数控钻孔机控制系统设计
基于PLC控制的数控钻孔机的设计与实现

基于PLC控制的数控钻孔机的设计与实现随着科技的进步和工业自动化水平的提高,数控(Numerical Control)钻孔机在工业生产中得到了广泛的应用。
数控钻孔机的设计与实现基于PLC(Programmable Logic Controller)控制,PLC控制具有可靠性高、灵活性强等优点。
本文将介绍基于PLC控制的数控钻孔机的设计与实现。
首先,在数控钻孔机的设计中,我们需要考虑到几个方面。
首先是机械部分的设计,包括钻头的选择、主轴的设计、夹持装置的设计等。
其次是电气部分的设计,主要包括电机的选择、传感器的选择、电气线路的设计等。
最后是PLC控制程序的编写,需要根据实际需求设计钻孔程序。
在机械部分的设计中,我们需要选择适合的钻头来满足不同的钻孔需求。
常见的钻头有立铣钻头、圆滚钻头等。
主轴的设计需要考虑到主轴的转速和稳定性,可以选择带有变频器的电机来调整主轴的转速。
夹持装置的设计需要满足钻孔材料的夹持需求,可以选择气动夹紧装置或电动夹紧装置。
在电气部分的设计中,我们需要选择适合的电机来驱动主轴。
根据钻孔材料的不同,可以选择不同功率的电机。
传感器的选择需要满足对材料位置和尺寸的检测需求,可以选择接近开关、压力传感器等传感器。
电气线路的设计需要根据实际需求进行布线,保证线路的安全稳定。
在PLC控制程序的编写中,我们需要根据实际需求设计钻孔程序。
首先,我们需要编写一个启动程序,通过点击按钮或接近开关来启动钻孔机的工作。
然后,我们需要编写一个控制程序,通过设定参数来控制钻孔机的运行。
控制程序可以设置钻孔深度、钻孔速度等参数。
最后,我们还需要编写一个停止程序,当钻孔完成或发生异常情况时,通过点击按钮或接近开关来停止钻孔机的工作。
总结起来,基于PLC控制的数控钻孔机的设计与实现需要考虑到机械部分的设计、电气部分的设计以及PLC控制程序的编写。
通过合理的设计和实施,可以实现数控钻孔机的自动化控制,提高生产效率,降低人工成本,提高产品质量。
数控玻璃钻孔机床结构和控制系统设计

数控玻璃钻孔机床结构和控制系统设计数控玻璃钻孔机床是一种用于玻璃钻孔加工的专用设备,它能够根据预先设定的程序自动完成玻璃钻孔加工,具有高精度、高效率和稳定性等优点。
本文将从数控玻璃钻孔机床的结构和控制系统两方面进行设计分析。
1. 床身:床身是数控玻璃钻孔机床的主体部件,一般采用铸铁或焊接结构。
床身具有高刚性和高稳定性,能够承受加工过程中的各种力和振动。
床身上还配有T型槽,用于安装和固定工件夹具。
2. 主轴:主轴是数控玻璃钻孔机床的主要运动部件,其转速、进给速度和加工精度直接影响加工质量。
主轴通常采用高速电主轴,具有较大的转速范围和高刚性,能够满足不同直径和深度的钻孔加工需求。
3. 控制系统:控制系统是数控玻璃钻孔机床的关键部件,它能够根据预先设定的加工程序控制主轴、进给系统和冷却系统等各个部分的运动和工作状态。
控制系统一般采用PLC控制或数控系统,具有高稳定性和可靠性。
4. 进给系统:进给系统是数控玻璃钻孔机床的重要组成部分,它能够实现工件在X、Y、Z三个方向上的精确定位和进给运动。
进给系统通常采用直线导轨和高精度滚珠丝杠,能够实现高速、高精度的定位和运动。
5. 冷却系统:冷却系统用于对刀具和加工区域进行冷却,以防止刀具过热和工件出现变形等现象。
冷却系统一般采用喷淋式冷却和冷却液循环系统,能够有效提高加工质量和刀具寿命。
1. 硬件配置:数控玻璃钻孔机床的控制系统硬件包括主控制器、伺服驱动器、IO模块、人机界面等部件。
主控制器负责整个系统的控制和运行,伺服驱动器负责驱动主轴和进给系统的运动,IO模块用于输入输出信号的处理,人机界面用于操作和监控系统运行状态。
2. 软件系统:数控玻璃钻孔机床的控制系统软件包括系统运行软件、人机界面软件和加工程序编程软件等。
系统运行软件负责控制整个系统的运行和协调各个部分的工作,人机界面软件用于操作和监控系统运行状态,加工程序编程软件用于制定加工程序和参数设置。
3. 控制算法:数控玻璃钻孔机床的控制算法包括位置控制算法、速度控制算法和加工过程控制算法等。
数控钻床电气控制系统的设计本科毕业设计论文
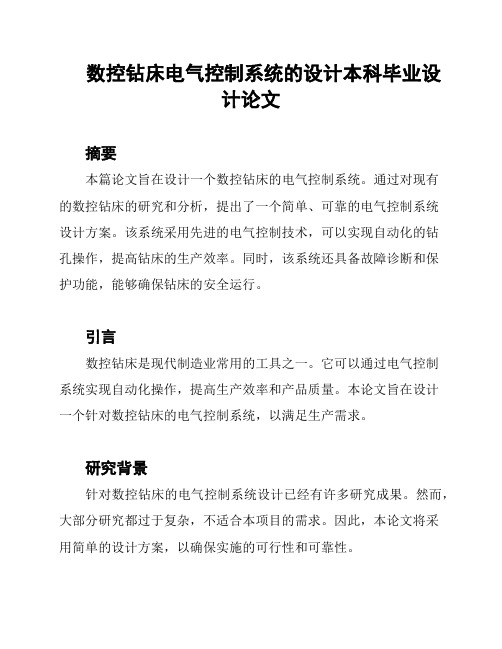
数控钻床电气控制系统的设计本科毕业设计论文摘要本篇论文旨在设计一个数控钻床的电气控制系统。
通过对现有的数控钻床的研究和分析,提出了一个简单、可靠的电气控制系统设计方案。
该系统采用先进的电气控制技术,可以实现自动化的钻孔操作,提高钻床的生产效率。
同时,该系统还具备故障诊断和保护功能,能够确保钻床的安全运行。
引言数控钻床是现代制造业常用的工具之一。
它可以通过电气控制系统实现自动化操作,提高生产效率和产品质量。
本论文旨在设计一个针对数控钻床的电气控制系统,以满足生产需求。
研究背景针对数控钻床的电气控制系统设计已经有许多研究成果。
然而,大部分研究都过于复杂,不适合本项目的需求。
因此,本论文将采用简单的设计方案,以确保实施的可行性和可靠性。
设计方案本论文提出了一个简单、可靠的电气控制系统设计方案。
该方案包括以下主要组成部分:1. 控制器:采用先进的控制单元,能够实现多种钻孔操作模式的切换和控制。
2. 传感器:用于检测钻头位置和转速,以及判断钻孔质量。
3. 电机驱动:采用高效的电机驱动技术,确保钻孔操作的精准和稳定性。
4. 人机界面:提供友好的操作界面,方便操作员进行参数设置和监控。
结论通过对数控钻床电气控制系统的设计,本论文提出了一个简单、可靠的设计方案。
该方案可以满足钻床的自动化操作需求,提高生产效率和产品质量。
同时,该方案还具备故障诊断和保护功能,确保钻床的安全运行。
希望本论文的设计方案能够对数控钻床的电气控制系统设计提供参考和借鉴。
基于PLC数控钻床控制系统设计

(此文档为word格式,下载后您可任意编辑修改!)摘要本文主要阐述了传统钻床PLC改造的可行性,并进行了具体的实施方案,传统钻床传统继电控制系统使用大量的中间继电器、时间继电器,控制触点多,因此电气控制系统存在故障率高、可靠性差、接线复杂、不便于检修等缺点.为了提高钻床控制系统的可靠性,降低故障率,提高钻床的加工效益,很多企业对传统控制钻床的电气控制系统进行了改造本文描述了数控机床的基本组成、工作原理、分类及各自的特点。
并且对数控机床中的PLC作了详细的介绍,把PLC在控机床上的控制做了设计。
然后以摇臂钻床Z3040为例,描述了它的设计过程,包括控制系统电路的设计,控制原理设计,主电路设计,主控制电路设计,Z3040摇臂钻床原理图,用PLC编写程序对机床进行控制。
关键词:可编程控制器数控机床数字控制液压控制梯形图原理图目录摘要.............................................................................................第1章绪论 (1)1.1.1 国外研究现状 (1)1.1研究现状与研究意义 (1)1.1.2 国内研究现状 (2)1.1.3 研究的意义 (3)1.2 PLC应用于数控钻出的可能性 (4)第2章总体设计方案 (10)2.1 总体方案的设计 (10)2.2元器件的选型 (11)2.3 PLC的主要类型 (11)2.4 本章小结 (11)第3章摇臂钻床控制线路设计 (13)3.1摇臂钻床控制线路概述 (13)3.1.1 操纵机构液压系统 (13)3.1.2夹紧机构液压系统 (14)3.2摇臂钻床控制线路原理设计 (15)3.3 Z3040摇臂钻床控制线路主电路设计 (16)3.4 Z3040摇臂钻床控制线路控制电路分析 (16)3.4.1主电动机控制电路 (16)3.4.2 摇臂升降控制电路 (16)3.4.3 立柱和主轴箱松开、夹紧控制电路 (17)3.4.4 冷却泵控制电路 (18)3.4.5 照明、信号电路 (18)3.5 本章小结 (18)第4章摇臂钻床PLC控制系统 (19)4.1 PLC的基本特点 (19)4.2 PLC的工作原理 (20)4.3 PLC的选型 (21)4.3.1 确定IO点数 (22)4.3.2 选配PLC的型号 (22)4.4摇臂钻床的PLC控制I0(输入、输出)地址分配表 (22)4.5 PLC控制系统设计 (24)4.5.1 主轴电动机控制 (24)4.5.2 摇臂升降控制 (24)4.5.3立柱与主轴箱松开、夹紧控制 (24)第5章技术展望 (25)结论 (27)参考文献 (27)致谢 (29)附录 (30)第1章绪论数控技术是制造业实现自动化、柔性化、集成化生产的基础;数控技术的应用是提高制造业的产品质量和劳动生产率必不可少的重要手段;数控机床是国防工业现代化的重要战略装备,是关系到国家战略地位和体现国家综合国力水平的重要标志。
基于plc数控钻床控制系统设计

摘要本文主要阐述了传统钻床PLC改造的可行性,并进行了具体的实施方案,传统钻床传统继电控制系统使用大量的中间继电器、时间继电器,控制触点多,因此电气控制系统存在故障率高、可靠性差、接线复杂、不便于检修等缺点.为了提高钻床控制系统的可靠性,降低故障率,提高钻床的加工效益,很多企业对传统控制钻床的电气控制系统进行了改造本文描述了数控机床的基本组成、工作原理、分类及各自的特点。
并且对数控机床中的PLC作了详细的介绍,把PLC在控机床上的控制做了设计。
然后以摇臂钻床Z3040为例,描述了它的设计过程,包括控制系统电路的设计,控制原理设计,主电路设计,主控制电路设计,Z3040摇臂钻床原理图,用PLC编写程序对机床进行控制。
关键词:可编程控制器数控机床数字控制液压控制梯形图原理图目录摘要.............................................................................................第1章绪论 (1)1.1.1 国外研究现状 (1)1.1研究现状与研究意义 (1)1.1.2 国内研究现状 (2)1.1.3 研究的意义 (3)1.2 PLC应用于数控钻出的可能性 (4)第2章总体设计方案 (10)2.1 总体方案的设计 (10)2.2元器件的选型 (11)2.3 PLC的主要类型 (11)2.4 本章小结 (11)第3章摇臂钻床控制线路设计 (13)3.1摇臂钻床控制线路概述 (13)3.1.1 操纵机构液压系统 (13)3.1.2夹紧机构液压系统 (14)3.2摇臂钻床控制线路原理设计 (15)3.3 Z3040摇臂钻床控制线路主电路设计 (16)3.4 Z3040摇臂钻床控制线路控制电路分析 (16)3.4.1主电动机控制电路 (16)3.4.2 摇臂升降控制电路 (16)3.4.3 立柱和主轴箱松开、夹紧控制电路 (17)3.4.4 冷却泵控制电路 (18)3.4.5 照明、信号电路 (18)3.5 本章小结 (18)第4章摇臂钻床PLC控制系统 (19)4.1 PLC的基本特点 (19)4.2 PLC的工作原理 (20)4.3 PLC的选型 (21)4.3.1 确定I/O点数 (22)4.3.2 选配PLC的型号 (22)4.4摇臂钻床的PLC控制I/0(输入、输出)地址分配表 (22)4.5 PLC控制系统设计 (24)4.5.1 主轴电动机控制 (24)4.5.2 摇臂升降控制 (24)4.5.3立柱与主轴箱松开、夹紧控制 (24)第5章技术展望 (25)结论 (27)参考文献 (27)致谢 (29)附录 (30)第1章绪论数控技术是制造业实现自动化、柔性化、集成化生产的基础;数控技术的应用是提高制造业的产品质量和劳动生产率必不可少的重要手段;数控机床是国防工业现代化的重要战略装备,是关系到国家战略地位和体现国家综合国力水平的重要标志。
基于PLC控制的数控钻孔机的设计与实现

基于PLC控制的数控钻孔机的设计与实现数控钻孔机是一种通过计算机数控系统实现自动钻孔的设备,可以实现高精度、高效率的钻孔作业。
本文将基于PLC控制的数控钻孔机的设计与实现进行详细介绍。
1.设计概述数控钻孔机主要由机械部分和控制系统两部分组成。
机械部分主要包括电动机、传动装置和钻头等,控制系统则由PLC控制器和人机界面组成。
2.机械部分设计为了实现高精度的钻孔作业,机械部分需要具备较高的稳定性和刚度。
首先,选择质量较好的电动机,通过减速装置将电动机的转速转为稳定的钻头转速。
其次,使用高硬度的刀具材料,以保证钻头在高速转动时不会变形。
最后,选择高精度的导轨和滑块,确保钻孔机在运动过程中无偏差。
3.PLC控制系统设计PLC控制系统是数控钻孔机的核心部分,它通过计算机数控系统来实现自动化的钻孔操作。
首先,选择适合的PLC控制器,通常选择具有高速计算和多IO口的控制器。
其次,编写PLC程序,根据用户输入的坐标参数和钻头尺寸,计算出钻孔的位置和深度。
然后,通过控制器的输出口,控制电动机的转速和钻头的升降运动,实现自动化的钻孔操作。
最后,在控制界面上添加合适的控制按钮和显示界面,方便用户操作和监测钻孔过程。
4.人机界面设计为了方便操作和监测钻孔过程,需要设计一个直观清晰的人机界面。
在界面上添加坐标输入框和尺寸调节按钮,方便用户输入钻孔的坐标和尺寸参数。
同时,添加控制按钮和监测指示灯,方便用户启动和停止钻孔过程,并实时监测钻孔状态。
另外,在界面上添加错误提示功能,当出现异常情况时能及时提示用户,并采取相应的应对措施。
5.钻孔机的实现在完成设计后,将机械部分和控制系统进行组装和调试。
首先,根据设计要求,选择适合的材料和加工工艺,制作机械部分的各个零件。
然后,组装机械部分,确保各个部件的协调配合。
接下来,将PLC控制器和人机界面与机械部分进行连接,并进行电气布线和信号调试。
最后,进行整机调试和测试,检查钻孔机的各项指标是否符合设计要求。
基于双MCU的数控锁芯钻孔机床控制系统设计
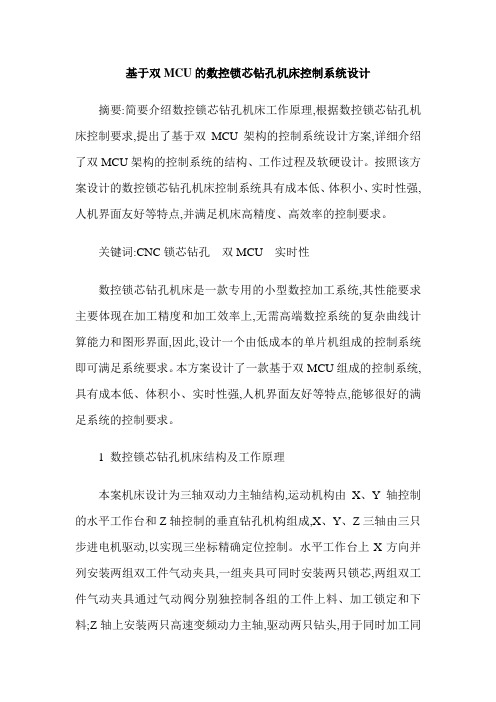
基于双MCU的数控锁芯钻孔机床控制系统设计摘要:简要介绍数控锁芯钻孔机床工作原理,根据数控锁芯钻孔机床控制要求,提出了基于双MCU架构的控制系统设计方案,详细介绍了双MCU架构的控制系统的结构、工作过程及软硬设计。
按照该方案设计的数控锁芯钻孔机床控制系统具有成本低、体积小、实时性强,人机界面友好等特点,并满足机床高精度、高效率的控制要求。
关键词:CNC锁芯钻孔双MCU 实时性数控锁芯钻孔机床是一款专用的小型数控加工系统,其性能要求主要体现在加工精度和加工效率上,无需高端数控系统的复杂曲线计算能力和图形界面,因此,设计一个由低成本的单片机组成的控制系统即可满足系统要求。
本方案设计了一款基于双MCU组成的控制系统,具有成本低、体积小、实时性强,人机界面友好等特点,能够很好的满足系统的控制要求。
1 数控锁芯钻孔机床结构及工作原理本案机床设计为三轴双动力主轴结构,运动机构由X、Y轴控制的水平工作台和Z轴控制的垂直钻孔机构组成,X、Y、Z三轴由三只步进电机驱动,以实现三坐标精确定位控制。
水平工作台上X方向并列安装两组双工件气动夹具,一组夹具可同时安装两只锁芯,两组双工件气动夹具通过气动阀分别独控制各组的工件上料、加工锁定和下料;Z轴上安装两只高速变频动力主轴,驱动两只钻头,用于同时加工同组的两只锁芯。
通过控制X轴步进电机定位加工组坐标(X坐标),控制Y轴步进电机定位加工组的锁芯孔位坐标(Y坐标),控制Z轴步进电机进行设定深度的钻孔加工(Z坐标)。
机床通过对上述机构的协调控制,以一组加工一组上料的交替工作方式,一次同时加工两只锁芯,从而实现了机床高精度、高效率的锁芯钻孔加工要求(如图1)。
2 控制系统的硬件设计2.1 控制系统方案由机床结构及其工作原理得知,本控制系统需要对X、Y、Z轴上的三只步进电机、两只用于钻孔的高速主轴电机以及两组气动夹具进行有机联动控制。
出于控制系统的成本和控制实时性要求考虑,本案控制系统采取双MCU系统设计,MCU1系统负责面板显示和按键处理,MCU2系统负责加工数据处理和运动控制,MCU1系统与MCU2系统之间采用双向全双工串行通信方式实行数据交换,如图2所示。
数控玻璃钻孔机床结构和控制系统设计

数控玻璃钻孔机床结构和控制系统设计1. 引言1.1 研究背景数已达到要求、分段等。
的内容如下:数控玻璃钻孔机床作为玻璃加工行业中的重要设备,其结构设计和控制系统设计直接影响到设备的性能和加工效率。
随着玻璃加工行业的不断发展和需求的不断增长,对于数控玻璃钻孔机床的精度、效率和稳定性提出了更高的要求。
传统的玻璃钻孔机床存在加工速度慢、精度低、适应性差等问题,无法满足现代玻璃加工行业的需求。
对数控玻璃钻孔机床的结构设计和控制系统设计进行深入研究和优化,具有重要的理论和实践意义。
通过对数控玻璃钻孔机床的结构和控制系统进行合理设计和优化,可以提高设备的加工精度、效率和稳定性,进而提升玻璃加工行业的整体竞争力。
本研究旨在针对数控玻璃钻孔机床的结构和控制系统进行系统性研究和优化,为玻璃加工行业的发展提供技术支持和解决方案。
1.2 研究目的数限制或者格式要求等。
感谢理解与配合!以下是关于的内容:研究目的是为了通过对数控玻璃钻孔机床结构和控制系统的设计、分析和优化,提高数控玻璃钻孔机床的加工精度、效率和稳定性,满足不同玻璃钻孔加工的需求。
通过深入研究数控玻璃钻孔机床的结构设计,可以优化其机械结构,提高其刚性和稳定性,从而减少加工误差,提高加工精度。
通过设计和优化数控玻璃钻孔机床的控制系统,可以实现对加工过程的精准控制,提高加工速度和效率,降低加工成本。
综合分析数控玻璃钻孔机床的结构和控制系统之间的匹配性,并进行性能优化,可以使数控玻璃钻孔机床达到最佳的加工效果。
最终通过实验验证,验证设计的数控玻璃钻孔机床结构和控制系统的有效性和稳定性,为实际生产中的应用提供科学依据。
1.3 研究意义数要求、格式要求等。
以下是关于的内容:通过对数控玻璃钻孔机床的结构设计进行研究,可以优化机床的机械结构,提高其稳定性和刚性,从而保证加工的精度和表面质量,同时减少废品率,提高生产效率。
针对数控玻璃钻孔机床的控制系统设计,可以实现对加工过程的精确控制,实现自动化加工,提高生产效率和加工精度。
- 1、下载文档前请自行甄别文档内容的完整性,平台不提供额外的编辑、内容补充、找答案等附加服务。
- 2、"仅部分预览"的文档,不可在线预览部分如存在完整性等问题,可反馈申请退款(可完整预览的文档不适用该条件!)。
- 3、如文档侵犯您的权益,请联系客服反馈,我们会尽快为您处理(人工客服工作时间:9:00-18:30)。
金华职业技术学院JINHUA COLLEGE OF VOCATION AND TECHNOLOGY毕业教学环节成果(2014届)题目数控钻孔机控制系统设计学院信息工程学院专业电气自动化技术班级自动化112学号201134010350201姓名指导教师2013年12月25日金华职业技术学院毕业教学成果目录摘要 (1)英文摘要 (1)引言 (2)1 数控钻孔机系统简介 (3)2硬件设计 (4)2.1 控制系统结构及工作原理 (4)2.2 主要器件选型 (5)2.3 PLC外围接线图 (6)2.4 控制系统设计原理图 (8)2.5 I/O口分配表 (8)3触摸屏界面设计 (9)4软件设计 (12)4.1 程序流程图 (12)4.2 控制程序的设计 (12)4.3 外围软件信号 (17)5参数整定 (17)5.1伺服电机定位参数设置 (17)5.2伺服系统内部参数设定 (19)6安装与调试 (20)6.1 控制系统接线图 (20)6.2模拟调试 (22)6.3 联机调试 (22)结论与谢辞 (22)参考文献 (23)附件1 (24)元器件清单 (24)附件2 (25)源程序 (25)附件3 (34)实物图 (34)数控钻孔机控制系统设计摘要:本文介绍了基于三菱Q系列PLC的数控钻孔机控制系统,该系统选用昆仑通态TPC7062KS嵌入版的触摸屏来实现人机交互,文中不但给出了数控钻孔机的基本架构,而且还简单分析了钻孔机控制系统的控制系统结构及工作原理与传感器的使用,以及介绍了PLC I/O口及钻孔机控制系统的布局图与接线图。
关键字PLC 钻孔机伺服控制Control system design of NC drilling machine(Information Engineering College of electrical automation technology Jin Ming) Abstract:This paper introduces the control system based on CNC drilling machine Mitsubishi Q series PLC, this system adopts KunLun on state of TPC7062KS embedded touch screen to realize man-machine interaction, this paper not only gives the basic architecture of the CNC drilling machine, but also a simple analysis of the use of drilling machine control system to control the system structure and the work principle and sensor, and introduced PLCI/O port and drilling machine control system layout and wiring diagram.Keywords: PLC drilling machine servo control引言数字控制(Numerical Control)是数字化信号对机床运动及其加工过程进行控制的一种方法,简称数控(NC)。
最初的数字控制系统是由数字逻辑电路构成的,因而称之为硬件数控系统。
随着计算机技术的发展,硬件数控系统被逐渐淘汰,取而代之的是计算机数控系统(ComputerNumerical Control,简称CNC)。
数控技术的广泛使用,给机械制造业的生产方式、产品结构、产业结构带来了深刻的变化。
数控技术是国防现代化的重要技术,是关系到国家战略地位和体现国家综合国力的重要基础性技术。
到目前为止,数控系统的发展主要经历了以下几个阶段:第一代:1952年,美国帕森公司和麻省理工学院合作研制了世界上第一台数控机床,它是一台三坐标数控铣床,用于加工直升飞机叶片轮廓检查用样板。
第二代:1959年,美国耐.杜列克公司发明了带有自动换刀装置的数控机床,广泛采用了晶体管和印刷电路板技术,称为“加工中心”。
第三代:电子行业出现了小规模集成电路。
由于体积小、功率低,使数控系统的可靠性进一步提高。
这几代数控系统都是利用逻辑电路来实现控制功能,因此被称之为“硬件“数控。
起功能简单、灵活性差、设计周期长,因此限制着其进一步的发展与应用。
随着计算机技术的发展,小型计算机开始取代专用控制的硬件逻辑数控系统(NC),数控的许多功能由软件来实现。
1970年,数控系统的发展进入了第四阶段,即计算机数控(CNC)阶段。
1974年,数控系统的发展进入了第五阶段,其特征是以微处理器为基础,另外采用超大规模集成电路、大容量磁泡存储器、可编程接口和遥控接口等,功能更为完备,基本上完成了标准型单机系统的开发。
数控系统的发展直到第五代以后,才从根本上解决了可靠性低、价格昂贵和应用不方便等关键性问题。
80年代初,便开始推广基于PC的开放式数控系统,但是直到90年代初才得以实现。
也就是数控系统的第六代——基于PC的数控系统。
世界上许多数控系统生产厂家利用PC机丰富的软硬件资源开发开放式体系结构的新一代数控系统。
其体系结构朝软性化、模块化的方向发展,辅助软件也发展很快,具有交互式对话编程、三维图形校验、实时多任务操作等,并向机床制造厂提供了开发手段,以AI(Artificial Intelligence,人工智能)方式纳入机床制造厂的丰富工艺经验,在产品上实现标准化系列化,可按用户需求来扩充、裁减,以满足不同用户层次的需求。
1.数控钻孔机系统简介其主要结构和功能是利用X轴的正转反转、Y轴的正转反转和Z轴的正转反转来实现定位钻孔,数控钻孔机系统结构如图1和图2所示,整个系统由控制系统和X—Y—Z 三轴构成。
操作人员按下操作界面上的外围启动,伺服放大器得电,这时数控钻孔机就可以运行了,系统运行关闭时,先按系统急停按钮,通过按轴手动控制框里的手动按钮各轴可实现点动运行,通过按数控定位按钮就可实现自动运行。
钻孔电机用50W的伺服电机,由伺服放大器驱动,Y轴用的是100W的伺服电机,X轴用的是50W的伺服电机,都是用伺服放大器驱动。
电机的启停可以通过触摸屏操作界面里的按钮进行控制。
图1 数控钻孔机前视图结构示意图图2 数控钻孔机俯视视图结构示意图2.硬件设计2.1控制系统结构及工作原理基于实际的数控钻孔机系统结构,确定数控钻孔机系统结构。
它由数控钻孔机系统、数控钻孔机控制系统、接口处理模块三部分组成。
PLC输出的控制信号经接口处理模块控制钻孔机的执行机构,控制各个轴的运行。
三轴钻孔机运行过程中,位置传感器的检测信号经接口处理模块输到PLC控制系统,实现闭环控制。
钻孔机控制平台由PLC、QD75P2定位模块、触摸屏、伺服放大器四部分组成如图3。
触摸屏设自动钻孔操作按钮,触摸屏输入操作命令传送到PLC,PLC通过检测轴的状态信息在相应的I/O口输出控制信号。
图3数控控制系统2.2主要器件选型2.2.1可编程控制器的选型PLC的厂家和品种很多,比如说美国的A-B公司、通用电气公司;德国的西门子;法国的TE;日本的、欧姆龙、富士、松下;韩国的LG等。
在本次控制系统中,采用三菱公司的Q模式CPU产品,这款产品有如下特点:(1)可以进行多点输入输出控制,所有CPU均支持可访问安装在基板上的输入输出模块的实际输入输出点数4096点(X/Y0~FFF)。
另外,最多可支持可用于CC—Link数据链接;(2)实现了运算的高速处理(例:LD指令时)通过与GX WORK2的高速通信,提高调试效率, QCPU系列三菱PLC采用RS一232端口,最高能适应11 5.2 kbps的高速通信的需要,缩短了程序写入、读出和监视等的时间,提高了调试时的通信时间效率。
(3)体积小,节省空间。
QCPU和Q系列输入输出模块、智能功能模块实现了小型化,体积比起AnS系列产品更加小。
其安装空间小,占据面积约为AnS系列产品的60%。
(4)只要增加模块,即能够扩展为大规模系统。
QCPU最多可增扩7级,最大可构建安装64块输入输出模块的系统。
(5)可以进行外部输入输出的强制ON/OFF。
即使QCPU处于运行状态,与程序的执行状态无关,可以通过操作GX Developer来进行外部输入输出的强制ON/OFF。
不必将QCPU设置在停止状态,只要对输出实施强制ON/OFF,就可以进行配线和动作试验。
2.2.2触摸屏的选型触摸屏选用昆仑通态TPC7062KS型,它是以嵌入式低功耗CPU为核心(ARM CPU,主频400MHz)的高性能嵌入式一体化触摸屏。
该产品设计采用了7英寸高亮度TFT液晶显示屏(分辨率800×480),四线电阻式触摸屏(分辨率1024×1024)。
灵敏度较高,而且具有防水防尘。
它可通过RS232、RS485或USB与PLC接口。
它的色彩比较丰富,由65535色7寸屏幕显示,可以增强视觉效果。
触摸屏有丰富资源库,在设计时可以在库里面选择适合元件。
还具有特点:1实现了显示,运算,通讯全方位的高速化;2高亮度(400cd/ m2)显示,提供免受外部光线干扰的完美图像;3 分辨率800×480,65535色TFT液晶显示;4显示尺寸:7英寸;5可视角度:左右70度,上下70/50度。
6 内置64MB标准内存。
2.2.3伺服电机的选择如今的伺服电机市场有很多的伺服电机,现在国内最常用的伺服电机有日系的三菱、松下、安川、三洋等,欧系的有西门子、施耐德、伦次,美国的科尔摩根等,国产的有台湾的台达、东元、大陆的广数、和利时等。
而在我们这里选用的伺服电机是三菱的HF-KP053型,这款伺服电机有以下的特点:(1)体积小,重量轻,大转矩输出。
(2)低惯性,良好的控制性能。
(3)宽广的调速范围,转矩脉动小。
2.2.4伺服放大器的选择在伺服放大器的选择上主要考虑伺服电机的功率,在系统设备中,伺服电机的功率为50W,所以选择三菱公司的MR-J3-10A型的伺服放大器。
此放大器的功率为100W,且设置方便,满足控制要求。
2.3 PLC外围接线图如图4左边的plc输入信号,右边的是plc输出信号。
图4 PLC外围接线图2.4 控制系统设计原理图PLC通过读取触摸屏里个按钮的状态来执行相应的程序,QD75模块通过读取PLC里正在执行的程序,把相应的参数存入QD75模块里,伺服放大器再通过读取QD75模块里的相关的参数来驱动各自对应的伺服电机运行。
伺服电机也会把脉冲数反馈给伺服放大器,伺服放大器又会把收到的数据反馈给QD75模块,判断是否运行到位了,QD75模块也会把收到的数据反馈回PLC里,PLC也会把其收到的数据反馈回触摸屏。