步进式加热炉
步进梁式加热炉
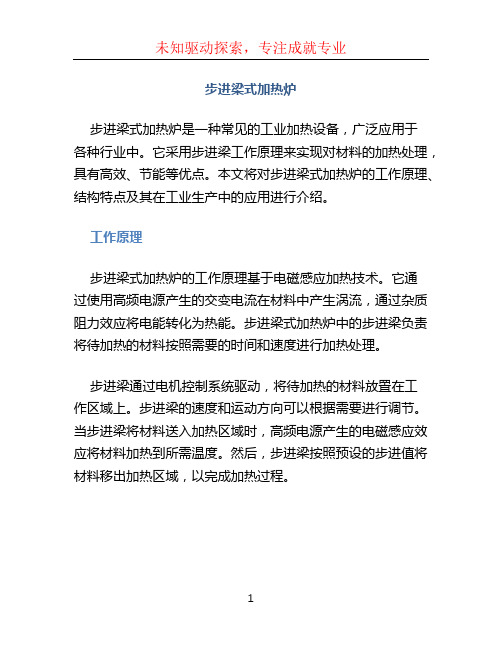
步进梁式加热炉步进梁式加热炉是一种常见的工业加热设备,广泛应用于各种行业中。
它采用步进梁工作原理来实现对材料的加热处理,具有高效、节能等优点。
本文将对步进梁式加热炉的工作原理、结构特点及其在工业生产中的应用进行介绍。
工作原理步进梁式加热炉的工作原理基于电磁感应加热技术。
它通过使用高频电源产生的交变电流在材料中产生涡流,通过杂质阻力效应将电能转化为热能。
步进梁式加热炉中的步进梁负责将待加热的材料按照需要的时间和速度进行加热处理。
步进梁通过电机控制系统驱动,将待加热的材料放置在工作区域上。
步进梁的速度和运动方向可以根据需要进行调节。
当步进梁将材料送入加热区域时,高频电源产生的电磁感应效应将材料加热到所需温度。
然后,步进梁按照预设的步进值将材料移出加热区域,以完成加热过程。
结构特点步进梁式加热炉的主要结构部件包括加热腔体、步进梁、电机控制系统和高频电源。
•加热腔体:加热腔体通常由耐高温材料制成,具有良好的隔热性能和耐腐蚀性能。
加热腔体内部通常配备了加热元件,如电磁感应线圈或加热电阻。
•步进梁:步进梁是步进梁式加热炉的核心部件,它通常由导轨、传动机构和工作台组成。
导轨负责引导步进梁的运动,传动机构则用于驱动步进梁的移动,工作台用于放置待加热的材料。
•电机控制系统:电机控制系统负责驱动步进梁的运动。
它通常由电机、传感器和控制器组成。
传感器用于检测步进梁的位置,控制器则根据传感器的反馈信号来控制电机的运转。
•高频电源:高频电源是步进梁式加热炉实现电磁感应加热的关键部件。
高频电源通常由变压器、电容器和整流器等组成,能够产生高频交流电供给加热线圈。
应用场景步进梁式加热炉在工业生产中有着广泛的应用场景。
1.金属加热处理:步进梁式加热炉可以对金属材料进行淬火、退火、正火、时效等热处理工艺,以改善金属材料的综合性能。
2.塑料热处理:步进梁式加热炉可以对塑料材料进行加热软化、烘干、热合等工艺,以满足塑料制品的成型需求。
步进式加热炉
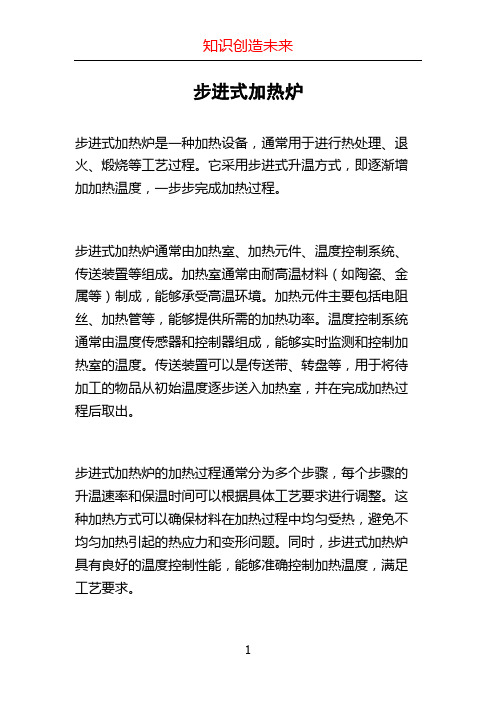
步进式加热炉
步进式加热炉是一种加热设备,通常用于进行热处理、退火、煅烧等工艺过程。
它采用步进式升温方式,即逐渐增加加热温度,一步步完成加热过程。
步进式加热炉通常由加热室、加热元件、温度控制系统、传送装置等组成。
加热室通常由耐高温材料(如陶瓷、金属等)制成,能够承受高温环境。
加热元件主要包括电阻丝、加热管等,能够提供所需的加热功率。
温度控制系统通常由温度传感器和控制器组成,能够实时监测和控制加热室的温度。
传送装置可以是传送带、转盘等,用于将待加工的物品从初始温度逐步送入加热室,并在完成加热过程后取出。
步进式加热炉的加热过程通常分为多个步骤,每个步骤的升温速率和保温时间可以根据具体工艺要求进行调整。
这种加热方式可以确保材料在加热过程中均匀受热,避免不均匀加热引起的热应力和变形问题。
同时,步进式加热炉具有良好的温度控制性能,能够准确控制加热温度,满足工艺要求。
总之,步进式加热炉是一种常用的加热设备,可用于多种热处理工艺,具有均匀加热、温度控制精度高等特点。
7种提高步进式加热炉节能技术的应用方案

1、步进式加热炉节能技术1.1加热炉采用空气蓄热和煤气换热综合燃烧技术,煤气经过麻花插件管式换热器预热,煤气预热温度350℃空气采用蓄热式燃烧技术,把20℃的助燃空气预热到850〜900高温,达到烟气余热的极限回收,提高燃烧介质物理热,从而降低燃料消耗,提高加热炉热效率30%,是节能、环保的新技术。
采用蓄热式燃烧技术,炉内火焰流动与传统加热炉比有很大的区别,废气横向流动,烧嘴成对工作,烧嘴布置于加热炉两侧,其中一侧烧嘴工作时另一侧烧嘴排烟蓄热。
(轧钢之家ID:zhagangzhijia)一侧烧嘴喷出的火焰被对侧烧嘴吸引,这相当于加长了火焰长度,因此加热炉宽度方向的温度较传统加热炉均匀。
采用蓄热式燃烧技术后,加热温度均匀,钢坯加热质量好,不发生粘炉事故煤气、空气蓄热后,采用低氧扩散燃烧技术,形成与传统火焰迥然不同的新型火焰型,炉内燃烧气氛较好,钢坯升温较快,钢坯氧化烧损可减少0.3%〜0.5%。
1.2棒材厂型钢车间加热炉采用空气单蓄热上下组合式烧嘴,共计52个单蓄热烧嘴单蓄热组合式烧嘴,每段烧嘴可以单独调节,蓄热式烧嘴成对工作,二者交替变换燃烧和排烟工作状态,烧嘴内的蓄热体相应变换放热和吸热状态成对的烧嘴分设于炉膛的A侧和B侧,当A侧烧嘴燃烧时,空气流经积蓄了热量的蓄热体而被加热,与此同时,B侧烧嘴排烟,烟气热量被蓄热体吸收进行蓄热如此周而复始,通过蓄热体这一媒介,出炉烟气的余热被转换成空气的物理热,而得到回收利用,见图1蓄热式烧嘴的空气喷口和煤气喷口为上下组合,烧嘴安装在炉膛上部时,空气喷口在上,煤气喷口在下,空、煤气流上下斜交混合,烧嘴安装在炉膛下部时则反之,是煤气喷口在上,空气喷口在下,也就是靠近坯料上表面和下表面的都是煤气流。
(轧钢之家ID:zhagangzhijia)空、煤气混合燃烧有一个短暂的过程,在这个过程中,与坯料表面接触的气氛是还原性或微还原性的,坯料氧化较缓慢,氧化烧损减少0.45%,这是组合式蓄热式烧嘴的明显特性。
步进式加热炉设计计算

二 步进式加热炉设计计算2.1 热工计算原始数据(1)炉子生产率:p=245t/h (2)被加热金属:1)种类:优质碳素结构钢(20#钢) 2)尺寸:250×2200×3600 (mm)(板坯) 3)金属开始加热(入炉)温度:t 始=20℃4)金属加热终了(出炉)表面温度:t 终=1200℃ 5)金属加热终了(出炉)断面温差:t ≤15℃ (3)燃料1)种类:焦炉煤气2)焦炉煤气低发热值:Q 低温=17000kJ/标m 33)煤气不预热:t 煤气=20℃表1-1 焦炉煤气干成分(%)废膛(5)空气预热温度(烧嘴前):t 空=350℃2.2 热工计算2.2.1 焦炉煤气干湿成分换算查燃料燃烧附表5,3/9.18m g g =10000124.0100124.0222⨯+=干干湿OHOHg g O H100100%%2湿干湿O H X X -⨯=由上式得 %2899.22=湿O H000025741.561002899.21009.57%H =-⨯=湿000048184.241002899.21004.25%CH =-⨯=湿00007939.81002899.21009%CO =-=湿0000428336.21002899.21009.2%H C =-⨯=湿000022702.11002899.21003.1%N =-⨯=湿000023909.01002899.21004.0%O =-⨯=湿000020290.31002899.21001.3%CO =-⨯=湿代入表2—1中,得表2-1 焦炉煤气湿成分(%)2.2.2 计算焦炉煤气低发热值)(低 +⨯+⨯+⨯+⨯⨯=424214100%8550%2580%3046187.4H C CH H CO Q=()0000008336.2141008184.2485505741.5625807939.83046187.4⨯+⨯+⨯+⨯⨯=17094.6830 KJ/m ³误差%557.0%10017000170006830.17094%=⨯-=计算值与设计值相差很小,可忽略不计。
步进式加热炉

∙步进式加热炉∙∙步进式加热炉是机械化炉底加热炉中使用较为广泛的一种,是取代推钢式加热炉的主要炉型。
70年代以来,国内外新建的许多大型加热炉大都采用了步进式加热炉,不少中小型加热炉也常采用这种炉型。
步进式加热炉的炉底基本由活动部分和固定部分构成。
按其构造不同又有步进梁式、步进底式和步进梁、底组合式加热炉之分。
一般坯料断面大于(120×120)mm2多采用步进梁式加热炉,钢坯断面小于(100×100)mm2多采用步进底式加热炉。
与推钢式加热炉相比,步进式加热炉有下列优点:1)加热的坯料不受断面形状和尺寸的限制,可以加热推钢式加热炉难以加热的大型板坯、异形坯以及细小和较薄的钢坯。
2)加热制度灵活,适应性较大。
在炉长一定的情况下,可以通过改变钢料之间的距离即可改变炉内装料的数目,以适应轧机产量和钢种变化的需要。
而调整步进周期,即可变化钢料在炉内的加热时间,从而适应不同钢种不同加热速度的需要。
∙∙步进式加热炉产品特点本公司步进式加热炉的优点:1.炉形:分为预热段、加热段和均热段三段连续式。
具有生产效率高、控温精确、工艺适用面广、高效节能等特点。
2.炉衬:选用我公司自产的耐火材料,寿命长,结实耐用。
3.供热方式:炉子供热制度两侧墙多点、小火供热,炉压稳定;炉温均匀:根据不同的状况可选用单蓄热或双蓄热等节能加热方式。
4.能耗: 1.1~1.2GJ/t5.产量: 30t/h~220t/h6.炉底水管冷却方式:水冷或汽化冷却7.二、三级自动控件系统∙步进式加热炉∙∙步进式加热炉步进式加热炉是机械化炉底加热炉中使用较为广泛的一种,是取代推钢式加热炉的主要炉型。
70年代以来,国内外新建的许多大型加热炉大都采用了步进式加热炉,不少中小型加热炉也常采用这种炉型。
步进式加热炉的炉底基本由活动部分和固定部分构成。
按其构造不同又有步进梁式、步进底式和步进梁、底组合式加热炉之分。
一般坯料断面大于(120×120)mm2多采用步进梁式加热炉,钢坯断面小于(100×100)mm2多采用步进底式加热炉。
步进式加热炉施工工法

步进式加热炉施工工法中冶集团华冶资源天津工业设备安装分公司沈洪斌1、前言天钢双棒材2#加热炉工程是和引进意大利达涅利公司棒材生产线的配套工程,该加热炉采用了国内外最新流行的、先进的蓄热式、步进加热炉。
是天钢建厂以来最先进的加热炉,同样也是我公司接手的第一台步进蓄热式加热炉。
为了干好这一工程我单位专门成立了技术攻关小组。
在施工过程中根据工程特点采用了炉墙结构整体分段安装及炉底机械现场拼装的施工工艺。
2、工法的特点:2.1合理布置测量控制网,定期进行沉降观测,采用高精度测量仪器测量进行针对性的测量保证关键设备的安装精度。
2.2炉底机械现场根据斜轨底座安装情况及现场实际加热炉中心线进行拼装,比传统的线外拼装好后再进行安装。
不但解决了吊装过程中的变形问题更主要的是提高了安装的针对性及精度。
2.3炉墙结构分段整体安装比先安装梁、柱再安装炉皮的散件安装方法,不但提高了结构安装精度而且提高了炉壳的平整度和炉壳开孔精度。
整体结构可以在安装现场进行拼装这样可以充分利用厂房内的天车,提高安装效率(减少了高空作业工作量提高了安装效率)及减少机械台班的使用。
3、适用范围:本工法适用于各种步进式加热炉的安装,包括炉底机械、炉体结构的安装。
4、工艺原理:4.1炉底机械现场拼装工艺,该工艺的操作要点是依据安装好的斜轨底座做拼装平台,将炉底机械(提升框架及平移框架)分段吊装固定在斜轨底座上,然后根据加热炉的实际纵横向中心线来确定炉底机械的纵横向中心线,进行现场拼装。
4.2炉墙结构分段整体安装安装工艺,该工艺的操作要点是先在安装现场搭设一个拼装平台,然后在平台上将炉墙结构的梁、柱及炉皮在现场利用厂房内天车进行分段拼装,分段的大小根据厂方内天车能够吊装为依据。
这种先拼装后整体安装的工艺不仅提高了安装质量而且提高了安装效率及节约了生产成本。
5、施工工艺流程及操作要点5.1加热炉的安装调整工艺流程:基础验收及放线炉底斜轨及机械安装水平、平移框架安装水封槽安装炉底立柱安装5.2基准点的埋设炉子安装必须设置三条基准线,即炉子中心、进料辊道中心线、出料辊道中心线,并埋炉底结构安装炉底冷却水管炉墙结构及平台安装炉墙砌筑及水梁浇涛悬臂辊道安装水梁系统安装炉顶结构安装炉底砌筑烧嘴及推齐钢机安装炉顶砌筑炉顶平台安装液压、润滑管道打压试验炉顶保温浇涛设备单机试运水梁打压试验煤气管道安装风道安装烟道安装水冷系统水压试验液压、润滑管道设备安装液压、润滑管道在线酸洗液压、润滑管道在线油冲洗液压、润滑管道在线滤油无负荷联动试运转设固定中心标板,这三条线是一切尺寸的基准,炉子安装时应层层安装、层层校验。
步进梁式加热炉炉压问题分析及处理方法

步进梁式加热炉炉压问题分析及处理方法摘要:加热炉作为钢铁工业轧钢生产线的关键设备和能耗设备,其自动化控制水平直接影响到能耗、烧损率、废钢率、产量、质量等指标。
关键词:步进梁式;加热炉;关键技术1加热炉发展和现状现代化的高产量热轧带钢轧机,由于对轧制带钢的厚度、尺寸、公差带、钢表面质量和板型控制的要求日益严格,因而对板坯加热温度均匀性和热板坯表面的质量要求也不断提高。
加热炉是热轧带钢轧机必须配备的加热设备,随着工业自动化技术的不断发展,现代化的热连轧机应该配置大型化的高度自动化的步进梁式加热炉,其生产应符合高产优质低耗节能、无公害以及生产操作自动化的工艺要求,以提高其产品的质量,增强产品的市场竞争力。
我国轧钢工业的加热炉型有推钢式炉和步进式炉两种,但推钢式炉有长度短产量低烧损大,操作不当时会粘钢造成生产上的问题,钢坯断面温差较大,板坯背面滑轨擦痕多难以实现管理自动化。
由于推钢式炉有难以克服的缺点,而步进梁式炉是靠专用的步进机构在炉内做矩形运动来移送板坯,可以留出空隙,板坯和步进梁之间没有摩擦,通过托出装置出炉完全消除了滑轨擦痕,又有适合加热断面较大的坯料钢坯,加热断面温差小、加热均匀,以及可出空炉料炉长不受限制、产量高、生产操作灵活等特点,其生产符合高产优质、低耗节能、无公害以及生产操作自动化的工艺要求。
2步进式加热炉工艺流程步进式加热炉炉型为三段供热端进端出步进梁加热炉。
加热炉自装料端至出料端沿炉长上分为预热段、加热一段、加热二段及均热段。
为了便于灵活调节各段炉温,在加热二段与均热段之间设有无水冷隔墙。
用无水冷隔墙隔开,可以精确控制两段炉温和炉压,减少两段之间的辐射干扰。
各段均为上下加热,采用分布在炉子侧墙上的烧嘴进行供热。
通过每对烧嘴的切换燃烧,加强了炉气在炉内的扰动,增强了炉气对钢坯的传热。
空气预热温度600℃以上,排烟温度250℃以下。
加热工艺的操作包括正常生产时的加热温度、加热速度、加热时间等工艺参数的控制,以及对炉内气氛和炉压控制等项。
步进式加热炉课程设计
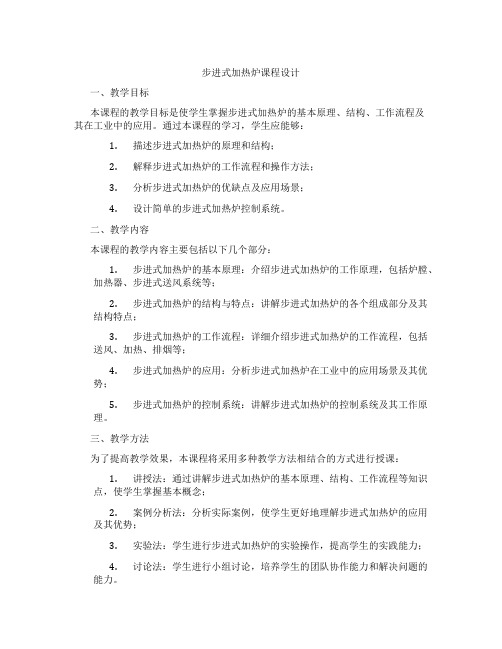
步进式加热炉课程设计一、教学目标本课程的教学目标是使学生掌握步进式加热炉的基本原理、结构、工作流程及其在工业中的应用。
通过本课程的学习,学生应能够:1.描述步进式加热炉的原理和结构;2.解释步进式加热炉的工作流程和操作方法;3.分析步进式加热炉的优缺点及应用场景;4.设计简单的步进式加热炉控制系统。
二、教学内容本课程的教学内容主要包括以下几个部分:1.步进式加热炉的基本原理:介绍步进式加热炉的工作原理,包括炉膛、加热器、步进式送风系统等;2.步进式加热炉的结构与特点:讲解步进式加热炉的各个组成部分及其结构特点;3.步进式加热炉的工作流程:详细介绍步进式加热炉的工作流程,包括送风、加热、排烟等;4.步进式加热炉的应用:分析步进式加热炉在工业中的应用场景及其优势;5.步进式加热炉的控制系统:讲解步进式加热炉的控制系统及其工作原理。
三、教学方法为了提高教学效果,本课程将采用多种教学方法相结合的方式进行授课:1.讲授法:通过讲解步进式加热炉的基本原理、结构、工作流程等知识点,使学生掌握基本概念;2.案例分析法:分析实际案例,使学生更好地理解步进式加热炉的应用及其优势;3.实验法:学生进行步进式加热炉的实验操作,提高学生的实践能力;4.讨论法:学生进行小组讨论,培养学生的团队协作能力和解决问题的能力。
四、教学资源为了支持本课程的教学,我们将准备以下教学资源:1.教材:选用权威、实用的教材,为学生提供系统的学习资料;2.参考书:提供相关的参考书籍,丰富学生的知识体系;3.多媒体资料:制作精美的PPT、视频等多媒体资料,提高学生的学习兴趣;4.实验设备:准备步进式加热炉实验设备,为学生提供实践操作的机会。
五、教学评估本课程的教学评估将采用多元化的评估方式,以全面、客观地评价学生的学习成果。
评估方式包括:1.平时表现:通过课堂参与、提问、小组讨论等环节,评估学生的学习态度和课堂表现;2.作业:布置相关的作业,评估学生的理解和应用能力;3.考试:安排期中和期末考试,评估学生对课程知识的掌握程度;4.实验报告:评估学生在实验过程中的操作技能和问题解决能力。
- 1、下载文档前请自行甄别文档内容的完整性,平台不提供额外的编辑、内容补充、找答案等附加服务。
- 2、"仅部分预览"的文档,不可在线预览部分如存在完整性等问题,可反馈申请退款(可完整预览的文档不适用该条件!)。
- 3、如文档侵犯您的权益,请联系客服反馈,我们会尽快为您处理(人工客服工作时间:9:00-18:30)。
步进式加热炉自动控制系统的设计2009-5-7 9:47:00 来源:作者: 网友评论 0 条 点击查看摘 要:目前,工业控制自动化技术正在向智能化、网络化和集成化方向发展。
本文通过对步进式加热炉 系统的设计,从而反映出当今自动化技术的发展方向。
同时,介绍了软件设计思想和脉冲式燃烧控制技 术原理特点及在本系统的应用。
1 引言 加热炉是轧钢工业必须配备的热处理设备。
随着工业自动化技术的不断发展,现代化的轧钢厂应该 配置大型化的、高度自动化的步进梁式加热炉,其生产应符合高产、优质、低耗、节能、无公害以及生 产操作自动化的工艺要求,以提高其产品的质量,增强产品的市场竞争力。
我国轧钢工业的加热炉型有推钢式炉和步进式炉两种,但推钢式炉有长度短、 产量低,烧损大,操作不当时会粘钢造成生产上的问题,难以实现管理自动化。
由于推钢式炉有难 以克服的缺点,而步进梁式炉是靠专用的步进机构,在炉内做矩形运动来移送钢管,钢管之间可以留出 空隙,钢管和步进梁之间没有摩擦,出炉钢管通过托出装置出炉,完全消除了滑轨擦痕,钢管加热断面 温差小、加热均匀,炉长不受限制,产量高,生产操作灵活等特点,其生产符合高产、优质、低耗、节 能、无公害以及生产操作自动化的工艺要求。
全连续、全自动化步进式加热炉。
这种生产线都具有以下特点: ①生产能耗大幅度降低。
②产量大幅度提高。
③生产自动化水平非常高,原加热炉的控制系统大多是单回路仪表和继电逻 辑控制系统,传动系统也大多是模拟量控制式的供电装置,现在的加热炉的控制 系统都是 PLC 或 DCS 系统,而且大多还具有二级过程控制系统和三级生产管理系 统。
传动系统都是全数字化的直流或交流供电装置。
本工程是某钢铁集团新建的 φ180 小口径无缝连轧钢管生产线中的热处理线部分的步进式加热炉设 备。
2 工艺描述 本系统的工艺流程图见图 1图 1 步进式加热炉工艺流程图 淬火炉和回火炉均为步进梁式加热炉。
装出料方式:侧进,侧出;炉子布料:单排。
活动梁和固定梁 均为耐热铸钢,顶面带齿形面,直径小于 141.3mm 钢管,每个齿槽内放一根钢管。
直径大于 153.7mm 的 钢管每隔一齿放一根钢管。
活动梁升程 180mm,上、下各 90mm,齿距为 190mm,步距为 145mm。
因此 每次步进时,钢管都能转动一角度,使钢管加热均匀,并防止在炉内弯曲变形。
步进梁能进行正循环, 送循环、单动、点动各种动作,升降时对钢管轻托轻放,前进时缓起缓停,无振动冲击和失控现象。
同 时,具有踏步功能,踏步时向后步距为 45mm,使钢管在原齿槽内不断转动。
固定梁用带保温支柱支撑其顶面高出炉底 520mm。
使炉气能围绕钢管形成良好的循环,保证均匀加 热。
淬火炉沿炉长方向分为装料段、加热段和保温段。
装料段炉顶压低,不装排烟予热钢管(三个测量 温度点),以免钢管突然受到强大热流冲击产生弯曲变形。
加热段沿炉宽方向分为四个区段进行比例燃烧和温度控制。
保温段沿炉宽方向分 4 区段进行脉冲燃 烧和温度控制(用二套控制器),以确保保温区炉温± 5℃和保温后钢管全长温度均匀性在 10℃以内的要 求。
同时更方便用户控制钢管端温度,满足淬火需要。
淬火炉最高控制炉温 960℃,允许 max1050℃。
回火炉沿炉长方向分为装料段,加热段,均温段和保温段。
同样装料段不设烧嘴。
加热段沿炉宽方 向分二个温区,中间 8 个烧嘴为一个温区,两边各 4 个烧嘴合起来为一温区,用一个脉冲控制器控制。
均温段、保温段沿炉宽方向各分为四区(每二个温区一个控制器),均采用脉冲燃烧温度控制。
确保炉温控制± 5℃,保温后钢管全长温度均匀性 10℃的要求。
回火炉最高控制炉温 750℃,允许 max800℃(为生产高压锅炉管作储备)。
淬火炉、回火炉炉内烟气均经装料段下方的八个分烟管引出,进入集烟管,由集烟管中部引至总烟 管,通过空气予热器回收烟气余热,再经烟道由烟囱排入大气。
这种方式可有效防止炉内烟气的偏流。
淬、回火炉进出料均采用侧进,侧出方式。
淬火炉装出料悬臂辊采用斜 80 角安装,使钢管在入炉和 出炉时产生自转并靠向装出料端墙一侧靠齐,其目的是防止钢管入炉时弯曲并有利装出料定位。
3 步进式加热炉生产中的关键控制技术3.1 生产节奏的控制 步进式加热炉生产中的生产节奏的控制是非常重要的,在管材线全自动、全连续工作时,加热炉区 的机械设备如进料辊道、步进梁、出料辊道、液压站及其它公辅设施,设备运行节奏必须高度统一,才 能实现管材物流全过程准确定位,以实现全自动、全连续工作。
依据生产调度计划而需要装炉时,通过上料台架输送至装料辊道,经光电开关及金属探测器而自动 输送到炉外辊道上。
待炉内装料端空出位置时,自动开启炉门,由其及炉内辊道托入炉内放置到固定梁 上,并由此开始进行炉内的管材物流跟踪。
管材通过炉子步进梁自装料端一步步地移送到炉子的出料端。
由装在出料端的光电开关检测到管材边缘并在步进梁完成此时的步距运行后,暂停步进梁的移送动作, PLC 同时测算等待出炉管材的位置。
在加热炉接到出钢信号后,再自动开启出料炉门,由出料辊道运至 炉外出料辊道上。
当金属检测器探测到管材时,在由出料辊道输送至其他设备,进行下一道工艺。
管材输送、测量、装出料、物流跟踪以及管材的数据信息交换通过 PLC 和二 级计算机系统进行顺序、定时、联锁与逻辑控制,实现操作自动化和计算机管理。
3.2 加热炉燃烧控制 工业炉的燃烧控制水平直接影响到生产的各项指标,例如:产品质量、能源消耗等。
目前国内的工 业炉一般都采用连续燃烧控制的形式,即通过控制燃料、助燃空气流量的大小来使炉内的温度、燃烧气 氛达到工艺要求。
由于这种连续燃烧控制的方式往往受到燃料流量的调节和测量等环节的制约,所以目 前大多数工业炉的控制效果不佳。
随着工业炉工业的迅猛发展,脉冲式燃烧控制技术也应运而生,并在 国内外得到一定程度的应用,取得了良好的使用效果。
目前高档工业产品对炉内温度场的均匀性要求较高,对燃烧气氛的稳定可控性要求较高,使用传统 的连续燃烧控制无法实现。
随着宽断面、大容量的工业炉的出现,必须采用脉冲燃烧控制技术才能控制 炉内温度场的均匀性。
本系统主要采用脉冲燃烧系统。
它是一种间断燃烧的方式,使用脉宽调制技术,通过调节燃烧时间 的占空比(通断比)实现窑炉的温度控制。
燃烧状态下的燃料流量可通过主燃料控制阀门在线调节,燃 烧器一旦燃烧,就处于其设计的最佳燃烧状态,保证燃烧器燃烧时的燃气出口速度不变。
控制系统使炉 内燃烧器交替燃烧,通过燃气在炉内的不断搅拌,使炉内温度场均匀分布。
当需要升温时,燃烧器燃烧 时间加长,间断时间减小;需要降温时,燃烧器燃烧时间减小,间断时间加长。
并根据炉内的设定温度来 控制燃烧时的燃料流量,当设定温度较低时,将主燃料控制阀门关小,当设定温度较高时,将主燃料控 制阀门开大,避免炉内处于低温状态时,燃气与炉内的温度差过大,对炉内制品造成的直接热冲击。
脉冲燃烧系统的主要优点为: 1) 系统简单可靠,造价低。
2) 可提高炉内温度场的均匀性。
3) 传热效率高,大大降低能耗。
4) 燃烧器的负荷调节比大。
5) 无需在线调整,即可实现空燃比的精确控制。
与传统的比例燃烧控制相比,脉冲燃烧控制系统中参与控制的仪表大大减少,仅有温度传感器、控 制器和执行器,省略了大量价格昂贵的流量、压力检测控制机构。
并且,由于只需两位式开关控制,执 行器也由原来的气动(电动)控制阀门变为电磁阀门,增加了系统的可靠性,大大降低了系统造价。
普通烧嘴的空燃比一般为 1:4 左右,当烧嘴在满负荷工作时,燃气流速、火焰形状、热效率均可达 到最佳状态,但当烧嘴流量接近其最小流量时,热负荷最小,燃气流速大大降低,火焰形状达不到要求, 热效率急剧下降,高速烧嘴工作在满负荷流量 50%以下时,上述各项指标距设计要求就有了较大的差距。
脉冲燃烧则不然,无论在何种情况下,烧嘴只有两种工作状态,一种是满负荷工作,另一种是不工作, 只是通过调整两种状态的时间比进行温度调节,所以采用脉冲燃烧可弥补烧嘴调节比低的缺陷,需要低 温控制时仍能保证烧嘴工作在最佳燃烧状态。
在使用高速烧嘴时,燃气喷出速度快,使周围形成负压, 将大量炉内烟气吸人主燃气内,进行充分搅拌混合,延长了烟气在炉内的滞留时间,增加了烟气与制品 的接触时间,从而提高了对流传热效率。
4 系统简介 4.1 系统构成 系统拓扑图见图 2图 2 系统拓扑图 本加热炉自动化控制系统由基础自动化系统(L1)和过程计算机控制系统(L2)共同构成。
本系统一级基础自动化控制系统由淬火炉电气传动部分、回火炉电气传动部分和淬火炉仪控部分、 回火炉仪控部分四个控制站。
淬火炉电气传动部分 PLC 为 S7 315-2DP 带 4 个 ET200M 从站和 3 个 PROFIBUS-DP 卡的西门子变频 器 MM440 系列,实现辊道的顺控,钢管在入炉辊道上的定位控制,步进梁控制的功能。
淬火炉传动系统采用变频控制,变频器是由西门子公司提供的 MM440 系列。
3 个带 PROFIBUS-DP 卡的 MM440 系列变频器控制 3 组辊道。
回火炉电气传动部分 PLC 为 S7 315-2DP 带 3 个 ET200M 从站和 2 个带 PROFIBUS-DP 卡的西门子变 频器 MM440 系列,实现辊道的顺控,钢管在入炉辊道上的定位控制,步进梁控制的功能。
回火炉传动系统采用变频控制,变频器是由西门子公司提供的 MM440 系列。
2 个带 PROFIBUS-DP 卡的 MM440 系列变频器控制 2 组辊道。
淬火炉仪控部分 PLC 主要由 S7 315-2DP 及功能模板 FM355C 闭环控制模块构成,每套 PLC 及其相 应的 PID 模块负责控制淬火炉的全部仪表,用来完成加热炉工艺参数的数据采集与过程控制。
采用西门 子 FM355C 闭环控制模块控制加热炉的工艺参数以达到加热炉最佳燃烧的控制效果。
回火炉仪控部分 PLC 与淬火炉仪控部分 PLC 的构成与功能基本上是一样的。
在过程计算机控制系统中,淬火炉和回火炉各设置一台计算机,对各自的加热炉系统进行硬件的组 态与参数设置、通讯的定义、编写、调试用户程序及画面的监控与数据的纪录,最终实现集中监控和操 作。
两台计算机为 SIEMENS 工控机,配置为 P4 2.0G,256M,并且带有工业以太网处理器 CP1613。
计 算机借助于 CP1613, 通过工业以太网光纤交换机 OSM, PLC 进行通讯。
与 工业以太网光纤交换机 OSM, 带有两个光纤接口和 6 个电气接口。