最新e-火电厂烟气脱硫技术与应用(之二-石灰石-石膏法系统简介)
火电厂烟气脱硫工程技术规范石灰石-石灰-石膏法
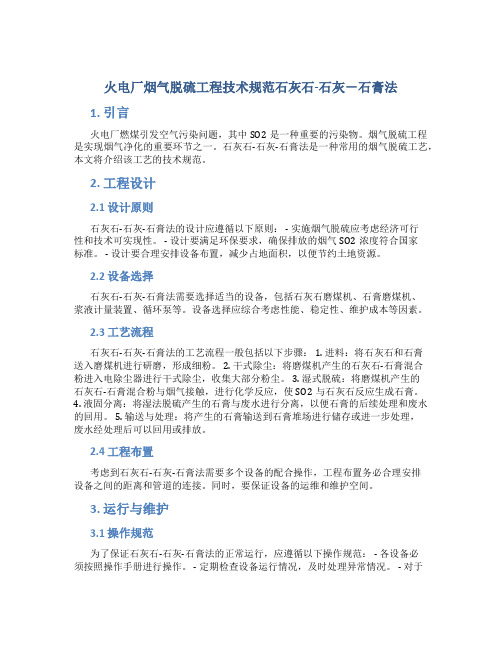
火电厂烟气脱硫工程技术规范石灰石-石灰-石膏法1. 引言火电厂燃煤引发空气污染问题,其中SO2是一种重要的污染物。
烟气脱硫工程是实现烟气净化的重要环节之一。
石灰石-石灰-石膏法是一种常用的烟气脱硫工艺,本文将介绍该工艺的技术规范。
2. 工程设计2.1 设计原则石灰石-石灰-石膏法的设计应遵循以下原则: - 实施烟气脱硫应考虑经济可行性和技术可实现性。
- 设计要满足环保要求,确保排放的烟气SO2浓度符合国家标准。
- 设计要合理安排设备布置,减少占地面积,以便节约土地资源。
2.2 设备选择石灰石-石灰-石膏法需要选择适当的设备,包括石灰石磨煤机、石膏磨煤机、浆液计量装置、循环泵等。
设备选择应综合考虑性能、稳定性、维护成本等因素。
2.3 工艺流程石灰石-石灰-石膏法的工艺流程一般包括以下步骤: 1. 进料:将石灰石和石膏送入磨煤机进行研磨,形成细粉。
2. 干式除尘:将磨煤机产生的石灰石-石膏混合粉进入电除尘器进行干式除尘,收集大部分粉尘。
3. 湿式脱硫:将磨煤机产生的石灰石-石膏混合粉与烟气接触,进行化学反应,使SO2与石灰石反应生成石膏。
4. 液固分离:将湿法脱硫产生的石膏与废水进行分离,以便石膏的后续处理和废水的回用。
5. 输送与处理:将产生的石膏输送到石膏堆场进行储存或进一步处理,废水经处理后可以回用或排放。
2.4 工程布置考虑到石灰石-石灰-石膏法需要多个设备的配合操作,工程布置务必合理安排设备之间的距离和管道的连接。
同时,要保证设备的运维和维护空间。
3. 运行与维护3.1 操作规范为了保证石灰石-石灰-石膏法的正常运行,应遵循以下操作规范: - 各设备必须按照操作手册进行操作。
- 定期检查设备运行情况,及时处理异常情况。
- 对于生产过程中的重要指标,如石膏产量、废水浓度等,应进行监测记录,以便进行评估与分析。
3.2 维护保养定期维护保养是确保石灰石-石灰-石膏法持续高效运行的关键。
石灰石-石膏湿法烟气脱硫脱水系统运行优化

石灰石-石膏湿法烟气脱硫脱水系统运行优化石灰石-石膏湿法烟气脱硫脱水系统是烟气脱硫脱水技术中常见的一种方法,对于工业生产中排放的烟气进行净化处理具有重要意义。
系统的运行优化对于提高处理效率、降低能耗、保障环境安全同样至关重要。
本文将对石灰石-石膏湿法烟气脱硫脱水系统运行优化进行探讨,并提出相关建议和解决方案。
一、系统结构与工作原理石灰石-石膏湿法烟气脱硫脱水系统主要由烟气脱硫脱水装置、石灰石浆液制备系统、脱水系统、石膏脱水再生系统等部分组成。
其工作原理是将排放的烟气经过脱硫塔,利用石灰石浆液中的Ca(OH)2与SO2反应生成CaSO3、CaSO4等沉淀物,并将烟气中的SO2、NOx 等有害物质吸收、氧化、转化成固体废物,然后通过脱水系统将脱硫脱水产生的石膏脱水,达到排放标准后进行再生利用。
二、系统运行优化1. 设备优化石灰石-石膏湿法烟气脱硫脱水系统中的关键设备包括脱硫塔、搅拌器、脱水设备等,对于这些设备的工作状态进行优化是系统运行优化的重要环节。
首先要做好设备的定期维护保养工作,保证设备的正常运行和使用寿命。
其次是对设备进行技术改造和升级,采用先进的技术手段完善设备功能,提高设备的稳定性和耐久性。
还要加强对设备运行数据的监测和分析,及时发现并处理设备运行中的问题,保障系统的平稳运行。
2. 工艺优化石灰石-石膏湿法烟气脱硫脱水系统的工艺优化主要包括石灰石浆液制备、脱硫反应、石膏脱水等环节。
在石灰石浆液制备过程中,应注意石灰石粉末与水的比例、搅拌速度、搅拌时间等参数的调整,以保证制备出浆液的浓度和稳定性。
在脱硫反应过程中,应根据烟气中SO2、NOx的含量和流速等参数,调整脱硫塔中浆液的供应量和分布方式,实现对有害物质的高效吸收和转化。
在石膏脱水环节,应根据脱水设备的特性,合理控制脱水速度和温度,提高脱水效率和质量。
3. 能耗优化石灰石-石膏湿法烟气脱硫脱水系统的运行中涉及大量的能源消耗,包括水泵、搅拌器、脱水设备等设备的驱动能耗,石灰石浆液制备、脱硫反应、石膏脱水等过程中的能量消耗等。
e-火电厂烟气脱硫技术与应用(之二-石灰石-石膏法系统简介)

• 烟气系统分段阻力见表3-4。
烟气再热方案的讨论
旋转式换热器(RGGH)是湿法烟气脱 硫系统中最广泛的一种换热设备
RGGH工作原理
RGGH组装现场
RGGH安装示意
1 增压风机 2 旋转式烟气/烟气再热器 3 吸收塔
虽然旋转式换热器有泄漏问题,且占用空间大,投 资高,但由于其运行成本低。因此到目前为止,旋转式 换热器在脱硫系统中的应用最为广泛。德国的80%湿法 FGD系统安装了这种再热器。在日本自从Shimenoseki 电厂1979年首先使用后,大多数的湿法FGD装置也都安 装了这种热交换器。
5 工艺水供应系统
脱硫岛的工艺水一般均从电厂主系统引接
脱硫工艺水系统负责向下列设备备冷却水
③石灰石制浆
④吸收塔氧化浆池液位调整
⑤石膏脱水建筑冲洗
⑥石膏及真空皮带脱水机冲洗
⑦脱硫场地冲洗
⑧ 氧化空气管道冲洗
⑨ 吸收塔干湿界面冲洗
⑩与浆液接触的阀门和管道的冲洗
用水量大和有废水产生是湿法脱硫的缺点
脱硫废水处理 工艺流程1
脱硫废水处理工艺流程 2
量消耗量按6kV馈线处功率) • 石灰石(粉)消耗量:FGD 装置连续运行7天的石灰石(粉)消耗量平
均值不大于2×8.714t/h • 工艺用水量:FGD 装置连续运行7天的工艺用水量平均值不大于
2×58.6t/h
(3) 脱硫岛布置 • 脱硫岛位于烟囱与煤场之间。
• FGD装置为室外装置,吸收塔不设置建筑物。
工艺流程总图
湿式石灰石—石膏法脱硫流程
back
优点
• 属气液反应,速度快 • 脱硫剂利用率高,脱硫率高 • 煤种适应性好
缺点
• 烟气需再热 • 有废水处理问题,投资大
石灰石——石膏湿法烟气脱硫技术

石灰石——石膏湿法烟气脱硫技术石灰石——石膏湿法烟气脱硫技术石灰石——石膏湿法烟气脱硫技术是已经开发和推广的烟气脱硫技术中的主流技术,占国内外安装烟气脱硫装置总容量的85%以上。
特点是商业应用时间长,工艺技术成熟,配套设备完善,工作稳定,操作简单,脱硫效率可达到95%以上,可靠性高达95%以上。
吸收剂为石灰石粉,资源丰富,价格低廉,使用安全;副产品为脱硫石膏,可用作水泥添加剂、农业土壤调节剂,或进一步清洗、均化、除杂后,生产建筑用石膏板等。
石灰石——石膏湿法烟气脱硫技术广泛应用于火电厂、冶金、各种工业锅炉、窑炉、水泥工业、玻璃工业、化工工业、有色冶炼等行业大型燃烧设备烟气中SO2的排放控制。
一、工艺流程石灰石——石膏湿法烟气脱硫装置主要由烟气系统、石灰石浆液制备系统、烟气吸收及氧化系统、石膏脱水系统、烟气排放连续监测系统(CEMS)以及自动控制系统和公用工程系统等组成。
工艺流程如图示。
一定浓度的石灰石浆液连续从吸收塔顶部喷入,与经过增加风机增压后进入吸收塔的烟气发生接触。
在烟气被冷却洗涤的过程中,烟气中的SO2被浆液中的碳酸钙吸收生成亚硫酸钙而成为净化烟气,净化后的烟气经除雾器除去烟气中的小雾滴,从吸收塔上部排出,进入大气。
向吸收塔底部的溶液中鼓入空气,溶液中的亚硫酸钙被氧化成为硫酸钙结晶物——石膏。
吸收塔底部的溶液是石灰石、石膏组成的浆状混合物,其部分被强制在塔内循环,部分作为产物排出而成为脱水石膏。
二、工艺原理石灰石——石膏湿法烟气脱硫系统中主要的化学反应包括:1. SO2的吸收2.与石灰石的反应3.氧化反应4.CaSO4晶体生成总的反应方程式为:SO2(g)+ CaCO3(s)+2H2O(l)+1/2O2(g)→CaSO4·2H2O(s)+CO2(g)三、脱硫系统的主要设备1.烟气系统烟气系统由进口烟气挡板门、旁路烟气挡板门、钢制烟道、脱硫增压风机等组成。
原烟气经烟道、烟气进口挡板门进入增压风机,经增压风机升压后进入吸收塔。
石灰石石膏法烟气脱硫湿法系统

石灰石筒仓①烟气中的二氧化硫溶解由于吸收剂循环量大和氧化空气的送入,吸收塔下部浆池中的HSO-3或亚硫酸盐几乎全部被氧化为硫酸根或硫酸盐,最后在CaSO4达到一定过饱和度后,结晶形成石膏-CaSO4·2H2O。
石膏可根据需要进行综合利用或作抛弃处理。
烟气脱硫装置由8个系统组成: 1) 烟气系统 2) SO2吸收系统 3) 石灰石浆液制备系统 4) 石膏脱水系统 5) 废水输送系统 6) 工艺水系统 7) 废水处理系统 8) 吸收塔紧急系统。
1) 烟气系统来自锅炉引风机的烟气经增压风机增压后进入烟气-烟气加热器。
在烟气-烟气加热器中,烟气(未经处理)与来自吸收塔的洁净的烟气进行热交换后被冷却。
被冷却的烟气引入到烟道的烟气冷却区域。
来自吸收塔的洁净烟气进入烟气-烟气加热器。
在烟气-烟气加热器中,洁净的烟气与来自锅炉的烟气进行热交换后,被加热到80℃以上。
被加热的洁净的烟气通过烟道和烟囱排向大气。
在锅炉起动阶段和烟气脱硫设备停止运行时,烟气通过旁路烟道进入烟囱。
2) SO2吸收系统该系统的核心设备是吸收塔,在吸收塔内完成对SO2的吸收氧化,塔内总体反应式如下:CaCO3+SO2+2H2O+O2→CaSO4·2H2O+CO2↑对于HCl和HF,还存在以下反应:CaCO3+2HCI→CaC12+H2O+CO2↑CaCO3+2HF→CaF2↓+H2O+CO2↑来自烟气-烟气加热器的烟气通过烟道的烟气冷却区域进入吸收塔。
在烟气冷却区域中,喷入补给水和吸收塔内浆液,使得烟气被冷却到饱和状态。
来自烟气冷却区域的烟气进入由上隔板和下隔板形成的封闭的吸收塔入口烟室。
装在入口烟室下隔板的喷射管将烟气导入吸收塔鼓泡区(泡沫区)的石灰浆液面以下的区域。
在鼓泡区域发生SO2的吸收、氧化、石膏结晶等所有反应。
发生上述一系列反应后,烟气通过上升管流入位于入口烟室上方的出口烟室,然后流出吸收塔。
吸收塔内浆液被吸收塔搅拌器适当地搅拌,使石膏晶体悬浮。
石灰石-石膏湿法烟气脱硫工艺原理
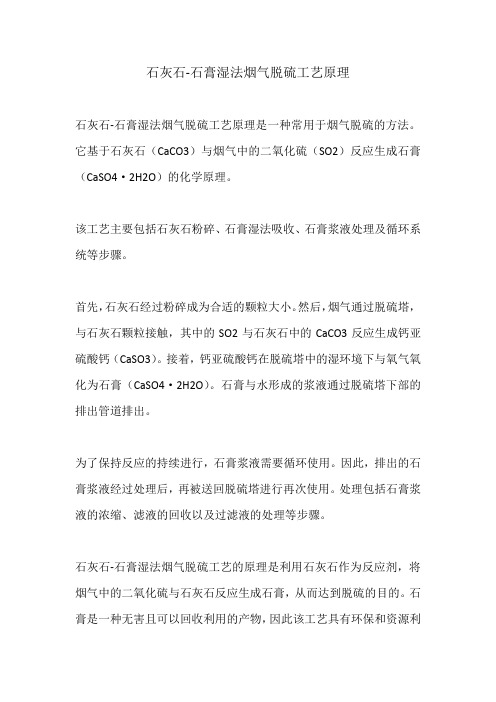
石灰石-石膏湿法烟气脱硫工艺原理
石灰石-石膏湿法烟气脱硫工艺原理是一种常用于烟气脱硫的方法。
它基于石灰石(CaCO3)与烟气中的二氧化硫(SO2)反应生成石膏(CaSO4·2H2O)的化学原理。
该工艺主要包括石灰石粉碎、石膏湿法吸收、石膏浆液处理及循环系统等步骤。
首先,石灰石经过粉碎成为合适的颗粒大小。
然后,烟气通过脱硫塔,与石灰石颗粒接触,其中的SO2与石灰石中的CaCO3反应生成钙亚硫酸钙(CaSO3)。
接着,钙亚硫酸钙在脱硫塔中的湿环境下与氧气氧化为石膏(CaSO4·2H2O)。
石膏与水形成的浆液通过脱硫塔下部的排出管道排出。
为了保持反应的持续进行,石膏浆液需要循环使用。
因此,排出的石膏浆液经过处理后,再被送回脱硫塔进行再次使用。
处理包括石膏浆液的浓缩、滤液的回收以及过滤液的处理等步骤。
石灰石-石膏湿法烟气脱硫工艺的原理是利用石灰石作为反应剂,将烟气中的二氧化硫与石灰石反应生成石膏,从而达到脱硫的目的。
石膏是一种无害且可以回收利用的产物,因此该工艺具有环保和资源利
用的双重优势。
总结起来,石灰石-石膏湿法烟气脱硫工艺原理是通过石灰石与烟气中的二氧化硫反应生成石膏,再将石膏浆液进行循环利用,以达到脱硫的效果。
这种工艺在工业生产中被广泛应用,为减少大气污染做出了重要贡献。
石灰石-石膏湿法脱硫技术的工艺流程、反应原理及主要系统
石灰石-石膏湿法脱硫技术的工艺流程如下图的石灰石-石膏湿法烟气脱硫技术的工艺流程图。
图一常见的脱硫系统工艺流程图二无增压风机的脱硫系统如上图所示引风机将除尘后的锅炉烟气送至脱硫系统,烟气经增压风机增压后(有的系统在增压风机后设有GGH换热器,我们一、二期均取消了增压风机,和旁路挡板,图二),进入脱硫塔,浆液循环泵将吸收塔的浆液通过喷淋层的喷嘴喷出,与从底部上升的烟气发生接触,烟气中SO2的与浆液中的石灰石发生反应,生成CaSO3,从而除去烟气中的SO2。
经过净化后的烟气在流经除雾器后被除去烟气中携带的液滴,最后从烟囱排出。
反应生成物CaSO3进入吸收塔底部的浆液池,被氧化风机送入的空气强制氧化生成CaSO4,结晶生成石膏。
石灰石浆液泵为系统补充反应消耗掉的石灰石,同时石膏浆液输送泵将吸收塔产生的石膏外排至石膏脱水系统将石膏脱水或直接抛弃。
同时为了防止吸收塔内浆液沉淀在底部设有浆液搅拌系统,一期采用扰动泵,二期采用搅拌器。
石灰石-石膏湿法脱硫反应原理在烟气脱硫过程中,物理反应和化学反应的过程相对复杂,吸收塔由吸收区、氧化区和结晶区三部分组成,在吸收塔浆池(氧化区和结晶区组成)和吸收区,不同的层存在不同的边界条件,现将最重要的物理和化学过程原理描述如下:(1)SO2溶于液体在吸收区,烟气和液体强烈接触,传质在接触面发生,烟气中的SO2溶解并转化成亚硫酸。
SO2+H2O<===>H2SO3除了SO2外烟气中的其他酸性成份,如HCL和HF也被喷入烟气中的浆液脱除。
装置脱硫效率受如下因素影响,烟气与液体接触程度,液气比、雾滴大小、SO2含量、PH值、在吸收区的相对速度和接触时间。
(2)酸的离解当SO2溶解时,产生亚硫酸,同时根据PH值离解:H2SO3<===>H++HSO3-对低pH值HSO3-<===>H++SO32-对高pH值从烟气中洗涤下来的HCL和HF,也同时离解:HCl<===>H++Cl-F<===>H++F-根据上面反应,在离解过程中,H+离子成为游离态,导致PH值降低。
百万火电机组石灰石-石膏湿法烟气脱硫工艺简介
百万火电机组石灰石-石膏湿法烟气脱硫工艺简介脱硫工艺系统采用石灰石-石膏湿法烟气脱硫工艺,结合以往的工程实际经验,优化后的工艺系统如下:1石灰石浆液制备系统采用石灰石制浆方案,用自卸车将石灰石输送入石灰石仓,再通过称重计量给料设备送至石灰石球磨机,磨制后的石灰石浆液经过石灰石旋流器旋流后合格的石灰石浆液进入石灰石浆液箱,通过石灰石供浆泵输送至吸收塔补充与SO2反应消耗了的吸收剂。
共设置2个石灰粉仓、2套卸料称重设施、2台石灰石浆液箱。
石灰石仓为混凝土结构,石灰石浆液箱采用碳钢衬玻璃鳞片,搅拌器为碳钢衬胶。
每台石灰石浆液箱设置2台石灰石浆液泵,一运一备,可分别对应2座吸收塔。
供浆管路是循环回路,通过循环回路的分支管线给吸收塔提供需要的石灰石浆液,多余的浆液经循环回路回到浆液箱。
供浆泵出口管线上设有密度测量,供浆的分支管线上设有流量测量和流量控制。
供浆量是根据进口SO2浓度、吸收塔进口烟气量、吸收塔出口SO2浓度、吸收塔内浆液的pH值、石灰石浆液浓度在DCS中进行运算来控制的。
2烟气处理系统从锅炉引风机后的烟道上引出的烟气经过原烟道后进入吸收塔。
在吸收塔内脱硫净化,经除雾器除去水雾后,通过净烟道进入烟囱排入大气。
在吸收塔中,烟气中的二氧化硫、粉尘及其他污染物得以去除。
从吸收塔中排出的经过处理后的烟气导入净烟道,由电厂的湿烟囱直接排放。
烟道最小壁厚按6mm设计,并考虑一定的腐蚀余量。
烟道内烟气流速不超过15m/s。
烟道能够承压为±6000Pa。
烟道壁厚考虑充分的腐蚀余量,横向有足够的槽钢加固,纵向有加强筋,尺寸精度在±0.5%的公差之内。
两台机组烟气分别经引风机升压,进入吸收塔脱硫,出吸收塔后进入主烟道,经烟囱排放。
在有冷凝液烟道设置排放系统。
锅炉与吸收塔的操作是独立的。
正常工况,烟气可以从FGD系统经吸收塔脱硫后至烟囱排放。
在烟气温度高于180℃或其它意外情况时,为避免高温烟气对吸收塔内设备、防腐造成损坏,在吸收塔入口设有事故冷却水系统。
石灰石石膏法烟气脱硫技术及应用
水力旋流器和真空皮带脱 水机
事故浆池、区域浆池及排 放管路
5.过程反应
吸收液通过喷嘴雾化喷入吸收塔,
分散成细小的液滴并覆盖吸收塔的
整个断面。这些液滴与塔内烟气逆 (1)吸收反应
流接触,发生传质与吸收反应,烟 (2HF被吸收。 SO2吸收产物的氧化和中和反应在 吸收塔底部的氧化区完成并最终形
吸收速率=吸收推动力/吸收系数(传质阻力为吸收系数的 倒数)
5.1.2强化吸收反应的措施:
a)提高SO2在气相中的分压力(浓度),提高气相传质动力。
b)采用逆流传质,增加吸收区平均传质动力。
c)增加气相与液相的流速,高的Re数改变了气膜和液膜的界面, 从而引起强烈的传质。
d)强化氧化,加快已溶解SO2的电离和氧化,当亚硫酸被氧化 以后,它的浓度就会降低,会促进了SO2的吸收。
脱硫效率高,>95%。 技术成熟,运行可靠性高。 对煤种的适应性强。 吸收剂资源丰富,价格低廉。 脱硫副产物便于综合利用。 站地面积大,运行费用高。
3.脱硫系统
烟气系 统
吸收液 系统
浆液控 制系统 石膏脱 水系统
排放系 统
烟道、烟气挡板、密封风机、 气——气加热器
吸收塔、除雾器及其冲洗设 备
磨机(湿磨时用)、粉仓 (干粉制浆时用)、浆液箱、
福 建 鑫 泽 环 保 设 备 工 程 有 限 公 司
石灰/石灰石-石膏法烟气脱硫技术是用于130t/h以上容量的 锅炉烟气脱硫技术。烟气经除尘后,通过吸收塔入口区从浆 液池上部进入塔体,在吸收塔内,热烟气逆流向上与自上而 下的浆液(循环喷射)接触发生化学吸收反应,并被冷却。 添加的石灰石浆液由石灰石浆泵输送至吸收塔,与吸收塔内 的浆液混合,混合浆液经循环向上输送由多喷嘴层喷出。浆 液从烟气中吸收硫的氧化物(SOX)以及其他酸性物质,在 液相中硫的氧化物(SOX)与碳酸钙反应,生成亚硫酸钙。 吸收塔自上而下可分为吸收区和氧化结晶区两个部分:上部 洗手去pH值较高,有利于SO2等酸性气体的吸收;下部氧化 区域在底pH值下运行,有利于石灰石的溶解,有利于副产 品的生成反应。从吸收塔排出的石膏浆液经浓缩、脱水,使 其含水量小于10%,生成石膏产品。
石灰石/石膏湿法烟气脱硫技术概述
石灰石/石膏湿法烟气脱硫技术概述摘要:本文主要对烟气脱硫工艺中的石灰石/石膏湿法烟气脱硫技术进行介绍。
首先介绍其工艺原理,烟气中的二氧化硫与浆液中的碳酸钙以及从塔下部浆池鼓入的氧化空气进行反应生成硫酸钙,硫酸钙达到一定饱和度后,结晶形成二水石膏。
关键词:FGD;石灰石/石膏湿法;烟气系统;吸收系统1 烟气脱硫工艺概述烟气脱硫(FGD)是目前燃煤电厂控制气体排放最有效和应用最广的技术。
20世纪60年代后期以来,烟气脱硫技术发展迅速,根据美国电力研究院的统计,大约有200种不同流程的FGD工艺进行了小试或工业性试验,但最终被证实在技术上可行、经济上合理并且在燃煤电厂得到采用的成熟技术仅有十多种。
2. 石灰石/石膏湿法烟气脱硫工艺石灰石/石膏湿法脱硫工艺是目前世界上应用最广泛、技术最为成熟的脱除技术,约占全部安装FGD 容量的70%。
它是以石灰石为脱硫吸收剂,通过向吸收塔内喷入吸收剂浆液,使之与烟气充分接触、混合,并对烟气进行洗涤,使得烟气中的与浆液中的碳酸钙以及鼓入的强制氧化空气发生化学反应,最后生成石膏,从而达到脱除的目的。
2.1 工艺原理石灰石粉加水制成重量浓度约为30%的浆液作为脱硫吸收剂,泵入吸收塔与烟气充分接触混合,烟气中的二氧化硫与浆液中的碳酸钙以及从塔下部浆池鼓入的氧化空气进行反应生成硫酸钙,硫酸钙达到一定饱和度后,结晶形成二水石膏。
脱硫后的烟气依次经过除雾器除去雾滴,再经过加热器升温至大于80℃后,由烟囱排入大气。
2.2.1工艺流程采用价廉易得的石灰石或石灰做脱硫吸收剂,石灰石经破碎磨成粉状与水混合搅拌成吸收浆液。
当采用石灰为吸收剂时,石灰经消化处理加水搅拌成吸收浆液。
锅炉的烟气从电除尘器或布袋除尘后(除尘效率大于97%),经烟气换热器降温后从吸收塔下部进入吸收塔(经过气-气换热器后的烟气温度下降到100℃左右)。
脱硫净化后的烟气依次经过除雾器除去雾滴然后再经气-气换热器升温后,从烟囱排放到大气空中。
- 1、下载文档前请自行甄别文档内容的完整性,平台不提供额外的编辑、内容补充、找答案等附加服务。
- 2、"仅部分预览"的文档,不可在线预览部分如存在完整性等问题,可反馈申请退款(可完整预览的文档不适用该条件!)。
- 3、如文档侵犯您的权益,请联系客服反馈,我们会尽快为您处理(人工客服工作时间:9:00-18:30)。
• CaSO3﹒1/2H2O 含量<1% Wt(以无游离水分的石 膏作为基准)。
• 溶解于石膏中的Cl-含量<0.01% Wt(以无游离水 分的石膏作为基准)。
(5)无有害物质积累 保证在FGD设备不运转的状况下没有损害运转的有
害物质发生积累。
e-火电厂烟气脱硫技术与应用 (之二-石灰石-石膏法系统简介)
一、设计工况与技术要求
(1) 设计工况
• 烟气量: 1928700Nm3/h(实际氧量,干基) • 烟气量: 2059499Nm3/h(实际氧量,湿基) • SO2浓度: 2394.8mg/Nm3(6%氧量,干基) • 烟气入口温度: 114℃
• 设备的位置及各个设施的布置最优化:使压损最小, 优化运行费用和运行程序,并使所有设备维修方便。
• 不同的设备和组件可露天布置或分别安装在单独的或 组合的建筑物中,使流程合理,建筑物相对集中;
• 烟道、增压风机、吸收塔、GGH为室外布置,应提供必 要的防雨措施。
(4)石膏品质 • CaSO4﹒2H2O 含量>87% Wt。
• 烟气挡板
单轴双百叶档板门(湖南加清环保设备有限公司供图)
本项目烟道旁路挡板采用单轴双百叶档板门,配气 动执行器,采用密封风机密封,确保有100%的气密性。 旁路挡板具有快速开启的功能,全关到全开的开启时间 应该尽量短(国产设备已经达到≤15秒)。
FGD入口原烟气挡板和出口净烟气挡板为双叶片挡 板,配电动执行器,采用密封风机密封,确保有100%的 气密性,全开到全关的关闭时间应该尽量短(国产设备 已经达到≤20秒)。
附属设备:
①挡板密封风机——共两台密封风机,一运一备。 风机设计有足够的容量和压头,密封气压力至少维持比 烟道内烟气最高压力高500Pa。
②电加热器——两台密封风机配有一台电加热器。
2 吸收系统
石灰石浆液通过吸收塔浆液循环泵从吸收塔浆 池送至塔内喷嘴,通过喷嘴形成细小浆液滴与烟 气接触发生化学反应,吸收烟气中的SO2。在吸收 塔循环浆池中生成石膏的过程中采取强制氧化, 氧化风机鼓入空气将浆液中未氧化的HSO3-和SO32氧化成SO42-。石膏排出泵将浓度为30%的石膏浆液 从吸收塔送到石膏脱水系统。脱硫后的烟气夹带 的液滴被安装在吸收塔顶部的除雾器收集,使净 烟气的液滴含量不超过保证值75mg/Nm3(干基) 。
回转式烟气再热器(RGGH)的蓄热元件采用涂有 搪瓷的碳钢板。采取防泄漏密封系统,减小未处理烟 气对洁净烟气的污染。RGGH原烟气侧向净烟气侧和净 烟气向原烟气侧的泄漏率始终保持小于1%。并配有全 套吹灰装置。当FGD进口原烟气温度大于或等于设计温 度时,RGGH出口的净烟气温度一般不低于80℃。
但现在有取消换热器的趋势
(6)废水排放 保证脱硫废水经废水处理系统处理后的排水水质
达到<<污水综合排放标准>>(GB8978-1996)中的二级 标准。
(7)烟气系统压降 烟气系统在各种工况的压降保证值2650Pa。
二、 工艺系统及设备
图3-1 湿式石灰石-石膏FGD工艺系统 1.锅炉; 2.电除尘器 3.未净化烟气 4.净化烟气 5.烟气/烟气换热器 6.吸收塔 7.吸收塔持 液槽(吸收塔底槽)8.除雾器 9.氧化用空气 10.工艺过程用水 11.粉状石灰石12.工艺过程 用水 13.粉状石灰石储仓 14.石灰石中和剂储箱 15.水力旋流分离器16.皮带过滤机 17.中间 储箱 18.溢流储箱 19.维修用塔槽储箱 20.石膏储仓 21.溢流废水 22.石膏
量消耗量按6kV馈线处功率) • 石灰石(粉)消耗量:FGD 装置连续运行7天的石灰石(粉)消耗量平
均值不大于2×8.714t/h • 工艺用水量:FGD 装置连续运行7天的工艺用水量平均值不大于
2×58.6t/h
(3) 脱硫岛布置 • 脱硫岛位于烟囱与煤场之间。
• FGD装置为室外装置,吸收塔不设置建筑物。
锅炉从45%BMCR到100%BMCR工况条件下,FGD装置的烟气系统能正常 运行,并留有一定的余量,当烟气温度超过限定的温度180℃时,烟气 旁路系统启运。
在主体发电工程烟道上设置旁路,当锅炉启动、FGD装置故障、检 修停运时,烟气由旁路挡板经烟囱排放。
烟道系统中设有人孔、排水孔和卸灰门。
主要设备有: 静叶可调轴流式增压风机 回转式烟气换热器 电动双百叶双密封挡板
一台 一台 三?个
主要仪表: 压力表、温度计和SO2分析仪等仪表。
增压风机的附属设备: ①电动机——露天布置,为节约用水,电动机选用全封闭空冷式。
②密封风机——每台增压风机配两台密封风机,一运一备。密封风
机强制冷却、密封。
后导叶
前导叶总装图AN系列静叶调轴流风机(成都电力机械厂提供)
增压风机的安放位置的讨论
• 烟气系统分段阻力见表3-4。
烟气再热方案的讨论
旋转式换热器(RGGH)是湿法烟气脱 硫系统中最广泛的一种换热设备
RGGH工作原理
RGGH组装现场
RGGH安装示意
1 增压风机 2 旋转式烟气/烟气再热器 3 吸收塔
虽然旋转式换热器有泄漏问题,且占用空间大,投 资高,但由于其运行成本低。因此到目前为止,旋转式 换热器在脱硫系统中的应用最为广泛。德国的80%湿法 FGD系统安装了这种再热器。在日本自从Shimenoseki 电厂1979年首先使用后,大多数的湿法FGD装置也都安 装了这种热交换器。
(2) 主要性能要求 • 脱硫效率≥ 95.5%(当含硫量增大25%时,旁路烟气挡板关闭,
脱硫系统仍能安全运行,且脱硫效率仍能达到94% ) • 可用率≥ 95% • 服务寿命:30年,大修期为5年。 • 除尘效率≥ 85% • 除雾器出口液滴含量≤75mg/Nm3 • 电耗:置连续运行7天的电量消耗量平均值不超过12750kW/h(电
工艺流程总图
湿式石灰石—石膏法脱硫流程
back
优点
• 属气液反应,速度快 • 脱硫剂利用率高,脱硫率高 • 煤种适应性好
缺点
• 烟气需再热 • 有废水处理问题,投资大
back
FGD 施工现场
back
工程应用:
香港南丫电厂
北京第一热电厂 杭州半山电厂 珞璜电厂
1. 烟道系统
脱硫工程的烟气系统从锅炉引风机后的总烟道上引出,烟气通过增 压风机升压后接入烟气-烟气换热器降温,然后再进入吸收塔脱硫净化 ,经除雾器除去水雾后,又经烟气-烟气换热器将从吸收塔出来的50℃ 左右的脱硫烟气升温至80℃以上,再接入主体发电工程的烟道经烟囱排 入大气。