[工学]机械制造工艺学第四节机械加工表面质量
机械制造技术:机械加工表面质量
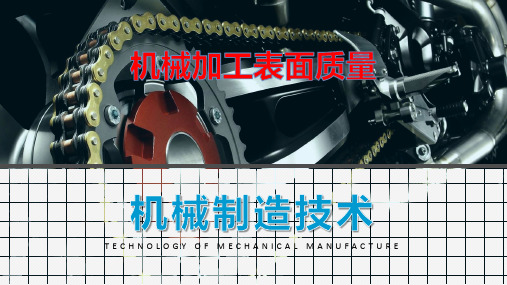
工件材料性质
•太硬、太软、韧性、导热性差
↑→ Ra↓
7
2、表面粗糙度的控制
8
3、表面物理力学性能的控制
影响显微硬度因素
表面物理力学性能
影响残余应力因素
影响金相组织变化 因素
•切削热
9
冷作硬化
机械加工时,工件表面层金属受到切削力的作用产生强烈的塑性变形,使晶格 扭曲,晶粒间产生剪切滑移,晶粒被拉长、纤维化甚至碎化,从而使表面层的强度和 硬度增加,这种现象称为加工硬化,又称冷作硬化和强化。
高速(35~ 50 m/s)打击被加 工零件表面
14
4、表面强化工艺
滚压加工
利用淬硬的滚压工具(滚轮或滚 珠)在常温下对工件表面施加压力, 使其产生塑性变形,工件表面上原 有的波峰被填充到相邻的波谷中, 以减小表面粗糙度值,并使表面产 生冷硬层和残余压应力,从而提高 零件的承裁能力和疲劳强度。
波峰被填充到 相邻的波谷中
金相组织变化 机械加工过积中,在工件的加工区及其邻近的区域,温度会急剧升高,当温度
超过工件材料金相组织变化的临界点,就会发生金相组织变化。
磨削热是造成金相组织变化的根源,故改善磨削烧伤可有两个途径:
尽可能减少磨削热的产生; 改善冷却条件,尽量使产生的热量少传入工件。
12
4、表面强化工艺
表面强化工艺是指通过冷压加工方法使表面层金属发生冷态塑性变形, 以降低表面粗糙度值,提高表面硬度,并在表面层产生残余压应力。这 种方法工艺简单、成本低廉,应用广泛。
机械加工 表面质量
表面的几何特征
表面层物理力学、
化学性能
Байду номын сангаас
(1)表面粗糙度 (2)表面波度 (3)纹理方向
机械加工表面质量

机械加工表面质量零件的表面质量是机械加工质量的重要组成部分,表面质量是指机械加工后零件表面层的微观几何结构及表层金属材料性质发生变化的情况。
一般而言,重要或关键零件的表面质量要求都比普通零件要高。
这是因为表而质量好的零件会在很大程度上提高其耐磨性、耐蚀性和抗疲劳破损能力。
经机械加工后的零件表面并非理想的光滑表面,它存在着不同程度的粗糙波纹、冷硬、裂纹等表面缺陷。
虽然只有极薄的一层(0.05~ 0 .15mm),但对机器零件的使用性能有着极大的影响;零件的磨损、腐蚀和疲劳破坏都是从零件表面开始的,特别是现代化工业生产使机器正朝着精密化、高速化、多功能方向发展,工作在高温、高压、高速、高应力条件下的机械零件,表面层的任何缺陷都会加速零件的失效。
因此,必须重视机械加工表面质量。
一、机械加工表面质量的含义机器零件的加工质量不仅指加工精度,还包括加工表面质量,它是零件加工后表面层状态完整性的表征。
机械加工后的表面,总存在一定的微观几何形状的偏差,表面层的物理力学性能也发生变化。
因此,机械加工表面质量包括加工表面的几何特征和表面层物理力学性能两个方面的内容。
( 一 ) 加工表面的几何特征加工表面的微观几何特征主要包括表面粗糙度和表面波度两部分组成,如图5— 1所示。
表面粗糙度是波距L小于1mm的表面微小波纹;表面波度是指波距L在1~20mm之间的表面波纹。
通常情况下,当L/H(波距/波高)﹤50时为表面粗糙度,L/H=50~1000时为表面波度。
1 .表面粗糙度表面粗糙度主要是由刀具的形状以及切削过程中塑性变形和振动等因素引起的,它是指已加工表面的微观几何形状误差。
2 .表面波度主要是由加工过程中工艺系统的低频振动引起的周期性形状误差,介于形状误差( L 1/H 1﹥ 1000)与表面粗糙度( L 3/H 3﹤ 50)之间。
( 二 )加工表面层的物理力学性能表面层的物理力学性能包括表面层的加工硬化、残余应力和表面层的金相组织变化。
机械制造工艺学 机械加工表面质量及其控制

机械加工表面质量及其控制
任何机械加工所得到的零件表面实际上都不是完全理想的表面。
实践表明,机械零件的破坏,一般都是从表面开始的,这说明零件的机械加工表面质量是至关重要的,它对产品的质量有很大影响。
研究加工表面质量的目的就是要掌握机械加工中各种工艺因素对加工表面质量的影响规律,以便控制加工过程,最终达到提高加工表面质量,提高产品使用性能的目的。
§4-1 加工表面质量及其对使用性能的影响
一.加工表面质量的含义
任何经过机械加工所得到的表面,虽然看起来很光亮,但实际上都存在着不同程度的凹凸不平和内部组织缺陷层,这个缺陷层虽然很薄,但它对零件使用性能的影响却很大。
表面质量是指零件表面的几何形貌和表面层材料的物理、力学性能。
1.加工表面的几何特征
加工表面的几何形貌是由加工过程中刀具与被加工工件的摩擦、切削分离时的塑性变形以及加工系统的振动等因素的作用,在工件表面上留下的表面结构,图4-1是在车床上用金刚石刀具车削无氧铜光学镜面所测得的工件表面三维形貌和其中的一个表面轮廓曲线。
a)
b)
a)表面三维形貌 b)表面轮廓曲线图
图4-1 无氧铜镜面三维形貌和表面轮廓曲线图
加工表面的几何形貌(表面结构)包括表面粗糙度、表面波度、纹理方向和表面缺陷等四个方面的内容,加工后的表面几何形状总是以“峰”、“谷”交替形式出现,如图4-2所示。
图4-2 加工表面的几何形状特征
1)表面粗糙度表面粗糙度是指加工表面的微观几何形状误差,其波。
机械制造工艺课件第四章机械加工表面质量

机械制造工艺
★★★
第四章
第一节
第二节 第三节 第四节
机械加工表面质量
基本概念
表面粗糙度的形成及其影响因素 加工表面力学物理性能的变化及其影响因素 机械加工中的振动
★★★
机械制造工艺
基本慨念
★★★
第一节
零件机械加工表面质量是指零件在机械加工后 表面层的微观几何形状误差和力学物理性能。零件 机械加工后表面层中存在着表面粗糙度、表面波度、 表面加工纹理等微观几何形状误差以及伤痕等缺陷, 零件表面层在加工过程中还会产生加工硬化、金相 组织变化及残余应力等现象。上述种种因素综合作 用的结果,直接影响了零件的寿命及可靠性,从而 影响产品的质量和使用性能。
★★★
机械制造工艺
★★★
图4-2
初期磨损量与零件表面粗糙度 1—轻载荷 2—重载荷
★★★
机械制造工艺
★★★
2、表面质量对零件疲劳强度的影响
零件在交变载荷的作用下,其表面微观不平的凹谷 处和表面层的缺陷处容易引起应力集中而产生疲劳裂纹, 造成零件的疲劳破坏。试验表明,减小零件表面粗糙度 值可以使零件的疲劳强度有所提高。因此,对于一些承 受交变载荷的重要零件,如曲轴其曲拐与轴颈交接处精 加工后常进行光整加工,以减小零件的表面粗糙度值, 提高其疲劳强度。
★★★
机械制造工艺
★★★
图4-3
表面残留面积
★★★
机械制造工艺
★★★
金属切削过程幻灯片
★★★
机械制造工艺
★★★
2、影响表面粗糙度的工艺因素及改善措施
(1)切削用量的影响 进给量大,切屑变形也大,切屑 与刀具前刀面的摩擦以及后刀面与已加工表面的摩擦加剧, 从而增大工件表面粗糙度值。因此,减小进给量利于减小工 vc 件表面粗糙度值。 切削速度对表面粗糙度的影响因工件材料而异。对于塑 性材料,一般情况下,低速或高速切削时,不会产生积屑瘤, 故加工表面粗糙度值都较小,但在中等切削速度下,塑性材 料的工件容易产生积屑瘤或鳞刺,且塑性变形较大,如图4-4 所示。对于脆性材料,加工表面粗糙度主要是由于脆性挤裂 碎裂而成,与切削速度关系较小。所以精加工塑性材料时往 往选择高速或低速精切,以获得较小的表面粗糙度值。
第四章机械加工表面质量及其控制

(三)表面质量对耐腐蚀性的影响
1.表面质量对耐蚀性的影响
零件在潮湿的空气中或在腐蚀性介质中工作, 会使金属表面发生腐蚀。由于粗糙表面的凹谷处容 易积聚腐蚀性介质而发生化学腐蚀,在表面粗糙度 的凹峰间容易产生电化学作用而引起电化学腐蚀。 所以粗糙度越大,腐蚀程度越大,因此减小表面粗 糙度就可提高零件的耐腐蚀性。
第一节 加工表面质量及其对使用性能的影响
1.表面质量的基本概念 加工表面质量包括:加工表面的几何形貌和表面 层材料的力学物理性能和化学性能。 (一)加工表面的几何形貌 1)表面粗糙度 微观误差 S/H<50 2)表面波度 S/H=50~1000
3)纹理方向 4)表面缺陷(伤痕) 如沙眼、气孔、裂痕等
2.表面层力学物理性质对耐蚀性的影响
表层加工硬化及金相组织变化易产生内应力, 导致腐蚀开裂,降低零件腐蚀性,而压应力有利微 裂纹闭合,有利于提高零件表面的抗腐蚀能力。
(四)表面质量对配合质量的影响
对于间隙配合表面,因粗糙度太大,使配合 间隙增大,降低了配合精度,降低了配合的稳定 性;对于过盈配合表面,表面粗糙度越大,两者 相配合时,部分表面凸峰易被挤掉,使过盈量减 小,降低了配合表面的结合强度。因此零件表面 的粗糙度与加工精度应相适应。
二、 表面层材料的金相组织变化
磨削加工表面粗糙度的形成也是由几何因素和表 面层金属的塑性变形(物理因素)决定的,但磨 削过程要比切削过程复杂的多。
(一)几何因素的影响
磨削表面是由砂轮上大量的磨粒刻划出的无 数极细的沟槽形成的。单纯从几何因素考虑,可 以认为在单位面积上刻痕越多,即通过单位面积 的磨粒越多,刻痕的等高性越好,则磨削表面的 粗糙度值越小。
恰好是积削瘤较严重和Rz提高区域,所以必须努力 提高切削速度。
机械制造工艺学教案_第四章_机械加工表面质量

第四章机械加工表面质量任何机械加工所得到的零件表面,实际上都不是完全的理想的表面,经对加工表面的测量和分析说明,零件表面加工后存在着表面粗糙度,表面波度等微观几何形状误差以及划痕裂纹等缺陷。
此外,零件表面层在加工过程中也会产生物理机械性能的变化,有的还会产生化学性质的变化。
实践表明,机械零件的破坏,一般总是从表面层开始的,这说明零件的表面层质量对产品的质量有很大的影响。
研究加工表面质量的目的,就是要掌握机械加工中各种工艺因素对加工表面质量影响的规律,以便应用这些规律控制加工过程,最终达到提高加工表面质量,提高产品性能的目的。
第一节加工表面质量及其对使用性能的影响一加工表面质量的概念用4-1 (a)所示为零件加工表面层治深度方向的变化情况,在最外层生成氧化膜或其它化合物,并吸收渗进了某些气体,液体和固体的粒子,称为吸收层。
厚度一般不超过8Xl(Turn,在加工过程中由切削力造成的表面塑性变形区称为压缩区,其厚度一般约为几十至几百微米,在此压缩区的纤维层,则是由被加工材料与刀具之间的摩擦力造成的。
加工过程中的切削热也会使加工表面层产生各种变化,如同淬火,回火一样将使表面层的金属材料产生金相组织和晶粒大小的变化等。
由上述种种因素综合作用的结果,最终使零件加工表面层的物理机械性能与零件基本有所差异,产生了图4-1 (b)的变化。
所以加工表面质量机械加工表面质量包括两方面的内容:加工表面的几何形状误差,表面层金属的力学物理性能和化学性能(物理-机械性能)(一)加工表面的几何形状误差加工表面的几何形状误差包括如下四部分,1) 表面粗糙度,2) 波度,3) 纹理方向,4) 伤痕。
加工后的表面几何形状总是“峰”“谷”交替出现的形式偏离理想的光滑表面,其偏差有宏观和微观之分。
一般一波距(峰峰或谷谷之间的距离) 和波高H (峰与谷之间的高的比值)不同加以区分,如下图所示。
S/H>1000时,属宏观几何形状误差,如圆度误差,圆柱度误差等,属于加工精度范畴,不属于加工表面质量。
机械制造工艺学 第四节 机械加工表面质量
。 表面层的加工硬化对疲劳强度影响
适当的加工硬化能阻碍已有裂纹的继续扩大和新裂纹的产生,有助于 提高疲劳强度。但加工硬化程度过大,反而易产生裂纹,故加工硬化程度 应控制在一定范围内。
3.表面质量对零件耐腐蚀性的影响
表面粗糙 表面粗糙度值越大,越容易积聚腐蚀性物质;
度的影响
波谷越深,渗透与腐蚀作用越强烈。
波距与波高
波距:峰与峰或谷与谷间的距离, 以L表示; 波高:峰与谷间的高度,以H 表示。
L/H>1000时,属于宏观几何形状误差;
L/H<50时,属于微观形状误差,称作表面粗糙度;
L/H=50~ 1000时,称作表面波度; 主要是由机械加工过程中工
艺系统低频振动所引起。
纹理方向 是指表面刀纹的方向,取决于表面形成所采用 的机械加工方法。一般运动副或密封件对纹理方向有要求。
砂轮的粒度要适度
砂轮的粒度越细,则砂轮单位面积上 的磨粒数越多,磨削表面的刻痕越细,表 面粗糙度值越小;但较度过细,砂轮易堵 塞,使表面组糙度值增大,同时还易产生 波纹和引起烧伤。 砂轮硬度要合适 砂轮的硬度是指磨粒受磨削力后从砂轮上脱落的难易程度。
砂轮太硬,磨粒磨损后不易脱落,使工件表面受到强烈的摩擦和挤 压,增加了塑性变形,表面粗糙度值增大,同时还容易引起烧伤;
二、加工表面质量对机器零件使用性能的影晌 1.表面质量对零件耐磨性的影响
零件的磨 第一阶段 初期磨损阶段 损可分为 第二阶段 正常磨损阶段 三个阶段 第三阶段 急剧磨损阶段
表面粗糙度对摩擦副的影响 不是表面粗糙度值越小越耐磨,
在一定工作条件下,摩擦副表面总是 存在一个最佳表面粗糙度值,表面粗 糙度Ra值约为0.32~0.25μm较好。
(二)、表面层的残余应力 l、表面层残余应力及其产生的原因
机械制造工艺学机械加工表面质量
➢ 合理选择砂轮 根据工件材料、磨削性质选择砂轮 旳硬度、结合剂和组织 ➢ 合理选择磨削用量
合理选择磨削过程旳ap、ft、vw、vs
➢ 改善冷却条件 内冷却、喷汽冷却、强制冷却等
§3.3影响表层材料力学物理性能旳工艺 原因及改善措施
磨削烧伤与磨削裂纹旳控制
➢ 内冷却砂轮 ➢ 选择开槽砂轮
表层比容增大→外压内拉 3)金相组织变化→体积变化 表层比容减小→外拉内压
影响切削残余应力旳工艺原因
◆ 切削用量
➢ v↑→残余应力(热起主 导作用)
残 余 应 力 (G pa )
0.20 0
-0.20
vc =7.7m/min vc =86m/min
vc =213m/min
0
50
100 150 200
200 2.0
8
h
4
0
1.5
0
20
40
60
80 100 120 140
v(m/min)
图4-➢ 其他影响原因:刀具几何角度、刃磨质量,切削液等
磨削加工表面粗糙度影响原因
➢磨削用量影响
❖ 砂轮速度vs↑,Ra↓ ❖ 工件速度vw↑,Ra ↑ ❖磨削深度ap↑,Ra ↑ ❖砂轮纵向进给f↑,Ra ↑ ❖光磨次数↑,Ra↓
200~1000
0.05~0.30
铣削
外压内拉
600~1500
碳钢淬硬
外压内拉
400~750
钢珠滚压钢件 外压内拉
700~800
喷丸强化钢件 外压内拉
1000~1200
渗碳淬火
外压内拉
1000~1100
镀铬
外拉内压
400
机械加工表面质量 机械制造技术基础
第五章 机械制造质量分析与控制
二、控制加工表面质量的途径 • 控制切削(磨削)参数 • 采用超精加工、珩磨等光整加工方法作为
终加工工序 • 采用喷丸、滚压、辗光等表面强化工艺
误差; • 波度: 介于加工精度(宏观)和表面粗糙
度之间的周期性几何形状误差。
第五章 机械制造质量分析与控制
在切削加工表面上,垂直于切削速度方向 的粗糙度称为横向粗糙度,在切削速度方 向上测量的粗糙度称为纵向粗糙度。一般 来说,横向粗糙度较大,它主要由几何因 素和物理因素两方面形成,纵向粗糙度则 主要由物理因素形成。此外,机床—刀具— 工件系统的振动也常是主要的影响因素。
第五章 机械制造质量分析与控制
第四节 机械加工表面质量 表面质量对零件耐磨性、零件疲劳强度、零 件抗腐蚀性能、配合质量等有着重要影响。
第五章 机械制造质量分析与控制
一、机械零件加工表面质量的主要内容 包括: 1.表面层的几何形状特征,主要由以下两个部
分组成: • 表面粗糙度: 就是表面的微观几何形状
第五章 机械制造质量分析与控制
2.表面层的物理、机械性能的变化,主要有以 下三方面的内容:
• 表面层因塑性变形变形引起的冷作硬化 ; 切削(磨削)过程中表面层产生的塑性变形使 晶体间产生剪切滑移,晶格严重扭曲,并 产生晶粒的拉长、破碎和纤维化,引起材 料的强化,这时,它的强度ຫໍສະໝຸດ 第五章 机械制造质量分析与控制
机械制造工艺学第四章机械加工表面质量
表面质量对零件使用性能的影响小结:
零件表面质量
粗糙度太大、太小都不耐磨
适度冷硬能提高耐磨性
对疲劳强度的影响
对耐磨性影响
对耐腐蚀性能的影响
对工作精度的影响
适度冷硬、残余压应力能提高疲劳强度
粗糙度越大、配合精度降低
残余应力越大,加工精度降低
粗糙度越大,耐腐蚀性越差
压应力提高耐腐蚀性,拉应力反之则降低耐腐蚀性ຫໍສະໝຸດ RZλHλ
RZ
1、表面的几何形状误差
表面粗糙度:加工表面的微观几何误差,波长与波高比值小于50。 表面波度:加工表面不平度波长与波高比值在50~1000的几何形状误差 纹理方向:表面刀纹的方向 伤痕:加工表面个别位置出现的缺陷
表面层金属的冷作硬化 表面层的残余应力 表面层金相组织的变化
2、表层金属的力学物理性能和化学性能。
01
02
*
2. 磨削烧伤的三种形式
淬火烧伤:
磨削时工件表面温度超过相变临界温度(碳钢为720)时,则马氏体转变为奥氏体。在冷却液作用下,工件最外层金属会出现二次淬火马氏体组织。其硬度比原来的回火马氏体高,但很薄,其下为硬度较低的回火索氏体和屈氏体。由于二次淬火层极薄,表面层总的硬度是降低的,这种现象称为淬火烧伤。
1
切削速度的影响
2
加工塑性材料时,切削速度对表面粗糙度的影响随切削速度的变化而变化(对积屑瘤和鳞刺的影响) 积屑瘤和鳞刺对表面粗糙度的影响较大。
3
鳞刺:工件表面上微小的鱼鳞状倒刺。
4
鳞刺的生成机理:在中低速切削塑性金属材料且 较大时,刀-屑之间由于冷焊而产生粘结现象,切屑在前刀面上流动时周期性地受阻而瞬时停留,切屑代替前刀面推挤切削层,造成已加工表面上出现拉应力而导裂,生成鳞刺。
- 1、下载文档前请自行甄别文档内容的完整性,平台不提供额外的编辑、内容补充、找答案等附加服务。
- 2、"仅部分预览"的文档,不可在线预览部分如存在完整性等问题,可反馈申请退款(可完整预览的文档不适用该条件!)。
- 3、如文档侵犯您的权益,请联系客服反馈,我们会尽快为您处理(人工客服工作时间:9:00-18:30)。
(2)表面层金相组织变化 指的是加工中,由于切削热的作用引起表层金属金相组织
发生变化的现象。如磨削时常发生的磨削烧伤,大大降低表面 层的物理机械性能。
(3)表面层产生残余应力
指的是加工中,由于切削变形 和切削热的作用,工件表层及其基 体材料的交界处产生相互平衡的弹 性应力的现象。残余应力超过材料 强度极限就会产生表面裂纹。
由于加工硬化提高了表面层的强度,减少了表面进一步塑 性变形和咬焊的可能。一般能提高耐磨性0.5 ~ 1倍。
过度的加工硬化会使金属组织疏松,甚至出现疲劳裂纹和 产生剥落现象,从而使耐磨性下降。
一般地,加工精度要求↑ ,加工成本↑ ,生产效率↓. h与f成正比,与r成反比 。
2.表面质量对零件疲劳强度的影响
在磨削过程中,由于磨粒大多具有很大的负前角,很不锋 利,所以大多数磨粒在磨削时只是对表面产生挤压作用而使表 面出现塑性变形,磨削时的高温更加剧了塑性变形,增大了表 面粗糙度值。
2)砂轮的粒度和砂轮的修整对表面粗糙度的影响
砂轮的粒度
磨粒的大小 磨粒间的距离
砂轮的粒度号越大, 磨粒和磨粒间离越小
砂轮的粒度号↑ ,参与磨削的磨粒↑ ,粗糙度↓ ;
修整砂轮时,纵向进给量对表面粗糙度的影响甚大; 纵向进给量↓ ,砂轮表面的等高性越好 ,粗糙度 ↓ ;
(2)金属表面层的塑性变形
零件的耐腐蚀性在很大程度上取决于表面粗糙度
表面残余应力对零件耐腐蚀性影响 残余压应力使零件表面紧密,腐蚀性物质不易进入,
可增强零件的耐腐蚀性; 拉应力则降低耐腐蚀性
4.表面质量对配合性质的影响
相配零件间的配合关系是用过盈量或间隙值来表示的。
表面粗糙 度的影响
对间隙配合而言,表面粗糙度值太大,会 使配合表面很快磨损而增大配合间隙,改变配 合性质,降低配合精度。
表面层的加工硬化对疲劳强度影响
适当的加工硬化能阻碍已有裂纹的继续扩大和新裂纹的产生,有助于 提高疲劳强度。但加工硬化程度过大,反而易产生裂纹,故加工硬化程度 应控制在一定范围内。
3.表面质量对零件耐腐蚀性的影响
表面粗糙 表面粗糙度值越大,越容易积聚腐蚀性物质;
度的影响
波谷越深,渗透与腐蚀作用越强烈。
表面粗糙度的影响
在交变载荷作用下,零件表面粗糙度、划痕、裂纹等缺陷员易形成应
力集中,并发展成疲劳裂纹,导致零件疲劳破坏。因此,对于重要零件表
面如连杆、曲轴等,应进行光整加工,减小表面粗糙度值,提高其疲劳强
度。 表面残余应力对疲劳强度的影响 影响极大
拉应力加剧疲劳裂纹的产生和扩展;
残余压应力,能延缓疲劳裂纹的产生、扩展,而使零件疲劳强度提高。
一、切削加工表面粗糙度
刀尖圆弧半径
主偏角
切削残留面积的高度
副偏角
进给量
金相组织
金相组织越大,粗糙度也越大;
切削液的选用及刀具刃磨质量
二、磨削过程中表面粗糙度的形成
1、形成因素
切削用量
几何原因 砂轮的粒度和砂轮的修整情况
塑性变形
机械加工振动
(1) 几何原因
1)切削用量对表面粗糙度的影响 砂轮的速度↑ ,单位时间内的磨削量↑ ,粗糙度↓ ; 工件的速度↑ ,单位时间内的磨削量↓ ,粗糙度↑ ; 砂轮纵向进给速度↑ ,每部位重复磨削次数 ↑ ,粗糙度↓。
波距与波高
波距:峰与峰或谷与谷间的距离, 以L表示; 波高:峰与谷间的高度,以H 表示。
L/H>1000时,属于宏观几何形状误差;
L/H<50时,属于微观形状误差,称作表面粗糙度;
L/H=50~ 1000时,称作表面波度; 主要是由机械加工过程中工
艺系统低频振动所引起。
纹理方向 是指表面刀纹的方向,取决于表面形成所采用 的机械加工方法。一般运动副或密封件对纹理方向有要求。
第四节 机械加工表面质量
概述
少数
机械产品的失效形式
因设计不周而导致强度不够; 磨损、腐蚀和疲劳破坏。 多数
实践表明,零件的破坏一般总是从表面层开始的。产品的工作性能,尤 其是它的可靠性、耐久性等,在很大程度上取决于其主要零件的表面质量。
研究机械加工表面质量的目的
掌握机械加工中各种工艺因素对表面质量影响的规律,并 应用这些规律控制加工过程,以达到提高加工表面质量、提高 产品性能的目的。
一、机械加工表面质量的含义
1.表面的几何特征
(1)表面粗糙度 (2)表面波度 (3)纹理方向
2.表面层物理 力学、化学性能
(1)表面层加工硬化(冷作硬化)。 (2)表面层金相组织变化。
(3)表面层产生残余应力。
1、表面的几何形状特征
加工后表面形状,总是以 “峰”、“谷”的形式偏离其 理想光滑表面。按偏离程度有 宏观和微观之分。
表面纹理方向对耐磨性的影响 表面纹理方向影响金属表面的实际接触面积和润滑液的存留情况。
轻载时,两表面的纹理方向与相对运动方向一致时,磨损 最小;当两表面纹理方向与相对运动方向垂直时,磨损最大。
重裁情况下,由于压强、分子亲和力和润滑液的储存等因 素的变化,其规律与上述有所不同。 表面层的加工硬化对耐磨性的影响
对过盈配合而言,装配时配合表面的波峰 被挤平,减小实际过盈量,降低了连接强度, 影响了配合的可靠性。
表面残余应力的影响 表面残余应力会引起零件变形,使零件形状和尺寸发生
变化,因此对配合性质有一定的影响。
第五节 影响表面粗糙度的工艺因素及其改善措施
表面粗糙度的形 成和影响因素
几何因素
物理因素
两方面
二、加工表面质量对机器零件使用性能的影晌 1.表面质量对零件耐磨性的影响
零件的磨 第一阶段 初期磨损阶段 损可分为 第二阶段 正常磨损阶段 三个阶段 第三阶段 急剧磨损阶段
表面粗糙度对摩擦副的影响 不是表面粗糙度值越小越耐磨,
在一定工作条件下,摩擦副表面总是 存在一个最佳表面粗糙度值,ห้องสมุดไป่ตู้面粗 糙度Ra值约为0.32~0.25μm较好。
伤痕 是指在加工表面个别位置出现的缺陷,如沙眼、气 孔、裂痕等。
2、表面层物理力学、化学性能
(1)表面金属层的冷作硬化 指工件在加工过程中,表面层金属产生强烈的塑性变形,使
工件加工表面层的强度和硬度都有所提高的现象。
表示方法
冷硬层深度 h 硬化程度 N
硬化程度:
H N 100%
H 0
其中: H——加工后表面层的显微硬度 H0——材料原有的显微硬度