第六章数控磨床编程
机械基础高级第六章数控机床加工知识第6讲第二节数控加工程序的编制3数控铣床29共30页文档
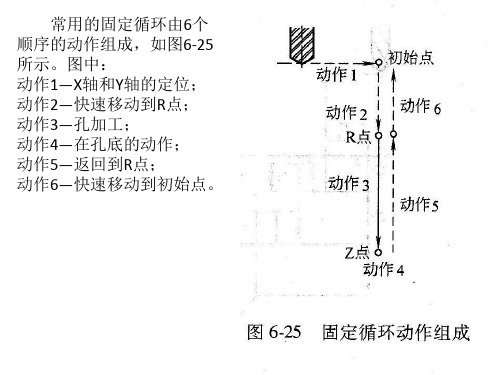
该循环的分步动作:
1、沿着X和Y轴定位; 2、沿Z轴快速移动到R点, 3、沿Z轴从R点到Z点执行钻孔加工, ①第一次钻孔,切削深度Q,增量值, ②后退(孔底→小行程△,增量值); ③后退(孔底→R点) ④前进(R点→离孔底空程高度△的点) ⑤钻孔(第2次或以后的钻孔,切削深度Q+△,增量值) 4、暂停 5、沿Z轴返回到R点(或初始平面),循环结束。如图6-31所示。
பைடு நூலகம்
(5)钻孔加工固定循环G81 格式:G81 X_Y_Z_R_F_K_; X_Y_:孔位数据; Z_ :从R点到孔底的距离; R_ : 从初始位置到R点的距离; F_ :切削进给速度; K_ :重复次数(可省略);
在沿着X和Y轴定位以后,快速移动到R点,再从R点到Z点执行钻 孔加工,然后刀具快速移动退回,如图6-29所示。
一般情况下,G99用于第一次钻孔,G98用于最后钻孔。
(3)高速钻深孔循环G73 格式:G73 X_Y_Z_R_Q_F_K_; X_Y_:孔位数据; Z_ :从R点到孔底的距离; R_ : 从初始位置到R点的距离; Q_ :每次切削进给的切削深度; F_ :切削进给速度; K_ :重复次数(可省略); 刀具沿着Z轴执行间歇进给,当使用这个循环时,切屑可以从
孔中排除,并且能够设定较小的回退值,如图6-27所示。
高速深孔钻循环格式举例:
该程序表示在 XY平面(即工作台)内分别钻削6个不同位置孔 时,其程序格式的应用,其中第一个钻削完以后没有回到起始平面,
而是使用G99方式回到R平面(即编程时设定的安全平面)。钻削其 它孔时不用写G73指令,表明G73指令是模态指令。 N10 M3 S2000;(主轴正转,转速2000) N20 G90 G99 G73 X300. Y-250. Z-150. R-100 Q15. F120.;(定位,钻1 号孔,然后返回到R点) (N30 G90 G99 G73 X300. Y-550. Z-150. R-100 Q15. F120.;) N30 Y-550;(钻2号孔,然后返回到R点) N40 Y-750;(钻3号孔,然后返回到R点) N50 X1000;(钻6号孔,然后返回到R点) N60 Y-550;(钻5号孔,然后返回到R点) N70 G98 Y-250;(钻4号孔,然后返回到初始平面 N80 G80 G28 G91 X0 Y0 Z0;(取消固定循环,返回到参考点) N90 M5 ;(主轴停止旋转)
机械基础(高级)_第六章_数控机床加工知识_第2讲_(第二节_数控加工程序的编制_1_编程基础)_22

宏程序钻孔如下: P0002(主程序号) G50 X100.0 Z200.0;(设定工件坐标系) G00 X0.0 Z102.0 S1000 M3;(快速靠近加工位置,主轴正转、每分 钟1000转) G65 P9100 Z50.0 K20.0 F0.3;(非模态调用9100号宏程序,孔深(绝 对值)Z(#26)=50.0,每次循环的切削量K(#6)=20.0,切削进给速 度F(#9)=0.3mm/min。) G00 X100.0 Z200.0 M05;(宏程序加工完以后,快速退回起刀点、 主轴停止) M30;(主程序结束) O9100(钻孔宏程 #2=0;(上次孔深清零,#2上次孔深变量) IF #23 NE #0 GOTO 1;(如果孔深增量值不等于零,程序转到N1) IF #26 EQ #0 GOTO 8;(如果孔深绝对值等于零,程序转到N8) #23 = #5200-#26;(孔深的增量值=工件长度-孔深的绝对值,#5200 为工件长度)
(3)操作面板MDI输入:预先设定6个工件坐标系(G54~G59)。
3、机床坐标系与原点 机床坐标系:机床的基本坐标系,用来确定工件坐标系。 机床坐标系的原点称之为“机械原点”,它是机床固有的一个 点,不能随意改变。 立式加工中心、卧式加工中心机床坐标系。 4、工件坐标系与原点 工件坐标系:编程时一般选择工件上的某一点作为程序的 原点,并以这个原点作为坐标系的原点,建立一个新的坐标系, 这个坐标系就是工件坐标系。
在编程与加工前,需要确定机床坐标系、工件坐标系、刀具起 点三者的相对位置才能加工。如图6-7所示,这是数控车床坐标系 (机床零点O′)、车削编程工件坐标系(工件原点O)、起刀点等 基准点的位置数据。
5、机床零点与参考点 机床零点:机床基本坐标系的原点。 机床参考点:又称机械原点,它指机床各运动部件在各自 的正方向退至极限位置,此时与机床零点之间的距离,该数值 存贮在数控系统中,由此建立机床零点。 实际上,机床参考点是机床上最具体的一个机械固定点, 而机床零点只是系统内的运算基本点,与机床处于何处无关。 参考点在机床出厂时已经调定,用户一般不做更改。 6、工件零点 工件零点:工件坐标系的原点,在编程时一般选择工件图 样上的设计基准作为编程零点,例如: 回转体零件的端面中心; 非回转体工件的角边; 对称图形的中心; 都可以作为几何尺寸绝对值的基准。这种在工件上以编程零点 建立的坐标系称为工件坐标系。
第6章手工编程
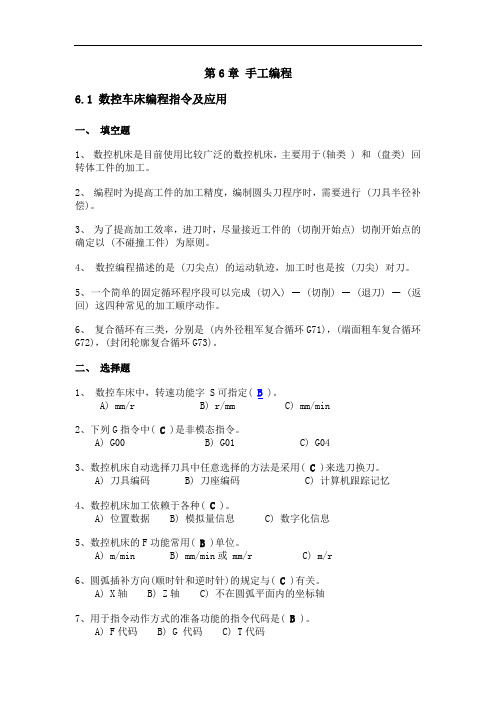
第6章手工编程6.1 数控车床编程指令及应用一、填空题1、数控机床是目前使用比较广泛的数控机床,主要用于(轴类 ) 和 (盘类) 回转体工件的加工。
2、编程时为提高工件的加工精度,编制圆头刀程序时,需要进行 (刀具半径补偿)。
3、为了提高加工效率,进刀时,尽量接近工件的 (切削开始点) 切削开始点的确定以 (不碰撞工件) 为原则。
4、数控编程描述的是 (刀尖点) 的运动轨迹,加工时也是按 (刀尖) 对刀。
5、一个简单的固定循环程序段可以完成 (切入)-(切削)-(退刀)-(返回) 这四种常见的加工顺序动作。
6、复合循环有三类,分别是 (内外径粗军复合循环G71),(端面粗车复合循环G72),(封闭轮廓复合循环G73)。
二、选择题1、数控车床中,转速功能字 S可指定( B )。
A) mm/r B) r/mm C) mm/min2、下列G指令中( C )是非模态指令。
A) G00 B) G01 C) G043、数控机床自动选择刀具中任意选择的方法是采用( C )来选刀换刀。
A) 刀具编码 B) 刀座编码 C) 计算机跟踪记忆4、数控机床加工依赖于各种( C )。
A) 位置数据 B) 模拟量信息 C) 数字化信息5、数控机床的F功能常用( B )单位。
A) m/min B) mm/min或 mm/r C) m/r6、圆弧插补方向(顺时针和逆时针)的规定与( C )有关。
A) X轴 B) Z轴 C) 不在圆弧平面内的坐标轴7、用于指令动作方式的准备功能的指令代码是( B )。
A) F代码 B) G 代码 C) T代码8、用于机床开关指令的辅助功能的指令代码是( C )。
A) F代码 B) S 代码 C) M代码9、切削的三要素有进给量、切削深度和( B )。
A) 切削厚度 B) 切削速度 C) 进给速度10、刀尖半径左补偿方向的规定是( D )。
A) 沿刀具运动方向看,工件位于刀具左侧 B) 沿工件运动方向看,工件位于刀具左侧C) 沿刀具运动方向看,刀具位于工件左侧11、设G01 X30 Z6执行G91 G01 Z15后,正方向实际移动量( C )。
数控车床编程与操作加工PPT课件

G00 Z104.0 X29.3 ap1=0.35 G32 Z56.0 F1.5 G00 X40.0 Z104.0 X28.9 ap2=0.2 G32 Z56.0 F1.5 G00 X40.0 Z104.0 X28.5 ap2=0.2 …….
1.绝对编程与增量编程
(1)绝对编程
绝对值编程是根据预先设定的编程原点计算出绝对值坐标尺寸进行编程的一种方法。即采用绝对值编程时,首先要指出编程原点的位置,并用地址X,Z进行编程(X为直径值)。
增量值编程是根据与前一个位置的坐标值增量来表示位置的一种编程方法。即程序中的终点坐标是相对于起点坐标而言的。
根据试切后工件的尺寸确定刀尖的位置。
O
(a) 确定刀尖在Z向的位置
L
图3-3 数控车床的对刀
O
(a) 确定刀尖在Z向的位置
L
图3-3 数控车床的对刀
O
(b) 确定刀尖在X向的位置
d
O
(b) 确定刀尖在X向的位置
d
三、有关编程代码说明
(一)G功能
准备功能也称为G功能(或称G代码),它是用来指令机床动作方式的功能。准备功能是用地址G及其后面的数字来指令机床动作的。如用G00来指令运动坐标快速定位。表3-2为FANUC-0TD系统的准备功能G代码表。
10.刀具偏置功能 (G40/G41/G42)
1. 格式 G41 X_ Z_;G42 X_ Z_;
在刀具刃是尖利时,切削进程按照程序指定的形状执行不会发生问题。不过,真实的刀具刃是由圆弧构成的 (刀尖半径) 就像上图所示,在圆弧插补和攻螺纹的情况下刀尖半径会带来误差。
2. 偏置功能
1、非直线切削形式的定位 我们的定义是:采用独立的快速移动速率来决定每一个轴的位置。刀具路径不是直线,根据到达的顺序,机器轴依次停止在命令指定的位置。
数控编程全

第三节 刀具补偿功能
31
第三节 刀具补偿功能
1.刀具补偿指令 G41——刀具半径左补偿 G42——刀具半径右补偿 G40——刀具半径补偿取消 格式: G41/G42/G40 G00/G01 D_ X(U)_ Z(W)_ (F_)
32
第三节 刀具补偿功能
2.刀尖圆弧半径对加工的影响
33
第三节 刀具补偿功能
40
第四节 车削固定循环
3.4.1 单一形状的固定循环 1.内外直径的切削循环(G90) 直线切削循环: G90 X(U)___Z(W)___F___ ;
41
第四节 车削固定循环
2.锥体切削循环: G90 X(U)___Z(W)___R___ F___ ; 必须指定锥体的 “R” 值。切削功能的用法与直线切削循环 类似 。
数控编程知识简介
➢ 数控编程定义
根据被加工零件的图纸和技术要求、工艺要求 等切削加工的必要信息,按数控系统所规定的指令 和格式编制成加工程序文件。
➢ 常用编程方法
手工编程 自动编程(图形交互式)
1
手工编程
利用一般的计算工具,通过各种数学方法,人 工进行刀具轨迹的运算,并进行指令编制。
这种方式比较简单,很容易掌握,适应性较大。 适用于中等复杂程度程序、计算量不大的零件编程, 对机床操作人员来讲必须掌握。
T0101 G00 X50. Z2.
程序主体
…… G00 X100 Z100
程序结束指令
M30
程序结束符
%
11
基础
1.2 程序指令字 1. 顺序字 N 1)作用 (1)对程序的校对和检索修改; (2)可直观地检查程序; (3)条件转向的目标。
12
数控复习资料
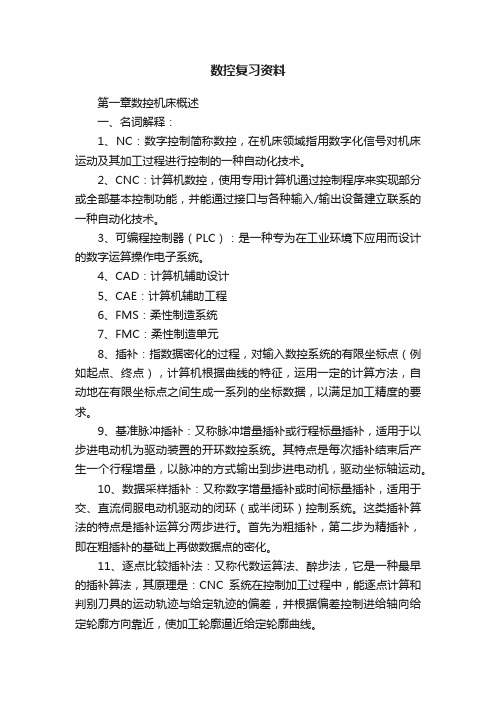
数控复习资料第一章数控机床概述一、名词解释:1、NC:数字控制简称数控,在机床领域指用数字化信号对机床运动及其加工过程进行控制的一种自动化技术。
2、CNC:计算机数控,使用专用计算机通过控制程序来实现部分或全部基本控制功能,并能通过接口与各种输入/输出设备建立联系的一种自动化技术。
3、可编程控制器(PLC):是一种专为在工业环境下应用而设计的数字运算操作电子系统。
4、CAD:计算机辅助设计5、CAE:计算机辅助工程6、FMS:柔性制造系统7、FMC:柔性制造单元8、插补:指数据密化的过程,对输入数控系统的有限坐标点(例如起点、终点),计算机根据曲线的特征,运用一定的计算方法,自动地在有限坐标点之间生成一系列的坐标数据,以满足加工精度的要求。
9、基准脉冲插补:又称脉冲增量插补或行程标量插补,适用于以步进电动机为驱动装置的开环数控系统。
其特点是每次插补结束后产生一个行程增量,以脉冲的方式输出到步进电动机,驱动坐标轴运动。
10、数据采样插补:又称数字增量插补或时间标量插补,适用于交、直流伺服电动机驱动的闭环(或半闭环)控制系统。
这类插补算法的特点是插补运算分两步进行。
首先为粗插补,第二步为精插补,即在粗插补的基础上再做数据点的密化。
11、逐点比较插补法:又称代数运算法、醉步法,它是一种最早的插补算法,其原理是:CNC系统在控制加工过程中,能逐点计算和判别刀具的运动轨迹与给定轨迹的偏差,并根据偏差控制进给轴向给定轮廓方向靠近,使加工轮廓逼近给定轮廓曲线。
二、选择填空1、数控机床主要由机床本体、数控系统、驱动装置、辅助装置等几个部分组成。
2、数控系统是数控机床的控制核心。
3、机床数控系统是由加工指令程序、计算机控制装置、可编程逻辑控制器、主轴进给驱动装置、速度控制单元及位置检测装置等组成,其核心部分是计算机控制装置。
4、计算机控制装置由硬件和软件两部分组成。
硬件的主体是计算机,包括中央处理器、输入/输出部分和位置控制部分。
数控外圆磨床编程实例
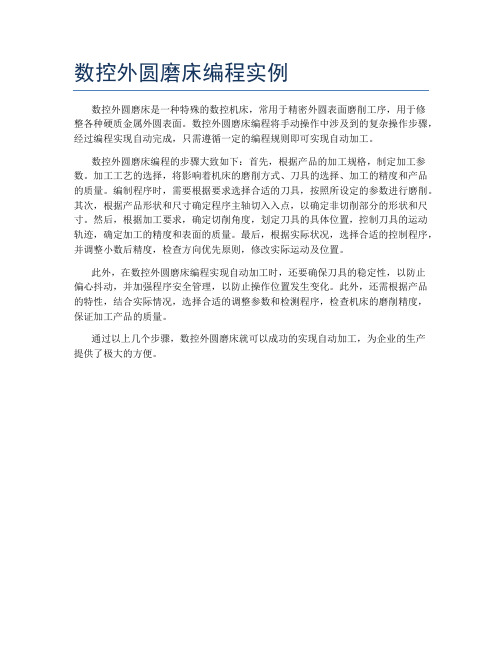
数控外圆磨床编程实例
数控外圆磨床是一种特殊的数控机床,常用于精密外圆表面磨削工序,用于修
整各种硬质金属外圆表面。
数控外圆磨床编程将手动操作中涉及到的复杂操作步骤,经过编程实现自动完成,只需遵循一定的编程规则即可实现自动加工。
数控外圆磨床编程的步骤大致如下:首先,根据产品的加工规格,制定加工参数。
加工工艺的选择,将影响着机床的磨削方式、刀具的选择、加工的精度和产品的质量。
编制程序时,需要根据要求选择合适的刀具,按照所设定的参数进行磨削。
其次,根据产品形状和尺寸确定程序主轴切入入点,以确定非切削部分的形状和尺寸。
然后,根据加工要求,确定切削角度,划定刀具的具体位置,控制刀具的运动轨迹,确定加工的精度和表面的质量。
最后,根据实际状况,选择合适的控制程序,并调整小数后精度,检查方向优先原则,修改实际运动及位置。
此外,在数控外圆磨床编程实现自动加工时,还要确保刀具的稳定性,以防止
偏心抖动,并加强程序安全管理,以防止操作位置发生变化。
此外,还需根据产品的特性,结合实际情况,选择合适的调整参数和检测程序,检查机床的磨削精度,保证加工产品的质量。
通过以上几个步骤,数控外圆磨床就可以成功的实现自动加工,为企业的生产
提供了极大的方便。
数控机床技术(第六章数控机床的进给传动系统)
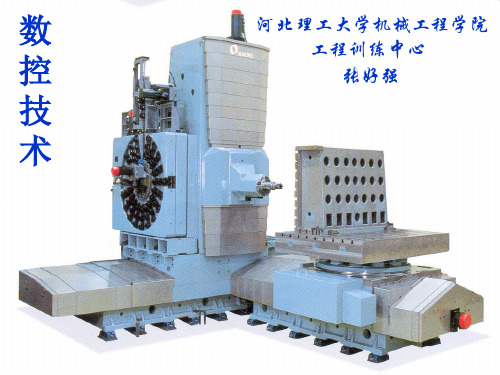
第六章 数控机床的进给传动系统
(2)滚珠丝杠副的特点 1)传动效率高。滚珠丝杠副的传动效率高达92 %-96%,是普通梯形丝杠的3-4倍,功率消耗减少 2/3-3/4。 2)灵敏度高、传动平稳。 3)定位精度高、传动刚度高。 4)不能自锁、有可逆性。 5)制造成本高。
第六章 数控机床的进给传动系统
第六章 数控机床的进给传动系统
下图所示是静压丝杠副的结构图。
第六章 数控机床的进给传动系统
螺纹面上油腔的连 接形式与节流控制方 式有两种,如图所示。 图 a 中每扣螺纹每侧 中径上开 3-4 个油腔, 每个油腔用一个节流 器控制,称为分散阻 尼节流。图 b 是将分 布于同侧、同方位上 的 3-4 个油腔用一个 节流器控制,称为集 中 阻 尼 节 流 。
第六章 数控机床的进给传动系统
一、滚珠丝杠副
中小型数控机床中,滚珠丝杠副是减少运动部件摩擦 阻力和动静摩擦力之差最普遍采用的结构。
1.滚珠丝杠副工作原理及特点 (1)滚珠丝杠副的工 作原理
滚珠丝杠副是回转 运动与直线运动相互转 换的新型传动装置,是 在丝杠和螺母之间以滚 珠为滚动体的螺旋传动 元件。
在开环、半闭环进给系统中,传动部件的间隙直接影 响进给系统的定位精度,在闭环系统中,它是系统的主要 非线性环节,影响系统的稳定性。常用的消除传动部件间 隙的措施是对齿轮副、丝杠副、联轴器、蜗轮蜗杆副以及 支承部件进行预紧或消除间隙。但是,值得注意的是,采 取这些措施后可能会增加摩擦阻力及降低机械部件的使用 寿命,因此必须综合考虑各种因统
四、双齿轮—齿条副 在大型数控机床(如大型数控龙门铣床)的直 线进给运动中,可采用的另一种传动方式是齿轮— 齿条结构,它的效率高,结构简单,从动件易于获 得高的移动速度和长行程,适合在工作台行程长的 大型机床上用作直线运动机构。但机构的位移精度 和运动平稳性较差。 当负载小时,可采用双片薄齿轮错齿调整法, 分别与齿条齿槽左、右两侧贴紧,从而消除齿侧间 隙。当负载大时,采用顶加负载双齿轮—齿条无间 隙传动机构能较好地解决这个问题。
- 1、下载文档前请自行甄别文档内容的完整性,平台不提供额外的编辑、内容补充、找答案等附加服务。
- 2、"仅部分预览"的文档,不可在线预览部分如存在完整性等问题,可反馈申请退款(可完整预览的文档不适用该条件!)。
- 3、如文档侵犯您的权益,请联系客服反馈,我们会尽快为您处理(人工客服工作时间:9:00-18:30)。
第六章 数控磨床编程
【例6-4】编写图零件的程序。
端面轴的直径和半径尺寸
第六章 数控磨床编程
四、用接触式测量头测量 MEAS, MEAW
编程格式: MEAS=1 G1 X__ Z__ F__ ;测量头上升沿时测量;取消 剩余行程 MEAS=-1 G1 X__ Z__ F__ ;测量头下降沿时测量;取消 剩余行程 MEAW=1 G1 X__ Z__ F__ ;测量头上升沿时测量;不取 消剩余行程 MEAW=-1 G1 X__ Z__ F__ ;测量头下降沿时测量;不 取消剩余行程
(2)刀具类型 刀具类型确定需要哪些 几何数据以及如何计算这 些数据(砂轮类型)。 (3)刀沿位置 对于修整器,还需另外 说明刀沿位置。图给出了 各个刀具类型所需的刀具 参数的信息。
刀具类型(磨削)
第六章 数控磨床编程
【例6-3】砂轮应具有图中展示的轮廓。使用MIRROR 和G41 由左向右进行修整。注意砂轮数据中的工件零点(XWP)必须 为110,这样才能在工件坐标系中编程轮廓。
轮廓修整举例
第六章 数控磨床编程
三、半径-直径尺寸: DIAMOF, DIAMON, DIAM90
编程格式: DIAMOF ;半径尺寸 DIAMON ;直径尺寸 DIAM90 ;G90 时为直径尺寸,G91 时为半径尺寸 注意:可编程的偏移 TRANS X__ 或者 ATRANS X__ 始终 为半径尺寸。
如图所示。 当在去程中接到跳段信号,如图a所示,在执行完W运动后,
B段进给不再执行,返回到Z轴的起始点位置结束。 当在返程中接到跳段信号,如图b所示,返回到Z轴起始点
位置结束。
在W运动时输入跳段信号
第六章 数控磨床编程
2)在A和B运动时切削立即结束并返回到循环开始时的Z坐标 ,如图所示。
当在A段运动时接到跳段信号,如图a所示,则立即终止运 动。
4)如果在一个程序段中仅编程了第 3 轴或者第 4 轴,则该 轴以有效的进给率 F 按 G1运行。若该轴为回转轴,F 的单位 在 G94 时相应为º/min,G95 时主轴的 F 单位为º/r。
5)对于该轴可以设置可设定的偏移 (G95~G59) 和可编程的 偏移 (TRANS, ATRANS) 。
当在B段运动时接到跳段信号,如图b所示,则立即停止B段 运动,返回到Z轴起始点位置结束。
在A和B运动时输入跳段信号
第六章 数控磨床编程
3)在暂停期间在暂停期间跳段信号有效,则立即结束暂停, 并返回到循环开始时的Z坐标,如图所示。
当在A段终点的暂停期间接到跳段信号,如图a所示,则立即 终止暂停并结束。
第六章 数控磨床编程
说明: 1)该功能在 SIEMENS 802D sl plus 和 pro可供使用。 2)MEAW 时: 测量头在触发后也会运行至编程的位置。 存 在损坏危险。 3)测量任务状态:如果已接通测量头,则将测量程序段后 的变量 $AC_MEA[1] 的值设为1;否则设为0。测量程序段开 始时,设置该变量值为0。 4)测量结果:在成功接通测量头后,测量结果包含了测量 程序段后的下列变量,供测量程序段中运行的轴使用: 在机床坐标系中: $AA_MM[Achse] 在工件坐标系中: $AA_MW[轴];轴为 X 轴或者 Z 轴。
第六章 数控磨床编程
第一节 FANUC系统数控磨床的编程 第二节 SIEMENS系统数控磨床基本指令 第三节 SIEMENS系统数控磨床固定循环
第六章 数控磨床编程
第二节 SIEMENS系统数控磨床基本指令
一、概述
SIEMENS 802D系统数控磨床的指令与SIEMENS 802D系统 数控车床与数控铣床类似,表6-1是与其他机床不同的指令表
根据经验和实测,在修整计数器中设一数值,每磨削一个零 件,M98指令使计数器减1,当计数器的值变为0时,若再启动 程序,便调用砂轮修整程序。
该程序的运动指令为砂轮运动,金刚笔不动,执行程序后, 砂轮被修成要求形状,如图所示。
修砂轮示意图
第六章 数控磨床编程
三、编程实例
【例6-1】零件如图所示,端面与外圆均需磨削,外圆磨削 余量为0.3mm,端面为0.08mm。
Y15.0;
G00 G90 Z10.0;
M05;
M30;
第六章 数控磨床编程
2.连续进给平面磨削循环(G78)
(1)指令格式:G78 I J K X F P L ; (2)G78的运行方式如图所示。
连续进给平面磨削循环 ①暂停,②磨削,③暂停,④磨削
第六章 数控磨床编程
3.间断进给平面磨削循环(G79)
修整器 1 (D7) 左砂轮边缘 修整器 2 (D8) 右砂轮边缘 修整器 3 (D9) 用于直径以及不能使用修整器 1 或者 2 时的 可选项。
1.编程格式
D__ ;刀补号 1~9, D0表示刀具补偿无效
第六章 数控磨床编程
2.说明
在刀具管理中通过输入来确定 T/D 数组刀具补偿的固定含义。 在此列出了参数表。一旦刀具有效,刀具长度补偿立即生效;如 果没有编写任何 D 号,则 D1 自动生效。最先编程的相关长度补 偿轴运行时,补偿开始。而刀具半径补偿必须另外通过 G41/G42 开启。
第六章 数控磨床编程
第一节 FANUC系统数控磨床的编程 第二节 SIEMENS系统数控磨床基本指令 第三节 SIEMENS系统数控磨床固定循环
第六章 数控磨床编程
第一节 FANUC系统数磨床的编程
一、平面磨床的编程
1.切入磨削循环(G75)及带量仪的切入磨削循环(G77)
(1)指令格式: G75/G77 I J K X/Z R F P L ; I:首次切深,方向由正负号决定; J:第二次切深,方向由正负号决定; K:总切削深度; X(Z):磨削范围,方向由正负号决定; R:I和J的进给速度; F:X(Z)的进给速度。 P:暂停时间; L:砂轮磨损补偿号。
二、刀具补偿号 D(磨削)
可以向某个特定刀具分配带不同刀具补偿程序段(用于多个 刀沿)的 1 到 9 个数组。如果需要特殊刀沿,可以编程 D 和相 应的编号。
刀沿 1、3、5 表示左边砂轮,刀沿2、4、6 表示用于标准轮 廓的右砂轮。
第六章 数控磨床编程
刀沿 7 到 9为一个砂轮的三个修整器。 它们固定分配在砂 轮的各个区域。
2)如果机床做相应的设计,则第 3 轴或者第 4 轴可以同时 与其他轴直线运行。
第六章 数控磨床编程
3)如果在一个程序段中用 G1 或 G2/G3 使轴与其他轴 (X,Z) 一起运行,则其不含有进给率 F的分量。其速度取决于 X,Z 轴的轨迹时间。其运动与其他轨迹轴一起开始并结束。速度不 能大于规定的极限值。
3.补偿存储器的内容
(1)几何尺寸 长度、半径;它们由几个部分组成(几何尺寸,磨损尺寸); 控制系统从这些部分计算出最后的尺寸(比如总长度 1,总半 径);各个总尺寸在激活补偿存储器时生效;如何计算出坐标轴 中的值,由刀具类型和当前平面G17,G18,G19(图6-15)来决 定。
第六章 数控磨床编程
磨削的步骤
第六章 数控磨床编程
例:磨削如图所示平面:
O0001;
G54 G90 M03 S4000;
G00 Z2.0;
X-60.0 Y-15.0;
G01 Z0.0 F20;
G75 I-0.1 J-0.1 K-0.5 X120.0
R20 F2000 P500 L01; G01 Y0.0;
平面的磨削
G75 I-0.1 J-0.1 K-0.5 X120.0 R20 F2000 P500 L01;
指令格式: G72 P A_ B_ W_ U_ I_ K_ H_ ; 式中P:量仪号(1~4)。 如果选择了多级跳段功能,可以规定量仪号。量仪号的规 定方法与多级跳段相同。如果不选择多级跳段功能,则普通 跳段信号有效。其他指令与G71相同。
第六章 数控磨床编程
在跳段信号输入时的运动: 1)在W运动时在W移动结束后,返回到循环开始时的Z坐标,
第六章 数控磨床编程
摆动磨削循环G73
在单程序段的情况下,用一次循环起动完成1,2,3和4的 运行。 除B以外,A,W,U和K均为模态值。
第六章 数控磨床编程
4.带量仪的摆动磨削循环(G74)
指令格式:G74 P__A__(B__)W__U__K__H__; 其中,P:量仪号(1~4)。 如果选择了多级跳段功能,可以规定量仪号。量仪号的规 定方法与多级跳段相同。如果不选择多级跳段功能,则普通跳 段信号有效。
磨削加工图
第六章 数控磨床编程
【例6-2】加工如图所示零件,图中所示的是在数控外圆 磨床上加工的一个较典型的零件。该零件要磨削圆柱面,
φ10h5,圆锥面 1:8,和圆弧面,R2.5,各处单边磨削余
量0.1mm。
零件加工图
第六章 数控磨床编程
(1)加工工艺的制订
由零件图样可以看出零件外圆φ10h5(0-0、006)和锥面粗糙 度Ra0.2μm ,以及同轴度φ0.005mm是磨削加工的重点。因为零
当在B段终点的暂停期间接到跳段信号,如图b所示,则立即 终止暂停,返回到Z轴起始点位置结束。
在暂停期间输入跳段信号
第六章 数控磨床编程
3.摆动磨削循环(G73)
指令格式:G73 A__(B__)W__U__K__H__; A:切削深度; B:切削深度,B指令仅在规定的程序段中有效,它不作为 模态信息保存,可以不指令,与G71和G72中的B不同; W:磨削范围; U:暂停时间; K:进给速度; H:重复次数,设置范围为1~9999次。 A,B和W指令都是增量值。
4.编程举例(略)
第六章 数控磨床编程
5.回转轴的特殊指令 DC, ACP, CAN
例如:回转轴 A A=DC(____) ;绝对尺寸说明,直接回位(最短距离) A=ACP(____) ;绝对尺寸说明,从正方向运行至某位置 A=ACN(____) ;绝对尺寸说明,从负方向运行至某位置