρ R T) / M。
其中,P为燃烧室压力,ρ为燃烧室内气体的密度,R为气体常数,T为燃烧室内气体的温度,M为气体的分子量。
通过这个公式,可以计算出燃烧室内气体的压力,从而评估燃烧室的工作状态。
2. 燃烧效率计算公式。
燃烧效率是衡量发动机燃烧过程完整程度的一个重要指标,其计算公式为:η = (1 (T2/T1)) 100%。
其中,η为燃烧效率,T2为实际燃烧温度,T1为理论燃烧温度。
通过这个公式,可以评估发动机燃烧效率的高低,从而对发动机的做工质量进行评估。
3. 燃烧室温度计算公式。
燃烧室温度是一个影响发动机工作状态的重要参数,其计算公式为:T = P V / (n R)。
其中,T为燃烧室温度,P为燃烧室内气体的压力,V为燃烧室内气体的体积,n为气体的摩尔数,R为气体常数。
通过这个公式,可以计算出燃烧室内气体的温度,从而评估燃烧室的工作状态。
4. 发动机功率计算公式。
发动机的功率是衡量其性能的一个重要指标,其计算公式为:P = T n / 5252。
其中,P为发动机的功率,T为发动机的扭矩,n为发动机的转速。
通过这个公式,可以计算出发动机的功率,从而评估其工作状态。
5. 发动机效率计算公式。
发动机效率是衡量发动机工作效率的一个重要指标,其计算公式为:η = (Output / Input) 100%。
其中,η为发动机效率,Output为发动机的输出功率,Input为发动机的输入功率。
通过这个公式,可以评估发动机的工作效率,从而对其做工质量进行评估。
发动机结构与设计各类计算与校核结构设计.doc

发动机结构与设计各类计算与校核结构设计一、摩托车发动机结构与设计(一)、发动机机体1.气缸体气缸体的作用除形成气缸工作容积外,还用作活塞运动导向,其圆柱形空腔称为气缸。
由于气缸壁表面经常与高温高压燃气接触,活塞在汽缸内作高速运动(最高速度可达100km/s )并施加侧压力,以及气缸壁与活塞环几活塞外圆表面之间反复摩擦,而其润滑条件由较差,所以气缸体必须耐高温、耐高压、耐腐蚀,还应具有足够的刚度和强度。
气缸体的材料一般用优质灰铸铁,为了提高气缸的耐磨性,可以在铸铁中加入少量的合金元素,如镍、铬、钼、磷、硼等。
汽缸内壁按二级精度珩磨加工,其工作表面有较高的关洁度,并且形状和尺寸精度也都比较高。
为了保证气缸壁表面能在高温下正常工作,必须对汽缸体和气缸盖随时加以冷却。
发动机有风冷和水冷两种。
用风冷却时,在汽缸体和气缸盖外表面铸有许多散热片,易增大冷却面积,保证散热充分。
用水冷却时在汽缸体内制有水套。
1.1 气缸直径气缸直径是指气缸内径,与活塞相配合,是发动机的重要参数,许多主要的尺寸如曲柄销直径、气门直径、活塞结构参数等,都要根据气缸直径来选取。
参数设计:气缸直径已标准化,其直径值按一个优先系列合一个常用系列来选取。
根据有关资料可确定气缸的直径D.1.2 气缸工作容积、燃烧室容积和气缸总容积上止点和下止点之间的气缸容积,称为气缸工作容积(也称为总排量)(图1)。
气缸工作容积与气缸直径的平方、活塞冲程的大小成正比。
气缸直径越大、工作容积越大、发动机的功率也就相应地增大。
气缸工作容积的计算公式为N S D V n ⋅⋅=42π式中:Vn——气缸工作容积(ml);D —— 气缸直径(mm ); S —— 活塞行程(mm;)N —— 气缸数目。
参数设计:因设计要求的是单缸发动机的排气量Vn为100ml ,那么其活塞行程为: 24n S V dπ=同时活塞行程S =2r ;r 为曲轴半径 那么:2S r =图1 气缸燃烧室容积和工作室容积 (a )燃烧室容积 (b )工作室容积1.3压缩比气缸总容积与燃烧室容积的比值,称为压缩比。
462Q1汽油机中连杆小头的结构设计与强度校核

角 系 数 , 表 示 平 均 应 力 对 脉 动 部 分 的 影 响 ,ψσ=
2σ-1-σ0 σ0
,此处取 0.2。
经计算,n=9.3, 考虑到连杆工作中由于偏斜引
起的压力沿轴向分布不均匀及活塞卡缸的可能性,
一般取许用安全系数[n]=1.5~2.5,这里取[n]=2.5。
3 结论
由以上校核的结果可以看出,连杆小头的疲劳 安全系数大于连杆小头的许用安全系数,可靠性能 够达到设计要求。 设计的 462Q1 汽油机连杆与测绘 出的 462Q1 汽油机连杆相比,连杆小头的曲柄销直 径增大,外壁直径减小,也就是连杆的小头变薄,小 头的外形尺寸有所减小。 因此,连杆小头的结构尺 寸设计合理,材料的选取也较为合理,能够满足连 杆的工作要求。
σa=8.99(MPa)
则可得安全系数 n= σ-1z
σa εσ"
ψσσm
式 中 :σ-1z 为 材 料 在 对 称 循 环 下 的 拉 压 疲 劳 极
限 ,为(2.0~2.5)×102 N/mm2,此处取 σ-1z=2.5×102 N/mm2;
εσ"为 工 艺 系 数 ,值 为 0.4~0.6,此 处 取 εσ"=0.5;ψσ 为
P'= Pj 2B1rm
Pj=(m'+m1')(1+λ)rω2=(0.21+0.047)×(1+0.3)×
0.066 ×( 2π×5500 )2=3 659.4(N)
2
60
rm=
D+d 4
=
18.5+24 4
=10.6(mm)
P'= Pj = 3659.4 =785(MPa) 2B1rm 2×22×10.6
- 1、下载文档前请自行甄别文档内容的完整性,平台不提供额外的编辑、内容补充、找答案等附加服务。
- 2、"仅部分预览"的文档,不可在线预览部分如存在完整性等问题,可反馈申请退款(可完整预览的文档不适用该条件!)。
- 3、如文档侵犯您的权益,请联系客服反馈,我们会尽快为您处理(人工客服工作时间:9:00-18:30)。
第二篇 设计部分一、摩托车发动机结构与设计(一)、发动机机体1.气缸体气缸体的作用除形成气缸工作容积外,还用作活塞运动导向,其圆柱形空腔称为气缸。
由于气缸壁表面经常与高温高压燃气接触,活塞在汽缸内作高速运动(最高速度可达100km/s )并施加侧压力,以及气缸壁与活塞环几活塞外圆表面之间反复摩擦,而其润滑条件由较差,所以气缸体必须耐高温、耐高压、耐腐蚀,还应具有足够的刚度和强度。
气缸体的材料一般用优质灰铸铁,为了提高气缸的耐磨性,可以在铸铁中加入少量的合金元素,如镍、铬、钼、磷、硼等。
汽缸内壁按二级精度珩磨加工,其工作表面有较高的关洁度,并且形状和尺寸精度也都比较高。
为了保证气缸壁表面能在高温下正常工作,必须对汽缸体和气缸盖随时加以冷却。
发动机有风冷和水冷两种。
用风冷却时,在汽缸体和气缸盖外表面铸有许多散热片,易增大冷却面积,保证散热充分。
用水冷却时在汽缸体内制有水套。
1.1 气缸直径气缸直径是指气缸内径,与活塞相配合,是发动机的重要参数,许多主要的尺寸如曲柄销直径、气门直径、活塞结构参数等,都要根据气缸直径来选取。
参数设计:气缸直径已标准化,其直径值按一个优先系列合一个常用系列来选取。
根据有关资料可确定气缸的直径D.1.2 气缸工作容积、燃烧室容积和气缸总容积上止点和下止点之间的气缸容积,称为气缸工作容积(也称为总排量)(图1)。
气缸工作容积与气缸直径的平方、活塞冲程的大小成正比。
气缸直径越大、工作容积越大、发动机的功率也就相应地增大。
气缸工作容积的计算公式为N S D V n ⋅⋅=42π式中:Vn——气缸工作容积(ml);D —— 气缸直径(mm ); S —— 活塞行程(mm;)N —— 气缸数目。
参数设计:因设计要求的是单缸发动机的排气量Vn为100ml ,那么其活塞行程为: 24n S V dπ=同时活塞行程S =2r ;r 为曲轴半径 那么:2S r =1.3压缩比图1 气缸燃烧室容积和工作室容积 (a )燃烧室容积 (b )工作室容积气缸总容积与燃烧室容积的比值,称为压缩比。
压缩比表示活塞由下止点到上止点时,可燃混合气在气缸内被压缩多少倍。
1.4气缸工作内压力、气缸总推力气缸工作内压力是一个变量,随作功行程的开始,数值急剧下降。
高质量的气缸在跳火燃烧的瞬间,内压力可达3~5MPa 。
气缸总推力是指一个周期内气缸对外实际作功量。
其计算式为:P D sF ηπ24=式中:F ——气缸总推力(N ); η ——气缸效率;一般η=30% P s ——气缸工作内压力(MPa ); D ——气缸直径(mm )。
参数设计:气缸工作内压力: P D sF ηπ24=1.5气缸盖气缸盖用螺柱与气缸体-曲轴箱或气缸体固连在一起。
为了增加密封性,气缸体和气缸盖之间加有气缸衬垫。
气缸盖的作用主要是封闭气缸上部,并与活塞顶部和气缸壁共同形成燃烧室。
燃烧室有很多种形式,不同形式的燃烧室气缸盖的结构又有所不同。
四行程顶置气门发动机的气缸盖上有进、排气门座及气门导管,并设有进气道和排气道,装有进、排气管等。
对气缸盖螺栓联接静强度计算:211.3[]4ca Qd σσπ=≤对螺栓的疲劳强度进行精确校核:1minmin 2()()(2)tc ca a K S S K σσσσσψσψσσ-+-=≥++max 214Qd σπ=min 214pQ dσπ=max min2a σσσ-=式中:1tc σ-――螺栓材料的对称循环拉压疲劳极限,Mpa 。
值见附表。
σψ――试件的材料特性,即循环应力中平均应力的折算系数,对于碳素钢为0.1~0.2,合金钢为0.2~0.3K σ――拉压疲劳强度综合影响系数. S ――安全系数1.6燃烧室燃烧室的种类较多,有锲形、盆形、菱形、半球形等燃烧室。
半球形燃烧室结构呈半球形,比起锲形、盆形燃烧室更为紧凑,面容比最小。
因进、排气门分别置于气缸轴线的两侧,故其配气机构比较复杂。
但有利于促进燃料的完全燃烧和减少排气中的有害成分,对提高经济性和排气净化有利。
(二)、曲柄连杆机构的受力分析与平衡2.1 曲柄连杆比曲柄连杆臂时指曲柄半径与连杆长度之比,简称为连杆比,用λ表示。
由下式定义lr=λ式中:r ——曲柄半径,即曲柄销中心到曲轴中心之间的距离; l ——连杆长度,即连杆大小头轴线之间的距离。
连杆比不仅影响曲柄连杆机构的运动特性,而且影响发动机的外形尺寸。
λ值越大,连杆越矩,发动机的总高度(立式发动机)或总宽度(卧式发动机)越小。
对于V 形发动机,其总高度和总宽度都会减少。
连杆过矩时易导致活塞在运动过程中与曲柄相碰。
因此一般情况下现代摩托车发动机的连杆比31~51=λ,尽可能地采用矩连杆。
参数设计:取λ那么连杆长度:l = r/λ=2.2 曲柄连杆机构运动学曲柄连杆机构运动学是研究曲柄连杆机构各主要零件的运动规律,分析其作用力和力矩及发动机的平衡和曲轴的扭转振动的一门科学。
在计算时,曲轴的转动可以近似看成等速转动,这是因为高速发动机在稳定工况下工作时,由于扭转的不均匀性而引起的曲轴旋转角速度的变化不大。
曲轴的角速度可以写为ω=30πn s rad式中:n ——曲轴转速,m in r 。
曲柄销中心的切向速度v t 和向心加速度a n 分别为: v t = ωr s m a n = ωr 2s 2m式中:r ——曲轴半径,m 。
在讨论连杆、活塞的运动规律时,不用时间t 表达,而是用曲轴转角α,并且规定:将活塞处于上止点位置所对应的曲轴位置作为曲轴转角的起点(即α=0),因而,活塞的速度、加速度的方向朝着曲轴中心线方向为正,背离曲轴中心线方向为负。
参数设计:曲柄的角速度:30nπω=曲柄销中心的切向速度v t 和向心加速度a n 分别为: v t = ωr a n = 2r ω2.3 连杆的角位移、角速度、角加速度对于活塞中心线通过曲轴中心线的曲柄连杆机构(图2)。
曲柄半径r 与连杆长度l 的比值:λ=r/l 则sin β =λsin α 于是可得到连杆的角位移 β =)sin arcsin(αλ当=90°和270°时连杆的角位移为最大,即 λβacrsin max==arcsin (1/4)=14.48 rad/s连杆摆动的角速度ααωλβαωλβλβsin 22'1cos cos cos -===dt d当α为0°和180°时,连杆角速度为最大值,ωλβ±='max当α为90°和270°时,连杆角速度为0。
连杆摆动的角加速度)sin 1(cos sin sincos coscoscos22sin )1()1(1sin sin )sin (cos cos sin 2322322222322222)cos cos (22"αλλωλλωλωβαλβαααλβαβαλβββαβαωωλωλββα---=----=--=---===dtd dtd dtd(三)、 连杆、曲轴组结构设计1. 连杆连杆的作用是将活塞承受的力传给曲轴,从而推动曲轴作旋转运动。
因此,其两端给安装一图2 中心曲柄连杆机构运动分析图个轴承,分别连接活塞销于曲轴销。
连杆一般用中碳钢或中碳合金钢,还可以采用低碳合金钢(如20Cr 、20MnB 、20CrMo )模锻成形,然后进行机械加工。
中碳钢制造的连杆一般要进行调质处理;低碳合金钢制成的连杆大小头内孔要进行渗碳淬火等表面处理,淬火硬度为HRc60~65。
连杆于活塞连接的部分称为连杆小头,与曲轴销连接的部分称为连杆大头,中间的部分称为杆身。
为了润滑活塞销和轴承,连杆小头钻有集油孔或铣有油槽,用以收集发动机运转时被激涨起来的机油,以便润滑。
连杆杆身通常做成“工”字形断面,以保证在合适的刚度和强度下有最小的质量。
连杆大头有剖分式和整体式两种。
整体式连杆倒头相应的曲轴采用组合式曲轴,用轴承与曲柄销相连。
连杆大头的内孔表面有很高的关洁度,以便与连杆轴瓦(或滚针轴承)紧密结合。
摩托车单缸汽油机一般采用整体式连杆,大、小头内分别装有滚柱或滚针轴承。
1.1 曲柄连杆机构的当量质量曲柄连杆机构中的连杆可以用无质量的刚性杆件联系的两个集中质量(连杆小头质量m 1和连杆大头质量m 2)组成的当量系统来代替。
这样往复运动质量m j 为l a m m m m m c p p j ⋅+=+=1 式中:m p ——活塞组的质量; m c ——连杆的质量a ——连杆的重心位置距连杆大头中心的尺寸。
旋转运动质量m r 为l b m m m m m c K k r ⋅+=+=2式中:m k ——曲柄上不平衡部分且相当几种在曲柄销中心的质量;b ——连杆的重心位置距连杆小头中心的尺寸。
1.2 连杆承受的载荷连杆承受的载荷主要视气压力和往复惯性力产生的交变载荷。
其基本载荷是压缩或拉伸。
对于四行程发动机,最大拉伸载荷出现在进气行程开始的上止点附近,其数值主要是活塞组和连杆计算断面以上那部分连杆质量的往复惯性力,即()ωλr G Gpgj2'1''1++=式中:G 'G '1——分别为活塞组和连杆计算断面以上那部分的质量。
最大压缩载荷出现在膨胀行程开始的上止点附近,其数值是最大爆发压力产生的推力减上述的惯性力pj',即pp p jz'.-=‘。
式中:pz——最大爆发压力产生的推力。
1.3 连杆小头的安全系数小头的安全系数按下式计算:σϕδσσσσma zn +=-"1式中:σz1-——材料在对称循环下的拉压疲劳极限;σa——应力副;σm——平均应力;"δσ ——考虑表面加工情况的工艺系数;6.0~4.0="δσ;ϕσ——角系数,()σσσϕσo o -=-12σ1- ——材料在对称循环下的弯曲疲劳极限;σo——材料在脉冲循环下的弯曲疲劳极限,对于钢小头应力按不对称循环变化,在固定角截面的外表面处应力变化较大,通常只计算该处的安全系数,此时循环最大应力 σσσaj a +'=max循环最小应力 σσσac a +'=min式中:'σa ——衬套过盈配合和受热膨胀产生的应力;σaj ——惯性力拉伸引起的应力;σac——受压是产生的应力。
应力副22min maxσσσσσacaja-=-=平均应力 ⎪⎭⎫ ⎝⎛'++=+=σσσσσσa ac aj m2212min max小头安全系数的许用值部小于1.5。
参数设计:连杆材料采用45号钢,它的有关疲劳极限如下: 屈服极限σs=686.5MPa强度极限σb=833.6MPa在对称循环下的拉压疲劳极限 10.23()z s b σσσ-=⨯+ 在对称循环下的弯曲疲劳极限σ1-=450.3MPa在脉冲循环下的弯曲疲劳极限 σσ15.1-=。